Обработка посадочного (центрального) отверстия
Структура технологического процесса при обработке цилиндрических зубчатых колес
Технология изготовления зубчатых колес зависит от следующих факторов: программы выпуска, конструкции, размеров, метода получения заготовок, материала, точности и термической обработки. Основными факторами являются точность и конструкция зубчатых колес.
Типовой технологический процесс изготовления зубчатых колес включает изготовление штамповок или поковок, токарную обработку наружных поверхностей и торцов; обработку центрального отверстия, зубонарезание, термическую обработку, отделочные и доводочные операции базовых и зубчатых поверхностей. Особенностью технологического процесса изготовления зубчатых колес – валов является наличие операций по обработке зубьев, а в остальном он тот же, что и при изготовлении ступенчатых валов.
Токарная обработка
В мелкосерийном производстве зубчатые колеса до нарезания зубьев обрабатываются на универсальных токарно-винторезных и токарно-револьверных станках. Схема технологической наладки для обработки зубчатого колеса на токарно-револьверном станке представлена на рис. 2.87.
Рис. 2.87 Технологическая наладка обработки зубчатого колеса на токарно-револьверном станке
При обработке деталь зажимают в трехкулачковом самоцентрирующем патроне. В позиции 1 револьверной головки двумя резцами обтачивают наружную поверхность заготовки. Одновременно одним резцом растачивают внутреннюю поверхность, другим резцом снимают внутреннюю фаску. После отвода револьверного суппорта, двумя резцами Б с поперечного суппорта подрезают торцы. В позиции 2 револьверной головки широкими пластинами подрезают внутреннюю торцовую поверхность. Резцом А поперечного суппорта снимают фаску на наружной поверхности. В позиции 3 револьверной головки растачивают центральное отверстие. В позиции 4 с помощью специального приспособления прорезают внутреннюю канавку. В позициях 5 и 6 револьверной головки центральное отверстие развертывают черновой и чистовой развертками.
|
|
В крупносерийном производстве зубчатые колеса обрабатывают на токарных и токарно-револьверных станках с ЧПУ моделей 16К20Ф3, 16К30Ф305, 16К20Т1, 1В340Ф3, 1Е365ПФ3 и пр. Общий вид токарного станка с ЧПУ показан на рис. 2.88.
Станок имеет следующие основные узлы: 1 – привод; 2 – передняя шпиндельная бабка; 3 и 7 - верхний и нижний суппорты; 4 и 6 – поворотные резцедержатели; 5 – задняя бабка; 8 – станина с направляющими.
|
|
|
Это дает возможность одновременно обрабатывать зубчатое колес с двух сторон.
Еще большая производительность обеспечивается применением токарных многорезцовых полуавтоматов (ТМП) моделей 1А720, 1А730 и пр. Схема наладки для обработки блока зубчатых колес на одношпиндельном ТМП представлена на рис.2.90.
В данном случае обработка цилиндрических поверхностей производится с переднего продольного суппорта, а обработка торцев, канавок и большинства фасок с заднего поперечного суппорта.
В массовом производстве применяют многошпиндельные токарные полуавтоматы моделей 1К282, 1283, 1Б284, 1А286-6 и пр. Наибольший диаметр обрабатываемой заготовки на станке модели 1А286-6 составляет 630 мм. Схема наладки для обработки зубчатого колеса показана на рис. 2.91.
Станок имеет поворотный стол, в центре которого расположена восьмигранная колонна. На гранях колонны установлены суппорта трех типов: продольного, поперечного и продольно-поперечного точения. Последний суппорт имеет салазки для продольного и поперечного перемещения резцов.
Напротив каждой грани колонны размещены вращающиеся шпиндели с патронами для закрепления заготовок. Согласно рис. 2.91 обработка на станке ведется по следующей схеме. На позиции I производится установка заготовки. В этой же позиции со станка снимается готовая деталь. На позициях II – IV заготовка обрабатывается с одной стороны. На позиции V заготовка переустанавливается и обрабатывается с другой стороны. Для точной обработки отверстия на позиции VI применяют плавающую развертку. На позициях VII и VIII для сверления и зенкерования восьми отверстий используют специальные многошпиндельные головки.
