Контроль параметров бронепанелей
ВВЕДЕНИЕ
Настоящие технические условия распространяются на бронепанели (БП) композитные, предназначенные для оснащения штурмовых бронежилетов (БЖ) для военнослужащих СВ, ВДВ, МП ВМФ и частей специального назначения.
Изделия представляют собой монолитные композитные пластины эргономичной формы на основе арамидной ткани, корундовой керамики и полимерного связующего, обеспечивающего герметичную защиту баллистических материалов от механических повреждений и воздействий негативных факторов. Техническое решение конструкции бронепанели защищено патентом РФ №2190823 от 05.07.01 на «Пулезащитную бронепанель».
Условия эксплуатации бронепанелей соответствуют условиям эксплуатации бронежилетов.
Бронепанели могут эксплуатироваться во всех климатических зонах.
Пример записи и обозначения бронепанелей при заказе и в документации другой продукции – «Бронепанель композитная, грудная/спинная 1-го размера» ТБМП.305249.131.
ТЕХНИЧЕСКИЕ ТРЕБОВАНИЯ
Общие требования
1.1.1. Бронепанели должны соответствовать требованиям настоящих технических условий, комплекту конструкторской документации и контрольным образцам, утвержденным в установленном порядке.
Основные характеристики
1.2.1. Бронепанели в составе БЖ должны обеспечивать пулестойкость1) при обстреле соответствующим оружием с дальностей, указанных в таблице 1, а также обладать живучестью 2 попадания на дм. кв. при пяти выстрелах в грудные (спинные) БП, трех выстрелах в БП боковые (фартука), одного выстрела в спинную нижнюю БП, расстояниях между воздействиями не менее 70 мм и от края БП не менее 15 мм.
|
|
1.2.2. Бронепанели в составе БЖ (защитная композиция из 20 слоев арамидной ткани
арт. 84127 и климатико-амортизационный подпор (КАП) должны обеспечивать снижение запреградного (контузионного) воздействия до 2 степени согласно
ОТТ 7.2.24-902.
1.2.3. Масса бронепанелей и их габаритные размеры должны соответствовать требованиям таблицы 2 и соответствующим чертежам.
1.2.4. Бронепанели должны сохранять свои защитные свойства во всех климатических зонах при температуре от минус 50 до плюс 50°С и относительной влажности воздуха до 100%. Влагопоглощение при погружении в воду не более 2%.
1.2.5. Не допускается разрушение БП без воздействия поражающими элементами в течение гарантийного срока эксплуатации.
1.2.6. Допускается камуфлирующая, либо однотонная темная окраска поверхности БП.
Примечание 1. – при условии не попадания двух поражающих элементов в одну плитку.
2.- при воздействии согласно требованиям ТБМП.305219.007ПМ.
Таблица 1
Параметры воздействия
| ||||||
Оружие, тип боеприпасов | Тип пули | Масса пули, г. | Начальная скорость, V5, м/с | Дальность обеспечения защиты, м | ||
СВД: (7,62 мм, 7-Б3-3); (7,62 мм, 7Н26) | Б-32 БП | 10,4 9,75 | 810 – 830 820 – 835 | 10 10 | ||
М60, МG3, М240 (7,62 мм, М61) | Патрон NATO | 9,72 | 850 | 10 | ||
М16А2 (7,62 мм, М855) | Со стальным сердечником | 4,0 | 930 – 950 | 10 | ||
АW, Sako TRG (8,58 мм) | Снайперский патрон, .338 Lapua Magnum | 16,2 | 900 – 915 | 300 |
Таблица 2
Назначение | Размер | Высота, мм | Ширина, мм | Площадь, дм2 (не менее) | Масса, кг не более |
Грудная/ спинная | 1 2 3 | 285±3 314±3 340±3 | 263±3 263±3 263±3 | 7,0 7,5 8,2 | 3,0 3,25 3,5 |
Спинная нижняя | 1-3 | 145±2 | 190±2 | 2,5 | 1,0 |
Боковая/ фартука | 1-2 3 | 206±3 213±3 | 164±2 186±2 | 3,0 3,5 | 1,35 1,6 |
1.2.7. Бронепанели не должны иметь видимых трещин, сколов и т.д. Допускаются складки по тыльной и боковой поверхностям БП, не превышающие величин допуска. Поверхности БП не должны иметь открытой пористости и повреждение полимерного слоя.
