Расчет теплового баланса ректификационной колонны
Тепловой баланс колонны (без учета теплопотерь) включает:
статьи прихода - тепло вносимое сырьем и через кипятильник ,
Статьи расхода - тепло выносимое дистиллятом , остатком и через конденсатор
где - подвод тепла, - съем тепла.
Расходы сырья F, дистиллята D, остатка W, энтальпию сырья , дистиллята и остатка мы рассчитали выше.
Построим комбинированную диаграмму и по ней определим минимальный теплоподвод и теплосъем.
Отложим на координатной прямой X, Y значения и , а также координаты ноды по изобаре (рис.6). Из этих точек проведем вертикальные пунктирные прямые до пересечения с энтальпиями. Таким образом мы получим ноду . Продолжим эту ноду до пересечения с вертикальными линиями и , получим минимальный теплосъем Pmin(D) и минимальный теплоподвод Pmin(w).
Энтальпия остатка
Энтальпия дистиллята
Минимальный теплоподвод Pmin(W)=5049 ккал/кмоль
Минимальный теплосъем Pmin(D)=22107 ккал/кмоль
По диаграмме найдем:
- величину ккал/кмоль
- величину ккал/кмоль
По полученным данным рассчитаем и :
В режиме рабочего орошения флегмовое и паровое числа больше минимального в 1,1-1,35 раз. В соответствии с этим и больше в 1,1-1,35 раз. По условию задания имеем коэффициент избытка теплоподвода n'=1,23, где
ккал/кмоль
Отложим на диаграмме отрезок и отметим точку P(D). Далее соединим полученную точку P(D) с точкой F и найдем точку P(W).
По диаграмме найдем
|
|
13077113,25=1480978,5 ккал/ч
Подставив известные данные в уравнение (40), проверим, с какой точностью сходится тепловой баланс:
Баланс сходится.
В результате расчета режимов минимального и рабочего орошения мы определили минимальный теплоподвод и теплосъем. По полученным данным построили главную рабочую линию на энтальпийной диаграмме, определили энтальпии сырья, дистиллята и остатка, а также составили тепловой баланс колонны, который сошелся.
Предметы | |||||||||||||||||||||||||||||||||||||||||||||
|
10 Вопрос
Составим систему уравнений материальных балансов для верхней секции (рисунок 8.1).
общий:
( 42 )
по низкокипящему компоненту
( 43)
Подставим одно уравнение в другое:
Поделим на Dправую часть уравнения
Обозначим R=gn+1/ D
Преобразуем уравнение
( 44 )
При этом R называется флегмовое число.
Это уравнение называется уравнением рабочей линии встречных неравновесных потоков верхней части колонны, уравнением концентраций, или уравнением оперативной линии. Оно устанавливает связь встречных потоков пара и жидкости в произвольном сечении колонны. В координатах x - yуравнение представляет собой кривую линию, т.к. в общем случае поток флегмы может изменяться по высоте верхней части колонны, что приводит к изменению тангенса угла наклона этой линии. Если поток флегмы не изменяется по высоте колонны, то рабочая линия будет прямой.
На диаграмме рабочая линия верхней части колонны имеет характерные точки (рисунок 9.2).
При x=yD
получим, y=yD=x
Одна из этих точек Dнаходится на диагонали и ее положение не зависит от потока паров и флегмы. Вторая точка (B) определяется при x = 0 тогда:
|
|
( 45 )
Положение точки B зависит от величины флегмового числа R=gn+1/ D.
При увеличении R точкаBперемещается вниз, а рабочая линия приближается к диагонали. В пределе при R®¥ (или g®¥),рабочая линия сольется с диагональюОА. Этот режим называется режим полного орошения.
Основные допущения:
1.Через любое сечение колонны проходит одно и тоже количество пара в единицу времени, а разделяемые компоненты обладают близкими теплотами испарения.
2.Жидкостные потоки, поступающие в колонну (исходная смесь и флегма), имеют температуру, равную их температуре кипения.
3.Разбавление смеси острым паром не происходит.
4.В дефлегматоре (конденсаторе) не происходит разделения исходной смеси и флегмы, т.е. состав жидкости, возвращаемой из дефлегматора в колонну на верхнюю тарелку, равен составу пара, поднимающегося с этой тарелки в дефлегматор.
