Способы изменения физико-химических свойств материалов
Каждый материал при нормальных условиях обладает вполне определенными свойствами. Но имеется ряд приемов, которые позволяют существенно изменить зафиксированные свойства материалов. Эти приемы позволяют повысить пластичность, твердость, снизить хрупкость материала, улучшить его магнитные свойства и т.д. К этим способам и приемам относятся: термические, химико-термические, механические и термомеханические.
1. Термические способы. Эти способы приводят к изменению структуры и физико-химических свойств материалов. К этим способам относятся:
1.1. Отжиг 1 рода без фазовых превращений. Основное назначение – уменьшение концентрации дефектов решетки и внутренних напряжений. Имеются следующие разновидности отжига 1 рода:
- гомогенизирующий (диффузный) отжиг позволяет устранять дендритную (древовидную) ликвацию (расслоение) в отливках и слитках сплавов металлов высоколегированных сталей.
С повышением температуры увеличивается скорость диффузии, что способствует повышению однородности материала; отжиг проводится при температуре (0,8÷0,9) от температуры плавления в течение от 8 до 100 часов;
- рекристаллизационный отжиг проводится при температуре рекристаллизации. В результате образуются новые зерна с меньшей концентрацией дефектов строения, снижаются внутренние напряжения, понижаются прочностные свойства материала, повышается пластичность.
|
|
- отжиг для снятия напряжений. Температура этого вида отжига должна быть ниже температуры рекристаллизации, так как процесс предполагает частично сохранить упрочнение материала, которое могли специально проводить с материалом. Процесс предназначен для снятия остаточных напряжений, внесенных в металл предварительной обработкой.
1.2. Отжиг II рода с фазовыми превращениями.
Этот вид отжига уменьшает концентрацию дефектов решетки, снимает внутренние напряжения, измельчает зерно, упрочняет структуру. В результате повышается пластичность, понижается прочность и твердость материала. По степени и полноте фазовых превращений различают полный (полностью осуществляется превращение при нагреве) и неполный (частичное превращение) отжиги.
Разновидностью полного отжига является нормализация, которая предполагает проведение после температурной обработки ускоренное охлаждение на воздухе. Нормализация применяется для придания материалу однородной более мелкозернистой структуры, при этом повышается пластичность и ударная вязкость при достаточно высокой прочности и твердости.
Все виды отжига проводятся при малых скоростях нагрева и охлаждения, кроме нормализации, по которой охлаждение проводят при более высоких скоростях снижения температуры.
|
|
1.3. Закалка. Этот вид термической обработки выполняется медленным нагревом и быстрым охлаждением, благодаря чему фиксируется структура, которая достигается при нагреве, замедляется диффузия, фиксируется пересыщенными легирующими элементами и вакансиями в твердый раствор. Закалка различных сплавов может привести к неодинаковым результатам: упрочнению, разупрочнению ли сохранению свойств. В результате в материалах закалка может приводить к повышенной прочности при сохранении высокой пластичности. Так при закалке железа и большинства его сплавов образцы становятся очень твердыми и хрупкими и находятся в очень напряженном состоянии, настолько, что приходиться применять дополнительные термообработки для снятия напряжений: отжиг I и II рода, отпуск высокий, средний или низкий и т.п. в зависимости от того, какие свойства материала нам необходимо получить. А при закалке алюминия – образцы становятся мягкими и, чтобы придать материалу твердость, необходимо искусственно состарить материал. Различают закалку с полиморфным превращением и закалку без полиморфных превращений, то есть с изменением и без изменения кристаллической структуры материала, соответственно. Температура закалки на 30-50 0С выше Солидуса. Для придания материалу дополнительных свойств закалку часто осуществляют в определенной среде: восстановительной, окислительной и т.д. В качестве охлаждающей среды используют воду, растворы солей, например 1% NaCl; 10% NaCl; 5-30% NaOH; 50% NaOH. Так как в большинстве случаев закалка приводит к тому, что структура материала находится в напряженном состоянии, то, как правило, после закалки необходимо провести дополнительную термообработку, которая поможет снять напряжения и придаст материалу необходимые свойства.
|
|
1.4. Отпуск и старение. Образующиеся при закалке пересыщенные твердые растворы нестабильны, хрупки и не стойкие к окислению. При нагревании закаленных образцов структуры, образованные при закалке распадаются и происходит перекристаллизация в другие, ненапряженные структуры. Если закалка была с полиморфным превращением, то процесс, в результате которого происходит распад пересыщенного твердого раствора, называется отпуском.
Если закалка была произведена без полиморфных превращений, то процесс называется старением.
Полнота изменения структуры свойств закаленных сплавов при отпуске и старении в основном зависят от температуры нагрева и длительности изотермической выдержки.
|
|
Обычно при отпуске охлаждение осуществляется медленно, это способствует предотвращению коробления материала.
