Конвейер привод питатель ленточный
Дробилки. Расчет основных эксплуатационных показателей валковой дробилки
Цель работы: Ознакомиться с дробильными машинами, изучить их виды (классификации), принцип действия. Рассчитать основные эксплуатационные показатели валковой дробилки.
1.1 Основные сведения
Измельчение твердых, сыпучих материалов широко используется в химической промышленности, так как применение измельченных сыпучих материалов позволяет значительно активизировать химическое взаимодействие, растворение, обжиг, а также другие процессы, скорость протекания которых напрямую зависит от показателей удельной поверхности твердых тел, участвующих в реакциях. Классификация дробильных машин по способу воздействия на измельчаемый материал: дробилки, разрушающие материал сжатием (щековые, конусные, валковые) или ударом (роторные, молотковые).
1.2 Валковые дробилки. Область применения, принцип действия, классификация
Валковые дробилки применяют для среднего и мелкого дробления материалов высокой и средней прочности, а также для измельчения пластичных и хрупких материалов.
Рабочими органами валковой дробилки (рисунок 1.2.1) являются два параллельных цилиндрических валка 2 и 4, вращающихся встречно. Попадающий в рабочую зону кусок материала увлекается трением о поверхность валков и затягивается в рабочее пространство, где подвергается дроблению в результате раскалывания, излома и истирания. Поверхности валков бывают гладкие и рифленые. Валки монтируются в станине 1 в подшипника 3 и 6. Подшипники одного либо двух валков имеют пружинные опоры 5, которые могут перемещаться в направляющих при попадании в дробилку недробимого предмета. Вращение валка сообщается от электродвигателя через клиноременную передачу с частотой 75-190 мин-1.
|
|
Рисунок 1.2.1 - Валковая дробилка: а — конструкция; б — схема
Максимальный размер кусков зависит от диаметра валков и размера разгрузочной щели. Так, диаметр гладкого валка должен в 20 раз превосходить размер камня, а при рифленых поверхностях валков — в 12 раз. Поэтому степень дробления составляет 4—12.
1.3 Расчет валковой дробилки
Соотношения для расчета основных параметров валковых дробилок – угла захвата, производительности, частоты вращения валков, усилий в деталях.
Угол захвата в валковых дробилках— это угол между двумя касательными к поверхности валков в точках соприкосновения с дробимым материалом (рисунок 1.3.1). Кусок материала будет захватываться, если
или
.
Так же как у щековых и конусных дробилок, угол захвата у валковых дробилок для нормального дробления не должен превышать двойного угла трения. При коэффициенте трения для реальных случаев f = 0,30—0,45, угол трения составляет = 16°40'—24°20'. На практике для гладких валков принимают
= 16—24°, чтобы исключить выдавливание дробимых кусков из рабочей зоны. Зубчатые и рифленые валки обеспечивают лучшие условия захвата, поэтому
= 20-30°.
|
|
Рисунок 1.3.1 - Расчетная схема валковой дробилки
Максимальный размер куска, захватываемого валками, можно определить по формуле
dmax=[D(1-k) + b]/k,
где k – коэффициент захвата (для гладких валков k = 0.954, для рифленых k = 0.92);
b – ширина выходной щели, м.
Производительность валковых дробилок Q, м3/с, можно вычислить, если представить процесс дробления как движение ленты материала. За один оборот валка через щель пройдет объем ленты материала V, м3:
V = DLb,
где D – диаметр валка, м,
L – длина валка, м.
Производительность дробилки при частоте вращения вала n
Q = 1,25 DLbn
,
где 1,25 – коэффициент, учитывающий возможное расхождение валков при работе; - коэффициент, учитывающий степень разрыхленности материала (для прочных материалов
= 0,2-0,3, для влажных
= 0,4-0,6).
Частота вращения валков n, об/с, валковой дробилки не должна превышать некоторого значения, при котором создаются неустойчивые условия захвата материала и возникают нежелательные колебания нагрузок.
|
|
Наиболее благоприятный режим работы наступает при окружной скорости валков oпт = 3-6 м/с. Отсюда находится частота вращения валков
Максимально возможную частоту вращения валков определяют по формуле, предложенной проф. Л.Б. Левенсоном:
,
где f – коэффициент трения материала о валок (для прочных пород f > 0,3, для глин f < 0,45); d – диаметр куска исходного материала, м; - плотность измельчаемого материала, кг/м3.
