Основные системы управления качеством строительного производства
Билет 27
Бетонирование методом вертикально перемещаемой трубы (ВПТ).
Метод ВПТ. Это наиболее совершенный метод подводного бетонирования на глубинах от 1,5 до 50 м. Таким методом конструкции бетонируют в котловане, огражденном от проточной воды. В качестве ограждения применяют либо специально изготовленную опалубку (рис. 66, а) в виде пространственных блоков (ящиков) из дерева, железобетона или металла, либо конструкции сооружения (плиты-оболочки, стены массивов-гигантов, опускных колодцев, свай-оболочек, оболочек большого диаметра, ряжей), либо шпунтовое ограждение. Конструкция опалубки должна быть непроницаемой для раствора и цементного теста. Смесь подают бетононасосами, пневмонагнетателями либо непосредственно из бетоносмесителей. Трубы должны быть все время погружены в бетон: не менее чем на 0,8 м при глубине бетонирования до 10 м и не менее чем на 1,5 м при глубине до 20 м. По мере бетонирования трубы поднимают краном и верхние звенья снимают, следя за тем, чтобы вода не прорвалась в трубу. Когда слой подводного бетона достигает проектной толщины, трубы извлекают из него. Бетонная смесь по методу ВПТ, укладываемая с вибрацией, должна иметь подвижность, измеряемую осадкой конуса 6—12 см, укладываемая без вибрации—16—20 см. Приготовляют ее на гравии или смеси гравия с 20—30% щебня, обязательно вводя пластифицирующие добавки.
Порядок операций.
|
|
При установке бетонолитной трубы в скважину 1. Строповка бункера. 2. Подъём и подача бункера с бетонолитной трубой к скважине. 3. Опускание бетонолитной трубы в скважину. 4. Расстроповка бункера. 5. Строповка и перемещение телескопической бетонолитной трубы. 6. Опускание телескопической трубы в скважину через бункер. 7. Расстроповка трубы. При бетонировании свай 1. Установка автобетоносмесителя к приёмному бункеру. 2. Выгрузка бетонной смеси в бункер бетонолитной трубы. 3. Строповка бетонолитной трубы за бункер. 4. Укладка бетонной смеси. 5. Расстроповка бетонолитной трубы. При снятии бетонолитной трубы 1. Строповка, извлечение, перемещение к месту укладки и расстроповка телескопической трубы. 2. Строповка и снятие бункера. 3. Подача к месту складирования. 4. Укладка и расстроповка бункера.
Cxeмa бетонирования под водой мeтoдoм BПT: 1) BПT; 2) oпaлубкa; З) улoжeнный pacтвop
Особенности монтажа железобетонных конструкций.
Строительные конструкции монтируют поточно. Подъем, установку, выверку и временное закрепление осуществляют с помощью грузоподъемных машин
без перерывов. Остальные процессы допускается выполнять с перерывами, если это вызвано необходимостью создания фронта работ и обеспечения безопасных условий труда.
|
|
Железобетонные конструкции монтируют по технологическим картам проекта производства монтажных работ (ППМР).
Крупнопанельные здания возводят башенными кранами, которые устанавливают со стороны, противоположной входам в лестничные клетки, выбирая горизонтально-восходящее направление развития фронта работ. За монтажный участок принимают одну-две секции в пределах этажа. Число монтажных кранов подсчитывают, исходя из директивного срока строительства и условия, что минимальное число участков, обслуживаемых одним краном, при поточном монтаже равно двум.
Последовательность установки конструкций зависит от конструктивной схемы здания.
Одноэтажные промышленные здания монтируют в продольном или поперечном направлениях с раздельной, комплексной или комбинированной последовательностью установки конструкции.
Самоходные краны при монтаже фундаментов или колонн проходят посредине пролета или по его краям. Возможен переход крана из первого пролета через один в третий и т. д.
Схемы перемещения самоходных кранов при монтаже элементов покрытий зависят от длины плит покрытия. Если их длина 6 м, кран перемещается вдоль пролета и с очередной ячейки монтирует элементы покрытия на предыдущей. При длине плит 12 м применяют одну из трех схем движения крана: 1) продольную; 2) для ферм продольную, а для укладки плит — поперечную; 3) поперечную для всех элементов покрытия. При продольной схеме движения требуется большая грузоподъемность крана
|
|
Схемы движения башенных или козловых кранов при монтаже конструкций обусловливаются расположением крановых путей.
