Обёрточная ткань для ремней должна обеспечить высокое трение между ремнем и шкивом
Билет 3
Плоские приводные ремни. Назначение, условия работы, конструкция. Характеристика применяемых материалов – резин и армирующих материалов. Основные стадии технологического процесса их изготовления.
Приводной ремень — элемент ременной передачи, рабочая деталь машин и механизмов, которая служит для передачи крутящего момента. Передача крутящего момента происходит за счёт сил трения.
Ременный привод служит для передачи энергии вращения через гибкую связь от шкивов двигателей к исполнительным органам.
Плоские ремни являются наиболее простым примером приводных ремней. Они имеют постоянную форму сечения без выступов и впадин и обладают хорошими эксплуатационными характеристиками: высокой тяговой способностью, достаточной прочностью и гибкостью, высоким коэффициентом трения, обеспечивающим работоспособность плоскоременной передачи.
Плоскоременная передача наиболее проста, может работать при высоких скоростях и вследствие большой гибкости ремня обладает сравнительно высокими долговечностью и КПД.
Плоскоременные передачи предпочтительны при больших межосевых расстояниях; они сравнительно дешевы, ремни их обладают большой гибкостью и повышенной долговечностью, шкивы просты по конструкции. Плоскоременные передачи применяют при скоростях ремня до 100 м/с.
Рис.. Типы плоскоременных передач
1. Открытые - наиболее распространенные (рис. а);
|
|
2. Перекрестные - повышенный износ от взаимного трения ремней (рис., б). Используются редко.
3. Передача с натяжным роликом - в настоящее время заменяется клиноременной (рис., в).
Плоские приводные резинотканевые ремни прямоугольного сечения получили большое распространение
Достоинства: Плоские ремни – ремни с гибкой связью, нет потребности в смазке, низкий уровень шума. Передают крутящий момент вращения за счет трения о поверхность шкивов.
Такие ремни приводные применяются при передаче больших мощностей (1000 кВт-1500 кВт) и способны работать на больших скоростях вращения (до 100 м/с). Материал, из которого изготовлены приводные ремни, может отличаться высокой стойкостью к воздействию химических веществ (масла, бензина, ацетона, жиров). Плоские ремни имеют высокий показатель эластичности и могут использоваться в приводах, работающих с несколькими шкивами одновременно. Плоская лента при малой толщине обладает высокой гибкостью и испытывает малые напряжения при изгибах и деформациях
К недостаткам плоских ремней можно отнести непостоянство передаточного отношения при перегрузках из-за проскальзывания ремня вдоль шкива. Необходимость обеспечивать значительное усилие натяжения для формирования силы трения, в результате снижается срок эксплуатации ленты. Кроме этого, под значительной нагрузкой работают ведущий и ведомый валы, подшипниковые блоки имеют значительный износ.
|
|
Плоские приводные ремни нашли применение в бытовых приборах: центробежных и пневматических насосах, генераторах. В промышленности такие ремни используются в приводах различных станков: шлифовальных, сверлильных, токарных, шипорезных, а также в ткацких и прядильных станках, пилорамах и деревообрабатывающих установках, в сельхозтехнике. Они применяются в приводах промышленного оборудования и сельскохозяйственных машинах при скоростях до 30 м/с.
Плоские приводные ремни характеризуются шириной ремня, числом прокладок (или толщиной ремня) и номинальной прочностью (на основе) ткани каркаса.
Ремни могут изготавливаться как конечными, так и бесконечными.
Конечные ремни выпускают обычно в виде рулонов длиной 50 м и более. Их устанавливают во всех случаях, когда по условиям работы допускается сшивка ремня.
В условиях эксплуатации основные усилия, испытываемые ремнем, действуют вдоль него, поэтому долговечность ремня в первую очередь зависит от его прочности в долевом направлении.
|
|
Для высокоскоростных передач предназначены бесконечные ремни из специальных тканей на основе синтетических волокон.
Общие требования, которые предъявляются к материалам приводных ремней, следующие: достаточно высокое сопротивление усталости, статическая прочность и износостойкость, высокий коэффициент трения, эластичность (малая жесткость при растяжении и изгибе).
Плоские ремни изготовляют различной ширины, конструкции и из различных материалов: хлопчатобумажных, прорезиненных, шерстяных тканей, кожи. Выбор материала для ремней зависит от условий работы (атмосферные влияния, вредные пары, температурные изменения, ударные нагрузки и т.п.) и тяговой способностью.
Типы плоских ремней .
Прорезиненные ремни - состоят из нескольких слоев хлопчатобумажной ткани — прокладок, связанных вулканизированной резиной.
