Отказы и неисправности гидросистемы.
Разнообразные нарушения работоспособности гидравлической системы можно объединить в две группы:
- нарушение нормальной циркуляции масла в соответствии с заданным режимом работы гидросистемы. Возможные причины — не плотное соединение маслопроводов и агрегатов; неисправности запорных устройств соединительных муфт; залегание (заклинивание); разрегулировка или потеря герметичности клапанов, управляющих циркуляцией масла;
- недопустимое отклонение функциональных характеристик агрегатов гидросистемы, вызванных в большинстве случаев нарушением герметичности их рабочих объемов из-за износа или разрушения деталей, снижение производительности гидронасосов, повышенные утечки масла в распределителе и других механизмах, а также в гидроцилиндрах (перетекание масла из одной его полости в другую через неплотности между поршнем и цилиндром).
Гидросистема при этом продолжает функционировать, однако значения основных результирующих характеристик ее рабочих процессов, например длительность подъема навешенного орудия, способность удерживать его в транспортном положении длительное время, отклоняются от номинальных значений. Допускаемое отклонение параметров устанавливают из технико-экономических соображений с учетом снижения производительности машинно-тракторных агрегатов и других эксплуатационных факторов. Отклонение параметра, превышающее допускаемое, считают отказом гидросистемы.
|
|
Диагностирование гидросистемы и ее агрегатов.
Плановое диагностирование гидросистемы в целях профилактики, предупреждения отказов в рабочий период, выполняют по ряду диагностических параметров, характеризующих работоспособность основного фильтра, гидронасоса, распределителя и силовых цилиндров. Проверяют агрегаты гидросистемы после того, как внешним осмотром определена исправность всех маслопроводов, соединений, установлено опросом механизаторов либо опробованием гидросистемы в работе наличие признаков нарушения работоспособности системы. В случае обнаружения таких признаков диагностируют гидросистему в последовательности, обеспечивающей быстрое обнаружение возможных неисправностей. До проверки агрегатов простейшими методами определяют качество масла в гидросистеме.
Ресурсные параметры агрегатов гидросистемы, которые надо контролировать в первую очередь, — производительность масляного насоса и создаваемое им давление, гидравлическая плотность сопряжения корпус — рабочий поясок золотника распределителя, герметичность клапанов и уплотнений силового цилиндра. Так как все эти параметры влияют на функциональные параметры гидросистемы в целом, на скорость подъема навешенного орудия и его усадку в транспортном положении, то проверку общего состояния гидросистемы можно выполнять по таким параметрам.
|
|
При разных режимах работы гидросистемы проверяют ее герметичность и устраняют подтеки. Среднее время полного подъема и опускания навешенного орудия определяют (после прогрева масла в гидросистеме до 45—55°С) при максимальной частоте вращения коленчатого вала двигателя по среднему результату десяти подъемов, засекая время секундомером.
Чтобы проверить исправность гидроцилиндра, поднимают навешенную машину в транспортное положение и проверяют усадку штока гидроцилиндра за 30 мин. Усадка не должна превышать допускаемых значений. Она характеризует суммарные утечки масла через неплотности поршня гидроцилиндра и сопряжение золотника с корпусом распределителя.
Усадка штока, превышающая допускаемое значение, свидетельствует об износе уплотнительного кольца поршня. Разность усадок штока, измеренных при первой и второй проверках, характеризует нарушение гидравлической плотности сопряжения рабочих поясков золотника с корпусом.
|
|
Описанные методы проверки технического состояния гидросистемы имеют важные достоинства: не требуют применения специальных приборов, обеспечивают достаточную точность диагноза. Однако большая длительность и трудоемкость проверок ограничивают применимость их на практике. В связи с этим для диагностирования гидросистемы выпускают специальные приборы, применение которых в несколько раз уменьшает длительность и трудоемкость проверок.
Для проверки технического состояния агрегатов гидросистемы без снятия их с трактора используют прибор КИ-1097Б (дроссель-расходомер ДР-70) и приспособление КИ-6272 для отключения нагнетательного трубопровода от распределителя гидросистемы (рис. 1).
Дроссели-расходомеры для контроля гидросистемы выпускают со шкалой расходов, действительной для масел Дп-11, давления перед дросселем 10 МПа при температуре масла 50±5°С. Для проверки производительности гидронасосов при номинальном скоростном режиме двигателя и подключенном к гидросистеме приборе дросселем повышают давление в нагнетательной магистрали насоса до 10 МПа (контролируют по манометру прибора) и по отметке на шкале прибора напротив указателя определяют производительность. Шкалу расходов периодически контролируют на стендах для испытания агрегатов гидросистемы и корректируют ее изменением положения указателя.
|
|
При проверке насосов, номинальная производительность которых больше 1,5 л/с (тракторы К-700, К-701, Т-150К и др.), определяют производительность Q насоса при пониженной частоте вращения коленчатого вала или ВОМ, а полную производительность Qн вычисляют по формуле
Qн = Q nн / n см3/с, где nн — номинальная частота вращения коленчатого вала или ВОМ.