Очередность монтажа конструкций одноэтажных зданий зависит от схем движения кранов. Фундаменты или колонны устанавливают поочередно по краям пролета при проходе крана посредине или по каждому ряду отдельно при проходе крана по краям пролета. В такой же очередности монтируют подкрановые балки и подстропильные фермы.
Плиты покрытия укладывают от одного края пролета к другому. Крайние плиты оборудуют ограждением. По фермам с фонарем плиты укладывают от краев к фонарю, а затем на рамах фонаря — от одного края к другому.
Рационален монтаж конструкций с транспортных средств. Если по каким-либо причинам этот метод нельзя применить, то конструкции раскладывают в зоне действия монтажного крана. Так поступают и при необходимости предварительного укрупнения.
|
|
Конструкции раскладывают не все сразу. Сначала колонны, а после их установки — элементы покрытия. Между штабелями и разгружающим краном оставляют проезд для транспортных средств.
Колонны раскладывают по одной вдоль пролета параллельно или под небольшим углом к продольной оси; фермы и балки — вдоль пролета так, чтобы центр их тяжести не попадал под ранее установленные конструкции покрытия; плиты покрытия — в штабеля по три-четыре по обе стороны пролета; стеновые панели — с внешней стороны здания против тех ячеек, где они должны быть установлены, и на таком расстоянии от стены, чтобы мог пройти монтажный кран.
Многоэтажные каркасно-панельные здания возводят с раздельной или комплексной последовательностью установки конструкций. При раздельной последовательности в пределах участка устанавливают колонны, после заделки стыков колонн на них укладывают ригели, а по ним — плиты перекрытия. В последнюю очередь навешивают стеновые панели. При комплексной последовательности, когда используют групповые кондукторы, в пределах части яруса (этажа), охватываемой кондуктором, устанавливают колонны, затем укладывают ригели и плиты перекрытия и только после этого все их окончательно закрепляют. Иногда плиты укладывают после перестановки кондуктора.
Конструкции монтируют башенными кранами, реже самоходными или козловыми. Расстановка башенных кранов зависит от конфигураций и размеров здания в плане, габаритов и массы поднимаемых конструкций, технических характеристик кранов.
Краны устанавливают по одному или по два с одной стороны, по одному или по два с каждой стороны, один в середине при большой ширине здания
При установке кранов с разных сторон здание делят на монтажные зоны для каждого крана, а те в свою очередь— на монтажные участки.
Если нельзя вести монтаж с транспортных средств, устраивают приобъектные склады. Их располагают с одной или двух сторон здания.
При монтаже конструкций используют горизонтально-восходящее, вертикально-восходящее и комбинированное направление развития фронта работ. Горизонтально-восходящее направление предусматривает поэтажную установку конструкций. При вертикально-восходящем направлении развития фронта работ конструкции монтируют по участкам на всю высоту здания. Комбинированное направление представляет собой сочетание первых двух.
Размеры монтажных участков рассчитывают исходя из того, что смонтированная часть конструкций должна быть устойчива, а монтаж непрерывным. Если колонны первого яруса устанавливают в стаканы фундаментов, то размер участка определяют по формуле. Он может быть принят и для участков остальных этажей, если по технологическим или другим условиям его не надо менять.
При вертикально-восходящем направлении развития фронта работ монтаж конструкций каждого вышележащего яруса начинают после полного и окончательного закрепления элементов нижележащего яруса. Если в этом случае кран установлен внутри здания, размер участка определяется радиусом действия крана.
Основные системы управления качеством строительного производства
Качество строительной продукции представляет собой совокупность свойств готового строительного объекта, обуславливающего его
пригодность удовлетворять определенные потребности.
Управление качеством – это установление, обеспечение и поддержание необходимого уровня качества строительной продукции при ее проектировании, производстве и эксплуатации, осуществляемого путем систематического контроля и целенаправленного воздействия на условия и факторы, влияющие на качество.
Внедрение различных систем управления качеством строительства
способствует улучшению качества продукции, повышает культуру производства, акцентирует внимание исполнителей на достижении конечной цели производства – выпуска продукции с требуемым уровнем качества. Однако в каждой из существующих систем имеется ряд существенных недостатков, которые снижают действия этих систем и в ряде случаев не создают условия для заинтересованности организаций в их применении.