Ткань передает основную часть нагрузки, а резина предохраняет ткань от повреждений и повышает коэффициент трения. Будучи прочными, эластичными, малочувствительными к влаге прорезиненные ремни получили большое применение для широкого диапазона мощностей при передаче спокойных нагрузок. Эти ремни непригодны в помещениях с повышенным содержанием паров нефтепродуктов, которые разрушают резину.
|
|
Прорезиненные ремни выпускаются трех типов:
- ремни типа А — нарезанные, с резиновыми прослойками между тканевыми прокладками (рис, А). Рекомендуются для шкивов малого диаметра и при v<=30 м/сек;
- ремни типа Б — послойно завернутые с прослойками или без прослоек между прокладками (рис. , Б). Рекомендуются для тяжелых условий работы при v<=20 м/сек;
- ремни типа В — спирально завернутые из одного куска ткани, без резиновых прослоек (рис., В). Рекомендуются для небольших нагрузок при v<=15 м/сек.
Прорезиненные ремни всех типов могут иметь резиновые обкладки для работы в сырых помещениях.
Самыми распространенными являются прорезиненные ремни, состоящие из нескольких слоев хлопчатобумажной ткани, связанных между собой вулканизированной резиной. Резиновые прослойки повышают гибкость ремней и коэффициент трения между ремнем и шкивами. Ткань обеспечивает прочность и долговечность.
Ремни плоские резинотканевые изготавливаются на основе тканей БКНЛ-65 (полиэфир/хлопок),ТК-200-2(из капроновых нитей),ТА-150,ТК-300 (из анидных нитей) изготавливают с внутренними тканевыми прокладками (от 3 до 6) и с наружными резиновыми обкладками (одной или двумя), а также без резиновых обкладок (рис.).
Рис.. Конструкция прорезиненного ремня: 1 – резиновая обкладка; 2 – тканевый каркас (тканевые прокладки); 3 – резиновая прослойка
Ремни выпускают нарезной конструкции, т. е. из целикового вулканизированного резинотканевого полотна нарезают ремни заданной ширины.
По назначению различают следующие плоские резинотканевые ремни:
• общего назначения (диапазон рабочих температур от 25 С до +60 С);
• морозостойкие (диапазон рабочих температур от 45 С до +60 С);
• антистатические (понижающее статическую электризацию химических волокон, резин) (диапазон рабочих температур от 45 С до +60 С).
Ремни на основе тканей из комбинированных нитей допускается изготовлять без резиновых прослоек. Морозостойкие и антистатические ремни должны изготавливаться с наружными резиновыми обкладками.
Ремни общего назначения изготавливаются как с наружными резиновыми обкладками, так и без резиновых обкладок.
Прорезиненные бесконечные приводные ремни (ширина от 20 мм до 1200 мм) состоят из кордового шнура или прочной ткани, связанных вулканизированной резиной. Плоские бесконечные ремни делятся на кордшнуровые и кордтканевые.
Кордшнуровые - более гибкие, поэтому их используют в передачах с малыми диаметрами шкивов, где они имеют большую долговечность.
Кордшнуровые ремни (рис.) состоят из несущего слоя, содержащего один ряд синтетического кордшнура 3, связующей резины 2 и тканевых обкладок 1.
Корд – прочная крученая нить из хлопчатобумажного или искусственного волокна. Кордшнуровые ремни выпускаются трех типов: I с односторонней тканевой обкладкой, II с двусторонней обкладкой и III без обкладки. Ремни прорезиненные с кордшнуровым несущим слоем рекомендуется применять как среднескоростные, так и быстроходные при скорости не выше 40 м/с.
Кордтканевые плоские бесконечные ремни (рис.) производятся с внутренними тканевыми прокладками (от 3 до 6) и наружными резиновыми обкладками (одной или двумя) или без резиновых обкладок. Ремни состоят из нескольких (обычно до шести) слоев обрезиненной ткани на основе комбинированных нитей (хлопок с лавсаном) или капроновой ткани.
1 – обертка (обкладка)
2 - резиновый слой (растяжение, сжатие, эластичность)
3 - несущий слой (кордшнур для ремней кордшнуровой конструкции или тканевый каркас для ремней кордтканевой конструкции)
В производстве плоских приводных ремней используют три типа резиновых смесей: для каркаса (промазочные), прослоечные (сквиджевые) и обкладочные.
Промазочная смесь – должна быть пластичной (мягкой), чтобы легко обеспечить глубокое проникновение между нитями ткани, клейкой – для лучшего сцепления с другими частями ленты. Смесь не должна быть очень липкой.
Необходимая клейкость достигается использованием каучука изопренового СКИ-3 или его смесей с бутадиен-стирольным (СКМС-30АРКМ-15), а также применением спец. компонентов в рецептуре.
