ТРЕБОВАНИЯ К ФОРМОВОЧНЫМ СМЕСЯМ
ФОРМОВОЧНЫЕ МАТЕРИАЛЫ И СМЕСИ
НАЗНАЧЕНИЕ И СВОЙСТВА
ФОРМОВОЧНЫХ МАТЕРИАЛОВ И СМЕСЕЙ
Разовые литейные формы и стержни изготовляют из материалов, которые называют формовочными. Различают исходные формовочные материалы, формовочные и стержневые смеси, а также вспомогательные формовочные составы.
Назначение. Исходные формовочные материалы разделяют на основные и вспомогательные.
К основным относят пески, являющиеся огнеупорной основой смесей, и связующие (глины, смолы и т. д.), соединяющие частицы песка между собой. Вспомогательные исходные материалы (различные добавки) предназначены для придания смесям специальных свойств, например, повышенной газопроницаемости.
Для получения формовочных и стержневых смесей смешивают различные исходные формовочные материалы, при этом состав смеси и количество входящих в нее компонентов зависят от назначения смеси. Кроме свежих исходных формовочных материалов в состав смеси обычно входит бывшая в употреблении смесь, подвергнутая специальной обработке (например, охлаждению, дроблению, магнитной сепарации, просеиванию, увлажнению).
Вспомогательные формовочные составы (краски, клеи, пасты) предназначены для улучшения качества поверхности форм и стержней, придания ей определенных свойств, для соединения частей стержней.
Свойства смесей. Качество форм и стержней определяется свойствами формовочных и стержневых смесей, которые должны отвечать определенным требованиям.
|
|
Текучесть - это способность смесей перемещаться под действием внешних усилий и заполнять опоки и стержневые ящики.
Пластичность - это свойство смеси деформироваться под действием внешних усилий и сохранять полученную форму после удаления модели или стержневого ящика. Пластичность зависит от состава смеси, например: в песчано-глинистых смесях от содержания в них глины и воды.
Прочность - способность смеси в уплотненном состоянии выдерживать, не разрушаясь, внешние воздействия. Она должна быть достаточной для того, чтобы формы и стержни не разрушались при их изготовлении, транспортировании, сборке и заливке расплавом.
Податливость - способность смеси в уплотненном состоянии деформироваться под действием сжимающих усилий, возникающих в процессе усадки при затвердевании и охлаждении отливок. При недостаточной податливости смеси в отливке могут образоваться трещины.
Газопроницаемость - свойство смеси пропускать газы. выделяющиеся при заливке и охлаждении из расплава, из стержня и самой формы, а также воздух, находящийся в ее полости. При недостаточной газопроницаемости в отливках образуются газовые раковины и поры.
|
|
Огнеупорность - способность смеси не размягчаться и не расплавляться под действием теплоты заливаемого в форму расплава.
Термохимическая стойкость - свойство смеси не вступать в физическое и химическое взаимодействие с жидким металлом, его оксидами и газами, выделяющимися в процессе заливки форм. Низкая термохимическая стойкость приводит к образованию трудно отделимого пригара, ухудшающего качество поверхности отливок и затрудняющего их очистку.
Кроме того, смеси должны обладать достаточной живучестью, т.е. сохранять свои свойства после приготовления в течение заданного промежутка времени, малой газотворностью, т.е. не выделять большого количества газов в процессе заливки, выбиваемос тью - легко удаляться из отливок после их охлаждения, негигроскопичностью.
ИСХОДНЫЕ ОСНОВНЫЕ И ВСПОМОГАТЕЛЬНЫЕ
ФОРМОВОЧНЫЕ МАТЕРИАЛЫ
Морфологический состав. Формовочные материалы являются продуктом разрушения горных пород под действием различных атмосферных явлений природы: тепловой энергии солнца, движения воздуха, воды. Перепады температуры в прогреваемой солнцем горной породе в различное время года создают в ней внутренние напряжения, вызывающие растрескивание, размельчение на более мелкие частицы. Измельченные частицы породы ветром и водами рек переносятся на значительные расстояния от места образования. По пути движения они осаждаются на дне водоемов, поверхности земли, образуя эллювиальные и аллювиальные отложения - залежи. В первом случае пески имеют остроугольную форму, во втором - округлую.
|
|
Залежи песков - не редкое явление, многие заводы с литейным производством работают на местных песках. Известный, например, своим художественным литьем Каслинский завод на Урале располагает местными, прекрасными для этого вида литья формовочными песками, обеспечивающими получение отливок с высоким качеством поверхности.
Зерновой состав характеризуется размером и формой зерен формовочного материала, соотношением между количеством зерен различных размеров. Зерновой состав влияет на свойства формовочных песков, определяющих качество приготовляемых из них формовочных смесей, литейных форм и отливок. Так, пески с крупными зернами, имеющими округлую форму и гладкую поверхность, обладают большей газопроницаемостью, чем пески с мелкими зернами, имеющими остроугольную форму и шероховатую поверхность.
|
|
Размер зерен песка влияет на качество поверхности отливки. Мелкие зерна обеспечивают более чистую поверхность отливки, чем крупные. Это очень важно в производстве художественного литья, где чистота поверхности и точность соответствия ее поверхности модели имеют первостепенное значение при оценке качества отливки.
Химический состав. В состав формовочных материалов входят различные минералы, которые, взаимодействуя с заливаемым в литейную форму металлом, создают в ней условия, влияющие на качество получаемой отливки. Зная химический состав формовочного материала, наличие в нем вредных и полезных примесей, можно оценить возможность его применения для приготовления формовочных смесей со свойствами, обеспечивающими получение отливок хорошего качества.
Качество формовочного материала улучшают на обогатительных фабриках. Там материал освобождают от вредных примесей путем промывки. С уменьшением количества вредных примесей (полевого шпата, извести и др.) в формовочном материале улучшается его химический состав, увеличивается вероятность получения отливки без пригара, газовых раковин, с гладкой поверхностью.
Технологические свойства формовочных материалов (прочность, газопроницаемость, пластичность, огнеупорность и др.) зависят от требований, предъявляемых к литейной форме. Например, формовочная смесь литейной формы для художественной отливки должна обладать хорошей пластичностью в целях обеспечения получения сложной поверхности.