Рис. 1. Прибор КИ-1097Б для диагностирования агрегатов гидросистем:
1 – корпус; 2 – гильза; 3 – плунжер; 4 – стержень; 5 – стрелка; 6 – манометр;
7 – рукоятка дросселя; 8 – лимб; 9 – установочный винт.
|
Рис. 2. Схема подключения прибора КИ-1097Б и приспособления КИ-0272 для проверки состояния агрегатов гидросистемы:
1 - насос; 2 — прибор КИ-1097Б; 3 — приспособление КИ-6272; 4 — запорное устройство; 5 — распределитель; 6, 7 — трубопроводы; 8 — гидроцилиндр;
9 — масштабная линейка; 10 — шток; 11 — поршень; 12 — бак гидросистемы.
Для определения гидравлической плотности сопряжений рабочих поясков золотников с корпусом, шланг (рис. 2) отсоединяют от трубопровода 6 (его заглушают) и соединяют со свободным штуцером приспособления КИ-6272. Золотники остаются в нейтральном положении. Создав давление 10 МПа, фиксируют по линейке 9 перемещения штока гидроцилиндра за 5 мин. Оно не должно превышать 80 мм.
Чтобы проверить герметичность уплотнений гидроцилиндра, устанавливают поршень 11 в среднее положение, разъединяют запорное устройство трубопровода 7 (или отсоединяют шланг и на штуцер ставят заглушку). Переводят рукоятку золотника в положение «Подъем», создают давление 10 МПа и фиксируют по линейке 9 выход штока 10 из цилиндра за 3 мин. Перемещение штока в пределах 6-7,5 мм. Проверяют гидроувеличитель сцепного веса и другие агрегаты гидросистем тракторов методами, аналогичными описанным выше.
Загрязненность или неисправность фильтра гидросистемы проверяют по давлению масла в сливной магистрали (перед фильтром) с помощью приспособления, состоящего из манометра со шкалой до 0,6 МПа, переходного штуцера, шланга и наконечника с резиновым уплотнением (КИ-5472). В переходном штуцере установлено демпфирующее устройство для сглаживания пульсаций масла.
Проверяют состояние фильтра после прогрева масла в гидросистеме до 45—50°С. Для выполнения проверки наконечник приспособления соединяют с маслопроводом для выносного цилиндра, соединенного со сливной магистралью распределителя (запорное устройство отсоединяют). Рукоятку соответствующего золотника устанавливают в плавающее положение. При номинальной частоте вращения коленчатого вала определяют по манометру приспособления давление масла перед фильтром.
Как видно, большинство методов диагностирования гидросистемы основано на измерении характеристик рабочего потока жидкости (давления, расхода) измерительными устройствами и параметров движения исполнительного органа с помощью секундомера, линейки. При этом обязательный элемент диагностирования — загрузка гидросистемы или обычным рабочим способом, или дросселированием рабочего потока. Первый способ весьма трудоемкий, а дросселирование вызывает интенсивный нагрев жидкости. Как следствие этого возрастает погрешность измерения.
Перспективна разработка универсальных методов диагностирования агрегатов и узлов машин, реализуемых электронными измерительными устройствами, с использованием измерительных преобразователей (датчиков), не требующих внедрения в объект.
Контрольные вопросы
1. Перечислите возможные неисправности рулевого управления и способы их устранения
2. Как проводят диагностирование рулевого управления?
3. Опишите отказы и неисправности гидросистемы
4. Какие причины вызывают уменьшение КПД насоса НШ-32Л?
5. Как подсчитать объемный КПД насоса?
6. Как определить действительную производительность насоса?
7. Какая причина вызывает утечку масла свыше допустимой через зазоры золотниковой пары распределителя Р-75?
8. Что необходимо сделать, чтобы предохранительный клапан и клапан автомата золотника преждевременно не срабатывали?
9. Каким образом можно уменьшить (устранить) утечку масла через предохранительный и перепускной клапаны распределителя гидросистемы?
10. Что нужно сделать, если имеется течь масла в уплотнениях гидроцилиндра?
Задание 12
Дата добавления: 2020-01-07; просмотров: 1403; Мы поможем в написании вашей работы! |
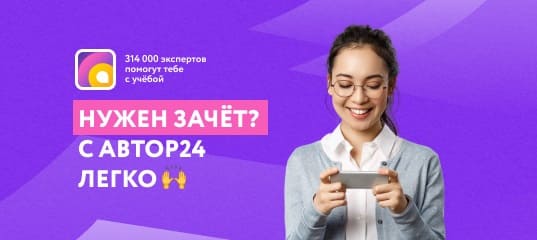
Мы поможем в написании ваших работ!