Управление качеством строительно-монтажных работ предусматривает выполнение следующих задач:
планирование качества, т.е. установление плановых уровней качества;
обеспечение готовности подразделений строительной организации к
выполнению строительно-монтажных работ на заданном уровне качества;
11
обеспечение материально-техническими ресурсами, отвечающими
проектам, требованиям государственных стандартов и других технических
нормативов;
метрологическое и геодезическое обеспечение точности и достоверности соответствующих параметров проекту и нормативно-технической
документации;
обеспечение кадрами и повышение их квалификации;
моральное и материальное стимулирование качества;
контроль информационного обеспечения и оценки качества.
КС УКСП разрабатывается в три этапа:
первый – подготовка и разработка системы, когда издается приказ об
организации работ по проектированию системы и создании координационной группы организации технической учебы специалистов, которые будут участвовать в разработке документации по системе, обследовании и
анализе существующего уровня качества СМР для плана разработки мероприятий по повышению организационно-технического уровня строительного производства и управления;
второй – разработка проекта системы, а именно технического задания
и проекта КС КУСП;
третий – внедрение системы, когда издается приказ о введении в
действие утвержденного технорабочего проекта КС УКСП и входящих в
него стандартов предприятия, организации службы управления качеством,
а также контроля внедрения и соблюдения основных положений системы и
стандартов предприятия.
Схема организации контроля качества приведена в прил.1.
2. НОРМАТИВНАЯ ДОКУМЕНТАЦИЯ ПО КАЧЕСТВУ
СТРОИТЕЛЬСТВА
Для достижения высокого качества строительства необходимо воздействие на факторы, от которых оно зависит. С этой целью при строительстве объектов КС УКСП предусматривается обеспечение нормативной
документацией и ее тщательное изучение. Нормативная документация –
основа управления качеством строительства. Она устанавливает показатели качества выполнения всех видов работ, регламентирует требования к
их производству и приемке, методы контроля.
В нормативно-техническую документацию, на которой базируются
требования к качеству СМР, входят: строительные нормы и правила
(СНиП), государственные стандарты (ГОСТ), проектно-сметная документация, отраслевые стандарты (ОТС), инструкции (И), указания и другие
нормативные документы, утвержденные в установленном порядке. Современная система нормативных документов (СНД) Российской Федерации в
12
строительстве создается в соответствии с новыми экономическими условиями, законодательством и структурой управления на базе действующих
в России строительных норм, правил и государственных стандартов.
Глобальный подход к испытаниям и сертификации в условиях международного интегрированного рынка, направленный на обеспечение доверия к изготовителям, испытательным лабораториям и органам по сертификации продукции и систем качества. С принятием стандартов ИСО 9000
был установлен определенный уровень организации работ, обеспечивающий эффективное управление качеством.
1. Ответственность руководства, предусматривающая обязанность
руководства предприятия определять политику и цели в области качества,
в создании и внедрении системы качества и руководство ею.
2. Система качества – элемент, обязывающий поставщика разработать, документально оформить и поддерживать в рабочем состоянии систему качества как средство для обеспечения соответствия продукции установленным требованиям. При этом должны быть разработаны все необходимые процедуры для выполнения функций системы качества и общее
описание системы качества – «Руководство по качеству».
3. Анализ контракта – элемент, который обязывает поставщика до
заключения контракта оценить свою способность выполнить его, а в процессе выполнения регулярно проверять и документально подтверждать
достижение требуемых контрактом характеристик.
4. Управление проектированием, в результате которого должен устанавливаться и подтверждаться в проекте уровень качества продукции,
соответствующего запросам потребителей и требованиям законодательства
по безопасности и защите окружающей среды. При этом должны быть
предусмотрены критерии оценки проекта, проводиться анализ и проверка
проекта по завершении определенных стадий проектирования, а также утверждение проекта после его разработки.
5. Управление документацией и данными – для установления порядка разработки, утверждения, выпуска и изменения всех необходимых документов.
20
6. Закупки, при которых основное внимание обращается на выбор
квалифицированных субподрядчиков и входной контроль качества покупных изделий и материалов.
7. Управление продукцией, поставляемой потребителям. Этот элемент должен предусматривать возможность поставщика обеспечить проверку, хранение и техобслуживание продукции при ее использовании в
производстве.
8. Идентификация продукции и прослеживаемость. Этот весьма
важный элемент необходим для создания уверенности в том, что в процессе производства используются требуемые материалы и покупные изделия,
для чего их качество должно быть подтверждено соответствующими документами. Изготавливаемые детали и узлы также должны иметь сопроводительные документы и необходимую маркировку для установления их
принадлежности к тому или иному изделию.