Огнеупорная основа
Кварц
В качестве огнеупорной основы наибольшее распространение получили кварцевые пески. По происхождению они относятся к осадочным горным породам, которые получаются в результате разрушения изверженных или первичных горных пород (гранита, диабаза, базальта и др.). Важнейшей их характеристикой является время отложения и кратность переноса. Наиболее округлые и равные по величине зерна имеют пески, которые в течение длительного времени подвергались многократным переносам и повторным отложениям. Основой кварцевых песков является кремнезем или диоксид кремния Si02. Минерал кварц имеет плотность 2,65 г/см3, твердость 7 (по шкале Мооса), температуру плавления 1713° С. При нагреве кварц претерпевает несколько аллотропических превращений, которые сопровождаются изменением объема.
При заливке металла в форму зерна кварцевого песка нагреваются до различной температуры и претерпевают объемные изменения. В результате зерна частично растрескиваются и разрушаются.
Плавленый кварц (кварцевое стекло) является аморфным материалом. При нагревании он не претерпевает аллотропических превращений и в интервале от 20 до 1000 °С имеет очень низкий коэффициент линейного расширения, равный 0,5 × 10-6. После размола его применяют для изготовления керамических форм, чтобы предупредить их растрескивание, например, при литье по выплавляемым моделям.
Формовочный песок состоит из зерновой части и глинистой составляющей. В соответствии с ГОСТ 2138-91 к зерновой части относятся зерна размером более 22 мкм, к глинистой составляющей - менее 22 мкм.
В формовочных песках помимо кварца присутствуют и другие минералы: полевые шпаты, слюды, гидраты оксидов железа и т. д. К числу основных требований, предъявляемых к литейной форме, особенно к формам для крупных стальных отливок, относится высокая газопроницаемость и минимальное химическое взаимодействие с жидким металлом. Эти требования соблюдаются, если огнеупорная основа (кварцевый песок) содержит минимальное количество пылевидной фракции и минеральных примесей, которые при взаимодействии с расплавом могут образовывать легкоплавкие соединения.
В целях повышения качества формовочных песков их обогащают путем водной обработки, потоки воды удаляют пылевидную фракцию, инородные оксиды.
Классификация формовочных песков по составу в соответствии с ГОСТ 1238-91 представлена в табл., из которой следует, что наиболее качественными являются обогащенные пески.
Таблица
Классификация формовочных песков по составу
Песок | Класс | Содержание глинистой составляющей, % | Содержание кремнезема SiO2, % | Содержание вредных примесей, %, не более | |
Оксиды щелочных и щелочноземельных металлов | Оксиды железа | ||||
Обогащенный кварцевый | об1К | 0,2 | 98,5 | 0,40 | 0,20 |
об2К | 0,5 | 98,0 | 0,75 | 0,40 | |
об3К | 1,0 | 97,5 | 1,00 | 0,60 | |
Кварцевый | 1К | 2,0 | 97,0 | 1,20 | 0,75 |
2К | 2,0 | 96,0 | 1,50 | 1,00 | |
3К | 2,0 | 94,0 | 2,00 | 1,50 | |
4К | 2,0 | 90,0 | Не регламентируется | ||
Глинистый: тощий полужирный жирный очень жирный | Не регламентируется | ||||
Т | 2,0 - 10,0 | ||||
П | 10,0 - 20,0 | ||||
Ж | 20,0 - 30,0 | ||||
ОЖ | 30,0 - 50,0 |
Фракционный состав песка определяют путем просеивания через 11 сит с размерами ячеек от 2,5 до 0,005 мм. Остаток песка, расположенный на трех смежных ситах, называют основной фракцией песка. Ее содержание не должно быть менее 70% (табл.).
Таблица
Классификация формовочных песков по размеру зерен
Песок | Группа | Размер зерен основной фракции, мм |
Грубый | 063 | 1,000—0,400 |
Очень крупный | 04 | 0,630—0,315 |
Крупный | ОЗ15 | 0,400—0,200 |
Средний | 02 | 0,315—0,160 |
Мелкий | 016 | 0,200—0.100 |
Очень мелкий | 01 | 0,160—0,063 |
Тонкий | 0063 | 0,100—0,005 |
Пылевидный | 005 | 0,063 и менее |
Наиболее крупные пески (групп 04 и 0315) применяют для приготовления стержневых смесей. Пески группы 02 входят в состав формовочных смесей для стальных отливок, группы 016 - для чугунных отливок. Пески групп 0063 и 005 используют для приготовления противопригарных красок.
В зависимости от распределения на ситах основной зерновой фракции пески разделяют на категории А и Б. Если остаток на верхнем из трех смежных сит больше, чем на нижнем, пески относят к категории А, если он меньше - к категории Б.
В маркировке песка на первом месте стоит обозначение класса, на втором - зерновой группы, на третьем - категории. Например, маркировка об1К02А означает: обогащенный кварцевый песок класса об1К зерновой группы 0,2 категории А.
Магнезит металлургический
Металлургический магнезит МgO имеет плотность 3,0 г/см3. Температура плавления 2800 °С. Твердость 5,5-6 по шкале Мооса. Металлургический магнезит получают путем обжига природного магнезита МgСОз при температуре 1500-1600 °С. Его применяют для изготовления крупных отливок из титановых сплавов преимущественно при стационарной заливке.
Электрокорунд
Безводный оксид алюминия существует в нескольких модификациях. В природе встречается только a-фаза в виде корунда, сапфира, рубина. Плотность корунда составляет от 3,98 до 4,01 г/см3 в зависимости от наличия примесей. Температура плавления a-корунда 2050° С. Твердость 9 по шкале Мооса. Электрокорунд широко применяют при литье сплавов по выплавляемым моделям.
Диоксид циркония
Технический диоксид циркония содержит не менее 97,5% ZrO2. Его плотность равна 5,7 г/см3. Температура плавления 2700° С. Твердость 6,5 по шкале Мооса. Диоксид циркония применяют для изготовления отливок по выплавляемым моделям.
Хромомагнезит
Хромомагнезит состоит из МgO (42%) и Сr2О3 (15%). Он имеет плотность 3,9 г/см3 и огнеупорность 2000 °С. Его часто применяют при изготовлении противопригарных паст и красок при производстве массивных отливок из легированных сталей.
