Методические указания к выполнению задания №1
Задание №1
На основе размерного анализа установить метод сборки механизма в указанных условиях производства. При использовании метода пригонки или регулирования рассчитать компенсирующее звено.
Таблица 4.1.1
Варианты заданий
Две последние Цифры шифра | Номер рисунка и вариант К заданию №1 |
00, 20, 40, 60, 80 01, 21, 41, 61, 81 02, 22, 42, 62, 82 03, 23, 43, 63, 83 02, 24, 44, 64, 84 05, 25, 45, 65, 85 06, 26, 46, 66, 86 07, 27, 47, 67, 87 08, 28, 48, 68, 88 09, 29, 49, 69, 89 10, 30, 50, 70, 90 11, 31, 51, 71, 91 12, 32, 52, 72, 92, 13, 33, 53, 73, 93 14, 34, 54, 74, 94, 15, 35, 55, 75, 95 16, 36, 56, 76, 96 17, 37, 57, 77, 97 18, 38, 58, 78, 98 19, 39, 59, 79, 99 | Рис. 4.1.1, вариант 1 Рис. 4.1.1, вариант 2 Рис. 4.1.1, вариант 3 Рис. 4.1.1, вариант 4 Рис. 4.1.2, вариант 1 Рис. 4.1.2, вариант 2 Рис. 4.1.2, вариант 3 Рис. 4.1.2, вариант 4 Рис. 4.1.3, вариант 1 Рис. 4.1.3, вариант 2 Рис. 4.1.3, вариант 3 Рис. 4.1.3, вариант 4 Рис. 4.1.4, вариант 1 Рис. 4.1.4, вариант 2 Рис. 4.1.4, вариант 3 Рис. 4.1.4, вариант 4 Рис. 4.1.5, вариант 1 Рис. 4.1.5, вариант 2 Рис. 4.1.5, вариант 3 Рис. 4.1.5, вариант 4 |
Рис. 4.1.1. Часть сборочного чертежа механизма:
1 – стойка левая; 2 – крышка; 3 – прокладка;
4 – колесо зубчатое (трибка); 5 – втулка (2 шт.); 6 – стойка правая
Рис. 4.1.1. (продолжение)
№ детали | Наименование размера | Обозначение | ||
N1,N6 Стойки | Размер от торца стоек до оси отверстий для втулок | A1 | ||
N4 Колесо зубчатое (трибка) | Радиальное биение зубчатого венца | ITA2 | ||
Диаметр венца трибки | D1 | |||
Диаметр ступиц трибки | ![]() | |||
N3 Прокладка | Толщина прокладки | A3 | ||
N5 Втулка
| Биение отверстия относительно наружной поверхности ![]() | ITA4 | ||
Диаметр отверстия втулки | ![]() | |||
Радиальный зазор между зубчатым колесом и крышкой | AD |
Параметр | Вариант | |||
№1 | №2 | №3 | №4 | |
A1 | 45±0,05 | 30±0,065 | 52±0,06 | ![]() |
ITA2 | 0,025 | 0,024 | 0,04 | 0,02 |
D1 | 96-0,036 | 66-0,046 | 108-0,052 | 60-0,046 |
![]() | ![]() | ![]() | ![]() | ![]() |
A3 | ![]() | ![]() | ![]() | 0 (нет прокл.) |
ITA4 | 0,04 | 0,04 | 0,05 | 0,04 |
![]() | 20+0,033 | 20+0,033 | 40+0,025 | 20+0,033 |
AD | ![]() | ![]() | ![]() | ![]() |
Тип произв-ва | Массовое | Мелкосерийное | Среднесерийное | Крупносерийное |
Рис. 4.1.1. (окончание)
Рис. 4.1.2. Часть сборочного чертежа механизма:
1 – колесо зубчатое; 2 – корпус; 3 – уплотнение; 4 – подшипник (2 шт.);
5 – вал; 6 – втулка; 7 – втулка; 8 – прокладка; 9 – уплотнение;
10 – втулка; 11 – крышка; 12 – колесо зубчатое; 13 – шайба; 14 – гайка
Параметр, мм | Вариант | |||
1 | 2 | 3 | 4 | |
A1 | 10-0,15 | 10-0,09 | 10-0,15 | 10-0,09 |
A2 | 2-0,1 | 3-0,06 | 4-0,048 | 3-0,04 |