1.2.8. БП и ее маркировка должны быть устойчивы к дегазации водными растворами и воздействию агрессивных сред (1 час при полном погружении в бензин, керосин, дизельное топливо, ружейную смазку, раствор для чистки ствола – без снижения защитных свойств).
|
|
1.2.9. БП должны сохранять свои защитные свойства (пулестойкость) после падения на твердое основание (бетон) любыми частями бронепанели (ребро, угол, плоскость) с высоты 1.5 м.
Требования по надежности
БП в составе бронежилета должны обеспечивать вероятность непробития (Р) БЖ не менее 0,98 при доверительной вероятности 0,8.
Требования к материалам для изготовления БП
1.4.1. Материалы, используемые для изготовления БП, допускаются в производство только при наличии паспортов заводов-изготовителей и положительных результатов входного контроля согласно ТБМП.305219.007 ДК.
1.4.2. Материалы не соответствующие требованиям НТД и не прошедшие входной контроль с положительным результатом должны быть изолированы от пригодных к использованию материалов.
ТЕХНОЛОГИЧЕСКИЕ ТРЕБОВАНИЯ
2.1. Бронепанели должны изготавливаться по технологической документации, утвержденной в установленном порядке и согласованной представителем заказчика (ПЗ).
2.2. Допускается изготовление части силового слоя композитного основания БП из двух кусков с укладкой встык. Такие слои должны чередоваться с цельными листами и их линии стыка не должны находиться на одной проекции. Количество таких листов в бронепанели должно быть не более пяти.
|
|
КОМПЛЕКТНОСТЬ
3.1. В состав комплекта поставки входят: бронепанель(ли) композитная (ые) и паспорт на БП (партию). Форма паспорта приведена в Приложении А (форма 1).
МАРКИРОВКА
4.1. Каждая бронепанель маркируется с указанием наименования изделия, назначения, размера, номера настоящих технических условий, года выпуска и номера БП, ее местоположения, ориентации в БЖ, наименования или шифра предприятия-изготовителя.
4.2. Способ нанесения маркировки любой, обеспечивающий ее прочтение и сохранность в течение гарантийного срока эксплуатации.
4.3. Места нанесения маркировки – согласно черт. №№ ТБМП.305249.131СБ, ТБМП.305249.132СБ, ТБМП.305249.133СБ, ТБМП.305249.134СБ, ТБМП.305249.135СБ, ТБМП.305249.138СБ, ТБМП.305249.139СБ. Допускается сведение всех надписей на одну этикетку, размещаемую на тыльной стороне БП.
4.4. Отметки ОТК и ПЗ о приемке проставляются в паспорте и на упаковочном листе.
УПАКОВКА
5.1. Бронепанели укладываются в деревянные ящики по ГОСТ 5959-80. Чертежи ящиков и схемы укладки БП в ящики должны быть согласованы с ПЗ.
5.2. Количество бронепанелей в одной упаковке не регламентируется и зависит от объема поставки и вида транспортной тары, при массе каждого ящика не более 25 кг.
5.3. Бронепанели в ящиках должны быть отделены друг от друга вкладышами-прокладками из гофрированного картона по ГОСТ 7376-89 или другого материала-амортизатора.
5.4. В каждый ящик должен быть вложен упаковочный лист, образец которого приведен в Приложении А (форма 2). Ящик должен быть снабжен ярлыком, содержащим:
– наименование или шифр предприятия-изготовителя;
– наименование продукции;
– обозначение настоящих технических условий;
– номер партии;
– номер ящика / количество ящиков в партии;
– наименование и размер БП;
– количество бронепанелей в ящике, шт.;
– дату упаковки;
– отметки ОТК и ПЗ.