Хромит
Хромит (хромистый железняк) FeO × Сг2О3 имеет плотность 4,0 г/см3. Температура плавления 2180 °С. Твердость по шкале Мооса 5,5. Хромит используют в качестве наполнителя облицовочных смесей, а также паст и красок при изготовлении крупных стальных отливок.
Циркон
Циркон (силикат циркония) состоит из ZrO2 (63%) и SiO2 (32%). Это природный минерал плотностью 4,6 г/см3. Температура плавления 2600 °С. Твердость по шкале Мооса 7,5. Циркон используют в качестве наполнителя облицовочных смесей и особенно противопригарных красок при изготовлении отливок из стали и чугуна.
Дистен -силлиманит
Дистен-силлиманит состоит из природных алюмосиликатных материалов Аl2О3 (57%) и SiO2; (39%). Плотность 3,5 г/см3. Огнеупорность 1830 °С. Его применяют главным образом при литье по выплавляемым моделям, а также в качестве наполнителя облицовочных смесей и противопригарных красок при изготовлении особо сложных отливок из сталей и медных сплавов при литье в песчаные формы.
Связующие материалы
Связующие материалы, входящие в состав стержневых и формовочных смесей, предназначены для склеивания зерен песка и придания смесям необходимой прочности вначале в сыром, а затем в сухом или химически отвержденном состоянии.
Связующие материалы подразделяют по химической природе - на органические и неорганические, по способности растворяться в воде - на водные и неводные, по характеру затвердевания - на затвердевающие необратимо, обратимо и с промежуточным характером затвердевания. В отличие от неорганических, органические связующие выгорают при заливке расплава в литейную форму, что обеспечивает хорошую податливость стержней и их выбиваемость. Неорганические связующие (жидкое стекло, цемент) не выгорают, что затрудняет выбивку форм II стержней. Водные связующие проявляют свои свойства после растворения их в воде (лигносульфонаты технические, декстрин, патока). Неводные связующие не растворяются в воде и используются в виде растворов в органических растворителях (спирте, ацетоне и др.).
Необратимо затвердевающие органические и неорганические связующие обеспечивают получение смесей, обладающих наибольшей прочностью в сухом состоянии. Из смесей на основе этих связующих изготовляют сложные тонкостенные стержни.
К этой группе относятся растительные масла (льняное масло, олифа, отходы хлопкового масла СКТ-10), масла, получаемые на основе продуктов переработки нефти (П, ПТ), синтетические смолы, а также жидкое стекло.
Связующие на основе масел затвердевают только в процессе тепловой сушки при температуре 200-220 °С. Процесс сушки является длительной и энергоемкой операцией. Кроме того, растительные масла дороги и дефицитны. Поэтому более широко применяются синтетические смолы, использование которых позволяет изготовлять стержни без сушки, отверждаемые химически с большой скоростью непосредственно в нагреваемой или холодной оснастке. В последнем случае в связующее вводят катализаторы - ускорители затвердевания. В промышленности наиболее широко применяют связующие холодного затвердевания на основе фенолофурановых (фф-1ф), карбамидно-фурановых (фуритол, БС-40), фенолоформальдегидных смол (ОФ1, СФ-3042). В качестве связующих смесей, отверждаемых в нагреваемой оснастке, используют смолы (УКС, К.Ф-90, СФП-011Л и др.), которые при нагреве сначала расплавляются, связывая зерна песка, а затем необратимо твердеют, придавая стержню необходимую прочность.
Неорганическое связующее жидкое стекло представляет собой водный раствор силиката натрия Na2O×mSiO2×nH2O.
Особенностью жидкого стекла является способность быстро затвердевать при продувке углекислым газом или при тепловой обработке, что резко сокращает или устраняет операцию сушки.
Связующие, затвердевающие обратимо, восстанавливают свои свойства после охлаждения (канифоль, битумы, пеки) или при воздействии растворителя (лигносульфонаты технические, декстрин и др.). К связующим с промежуточным характером затвердевания относятся главным образом комбинированные составы, т. е. часть компонентов в них затвердевает необратимо, а часть обратимо. Стержневые смеси на основе этих связующих имеют повышенную прочность во влажном состоянии, их используют при изготовлении основной массы стержней. В промышленности широко применяют водорастворимые связующие этой группы. Наиболее дешевыми из них являются технические лигносульфонаты (ЛСТ)—продукты переработки древесины, поставляемые в жидком виде или в виде твердого концентрата. На их основе разработаны и широко применяются комбинированные связующие в виде эмульсий ЛСТ с окисленным петролатумом (СП) и тяжелой фракцией сланцевой смолы ГТФ (СБ).
Обобщенную классификацию связующих можно представить в виде табл.
Таблица
Классификация связующих
Класс | Группа | Обозначение | Наименование | Удельная прочность, Мпа |
1 | A-l | Синтетические смолы, высыхающие масла | Св. 0,5 | |
А | 2 | А-2 | Смолосодержащие продукты в сочетании с органическими материалами | 0,3—0,5 |
3 | А-З | Пеки (древесный, торфяной, каменноугольный), канифоль | До 0,3 | |
1 | Б-l | Синтетические смолы | Св. 0,5 | |
Б | 2 | Б-2 | Декстрин, пектиновый клей | 0,3—0,5 |
3 | Б-З | Сульфитно-дрожжевая бражка, патока | До 0,3 | |
1 | В-1 | Жидкое стекло | Св. 0,5 | |
В | 2 | В-2 | Ортофосфорная кислота и ее соли | Св. 0,5 |
3 | В-З | Цементы, глины | Св. 0,5 |
К классу А относятся органические связующие, не смачиваемые водой, к классу Б - органические связующие, растворяемые или смачиваемые водой, к классу В - неорганические связующие, растворяемые и смачиваемые водой.
Органические связующие (классы А и Б) при высоких температурах сравнительно легко разлагаются и обеспечивают хорошую податливость и выбиваемость.
Неорганические связующие (класс В) хорошо выдерживают воздействие высоких температур, но имеют низкую податливость и выбиваемость.