Усилия в деталях валковой дробилки определяются нагрузкой, которая создается пружинами предохранительного устройства. Эта нагрузка зависит от многих факторов и может быть вычислена лишь приближенно.
Суммарное усилие дробления P, H,
Р =
где – предел прочности материала при сжатии, Па;
- длина дуги на участке измельчения материала, м.
Сила нажатия пружин подвижного валка должна обеспечивать суммарное значение P.
Для расчета мощности валковых дробилок можно рекомендовать эмпирические формулы. При переработке пород средней прочности (мергель, известняк, уголь) для расчета N, Вт, используется формула Аргаля
N = 47,6KL , Bt,
где К= 0,6(D /d) + 0,15 - коэффициент;
|
|
=
Dn - окружная скорость валков, м/с.
Таблица 1.3.1 - Техническая характеристика валковых дробилок с гладкими (ГОСТ 18266-72) валками
Параметр | ДГ 400х250 | ДГ 600х400 | ДГ 800х500 | ДГ 1000х500 | ДГ 1500х600 |
Диаметр валка, мм | 400 | 600 | 800 | 1000 | 1500 |
Длина валка, мм | 250 | 400 | 500 | 550 | 600 |
max размер исходного куска, мм | 20 | 30 | 40 | 50 | 75 |
Зазор между валками, мм | 2-12 | 2-14 | 4-16 | 4-18 | 4-20 |
Частота вращения, об/с | 2,38 3,33 4,75 | 2,00 2,50 3,16 | 1,20 1,66 2,42 | 0,95 1,50 1,92 | 0,63 1,00 1,26 |
Производительность, м3/ч | 3-12 | 4-24 | 6-35 | 10-45,6 | 15-75 |
Мощность двигателя, кВт | 8 | 22 | 30 | 40 | 55 |
1.4 Пример расчета валковой дробилки
Выбрать марку валковой дробилки для переработки 24 м3/ч мягкого известняка, имеющего куски средневзвешенным диаметром 73 мм. Продукт дробления должен иметь средневзвешенный размер 15 мм. Определить основные эксплуатационные показатели: частоту вращения валков (рассчитать по формуле, а затем выбрать ближайшее стандартное значение по табл.1.3.1); усилие, необходимое для дробления материала; мощность электродвигателя.
Механические свойства мягкого известняка:
плотность
предел прочности при сжатии
модуль упругости
При выборе типоразмера валковой дробилки учитываем, что размер между валками не может быть меньше среднего размера куска продукта дробления. С учетом заданных параметров по производительности и размеру куска по таблице 1.3.1 выбираем дробилку марки ДГ 1500х600, имеющую следующие технические характеристики: D=1,5м; dmax=0,0075м; b=4-20мм; Q=15-75м3/ч; N=55кВт.
Задавшись значением окружной скорости валка ω=4м/с, находим оптимальную частоту вращения валков nопт, об/с:
Ближайшее рабочее значение частоты вращения валков дробилки принимаем равным n = 1 об/с. Тогда фактическая окружная скорость вращения валков равна:
.
Длина дуги на участке измельчения l, м:
где α=16ᵒ (0,279 рад)
Необходимое усилие дробления материала при длине дуги на участке измельчения Р, Н:
Мощность электродвигателя N, кВт:
1.5 Задача для самостоятельного решения
Задача: По таблице 1.3.1 выбрать марку валковой дробилки для переработки Q м3/ч известняка, имеющего куски средневзвешенным диаметром ,м. Определить основные эксплуатационные показатели: частоту вращения валков (рассчитать по формуле, а затем выбрать ближайшее стандартное значение по таблице 1.3.1); усилие, необходимое для дробления материала; мощность электродвигателя. Исходные данные в таблице 1.5.1.