9. Управление процессами с целью соблюдения требований конструкторской документации при изготовлении продукции путем создания
управляемых условий. Для этого необходима разработка технологии производства, применения необходимого оборудования и контроль за выполнением установленных параметров производственного процесса и достижением требуемых характеристик продукции.
10. Контроль и проведение испытаний, в результате чего определяется достигнутый уровень качества и оценивается его соответствие тому
уровню, который был заложен в конструкторской документации. При этом
предусматривается входной контроль материалов и покупных изделий,
контроль и испытания в процессе производства и окончательный контроль
и испытания с оформлением соответствующих протоколов.
11. Управление контрольным, измерительным и испытательным
оборудованием, без чего невозможна объективная оценка качества продукции. Здесь должно быть предусмотрено: установление необходимых
измерений и их точность, идентификация, калибровка (определение погрешностей или поправок для совокупности мер) и проверка оборудования, а также обеспечение требуемых условий их сохранности.
12. Статус контроля и испытаний. Этот элемент требует поддержания определенного уровня контроля и испытаний: проведение контроля
и испытаний аттестованным оборудованием, подготовленными специалистами с помощью проверенных и откалиброванных средств измерения,
чтобы можно было доверять полученным результатам.
13. Управление несоответствующей продукцией – устанавливающие правила использования изделий с отступлениями от документации
или порядок изоляции окончательно забракованных изделий с тем, чтобы
гарантировать, что в изготавливаемой продукции нет деталей, узлов или
материалов, не соответствующих установленным требованиям. При этом
должно быть предусмотрено своевременное обнаружение, изъятие и изоляция брака.
14. Корректирующие и предупреждающие действия, необходимые
для устранения дефектов и предупреждения их повторения путем устранения причин их появления.
15. Погрузочно-разгрузочные работы, хранение, упаковка, консервация и поставка. Эти элементы системы качества предназначены для
обеспечения поставщиком сохранности продукции вплоть до ее поставки
потребителю.
16. Управление регистрацией данных о качестве. Здесь требуется
иметь установленный порядок сбора, систематизации, ведения, хранения и
представления потребителю данных о качестве для подтверждения соответствия продукции установленным требованиям и эффективности системы качества.
17. Внутренние проверки качества, позволяющие регулярно контролировать выполнение функций (элементов) системы качества и соблюдение соответствующих нормативных документов. При этом должны составляться планы проверок и протоколироваться их результаты, а сами проверки должны проводиться персоналом, не несущим непосредственную ответственность за проверяемую деятельность.
18. Подготовка кадров – для обеспечения требуемой квалификации
персонала.
19. Техническое обслуживание. Необходимость обслуживания определяется в зависимости от установленных требований.
20. Статистические методы – поставщик должен определить потребности в статистических методах, применяемых при разработке, управлении процессами и оценке характеристик продукции. При этом должны
быть установлены соответствующие процедуры их применения
БИЛЕТ 28
1. Производительность труда в строительстве: сущность, расчет и пути повышения.
Производительность труда — это показатель, который определяется количеством продукции, произведенной в единицу рабочего времени, или затратами труда на единицу произведенной продукции или выполненной работы. [3]
Производительность труда (П) измеряется количеством работы (продукции, оборота, услуг), производимых одним работником в единицу времени (час, смену, неделю, месяц, год), и рассчитывается по формуле:
где О — объем работы в единицу времени;
Ч — число работников.
В практической деятельности для планирования, учета и анализа производительности и эффективности труда используется определенная система показателей, которая предусматривает измерение производительности труда на рабочих местах, в трудовых коллективах на предприятиях, в отдельных отраслях производства, а также в масштабе всей экономики или народного хозяйства страны.
В отраслях экономики, на предприятиях, в трудовых коллективах, на рабочих местах показателями производительности труда являются выработка (В) и трудоемкость (Q). [6]
1) Выработка продукции в единицу времени – среднее количество продукции, произведенное в единицу рабочего времени. Выработка характеризует эффективность использования рабочей силы, поэтому этот показатель служит основной характеристикой уровня производительности труда в статистической отчетности.
