Методика и последовательность выполнения курсовой работы
5.1 Расчет рабочего колеса насоса
5.1.1 Определений мощности, потребляемой насосом
Находим секундную производительность насоса м3/с по формуле
(5.1.1)
Определяем коэффициент быстроходности насоса по заданной частоте вращения по формуле
(5.1.2)
где – коэффициент быстроходности;
– частота вращения рабочего колеса, мин-1
– секундная производительность насоса, м3/с;
Н – напор, развиваемый насосом, м.в.ст.
По полученному значению определяем быстроходность насоса: тихоходные центробежные насосы (
=40-80), средней быстроходности (
=80-150).
Если , то расчет ведем для насоса типа D.
Находим полный к.п.д. насоса по формуле
(5.1.3)
где – полный коэффициент полезного действия насоса;
– объёмный к.п.д.;
– гидравлический к.п.д.;
– механический к.п.д.
Чистые к.п.д. определятся по следующим эмпирическим формулам:
объёмный к.п.д.
(5.1.4)
гидравлический к.п.д.
(5.1.5)
где – эквивалентный диаметр входа в рабочее колесо
, мм (5.1.6)
где – расчетная производительность насоса, м3/с;
, м3/с (5.1.6а)
|
|
– частота вращения рабочего колеса, мин-1,
механический к.п.д. определяется по формуле
(5.1.7)
где – механический к.п.д., учитывающий потери энергии на трение в подшипниках и сальниках насоса, лежит в пределах
. Высокие значения относятся к подшипникам качения и хорошим сальникам, нижнее – к подшипникам скольжения;
– внутренний механический к.п.д., учитывающий трение жидкости в водяном зазоре между рабочим колесом и корпусом насоса. Он находится по формуле
(5.1.8)
Находим мощность N, потребляемую насосом
, кВт (5.1.9)
где q – секундная производительность насоса, м3/с;
H – напор, развиваемый насосом, м.в.ст.;
- полный к.п.д. насоса.
5.1.2 Расчет окружности входа рабочего колеса
Определяем крутящий момент на валу рабочего колеса Мкр
,
(5.1.10)
где N – мощность, потребляемая насосом, кВт;
ω – угловая скорость, рад/сек.
, рад/сек (5.1.10а)
|
|
Находим наименьший диаметр вала , по условию прочности на кручение
, м (5.1.11)
где Мкр – крутящийся момент, ;
– допускаемое напряжение на кручение можно принять
.
Полученное значение округляется до ближайшего бóльшего значения по ГОСТ на рекомендуемый ряд размеров.
Принимаем диаметр ступицы (втулки) рабочего колеса по конструктивным соотношениям
, м (5.1.12)
Определяем диаметр подходной горловины рабочего колеса по формуле
, м (5.1.13)
где Со – скорость при подходе жидкости к рабочему колесу, ее находят по формуле С.С. Руднева
, м/с (5.1.14)
где – расчетная производительность, м3/с;
n – частота вращения рабочего колеса, мин-1.
Принимаем диаметр окружности входа D1 из следующих соотношений:
для тихоходных насосов ( ) и средней быстроходности (
)
для быстроходных ЦБН ( )
, м
Определяем ширину лопатки b1, на входе по формуле
, м (5.1.15)
где – радиальная составляющая абсолютной скорости на входе. При отсутствии направляющего аппарата на входе
и
, м/с;
|
|
– абсолютная скорость на входе для получения экономичного насоса принимается равной
;
– коэффициент стеснения прохода на входе в рабочее колесо
.
Находим окружную скорость на входе
, м/с (5.1.16)
Определяем расчетное значение угла из треугольника скоростей на входе. При α=90° он будет равен
(5.1.17)
Конструктивный угол должно лежать в пределах
.
5.1.3 Расчет окружности выхода рабочего колеса
Находим необходимую окружную скорость на выходе u2, для достижения заданного напора насоса по формуле
, м/с (5.1.19)
где – радиальная составляющая абсолютной скорости на выходе, м/с;
– для достижения высокого к.п.д. насоса принимается равной
или
;
угол принимается равным
;
– ускорение свободного падения, м/с2;
Н – напор насоса м.в.ст.;
K – коэффициент потерь на циркуляцию жидкости в межлопаточном канале. У выполненных насосов он составляет . Для расчета окружности входа в первом приближении можно принять K=0,7. В последствии он будет уточнен;
– гидравлический к.п.д. (см. пункт 1.3.3).
Определяем диаметр рабочего колеса на выходе D2 по окружной скорости на выходе u2
|
|
, м (5.1.20)
Находим ширину лопатки на выходе по формуле
, м (5.1.21)
где K2 - коэффициент стеснения на выходе рабочего колеса, принимается .
Количество лопаток рабочего колеса находим по формуле
(5.1.22)
Полученное значение округляем до целого числа.
Вычисляем коэффициент потерь на циркуляцию K по формуле К. Пфлейдерера.
(5.1.23)
где – коэффициент, определяемый по формуле
, меньшее значения коэффициента в скобках 0,55 соответствует насосам, имеющим направляющий отвод с лопаточным аппаратом, имеющим место в многоступенчатых насосах. Для одноступенчатого насоса коэффициент в скобках данной формулы можно принять равным
;
– количество лопаток;
R1 и R2 – радиусы входной и выходной окружностей колеса.
После определения K производится повторный расчет окружности входа, подставив полученное значение K в формулу для u2 (пункт 1.19). Если полученное значение K в п.1.23 отличается от значения K, принятого в п.1.19 не более чем на 0,02, повторный расчет не требуется.
5.1.4 Построение теоретического профиля лопатки
Порядок построения следующий (рис. 1.1).
Из центра О, проводятся две концентрические окружности: окружность входа диаметром D1 и выхода диаметром D2 в принятом для построения масштабе.
В произвольную точку А проводится радиус ОА.
Откладывается угол АОВ, равный сумме углов +
и проводится радиус ОВ.
Проводится прямая линия через точки А и В до второго пересечения с окружностью входа в точке С.
Отрезок АС делится пополам, и его середина обозначается точкой Е.
Из точки Е проводится луч Еm, перпендикулярный к отрезку АС.
В точке А откладывается угол, равный , и проводится луч Аn.
Пересечения лучей Еm и Аn обозначается точкой О1.
Из центра О1 радиусом О1А проводится дуга АС. Она является теоретическим профилем лопатки.
Рис. 1.1. Построение теоретического профиля лопатки.
Рис.2 Графики зависимости коэффициентов Кн и Кс от
5.2 Расчет основных размеров и построение контура обводного канала (улитки) корпуса.