5.Состав жидкости, стекающей с последней, нижней тарелки колонны, равен составу пара, поднимающегося из кипятильника или куба колонны на эту тарелку, т. е. принимается, что куб не производит разделяющего действия.
Вдействительности в куб стекает жидкость и получаемый из нее пар. Это допущение позволяет иметь в запасе одну теоретическую тарелку.
|
|
С учетом допущений 4 и 5 имеет место равенство:
хр=ур;хw=yw,
где ур и yw – составы пара по летучему компоненту, поднимающемуся с верхней тарелки колонны и из кипятильника.
Введем безразмерные величины:
- число питания - F = G f ;
Gp
- кубовое число - W = GW ;
Gp
- флегмовое число - R = Ф .
Gp
Здесь базовой величиной является количество дистиллята G p .
В общем виде уравнение материального баланса имеет вид: | |||
Gdy = − Ldx | (2.80) | ||
Выразим величины G иL, учитывая, что количество пара, | |||
поднимающегося по колонне υ после дефлегматора, дает | жидкость на | ||
орошение верхней части колонны Ф и дистиллятаG p : | |||
υ = Ф + Gp | (2.81) | ||
Вводя безразмерные отношения, получим: | |||
υ | =G =R +1 | (2.82) | |
Gp |
Количество жидкости, стекающей в верхней части колонны (флегма),
равно Ф или в виде безразмерного отношения: | |||
Ф | = R | (2.83) | |
Gp | |||
Таким образом, уравнение (2.80) принимает вид: | |||
(R + 1)dy = − Rdx | (2.84) |
Проинтегрируем уравнение (2.84), вынося за знак интеграла величины (R+1) иR, учитывая, что в колонне непрерывного действия количество пара и
количество жидкости остается неизменным: | ||||||||
y | x | dx | (2.85) | |||||
(R + 1) ∫ yP dy | = − R ∫ x | |||||||
откуда получаем: | P | |||||||
(2.86) | ||||||||
(R + 1)(yP − y) = R(xP − x) | ||||||||
Учитывая, что х р =у р , преобразуем (9.86) к виду: | ||||||||
y = | R | x + | xP | (2.87) | ||||
R + 1 | R + 1 | |||||||
Уравнение (2.87) устанавливает связь между составом пара и составом жидкости в любом сечении верхней части колонны при заданных значениях орошения (флегмового числа R) и состава дистиллята (хР). Это уравнение
является уравнением рабочей линии верхней части ректификационной колонны.
Уравнение рабочей линии нижней части колонны отличается тем, что в нижней части колонны, которая начинается после питающей тарелки, количество стекающей жидкости по сравнению с верхней колонной возрастает на величину питания
(R + 1) | ∫ | у | dy =− R | xWdx | (2.88) | ||||||||||
yW | ∫ | ||||||||||||||
Откуда (R+1)(y-y w )=(R+F)(x-x w ) | x | (2.89) | |||||||||||||
Учитывая, что x w =y w и F=(W+1), после преобразований (2.89), находим у: | |||||||||||||||
R + F | xw | ||||||||||||||
y = | R + 1 x − W | (2.90) | |||||||||||||
R + 1 | |||||||||||||||
Так как для колонны непрерывного действия остаются постоянными | |||||||||||||||
величины: | xP | xw | |||||||||||||
R | = A; | = B; R + F = A ;W | = B , | ||||||||||||
R + 1 | R + 1 | R + 1 | |||||||||||||
R + 1 1 | 1 | ||||||||||||||
то уравнения (2.86) и (2.89) есть уравнения прямых линий: | |||||||||||||||
у=Ах+В | (2.91) | ||||||||||||||
у=А 1 х+В 1 | (2.92) |
На рис 2.16 представлены кривая равновесия для процесса ректификации в координатах у-х и рабочие линии верхней и нижней частей колонны, которые пересекаются в точке, отвечающей составу исходной смеси (питающей
тарелки) xf .
y = 1
Равновесная
y p
0,5
Рабочая
y W B
0,5
x W | x B | x p x = 1 |
B 1 |
Рис. 2.16. Рабочая и равновесная линии в процессе ректификации
Верхняя рабочая линия начинается в точке хР=уР, лежащей на диагонали и отсекает на оси ординат отрезок:
B = RxP + 1,
имея тангенс наклона, равный:
A = RR + 1
Нижняя рабочая линия пересекается с верхней рабочей линией и
диагональю в точке x W = y W и отсекает на оси ординат отрезок
B1 = RW + 1x
Очевидно, что неопределенным остается значение ординаты, отвечающей составу x f . Выбор этого значения является определяющим для расчета
процесса ректификации.
