Сушка воздухонагревателей и доменной печи
Сушка доменной печи и блока воздухонагревателей производится после испытания их на плотность и после установки всей аппаратуры.
Для удаления влаги из огнеупорной кладки необходимо нагреть кладку до температур 100-165 оС.
Разогревать воздухонагреватель нужно постепенно, особенно в том случае, когда верхние ряды кладки и насадки выложены динасовым огнеупором. В этом случае необходимо учесть модификационный рост динасового кирпича в температурных интервалах 100-168 °С и 180-300 °С, а также кварцевый эффект при температуре 573 °С. Поэтому подъем температуры в интервалах 100-300 °С и 550-600 °С не должен превышать 10 град/ч и при дальнейшем разогреве огнеупорной кладки должны быть исключены случаи снижения температуры ниже 300 °С. Обычно продолжительность сушки и разогрева воздухонагревателей составляет около 7 суток.
Огнеупорная кладка доменной печи содержит значительное количество влаги. При сушке печи влага удаляется через колошник. Однако, часть влаги, поступая в еще не нагретые зоны, конденсируется, что может вызвать размывание растворов, которым скрепляется кладка. В том случае, когда влага конденсируется в толще углеродистой лещади, разрушение лещади возможно за счет взаимодействия углерода кладки с парами воды, а также с водородом, получающимся при разложении влаги:
Согн + Н2О = СО + Н2,
Согн + 2Н2 = СН4.
|
|
Для облегчения удаления влаги из лещади сушка ее производится по мере кладки каждого ряда с помощью электронагревательных устройств.
Наиболее удобным, безопасным и дешевым способом сушки доменной печи является ее сушка горячим воздухом. Поэтому сушка воздухонагревателей должна быть закончена ранее - до сушки печи.
Для направления нагретого воздуха на лещадь, на воздушные фурмы устанавливают трубы (чаще всего диаметром 160 мм) из листового железа. Они направляются вниз под углом 90° и не доходят до лещади примерно на 1 метр. Чугунная летка закладывается кирпичом. Большой конус закрывается, открываются свечи на газоотводах и свечи на пылеуловителях. Сушка доменной печи осуществляется по следующему графику: постепенный разогрев до 600 °С в течение 2 суток, выдержка при этой температуре в течение 1,5 суток и естественное охлаждение (обычно около 1,5 суток).
Задувочная шихта и другие параметры задувки
К задувочной шихте предъявляются особые требования. Они состоят в следующем.
1. Железорудные материалы, входящие в состав задувочных шихт, должны быть легковосстановимыми. Это очень важно для снижения степени прямого восстановления в процессе задувки печи и снижения удельного расхода кокса.
|
|
2. Шихтовые материалы должны быть прочными, поскольку загрузка материалов в печь осуществляется с большой высоты, что может вызвать увеличение мелких фракций шихты и вероятность ее подвисаний в процессе задувки, что является недопустимым.
3. Количество мелочи (фракции менее 5 мм) в железорудном материале должно быть минимальным. Это обусловлено вышеуказанными причинами.
4. Кокс, входящий в состав задувочной шихты, должен быть малосернистым. Это, как будет показано ниже, связано с большим расходом кокса в задувочной шихте, что делает проблематичным получение чугуна, кондиционного по содержанию серы.
5. Шихтовые материалы должны содержать минимальное количество гигроскопической влаги. Это связано с тем, что испарение влаги из шихты в процессе задувки в отличие от обычного режима доменной плавки происходит с дополнительными затратами тепла и возрастанием расхода кокса.
Задувочную шихту характеризует прежде всего высокий удельный расход кокса. Это связано с необходимостью разогрева как столба шихты, так и огнеупорной кладки до рабочих температур. Кроме того, первоначально процессы восстановления оксидов железа происходят прямым путем, что требует затрат тепла и дополнительного расхода кокса. Поэтому удельный расход кокса в задувочной шихте достигает 2 т/т чугуна, а при задувке печи на холодном дутье он может увеличиваться и до 3 т/т.
|
|
Задувочная шихта рассчитывается на получение литейных чугунов с содержанием кремния 1,5-3,0 %. Это объясняется рядом причин. Во-первых, при расчете задувочных шихт возможны ошибки в определении удельного расхода кокса. В том случае, когда расход кокса оказывается заниженным, то получаются чугуны с заниженным содержанием кремния. Напротив, при повышенном нагреве горна (завышенном расходе кокса) в период задувки получаются литейные чугуны с высоким содержанием кремния. Во-вторых, при плавке литейного чугуна происходит графитизация огнеупорной кладки и образование устойчивого гарниссажа.
