Техника безопасности при нарезании резьбы
· при нарезании резьбы вручную в заготовках с сильно выступающими острыми частями необходимо следить за тем, чтобы при повороте метчика с воротком не поранить руку;
· во избежание поломки метчика нельзя работать затупившимся метчиком, а при нарезании резьбы в глухих отверстиях следует чаще удалять стружку из отверстия;
· особую осторожность следует соблюдать при нарезании резьб малого диаметра (5мм и менее) во избежание поломки метчика;
· надеть спецодежду, волосы тщательно заправить под берет;
· прочно закреплять заготовку в тисках;
· при опиливании заготовок с острыми кромками нельзя поджимать пальцы левой руки под напильником при обратном ходе;
· во избежание травматизма верстак, тиски, рабочий и измерительный инструмент должны содержаться в порядке и храниться в надлежащих местах.
Изм. |
Лист |
№ докум. |
Подпись |
Дата |
Лист |
20 |
Слесарные работы |
Изм. |
Лист |
№ докум. |
Подпись |
Дата |
Лист |
21 |
Слесарные работы |
Клепка
Клепка – операция по соединению двух и более деталей с помощью заклепок. При этом образуется неразъемное соединение деталей. Широко применяется при изготовлении ферм, рам, балок, в самолетах и судостроении.
Соединяющей деталью является заклепка – цилиндрический стержень с закладной головкой.
|
|
Устанавливается в предварительно просверленное или пробитое отверстие всклепываемых деталях и ее выступающий цилиндрический цилиндр расклепывается вручную либо клепальными машинами (механизмами). При этом образуется замыкающая головка соединяющая деталь.
Заклепки бывают:
· С полукруглой высокой головкой
· С полукруглой низкой головкой
· С плоской потайной головкой
· С полупотайной головкой
Угол конуса головки в зависимости от диаметра заклепки может быть 60-900 .
Заклепки должны быть из того же материала, что и закрепляемый материал или близкий ему по свойствам.
Клепка разделяется на
· Холодную (выполняется без нагрева заклепок)
· Горячую (перед клепкой заклепку нагревают до 750-10000 С.
При ручной клепке для осаживания стержня заклепки используется кувалда или ручной клепальный пневматический молоток. Ручная клепка выполняется следующим образом. Клепальщик вставляет в буксу молотка наковальню-поддержку, затем в правую руку берет рукоятку молотка, одновременно левой рукой поддерживая его ствол, направляемый на расклепываемую заклепку. Прижав молоток к заклепке, клепальщик пускает его в работу.
Как правило, в процессе клепки участвуют два человека – клепальщик и его подручный. Подручный молотком меньшей мощности клепает с внутренней стороны, подбивая заклепку, а клепальщик в это время клепает с наружной стороны, заклепку осаживая. Таким образом достигается уплотнение листов и, как результат, высокое качество клепки.
|
|
В последнее время для выполнения клепки вместо клепального молотка и наковальни-поддержки все чаще применяются клепальные прессы с ЧПУ, которые позволяют увеличить производительность и автоматизировать процесс клепки.
Преимущества и недостатки заклепочных соединений
В число недостатков заклепочных соединений входят трудоемкость процесса, повышенная материалоемкость соединения, необходимость специальных мер для обеспечения герметичности, а также шум и вибрация, сопровождающие процесс. При этом заклепочные соединения препятствуют распространению усталостных трещин, повышая надежность всего изделия.
Еще одно преимущество – возможность соединения не поддающихся сварке материалов.
Техника безопасности при клепке.
· работать исправным инструментом
· на рабочем месте не держать ничего лишнего
· при регулировании пневматического инструмента нельзя пробовать молоток, придерживая обжимку руками, так как из-за большой силы удара удержать ее очень трудно, в результате могут быть повреждены руки.
|
|
· поддержку не следует сжимать в руках, ее лишь надо направлять на заклепку.
Клепка сопровождается резким стуком, вредно действующим на слух и нервную систему работающих и понижающим производительность труда.
Изм. |
Лист |
№ докум. |
Подпись |
Дата |
Лист |
22 |
Слесарные работы |
Изм. |
Лист |
№ докум. |
Подпись |
Дата |
Лист |
23 |
Слесарные работы |
Пайка — технологическая операция, применяемая для получения неразъёмного соединения деталей из различных материалов путём введения между этими деталями расплавленного металла (припоя).
Пайка металлов происходит за счет смачивания поверхностей заготовок жидким припоем, которым заполняется зазор между двумя металлическими изделиями.
|
|
В реализации пайки элементов важны припои.
Припой – это металл или сплав нескольких металлов, обычно олова и свинца.
Изготавливают их из чистых металлов или их сплавов. При выборе обращают внимание на две основные их характеристики: смачиваемость и температура плавления. Первое свойство – это сцепление припоя с заготовками, где прочность соединения между ними становится выше, чем между молекулами самого припойного материала.
Что касается температуры, то тут есть одно требование – температура плавления припойного металла должна быть ниже, чем тот же показатель у заготовок. Поэтому припойный материал делится на две категории: легкоплавкие и тугоплавкие.
Легкоплавкие – материалы на основе олова и свинца в чистом виде или с добавлением различных компонентов.
Тугоплавкие – материалы на основе серебра или меди. Это медно-цинковые припои, которыми можно паять медные, бронзовые и стальные заготовки.
Соединение с помощью пайки, без расплавления, дает возможность в будущем разъединить детали (распаять или перепаять заново), не нарушая их свойств. Качество пайки зависит от типов соединяемых металлов, от припоя и флюса, нагрева и вида соединения.
