ГЛАВА 7. ПЕРЕМЕШИВАНИЕ МАТЕРИАЛОВ
Общие сведения
Перемешивание материалов широко применяется в химической промышленности для интенсификации химических, тепловых и массоббменных процессов, а также для приготовления растворов, эмульсий и суспензий. В ряде химических производств возни-, кает также необходимость в смешении сыпучих материалов, сос-
|
^(или nc / fij , |
Рис. 62. Способы перемешивания жидких сред:
-механической мешалкой, б —пневматическое перемешивание, циркуляционным насосом
тоящих из частиц различного размера, и смешении различных паст. Необходимость такой обработки возникает как при проведении подготовительных операций перед осуществлением химического взаимодействия, так и в заключительной стадии производства-;-при доведении продуктов до определенных товарных кондиций, обеспечивающих выполнение требований ГОСТов и технических условий. Подобные конечные операции выполняются при обработке красителей, лакокрасочной продукции и пр.
Перемещивание в гомогенных и гетерогенных системах всегда приводит к увеличению скорости химических, тепловых и массооб-менных процессов, так как с увеличением турбулентности улучшат ются условия подвода теплоты ил« вещества к поверхности теплообмена или границе раздела фаз. Это достигается в результате уменьшения толщины пограничного слоя, увеличения и непрерывного обновления поверхности раздела взаимодействующих фаз.
|
|
При приготовлении растворов или суспензий, нагревании или охлаждении перемещивание проводится с целью выравнивания-температур и концентраций в объеме аппаратов, что также интенсифицируют происходящие процессы:
sa
Способы перемешивания и аппаратура для проведения этого! процесса зависят от агрегатного состояния перемешиваемых матё»1 риалов. Широкое распространение в химической промышленности! получили процессы смешения в жидких средах. Независимо ота того, какая среда смешивается с жидкостью—газ, жидкость или! твердое сыпучее вещество, различают'два основных способа пере-1
а) |
б) |
|
мешивания в жидких средах — механическое] перемешивание (рис. 62, а) с помощью меша-;? лок различных конструкций и пневматическое.-' НЕОГЕН перемешивание сжатым воздухом или инерт-' ным газом (рис. 62, б). Кроме того, применяют перемешивание с помощью циркуляцион- ■ ных насосов или сопл (рис. 62, в).
Наиболее важными характеристиками перемешивающих устройств являются зффек- ■ тивность перемешивающего устройства и ин- ■ Рис 63. Типы меха- тенсивность его действия. Эффективность пе-« ннческих мешалок. ремешивания характеризуется равномерностью
л — лопастная, о —про- г „ ,
|
|
пеллерная распределения дисперсной фазы и зависит не
только от конструкции перемешивающего устройства, но и от количества затрачиваемой энергии. Интенсивность перемешивания определяется временем достижения заданного результата. Чем выше интенсивность, тем меньше времени требуется для достижения равномерного распределения дисперсной, фазы и тем выше производительность аппарата. N
Перемешивание в жидких средах
При механическом перемешивании механическая энергия передается жидкости с помощью мешалки. Мешалка, которая закреплена на вертикальном валу, служит рабочим элементом аппарата-смесителя (рис. 62, а). Привод мешалки осуществляется непосредственно от электродвигателя либо через редуктор или 'клиноремен-ную передачу. По устройству лопастей различают лопастные, пропеллерные и турбинные мешалки.
Лопастные мешалки (рис. 63, а) представляют собой ус-тройства, состоящие из двух или большего числа лопастей прямоугольной формы, закрепленных на вращающемся валу. Основное достоинство лопастных мешалок состоит в простоте и невысокой стоимости изготовления. Недостатком является неполное перемешивание жидкости в объеме аппарата вследствие слабого потока жидкости вдоль оси мешалки. Лопастные мешалки перемешивают только те слои жидкости, которые находятся в непосредственной близости от лопастей. Лопастные мешалки нельзя применять для перемешивания вязких жидкостей. Пропеллерные мешалки (рис. 63, б) осуществляют более интенсивное перемешивание. Для создания осевого перемещения жидкости при перемешивании лопастными мешалками и перемешивания всего объема жидкости применяются однорядные мешалки с наклонными лопастями (рис. 64, а) снакло-
|
|
84
ном лопастей 30—40° к оси вала и многорядные двухлопастные мешалки (рис. 64, б). Расстояние между отдельными рядами лопастей составляет приблизительно половину диаметра мешалки.