5.2.1 Определение значений коэффициента Kн и Kс
По ранее определенному значению коэффициента быстроходности из графиков на рис. 2. снимаются значение коэффициентов.
5.2.2 Определяется радиус внутренней окружности корпуса по формуле
, м (5.2.1)
где – радиус окружности выхода рабочего колеса, м.
Выбрав необходимый масштаб из центра О (рис.1.3), радиусами и
проводится две окружности.
Окружность корпуса разбивается на 12 равных частей, и через каждые 30° проводятся радиальные лучи, которые обозначаются номерами от начала улитки 0; 1; 2;3;…;12.
5.2.3 Определяем среднюю скорость протекания жидкости в сечении улитки , по формуле
, м/с (5.2.2)
где Kc – коэффициент (см.п. 1.7.1);
м/с2 – ускорение свободного падения;
Н – напор, развиваемый насосом, м.в.ст.
5.2.4 Определяем расход через каждое сечение по формуле
, м3/с (5.2.3)
где q – секундная производительность насоса, м3/с;
qi – секундная производительность рассматриваемого сечения (первого, второго и т.д.);
– угол положения сечения от начала улитки. Для первого сечения
, для второго
, для третьего
и т.д.
5.2.5 Определение площадей каждого сечения
, м2 (5.2.4)
5.2.6 Определяем радиус каждого сечения r1
, м (5.2.5)
Результаты расчетов по пунктам 5.2.1, 5.2.2, 5.2.3 сводим в таблицу 3.
Таблица 3
№ сечения | Угол
сечения ![]() | Расход по
сечению
![]() | Площадь
сечения ![]() | Радиус
сечения ![]() |
1. | ||||
2. | ||||
3. | ||||
4. | ||||
5. | ||||
6. | ||||
7. | ||||
8. | ||||
9. | ||||
10. | ||||
11. | ||||
12. |
Рис.3 Построение контура отводного канала (улитки) корпуса.
5.2.7 На каждом луче касательно к окружности радиуса R3 проводим окружности сечений соответствующими радиусами .
С помощью лекала проводим кривую, огибающую окружности сечений, которая является контуром отводного канала.
5.2.8 Определение диаметра нагнетательного патрубка и длины диффузора определяется по формула:
, м (5.2.6)
, м (5.2.7)
где q – секундная производительность насоса, м3/с;
Vн – скорость в нагревательном патрубке, принимается в пределах м/с;
- угол конусности диффузора, равный
.
5.3 Определение максимальной высоты всасывания
5.3.1 Определение максимальной высоты всасывания Максимальная высота всасывания (напор) определяется по формуле: (5.3.2)
где - максимальная вакуумметрическая высота всасывния, м.в.ст.;
Ра=101·103 – атмосферное давление, Па;
- плотность воды, кг/м3;
g = 9,81 – ускорение свободного падения, м/с2;
= 1,15-1,30 – коэффициент запаса;
- критический кавитационный запас м.в.ст., определяемый по формуле С.С. Руднева.
(2.3)
где n – частота вращения рабочего колеса, мин-1;
q – производительность консольного насоса, м3/с. Для насоса типа D вместо q подставляется q1=q/2;
с – кавитационный коэффициент быстроходности, зависящий от коэффициента быстроходности nS. Величины C приведены в табл. 3
Таблица 3
Значение коэффициента C
nS | 50 | 70 | 80 | 150 | 200 |
С | 600 | 750 | 800 | 1000 | 1200 |
5.4 Расчет на прочность основных элементов центробежного насоса
При проектировании насосов, обычно, основные размеры деталей определяются в ходе гидравлического расчета, а размеры, характеризующие прочность элементов насоса, принимаются конструктивно, исходя из технологических возможностей производства и желания снизить материалоемкость насоса. Для назначения конструктивных размеров нужно пользоваться данными прототипов. В этом случае расчет элементов насоса имеет проверочный характер. В курсовом проекте производится расчет вала рабочего колеса, шпоночного соединения, рабочего колеса, корпуса насоса, болтов, соединяющих корпус насоса и расчеты, необходимые для выбора подшипников и муфты.
5.4.1 Расчет вала на статистическую прочность, выносливость и жесткость.
При работе насоса вал подвержен действию различных нагрузок (сил, изгибающих и крутящих моментов), поэтому он рассчитывается на статическую прочность, на выносливость и на жесткость.
Расположение нагрузок неравномерно по длине вала и направление их действий лежит, как правило, не в одной (вертикальной) плоскости. Поэтому при проектировании насосов строят эпюры сил, распределенных нагрузок и моментов в вертикальной и горизонтальной плоскостях, и проверку осуществляют в нескольких сечениях по длине вала.
В настоящем курсовом проекте проверочные расчеты проводятся для одного опасного сечения вала, которым является у консольного насоса сечения в подшипнике ближнему к рабочему колесу и у насосов с двухсторонним всасыванием – по середине длины ступицы рабочего колеса.
а) Расчет внешних нагрузок.
Осевое усилие определяется по формуле
(5.4.1)
где - осевое усилие, Н;
- сила, действующая на диск колеса, Н ;
- сила, действующая на торец вала, Н ;
- сила, обусловленная давлением потока всасываемой жидкости на колесо . Формулы для определения составляющих осевого усилия
(5.4.2)
(5.4.3)
(5.4.4)
где м/с2 – ускорение свободного падения.
– плотность перекачиваемой жидкости, для пресной воды
Н – напор, развиваемый насосом, м.в.ст.;
D2 – диаметр окружности выхода колеса, м;
d2 – диаметр вала в районе сальника, м;
– напор во всасывающей линии, м.в.ст. ; Co – скорость при подходе жидкости к рабочему колесу, м/с .
Направление действия осевого усилия – в сторону всасывающего патрубка.
Радиальное усилие. При работе центробежного насоса на рабочее колесо действует радиальное усилие, обусловленное различным значением давления вдоль отливного канала. Величина и направление радиальной силы различны и зависят от режима работы насоса, его эксплуатационной производительности.
В курсовом проекте определяем максимальное значение этой силы в режиме повышенной производительности по формуле
(5.4.5)
где k = 0,36 коэффициент для максимального значения радиальной силы;
- ширина колеса на выходе
(5.4.6)
где b2- ширина лопатки на выходе, м;
- толщина дисков колеса, м;
Н – напор, развиваемый насосом, м.в.ст.;
D2 – диаметр окружности выхода, м;
- плотность перекачиваемой среды, кг/м3;
Направление действия радиального усилия определяется углом (рис.4). В курсовом проекте принимаем
.