Возможны два крайних положения точки пересечения рабочих линий:
-точка пересечения лежит на диагонали;
-точка пересечения лежит на кривой равновесия.
Впервом случае угол наклона рабочей линии, совпадающий с диагональю, составит 450, а tg450=1. Это соотношение может быть удовлетворено только при условии:
l im | R | = 1 | (2.93) | |
→∞ R + 1 | ||||
R |
Следовательно, флегмовое число R=∞.
Это практически означает, что весь конденсируемый в дефлегматоре пар полностью возвращается в виде жидкости на орошение в колонну, колонна работает «на себя» и дистиллят не отбирается.
Движущая сила процесса при этом, если ее выразить как разность рабочих и равновесных концентраций ( у=у -уих=х-х ), будет максимальной, ступени изменений концентраций будут велики, а число ступеней будет минимальным.
Минимальное число ступеней можно найти путем совместного решения уравнения Рауля и рабочей линии, если равновесная кривая описывается уравнением Рауля.
y
y11 y22
x 3 | x 2 | x 1 x |
Рис. 2.17. К выводу уравнения Фенске
Для точки, лежащей на линии равновесия (рис. 2.17), имеем:
у1 | =α | х2 | (2.94) | ||
1 − | у | 1 − | х | ||
1 | 2 |
Для точки, лежащей на рабочей линии:
у1= х1 | (2.95) | ||||||||||||||||||||||||||||||
Совместное решение уравнений (2.93) и (2.94) дает: | |||||||||||||||||||||||||||||||
х1 | =α | х2 | (2.96) | ||||||||||||||||||||||||||||
1−х | 1−х | ||||||||||||||||||||||||||||||
1 | 2 | ||||||||||||||||||||||||||||||
Аналогично получим для второй точки: | х3 | ||||||||||||||||||||||||||||||
у2 |
| =α |
| ||||||||||||||||||||||||||||
|
| ||||||||||||||||||||||||||||||
1− | у | 1− | х | ||||||||||||||||||||||||||||
2 | 3 | ||||||||||||||||||||||||||||||
| или | х2 |
| =α | х3 | , | |||||||||||||||||||||||||
1 | − х | 1 | − х | ||||||||||||||||||||||||||||
2 | 3 | ||||||||||||||||||||||||||||||
но согласно уравнению (2.96), имеем: | |||||||||||||||||||||||||||||||
х2 | = | 1 | х1 | ||||||||||||||||||||||||||||
1− | х |
| α |
| 1− | х |
| ||||||||||||||||||||||||
х1 | 2 | х3 | 1 | ||||||||||||||||||||||||||||
тогда | 1 | =α | |||||||||||||||||||||||||||||
α | 1−х | 1−х | |||||||||||||||||||||||||||||
1 | 3 | х3 | |||||||||||||||||||||||||||||
или | х1 | =α2 | (2.97) | ||||||||||||||||||||||||||||
1−х | 1−х | ||||||||||||||||||||||||||||||
1 | 3 | ||||||||||||||||||||||||||||||
Так как согласно рис. 2.17 | мы имеем две теоретические тарелки, т.е. n=2 |
и показатель степени при α соответствует числу тарелок, то в общем виде уравнение (2.97) выразим в форме:
хК | =α nхH | ||
1 − хК | 1 − хH |
Логарифмируя уравнение (2.98), получим:
l g | xK | = n l g α +l g | xH | ||
1 − xH | |||||
1 | − xK |
Откуда получаем число теоретических тарелок:
l g xK(1 − xH)n = xH (1 − xK )
lg α
(2.98)
(2.99)
Уравнение (2.99) в теории дистилляции известно как уравнение Фенске, используемое для определения коэффициента полезного действия тарельчатых ректификационных колонн.