Основные размеры лопастных мешалок: диаметр мешалки d = = (0,64-0,9)1); ширина лопасти b = (0,1h-0,2)D; расстояние от дна сосуда h ^.0,3 D , где D — внутренний диаметр аппарата.
|
К лопастным относятся также якорные, рамные и листовые мешалки. Рамные и якорные мешалки • (рис. 65, а, б) имеют диаметр и форму, близкие к внутреннему диаметру и внутренней форме аппарата. При вращении эти мешалки очищают стенки и дно аппарата от налипающих загрязнений.
|
|
V |
") |
Рис. 64. Лопастные мешалки: |
а — однородйая, б — трехряд» иая |
Листовые мешалки" имеют лопасти большей, ширины, вследствие чего около верхней и нижней кромок лопастей создаются вихревые потоки, способствующие повышению турбулентности в перемеши-
|
, 6 |
Рис. 65. Типы лопастных мешалок: а — рамиая, б — якорная, в — листовая
ваемом материале. Листовые мешалки применяют.для перемешивания маловязких жидкостей. При перемешивании в процессе растворения применяют листовые мешалки с отверстием в лопастях (рис. 65, в).
'Пропеллерные мешалки. Рабочей частью пропеллерной мешалки служит пропеллер (рис. 66), который установлен на оси мешалки. Наибольшее распространение получили мешалки с трехлопаст^ ными пропеллерами. Пропеллерные мешалки создают осевые потоки жидкости, что существенно повышает интенсивность перемешивания. Эффективность мешалки ■ сильно / зависит от формы аппарата и расположения мешалки. Пропеллерные мешалки устанавливают в цилиндрических аппаратах со сферическими днищами. Основные размеры пропеллерной мешалки: диаметр мешалки ^=(0,2-4-0,5)1), расстояние ют-дна h = (0,5-4-1,0) £>.
85
Частота вращения пропеллерных мешалок значительно выше, чем у мешалок Других типов, и достигает в некоторых случаях 40 об/с.
|
Турбинные мешалки имеют форму колес водяных турбин с ло
патками, укрепленными на вертикальном валу. Типы турбинных
мешалок приведены на рис. &7. Мешалки этого типа обеспечивают
интенсивное перемешивание во всем объеме аппарата и применяют
ся для образования суспензий, ра
створения твердых материалов, при
проведении химических реакций. Тур
бинные мешалки имеют диаметр d =
= (0,15-7-0,6)D и частоту вращения
2—5 об/с. Мощность, потребляемая
механическими мешалками, • зависит
от плотности перемешиваемой жидко-
Рис. 66. Пропеллерная сти, частоты вращения и диаметра ме-
мешалка. шалки.
|
|
щжш |
Рис. 67. Типы турбинных мешалок:
а — открытая с радиальными прямыми , лрпастямн, б — открытая с криволинейными лопастями, в — открытая с наклонными лопастям»
При перемешивании механическими мешалками различают дв^ гидродинамических режима — ламинарный и турбулентный. Ламинарный режим соответствует неинтенсивному перемешиванию, при квтором жидкость плавно обтекает лопасти мешалки и практически вращается с частотой, близкой к частоте вращения мешалки. При этом перемешиваются только те слои жидкости, которые непосредственно примыкают к лопастям. Расход мощности при этом невелик. С увеличением числа оборотов резко возрастает сопротив-. ление вращению мешалки за счет турбулизации жидкости и интенсивность перемешивания также возрастает. Дальнейшее увеличение числа оборотов ин-тенсифицирует перемешивание. Однако» значительно увеличивать число оборотов невыгодно, так как расход мощности растет пропорционально третьей степени числа оборотов. Геометрические размеры мешалки в еще большей степени влияют на потребляемую мощность.-Расход мощности растет про-
86
порционально пятой степени диаметра мешалки. Эти особенности должны всегда приниматься во внимание при . конструировании, эксплуатации и замене существующих мешалок.
Пневматическое перевешивание сжатым инертным газом или воздухом' применяется в тех случаях^ когда перемешиваемая жидкость обладает высокой коррозионной активностью и быстро разрушает механические мешалки. Перемешивание. сжатым газом — процесс малой интенсивности и требует больших, чем при механическом перемешиваии, затрат энергии. Пневматическое перемешивание не применяется для обработки легколетучих жидкостей вследствие больших потерь перемешиваемого продукта.
Перемешивание сжатым газом проводят в аппаратах, снабженных специальными устройствами—барботером или центральной циркуляционной трубой.