A3 | 18+0,18 | 20+0,13 | ![]() | ![]() |
A4 | 12-0,07 | 12-0,07 | 15-0,07 | 15-0,07 |
A5 | 60+0,3 | 65+0,19 | ![]() | ![]() |
A6 | 12-0,07 | 12-0,07 | 15-0,07 | 15-0,07 |
A7 | ![]() | ![]() | 96+0,14 | 95+0,14 |
Торцовое биение зубчатого венца (поз. 12) | A8=0±0,015 ITA8=0,03 | A8=0±0,015 ITA8=0,03 | A8=0±0,015 ITA8=0,03 | A8=0±0,015 ITA8=0,03 |
A∆ | ![]() | ![]() | ![]() | ![]() |
Тип производства | Массовое | Мелкосерийное | Среднесерийное | Среднесерийное |
Рис. 4.1.2. (окончание)
|
|
Рис. 4.1.3. Часть сборочного чертежа механизма:
1 – вал; 2 – шайба; 3 – корпус; 4 – втулка (2 шт.);
5 – колесо зубчатое; 6 – шайба; 7 – гайка
Параметр, мм | Вариант | |||
1 | 2 | 3 | 4 | |
A1 | 8-0,15 | 8-0,15 | 8-0,09 | 6-0,075 |
A2 | 90-0,22 | 90-0,22 | 90-0,14 | 75-0,19 |
A3 | 8-0,15 | 8-0,15 | 8-0,09 | 6-0,075 |
A4 | 3-0,06 | ![]() | ![]() | ![]() |
A5 | 110+0,35 | 110+0,35 | 110+0,22 | 90+0,22 |
Торцовое биение зубчатого венца (поз. 5) | 0±0,02 ITA6=0,04 | 0±0,02 ITA6=0,04 | 0±0,02 ITA6=0,04 | 0±0,015 ITA6=0,03 |
A∆ | ![]() | 1+0,7 | 1+0,2 | ![]() |
Тип производства | Массовое | Крупносерийное | Мелкосерийное | Среднесерийное |
Рис. 4.1.3. (окончание)
Рис. 4.1.4. Часть сборочного чертежа механизма:
1 – колесо зубчатое; 2 – корпус; 3 – втулка (сб.);
4 – прокладка; 5 – крышка; 6 – втулка (сб.)
|
|
Параметр, мм | Вариант | |||
1 | 2 | 3 | 4 | |
A1 | 15-0,18 | 15-0,11 | 15-0,11 | 12-0,18 |
A2 | 56-0,19 | 60-0,12 | 58-0,12 | 60-0,3 |
A3 | 102-0,22 | 100-0,14 | 90-0,14 | 80-0,19 |
A4 | ![]() | ![]() | ![]() | ![]() |
A5 | 35-0,16 | 45-0,16 | 60-0,12 | 54-0,19 |
A6 | 56-0,19 | 50-0,1 | 58-0,12 | 50-0,25 |
A7 | 12-0,18 | 20-0,13 | 20-0,13 | 12-0,18 |
Торцовое биение поз. 6 (ITA8) | A8=0±0,015 ITA8=0,03 | A8=0±0,015 ITA8=0,03 | A8=0±0,015 ITA8=0,03 | A8=0±0,015 ITA8=0,03 |
Торцовое биение поз. 3 (ITA9) | A9=0±0,02 ITA9=0,04 | A9=0±0,02 ITA9=0,04 | A9=0±0,02 ITA9=0,04 | A9=0±0,02 ITA9=0,04 |
A∆ | 1+0,4 | 2+0,25 | 2+0,25 | ![]() |
Тип производства | Массовое | Среднесерийное | Мелкосерийное | Крупносерийное |
Рис. 4.1.4. (окончание)
Рис. 4.1.5. Часть сборочного чертежа (упрощенно):
1 – стойка левая; 2 – колесо зубчатое;
3 – втулка; 4 – стойка правая; 5 – вал
Параметр, мм | Вариант | |||
1 | 2 | 3 | 4 | |
A1 | 80-0,19 | 60-0,19 | 60-0,3 | 60-0,3 |
A2 | 120+0,35 | 85+0,22 | 85+0,35 | 85+0,35 |
A3 | ![]() | 24-0,084 | 24-0,21 | 24-0,052 |
Торцовое биение зубчатого венца | ITA4=0,04 A4=0±0,02 | ITA4=0,02 A4=0±0,01 | ITA4=0,04 A4=0±0,02 | ITA4=0,04 A4=0±0,02 |
A∆ | ![]() | ![]() | 1+0,2 | 1+0,2 |
Тип производства | Массовое | Крупносерийное | Мелкосерийное | Среднесерийное |
Рис. 4.1.5. (окончание)
|
|
Библиографический список
1. Маталин, А. А. Технология машиностроения: учебник для вузов / А. А. Маталин. – 2-е изд. – СПб.: Лань, 2008.