Вэтом случае в колонне разделяют идеальную смесь при R=∞ «на себя»
иизмеряют концентрации вверх (хК) и внизу колонны (хН).
Полученное по уравнению (2.99) число теоретических тарелок делят на число действительных тарелок, имеющихся в испытываемой колонне, и получают КПД колонны. Уравнение (2.99) используется также для установления эффективности насадочных и др. ректификационных колонн.
Для удобства проведения анализа уравнение (2.99), введем обозначения:
ψ = l g | xK(1 − xH) | , | (2.100) | |||
xH(1 − xK) | ||||||
Тогда уравнение (2.99) примет вид: | ψ | |||||
n = | (2.101) | |||||
l g α | ||||||
Фле́гмовое число́ (коэффицие́нт ороше́ния) — параметр работы ректификационной колонны, определяющий эффективность процесса разделения в концентрационной секции колонны; наряду с числом теоретических тарелок является важнейшим параметром, определяющим качество разделения.
Флегмовое число представляет собой отношение количества жидкости, стекающей с любой тарелки в концентрационной секции колонны (от места ввода сырья до отбора верхнего продукта — дистиллята), к количеству отбираемого дистиллята.
Уравнение материального баланса для произвольно выбранного контура концентрационной секции колонны:
{\displaystyle G_{j}=g_{j-1}+D}
где {\displaystyle G_{j}} — расход пара, покидающего j-ю тарелку, {\displaystyle g_{j-1}} — расход жидкости, поступающей на j-ю тарелку с вышележащей тарелки, D — расход дистиллята.
Тогда флегмовое число запишется как отношение {\displaystyle F_{j}={\frac {g_{j-1}}{D}}}.
Флегмовое число является характеристикой только укрепляющей (концентрационной) секции колонны; ниже зоны питания в качестве аналогичной характеристики выступает паровое число, которое представляет собой отношение количества пара, поднимающегося с любой тарелки в отгонной секции колонны (от места ввода сырья до отбора нижнего продукта — остатка), к количеству отбираемого остатка. В случае полной ректификационной колонны (имеющей и концентрационную, и отгонную секции) часто упоминают лишь флегмовое число, поскольку его изменение влияет на величину парового числа. Стоит однако помнить, что в случае неполной отгонной колонны качество отбираемого продукта (остатка) будет зависеть только от парового числа.
Флегмовое число может принимать любые значения в интервале от Fmin (в режиме минимального орошения) до бесконечности (в режиме полного орошения) при заданном качестве дистиллята, а также других параметрах, определяющих процесс разделения в колонне (давление, доля пара в сырье, поступающем в зону питания колонны). В случае невыполнения этого условия на практике заданная чистота дистиллята достигаться не будет.
Увеличение флегмового числа на работающей колонне (с известным числом теоретических тарелок), то есть уменьшение отбора дистиллята с одновременным увеличением количества орошения, направляемого обратно в колонну, будет приводить к повышению эффективности разделения и увеличению содержания низкокипящих компонентов в дистилляте.
11 Вопрос
Проанализируем работу нижней части колонны, для чего рассмотрим потоки ниже сечения 2-2 (рисунок 8.1). Система балансовых уравнений имеет следующий вид:
( 46 )
для низкокипящего компонента:
( 47 )
Решая совместно уравнения, вставим одно уравнение в другое:
Поделим на W:
обозначим П = Gn / W-паровое число:
Выделим y:
( 48 )
Это уравнение называется уравнением рабочей линии парового орошения или уравнение встречных неравновесных потоков в нижней части колонны.
В координатах x - yуравнение представляет собой кривую линию, т.к. в общем случае поток пара может изменяться по высоте нижней части колонны, что приводит к изменению тангенса угла наклона этой линии. Если поток пара не изменяется по высоте колонны, то рабочая линия будет прямой.
На диаграмме рабочая линия нижней части колонны имеет характерные точки (рисунок 9.4). Одна из этих точек Wнаходится на диагонали и ее положение не зависит от потока паров и флегмы.x=xw
Другая точка (С) определяется при y = 1, тогда:
( 49 )
Положение точки С зависит от величины парового числаП = Gn / W. При увеличенииПточкаСперемещается вправо, а рабочая линия приближается к диагонали. В пределе при П®¥(илиG®¥), рабочая линия сольется с диагональюОА. Этот режим называется режим полного орошения.