5.5. Если в одной упаковке содержатся БП различных типов, то в ярлыке указывается их общее количество и количество БП каждого типа.
5.6. Транспортную маркировку осуществляют в соответствии с требованиями
ГОСТ 14192-96 с нанесением манипуляционных знаков «Верх», «Не кантовать», «Хрупкое-осторожно» и «Штабелирование ограничено».
5.7. Ящики должны быть опломбированы представителем заказчика и (или) ОТК.
ПРАВИЛА ПРИЕМКИ
Общие положения
6.1.1. Бронепанели принимают поштучно или партиями. К одной партии относят БП, изготовленные за ограниченный период времени по одной технологии и оформленные единым документом о качестве. Количество грудных/спинных БП в одной партии должно быть не более 1200* шт. (плюс необходимое количество бронепанелей, отбираемых для проведения приемосдаточных и периодических испытаний согласно п. 6.3.4 и п 6.4.5). Допускается формирование сборных партий, например, из бронепанелей, доработанных после забракования.
6.1.2. Для контроля качества и приемки БП (партии) проводят следующие категории испытаний:
– квалификационные (по ГОСТ В 15.301);
– приемосдаточные (ПСИ);
– периодические (ПИ);
– типовые (ТИ).
Приемосдаточным и периодическим испытаниям должны предшествовать предъявительские испытания (ПрИ).
6.1.3. Основным документом при проведении испытаний и приемке БП (партии) являются настоящие технические условия (ТУ).
6.1.4. Основанием для принятия решения о приемке БП (партии) являются положительные результаты приемосдаточных испытаний, а также предшествующих периодических испытаний, проведенных в полном объеме и в сроки, согласно настоящим техническим условиям.
Предъявительские испытания
6.2.1. Предъявительские испытания производит отдел технического контроля предприятия-изготовителя на соответствие БП (партии) требованиям настоящих технических условий, и определения готовности БП для предъявления на ПСИ представителю заказчика.
6.2.2. На испытания в ОТК (техническому контролеру) БП (партию) предъявляет цех-изготовитель, прилагая извещение по ГОСТ РВ 15.307-2002 (Приложение А,
форма 3). Извещение подписывает начальник цеха.
6.2.3. Испытания БП ОТК (технический контролер) предприятия-изготовителя производит в объеме и последовательности, установленными в таблице 4.
6.2.4. Результаты предъявительских испытаний и заключение по ним оформляют протоколом (форма 4), который подписывает начальник ОТК (технический контролер).
6.2.5. На основании положительных результатов предъявительских испытаний, ОТК предприятия-изготовителя дает заключение (на оборотной стороне извещения) о возможности предъявления БП (партии) на испытания представителю заказчика.
6.2.6. БП, не выдержавшие предъявительские испытания, возвращают в цех-изготовитель для устранения дефектов, проведения мероприятий по установлению причин, вызвавших эти дефекты, и их устранения и предъявления для повторных испытаний. При невозможности устранения дефектов БП окончательно бракуются. Повторное предъявление БП (партии) в ОТК цех осуществляет извещением с надписью «вторично», подписанным начальником производства.
6.2.7. На принятые БП (партию) отдел технического контроля (технический контролер) оформляет паспорт с перечнем номеров всех БП, входящих в партию.
* При включении в состав партии БП «боковых/фартука» и (или) «спинных нижних» общее число БП в партии рассчитывается из соотношений: 5 БП «боковых/фартука» вместо 2-х БП «грудных/спинных» или 3 «спинных нижних» БП вместо одной «грудной/спинной» и может превышать 1200 шт.
Приемосдаточные испытания
6.3.1. Приемосдаточные испытания (ПСИ) проводят с целью контроля БП (партии БП) на соответствие требованиям настоящих технических условий, контрольным образцам и определения возможности приемки.
6.3.2. Испытания и приемку проводит представитель заказчика силами и средствами предприятия-изготовителя, в присутствии представителя ОТК, в объеме и последовательности, которые предусмотрены настоящими техническими условиями (таблица 4). Допускается по согласованию с представителем заказчика изменение последовательности испытаний.