Многие свойства формовочных смесей определяются соотношением сил адгезии и когезии связующих материалов.
Адгезия - это слипание поверхностей двух разнородных или жидких тел под влиянием сил межмолекулярного взаимодействия. Она определяет, например, прочность сцепления пленки связующего материала с огнеупорным зерном.
Когезия - процесс межмолекулярного взаимодействия внутри одного тела. Силы когезии определяют, например, прочность пленки связующего материала или прочность огнеупорного зерна.
В зависимости от соотношения напряжений, создаваемых силами когезии и адгезии, разрыв двух зерен песка, связанных между собой пленкой связующего (рис. 1, а), может носить различный характер:
1) при sког > sадг происходит адгезионный разрыв (рис. 3.3, б);
2) при sадг > sког имеет место когезионный разрыв на пленке связующего (рис. 3.3, в);
3) при sадг » sког наблюдается смешанный разрыв (рис. 3.3. г);
4) при sадг+ sког > sког.зерна, отмечается когезионный разрыв по
зерну (рис. 3.3, д).
Рис. 1. Схема разрыва двух зерен песка,
связанных пленкой связующего материала:
1 - зерно песка; 2 - пленкя связующего материала.
В реальных условиях чисто когезионный разрыв по пленке связую-
щего практически не происходит. Для большинства связующих материалов наиболее характерен адгезионный разрыв. Исключение составляют жидкостекольные смеси, в которых из-за значительных сил адгезии связующего к поверхности зерен песка имеет место смешанный разрыв или когезионный разрыв по зерну.
Глины
Формовочные глины являются горными породами, которые состоят из тонкодисперсных частиц водных алюмосиликатов, обладающих высокой связующей способностью и термохимической устойчивостью, а также пластичностью после увлажнения.
В состав формовочных глин входят минералы группы каолинита, монтмориллонита (бентонита) и гидрослюд.
Каолинит А120з • 2SiO2 • 2H2O имеет твердость 2 по шкале Мооса, плотность 2,6 г/см3, температуру плавления 1750° С. Кристаллы каолинита представляют собой двухслойные пакеты с размером в поперечнике 2 - 4 мкм. В сухом состоянии каолинит поглощает влагу, образуя пластичное тесто. При нагреве претерпевает следующие превращения: в интервале температур 100 - 400°С удаляется поверхностно-связанная влага, при 550 - 690 °С - химически связанная влага, при 900 - 1050 °С полностью разрушается кристаллическая решетка каолинита и он превращается в аморфные глинозем и кремнезем, при 1200 - 1280 °С образуется новый минерал - муллит (ЗAl2O3·2SiO2).
Монтмориллонит (бентонит) Аl2O3 ·4SiO2 • Н2O • пН2O имеет температуру плавления 1250 - 1300 °С. Плотность 1,0 – 2,0 г/см3. Кристаллы монтмориллонита представляют собой трехслойные пакеты с размером в поперечнике 0,2 – 1,0 мкм. При нагреве до 100 - 200 °С удаляется поверхностно-связанная влага, при 500 - 700 ° С - химически-связанная влага, что сопровождается необратимой дигидратацией минерала, при 700 - 900 ° С кристаллическая решетка разрушается и минерал превращается в аморфные вещества. Отличительной особенностью монтмориллонита является высокая интенсивность набухания при увлажнении. При набухании промежутки между отдельными пакетами значительно расширяются, содержание поверхностно-связанной воды при этом увеличивается с 6 до 30% и более.
Гидрослюды являются промежуточным продуктом разложения слюды в каолин.
Кроме упомянутых выше минералов в формовочных глинах присутствуют кварц, полевой шпат, гидриды или оксигидриды железа.
Размер зерна формовочных глин оказывает существенное влияние на их связующую способность. Мелкозернистые (высокодисперсные) глины имеют большую связующую способность. При анализе фракционного состава глин, также, как и для формовочных песков, различают зерновую часть (частички размером более 22 мкм) и глинистую составляющую (частички размером менее 22 мкм). В свою очередь, глинистая составляющая подразделяется на грубодисперсную (размер частичек составляет от 22 до 5 мкм), мелкодисперсную (от 5 до 1 мкм) и коллоидную (менее 1 мкм) части.
При определении дисперсности глин используют метод осаждения глинистых частичек из водных суспензий. В отличие от дисперсной, коллоидная часть не осаждается. Частички размером менее 1 мкм в водной среде получают электрический заряд, и вокруг них образуется сольватная оболочка.
При оценке коллоидальности глин в раствор добавляют электролит. Объем осадка, отнесенный к объему всего раствора и выраженный в процентах, является мерой коллоидальности глины. Чем выше коллоидальность, тем выше связующая способность глины. Например, связующая способность монтмориллонитных глин, коллоидальность которых достигает 100%, почти в два раза выше, чем каолинитовых.
Этилсиликат
Этилсиликат является основой для приготовления связующего при литье по выплавляемым моделям. Он представляет собой смесь этиловых эфиров ортокремниевой кислоты. Это - прозрачная жидкость с температурой кипения 165°С, плотностью 0,98 - 1,05 г/см3. Этилсиликат состоит из эфиров разной молекулярной массы, например: моноэфира (С2H5O)4Si, условно в пересчете содержащего 28,8% SiO2; диэфира (С2H5O)SiO2, содержащего 35,1% SiO2; триэфира (С2H5O)8Si3O2, содержащего 39,7% SiO2 и так далее (тетра- и пента- эфиры).
Для придания этилсиликату свойств связующего его подвергают гидролизу. При этом в процессе химической реакции этоксильные группы (С2H5O) замещаются на гидроксильные (ОН). В результате реакции образуются коллоидные растворы кислот (золи), из которых при сушке и прокаливании форм выделяется собственно связующее SiO2, соединяющее зерна огнеупорной основы суспензии.
Гидролиз этилсиликата затруднен тем, что вода и этилсиликат взаимно не растворяются. Поэтому применяют органические растворители (спирты, ацетон), которые растворяют и этилсиликат, и воду. При сушке и прокаливании растворители удаляются.
Гидролиз может осуществляться любым количеством воды.