В дальнейших расчетах для определения направления радиального усилия, необходимо учитывать ориентацию отливного канала. Обычно у консольных насосов он своим выходом направлен вверх (рис.4, а), а у насосов с двусторонним всасыванием горизонтально (рис.4, б).
Усилие от массы рабочего колеса. Это усилие находим по формуле
(5.4.7)
где - плотность материала рабочего колеса, кг/м3. для серого чугуна
=7200кг/м3, для бронзы – 8700, для пластмасс – 1450, для дюралюминия 2700 кг/м3;
g – ускорение свободного падения, 9,81 м/с2;
Vk – объем материала рабочего колеса, м3.
Для определения Vk, м3 ,можно воспользоваться приближенным методом, в котором сложные по конфигурации объемы заменяются простыми геометрическими формами. Для консольного насоса вычисление объема колеса можно представить следующим образом (рис. 5)
(5.4.8)
где - объем описанный ступицей.
(5.4.9)
длину ступицы можно принять ;
- объем диска колеса, м;
(5.4.10), где
- толщина диска колеса принимается конструктивно 8-20 мм;
а)
в)
Рис.4 Направление радиального усилия
а-консольный насос; в-насос типа Д
Рис.5 Сечение колеса
- объем покровного диска.
(5.4.11)
где - толщина диск, м. обычно
;
К - коэффициент, учитывающий конусность покровного диска, определяемый по следующим формулам
(5.4.12)
(5.4.13)
где - ширина лопаток и диаметр рабочего колеса, м;
- объем лопаток рабочего колеса, м3
(5.4.14)
где - ширины лопаток, диаметры рабочего колеса, м;
– угол из треугольника скоростей на входе (см. расчет окружности входа);
Z – количество лопаток;
- толщина лопатки, принимаем равной 0,8 от толщины диска колеса;
(5.4.15)
Усилие от массы полумуфты определяется по формуле
(5.4.16)
где q =9,81м/с2;
– масса полумуфты, определяется при выборе муфты.
Изгибающий момент (пара сил) от остаточной неуравновешенности колеса , Н·м определяется по формуле
(5.4.17)
где – расстояние от центра тяжести рабочего колеса до плоскости установки балансировочных грузов, м.
Величину – можно принять равной
, (см. рис.5)
– центробежная сила от неуравновешенной массы рабочего колеса, определяется по формуле
(5.4.18)
где - масса рабочего колеса (ротора), кг
(5.4.19)
(см. пояснения к формуле (3.6.))
– угловая скорость рабочего колеса,
,
,
n – частота вращения, об/мин;
eр – остаточная неуравновешенность рабочего колеса, м.
Предельные значения eр приводятся в табл.4.
Таблица.4
Значения eр
n, об/мин | 750 | 1000 | 1500 | 2000 | 3000 |
eр∙10-6, м | 30 | 25 | 17 | 14 | 11 |
Для рабочих колес массой менее 10 кг и частой вращения до 3000 об/мин можно пренебречь влиянием остаточной динамической неуравновешенности и величину Мц не вводить в дальнейший расчет.
Распределенная нагрузка от массы вала не учитывается ввиду ее малого влияния на прочностные размеры.
Расчет статической прочности вала.
Расчетная схема вала может быть представлена как неразрезанная балка переменного сечения, лежащая на двух опорах и нагруженная системой внешних нагрузок. Подшипники можно принять как шарнирные жесткие опоры. За геометрическую точку шарнира принимается середина подшипника качения и 0,5 , но не более 0,3
от его кромки со стороны пролета для подшипника скольжения, при этом
. Влияние сальников, как опор, не учитывается.
При конструировании насосов иногда вместо одного подшипника на опоре ставят два подшипника рядом (сдвоенный подшипник). В этом случае за ширину подшипников следует принимать суммарную ширину двух подшипников.
Подшипники скольжения применяются у простейших маленьких насосов и очень больших тяжелонагруженных насосах, таких как грунтовые насосы землесосов.
Порядок расчета
1. Изображаем расчетную схему вала в вертикальной плоскости и горизонтальной плоскости.
Для консольного насоса расчетная схема имеет следующий вид (рис. 6).
Рис. 6 Расчетная схема вала консольного насоса.
Рис. 7 Расчетная схема вала для насоса с двухсторонним всасыванием.
На этих рисунках:
Рк – нагрузка от массы колеса, Н;
Рм – нагрузка от массы полумуфты, Н;
– проекция радиальной нагрузки
на вертикальную плоскость (Z) определяется по выражениям для консольного насоса
(5.4.20)
для насоса типа D
(5.4.21)
где - угол действия радиального усилия равный 300°;
- проекция радиальной нагрузки на горизонтальную плоскость (у) определяется по выражениям для консольного насоса
(5.4.22)
для насоса типа D
(5.4.23)
Мц – момент изгибающий (пара сил) от остаточной неуравновешенности рабочего колеса, Н∙м;
и
- ре акции опор А и В на вертикальную (z) и горизонтальную (у) плоскости, Н;
- длины участков балки (вала), м.
2. Определяем по уравнениям статики реакции опор.
Для консольного насоса
(5.4.24)
(5.4.25)
(5.4.26)
(5.4.27)
Для насоса типа D
(5.4.28)
(5.4.29)
(5.4.30)
(5.4.31)
Результирующие реакции опор определяются по теореме Пифагора
(5.4.32)
(5.4.33)
3. Определяем изгибающий момент в опасном сечении. Для консольного насоса
(5.4.34)
(5.4.35)
Полный изгибающий момент
(5.4.36)
Для насоса типа D
(5.4.37)
(5.4.38)
Полный изгибающий момент
(5.4.39)
4. Определяем нормальные рабочие напряжения в опасном сечении , Па.
(5.4.40)
где - полный изгибающий момент, Н·м
- осевое усилие, Н;
- диаметр опасного сечения вала, м.
5. Определим рабочие касательные напряжения в опасном сечении вала.
(5.4.41)
где Мкр – крутящийся момент, Н∙м (см. формулу ).
6. Находим предельно допустимые напряжения в опасном сечении
(5.4.42)
(5.4.43)
где - предельно допустимые нормальные и касательные напряжения, Па;
- пределы текучести материала вала по нормальным и касательным напряжениям, Па;
- коэффициент, учитывающий влияние характерных размеров (диаметр) вала на его прочность. Определяем по табл. 5
Таблица 5
Значение коэффициента
![]() | 10 | 15 | 20 | 25 | 30 | 40 | 50 | 100 | 200 |
![]() | 1,00 | 0,93 | 0,89 | 0,87 | 0,85 | 0,82 | 0,80 | 0,75 | 0,72 |
Величина предела текучести по нормальным напряжениям для рекомендуемых сталей на изготовление валов и приделы прочности следующие
![]() | ![]() | |
ст – 4 | 260·106 | 450·106 |
ст -5 | 280·106 | 550·106 |
25 | 260·106 | 440·106 |
30 | 290·106 | 480·106 |
1025 | 220·106 | 470·106 |
1030 | 260·106 | 550·106 |
Предел текучести по касательным напряжениям принимаем .