6.3.3. Предъявление БП (партии) производит ОТК предприятия-изготовителя извещением по форме 5 (Приложение А), подписанным руководителем предприятия-изготовителя или лицом, им уполномоченным приказом по предприятию и начальником ОТК (техническим контролером). По согласованию с представителем заказчика допускается предъявлять БП (партию) по журналу.
6.3.4. БП для проведения испытаний в количестве, установленном в таблице 4, отбирает представитель заказчика в присутствии представителя ОТК предприятия-изготовителя.
Таблица 4
Проверяемые параметры | Номер пункта, раздела технических требований | Метод контроля (описательная часть) | Объем испытаний от партии, % | |
ПрИ | ПСИ | |||
1. Качество материалов | 1.4 | Визуальный осмотр | 100 | 10 |
2. Внешний вид | 1.1.1, 1.2.6, 1.2.7 | Визуальный осмотр | 100 | 10 |
3. Масса | 1.2.3 | Взвешивание | 100 | 5 |
4. Маркировка | 4 | Визуально | 100 | 10 |
5. Комплектность* | 3 | Визуально | 100* | 100* |
6. Упаковка* | 5 | Визуально | 100* | 100* |
7.Пулестойкость, живучесть | 1.2.1 | Согласно ТБМП.305219.007ПМ | — | 1 грудная/спинная или 2 боковых БП от партии. |
*) – при самостоятельной поставке бронепанелей.
6.3.5. Результаты испытаний оформляют протоколом ПСИ (форма 6) и считают положительными, если все БП, отобранные согласно п. 6.3.4, соответствуют требованиям настоящих технических условий. По согласованию с представителем заказчика результаты ПрИ и ПСИ могут быть оформлены единым протоколом испытаний.
6.3.6. Результаты испытаний считают отрицательными, а БП (партию) не выдержавшими испытания, если по результатам испытаний будет обнаружено несоответствие БП (партии) хотя бы одному требованию настоящих ТУ.
6.3.7. При получении неудовлетворительных результатов приемосдаточных испытаний БП (партию) возвращают предприятию-изготовителю для выявления причин несоответствия требованиям технических условий, их устранения или исключения дефектных БП и повторного предъявления.
Результаты выявления причин несоответствия и принятые предприятием меры по их устранению отражаются в акте (форма 7, Приложение А).
6.3.8. Возвращенную представителем заказчика партию после устранения брака (или исключения дефектных БП) повторно предъявляют представителю заказчика с надписью «Вторичное».
Вторичное извещение подписывают только руководитель предприятия-изготовителя и начальник ОТК.
Вместе с вторичным извещением представителю заказчика предъявляют акт (п.6.3.6).
6.3.9. Повторные испытания проводят в полном объеме приемосдаточных испытаний на удвоенном количестве БП.
Допускается, по согласованию с представителем заказчика, повторные испытания проводить только по параметрам, по которым БП не соответствовали требованиям ТУ и параметрам, по которым испытания не проводились.
6.3.10. Если и при повторных испытаниях БП (партии) выявляют несоответствие требованиям настоящих технических условий, то всю партию забраковывают.
6.3.11. Решение об использовании окончательно забракованной партии в каждом конкретном случае принимают заказчик (или по его поручению представитель заказчика) и руководитель предприятия-изготовителя.
6.3.12. Принятыми считают БП (партии), которые выдержали испытания, укомплектованы и упакованы в соответствии с требованиями настоящих технических условий, опломбированы представителем заказчика или ОТК, и на которые оформлены документы, удостоверяющие их приемку.
Принятые БП (партии) подлежат отгрузке или сдаче на ответственное хранение предприятию-изготовителю.
6.3.13. На каждую партию бронепанелей, прошедших приемосдаточные испытания и подлежащих самостоятельной поставке оформляется паспорт с указанием:
– наименования или шифра предприятия-изготовителя;
– наименования изделия;
– уровня защиты;
– номера настоящих технических условий;
– номера партии;
– количества БП в партии, шт.; их номера;
– даты изготовления партии бронепанелей или даты проведения приемосдаточных испытаний;
– гарантии изготовителя;
– заключения ОТК и ПЗ.