Продукты частичного гидролиза полимеризуются, образуя преимущественно полимеры линейного строения, в которых неорганические главные цепи молекул, построенные из атомов кремния и кислорода на основе весьма прочных силикатных связей (—Si—О—Si—), обрамлены органическими этоксильными группами.
В России производят этилсиликат двух марок ЭТС-32 и ЭТС-40. Число, указанное в марке, соответствует среднему условному содержанию диоксида кремния (в процентах по массе).
Для приготовления связующих растворов из ЭТС-32 и ЭТС-40 их подвергают гидролизу и разбавляют таким образом, чтобы содержание SiO2 составляло 10 - 18%. Особенность приготовления таких растворов состоит в том, что в зависимости от количества вводимой в них воды можно получить совершенно различные по составу и свойствам связующие.
При гидролизе малым количеством воды образуются связующие растворы из линейных полимеров, пригодные для длительного хранения. В структуре имеется большое количество негидролизованных этоксильных групп. Пленки таких связующих при сушке на воздухе полностью не отверждаются. Догидролиз обычных полимеров осуществляется подачей в сушильную камеру паров влаждого аммиака. Отвержденные полимеры образуют прочные и достаточно эластичные пленки связующего. Оболочки с таким связующим имеют прочность при изгибе 8-10 МПа.
При гидролизе средним количеством воды образуется смесь истинных растворов кремнийорганических полимеров и коллоидных растворов кремнекислот. При хранении их вязкость постепенно повышается. Сушка должна производиться при повышенной влажности воздуха. Применение аммиачной сушки нежелательно. Прочность при изгибе оболочек с этим связующим составляет 5 - 7 МПа, что в большинстве случаев вполне достаточно.
Связующие, образующиеся при гидролизе этилсиликата большим количеством воды, представляют собой коллоидные растворы кремнекислот, т. е. гели. В этих растворах происходит самопроизвольное укрупнение коллоидных частиц - мицелл. Гели обладают структурой рыхлой пространственной сетки. Существенным недостатком этого связующего является малая живучесть. Кроме того, прочность оболочек при изгибе существенно ниже по сравнению с предыдущими вариантами и составляет 2,5 - 4,0 МПа. Сушка производится без использования аммиака. Для ускорения сушки применяют сухой подогретый воздух.
Жидкое стекло
Жидкое стекло (ГОСТ 13078-81) является водным раствором силиката натрия. Его получают сплавлением кварцевого песка и соды либо кварцевого песка, сульфита натрия и угля при температуре 1400 - 1500°С с последующим растворением в воде до плотности 1,36 - 1,50 г/см3, осуществляемым в автоклавах.
Связующая способность жидкого стекла определяется его модулем, который отражает отношение массовых долей диоксида кремния (Si02) и оксида натрия (Na2O).
Модуль определяют по формуле
Si02
М=— • 1,032,
Na 2O
где 1,032 - соотношение молярных масс оксида натрия и диоксида кремния.
В зависимости от значения модуля различают три марки жидкого стекла: А, Б и В. Наибольшее распространение получило жидкое стекло марки В с модулем 2,61-3,0, в котором массовая доля Si02; составляет 31-33%. a Na 2O - 10-12% .
От значения модуля жидкого стекла зависит удельная прочность и живучесть смеси. Чем выше модуль, тем выше прочность и ниже живучесть (рис. 3.6). В целях повышения живучести смесей для крупных форм, изготовление которых занимает много времени, значение модуля жидкого стекла искусственно снижают до 2,0-2,3 введением водного раствора едкого натра.
Упрочнение форм осуществляется тремя способами: 1) воздушной сушкой в течение 2-8 ч; 2) тепловой сушкой при температуре 220-250 ° С в течение 30-60 мин; 3) химической сушкой (продувкой углекислым газом, введением феррохромового шлака, эфиров угольной кислоты).
При продувке углекислым газом происходит следующая реакция:
Na 2O • Si02 + CO2 +Н 20® Na 2C0 3+ nSi02 · mH 2O.
гель кремниевой кислоты
Синтетические смолы
В качестве связующих применяют различные фенольные, фенолофурановые, карбидофенолофурановые, карбидофурановые и другие искусственные (синтетические) смолы.
При использовании смол, функциональные группы которых не способны к интенсивному межмолекулярному взаимодействию, их отверждение достигается за счет применения катализатора без теплового воздействия.
Отверждение смол, функциональные группы которых склонны к межмолекулярному взаимодействию (например, термореактивных формальдегидных смол), не требует использования катализаторов. Отверждение ускоряется тепловым воздействием.
Сульфитно-дрожжевая бражка
Сульфитно-дрожжевую бражку, которая относится к лигносульфонатам, получают из сульфитного щелока, образующегося при сульфитной варке целлюлозы. Путем биохимической обработки сульфитного щелока из него извлекают этиловый спирт, кормовые дрожжи, органические кислоты, многоатомные спирты. Продукт, оставшийся после упаривания, и есть концентрат сульфитно-дрожжевой бражки.
Отверждение формовочных смесей осуществляется как тепловой обработкой, так и химическим способом путем введения отвердителей.
Фосфатные композиции
Связующим материалом является композиция, которая состоит из порошкообразных оксидов, обладающих основными свойствами, и ортофосфорной кислоты или водных растворов ее солей.
Например, при формировании железофосфатов химическая реакция протекает по следующей схеме:
Fe0 + 2Н 2РО 4 +Н 2О® Fе(Н 2Р0 4)2 · 2Н 20
кристаллогидрат фосфата железа
В последнее время широкое применение находят алюмохромофосфатные и магниеалюмофосфатные связующие (АХФС и МАФС).
Цемент
В качестве связующего материала используют два типа цементов - портландцемент и глиноземистый цемент.
Цемент получают путем обжига сырьевой смеси, например, известняка и глины.
Твердение смеси происходит в результате выделения из перенасыщенного водно-цементного раствора кристаллогидратов, которые, срастаясь друг с другом, образуют прочный кристаллический каркас, скрепляющий зерна песка. При использовании портландцемента кристаллогидратами является гидросиликаты кальция, а при использовании глиноземистого цемента - гидроалюминаты кальция.
Механизм твердения портландцемента можно представить следующей химической реакцией:
2(ЗСаО ·SiO2) +6H 20®ЗСаО · 2Si02· ЗН 2О + ЗСаО(ОН)2.