Барботер (см. рис. 62, б) представляет собой расположенные на дне аппарата трубы с отверстиями. Газ или воздух, выходя из отверстий.в трубах, перемешивает жидкость в аппарате.
В аппарате с циркуляционной трубой газ подается в трубу, расположенную в средней части аппарата. Пузырьки газа, поднимаясь, увлекают за собой по трубе жидкость, находящуюся в сосуде. Поднявшись по циркуляционной трубе, жидкость опускается вниз в кольцевое пространство между трубой и стенк'ами аппарата, обеспечивая циркуляционное перемешивание.
Расход воздуха для перемешивания в барботерах и -аппаратах с циркуляционной трубой составляет. 0,5—1 'м3/мин на 1 м2 свв-бодной поверхности -жидкости.
Смешение твердых материалов
Наиболее простым аппаратом, применяемым для смешения сыпучих материалов, является цилиндрический сосуд, ось которого не совпадает с осью Цилиндра, — так называемая «пьяная бочка»
|
Рис. 68. Смеситель периодического действия «пьяйая бочка>
(рис. 68). Частицы загруженного в аппарат твердого сыпучего_ материала при вращении бочки совершают сложный путь,'их траектории пересекаются,-что и обеспечивает смешение. Процесс . смешения проводится периодически, загрузка и выгрузка материала осуществляются через люк.
Смесители с вращающимися лопастями (рис. 69, а) также применяются для периодического смешения сыпучих и пастообразных материалов. Смеситель представляет собой корпус 1 с днищем в форме двух полуцилиндров, в котором навстречу друг другу вра-
«7
щаются два горизонтальных вала 2 с лопастями, перемешивающем
ми материал. Наиболее распространенной является Z-образна^
форма лопастей (рис. 69, б). Такие смесители часто снабжаются
рубашками для подогрева. ' . .
В шнековых лопастных смесителях рабочими органами служат валы-шнеки с Т-образными лопастями (рис. 70). Валы 2 вращаютт-ся в корпусе /с цилиндрическим днищем с разными частотами.
|
0
О-
а
Рнс. 69. Смеситель с вращающимися лопастями: а. — смеситель, б — лопасть мешалки; / — корпус. 2— валы с лопастями |
Рис. 70. Шнековыи лопастный смеситель: / — корпус, 2 — валы, с лопастями, 3 — разгрузочное отверстие
осуществляя перемешивание и транспортировку сыпучих материалов. Ленточные смесители отличаются только формой лопастей, изготовленных из плоских лент, изогнутых по винтовой линии и закрепленных на валу смесителя. Частота вращения вала в лопастном и ленточном смесителе невелика—10—15 об/мин. Поэтому . процесс смешения в аппаратах с вращающимися лопастными рабочими органами довольно продолжителен.
Более интенсивная циркуляция сыпучего материала, необходимая для интенсивного смешения, достигается в центробежных смесителях. Смеситель центрсгбежного действия с вращающимся конусом (рис. 71) состоит из корпуса 3, в котором на валу 6 вращается полый конус 7 с двумя окнами 5. При вращении конуса 7 частицы материала под действием центробежной силы поднимаются по внутренней поверхности конуса, сбрасываются в пространство между конусом и корпусом.и через окна 5 вновь попадают внутрь конуса 7. Загрузка и выгрузка материала производятся через люки в крышке и днище корпуса. Для разрыхления материала служит мешалка 2, частота вращения которой регулируется тормозом 4.
88
Смесовые барабаны применяются для смешения сыпучих материалов, главным образом в заключительных технологических операциях. В анилинокрасочной промышленности подобные аппараты применяются для обеспечения однородности качества выпускаемых красителей. Такая операция носит название «установка на тип».
Смесовой 'барабан (рис. 72) состоит из цилиндрического корпуса 3, вращающегося на роликах /. Внутри барабана имеютсч спиральные лопасти 4 и полки 5, обеспечивающие интенсивное перемешивание материала при его вращении. Загрузка и выгрузка материала осуществляются шнеком 2."
Рис. 71. Центробежный смеситель: Рис. 72. Смесовой барабан:
/ — мешалка, 2— рамная мешалка, 3-- 1—ролики, 2 — шнек для загрузки и
корпус, 4— тормоз, 5 — окна в конусе, выгрузки, 3 — корпус, 4— спиральные
О — вал, 7 — внутренний конус лопасти, 5 ;— полки
Кроме рассмотренных типов смесителей применяются также вибросмесители, в которых циркуляция сыпучих материалов создается с помощью высокочастотных вибраций.