Резиновая смесь для прослоек – должна обеспечить сцепление обрезиненных тканевых слоев, предохранять прокладки от быстрого истирания, воздействия влаги, обеспечить гибкость изделия. В соответствии с эти резиновая смесь должна иметь хорошие технологические свойства (хорошо каландроваться), обладать достаточной клейкостью, эластичностью, хорошим сопротивлением многократному изгибу.
Резина для обкладки должна иметь повышенную износостойкость при большой прочности при растяжении. Резиновая обкладка защищает каркас от атмосферных, механических, термических и др. воздействий, н-р, ударные нагрузки, порезы и др.
Обёрточная ткань для ремней должна обеспечить высокое трение между ремнем и шкивом
Обкладочные резины изготавливают из СКИ-3 и СКД, применяют смеси на основе БСК (бутадиенстирольный) или комбинированные – БСК +СКИ.
Конструкция и технология изготовления плоских приводных ремней аналогичны таковым для конвейерных лент.
Основные операции:
1) изготовление резиновых смесей, клеевых и пропиточных составов (резиносмеситель, вальцы, охлаждающая установка)
Резиновые смеси изготавливают в резиносмесителях РСВД-250-20 в комплекте с смесительными вальцами См 2100x660 с переменной фрикцией. Использование таких вальцев связано с особенностями переработки резиновых смесей с волокнистым наполнителем, которые имеют тенденцию перехода на задний быстроходный валок. Большинство зарубежных фирм применяют резиносмесители типа «Бенбери» с емкостью загрузочной камеры 140-250 л и частотой вращения ротора 20-40 мин-1. Для качественного охлаждения резиновых смесей после листовальных вальцев применяют специальные установки, работающие в комплекте с вальцами, фестонная установка УФТ-15, охлаждающая путем обдува воздухом и орошения антиадгезионным составом резиновой ленты, срезанной с листовальных вальцев.
2) Каландрование резиновых смесей. Резиновые смеси для слоев сжатия, растяжения и эластичного каландруют на каландрах с количеством валков от двух до четырех. Чаще применяют трехвалковые каландры. Скорость каландрования 8-10 м/мин. В зависимости от конструкций сердечников ремней каландрованные резиновые смеси выпускают разной толщины. Основными требованиями к качеству каландрованного полотна являются соблюдение равномерности калибра по длине и ширине полотна, обеспечение хорошего качества поверхности, качественное охлаждение полотна и намотка в холст с минимальным колебанием ширины закатки
3) Пропитка, сушка ткани
Сначала производят пропитку тканей. Параметры процесса пропитки зависят от типа волокна и структуры ткани.
Для того чтобы ткани не набирали влагу после пропитки их следует хранить в термокамерах при температуре 50-70 °С, что позволяет избегать их просушивания на сушильных машинах. В тканях, хранившихся длительное время, содержание влаги не должно превышать 2 % для полиамидных и 7 % для вискозных.
Сушка ткани из искусств. и хим. волокон, поступающей из пропиточной ванны, проводится в конвективных воздушных сушилках, воздух для которых подогревают паровыми калориферами. Удаление избытка состава с поверхности ткани, прошедшей пропиточную ванну, проводят скребками, обжимными валками, вакуум-отсосом или сдувом струей воздуха. Температура сушки обычно составляет 130–160°С.
Для снижения усадки ткани из химических волокон после пропитки и сушки ее подвергают термической обработке и нормализации. Сущность термической обработки состоит в фиксации полученного удлинения ткани под действием высокой температуры.
Ткани из хлопкосодержащих и комбинированных нитей сушат и обрезинивают с обеих сторон, а в отдельных случаях на промазанную ткань накладывают резиновую прослойку.
Сушку тканей-суровья (бельтинг), содержащих хлопок, производят, пропуская их через несколько барабанов, обогреваемых паром, и затем закатывают в рулон. Ткани сушат в сушильных агрегатах из барабанов при 80–100°С.
Промазанный с двух сторон бельтинг (хлопчатобумажная ткань повышенной прочности) поступает в цех изготовления ремней.
Наиболее совершенной отечественной линией для пропитки, сушки и термообработки кордшнуров из полиэфирных и полиамидных волокон является линия ЛН-24 , состоящая из закаточного и раскаточного устройства; устройства для контроля натяжения; пропиточные ванны; камера термофиксации; камера сушки и термовытяжки. Линия ЛН-24 обрабатывает одновременно 24 кордшнура со скоростью 60 м/мин. Толщина их от 0,8 до 3,0 мм; вытяжка кордшнуров обеспечивается в первой термокамере до 10, во второй - до 7 %. Максимальная температура в термокамерах может достигать 230°С, нагрев воздуха осуществляется электрокалориферами. Операции сушки и термообработки в агрегате совмещены, в связи с чем он имеет не три, а две термокамеры: камеру сушки и термовытяжки и камеру термофиксации. Пропитку кордшнуров можно производить двумя пропиточными составами, для чего в линии имеются две ванны для пропитки. После второй пропитки шнур сушат ИК-лампами.