гидросиликат кальция
Масло и его заменители
Растительные масла являются лучшими связующими для стержневых смесей. Они придают им исключительно высокие физико-механические свойства, что позволяет из таких смесей изготавливать очень сложные тонкие с несколькими полостями стержни.
Связующее действие масла заключается в том, что оно обволакивает каждую песчинку и при сушке окисляется, образуя плотную пластичную пленку, состоящую из сложного соединения - линоксина. Окисление масла протекает быстрее при повышенных температурах и в присутствии катализаторов - сиккативов. Оптимальная температура сушки 200 - 220° С. Процесс окисления масла является необратимым.
Поскольку применение в литейном производстве растительных масел, относящихся к продуктам питания, запрещено, вместо них используют заменители:
связующее 4ГУ - раствор растительного масла или рыбьего жира (25%) и канифоли (50%) в уайт-спирите;
связующее П - раствор окисленного бакинского петролатума (32%) и битума (18%) в уайт-спирите (55%);
связующее ГТФ - генераторная тяжелая фракция сланцевой смолы, получаемая при тепловой обработке эстонских сланцев;
связующее ЗИЛ - раствор битума (25%) и ГТФ (55%) в уайт-спирите (20%);
связующее СП - эмульсия сульфитно-дрожжевой бражки; связующее УСК-1 - продукт термообработки кубового остатка синтетических жирных кислот, асфальтосмолистых веществ и парафиновых углеводородов;
раствор канифоли в ацетоне, скипидаре, спирте и других органических жидкостях.
Гипс
Гипс как связующее применяется главным образом в ювелирной промышленности. Имеются сведения о применении гипсовых форм при изготовлении отливок из цветных сплавов в основном с низкой температурой плавления.
В природе гипс встречается преимущественно в виде дигидрата гипсового камня (CaSO4 • 2H2O).
Гипсовый камень при нагреве до 107°С разлагается. Реакция протекает по следующей схеме:
CaSO4 · 2Н 2О = CaS04 • 0,5H 20 + 1,5H 20.
В зависимости от способа тепловой обработки образуется b- или a-модификация полуводного гипса. Модификации различаются кристаллической структурой и свойствами.
В интервале температур 170-200 ° С продолжается удаление химически-связанной воды.
После полного удаления воды в интервале температур 200-300 ° С полугидрат почти полностью переходит в растворимый ангидрид.
При температурах 300-450 °С получается «намертво» обожженный гипс, который почти совсем не схватывается.
При более высоких температурах (750-1000 °С) образуется эстрих-гипс, характеризующийся медленным схватыванием и небольшой механической прочностью.
Прочность гипса определяется тем, насколько тесно кристаллы дигидрата сплелись друг с другом, как срослись в кристаллические группы и агрегаты. Значительную роль при этом играют форма и размер кристаллов.
В процессе затвердевания гипса происходит ряд химических и физических изменений. Процесс затвердевания заключается в том, что гипсовое тесто, представляющее собой механическую смесь порошкообразного гипса (полугидрата) и воды, превращается в камневидное тело, постепенно густея и уплотняясь. Затвердевание заканчивается после того, как образовалась структурная решетка из кристаллов двугидрата. Прочность гипса достигает максимума при высушивании,
Специальные добавки
Основное назначение добавок - изменять качество формовочных смесей и предупреждать образование дефектов в отливках.
Феррохромовый шлак, углекислый газ, антипирен, пропиленкарбонат ускоряют отверждение песчано-жидкостекольных смесей.
Хромовый ангидрид, гидрогранат (трехкальциевый силикат) используют в качестве отвердителей песчано-лигносульфонатных смесей.
Ортофосфорная кислота и бензосульфокислота ускоряют отверждение формовочных смесей, в которых в качестве связующего используются карбамидоформальдегидные, карбамидофурановые и фенолформальдегидные синтетические смолы.
Едкий натр и крахмалит повышают живучесть жидкостекольных смесей.
Для улучшения выбиваемости жидкостекольных смесей применяют гидрол, инден-кумароновую смолу, асбестовую крошку, древесные опилки.
Переход жидкостекольных смесей из пластичного в жидкое состояние ускоряют различные поверхностно-активные вещества.
Образование пригара на отливках предупреждают добавки, создающие в форме восстановительную атмосферу (уголь гранулированный и пылевидный, мазут топочный, древесный пек, древесная мука) или окислительную атмосферу (марганцевая руда, железная руда, пентаоксид ванадия, сульфат натрия).
Чтобы исключить появление горячих трещин, в смесь вводят древесные опилки, древесную муку, мазут топочный.
В качестве добавок, снижающих окисляемость магниевых сплавов, используют борную кислоту, фтористые присадки, присадки ВМ (борная кислота, мочевина, сернокислый алюминий).
ТРЕБОВАНИЯ К ФОРМОВОЧНЫМ СМЕСЯМ
Классификация формовочных смесей
Вне зависимости от заливаемого металла формовочные смеси делят по характеру использования, по состоянию формы и классу применяемого песка.
Формовочные смеси, применяемые в литейном производстве, подразделяют по нескольким признакам:
1) по виду использования - облицовочные, наполнительные, единые;
2) в зависимости от применяемых при приготовлении смеси песков - природные (естественные) и искусственные (синтетические);
3) по роду применяемого для отливки металла - для стального, чугунного и цветного литья;
4) по состоянию формы перед заливкой - для форм, заливаемых в сыром состоянии, и для форм, заливаемых после сушки;
5) специальные формовочные смеси.
В массовом производстве применяют единые смеси, в единичном и мелкосерийном производстве для изготовления крупных форм - две смеси: облицовочную, наносимую на поверхность модели, и наполнительную, заполняющую остальной объем формы.
Единые смеси должны обладать высокими свойствами, потому что они соприкасаются с жидким металлом. Степень освежения единых смесей (5-15 %) значительно меньше, чем у облицовочных (20-100 %), так как вводимые в единую смесь свежие пески и глины при одинаковом их расходе распределяются по всему объему формы, а не только в облицовочном слое. Степень освежения смесей зависит от количества заливаемого в форму металла, его температуры, а также от безвозвратных потерь смеси в процессе производства отливок.