Флегмавое (паровое)число
анализа ректификационных процессов принято использовать приведённые фазовые потоки (рис. 6.3.1). Обозначим:
где g и D – количество жидкости в любом произвольном сечении колонны и количество дистиллята.
Это отношение является флегмовым числом; оно представляет собой количество кмоль флегмы, возвращаемой в колонну в расчёте на один кмоль отводимого дистиллята.
Число теоретических тарелок зависит от флегмового числа. В колонне заданные составы продуктов могут быть получены при варьировании флегмового числа в определённых пределах и, как следствие, изменении числа тарелок в колонне.
При бесконечном орошении число тарелок будет минимальным Nmin. При уменьшении флегмового числа число тарелок в колонне увеличивается и при некотором минимальном флегмовом числе Rminчисло тарелок, обеспечивающих заданное разделение смеси, возрастает до бесконечно большого.
Если рассмотреть данный вопрос в практической плоскости, то при снижении количества жидкости по колонне (орошения) наблюдается увеличение количества дистиллята (пара) и, как следствие:
т.е. стремится к снижению Rmin
При этом будет наблюдаться насыщение потока пара высококипящими компонентами, что подтверждает теорию о снижении числа теоретических тарелок.
Обычно выбирают такое флегмовое число, которое обеспечивает оптимальные эксплуатационные показатели. В общем случае флегмовое число определяют экономическими расчётами, т.к. с ростом R увеличиваются потоки (затраты) теплоты в кубе колонны и конденсаторе колонны: рост R при постоянном потоке дистиллята D означает увеличение потока флегмы. Поэтому с повышением R возрастают расходы теплоносителя (нагрузка на теплообменники, трубчатые печи и т.д.)
12 Вопрос
Для образования потока флегмы в верхней части колонны необходимо отводить тепло, обеспечивая конденсацию соответствующего количества паров. В промышленности получили применение следующие три основных способа отвода тепла: парциальным конденсатором, холодным испаряющимся орошением и циркуляционным неиспаряющимся орошением (рисунок 11) .
Парциальный конденсатор.Представляет собой кожухотрубчатый теплообменный аппарат, установленный горизонтально или вертикально на верху колонны. Охлаждающим агентом служит вода, иногда исходное сырье, Поступающие в межтрубное пространство пары частично конденсируются и возвращаются на верхнюю тарелку в виде орошения, а пары ректификата отводятся из конденсатора. Из-за трудности монтажа и обслуживания и значительной коррозии конденсатора этот способ получил ограниченное применение (в малотоннажных установках и при необходимости получать ректификат в виде паров).
При парциальной конденсации принимают, что пары ректификата D и флегмы находятся в равновесии, т.е. парциальный конденсатор эквивалентен одной теоретической тарелке.
![]() |
Рис.11 - Способы регулирования температурного режима в ректификационной колонне: а — отводом тепла — парциальным конденсатом; б — испаряющимся холодным (сырым) орошением; в — неиспаряющимся циркуляционным орошением; г — подводом тепла — подогревателем-кипятильником; д — горячей струей
Парциальный конденсатор для отвода тепла на верху ректификационных колонн обычно используют при небольшой их производительности, наличии паров с небольшим корродирующим действием и при сравнительно невысоких температурах верха колонны.
Такое ограничение обусловлено трудностями размещения теплообменного аппарата большой поверхности на верху колонны. Применение парциального конденсатора при ректификации коррозионного сырья, а также при повышенной температуре верха колонны, когда возможно интенсивное отложение накипи на поверхности конденсатора, нецелесообразно из-за необходимости частого ремонта конденсатора и чистки труб от накипи. Осуществление этих работ на большой высоте также затруднено.
Холодное испаряющееся орошение.Этот способ отвода тепла получил наибольшее распространение на нефте- и газоперерабатывающих заводах. Схема варианта с отводом тепла в верху колонны дана на рис. 11, б. Паровой поток, уходящий с верха колонны, полностью конденсируется в конденсаторе – холодильнике (водяном или воздушном) и поступает в емкость или сепаратор, откуда часть ректификата насосом подается обратно в ректификационную колонну в качестве холодного испаряющегося орошения, а балансовое его количество отводится как целевой продукт.