Паспорт подписывает руководитель предприятия-изготовителя, либо лицо им уполномоченное, начальник ОТК (технический контролер) и представитель заказчика. Паспорт вкладывают в один из ящиков, на котором делают надпись: «Паспорт здесь».
Копия паспорта, извещения и протокола ПСИ подлежат хранению в отделе технического контроля предприятия-изготовителя в течение 15 лет.
Периодические испытания
6.4.1. Периодические испытания (ПИ) проводятся с целью периодического контроля качества БП, контроля стабильности технологического процесса в период между предшествующими и очередными испытаниями, подтверждения возможности продолжения изготовления БП по действующей конструкторско-технологической документации и их приемки.
6.4.2. Испытания проводит предприятие-изготовитель при участии и под контролем представителя заказчика, который дает заключение по результатам испытаний (при проведении испытаний на предприятии-изготовителе).
Допускается по согласованию с заказчиком проведение испытаний в организации заказчика.
6.4.3. При проведении испытаний контролируют требования п.п. 1.2.1. , 1.2.2 и 1.2.9.
6.4.4. Периодические испытания проводят после изготовления 3600 (трех тысяч шестисот) БП (грудных/спинных, с учетом примечания к п. 6.1.1), но не реже одного раза в год в соответствии с графиком периодических испытаний, где указывают место и сроки проведения испытаний. График составляет предприятие-изготовитель с участием представителя заказчика и утверждает руководитель предприятия-изготовителя и представитель заказчика.
6.4.5. Для проведения испытаний представитель заказчика в присутствии представителя ОТК отбирает шесть грудных (спинных) БП (либо 12 боковых БП) в течение года, либо периода производства 3600 шт. Отбор производят равномерно по времени изготовления из числа БП, изготовленных в контролируемом периоде (количестве), после предыдущих периодических испытаний и выдержавших приемосдаточные испытания. Оформляют отбор актом (форма 8, Приложения А).
Передачу БП на испытания проводят после отбора всех БП, но не позже 10 декабря текущего года. Испытания проводят на двух БП, а четыре других испытывают в случае получения отрицательных результатов на первых двух.
6.4.6. Результаты испытаний считают положительными при получении положительных результатов испытаний БП, отобранных в соответствии с п.6.4.5.
6.4.7. Результаты периодических испытаний оформляют актом в сроки, определенные графиком. Акт утверждает руководитель предприятия-изготовителя, а также представитель заказчика или руководитель организации заказчика, проводившей испытания. Форма акта приведена в Приложении А (форма 9).
6.4.8. При получении отрицательных результатов испытаний БП приемку и отгрузку принятых партий приостанавливают до выявления причин возникновения дефектов, их устранения и получения положительных результатов повторных периодических испытаний.
6.4.9. Повторные испытания проводят в полном объеме периодических испытаний на удвоенном количестве БП. Допускается по согласованию с представителем заказчика повторные ПИ проводить в объеме следующих видов испытаний:
– на которых обнаружены несоответствия БП (партии) установленным требованиям;
– которые могли повлиять на возникновение дефектов;
– по которым испытания не проводились.
6.4.10. При положительных результатах повторных периодических испытаний приемку и отгрузку БП возобновляют.
6.4.11. Если БП не выдержали повторных испытаний, то их приемку и отгрузку прекращают до совместного решения представителя заказчика и предприятия-изготовителя на основании анализа выявленных дефектов и их причин.
Типовые испытания
6.5.1. Типовые испытания (ТИ) проводят для оценки эффективности и целесообразности предлагаемых изменений конструкции, технологии или введения новых материалов, которые могут повлиять на технические характеристики БП или их эксплуатационные свойства.
6.5.2. Необходимость проведения типовых испытаний определяется предприятием-разработчиком совместным решением с представителем заказчика, либо в других случаях согласно ГОСТ РВ 15.307-2002.
Типовым испытаниям подвергают БП (партии), изготовленные с учетом предлагаемых изменений.