2. Ковшов, А. Н. Технология машиностроения: учебник для студентов машиностроительных специальностей вузов / А. Н. Ковшов.– СПб.: Лань, 2008.
3. Иващенко, И. А. Технологические размерные расчеты и способы их автоматизации / И. А. Иващенко. – М.: Машиностроение, 1975.
4. Единая система технологической документации, классификационная группа 1. – М.: Изд-во стандартов,1974.
5. Методические указания по заполнению технологической документации при выполнении контрольных работ, курсовых и дипломных проектов / Сост. Н.Н. Богородский и др. – Л.: СЗПИ,1985.
6. Справочник технолога-машиностроителя: в 2-х т. / под ред. А. Г. Косиловой и Р. К. Мещерякова. – М.: Машиностроение, 1985.
Методические указания к выполнению задания №1
Для решения задачи назначения метода сборки следует изучить конструкторские размерные цепи. При выявлении размерных цепей необходимо иметь в виду, что от чёткости формулировки задачи зависит правильность выявленной размерной цепи и поставленную задачу можно решить только единственной правильно построенной размерной цепью. Обычно замыкающим в сборочной размерной цепи является расстояние или относительный поворот поверхностей (или их осей) деталей, относительное положение которых требуется обеспечить.
Составляющими звеньями размерной цепи могут быть либо расстояния (относительные повороты) между поверхностями (их осями) деталей, образующих замыкающее звено, и основными базами этих деталей, либо расстояния (относительные повороты) между поверхностями вспомогательных и основных конструкторских баз деталей.
Руководствуясь указанными положениями, для выявления размерной цепи следует двигаться от замыкающего звена к основным базам, от них – к основным базам деталей, базирующих первые детали, учитывая отдельными звеньями несовпадения основных и вспомогательных баз и т.д., вплоть до вспомогательных баз базируемой детали сборочной единицы и образования замкнутого контура.
Точность замыкающего звена при сборке может быть достигнута одним из следующих методов: полной, неполной и групповой взаимозаменяемостью, пригонкой и регулированием.
Наиболее простым надёжным является метод полной взаимозаменяемости, так как сборка в этом случае сводится к простому соединению деталей или сборочных единиц. При этом сумма допусков составляющих звеньев, заданных по рабочим чертежам, не должна превышать допуск замыкающего звена, т.е. должно удовлетворяться основное уравнение метода расчёта размерных цепей на максимум-минимум
, (3.1)
где – допуск замыкающего звена;
TAi – допуск составляющего звена;
– передаточное отношение, которое в общем случае есть частная производная:
; для линейных цепей с параллельными звеньями
для увеличивающих и
- для уменьшающих звеньев;
m – общее количество звеньев размерной цепи.
Координата середины поля допуска размера определяется по формуле
, (3.2)
где ,
– соответственно верхнее и нижнее отклонения размера.
Координата середины поля допуска замыкающего звена связана с координатами середины полей допусков составляющих звеньев следующим уравнением
. (3.3)
Тогда
;
. (3.4)
Если указанное условие (3.1) не выполняется, полная взаимозаменяемость при заданных допусках невозможна.
Тогда следует проанализировать каждое составляющее звено размерной цепи, рассмотреть при этом, какой детали и сборочной единице оно принадлежит и на каких технологических операциях при обработке обеспечивается заданная точность звена. Если применяемые методы обработки имеют резерв точности и возможно выдержать более высокую точность без существенного усложнения и удорожания технологического процесса, технолог устанавливает технологически более жёсткие допуски на составляющие звенья и заново рассчитывает размерную цепь с целью обеспечения полной взаимозаменяемости при сборке, внося соответствующие изменения в рабочие чертежи.