Вопросы для повторения. 1. С какой целью применяется перемешивание гомогенных и гетерогенных систем? 2. Какие способы перемешивания жидких сред применяются в химической промышленности? '3. Какие типы мешалок применяются на производстве и каковы их характеристики? 4. В чем состоят преимущества и недостатки пневматического перемешивания? 5. В каких аппаратах производится смешение твердых сыпучих материалов?
ГЛАВА 8. ИЗМЕЛЬЧЕНИЕ, СОРТИРОВКА, ДОЗИРОВАНИЕ И ПЕРЕМЕЩЕНИЕ ТВЕРДЫХ МАТЕРИАЛОВ *
Общие сведения
Химико-технологические процессы, сопровождающиеся диффузией вещества, протекают тем быстрее, чем больше межфазная поверхность взаимодействия. Увеличение поверхности контакта фаз облегчает процесс перехода молекул одного вещества в другое, что необходимо для последующего химического взаимодействия. Особенно важно увеличивать поверхность соприкосновения в том случае, когда в процессе участвует твердая фаза. В структуре твер-'
8»
дых веществ положение отдельных молекул строго фиксировано в отличие от газообразных и-жидких веществ, молекулы которых обладают высокой подвижностью. Поэтому для того, чтобы в химическое или физическое взаимодействие вступало сразу большое количество молекул твердого вещества, необходимо увеличивать поверхность. Увеличение поверхности твердых веществ достигается путем механического измельчения материала.
В зависимости от размеров кусков материала до измельчения и размеров частиц измельченного материала прЪцессы классифицируют следующим образом:
Средние размеры кусков, мм:
до измель- после измель-
чения чения
Крупное дробление" ....... 1500—300 300—100
Среднее дробление................................... ..... 300—100 50—10
Мелкое дробление . .-......................... 50—10 10—2
Тонкое измельчение ........ 10—2 2—0,75
Сверхтонкое измельчение ..... 2—0,075 75-Ю3—Ы0*
|
Отношение среднего характерного • размера, кусков до измельчения к среднему характерному размеру кусков после измельчения называют сте пенью измельчения.
Рис. 73. Способы измельчения.материалов: а — раздавливание, б — раскалывание, в — истирание, г —удар |
В существующих типах измельчающих машин не удается сразу достичь высоких степеней измельчения. Имеющиеся устройства обеспечивают ограниченные степени измельчения. Поэтому при необходимости достичь высокой тонины помола материал пропускают последовательно через несколько агрегатов.
Измельчение материала осуществляют путем разрушения ' его" первоначальной структуры различными видами деформации (рис. 73): раздавливанием, раскалыванием, истиранием, ударом. В зависимости от механических свойств и начальных размеров кусков обрабатываемого материала применяют один из перечисленных способов разрушения или. их сочетание.
Крупное, среднее и мелкое дробление твердых и хрупких мате-. риалов целесообразно осуществлять раздавливанием,. ударом и _ раскалыванием. Твердые и вязкие тела в основном разрушаются раздавливанием и истиранием. Тонкое и сверхтонкое измельчение проводят главным образом как мокрое—в воде или других жидкостях, что исключает пылеобразование и агломерирование уже полученных сверхтонких частиц.
Дробление и особенно измельчение — весьма энергоемкие операции. Поэтому, во-первых, не следует измельчать . материал до меньших, чем необходимо, размеров частиц и, во-вторых, нужно
90
отбирать частицы материала мельче тех, которые должны быть получены на данной стадии до начала измельчения. . Машины для измельчения работают в открытом и замкнутом циклах. В первом случае через измельчающее устройство материал проходит один раз. Таким образом осуществляется крупное и среднее дробление. В 'замкнутом цикле материал после обработки в измельчающем устройстве поступает на классифицирующий аппарат, который отбирает крупные частицы и возвращает их на доиз-мельчение в то же устройство. Замкнутый цикл, Применяемый при тонком измельчении, позволяет значительно снизить расход энергии и повысить производительность измельчающих машин..
Работа, затрачиваемая на дробление, расходуется на деформацию объема разрушаемых кусков и на образование новых поверхностей. Для крупного дробления с малой степенью измельчения справедлив закон Кика — Кирпичева; работа дробления пропор-. циональна объему раздробляемого куска. Если принять, что А — затрачиваемая работа, К—коэффициент пропорциональности, D — диаметр куска разрушаемого материала, то для крупного измельчения необходимо совершить работу
A = KtD 3 . (8.1)
Для измельчения справедлив закон Риттингера: работа измель
чения пропорциональна величине вновь образованной поверхно
сти, т. е. ,
А=/С2ЕЙ. (8.2)
По назначению измельчающие машины условно делят на дробилки крупного, среднего и мелкого дробления и мельницы тонкого и сверхтонкого измельчения.