|
|
Токарную обработку крупных цилиндрических колес диаметром свыше 500 мм для тяжелом машиностроения выполняют на токарно-карусельных станках (ТКС). Колеса 8 степени точности и менее точные обрабатываются на ТКС окончательно. Колеса 7 степени точности и более точные обрабатываются на ТКС с припуском для окончательной обработки после сборки с валом. Диаметр заготовок, обрабатываемых на ТКС, достигает 20 м. По своей компоновке ТКС делятся на одностоечные (моделей 1508, 1510, 1512 и пр.) и двухстоечные (моделей 1520, 1525, 1540 и пр.). Широко применяются ТКС с ЧПУ моделей 1512Ф3, 1516Ф3, 1525Ф3 и пр. При чистовой обработке на ТКС достигается точность по 7-8 квалитетам и шероховатостью поверхности 3,2-6,3 мкм.
|
|
Обработка посадочного (центрального) отверстия
Это отверстие является технологической базой при обработке зубчатого колеса. Для передачи крутящего момента посадочное отверстие имеет шпоночный паз или шлицевую поверхность. Точность отверстия и перпендикулярность его оси торцу ступицы у незакаленных колес обеспечивается чистовым точением, развертыванием, шлифованием или протягиванием.
Отверстие протягивают после сверления или зенкерования круглыми протяжками. Точность отверстия после протягивания соответствует 7 – 9 квалитету. Шероховатость составляет Ra0,32 – 2,5 мкм. Производительность при протягивании значительно выше, чем при шлифовании.
Схема протягивания гладкого отверстия зубчатого колеса на шаровой опоре представлена на рис. 2.94. Применение шаровой опоры обеспечивает перпендикулярность оси отверстия торцу ступицы колеса.
У колес, подвергаемых закалке, отверстие шлифуют на внутришлифовальном станке, а торец ступицы - на плоскошлифовальном станке. Для повышения точности шлифование отверстия и торца рекомендуется выполнять с одного установа.
При этом колесо закрепляют в специальном патроне (рис. 2.96). Базирование колеса осуществляют роликами по боковой поверхности зубьев, что обеспечивает соосность центрального отверстия и делительной окружности. Шлифование отверстия производят кругом 1, а шлифование торца – кругом 2, установленным на шпинделе дополнительной шлифовальной бабки.
Шпоночные канавки и шлицы в отверстиях зубчатых колес прорезают до закалки. В единичном и мелкосерийном производстве шпоночные канавки обрабатывают на долбежных станках.
В крупносерийном и массовом производстве шпоночные канавки получают протягиванием. На рис. 2.97 показано протягивание шпоночной канавки в заготовке зубчатого колеса на горизонтально-протяжном станке. Заготовка 1 насаживается на направляющий палец 4, внутри которого имеется паз, для направления протяжки 2. Когда канавка протягивается за 2 рабочих хода одной и той же протяжкой, то под протяжку помещают подкладку 3.
Шлицевые отверстия в зубчатых колесах обрабатывают протягиванием. Если зубчатое колесо после протягивания подвергается закалке, то центрирование шлицевого соединения осуществляется преимущественно по внутреннему диаметру вала. В этом случае после закалки отверстие шлифуют на круглошлифовальном станке, а у вала шлифуют впадины шлицев. Если все же при закалке зубчатого колеса требуется осуществить центрирование шлицевого соединения по наружному диаметру вала, то шлицы в отверстии подвергают хонингованию по впадинам. С этой целью создан специальный станок модели 3А856Ф1. Ширина бруска хона меньше ширины впадины шлицов. Это позволяет хону совершать качательные движения в окружном направлении при перемещении вдоль оси отверстия. Вал при этом шлифуют по наружному диаметру.
Дата добавления: 2020-04-25; просмотров: 129; Мы поможем в написании вашей работы! |
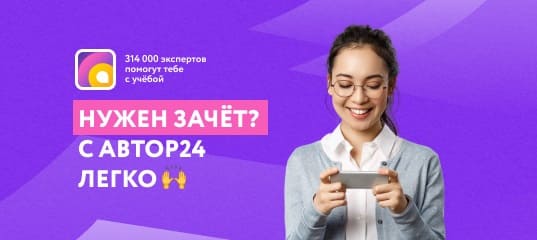
Мы поможем в написании ваших работ!