Задувочная шихта рассчитывается на основность шлака CaO / SiO 2 = 0,8-1,1. Несмотря на высокое содержание серы в задувочной шихте, увеличение основности шлака сверх указанной считается нецелесообразным из-за возрастания температур его плавления, а также из-за того, что основные шлаки относятся к типу “коротких”, все это может способствовать образованию настылей в начальный период работы доменной печи.
|
|
Задувочная шихта часто состоит из 4-5 шихт, каждая из которых обеспечивает заполнение определенного объема печи.
Имеется так называемая нулевая шихта. Она состоит только из кокса, не принимает участия в процессе горения и играет роль дренажной коксовой насадки. Этой шихтой заполняются рабочее пространство до верхней части распара..
Первая шихта состоит из кокса, известняка и шлакообразующих. Известняк загружается в количестве, необходимом для ошлакования золы кокса этой шихты с заданной основностью. В эту шихту необходим ввод шлакообразующих для снижения концентрации глинозема в шлаке, повышенная концентрация которого обусловлена составом золы кокса. Без ввода шлакообразующих возможно повышение содержания в шлаке А l 2 O 3 свыше 17 %, что делает шлаки тугоплавкими и вязкими. В качестве шлакообразующих материалов используется доменный шлак, кварцит, железные руды. Первая шихта заполняет рабочее пространство примерно до середины шахты печи.
Вторая и последующие шихты помимо кокса и флюсующего материала включают и железорудный материал. Рудная нагрузка в каждой последующей загружаемой в печь шихте постепенно возрастает.
В последнее время появляются новые технологии задувки доменных печей. Так, согласно работе Б.Ф. Чернобривца, В.В. Капорулина и В.А. Завидонского, помимо “нулевой” шихты нужно загружать только две: первая из них должна быть представлена только коксом (без известняка и шлакообразующих), а вторая шихта включает в себя все компоненты и загружается в печь с не изменяющейся по высоте рудной нагрузкой, характерной для нормального технологического режима. Высота загружаемой в печь первой шихты должна быть не менее 10 метров и не должна содержать известняка и шлакообразующих. Этим, по мнению авторов работы, достигаются две цели: первая заключается в том, чтобы исключить приход в нижнюю часть железистого шлака и исключить вероятность его замораживания на коксовой насадке (для этого достаточно иметь слой шихты до 10 метров), а вторая – избежать раннего шлакообразования, предупредить приход в горн печи холодного шлака и исключить имеющиеся случаи затруднений с выпуском первых порций образовавшихся расплавов чугуна и шлака. Пример расположения задувочных шихт приводится на рис.10
Рассчитанную задувочную шихту проверяют, для чего по полученному конечному составу шлака определяют температуру его плавления, вязкость и устойчивость по диаграммам состояния шлаковых систем.
![]() |
Рис.10
К сожалению, следует отметить, что в настоящее время строгой, научно обоснованной методики расчета задувочных шихт нет. Технологический персонал доменных цехов пользуется в таких случаях приблизительными расчетами, которые основаны на практике задувки доменных печей других металлургических предприятий или же ранее задутых печей в своем цехе. Это приводит порой к необоснованным расходам кокса, что сопровождается часто перегревом горна печи, к значительному превышению содержания кремния в чугуне относительно заданного, к возникновению термических ударов на огнеупорную кладку и т.п.
Дата добавления: 2019-09-13; просмотров: 209; Мы поможем в написании вашей работы! |
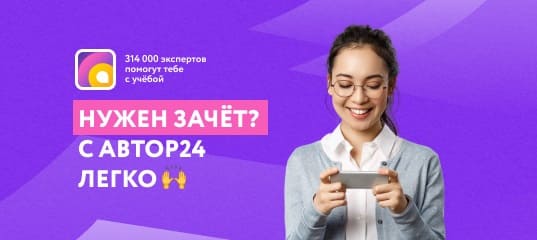
Мы поможем в написании ваших работ!