Критерии работоспособности валов
Основными критериями работоспособности валов являются прочность и жесткость.
Для расчета валов на прочность строят эпюры изгибающих и вращающих моментов, продольных сил. Валы при работе испытывают действие циклически изменяющихся напряжений.
Прочность оценивают коэффициентами запаса прочности S Т при расчете валов на статическую прочность и S – на сопротивление усталости, а жесткость – прогибом, углами поворота или углами закручивания в местах установки деталей.
Практикой установлено, что разрушение валов и осей быстроходных машин в большинстве носит усталостный характер, поэтому основным является расчет на сопротивление усталости.
Основными расчетными силовыми факторами являются вращающие Т и изгибающие М моменты. Влияние растягивающих и сжимающих сил на прочность мало и их в большинстве случаев не учитывают.
Проектировочный расчет валов
Проектировочный расчет валов выполняют на статическую прочность с целью ориентировочного определения диаметровотдельных ступеней. В начале расчета известен только вращающий момент Т. Значения изгибающих моментов можно определить лишь после разработки конструкции вала, когда согласно общей компоновке выявляют его длину и места приложения действующих нагрузок. Поэтому проектировочный расчет вала выполняют условно только на кручение, а неучитываемое влияние на прочность вала изгиба, концентрации напряжений и характера нагрузки компенсируют понижением допускаемого напряжения на кручение.
|
|
Для валов из сталей марок Ст5, Ст6, 45 принимают: =20…28 МПа при определении диаметра выходного конца быстроходного или тихоходного вала;
=14…20 МПа – диаметра участка промежуточного вала в месте установки зубчатого колеса.
Начинают проектирование быстроходного или тихоходного вала с ориентировочного определения диаметра выходного конца из расчёта на чистое кручение по пониженному допускаемому напряжению без учёта влияния изгиба:
d , (7.1)
где Т – вращающий момент, действующий в расчетном сечении вала, Нм;
– допускаемое напряжение на кручение, МПа.
Полученный диаметр вала округляют до ближайшего значения из ряда нормальных линейных размеров R40: 10; 10,5; 11; 11,5; 12; 13; 14; 15; 16; 17; 18; 19; 20; 21; 22; 24; 25; 26; 28; 30; 32; 34; 36; 38; 40; 42; 45; 48; 50; 52; 55; 60; 63; 65; 70; 75; 80; 85; 90; 95; 100; 105; 110; 120; 125; 130; 140; 150; 160.
Примечание. В случае необходимости допускаются размеры: в интервале 12 до 26 мм – кратные 0,5; в интервале 26 до 30 – целые числа; в интервале 50 до 120 – размер 115 и размеры, оканчивающиеся на 2 и 8; в интервале 120 до 160 – кратные 5.
Диаметр выходного конца вала редуктора не должен отличаться от диаметра вала электродвигателя больше чем на 20%. При выполнении этого условия соединение валов осуществляют стандартной муфтой. Диаметры других участков назначают при разработке конструкции вала с учетом их функционального назначения, технологии изготовления и сборки. При этом могут быть использованы эмпирические зависимости. Так, диаметры шеек коленчатых валов определяют по эмпирическим формулам в зависимости от диаметра цилиндра двигателя; диаметры шпинделей станков – в зависимости от основного геометрического размера сианка и т.д.
|
|
При проектировании промежуточного валадвух- или трехступенчатого редуктора обычно первоначально определяют диаметр в месте посадки зубчатого колеса по формуле (7.1.). Остальные диаметры также назначают по конструктивным соображениям
Диаметры валов в местах посадок сопряженных с валом деталей должны быть взяты из стандартного ряда нормальных линейных размеров. При назначении диаметров цапф под подшипники следует помнить, что диаметры внутренних колец подшипников качения более 20 мм кратны 5.
Дата добавления: 2019-09-13; просмотров: 563; Мы поможем в написании вашей работы! |
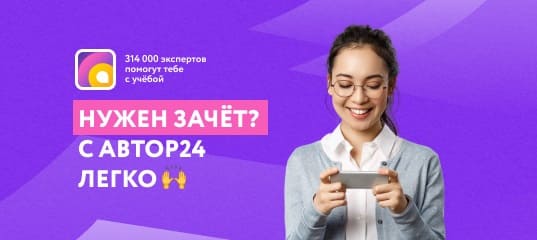
Мы поможем в написании ваших работ!