6.5.3. Испытания проводит предприятие-изготовитель с участием представителя заказчика по программе, утвержденной в установленном порядке и согласованной с представителем заказчика. Готовность БП (партии) к типовым испытаниям определяют ОТК (технический контролер) предприятия-изготовителя и представитель заказчика.
6.5.4. Объем испытаний, включенных в программу типовых испытаний, должен быть достаточным для оценки влияния внесенных изменений на технические характеристики БП.
Программу типовых испытаний разрабатывает предприятие-изготовитель и согласовывает с ПЗ.
6.5.5. Программа испытаний должна содержать:
– перечень необходимых испытаний из состава приемо-сдаточных и периодических испытаний;
– требования к количеству БП, необходимых для проведения испытаний;
– перечень методов испытаний.
6.5.6. Если эффективность и целесообразность прилагаемых изменений подтверждены положительными результатами типовых испытаний, то их вносят в документацию на БП.
Бронепанели, изготовленные после внесения изменений в документацию, испытывают как указано в ГОСТ РВ 15.307-2002.
6.5.7. Результаты испытаний оформляют актом с отражением всех результатов испытаний. Акт подписывают лица, проводившие испытания и утверждает руководитель предприятия-изготовителя и представитель заказчика.
МЕТОДЫ КОНТРОЛЯ
Общие положения
7.1.1. Методы контроля, изложенные в настоящих технических условиях, являются руководящим материалом при проверках и испытаниях БП ОТК (техническим контролером) предприятия-изготовителя и представителем заказчика и содержат практические указания о приемке и испытаниях БП.
7.1.2. Контролю подлежат все параметры БП, приведенные в таблице 5.
7.1.3. Все испытания, при отсутствии специальных указаний, проводят в нормальных климатических условиях по ГОСТ 10681-75:
– температура воздуха ;
– относительная влажность (65±5)%.
Освещенность рабочего места контролера должно быть не менее 200 лк.
7.1.4. Допускается, по согласованию с представителем заказчика, проводить контроль нескольких параметров одновременно. Например, совместить контроль внешнего вида, маркировки и комплектности.
Таблица 5
Контролируемый параметр | Номер раздела, пункта ТУ | Норматив-ный показатель | Метод контроля (основной принцип) | Применяемое оборудование, документация, эталон |
1. Качество исходных материалов | 1.4 | Согласно ТБМП.305219.007ДК | ||
2. Внешний вид | 1.1.1, 1.2.6, 1.2.7 | По контроль-ным образцам | Визуальное сличение с образцом | Контрольные БП и поверочный стол |
3. Масса | 1.2.3 | По табл. 2 | Взвешивание | Весы с пределом измерения не более 25 кг по ГОСТ 29329-82 |
4. Маркировка | 4 | — | Сличением с контрольным образцом | Контрольный образец БП |
5. Комплектность | 3 | — | Визуально | Образец паспорта |
6. Упаковка | 5 | — | Визуально | Настоящие ТУ, образец упаковочного листа, схема укладки. |
7. Пулестойкость | 1.2.1, | По табл. 1 | Согласно | |
степень контузии | 1.2.2 | не более 2 степени | ТБМП.305219.007ПМ | ТБМП.305219.007ПМ |
Контроль параметров бронепанелей
7.2.1. Качество исходных материалов проверяется при проведении входного контроля согласно «Инструкции по проведению входного контроля» ТБМП.305219.007 ДК.
7.2.2. Внешний вид бронепанелей контролируется визуально, на специальном поверочном столе, путем сличения с контрольным образцом БП.
7.2.3. Контроль массы БП проводится взвешиванием БП на весах по ГОСТ 29329-82 с пределом измерения не более 25 кг. Погрешность измерения при этом должна быть не более ±10 г.
7.2.4. При проверке размеров бронепанелей проводится сравнение фактических габаритных размеров контролируемых БП с требованиями настоящих технических условий. Измерения проводят на поверочном столе со специальным упором.