Выработка характеризует объем произведенной продукции в единицу времени:
где В – выработка продукции;
V – количество произведенной за период продукции в натуральных или стоимостных измерителях;
T – численность работников (основных рабочих, основных и вспомогательных, промышленно-производственного персонала). [17]
Измерение выработки в разных отраслях экономики имеет отличительные черты в связи с особенностями производства выпускаемой продукции.
В промышленности выработка определяется отношением объема выпускаемой продукции к затратам труда не ее производство, выраженный в среднесписочной численности работников промышленно-производственного персонала за один и тот же временной период.
В строительстве выработка определяется отношением объема строительно-монтажных работ (в сметных ценах) к среднесписочной численности работников, занятых на строительно-монтажных работах и в подсобных производствах.
На транспорте выработка рассчитывается как отношение объема перевозок (т/км) к численности работников, занятых на перевозках.
В торговле выработка рассчитывается отношением объема розничного товарооборота к среднесписочной численности работников торговли.
В сфере услуг выработка определяется отношением стоимости услуг без стоимости материальных затрат на их оказание за определенный период календарного времени к среднесписочной численности персонала сферы услуг за тот же период. [6]
2) Трудоемкость – обратный показатель, характеризует затраты труда на единицу продукции. Трудоемкость используется при планировании необходимых затрат на производство заданного количества продукции.
Трудоемкость измеряется, как правило, в нормо-часах (фактических часах работы, затраченных на производство единицы работы):
где Q – трудоемкость
T – численность работников (основных рабочих, основных и вспомогательных, промышленно-производственного персонала)
V – количество произведенной за период продукции в натуральных или стоимостных измерителях.
Трудоемкость продукции, как и выработка, может быть рассчитана в разных вариантах. В зависимости от состава включаемых в неё трудовых затрат различают следующие виды трудоемкости:
1) технологическая трудоемкость (Qтех) определяется затратами труда основных рабочих – как сдельщиков, так и поставщиков. Она рассчитывается по производственным операциям, отдельным деталям, узлам, готовым изделиям.
2) трудоемкость обслуживания производства (Qобсл) включает затраты труда вспомогательных рабочих, занятых обслуживание производства во всех производственных подразделениях. Расчет ее осуществляется по каждой операции, изделию либо пропорционально технологической трудоемкости изделия.
3) трудоемкость управления производством (Qупр) состоит из затрат труда руководителей, специалистов, охраны и т.п. Затраты труда этих категорий работников в трудоемкости учитываются по-разному: та их часть затрат, которая непосредственно не связана с изготовлением изделия пропорционально производственной трудоемкости.
4) производственная трудоемкость (Qпроизв) представляет собой затраты труда основных и вспомогательных рабочих на производство единицы продукции и складывается из трудоемкости технологической и трудоемкости обслуживания
5) полная трудоемкость (Qполн) отражает затраты труда всех категорий персонала и определяется по формуле:
Каждый из указанных показателей трудоемкости может быть нормативным, плановым (проектным), фактическим.
Нормативная трудоемкость определяется на основе норм труда: норм времени, норм выработки, нормы времени обслуживания, норматив численности. Она используется для определения общей величины трудовых затрат, необходимых как для изготовления отдельных затрат, необходимых как для изготовления отдельных изделий, так и для выполнения всей производственной программы.
Плановая трудоемкость отличается от нормативной на величину снижения трудозатрат, планируемых в текущем периоде за счет реализации организационно-технических мероприятий (в целях достижения проектной трудоемкости при максимально возможном освоении новой техники и технологии или повышения эффективности производства).
Фактическая трудоемкость – это сумма уже совершенных затрат труда на выполненный объем работ или выпуск производственной продукции.
Применение показателя трудоемкости позволяет связать проблему измерения производительности труда с выявлением резервов его роста, сопоставить затраты труда на одинаковые изделия в разных цехах и на разных предприятиях.[13]
Между выработкой и трудоемкостью существует обратно пропорциональная зависимость, однако если мы учитываем процент повышения выработки или процент снижения трудоемкости, то необходимо применять следующие формулы
где b – процент повышения выработки;
а – процент снижения трудоемкости. [10]
Применяются три метода измерения производительности труда: стоимостной, натуральный и трудовой, которые отличаются единицами измерения объема работы.
Натуральный метод измерения производительности труда применяется в случае производства (выпуска) однородной продукции. Объем работы в этом случае определятся с помощью натуральных измерителей, таких, как: тонны, штуки, метры, литры и др. Уровень произведенных работ в натурально-вещественном измерении является наиболее объективным и достоверным показателем производительности труда. Посредством этого метода можно измерять и сравнивать производительность труда отдельных бригад и работников, планировать их численность, определять профессиональный и квалификационный состав, сопоставлять производительность труда разных предприятий.