3) Обкладка и промазка тканей
При помощи электротельфера рулон промазанного бельтинга подвешивают в раскаточные стойки каландра.
Нанесение резиновых прослоек на ткань осуществляется на трех- или четырехвалковых каландрах на линиях, включающих питающие машины (червячные машины холодного питания или вальцы). В это время на вальцах разогревают резиновую смесь для наложения резиновых прослоек (сквидж). Вручную раскатывается рулон бельтинга и заправляется в зазор между средними и нижними валками каландра для наложения прослоек. Толщина прослойки определяется зазором каландра (0,3 - 1 мм).
При обкладке или наложении резиновой прослойки ткань одновременно с разогретой резиновой смесью пропускают через зазор каландра.
Обкладку тканей осуществляют на агрегатах с четырехвалковым каландром с Г-образным расположением валков
На качество обработанной ткани оказывают влияние пластоэластические свойства резиновой смеси, температуры валков каландра и поступающей смеси, равномерность питания зазоров смесью, запас ее в зазоре, скорость обрезинивания, наличие устройств, регулирующие зазоры между валками и компенсирующих прогибы валков.
Температура валков каландра зависит от состава промазочной резиновой смеси. Обычно температура среднего валка выше температуры двух других валков. Например, температура нижнего, среднего и верхнего валков составляет 60, 85 и 70°С. Скорость промазки – 30–40 м/мин.
Наложение двухсторонней резиновой прослойки на пропитанную ткань обычно проводят на четырехвалковом каландре за один проход.
После обрезинивания полотно имеет толщину 1-1.3 мм в зависимости от типа ткани.
4) Сборка каркаса лент и обкладка каркаса.
Обрезиненная ткань поступает на сборку сердечника, т. е. путем дублирования создается многослойная конструкция. Сборка сердечника (каркаса) осуществляется на дублирующих агрегатах либо с параллельной подачей всех слоев, входящих в конструкцию, в зазор между дублирующими валками, либо с послойной (последовательной) намоткой слоев бесконечного браслета, располагающегося в петлях дублирующего агрегата (дублера Чижова), до заданного количества. После дублера, при необходимости, сердечник на каландровой линии обкладывается слоями резины и направляется (как с обкладкой, так и без обкладки) на вулканизацию
Многопетлевые сборочные агрегаты (дублеры) устанавливаются в одной линии с каландрами для обрезинивания тканей или для наложения резиновой прослойки.
5) Вулканизация ремневых пластин и вытяжка заготовки
производится в гидравлическом вулканизационном прессе длиной участков 8-10м (соответствуют длине пресса) при температуре ~150°С (143-151°С)
Режим вулканизации зависит от рецептуры смеси и количества прокладок в среднем 10-20мин)
Удельное давление на плите пресса -10-15∙105 Па (ремни -3-5 прокладки), для ремней большей толщины - 20-30∙105 Па.
Излишне высокое давление может привести к выдавливанию резиновой смеси из ремневой заготовки.
После вулканизации вулканизированный участок вытягивают с помощью растяжного приспособления (2-4% для бельтинга, 4-6% для уточно-шнуровой ткани).
Вытяжкой достигается распрямление прокладок, выравнивание их натяжения и и уменьшение остаточного удлинения в готовом изделии)
Вулканизированные пластины проходят вылежку 2-4 часа, затем подаются на резку.
Последующие участки пластин вулканизируют аналогично.
6) Резка пластин на ремни
продольная резка ремней – пластина раскатывается между валками обложенной резиной, проходит через рад параллельно расположенных ножей через определенное расстояние.
Дата добавления: 2019-09-13; просмотров: 525; Мы поможем в написании вашей работы! |
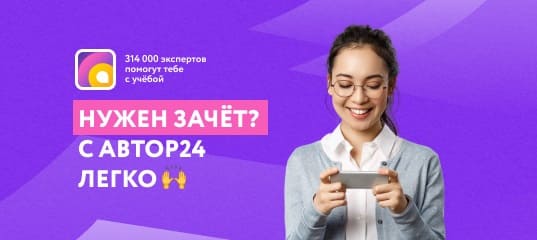
Мы поможем в написании ваших работ!