Крупное дробление
Размеры оборудования для крупного, дробления зависят от максимальных размеров кусков, поступающих на дробление, размеров кусков материала после дробления, его физико-механических свойств и производительности дробилок. Для крупного дробления применяют щековые и конусные дробилки.
Щековые дробилки. Основными рабочими органами щековой дробилки (рис. 74) служат неподвижная щека /, составляющая часть станины, и подвижная щека 2. Щеки защищены от истирания стальными рифлеными литыми плитами 10 из износоустойчивой марганцевой стали. Подвижная щека 2, подвешенная в верхней части на оси 3, может совершать кблебательное движение. Качание подвижной щеки 2 осуществляется с помощью вала 5, ■ шатуна с эксцентриком 9 и распорными плитами 8, передающими усилие на подвижную щеку 2. Нижний зазор между щеками, а следовательно, и размеры выходящего из дробилки материала регулируются колодками 7.. .
' Материал поступает на дробление в верхнюю часть пространства между щеками, измельчается раскалыванием и раздавливанием за счет качательного движения подвижной щеки, постепенно проваливается и выходит через нижнюю щель. Измельчение происходит при рабочем ходе, когда расстояние между щеками уменьшается. При холостом ходе подвижная щека отодвигается пружиной с тягой 6.
Энергия потребляется дробилкой неравномерно и практически лишь за рабочий ход, когда загруженный материал подвергается
|
дроблению. При холостом ходе энергия затрачивается только на трение в механизме и расход ее незначителен. Для обеспечения равномерности хода машины на валу 5 установлен маховик 4 с большой массой, аккумулирующий механическую энергию при холостом ходе и расходующий ее при больших мгновенных нагрузках рабочего хода.
10 9 ' 8 7 6 Рис. 74. Щековая-дробилка: J — неподвижная щека, 2 — подвижная щека, 3 — ось подвеса подвижной щекч, 4— маховик, 5 —вал, 6 — пружина отягой, 7 — регулировочные колодки, 8 — распорные плиты, 9 — шатун с эксцентриком, 10~* плиты из марганцевой стали |
Кроме Дробилок с ' верхним подвесом подвижной щеки применяют машины с нижней точкой подвеса. Ширина . разгрузочного отверстия у этих дробилок постоянна, что гарантирует определенную крупность выходящего продукта. Производительность дробилок с нижней точкой подвеса ниже производительности машин с верхним, подвесом подвижной щеки. Существуют конструкции дробилок со сложным движением подвижной-щеки, в которых^ происходит в основном истирание материала.
Щековые дробилки широко применяются при подготовке сырья в различных отраслях промышленности. Наиболее мощные агрегаты позволяют дробить куски размером до 1,5 м в поперечнике. В этом случае каждый аппарат представляет собой сложный комплекс, потребляющий значительное количество энергии.
В конусных дробилках (рис. 75) материал измельчается раз
давливанием и истиранием- при сближении поверхностей непод
вижного усеченного конуса 3 и эксцентрично вращающегося внут
реннего конуса 2. Конус 2 с помощью вала / шарнирно подвешен
в подпятнике и с помощью стакана 4 совершает эксцентрично-вра
щательное движение. Привод стакана осуществляется через шес
терню 5. -
Материал, загружаемый в пространство между конусами 3 и 2; дробится между ними и поступает в нижнюю часть машины. Процесс дробления в конусных дробилках отличается от подобного процесса в щековых дробилках тем, что дробление материала про-
92
исходит непрерывно путем воздействия дробящих поверхностей криволинейной формы.
Конусные дробилки работают непрерывно и поэтому обладают большей производительностью, чем щековые. По конструкции конусные дробилки сложнее и требуют значительной высоты помещения.
Рис. 75. Конусная дробилка: Рис. 76. Валковая дробилка:
/ — вал с шаровой пятой, 2 — внутренний вра- / — пружина, 2 —валок с подвижным»
щающийся конус, 3—неподвижный конус. 4— чподшипниками, 3— бупке.р для загруз-
эксцентриковый стакан, 5 — шестерня , ки, 4 — валок с неподвижными под-
шипниками
Среднее и мелкое дробление
Материал, прошедший крупное дробление, часто подвергают дальнейшему измельчению и доводят крупность зерен от 10 до 2 мм. Для этой цели применяют валковые дробилки!