7. Рассчитываем коэффициенты запаса статической прочности в опасном сечении
от действия нормальных напряжений
(5.4.44)
от действия касательных напряжений
(5.4.45)
от совместного действия нормальных и касательных напряжений
(5.4.46)
8. Проверяем выполнение условий прочности, при котором
;
;
,
где - расчетные значения коэффициентов запаса статической прочности;
- допустимое значение коэффициента запаса статической прочности, зависящее от пластичности материала вала, которая выражается отношением предела текучести к пределу прочности
. Величины
приведены в табл. 6
Значения коэффициента запаса статической прочности
Таблица 6
![]() | 0,6 | 0,6-0,8 | 0,8-0,9 |
![]() | 1,2-1,4 | 1,4-1,6 | 1,6-2,2 |
Расчет вала на выносливость.
Расчетные нагрузки представляются следующим:
1. Массы рабочего колеса и полумуфты, радиальная нагрузка на колесо постоянные по величине и направлению, они вызывают переменные нормальные напряжения в валу, изменяющиеся по симметричному циклу.
2. Изгибающий момент центробежных сил дисбаланса рабочего колеса и осевое усилие – неизменные в системе координат связанной с валом, вызывают в нем постоянные нормальные напряжения.
3. Крутящий момент, вызывающий касательные напряжения в сечении вала переменной величины из-за пульсирующего силового воздействия потока перекачиваемой жидкости на рабочее колесо.
Порядок расчета
1. Определяем изгибающий момент , Н·м вызывающий переменные нормальные напряжения по формуле
(3.45)
где – изгибающий момент, вызывающий переменные нормальные напряжения;
М'изz – изгибающий момент от постоянных по направлению нагрузок, действующий в вертикальной плоскости, определяется по формуле
Для консольного насоса
(5.4.47)
Мизу – изгибающий момент в горизонтальной плоскости от постоянных по направлению нагрузок.
Значения ,
,
и
см. раздел «Расчет статистической прочности вала» формулы 5.4.33, 5.4.34.
Для насоса типа D
(5.4.48)
2. Определяем амплитудное значение цикла изменения нормальных напряжений по формуле
(5.4.49)
3. Определяем величину постоянной составляющей цикла изменения нормальных напряжений по формуле
(5.4.50)
Значение, входящих величин см. в разделе «Расчет внешних нагрузок» и «Расчет статистической прочности вала».
4. Определяем величину переменной составляющей цикла касательных напряжений по формуле
(5.4.51)
5. Определяем пределы выносливости гладких полированных валов из углеродистой стали по формуле
(5.4.52)
(5.4.53)
где – предел выносливости по нормальным напряжением;
– предел выносливости по касательным напряжением;
– предел прочности, Па.
6. Определяем допустимые пределы усталости прочности и
по формулам
(5.4.54)
(5.4.55)
где и
- допустимые коэффициенты концентрации нормальных и касательных напряжений в опасных сечениях, определяемые по формуле
(5.4.56)
(5.4.57)
где ,
– эффективные коэффициенты концентрации нормальных и касательных напряжений в расчетном сечении. Они зависят от геометрии опасного сечения и предела прочности материала; выбираются по справочным таблицам (см. приложение);
и
- коэффициенты, учитывающие влияние абсолютных размеров (диаметра) вала на его выносливость. Для углеродистых сталей см. табл.7
Таблица 7
![]() | 20 | 30 | 40 | 50 | 70 | 100 |
![]() | 0,92 | 0,88 | 0,85 | 0,82 | 0,76 | 0,70 |
![]() | 0,83 | 0,77 | 0,73 | 0,70 | 0,65 | 0,59 |
– коэффициент, характеризующий влияние окружающей среды и чистоты поверхности вала. Для углеродистой стали и чистовой обработке его можно рекомендовать:
для воздуха ………………0,95
для пресной воды ………..0,85
для морской воды………...0,55
7. Рассчитываем коэффициенты запаса усталостной прочности в опасном сечении по формуле
(5.4.58)
(5.4.59)
(5.4.60)
где - коэффициент запаса усталостной прочности по нормальным напряжением;
- то же по касательным напряжением;
- то же совместного действия нормальных и касательных напряжений
,
- допустимые значения коэффициентов влияния асимметрии цикла определяемые по формулам
(5.4.61)
(5.4.62)
где и
- коэффициенты влияния асимметрии цикла. Для сталей с пределом прочности. Значения коэффициентов принимаются
;
, а при
Па,
;
;
- постоянное значение касательных напряжений, определяемое по формуле
(5.4.63)
8. Проверяем выполнение условий усталостной прочности
,
,
,
где - допустимое значение коэффициента усталостной прочности, величина которого составляет 1,5.
Расчет вала на жесткость.
В результате действия радиальных нагрузок на вал, он имеет поперечные деформации (прогиб). При больших прогибах возможно нарушение работы насоса, заклинивание вала, разрушение уплотнения и т. д.
Допустимое значение максимального прогиба находится в пределах 0,0002-0,0005 длины его пролета.
При наличии прогиба и неполной уравновешенности вала (вместе с колесом) возможно появление резонанса между частотой собственных колебаний вала, с частотой вынужденных колебаний, которым соответствует критическое число оборотов. Работа на недопустима, может возникнуть аварийная ситуация для насоса.
Порядок расчета
1. Определяем нагрузку, сосредоточенную в плоскости рабочего колеса по формуле
(5.4.64)
где Рр - радиальная суммарная нагрузка в плоскости колеса, Н;
Рк – нагрузка от массы колеса, Н;
и
- проекции на вертикальную и горизонтальную плоскости радиальной нагрузки на колесо (см. формулы 5.4.20-5.4.23).
2.Определяем величину прогиба вала по формулам
для консольного насоса
, м (5.4.65)
для насоса типа D
, м (5.4.66)
где Рр – радиальная суммарная нагрузка (формула 3.63), Н;
– длина пролета, м. Для консольного насоса – длина консольной части вала, для насоса типа D – длина вала между подшипниками;
E- модуль упругости, Па. Для стали Е =21∙1010, Па;
- момент инерции сечения вала
(5.4.67)
где - диаметр вала в рассматриваемом пролете, м.