К преимуществам процесса пайки можно отнести:
· возможность соединять сталь с цветными металлами;
· высокая технологичность процесса;
· возможность проводить паяльные операции в труднодоступных и неудобных местах;
· возможность соединять сложные по конструкции узлы и детали;
· процесс можно проводить не точно по контуру соединения, а по всей плоскости;
· нагрев при пайке обеспечивает термическую обработку металлических заготовок.
Изм. |
Лист |
№ докум. |
Подпись |
Дата |
Лист |
24 |
Слесарные работы |
К недостаткам относится:
· невысокая прочность паяного соединения на отрыв и сдвиг за счет мягкости припойного металла (сложно проводить операции, которые касаются высокотемпературной технологии).
После сварки пайка находится на втором месте по применению в категории стыковки металлов. А в некоторых областях производства она занимает главенствующую позицию.
К примеру, в производстве компьютеров, сотовых телефонов и другой IT-ной техники. Ведь мельчайшие детали этой техники требуют компактного контакта между собой.
Техника безопасности при пайке:
· Проверить целостность шнура, штепсельной вилки и розетки.
· Проверить целостность самого паяльника, на наличие повреждений изоляции.
· Если при включении паяльника слышен треск - немедленно выключайте его.
· Не работать в помещениях с повышенной влажностью.
· Не работать влажными руками.
· При выключении не тянуть за провод.
· Держать паяльник только за ручку, избегая прикосновений к металлическим частям (очень высокая температура)
· Работать только в проветриваемом помещении.
· При пайке не наклоняться над паяльником ближе чем на 20 см. во избежание попадания брызг олова и горячих паров в глаза.
· Не работать вблизи горючих и легковоспламеняющихся предметов и на столах из горючих материалов без негорючей подставки.
· В перерывах между работой ставить паяльник только на подставку.
· Ни в коем случае не ронять даже выключенный паяльник.
· После окончания работы не прикасаться к жалу и корпусу паяльника до его полного остывания (15-30 минут).
Изм. |
Лист |
№ докум. |
Подпись |
Дата |
Лист |
25 |
Слесарные работы |
Шабрение — технология высокоточного (прецизионного) выравнивания поверхности изделия из металла (реже — из дерева или пластика) специальным режущим инструментом — шабером.
С помощью шабера с детали последовательно срезают тонкий слой металла (0,005– 0,01 мм). Шабрение обычно применяют для окончательной доводки вручную поверхностей при изготовлении или ремонте точных деталей: направляющих станин и суппортов металлорежущих станков, вкладышей подшипников, контрольно-измерительных плит, деталей приборов и инструмента и т.п, т.е. в тех случаях, когда нет необходимого оборудования или оно не может обеспечить обработку с требуемой точностью и шероховатостью.
Шабрение применяют, как правило, после обработки поверхностей деталей фрезой, резцом или напильником для лучшей отделки и получения более точных размеров, формы и расположения поверхностей детали.
Для шабрения различных поверхностей применяют шаберы цельные, составные, односторонние с деревянной ручкой и двусторонние без ручки, плоские, трехгранные, с прямолинейной и криволинейной кромкой.
Способы и приемы шабрения
При обработке плоской поверхности от себя шабер, удерживаемый правой рукой за рукоятку, устанавливают под углом 20–30° к поверхности, а левой рукой нажимают на конец шабера вблизи режущей кромки и двигают его вперед (рабочий ход) и назад (холостой ход). Для работы плоским прямым двусторонним шабером в правую ладонь руки берут жгут ветоши такой величины, чтобы пальцы могли смыкаться с большим пальцем, и в эту ветошь по центру ладони упирают при работе лезвие шабера, удерживая его в рабочем положении под углом 20–30° к поверхности пальцами правой руки. Левой рукой держат шабер за стержень, за цевье, прижимают к обрабатываемой поверхности и направляют его движение.
Техника безопасности
· обрабатываемая деталь должна быть надежно установлена и прочно закреплена;
· не допускается работа неисправными шаберами (без ручек или с треснувшими ручками);
· при выполнении работ шлифовальными головками соблюдать правила электробезопасности.
Изм. |
Лист |
№ докум. |
Подпись |
Дата |
Лист |
26 |
Слесарно-сборочные работы |
Слесарно-сборочные работы
Слесарные работы — обработка преимущественно металлических заготовок и изделий, осуществляемая слесарно сборочным инструментом вручную, с применением приспособлений и станочного оборудования.
Сборка является заключительным этапом в производственном процессе. Сборочный процесс, как правило, состоит из таких последовательных стадий:
· ручная слесарная обработка и подготовка отдельных деталей к сборке — зачистка заусенцев, снятие фасок и др. (применяется преимущественно в единичном и мелкосерийном производствах и в малых объемах — в серийном);
· узловая сборка — соединение деталей в комплекты, подузлы, агрегаты (механизмы);
· общая сборка — сборка всей машины;
· регулирование — установка и выверка правильности взаимодействия частей и испытание машины.
Технологический процесс сборки — это соединение деталей в сборочные единицы, а сборочных единиц и отдельных деталей — в механизмы (агрегаты) и машины.
Дата добавления: 2020-01-07; просмотров: 2561; Мы поможем в написании вашей работы! |
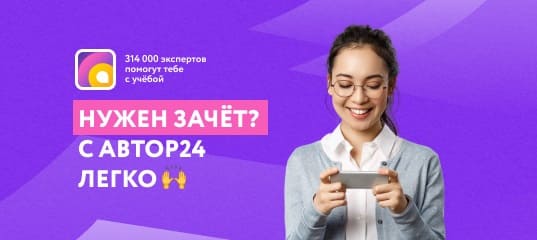
Мы поможем в написании ваших работ!