В многозвенных размерных цепях при высоких требованиях к точности замыкающего звена метод полной взаимозаменяемости может оказаться нерентабельным ввиду слишком жёстких допусков на составляющие звенья и трудности, а иногда и невозможности их обеспечения при обработке. В этом случае может быть применён метод неполной взаимозаменяемости. При проверке возможности осуществления сборки этим методом предусматривается некоторый экономически допустимый процент риска получения брака, а допуск замыкающего звена рассчитывается по формуле:
, (3.5)
где t – коэффициент риска, характеризующий вероятность выхода отклонений замыкающего звена за пределы допуска и равный: 1 – при проценте риска 32; 1,65 – при проценте риска 10; 2 – при проценте риска 4,5; 3 – при проценте риска 0,27 и т.д.;
– коэффициент относительного рассеяния. Для закона нормального распределения
, для закона равной вероятности
, для закона Симпсона
.
Сборка по методу групповой взаимозаменяемости применяется, как правило, при наличии в сборочной единице короткой размерной цепи типа «отверстие-вал-зазор», если полная взаимозаменяемость невозможна по техническим или экономическим причинам. Замыкающим звеном в таких случаях является зазор, регламентированный на основе эксплуатационных требований. При осуществлении метода сначала рассчитывается средняя величина допуска составляющих звеньев размерной цепи по формуле:
. (3.6)
Затем, исходя из возможности экономически целесообразного достижения точности, устанавливается средняя величина производственного допуска путём увеличения расчётного в n раз
. (3.7)
Ориентируясь на это значение, устанавливают производственные допуски составляющих звеньев, которые состоят из n обычно равных по величине групповых полей.
При использовании методов пригонки или регулирования в конструкцию изделия вводиться специальная деталь – компенсатор, размеры которого могут изменяться при сборке путём удаления слоя металла пригонкой или регулироваться при сборке (с помощью винтовой пары, наборы прокладок и т.п.).
Наибольшая возможная компенсация и величина поправки
к значению координаты середины поля допуска компенсирующего звена при методе пригонки определяются по формулам
, (3.8)
, (3.9)
где ,
– допуск и координата середины поля допуска замыкающего звена, получаемые по методу полной взаимозаменяемости;
,
– допуск и координата середины поля допуска замыкающего звена, определяемые служебным назначением или поставленной задачей.
При методе регулирования используются следующие формулы:
Число ступеней компенсатора
. (3.10)
где – допуск на изготовление компенсатора.
Величина поправки к значению координаты середины поля допуска компенсирующего звена при условии совмещения нижних границ допусков замыкающих звеньев
. (3.11)
При определении величины следует применять координату середины поля допуска компенсирующего звена равной нулю. Величина
определяется по формуле:
. (3.12)
Здесь знак плюс применяется, если компенсирующее звено увеличивающее, а минус – если оно уменьшающее.
Величина ступени компенсации
. (3.13)
Используя указанные выше зависимости, проводят необходимые расчёты при назначении метода сборки.
Пример выполнения задания №1
Задание: установить метод сборки механизма, чертёж которого представлен на рис. 4.1.36, в условиях среднесерийного производства. При использовании метода регулирования или пригонки рассчитать компенсирующее звено.
На основе структуры размеров, представленных на рис. 4.1.36, построим размерную схему, в которой выделим составляющее и замыкающее звенья. В качестве замыкающего звена примем торцевой зазор между втулкой и зубчатым колесом. При построении размерной схемы следует учитывать, что одним из составляющих звеньев является торцевое биение зубчатого колеса, так как в механизме вращается колесо на валу, а сам вал с закреплённой втулкой не вращается. Размерная схема представлена на рис. 4.1.37.
Составим уравнение размерной цепи
В этом уравнении звенья имеют следующие значения:
мм;
0,2 мм;
0,1 мм;
мм;
мм;
-0,15мм;
мм;
0,35мм;
0,175мм;
мм;
0,052мм;
-0,026мм;
мм;
мм;
мм.