Отпуск предназначен для частичного или полного уменьшения метастабильности закаленного материала. Температура нагрева не должна превосходить температуру фазового перехода. Отпуск в зависимости от температуры нагрева уменьшает внутренние напряжения и хрупкость, снижает твердость и прочность, повышает вязкость и пластичность при оптимальном сочетании.
Старение может происходить при естественных условиях. В этом случае закаленные материалы – сплавы – подвергаются выдерживанию и вылеживанию. При этом увеличивается твердость и прочность материала, одновременно снижается пластичность и вязкость.
Для ускорения процесса старения применяют термическую активацию процесса – искусственное старение – для этого сплав нагревают до температуры 20-40 % от температуры закалки и подвергают длительной изотермической выдержке – до нескольких десятков часов. Такой режим способствует интенсификации процесса распада решетки пересыщенного твердого раствора.
2. Химико-термическая обработка – это своеобразное совмещение металлургических процессов и тепловой обработки, а именно: насыщение поверхности металлов и сплавов элементами, повышающими: твердость, износостойкость, коррозионную устойчивость. Процесс основан на диффузии в материал в твердом состоянии вещества, изменяющего его свойство. Для активизации диффузии процесс проводят при повышенной температуре и длительной выдержке. Чаще химико-термической обработке подвергаются черные металлы, то есть железосодержащие, реже – цветные. Разновидности химико-термической обработки.
2.1. Цементация; обычно цементации подвергают стали с низким содержанием углерода 0,1-0,3% - процесс насыщения поверхности стали углеродом. Цементация повышает поверхностную твердость при наличии вязкой сердцевины. Обычно науглероживают поверхность на глубину 0,5-1,5 мм. Осуществляют либо с помощью твердых науглероженных веществ – карбюризаторов – это уголь с различными добавками, в качестве которых используют чаще углеродистые соли: бария BaCO3, натрия Na2CO3, калия К2СО3; или в газовой среде, содержащей природные газы: пропан, метан, этил или их смеси. Температура цементации в первом или втором случае 900-9500С. В первом и втором случае процесс сопровождается вначале образованием атомарного углерода высокоактивного, а затем его проникновение в тело материала в результате диффузии, далее атомарный высокоактивный углерод реагирует с материалом, например γ-железо с образованием Fe3C. Добавляемые углекислые соли в первой схеме активизируют процесс и являются дополнительным источником атомарного углерода.
Для получения науглероженного слоя в 1 мм требуется 10 часов с применением 1 метода.
2.2. Азотирование при газовой химико-термической обработке – насыщение поверхностного слоя, например сталей, азотом. Азотируемый слой обладает высокой твердостью, износоустойчивостью и коррозионной стойкостью. Исходным материалом для азотирования является аммиак, который при температуре 500-6000С разлагается с образованием атомарного азота, который далее диффундирует в металлический материал и образует, например с железом и легирующими присадками нитриды: FeN, MoN, AlN, MpN и др. Азотирование - процесс продолжительный: 0,5 мм достигается за 40-45 часов.
2.3. Цианирование – процесс одновременного насыщения материала углеродом и азотом, в результате поверхность становится повышенной твердости, износостойкости и коррозионной стойкости. В зависимости от среды, в которой проводится цианирование, различают: твердое, жидкое и газовое цианирование. В зависимости от температурных режимов различают низкотемпературное (при 500-6000С) и высокотемпературное (800-9500С) цианирование.
При твердом цианировании используют желтую кровяную соль K4Fe(CN)6 в смеси с другими солями и молотым древесным углем при температуре 5500С: 40% NaCN; 40% Na Cl$ 20% Na2CO3.
При газовом цианировании процесс происходит в смеси науглероживающих и азотирующих газов: пропан, метан или этил с аммиаком при температуре 800-8500С. Газовое цианирование менее продолжительно.
2.4. Диффузная металлизация – насыщение поверхности материала, например стали, каким-либо металлом.
2.4.1. Диффузное хромирование повышает сопротивление газовой коррозии до температуры 8000С, коррозионную стойкость в азотной кислоте, морской среде и пресной воде. Проводится при температуре 950-11000С, 5-20 часов в жидкой среде на глубину 0,1-0,3 мм, приводит, в отличие от гальванического покрытия, к образованию карбидов хрома, которые к тому же обеспечивают высокую твердость и износоустойчивость углеродистых сталей.
2.4.2. Диффузное алитирование – это насыщение поверхности алюминием, проводится в твердой (при температуре 950-10000С) или жидкой (при температуре 750-8000С) средах. В первом случае используют порошковый алюминий, который реагирует и хлором, выделяющимся при разложении NH4Cl с последующим образованием хлорида алюминия AlCl3, который разлагается с образованием атомарного алюминия. Во втором случае используют расплав алюминия.
