Генеративный дизайн в Fusion 360
В настоящее время функции генеративного дизайна (рис. 3.22) доступны в таких продуктах Autodesk, как Netfabb Ultimate и Fusion 360.
С точки зрения пользователя принцип работы этой технологии проектирования Autodesk достаточно прост. Конструктор задает объем, в котором системе разрешено производить поиск решения, указывает неприкосновенные для изменения зоны, препятствия, которые необходимо огибать, крепежные и рабочие участки детали, а также условия функционирования детали – закрепления и действующие на деталь нагрузки. Далее задача отправляется на решение – в облако Autodesk. Пока облако ищет возможные варианты, конструктор и его компьютер полностью свободны и могут заниматься другими творческими задачами. Как только система закончит поиск решений, она уведомит об этом пользователя и предоставит ему для просмотра все найденные варианты геометрии детали. От конструктора потребуется лишь выбрать наиболее подходящие – по массе, прочности, допустимым деформациям, технологичности и другим критериям. Далее останется только, при необходимости, доработать деталь в САПР и/или ЧПУ-решениях Autodesk, проанализировать ее в расчетных программах Autodesk и подготовить к производству.
Рис. 3.22. Примеры моделей изделий, полученных при помощи технологии генеративного дизайна
По сравнению с деталями, которые изготавливаются при помощи средств «традиционного» 3D-моделирования, масса деталей может быть уменьшена до 10 раз – при условии сохранения тех же значений запаса прочности, износостойкости и иных ограничений (рис. 3.23, 3.24).
|
|
Рис. 3.23. Оптимизация формы кронштейна при помощи генеративного дизайна
Рис. 3.24. Варианты исполнения изделия, выданные технологией генеративного дизайна во Fusion 360
Авиационный гигант Airbus и производитель программного обеспечения для проектирования Autodesk совместно реализуют уникальный проект по снижению веса отдельных элементов гражданских самолетов. В частности, партнеры модернизировали дизайн одного из элементов салона лайнера Airbus A320 – перегородку между пассажирским салоном и отсеком бортпроводников (рис. 3.25).
Это обычная на первый взгляд стенка внутри самолета; к ней крепятся откидные сидения, которыми пользуются члены экипажа во время полета. Однако этот элемент конструкции должен быть очень прочным, что делает его вес при производстве традиционными методами высоким.
Airbus и Autodesk совместно разработали новую структуру для перегородки. В ее основе своеобразная сеть из металлических частей, геометрия которых рассчитана в специальном программном продукте Autodesk с учетом прочностных требований к конструкции. Конструкция была изготовлена по частям с помощью технологии селективного лазерного плавления порошков. Материал – сплав Scalmalloy.
|
|
Рис. 3.25. Проект Airbus на технологиях Autodesk
Volkswagen с помощью облачной платформы Autodesk Fusion 360 создал концепт электрокара Volkswagen на базе классического микроавтобуса 1962 года выпуска (рис. 3.26). Пока разработчикам удалось уменьшить вес колес на 18%, а также снизить эффект трения на шины. Также в компании отметили, что искусственный интеллект позволит ускорить создание проекта автомобиля: вместо первоначально запланированных полутора лет потребуется лишь несколько месяцев. Использование генеративного дизайна упростит работу инженеров и сократит объемы рутинной работы.
Рис. 3.26. Концепт электрокара Volkswagen на базе классического микроавтобуса 1962 года выпуска
Лаборатория реактивных двигателей NASA и инженеры компании Autodesk показали посадочный модуль, спроектированный для исследования спутников Сатурна и Юпитера (рис. 3.27, 3.28).
Команда разработала аппарат с помощью технологии генеративного дизайна. Сначала были заданы ограничения: например, программа искусственного интеллекта могла работать только с определенными материалами и только в соответствии с ожидаемыми условиями окружающей среды. Затем программа вывела проект, соответствующий этим ограничениям.
|
|
После почти шести недель работы инженеры остановились на паукоподобном дизайне, который затем и сконструировали для изготовления при помощи технологии послойного синтеза. Создан модуль в основном из алюминия, его длина – 2,3 м, а высота – почти метр [8].
Рис. 3.27. Посадочный модуль
Рис. 3.28. Шасси посадочного модуля в процессе изготовления
Сотрудники голландской компании MX3D закончили производство несущей основы моста (рис. 3.29), который планируется установить в Амстердаме. При изготовлении моста использовались ПО Autodesk и технология WAAM – наплавление металлического прутка промышленным роботом-манипулятором [12], [32].
Рис. 3.29. Несущая основа моста
Поддержка традиционных методов субтрактивной обработки во Fusion 360
Как уже было сказано в разделе, посвященном подготовке производства (2.2.3.6), сильной стороной ПО для генеративного дизайна служит возможность адаптировать конструкцию изделия под возможности традиционных субтрактивных методов обработки. В частности, новейшие версии Fusion 360 поддерживают методы многоосевой механообработки (2/2.5/3/5-осевая обработка и их комбинации), что показано на рис. 3.30-3.32.
|
|
Рис. 3.30. Поддержка 2,5- и 3-осевой обработки во Fusion 360
Рис. 3.31. Поддержка 3+2-осевой обработки во Fusion 360
Рис. 3.32. Поддержка 5-осевой обработки во Fusion 360
Дата добавления: 2020-01-07; просмотров: 336; Мы поможем в написании вашей работы! |
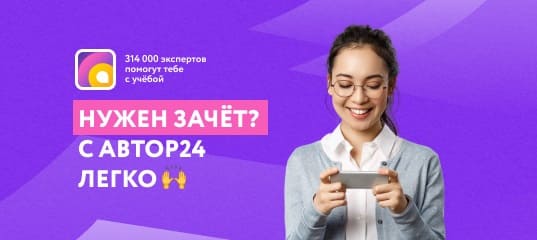
Мы поможем в написании ваших работ!