Облицовочной называют такую смесь, которую используют для изготовления рабочего слоя формы, соприкасающегося с моделью (а, следовательно, и с отливкой). Облицовочная смесь, воспроизводящая отпечаток поверхности модели, первая принимает на себя температурные воздействия заливаемого в форму металла и должна обладать хорошей прочностью, пластичностью, огнеупорностью и газопроницаемостью. Поэтому облицовочная смесь содержит, как правило, большой процент свежих формовочных материалов и, как наиболее дорогая, используется в форме в небольших количествах, слоем 20-30 мм (на поверхности модели).
Наполнительные смеси отделены от металла слоем облицовочной смеси, поэтому к ним в основном предъявляют требования по газопроницаемости и прочности, которые должны быть не ниже, чем у облицовочных смесей. В наполнительные смеси свежие материалы не вводят.
Формовочные смеси при машинной формовке вследствие особенностей технологического процесса формовки используются одновременно в качестве облицовочной и наполнительной смеси и называются едиными.
Природные (естественные) смеси представляют собой глинистые пески марок П0063 и Ж005 с содержанием глины от 12 до 30%. Природные формовочные смеси широко применяют в производстве тонкостенных ажурных и кабинетных чугунных и цветных отливок для форм, заливаемых в сыром состоянии и после сушки. Эти смеси обладают хорошей пластичностью и прочностью.
Искусственные (синтетические) смеси - наиболее распространенные в производстве художественных и архитектурных отливок. Они представляют собой смесь песка и глины или нескольких песков с большим или меньшим содержанием глины и отработанной смеси. Пески и оборотную смесь смешивают в таких пропорциях, чтобы в результате образовалась формовочная смесь, обладающая необходимыми технологическими свойствами.
Формовочные смеси для форм чугунных отливок. Состав формовочных смесей (табл. 8) зависит от конфигурации и сложности поверхности отливок, толщины их стенок и состояния литейной формы перед заливкой. Смеси для ажурных отливок, имеющих сложную поверхность, тонкие стенки и большое число просветов, образующих ажур, должны обеспечивать получение в форме четкого отпечатка сложной поверхности модели и прочность мельчайщих болванчиков, дающих просветы в отливке. Кроме того, при заливке в форму чугун по сравнению с цветными сплавами имеет более высокую температуру. Поэтому формовочные смеси для форм, заливаемых чугуном, должны иметь достаточную огнеупорность.
Повышение температуры заливки чугуна приводит, к более интенсивному газовыделению при прогреве формы, поэтому формовочные смеси должны иметь хорошую газопроницаемость. Таким образом, формовочные смеси для форм, заливаемых чугуном, при достаточной прочности должны быть газопроницаемыми и огнеупорными.
Формовочные смеси для форм отливок из цветных сплавов . Латунь, бронза и алюминиевые сплавы, применяемые в производстве художественного литья, по сравнению с чугуном имеют более низкую температуру заливки и большую жидкотекучесть. Поэтому при изготовлении литейных форм представляется возможным применять мелкозернистые формовочные смеси, дающие чистую и гладкую поверхность отливки.
Формовочные смеси для формовки по-сырому . Формовкой по-сырому изготовляют литейные формы для тонкостенных и ажурных отливок (барельефы, ажурные тарелки, вазы, детали статуэток).
Для получения в форме хорошего отпечатка, сложной поверхности модели и обеспечения прочности небольших болванчиков, образующих просветы в отливке, формовочные смеси должны иметь хорошую газопроницаемость, пластичность и быть достаточно прочными. Поэтому при приготовлении смесей применяют мелкозернистые пески с повышенным содержанием глины.
Смеси для форм, заливаемых в сыром состоянии, применяют и при изготовлении форм для архитектурных отливок. В этом случае большая масса отливки и размеры форм требуют применения в формовочных смесях более крупных песков и повышающих огнеупорность смеси добавок.
Формовочные смеси для формовки по-сухому . Литейные формы статуй и бюстов значительно сложнее обычных. Для их изготовления применяют, как правило, сложную кусковую формовку. При такой формовке формовщик, разбирая форму для удаления модели, имеет дело не с полуформами, предохраняемыми от разрушения, а с частями формы в виде спрессованных кусков формовочной смеси. Естественно, что такие формы должны быть изготовлены из более прочных формовочных смесей.
При кусковой формовке поверхность формы должна выдерживать давление не менее 0,9 МПа. Газопроницаемость таких смесей в сыром состоянии вследствие содержания большого количества глины низкая (20-25 единиц). Поэтому литейные формы, изготовленные из этих смесей, нельзя заливать в сыром состоянии, так как повышенное количество пара и газа не сможет свободно выходить из формы через ее стенки. Газопроницаемость форм, изготовляемых из жирных формовочных смесей, повышают путем их сушки. В процессе сушки в результате испарения влаги и выгорания добавок увеличивается пористость формы. Газопроницаемость смеси в форме после сушки повышается до 60 - 70 единиц.
Смеси, формы из которых заливают после сушки, называют формовочными смесями для формовки по-сухому.
В качестве наполнительной смеси используют одну отработанную смесь. Освежают ее неперегоревшими кусками форм, набиваемых из жирной облицовочной смеси.
Специальные формовочные смеси . К специальным относятся смеси, в которых кварцевые пески заменены другими высокотеплопроводными материалами, и смеси, в которых связующим является не глина.
В производстве художественного литья часты случаи, когда сложность отливки требует применения особых способов изготовления литейной формы, применения специальных формовочных смесей.
Облицовочные смеси с высокой теплопроводностью применяют для изготовления крупных или сложных стальных отливок. Это смеси на основе хромита и воды (6-7 %) без добавления связующего. Применяют также смеси на основе хромомагнезита, который вводят в смесь в виде мелкого порошка. В качестве связующего в этих смесях используют сульфитно-спиртовую барду или жидкое стекло.
Формовочные и стержневые смеси, в которых связующим является жидкое стекло, широко применяют на практике для производства отливок из стали, чугуна, медных и алюминиевых сплавов. Смеси приготовляют из 97-95 % песка 1К01А - ЗК02А, 3-5 % глины, 5-7 % жидкого стекла. Влажность смесей 3-4,5 °/о. Можно использовать вместо кварцевого песка до 50 % отработанной смеси.