3. Определяем допустимый прогиб
(5.4.68)
4. Проверяем условие жесткости по прогибу вала
5. Определяем критическое число оборотов , мин-1 по формуле
(5.4.69)
6. Проверяем вал на критические обороты из соотношения
(5.4.70)
где n – число оборотов вала рабочего колеса насоса
5.4.2 Расчет шпоночного соединения
Соединение вала с рабочим колесом и с муфтой обычно осуществляется с помощью шпоночного соединения, которое часто выполняют еще и предохранительную функцию. При повышении нагрузки шпонка срезается, предохраняя вал, рабочее колесо и другие детали насоса от разрушения. Обычно применяют призматические стандартные шпонки.
Проверочный расчет сводится к определению напряжения смятия боковой поверхности шпонки по формуле
(5.4.71)
где Мкр – крутящий момент, Н·м;
d – диаметр вала, м:
h – высота, шпонки, м:
b – глубина шпоночного паза, м;
l – длина шпонки, м.
Условие прочности
Допускаемые напряжения смятия составляют для стальной ступицы Па, чугунной
Па, бронзовой
Па, для пластмассовых
Па.
Если расчетное напряжение превышает допустимое, можно поставить две шпонки.
5.4.3 Расчет рабочего колеса
В данном расчете осуществляем проверку прочности диска рабочего колеса, который подвержен действию центробежных сил. Методика расчета зависит от механических свойств материала, из которого он изготовлен.
Расчет диска колеса из хрупкого материала.
Отношение /
для этих материалов равно или более 0,8.
Последовательность расчета
1. Максимальные напряжения в диске колеса определяем по формуле
(5.4.72)
где – максимальные напряжения, Па;
– плотность материала колеса, кг/м3;
– угловая скорость рабочего колеса, с-1
(5.4.73)
где n – частота вращения, мин-1;
R2 – радиус окружности выхода рабочего колеса, м.
2. Определяем допустимые напряжения по формуле
(5.4.74)
где – предел прочности материала, Па;
– коэффициент, учитывающий влияние характерных размеров (толщины) диска колеса. Определяется по табл. 5; где вместо
– берем толщину диска колеса
, мм.
3. Находим коэффициент запаса прочности
(5.4.75)
4. Определяем выполнимость условия прочности
где – минимально допустимое значение коэффициента запаса прочности. Для чугунных и бронзовых рабочих колес
.
Расчет диска колеса из пластического материала.
К данным колесам относятся те, у материала которых отношение <0,8. Это обычно стальные и пластмассовые колеса. Расчет сводится к определению угловой скорости, при которой наступает разрушение колеса.
Последовательность расчета
1. Определяем площадь и осевой момент инерции половины меридионального сечения диска колеса. Для этого сложное очертание сечения заменяем несколькими простейшими геометрическими фигурами (прямоугольник, треугольник). На рис. 8 показан пример для консольного насоса, а на рис. 9 – для насоса типа D.
Для консольного насоса площадь сечения определяем по формуле
(5.4.76)
Рис. 8 Сечение диска и ступицы рабочего колеса консольного насоса.
момент инерции сечения
(5.4.77)
(5.4.78)
(5.4.79)
(5.4.80)
(5.4.81)
где ,
, h1, h2 – ширины и высоты простейших фигур (прямоугольников) сечения колеса, м;
,
– моменты инерции простейших фигур относительно оси, проходящей через центр тяжести данной фигуры, м4;
,
– расстояние между осью колеса и осями, проходящими через центр тяжести данной фигуры, м;
F1, F2 – площади фигур, м2.
Для насоса типа D (Рис.9). Расчет ведется аналогично консольному. Площадь сечения определяется по формуле
(5.4.82)
(5.4.83)
(5.4.84)
(5.4.85)
(5.4.86)
(5.4.87)
Рис. 9 Сечение диска и ступицы рабочего колеса насоса типа D
2. Рассчитываем угловую скорость , при которой происходит разрушение колеса по формуле
(5.4.88)
где – коэффициент, учитывающий толщину диска колеса (см. Пояснения к формуле (5.4.75);
– предел прочности материала колеса. Па;
F – площадь половины меридианального сечения колеса,;
– плотность материала колеса, кг/м3;
– момент инерции половины меридианального сечения колеса, м4.
3. Определяем коэффициент запаса прочности
(5.4.89)
где – угловая скорость, при которой разрушается колесо;
– рабочая угловая скорость рабочего колеса.
4. Проверяем условие прочности
(5.4.90)
где – допускаемый коэффициент запаса прочности
=1,8–2,2.
5.4.4 Расчет корпуса насоса.
Корпус любого насоса имеет сложную форму. Представим его в виде простейших фигур. Обычно расчет корпуса производят по методике для цилиндрических оболочек, а крышки корпуса рассматривают, как круглые пластины с шарнирами по контуру.
Расчет цилиндрической части корпуса.
1.Определяем меридианальные напряжения (вдоль оси насоса) по формуле
(5.4.91)
где р – избыточное давление внутри корпуса насоса, Па
( р = Н∙104 Па, где Н – напор насоса, м. в. ст);
R3 – внутренний радиус корпуса, м;
– толщина стенки корпуса, м.
2. Определяем окружные напряжения по формуле
(5.4.92)
3. Определяем эквивалентные напряжения в расчетном сечении для плосконапряженного состояния по формуле
(5.4.93)
4. Рассчитываем допускаемые напряжения по формулам для пластичных материалов (сталь, пластмасса)
(5.4.94)
для хрупких материалов
(5.4.95)
где – допускаемое напряжение, Па;
– предел текучести материала, Па;
– коэффициент, учитывающий толщину стенки корпуса (табл.5);
– коэффициент, учитывающий влияние среды, значения которого для чугуна для
=1, углеродистой стали
=0,90, для пресной воды и
=0,60 для морской воды.
5. Определяем запас прочности
(5.4.96)
6. Проверяем условие прочности
– допускаемый коэффициент запаса прочности составляет 3,0 … 3.4.
Расчет крышек корпуса консольного насоса.
1. Изображаем расчетную схему крышки (рис.10). На этом рисунке , - давление, развиваемое насосом, 2а - диаметр крышки по внутреннему очертанию корпуса М , 2в - диаметр вала (отверстия в сальнике) М , h - толщина крышки, м.
