Проектирование технологичных заготовок
При проектировании порошковых деталей следует максимально уменьшать количество изменений толщины или диаметра заготовки вдоль оси, особенно тогда, когда это не вызывается конструктивной необходимостью (рис.20.2, 1). Толщина стенки изделия диаметром 10..15 мм и высотой 15…20 мм должна быть не менее 1,2…1,5 мм. У более крупных заготовок минимальная толщина стенки возрастает примерно по 0,8 мм на каждые 25 мм длины. Толщина данной части глухих отверстий должна быть не менее 2…3 мм. Отверстия располагаются на расстоянии не менее 2…3 мм от края заготовки и друг от друга.
В конструкциях изделий следует избегать:
- резких изменений толщины стенок (рис.20.2, 2);
- узких и длинных выступов (рис.20.2, 3) и выемок (рис.20.2, 4); обратной конусности (рис.20.2, 5);
- острых углов (рис.20.2, 6) и других форм, приводящих к ослаблению пресс форм;
- радиальных канавок (рис.20.2, 8), выемок и отверстий, расположенных перпендикулярно к оси прессования
Заготовки, получаемые холодным прессованием с последующим спеканием, должны, как правило, отвечать следующим требованиям:
- поперечное сечение - 50…6000 мм2;
- высота - 2…60 мм;
- масса не более 5…10 кг;
- отношение длины к диаметру не более 2,5…3;
- острые углы и грани должны быть закруглены радиусом не менее 0,13 мм;
- точность размеров некалиброванных деталей - 8 - 14 квалитет, калиброванных - 6 - 7 квалитет;
|
|
- шероховатость поверхности некалиброванных деталей Ra 2,5…0,63 мкм, калиброванных - Ra 0,32…0,08 мкм.
Точность изготовления порошковых заготовок зависит от точности пресса, пресс-форм, стабильности упругих последействий при холодном прессовании, объемных изменений при спекании и т.д.
Методы порошковой металлургии позволяют экономить трудовые и
материальные ресурсы при изготовлении и эксплуатации машин. Экономическая эффективность изготовления порошковых заготовок тем выше, чем больше их серийность. Поэтому такая технология целесообразна только при годовой программе выпуска в несколько тысяч штук.
Коэффициент использования металла при изготовлении порошковых деталей может достигать 90…98%. Изделия из композиционных материалов, получаемые МПМ, обладают высокими эксплуатационными характеристиками. Например, антифрикционные спеченные заготовки широко используют для изготовления деталей узлов трения (подшипников скольжения, колец, торцовых уплотнений, шайб и др.) различных механизмов и машин. Введение в состав антифрикционных порошков веществ, играющих роль твердой смазки и повышающих прочностные свойства изделия, а также наличие в материале подшипника пор, пропитанных смазочными жидкостями, увеличивает срок службы деталей в 1,5 и более раз.
|
|
Преимущества и недостатки
Преимуществами производства заготовок МПМ является возможность получения:
ñ изделий из разнородных порошков (медь-вольфрам, железо-графит и др.);
ñ пористых изделий (фильтроэлементов, самосмазывающихся подшипников и др.);
ñ изделий, требующих минимального объема механической обработки резанием для получения деталей с заданной точностью и качеством поверхностного слоя.
К недостаткам получения заготовок относятся:
ñ ограниченность размеров получаемых деталей;
ñ остаточную пористость изделий, условия работы которых
связаны с воздействием динамических напряжений большой интенсивности;
ñ высокую стоимость порошков (примерно в 3 раза дороже традиционных сталей того же химического состава).
Типовые детали
Типовыми деталями, изготовляемыми из порошковых заготовок, являются шестерни, кулачки, звездочки, шайбы, заглушки, гайки, втулки, фланцы и пр.