Натуральный метод измерения производительности труда отличается простотой и наглядностью расчетов. Однако его использование ограничено: им нельзя пользоваться при расчетах производительности труда на тех участках, где производится или выпускается разнородная продукция, например, машины и инструменты. Кроме того, он не учитывает изменение запасов незавершенного производства.
Разновидностью натурального метода является условно-натуральный метод, когда объем работы учитывается в условных единицах однородной продукции. Так, разные по емкости вагоны переводятся в двухосные, консервные банки разной емкости — в условные банки, а различная обувь — в условную пару. Пересчет в условные измерители производится, как правило, с помощью переводных единиц (коэффициентов).
Трудовой метод используется в тех случаях, когда на предприятии производится большое количество продукции, ассортимент которой часто меняется. Этот метод основан на измерении выработки продукции в нормо-часах рабочего времени. Он применяется, если на каждый вид продукции установлен временной норматив (нормативная трудоемкость).
2. Календарный план строительства. Назначение и элементы сетевого графика.
К календарному строительству относится все документы по планированию, которых на основе объемов смр и принятых организационно-технологических решений определены последовательность и сроки осуществления строительства. Календарный план –основной документ в составе ПОС и ППР. На основе календарного плана определяется потребность в основных материально-технических ресурсов, сроки поставки оборудования, а также ведется контроль за ходом работ и координируется работа исполнителя.
КП разрабатывается в следующем порядке:
1. составляют перечень работ
2. определяют объем работ
3. выбираются методы производства работ и использования машин
4. рассчитывают нормальную машинную трудоемкость
5. определяют состав бригад и звеньев
6. выявляют технологическую последовательность выполнения работ
7. устанавливают сменность работ.
Для разработки КП в составе ППР используются следующие исходные данные:
1. КП в составе ПОС
2. Организ. Документы.
3. Нормативы продолжительности строительства
4. Технологические карты на строительные, монтажные и специальные работы
5. Рабочие чертежи и сметы
КП на объектах состоит из 2-х частей:
1. Расчетная часть
2. Графическая часть (линейная и сетевая)
На планирование строительства используется сетевые графики представляющие собой стрелочку. Диаграмму отображающию последовательность осуществления всех технологических операций и их взаимозависимость.
Сетевой график позволяет выбрать оптимальный вариант продолжительности выполнения работ, использовать резервы, оперативно вносить коррективы в ходе строительства. В основе построения сети лежат понятия: работа-производственный процесс, требующий затрат времени, материальных ресурсов, приводящих к достижению определенных результатов.
Работа на сетевом графике обозначается сплошной стрелкой. Под стрелкой - наименование работ; над – продолжительность в днях.
Ожидание – процесс требующий только затрат времени, не требующий никаких ресурсов. Обозначается пунктирной стрелкой.
События – факт окончания или нескольких работ, необходимый или достаточный для начала следующих работ. Изображается кружком с номером – кодом события внутри.
Путь – непрерывная последовательность работ в сетевом графике. Его длину определяют суммой продолжительности составляющих его работ.
Критическим называют полный путь, имеющий наибольшую длину (продолжительность) из всех полных путей. Его длину определяет срок выполнения работ по сетевому графику. Обозначается жирной линией.
Работы, лежащие на критическом пути, называют критическими.
Пути, продолжительность которых несколько меньше критического называют под критическим.
3. Особенности монтажа металлических конструкций.
Монтаж металлических конструкций
Технологически, монтаж металлических конструкций специфичен в силу особенностей физических свойств металла. Так как металл обладает высокой прочностью, сечения металлических конструкций, будь-то колонны, балки, мембраны или стержни ферм, характеризуются небольшой но достаточной площадью поперечного сечения. Это позволяет выполнять конструкции из металла более легкими чем из железобетона. Именно поэтому металлические конструкции применяются при изготовлении большепролетных ферм (свыше 30м), оболочек, мембран, подкрановых балок, легких профильных настилов.
Изготовление габаритных конструкций из металла ставит дополнительные трудности перед монтажниками. Например, подъем и установка большепролетных конструкций возможна лишь при скоординированных действиях нескольких кранов, что само по себе является трудной задачей. Но обо всем по порядку.