2. Определяем максимальные напряжения в крышке по формуле
(5.4.97)
где р, а, h - см. расчетную схему (рис. 10);
с2 - коэффициент, зависящий от отношения
радиусов пластины и центрального отверстия в ней а/в. Величина которого приведена в табл.8
Таблица 8
а/в | 3 | 4 | 5 | 6 | 8 | 10 |
С2 | 1,88 | 2,08 | 2,19 | 2,25 | 2,31 | 2,35 |
3. Рассчитываем допускаемые напряжения формулам 5.4.94, 5.4.95.
4. Определяем запас прочности
5. Проверяем условие прочности
Рис. 10 Расчетная схема крышки корпуса
Расчет болтов (шпилек), соединяющих детали корпуса.
1. Определяем площадь корпуса (внутренний контур) в плоскости разъема F, м2, для насоса типа D или площадь крышки корпуса для консольного насоса по формуле
(5.4.98)
где и
– радиусы крышки наружный (входящий в корпус) и отверстия для прохода вала рабочего колеса, м.
2. Определяем усилие, действующее на болты в плоскости разъема по формуле
(5.4.99)
где P – усилие, действующее в плоскости разъема корпуса, H;
F – площадь разъема корпуса, м2;
p – давление, развиваемое насосом. Па.
3. Определяем усилие затяжки по формулам
(5.4.100)
(5.4.101)
где Т – усилие затяжки одного болта;
– напряжение, возникающее в болтах от затяжки их при монтаже корпуса насоса, Па;
F1 – площадь болта по внутреннему диаметру резьбы, м2;
– коэффициент затяжки, для мягких прокладок
=1,5…2,5; для металлических прокладок
= 4;
Р – усилие действующее в плоскости разъема, H ;
Z – количество болтов в плоскости разъема, шт.
4. Определяем расчетную нагрузку на один болт
(5.4.102)
где Q – расчетная нагрузка, Н ;
– коэффициент
= 0,2 – 0,3.
5. Определяем нормальное (растягивающее) напряжение в нарезной части болта
(5.4.103)
6. Определяем крутящий момент, действующий на болт, при затяжке
(5.4.104)
где – крутящий момент, Н∙м;
Т – усилие затяжки, Н ;
– наружный диаметр резьбы, м;
К – коэффициент, обычно К = 0,12.
7. Определяем наибольшие касательные напряжения в нарезной части болта по формуле
(5.4.105)
где – внутренний диаметр резьбы, м.
8. Определяем наибольшие приведенные напряжения
(5.4.106)
9. Определяем коэффициент запаса прочности болтов по формуле
(5.4.107)
10. Проверяем условие прочности
5.4.5. Расчеты для выбора муфты.
В данном проекте муфты не рассчитываются. Они подбираются стандартные по диаметру вала и расчетному значению крутящего момента , определяемого по формуле
(5.4.108)
где – коэффициент режима работы.
=1,25…2,0 меньшие значения для быстроходных насосов, большие для тихоходных;
– крутящий момент на валу насоса, полученный в гидравлическом расчете, Н∙м.
5.4.6 Расчеты для выбора подшипников вала рабочего колеса.
Обычно, в качестве подшипников, используют шариковые однорядные и двухрядные подшипники. Для крупных насосов возможно применение роликовых конических подшипников и для особо крупных насосов (например на землесосах) применяют опорные подшипники скольжения в сочетании с упорным подшипником качения. При выполнении курсового проекта рекомендуется применять подшипники качения.
Подшипники качения (его серия и номер) выбираются, исходя из диаметра посадочного места на валу и расчетной динамической грузоподъемности С.
Расчет шарикоподшипников однорядных.
коэффициент долговечности определяем по таблице:
![]() | 3 | 4 | 5 | 6 | 7 | 8 | 9 | 10 | 11 | 12 | 13 | 14 | 15 |
![]() | 1,815 | 2,0 | 2,15 | 2,29 | 2,41 | 2,52 | 2,62 | 2,71 | 2,80 | 2,89 | 2,96 | 3,04 | 3,11 |
Коэффициент частоты вращения определяем по таблице:
![]() | 960 | 1450 | 2900 |
![]() | 0,326 | 0,284 | 0,226 |
Для нахождения коэффициента динамической осевой нагрузки, определяем отношение радиального и осевого усилия .
По полученному значению , находим
по таблице:
![]() | 0,22 | 0,24 | 0,27 | 0,31 | 0,37 | 0,44 |
![]() | 2,0 | 1,8 | 1,6 | 1,4 | 1,2 | 1,0 |
Определяем динамическую эквивалентную динамическую нагрузку по формуле:
, где
– коэффициент динамической радиальной нагрузки, принимаем 0,56;
– коэффициент динамической осевой нагрузки;
– радиальная нагрузка на подшипник (3,30);
– осевая нагрузка на подшипник (3,31).
Расчетная динамическая грузоподъемность:
5.5 Расчет объемных потерь в уплотнениях насоса
В зазорах между рабочим колесом и корпусом центробежного насоса, разделяющих полости с различным давлением, возникают протечки жидкости. Величину этих протечек можно определить с помощью объемного КПД насоса , вычисленного по эмпирической формуле в гидравлическом расчете насоса. Однако эти потери можно найти путем расчета протечек жидкости через зазоры уплотнений, используя формулы истечения жидкости. На рис. (найти) приведены типы уплотнений, применяемых в центробежных насосах.
Типы уплотнений рабочих колес:
а), б), в) – уплотнения с плоскими кольцами;
г), д) – лабиринтные уплотнения
Рис.4.1
Варианты а,б,в- с плоскими уплотнительными кольцами (ввиду их простоты находят наибольшее применение), варианты г,д - лабиринтовые уплотнения, используются значительно реже и применяются при больших напорах, развиваемых насосом. Размеры, приведенные на рис.1.1, означают следующее:
Ri -радиус уплотнения, м;Bi -радиальный зазор уплотнения ,м;Ba-осевой зазор уплотнения,м;l,l1,l2,l3- длины щелей, м.
Порядок расчета
1. Определяем размеры уплотнения.
Радиус уплотнения Ri. - снимается с чертежа общего вида. Радиальный зазор Bi зависит от размеров насоса для насосов, имеющих м,
для насосов с
м определяется по формуле:
Осевой зазор Ba принимаем в зависимости от размеров насоса в пределах (0,25-1,5) 10-3м. Большие значения берем для крупных насосов.
Размеры длин щелей l,l1,l2,l3 снимаем с чертежи общего вида насоса. При этом длина l равняется ширине кольца плоского уплотнения By, которое находится из соотношения:
,
где D0 - диаметр подходной горловины рабочего колеса,меньшие значения коэффициента перед D0 имеют быстроходные насосы, большие значения - тихоходные.