Валковые дробилки (рис. 76) представляют собой два валка 2 и 4, вращающиеся навстречу друг другу. Подшипники валка 4 закреплены неподвижно, а подшипники валка 2 имеют направляющие, по которым они могут перемещаться в горизонтальном направлении и изменять величину зазора между валками. При случайном попадании в дробилку предмета чрезмерной твердости пружина 1 сжимается, позволяя увеличить зазор между валкам» и предотвращая тем самым их поломку.
Поверхность валков может быть гладкой, рифленой или зубчатой. Последняя применяется для хрупких материалов, измельчаемых в основном рдскалыванием. Для дробления вязких материалов валкам сообщают различную частоту вращения, чтобы усилить-их истирающее действие. При однократном сжатии не происходит переизмельчения материала."Валковые дробилки наиболее эффективны для измельчения материала умеренной твердости. Дробилки этого типа не приспособлены для измельчения кусков материала большого размера, так как они не будут захватываться валками-Угол,' образованный касательными к поверхности валков в точках: соприкосновения с куском дробимого материала, не должен превышать 30°. Его называют углом захвата.
S
Молотковая дробилка (рис. 77) относится к ударно-центробежным дробилкам. Она состоит из корпуса /, футерованного плитами из износостойкой марганцевой стали, и вала 2, на котором укреплен диск 3. На диске 3 с помощью пальцев 4 свободно закреплены молотки 6, также изготовленные из марганцевой стали. В нижней части корпуса имеется колосниковая решетка 5. Диск с молотками
Рис. 77. Молотковая дробилка:
/ — корпус, 2 — вал, 3 —диск; 4 — пальцы, 5 — колосниковая ре-
* тетка, 5 — молотки
вращается с окружной скоростью около 40 м/с. Материал, попадающий в машину, дробится не только вследствие ударов молотков, но также при ударах о плиты. При прохождении через колосниковую решетку материал дополнительно истирается, и раздавливается.
Молотковые дробилки отличаются высокой производительностью и применяются главным образом для измельчения хрупких материалов умеренной'твердости (известняк, каменный уголь). Несмотря на применение износостойких материалов, рабочие органы дробилки быстро изнашиваются, а роторч требует периодической балансировки, что является 'недостатком этой конструкции.
Дезинтеграторы (рис. 78) представляют собой машины ударного действия. Рабочими органами дезинтегратора служат два ротора, вращающиеся в противоположные стороны. На валу / укреп-
S 4
диска (рис. 78, а). Привод. Окружная скорость на внеш- |
лен диск 2, на котором по окружностям размещены пальцы 3. Второй вал 5 имеет диск 7 с пальцами 8. Стальные Пальцы одного диска входят в междурядья второго валов осуществляется шкивами 6 и 3 ней окружности ротора около 30 м/с.
|
Измельчаемый материал через бункер 4 поступает в центральную часть дезинтегратора, дробится пальцами, расположенными на внутренней окружности, отбрасывается к периферии й встречается с пальцами на окружности второго ротора, вращающимися в противоположную сторону. Измельчаемые частицы совершают зигзагообразное движение, как показано На рис. 78, б, многократно подвергаясь дроблению.
Рис. 78. Дезинтегратор: |
а — схема устройства аппарата, б — движение измельчаемой частицы при дроблении; 1,5 — валы, 2 — диск,. 1,3 — пальцы, 4 — загрузочный бункер, 6, 9 — шкивы, 7—диск II , 8—' пальцы |
Близкие по. конструкции к дезинтеграторам машины называются дисмембраторами. У этих машин вращается только один ротор, а второй неподвижно укреплен на .станине.
Ударно-центробежные измельчители обладают высокой произво-" дительностью и используются в широком диапазоне степеней измельчения.
Дата добавления: 2019-07-17; просмотров: 568; Мы поможем в написании вашей работы! |
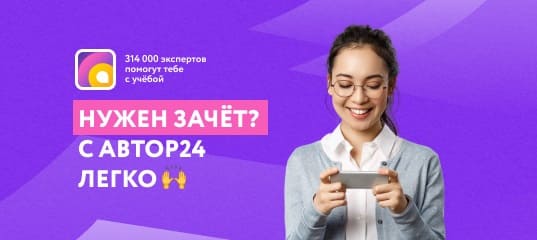
Мы поможем в написании ваших работ!