Монтаж металлических конструкций ферм
Специфической проблемой при монтаже ферм является их повышенная гибкость. Это делает конструкцию фермы крайне уязвимой при подъеме и монтаже. Ферма состоит из тонких стержней, рассчитанных на перераспределение усилий от равномерной нагрузки верхнего пояса фермы при опорах на концах нижнего пояса. Вследствии больших габаритов, закрепление фермы стропами за опорные части невозможно. Поэтому напряжение в стержнях фермы при монтаже отличается от предусмотренного проектом. Поэтому для монтажа ферм практикуют следующие методы.
Монтаж
Монтажное усиление фермы дополнительными стержнями.
Стержни крепят таким образом, чтобы они воспринимали вес фермы от точек закрепления строп. Стропы крепятся в двух или четырех точках верхнего пояса в зависимости от пролета ферм.
Использование плоскостной траверсы.
Эта рамная конструкция фиксирует ферму по поясам, придавая ей необходимую жесткость.
Монтаж ферм выполняют после полного закрепления колонн со всеми предусмотренными проектом пространственными связями. Первую смонтированную ферму крепят расчалками. Каждую последующую крепят пространственными связями к предидущей. После монтажа и раскрепления ферм, выполняют покрытие ребристыми железобетонными плитами, укладывая их поперек ферм. Таким образом образуется жесткий диск по верхнему поясу ферм и их окончательная фиксация.
Монтаж металлических колонн
Первая трудность с которой сталкиваются при монтаже металлических колонн, это повышенные требования точности к геометрии фундаментов. Крепление металлической колонны к фундаменту осуществляется посредством анкерных болтов. Отклонение закладных от проектных положений допускается не более чем на 2мм. Если отклонение по вертикали составляет 40-50мм, опорную часть доводят до требуемого уровня с помощью металлических пластин.
Монтажv колонн ведут с помощью кранов, на весу. Предварительно, колонны раскладывают у мест монтажа. Там же, выполняют обустройство конструкции колонн приваркой креплений для закрепления подмостей, а также приваривают закладные детали и монтажные крепления.
Так как монтаж колонн выполняется с крана, важно чтобы колонна подвешивалась строго вертикально. Если колонна симметрична, то ее подвешивают за верхнюю точку. Если же не симметрична (например, крайняя двужветвевая колонна промышленного здания), для монтажа используют траверсы, позволяющие придать колонне вертикальное положение на весу.
Для предотвращения среза резьбы с анкерных болтов фундамента, на них надевают защитные колпачки. При установке колонны, ее закрепляют на анкерах, затем, выполняют контрольную выверку геодезисты, после чего, окончательно закрепляют обваркой опорной пяты к закладной детали фундамента.
Монтаж металлических конструкций подкрановых балок
Монтаж
Подкрановые балки пролетом до 24 м выполнены цельными, составного двутаврового сечения. Перед монтажем, они доставляются на объект и размещаются у опор смежных колонн. Монтаж подкрановых балок ведется с помощью крана. Балки с торцов заглушены толстым стальным листом, выступающим за нижнюю плоскость сечения. Этот лист устанавливается на опорный столик колонны. Окончательная выверка выполняется с помощью подкладок из листовой стали. Затем, балки скрепляются между собой болтами для образования неразрывной многопролетной конструкции воспринимающей массу движущейся кран-балки.
Если пролет подкрановой балки достигает 24 м, ее изготавливают и доставляют на стройку по частям. Части балки транспортируют к месту монтажа и производят укрупнительную сборку непосредственно под местом монтажа у основания колонн. Так как вес балки в этом случае выходит примерно 45-65 т, монтаж выполняется двумя кранами.
Так же есть технология монтажа тяжелых подкрановых балок с устройством временной промежуточной опоры. Это позволяет выполнить подъем балки по частям, а собрать ее уже на верху, в проектном положении.
Дата добавления: 2019-07-17; просмотров: 113; Мы поможем в написании вашей работы! |
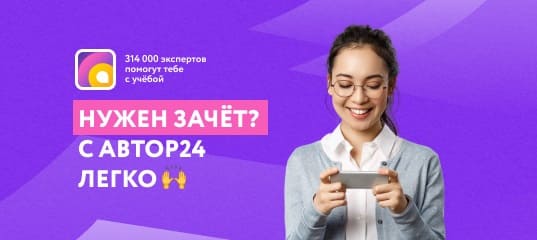
Мы поможем в написании ваших работ!