2. Определяем коэффициент расхода жидкости при истечении через щель уплотнения с плоскими кольцами по формуле:
Для лабиринтного уплотнения по формуле:
Где λ- коэффициент, учитывающий трение жидкости о стенки щели ;
l - длина щели, м;
Bi - радиальный зазор, м;
Z - число щелей лабиринтного уплотнения;
L - суммарная длина щелей лабиринтного уплотнения, м, определяется по формуле
,
Обычно коэффициент расхода µ лежит в пределах 0,2-0,6.
3. Определяем потенциальный напор, срабатываемый в уплотнении по формуле:
,
где Hpi - потенциальный напор, срабатываемый в уплотнении, м.ст. жидкости;
U2 - окружная скорость на выходе, м/с (см.гидравлический расчет);
Ri - радиус уплотнения ,м;
R2 - радиус окружности выхода рабочего колеса ,м;
Нp - потенциальный напор, развиваемый рабочим колесом, м.ст.жидкости. Определяется по формулам:
,
,
где ρ - коэффициент реактивности насоса, .
Представляет отношение статического напора, создаваемого в рабочем колесе, по всему напору.
Верхние значения ρ принимаем для насосов с малым ng (тихоходные, высоконапорные), нижние значения ρ для насосов с большим ns (быстроходных, низконапорных).
Ht - теоретический напор, развиваемый колесом с конечным числом лопаток, м.ст.ж ;
H - напор, развиваемый насосом, м. ст. жидкости ;
ηr - гидравлический КПД (см.гидравлический расчет насоса).
4. Определяем величину протечек через уплотнение колеса qпр1 по формуле:
,
5. Определяем величину протечек через сальники и дренаж сальников Qпр2 по соотношению:
,
где Q - производительность насоса, м3/ч.
Меньшие значения коэффициента перед Q принимаем для насосов консольных, большие для насосов типа D .
6. Определяем объемные потери насоса (протечки) по формуле
,
7. Определяем объемный КПД насоса η0 по формуле:
Полученное значение η0 сравнивается с его величиной, определенной в гидравлическом расчете, и делается заключение на сколько они отличаются друг от друга.
5.6.6 Расчет и построение напорно расходной характеристики насоса
Эта характеристика представляет собой зависимость между расчетными производительностью Q и напором Н.Она получается на основании использования зависимости Н∞ = f ( Q ) из теории центробежного насоса и определяемых расчетным путем объемных и гидравлических потерь.
Расчет и построение характеристик ведется по нескольким точкам для различных производительностей. В данном курсовом проекте принимаем 6 точек, включая нулевую производительность. Расчет сводим в табл. 5.1.
Последовательность расчета
1. Определяем теоретическую расчетную производительность насоса по формуле:
,
где Q - производительность насоса по заданию на курсовой проект, м3/ч;
η0 - объемный КПД насоса, полученный по формуле.
2. Заготавливаем форму расчетной таблицы (см.таблица 5.1).
3. Определяем теоретическую производительность Qti для каждого режима работы насоса по следующим соотношениям :
Режим работы
| №1 | Qt1=0,00 |
№2 | Qt2=0,25*Qtp | |
№3 | Qt3=0,50*Qtp | |
№4 | Qt4=0,75*Qtp | |
№5 | Qt5=1,00*Qtp | |
№6 | Qt6=1,25*Qtp |
Результаты расчета заносим в таблицу 5.1.
Таблица 5.1
Расчет напорно – расходной характеристики
1 №№ режимов | 1 | 2 | 3 | 4 | 5 | 6 |
2 Qti/Qtp | 0,00 | 0,25 | 0,50 | 0,75 | 1,00 | 1,25 |
3 Hti | ||||||
4 (Qti/Qtp)2 | ||||||
5 hri | ||||||
6 Hlˈ=Hti-hri | ||||||
7 hyi | ||||||
8 Hi=f(ηp)= Hiˈ- hyi |
4. Определяем теоретический напор для колеса с бесконечным числом лопастей Ht∞ для первого режима (Qti=0) по формуле:
,
где U2 - окружная скорость на выходе (см. гидравлический расчет);
g - ускорение свободного падения g = 9,81 м/с2
5. Выбираем масштабы производительности и напоров с таким расчетом, чтобы график характеристики имел размеры не менее 250x250 мм и не более 350x350 мм. Строим координатную сетку (см.рис.5.1).
6. Наносим на координатную сетку точку "a", соответствующую Ht∞
Построение расчетной напорно-расходной характеристики
Рис.5.1
7. Определяем расчетный теоретический напор для колеса с конечным числом лопаток Ht5 при Qt5=Qp по формуле:
,
где Н - напор, развиваемый насосом по заданию на курсовой проект;
ηr - гидравлический КПД (см.гидравлический расчет).
Наносим точку "в" соответствующую Qt5, Ht5.
8. Определяем расчетный теоретический напор для колеса с бесконечно
большим числом лопаток Ht∞5 для расчетной теоретической производительности Qt5=Qp по формуле:
,
где Ht5 - теоретический напор при конечном числе лопаток м.в.ст.
K - коэффициент потерь напора на циркуляцию жидкости в межлопаточном канале (см.гидравлический расчет насоса).
Наносим точку "c" соответствующую Qt5 и Ht∞5 .
9. Через точки "а" и "с" проводим прямую линию графика Ht∞=f(Qt).
10. Определяем Ht1 при Qt1=0 по формуле:
,
где K - коэффициент потерь напора на циркуляцию жидкости;
Ht∞1- теоретический напор, определенный по формуле.
Наносим на координатную сетку точку " d ", соответствующую Qt1=0 и Ht1.
11. Через точки "d " и "в" проводим прямую линию графика Ht=f(Qt).
12. Снимаем с графика значения Ht для всех режимов и вносим в таблицу.
13. Находим значения (Qti/Qtp)2 и вносим в таблицу.
14. Определяем для каждого режима гидравлические потери по формуле:
,
Результаты расчета вносим в таблицу.
15. Строим график hr=f(Qt).
16. Строим вспомогательный график напора Hi/=f(Qt) для чего при каждом
значении Qti находим ординату Hi/ по формуле:
Результаты вносим в таблицу.
