Упрочнение термической объемной обработкой
Термическая обработка включает следующие основные типы: отжиг I рода, отжиг II рода, закалка без полиморфного превращения, закалка с полиморфным превращением, отпуск и старение. Каждый из этих типов термической обработки качественно отличается один от другого характером фазовых и структурных превращений.
Отжиг I рода частично или полностью устраняет отклонения от равновесного состояния, возникшее при предыдущей обработке (литье, штамповке, сварке и пр.), причем его проведение не связано с фазовыми превращениями. Различают следующие разновидности отжига I рода: гомогенизация, рекристаллизация, уменьшение остаточных напряжений.
Отжиг II рода, полностью основанный на фазовых превращениях, бывает: полный, неполный, изотермический, сфероидизирующий. Разновидностью отжига II рода является также нормализация.
Закалка без полиморфного превращения образует пересыщенный твердый раствор.
Старение обеспечивает распад пересыщенного твердого раствора с вьщелением дисперсных фаз, приводящих к упрочнению. Старение подразделяется на естественное (20°С) и искусственное с нагревом до определенной температуры.
Закалка на пересыщенный твердый раствор со старением — это основной способ упрочняющей обработки сплавов цветных металлов. Он применяется также для сталей, в частности — мартенситно- стареющих.
Закалка с полиморфным превращением (закалка на мартенсит) связана с мартенситным превращением высокотемпературной фазы. С целью упрочнения закалке на мартенсит подвергают титановые сплавы, но особенно широко ее применяют в производстве стальных деталей.
|
|
В зависимости от нагреваемого объема закалку разделяют на объемную и поверхностную, а в зависимости от метода охлаждения, принятого при закалке, различают закалку непрерывную, прерывистую, ступенчатую, изотермическую и закалку с самоотгпуском.
Отпуску подвергают закаленную на мартенсит сталь для перевода неравновесной структуры в более равновесную, обеспечивающую заданный комплекс свойств. В зависимости от температуры нагрева различают низкий, средний и высокий отпуск.
Закалка с высоким отпуском называется улучшением.
Термическая обработка — совокупность технологических операций, связанных с нагревом, вьдержкой и охлаждением. Основная задача нагрева стали — перевод структуры в аустенитное состояние и получение возможно более мелкого зерна.
Температура нагрева под закалку большинства конструкционных и инструментальных легированных сталей находится в пределах 800-880°С (для каждой марки стали свой узкий интервал закалочных температур). Для сталей с большим содержанием карбидообра- зующих элементов температура нагрева под закалку значительно превышает критические точки Ас1 и Ас3.
|
|
Например, штамповые стали типа ЗХ2В8Ф закаливают с температур 1050...1100°С, а быстрорежущие типа Р9 и Р18 — с температур 1250...1300°С. Продолжительность нагрева (табл.1) должна обеспечить нагрев изделия по сечению и завершение фазовых превращений, но не должна быть слишком большой, чтобы не вызвать рост зерна и обезуглероживание поверхности стали.
Табл. 1 Ориентировочная продолжительность нагрева изделий для закалки до 800-850°С в различных печах.
Продолжительность изотермической выдержки, обеспечивающей завершение фазовых превращений и гомогенизацию аустенита, принимают равной 15—25% от продолжительности сквозного нагрева. Для предотвращения окисления и обезуглероживания поверхности деталей нагрев под термическую обработку проводят в защитных, контролируемых по углеродному потенциалу средах, в вакууме (10х2... 10х3 кПа), в расплавленных солях CaCl2, NaCl, BaCl2 и др.
Режим охлаждения при закалке должен обеспечить необходимую глубину прокали- ваемости, но не вызвать при этом значительных закалочных напряжений, приводящих к короблению изделия и образованию закалочных трещин. Он устанавливается по диаграммам изотермического и термокинетического распада аустенита. В зависимости от степени переохлаждения аустенита различают перлитное превращение, бейнитное (промежуточное) превращение и мартенситное превращение. Последнее происходит в диапазоне температур начала (M) и конца (Л) превращения мартенсита. Положение мартенситных точек М и Л определяется составом аустенита и не зависит от скорости охлаждения. При закалке сталей возникают тепловые и структурные фазовые напряжения. Наиболее опасны фазовые напряжения, возникающие в результате мартенситного превращения аустенита, так как образуется хрупкая фаза-мартенсит.
|
|
Выше точки Л возникают только термические напряжения, причем сталь находится в аустенитном состоянии, а аустенит пластичен. В качестве закалочных сред для углеродистых сталей наиболее широко используют воду, 10%-ный раствор NaOH или NaCl, а для легированных — минеральные масла (табл. 2)
Табл. 2. Скорость охлаждения стали в различных средах.
Находят применение водные растворы полимеров, которые по охлаждающей способности занимают промежуточное положение между водой и маслом. Сразу после закалки стали применяется отпуск, в результате которого сталь получает требуемые свойства.
|
|
Кроме того, отпуск полностью или частично устраняет внутренние напряжения, возникающие при закалке.
Низкий отпуск (150...250 °С) применяют для режущего, измерительного инструмента, деталей подшипников качения, а также деталей после поверхностной закалки, цементации, нитроцементации и цианирования.
Средний отпуск (350...500°С) применяют главным образом для пружин, рессор и штампов. Структура стали (0,45...0,8% С) после среднего отпуска — троостит отпуска или троостомартенсит с твердостью 40...50 HRC.
Температуру отпуска следует выбирать таким образом, чтобы не вызывать необратимой отпускной хрупкости (отпускной хрупкости I рода).
Высокий отпуск (500...680 °С) применяют для среднеуглеродистых (0,3...0,5% С) улучшаемых сталей. Улучшение создает наилучшее соотношение прочности и вязкости стали. Легирующие элементы Мо, W, Сг, V замедляют процессы диффузии и коагуляцию карбидов, поэтому процессы, происходящие при отпуске, в легированных сталях смещаются к большим температурам. Это позволяет полнее снять остаточные закалочные напряжения.
Продолжительность среднего и высокого отпуска обычно составляет 1...2 ч для деталей небольшого сечения и 2...8 ч для массивных деталей. Для нагрева под закалку, нормализацию и отжиг мелких и средних деталей в термических цехах единичного и мелкосерийного производства применяют камерные печи с защитной атмосферой (СНЗ) и без защитной атмосферы (СНО).
Для нагрева деталей большой длины применяют шахтные печи типа СШО и СШЗ. В массовом производстве применяются высокомеханизированные закалочно-отпускные афегаты, имеющие как универсальное, так и специальное назначение (типа СНЗА, СКЗА).
Все шире применяются вакуумные печи и установки на их основе, в которых проводится термическая обработка с последующей закалкой в азотоводородной атмосфере при давлениях до 2 МПа со скоростями охлаждения, близкими к охлаждению в масле. В таких устано"вках удается получить чистую поверхность деталей при минимальных деформациях.
Дата добавления: 2020-01-07; просмотров: 288; Мы поможем в написании вашей работы! |
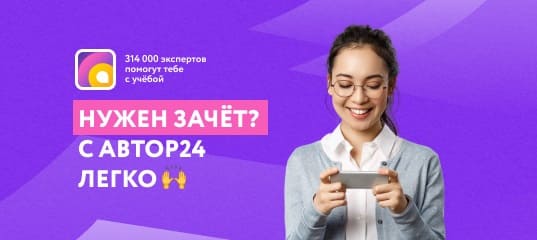
Мы поможем в написании ваших работ!