Средствами измерений служат: линейка металлическая по ГОСТ 427-75 или рулетка металлическая по ГОСТ 7502-89 с пределами измерения до 1 м и штангенциркуль по ГОСТ 166-89.
7.2.5. Проверку защитных свойств БП на соответствие требованиям п.1.2.1 и 1.2.2 настоящих технических условий проводят по ТБМП.305249.007 ПМ.
7.2.6. Контроль маркировки БП, комплектности и упаковки проводится визуально, сличением маркировки на контролируемой БП с контрольной БП, либо соответствующим чертежом. Наличие паспорта и правильность упаковки проверяют в процессе упаковки.
7.2.7. Характеристики БП, перечисленные в п.п. 1.2.4, 1.2.5 и 1.2.8 проверены в ходе государственных испытаний и опытной войсковой эксплуатации БЖ 6Б43 и в дальнейшем проверяются при изменении конструкции и (или) материалов БП в ходе типовых испытаний. Характеристики БП по п. 1.2.9, 1.3 проверяются при ПИ бронежилетов.
Габаритные размеры и радиус кривизны БП обеспечиваются технологической оснасткой и при проведении ПрИ и ПСИ не контролируются. Периодичность контроля технологической оснастки по обеспечению стабильности габаритных размеров БП установлена в технологической документации.
ТРАНСПОРТИРОВАНИЕ И ХРАНЕНИЕ
8.1. Принятые представителем заказчика БП до их отправки сдают на ответственное хранение предприятию-изготовителю.
8.2. Упакованные согласно разделу 5, БП хранят в сухих складских помещениях на стеллажах или в штабелях. Высота штабеля не более 4-х ящиков.
Температура в помещении должна быть не ниже минус 40°С и не более плюс 40°С, влажность воздуха не более 65%.
8.3. НЕ ДОПУСКАЕТСЯ хранение БП в одном помещении с химически активными веществами.
8.4. Транспортирование упакованных, согласно разделу 5, БП может осуществляться любым видом транспорта в соответствии с действующими правилами перевозок грузов, техническими условиями перевозок и крепления грузов, утвержденных соответствующими инстанциями Российской Федерации.
За погрузку и отправку ответственность несет предприятие-изготовитель.
8.5. Хранение и транспортирование введенных в эксплуатацию БП (т.е. установленных в БЖ) осуществляется в соответствии с требованиями руководства по эксплуатации на БЖ с учетом выше перечисленных требований.
СПЕЦИАЛЬНАЯ ОБРАБОТКА БП
9.1. ВНИМАНИЕ! Не допускается проведение дегазации бронепанелей обработкой дихлорэтаном на установке ЭПАС.
9.2. Проведение обработки БП необходимо осуществлять отдельно от БЗК с использованием дегазирующих комплектов: ИДК, ДК-4, ДК-5, ДКВ или авторазливочных станций АРС-14, АРС-14К, АРС-15М в соответствии с «Руководством по специальной обработке», Воениздат, 1988 и «Руководством по специальной обработке в подразделениях», Воениздат, 1989.
ГАРАНТИИ ИЗГОТОВИТЕЛЯ
10.1. Изготовитель гарантирует соответствие БП требованиям настоящих технических условий и комплекта конструкторской документации.
10.2. Гарантийный срок хранения БП устанавливают 10 лет со дня изготовления, включая 4-летний срок эксплуатации, без прямого воздействия поражающими элементами при соблюдении условий и правил хранения, транспортирования и эксплуатации (в составе БЖ).
Дата добавления: 2020-04-25; просмотров: 463; Мы поможем в написании вашей работы! |
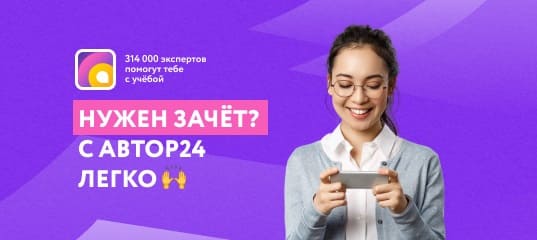
Мы поможем в написании ваших работ!