Смеси называются самотвердеющими, если выполненные из них формы и стержни твердеют на воздухе без обработки. Для этого в самотвердеющие жидкостекольные смеси вводят материалы, ускоряющие процесс твердения, например, феррохромный шлак с высоким содержанием СаО. В результате в смеси образуется кальцевый силикат вместо натриевого, который не растворяется в воде и способствует быстрому твердению смеси на воздухе.
Жидкие формовочные смеси применяют при формовке скульптурных отливок для нанесения облицовочного слоя на поверхность восковой модели и изготовления стержня в форме. На поверхность модели жидкую смесь наносят путем оплескивания модели, при изготовлении стержня смесь заливают в полость гипсовой формы. В состав жидкой формовочной смеси входят кварцевые пески, маршаллит, цемент и вода.
Суспензию на этилсиликатном связующем применяют для нанесения на поверхность выплавляемой модели слоя, который после ее выплавления образует неразъемную керамическую форму - оболочку для отливки.
Связующим суспензии является гидролизованный раствор этилсиликата, наполнителем - пылевидный кварц (маршаллит) марок КП1, КП2, прокаленный при температуре 850-900 °С и просеянный через сито с шелковой сеткой.
Песчано-смоляные смеси применяют в производстве отливок, получаемых в оболочковых формах. В состав смеси в качестве наполнителя входит кварцевый песок с зернами размером менее 0,2 мм. В качестве связующего используют термореактивную смолу. В целях экономии дорогостоящих смол оболочки полуформ изготовляют двухслойными. В этих случаях песчано-смоляные смеси делят на облицовочные и наполнительные. Облицовочные приготовливают с большим содержанием смол, наполнительные - с меньшим.
Приведенные в табл. 8 сведения о составе и свойствах смесей являются средними ориентировочными. Эти данные могут уточняться в зависимости от конкретных производственных условий.
Стержневые смеси. К стержневым смесям предъявляют более высокие требования, чем к формовочным в отношении прочности, газопроницаемости, газотворности, податливости, выбиваемости и огнеупорности, так как во время заливки и охлаждения металла в форме стержни в большей мере соприкасаются с металлом и интенсивнее прогреваются. Стержневые смеси выбирают в зависимости от конфигурации и размеров стержней, положения их в форме, заливаемого сплава и толщины стенки отливки.
К вспомогательным формовочным составам относят материалы, наносимые на поверхность форм и стержней для улучшения чистоты поверхности отливок.
На поверхность форм, заливаемых в сыром состоянии, наносят противопригарные покрытия, называемые припылами. В качестве припыла форм стальных отливок применяют пылевидный кварц, а форм крупных толстостенных чугунных отливок - серебристый графит.
Сухие формы и стержни покрывают противопригарными красками. В состав красок входят огнеупорные материалы, связующие и специальные добавки, уменьшающие расслаивание красок.
Огнеупорный материал (наполнитель) выбирают для красок в зависимости от сплава отливки, например, для стальной отливки - пылевидный кварц; чугунной - графит или смесь из графита, кокса и пылевидного кварца, а для отливок из цветных сплавов - тальк.
В краски вводят 3-10 % связующих класса Б. Растворителем в красках служит вода. Таккак порошок противопригарного материала находится в воде во взвешенном состоянии и постепенно оседает при прекращении взбалтывания, то для замедления этого процесса в краски добавляют 3,5 % монтмориллонитовой глины, увеличивающей вязкость раствора и препятствующей расслаиванию краски. С этой же целью в краски вводят до 0,5 % технического мыла. На практике широко применяют краски на основе циркона.
После нанесения слоя краски ранее высушенные формы и стержни требуют повторной подсушки. Чтобы исключить эту операцию, краски иногда наносят на горячие формы и стержни, еще не успевшие остыть после основной сушки. Для этой же цели используют краски, содержащие вместо воды легкоиспаряющиеся жидкости (спирт и др.).
Характер использования. Если форма изготавливается из одной смеси, то такая смесь называется единой. Единые смеси применяют при машинной формовке для серийного и массового производства. При переработке каждый раз вводится значительное количество свежих материалов.
Облицовочные смеси применяются в условиях единичного производства. Их наносят вокруг модели слоем толщиной 15 - 20мм в зависимости от толщины отливки. Облицовочные смеси используют в тех случаях, когда применение единой смеси дает значительный брак.
Наполнительные смеси наносят поверх облицовочных, они заполняют остальную часть формы. Наполнительные смеси готовят из отработанных материалов.
Класс применяемого песка. В природе встречаются, но довольно редко, пески, содержащие такое количество глины, что их можно использовать после увлажнения и перемешивания в качестве формовочной смеси. Примером может служить тамбовский песок, который применяют без всяких добавок при цветном литье. Смеси, приготовленные на таких песках, называются естественными.
Смеси, в которые глина вводится как самостоятельная добавка, называются синтетическими.
Состояние формы. В смеси для сухих форм рекомендуется вводить крупный песок, обеспечивающий большую газопроницаемость. Шероховатость отливки при этом не повышается, так как форму окрашивают огнеупорной краской.
При формовке по-сырому особое значение имеет прочность, газопроницаемость, влажность смеси. В этом случае стремятся сочетать требуемую прочность и газопроницаемость с минимальным содержанием глины, чтобы уменьшить влажность. Поэтому используют жирные огнеупорные глины и бентониты, обладающие наибольшей связующей способностью во влажном состоянии.
Таблица 8
Дата добавления: 2020-11-15; просмотров: 866; Мы поможем в написании вашей работы! |
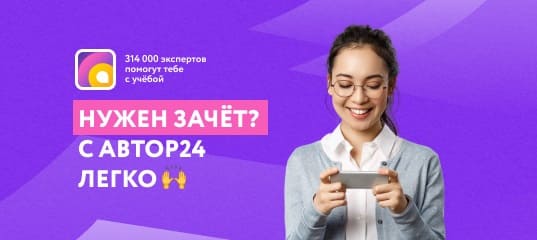
Мы поможем в написании ваших работ!