Алитирование позволяет получать на поверхности материала пленку Al2O3, предохраняющую материал от коррозии в атмосферной и даже морской средах, она предотвращает окисление материала. Твердость слоя средняя (до 500 HV), износостойкость низкая.
2.4.3. Диффузное силицирование – это насыщение поверхности стали кремнием, путем обработки материала в газовой среде, содержащей кремний. Твердость получается низкой (повышенная пористость слоя), но слои обладают высокой износоустойчивостью, жаростойкостью и коррозионной стойкостью. Силицированию подвергают: арматуру, болты, гайки, изделия, которые работают в условиях повышенной окисляемости при повышенных температурах.
2.4.4. Диффузное борирование - насыщение поверхности материала бором. При этом повышается износостойкость, даже абразивная износостойкость, коррозионная стойкость. Процесс борирования осуществляется либо в расплавленных солях, содержащих бор, электролизом при температуре 930-9500С в течение 2-6 часов, или газовым борированием при температуре 850-9000 (разложением треххлористого бора в смеси с водородом). В основном применяют для повышения износостойкости штампов, пресс-форм, литиевых форм. При борировании стойкость повышается в 2-10 раз.
3. Механические способы изменения физико-химических свойств материалов. К ним относится нагартовка (или наклеп), которая представляет собой изменения структуры и свойства металлов и сплавов в результате пластической деформации. При нагартовке уменьшается пластичность и ударная вязкость, но повышается твердость и прочность. Этот процесс используется для упрочнения поверхности. Достигается наклеп приложением к материалу усилий выше предела пропорциональности. При сильных деформациях металлических материалов происходит упорядоченная одинаковая ориентация кристаллов, что для некоторых материалов, например магнитных, является обязательным. Материалы, имеющие такую упорядоченную структуру, называются текстурованными.
4. Термомеханическая обработка. В этом методе обработки сочетают пластичную деформацию и термическую обработку. Для реализации метода деформацию материала осуществляют при повышенной температуре, а затем быстро охлаждают. При этом в материале фиксируется повышенная концентрация дефектов, которые достигаются при деформации. Они суммируются с дефектами, которые возникают при воздействии температуры. Такое совместное воздействие с последующим фиксированием состояния материала позволяет увеличить вязкость разрушения, увеличить прочность при сохранении, а иногда и при улучшении пластичности. Различают термомеханическую обработку высокотемпературную и низкотемпературную, которые проводятся соответственно выше и ниже температуры рекристаллизации.
Металлические материалы
К этой группе материалов относят: металлы, металлические сплавы и композиты.
Металлы состоят из одного основного элемента и незначительного количества примесей других элементов. По степени чистоты различают металлы технической, высокой и особой чистоты.
Металлические сплавы представляют собой вещества, обладающие металлическими свойствами и получаемые при плавлении или спекании двух и более элементов.
Композиты в свой состав, кроме металлов, могут включать неметаллические компоненты, такие как: графит, окись алюминия Al2O3, двуокись кремния SiO2 и т.д.
Сплавы и композиты обладают самыми разнообразными сочетаниями полезных свойств, которые получают за счет композиционного состава.
Технологической переработке в РЭС подвергают металлические материалы:
- в виде листа – для изготовления: шасси, панелей, кожухов, корпусов, отражателей зеркальных антенн, больших телеэкранов и т.д.;
- прутка для изготовления: деталей стаканчатой формы, винтов, гаек, заклепок, осей и т.д.;
- профильного проката для изготовления: этажерок, рам, направляющих, каркасов, ферм, консолей и т.д.;
- проката трубчатой формы, он применяется для изготовления волноводных каналов;
- проволоки для изготовления: проводов, заклепок, винтов, болтов и т.д.;
- порошков для изготовления деталей небольших размеров: вкладышей, экранов, шайб, деталей коробчатой формы, магнитов и т.д.;
- в виде чушки – для изготовления деталей различной формы литьем: радиаторов, волноводных каналов, деталей коробчатой формы.
По химическому составу металлические материалы делят на черные и цветные.
Дата добавления: 2020-04-25; просмотров: 1812; Мы поможем в написании вашей работы! |
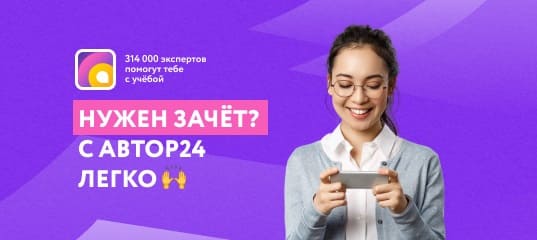
Мы поможем в написании ваших работ!