17. Определяем для каждого режима потери напора на удар жидкости при
входе на рабочее колесо по формуле:
где Н - напор, развиваемый насосом (по заданию),м.в.ст;
К - коэффициент потерь на циркуляцию;
U2 - окружная скорость на выходе, м/с;
Q - коэффициент, представляющий отношение напора развиваемого насосом при закрытом клинкете НЗ k к напору развиваемому насосом H (по заданию)
коэффициент "а" у выполненных насосов составляет 0,9-1,3. Значение "а" в расчетах рекомендуется следующее:
для тихоходных насосов - 0,9-1,0
для средней быстроходности - 1,0-1,1
для быстроходных - 1,2-1,3
18. Результаты расчета hyi вносим в таблицу, строим график;
19. Строим вспомогательный график H=f(Qi). Для получения ординат этого графика используем формулу:
, м
20. Строим график H=f(Q). Для этого проводим ряд вспомогательных
горизонтальных линий. На каждой линии из абсциссы графика H=f(Qt), отнимаем постоянную величину объемных потерь (протечек) Qпр, рассчитанную по формуле для теоретической расчетной производительности. Через полученные точки проводится искомый график H=f(Q) который представляет расчетную напорно-расходную характеристику. Этот график на чертеже нужно выделить либо увеличенной толщиной линии, либо используя цветное изображение.
Приложение
Коэффициенты концентрации напряжений в опасном сечении
Таблица П.1
Значение Kτ и Kσ для валов с галтельным
переходом
| ||||
Σв, МПа | К σ (изгиб) | |||
h/r | ||||
I | 2 | 3 | 5 | |
r/d | ||||
0,01-0,10 | 0,01-0,05 | 0,01-0,03 | 0,01-0,02 | |
400 600 800 | 1,50 1,60 1,70 | 1,70 1,80 1,90 | 1,85 1,95 2,05 | 2,08 2,25 2,40 |
Кτ «с (кручение) | ||||
400 600 800 | 1,35 1,37 1,47 | 1,45 1,47 1,52 | 1,58 1,62 1,67 | 2,08 2,17 2,30 |
Таблица П.2
Значение Kτ и Kσ вытачки
σв Мпа | Kσ | |||||||||||
h/r | ||||||||||||
0,5 | 1 | |||||||||||
r/d | ||||||||||||
|
|
| 0,01 | 0,02 | 0,03 | 0,05 | 0,1 | 0,01 | 0,02 | 0,03 |
| |
400 |
| 1,9 | 1,6 | 1,7 | 1,6 | 1,4 | 2,1 | 1,9 | 1,8 |
| ||
600 |
| 2 | 1,9 | 1,8 | 1,7 | 1,5 | 2,2 | 2 | 1,9 |
| ||
800 |
| 2,1 | 2 | 1,9 | 1,8 | 1,6 | 2,3 | 2,1 | 2 |
| ||
σв Мпа | Kσ(изгиб) Kτ(кручения) | |||||||||||
h/r | ||||||||||||
2 | 3 | 3,5-2 | ||||||||||
r/d | ||||||||||||
0,01 | 0,02 | 0,03 | 0,01 | 0,02 | 0,01 | 0,02 | 0,03 | 0,05 | 0,1 | |||
400 | 2,3 | 2,2 | 2,1 | 2,4 | 2,3 | 1,6 | 1,5 | 1,4 | 1,3 | 1,2 | ||
600 | 2,4 | 2,2 | 2,2 | 2,6 | 2,6 | 1,8 | 1,6 | 1,6 | 1,5 | 1,2 | ||
800 | 2,5 | 2,5 | 2,4 | 2,7 | 2,7 | 2 | 1,8 | 1,8 | 1,6 | 1,3 | ||
Таблица П.3
Значение Kτ и Kσ для валов со шпоночным пазом
Вал со шпоночным пазом | σв Мпа | Kσ(изгиб) | Kτ(кручение) | |
| 400 | 1,51 | 1,2 | |
600 | 1,76 | 1,54 | ||
800 | 2,01 | 1,88 |
Таблица П.4
Значение Kτ и Kσ для валов с метрической резьбой
Вал с резьбой | σв Мпа | Kσ(изгиб) | Kτ(кручение) | |
| 400 | 1,45 | 1 | |
600 | 1,96 | 1 | ||
800 | 2,32 | 1 |
Примечание: для материалов, имеющих предел прочности, отличающийся от значений σв приведенных в табл. П.1 - П.4, величина коэффициентов концентрации напряжений определяется линейной интерполяцией .
Список литературы
1 Харин В.М. Судовые машины, установки, устройства и системы. [Текст]: учебник для ВУЗов/ В.М. Харин и др. – М.: «Транспорт», 2010. – 648 с.
2 Сизов Г.Н. Судовые насосы и вспомогательные механизмы. [Текст]: учебное пособие для ВУЗов/ Г.Н. Сизов, Ю.К. Аристов, Н.В. Лукин. – М.: «Транспорт», 1982. – 303 с.
3 Егоров Г.Л. Центробежный насос. [Текст]: методическое указание по выполнению курсовой работы/ Г.Л. Егоров. – Новосибирск: «НИИВТ», 1991. – 430 с.
4 Будов В.К. Судовые насосы. [Текст]: справочник/ В.К. Будов – Л.: «Судостроение», 1988. – 430 с.
5 Дипломное проектирование на технических специальностях ВУЗов/ учебное пособие на сайте ОИВТ: http://www.ngavt.omskcity.com/files/STD/Dip.oivt
Учебное издание
Березин Игорь Сергеевич
Малахов Иван Игоревич
Учебное пособие
“Расчет одноступенчатого центробежного насоса”
для студентов технических специальностей по дисциплине
“ Судовое вспомогательное энергетическое оборудование”
Ответственный за выпуск: И.А. Кибанова
Редактор: В.А. Филатова
Подписано в печать г.
Формат 60х80/16. Бумага ксероксная
Гарнитура Times New Roman
Оперативный способ печати
Усл.п.л., уч.-изд.л.
Тираж экз. Заказ №
Цена договорная
Омский институт водного транспорта (филиал)
ФБОУ ВПО «НГАВТ»
644099, г. Омск, ул. И. Алексеева, 4
Отпечатано в типографии ИП Шелудивченко А.А. «ТЕХНОТРАНС»
644012, г. Омск, ул. 9 Дунайская, 20
Дата добавления: 2019-07-17; просмотров: 310; Мы поможем в написании вашей работы! |
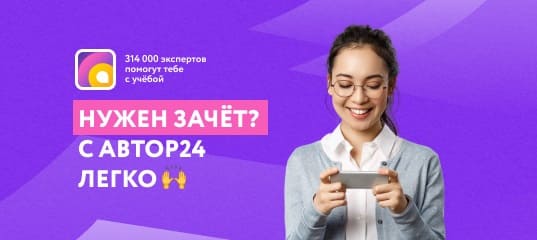
Мы поможем в написании ваших работ!