Определим допуск замыкающего звена по методу полной взаимозаменяемости по формуле (3.1) и координату середины поля допуска по формуле (3.3)
мм;
мм.
Рис. 4.1.36. Часть сборочного чертежа (упрощенно):
1 – стойка левая; 2 – втулка;
3 – колесо зубчатое; 4 – стойка правая; 5 – вал
Рис. 4.1.37. Размерная схема
Так как мм
>
=0,2мм полная взаимозаменяемость при заданных допусках составляющих звеньев не обеспечивается. Чтобы осуществить метод полной взаимозаменяемости, нужно уменьшить сумму допусков составляющих звеньев. Для этого технологически уменьшим допуски составляющих звеньев, но не увеличивая стоимость обработки.
Допуск размера задан по 12 квалитету, что, согласно [6], соответствует черновому или получистовому точению. Ужесточим допуск до 11 квалитета, что не увеличивает стоимость обработки, так как 11 квалитет является нижней границей получистового точения. Тогда допуск размера
станет равным
мм.
Аналогично ужесточим допуски размеров 2 и А3 соответственно до 11 и 8 квалитетов: ТА2=0,29мм и ТА3=0,033мм.
Тогда допуск замыкающего звена по методу полной взаимозаменяемости будет равен
мм
Так как 0,533>0,2, то и в этом случае полная взаимозаменяемость не обеспечивается.
Проверим возможность обеспечения точности замыкающего звена по методу неполной взаимозаменяемости. Принимаем риск получения брака Р=0,27%, тогда коэффициент t=3 [1]. Так как детали обрабатываются на настроенных станках и распределение размеров подчиняется закону Гаусса, принимаем . Тогда допуск замыкающего звена определится по формуле 3.5
мм.
Так как 0,465>0,2, то и неполная взаимозаменяемость при заданных допусках составляющих звеньев не обеспечивается.
Проверим возможность использования неполной взаимозаменяемости при условии принятого выше технологического ужесточения допусков составляющих звеньев. Тогда допуск замыкающего звена будет равен
мм.
Так как 0,28>0,2, то и при условии ужесточения допусков метод неполной взаимозаменяемости не обеспечивается.
Согласно [1], в заданных условиях среднесерийного производства при невозможности метода полной или неполной взаимозаменяемости наиболее экономичным является метод регулирования, который и примем для данного случая.
В качестве компенсатора примем деталь №2 – втулка ( ), имеющая размер 24 мм и допуск
мм.
Требуется определить число ступеней компенсатора и предельные отклонения размера каждой ступени.
Наибольшая величина возможной компенсации
мм.
Число ступеней компенсатора определим по формуле (3.10)
.
Определим координату середины расширенного поля допуска замыкающего звена, условно принимая координату середины поля допуска компенсирующего звена
мм.
Поправку к координате середины поля допуска компенсирующего звена определим по формуле (3.12)
мм.
Так как компенсирующее звено является уменьшающим, поправку учитываем с обратным знаком. Поэтому координата середины поля допуска первой ступени компенсирующего звена
мм.
Координаты середины полей допусков каждой последующей ступени будут отличаться от координат середины полей допусков предшествующей ступени на величину ступени компенсации, определяемой по формуле (3.13)
мм.
Тогда: мм;
мм;
мм.
Используя формулы (3.4), рассчитаем отклонения компенсаторов. Так, например, для первой ступени компенсатора
мм;
мм.
Аналогично рассчитываются отклонения для других ступеней компенсаторов.
В результате проведенных расчётов для сборки механизма принят методом достижения точности – метод регулирования с помощью четырёх компенсаторов, имеющих следующие размеры:
I степень - ; II -
; III -
; IV -
.
Дата добавления: 2020-01-07; просмотров: 222; Мы поможем в написании вашей работы! |
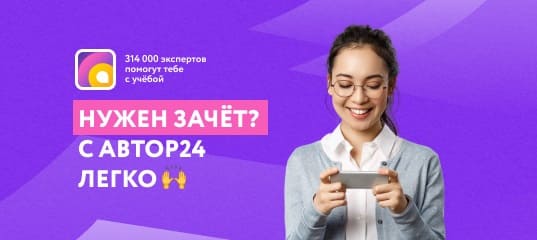
Мы поможем в написании ваших работ!