Свойства и области применения порошковых материалов
|
|
Антифрикционные пористые материалы изготавливают на основе порошков железа или меди с пропиткой жидкой смазкой (маслом) или с добавками твёрдой смазки (графит, свинец, дисульфид молибдена, сернистый цинк). Данные материалы обладают высокими триботехническими свойствами, хорошей прирабатываемостью, высокой теплопроводностью, достаточной вязкостью при ударной нагрузке, обеспечивают низкий коэффициент трения.
К фрикционным относят материалы с высоким коэффициентом трения. Они обладают высокой фрикционной теплостойкостью и коррозионной стойкостью. Их изготавливают на основе меди или железа с металлическими и неметаллическими компонентами для деталей, работающих в масле (75%) и при сухом трении. Фрикционные изделия состоят из стальной основы и фрикционных накладок, которые припекаются к основе под давлением.
Электротехнические материалы подразделяются на электроконтактные (металлические, металлографитовые, металлооксидные и металлокарбидные), магнитомягкие (железоникелевые сплавы, сплавы железа с кремнием и алюминием или хромом и алюминием), магнитотвёрдые (сплавы на основе Fe–Al–Ni(Co), называемые альни, альнико, магнико), магнитодиэлектрики (карбонильное железо, пермаллой, альсифер), ферриты (Fe3О4 с добавками NiO, MgO, MnO, ZnO).
|
|
Аморфные материалы, получаемые быстрым (со скоростью 105 …106 0С/с) охлаждением расплава (Fe40N40P10B8O), являются новым классом магнитных материалов, из которых изготавливают магнитные экраны, трансформаторы и электродные приборы.
Спечённые конструкционные материалы изготавливаются на основе конструкционной стали (углеродистой, меднистой, кремнистой, молибденовой, хромомолибденовой), титановых и алюминиевых сплавов.
Повышение твёрдости обрабатываемых заготовок потребовало расширения диапазона используемых режущих материалов от твёрдых сплавов, минералокерамических материалов до искусственных алмазов и других сверхтвёрдых материалов, получаемых методами порошковой металлургии.
Твёрдые сплавы используют в режущих и контрольно-измерительных инструментах, рабочих вставках фильер при волочении, матрицах и пуансонах при штамповке и прессовании. В машиностроении и приборостроении широко применяют армированные твёрдыми сплавами детали. Например, в текстильной промышленности применяют твёрдые сплавы для направляющих колец и других трущихся деталей; в порошковой металлургии твёрдые сплавы используют для размольных тел и прессового инструмента.
Минералокерамику применяют для получистовой и чистовой обработки резанием чугунов, закалённых и улучшенных сталей, цветных и тугоплавких сплавов при высоких (до 800 м/мин) скоростях резания. Основу минералокерамики составляет - модификация Al2O3 (электрокорунд) зернистостью до 1 мкм. Плотность кермета (керамики с металлической связкой) составляет 3,96 г/см3 , твёрдость – HRA до 92 единиц. Оксидокарбидная керамика имеет Плотность 4,2 … 4,6 г/см3 и твёрдость – HRA 92 … 94 единицы.
Эрозионно-стойкие и потеющие материалы обладают комплексом свойств, которые невозможно получить в сплавах. Они изготавливаются на основе тугоплавких металлов или углерода в виде композиций.
Например, путём пропитки вольфрамового или углеродного каркасов жидкой медью или серебром. Детали из такого материала работают в двигателях при температуре свыше 2500 0С. Во время работы медь (серебро) испаряется, что понижает тепловой поток и улучшает условия работы вольфрамового или углеродного каркасов.
Дата добавления: 2020-04-25; просмотров: 93; Мы поможем в написании вашей работы! |
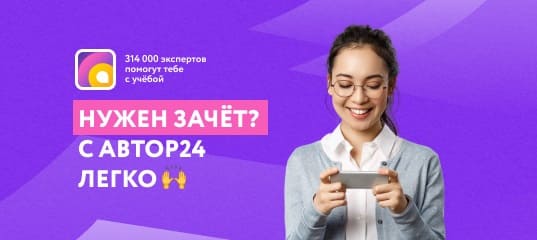
Мы поможем в написании ваших работ!