Таблица 1.5.1 – Варианты для решения задачи
N варианта | Q, ![]() | ![]() | ![]() | ![]() | ![]() | ![]() |
1 | 24 | 0,073 | 4 | 50 | 0,5 | 0,279 |
2 | 30 | 0,055 | 4 | 70 | 0,5 | 0,279 |
3 | 18 | 0,042 | 5 | 110 | 0,5 | 0,279 |
4 | 9 | 0,031 | 5 | 45 | 0,5 | 0,279 |
5 | 5 | 0,023 | 4 | 65 | 0,5 | 0,279 |
6 | 17 | 0,038 | 4 | 90 | 0,5 | 0,279 |
7 | 60 | 0,076 | 5 | 115 | 0,5 | 0,279 |
8 | 33 | 0,051 | 5 | 80 | 0,5 | 0,279 |
9 | 6 | 0,019 | 4 | 78 | 0,5 | 0,279 |
10 | 30 | 0,035 | 4 | 55 | 0,5 | 0,279 |
Производительность дробилки Q, т/ч, пропорциональна площади отверстия F и окружной скорости н
где L - длина валка, м; b - ширина щели между валками, м; µ- коэффициент разрыхления, принимается в зависимости от размера дробленого продукта, µ=0.33ч0,0005d (d, мм); д - средняя плотность, т/м3 (для бентонита 0,1-1,0 т/м3).
Частота вращения валков, мин-1,
Или
Мощность электродвигателя, кВт, валков пропорциональна длине валков и окружной скорости:
где К=0.85 для зубчатых валков.
В валковых дробилках материал дробится двумя валками, вращающимися навстречу один другому. Валковые дробилки бывают с гладкими, рифлеными и зубчатыми валками. Размеры валковых дробилок определяются диаметром D и длиной L валков. Окружная скорость на поверхности валков составляет 4-6 м/с. Степень дробления 4-6. Технические характеристики валковых дробилок приведены в табл. 3.13.
Процесс дробления в дробилках с зубчатыми валками происходит за счет скалывания пород и осуществляется при меньших переизмельчении и расходе электроэнергии, чем в щековых и конических дробилках.
При крупном дроблении форма зубьев клювообразная, высота их от 70 до 110 мм; при мелком - копьевидная, высота зубьев около 30 мм.
Технические характеристики валковых дробилок с зубчатыми валками приведены в табл. 3.14. Производительность валковой дробилки Q (т/ч) можно вычислить по формуле [1,4]
(3.30)
где п - частота вращения валков,(80) мин-1; D и l - соответственно диаметр и длина валка, м; S - ширина щели между валками, м; δ - плотность дробимого материала, (0,5) т/м3; А: - коэффициент разрыхления -0,5 (0,1-0,2).
Ленточные питатели
Рисунок 1 — Ленточный питатель
Ленточные питатели используются для подачи мелко- и, реже, среднекусковых сухих и влажных сыпучих материалов. Питатели устанавливают горизонтально или с уклоном 10° в сторону подачи. В горизонтальной части короба (рисунок 1) имеется заслонка для регулирования производительности питателя, т/ч, определяемой по формуле:
Ленточный питатель не может работать непосредственно под бункером. Для разгрузки ленты от столба материала предусматривается наклон стойки над бункером под углом α = 45 — 50°.
Основы расчета питателей.
Производительность ленточного и пластинчатого питателя, т/ч:
, где
B – расстояние между бортами питателя, м;
Н – высота слоя материала на ленте(или подъем заслонки)
м
V – скорость движения ленты питателя, м/с;
kH – коэффициент заполнения
;
ρ - насыпная плотность материала, т/м.
конвейер привод питатель ленточный
Исходные данные
Производительность 40 т/ч
Транспортируемый материал земля формовочная
Загрузка из бункера
Разгрузка через приводной барабан
Общая длина питателя 4 м
Рисунок 3 - Принципиальная схема питателя
Выбор элементов питателя
Определение ширины ленты
При транспортировки насыпных грузов ширину ленты определяют по максимальной расчетной производительности и крупности транспортируемых кусков.
Необходимая ширина ленты определяется по формуле (83)
(83)
где КП -коэффициент площади поперечного сечения груза на ленте, КП= 240 /9, с. 130/.
По конструктивным соображениям выбираем ширину ленты из стандартного ряда по ГОСТ Ту 22644-77 В=1000мм.
Дата добавления: 2020-04-08; просмотров: 286; Мы поможем в написании вашей работы! |
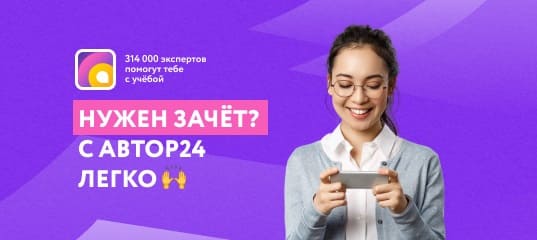
Мы поможем в написании ваших работ!