Отвод тепла при помощи холодного испаряющегося орошения позволяет размещать конденсатор — холодильник на любой удобной для эксплуатации высоте колонны. При этом размеры и конструкция конденсатора не имеют ограничений, легче осуществляются его монтаж и ремонт.
Однако в отличие от парциального конденсатора для эксплуатации такой схемы отвода тепла требуется установка насосов и затрачивается дополнительно энергия для подачи орошения на верх колонны.
Кроме того, требуется на одну теоретическую тарелку больше (парциальный конденсатор эквивалентен одной теоретической тарелке).
Циркуляционное (неиспаряющееся) орошение.Этот вариант отвода тепла в концентрационной секции колонны в технологии нефтепереработки применяется исключительно широко для регулирования температуры не только наверху, но и в средних сечениях сложных колонн.Циркуляционное орошение используется для:
- обеспечения более равномерного распределения потоков паров и флегмы по высоте сложной колонны,
- разгрузки вышележащих сечений
регенерации тепла съемом части тепла с целью образования дополнительного потока флегмы
Для создания циркуляционного орошения с некоторой тарелки колонны выводят часть флегмы (или бокового дистиллята), охлаждают в теплообменнике, в котором она отдает тепло исходному сырью, после чего насосом возвращают на вышележащую тарелку. На современных установках перегонки нефти чаще применяют комбинированные схемы орошения. Так, сложная колонна атмосферной перегонки нефти обычно имеет вверху острое орошение и затем по высоте несколько промежуточных циркуляционных орошений. Из промежуточных орошений чаще применяют циркуляционные орошения, располагаемые обычно под отбором бокового погона или использующие отбор бокового погона для создания циркуляционного орошения с подачей последнего в колонну выше точки возврата паров из отпарной секции. В концентрационной секции сложных колонн вакуумной перегонки мазута отвод тепла осуществляется преимущественно посредством циркуляционного орошения.
Использование только одного острого орошения в ректификацонных колоннах неэкономично, так как низкопотенциальное тепло верхнего погона малопригодно для регенерации теплообменом. Кроме того, в этом случае не обеспечивается оптимальное распределение флегмового числа по высоте колонны: как правило, оно значительное на верхних и низкое на нижних тарелках колонны. Соответственно по высоте колонны сверху вниз уменьшаются значения КПД тарелок, а также коэффициента относительной летучести и, следовательно, ухудшается разделительная способность нижних тарелок концентрационной секции колонны, в результате не достигается желаемая четкость разделения. При использовании циркуляционного орошения рационально используется тепло отбираемых дистиллятов для подогрева нефти, выравниваются нагрузки по высоте колонны и тем самым увеличивается производительность колонны и обеспечиваются оптимальные условия работы контактных устройств в концентрационной секции.
Масса циркуляционного неиспаряющего орошения равна:
( 55 )
Из уравнения следует, что количество циркуляционного неиспаряющего орошения требуется тем меньше, чем ниже его температура.
Циркуляционное неиспаряющееся орошение чаще всего применяется при переработке агрессивного сырья, особенно в присутствии водяного пара, так как в этих условиях наиболее интенсивной коррозии подвергаются конденсаторы и в меньшей степени холодильники.
Выбор того или иного способа отвода тепла в верху колонны определяется особенностями эксплуатации, свойствами перерабатываемого сырья и экономическими соображениями.
Также используются другие схемы отвода тепла: парциальная конденсация с переохлаждением флегмы, отбор второго потока дистиллята из контура циркуляционного орошения и др.
Для проведения процесса ректификации необходимо в низ колонны подвести тепло. При этом часть жидкости, стекающей с нижней тарелки отгонной части колонны, испаряется, образуя необходимый для процесса ректификации встречный поток паров. Подвод тепла может быть осуществлен различными способами.
На установках для подвода тепла применяют змеевики или пучки труб, вмонтированные непосредственно в корпус колонны.. Змеевики и пучки труб целесообразно применять лишь при сравнительно небольшой поверхности теплообмена и при переработке чистых и некоррозионных сред.
Поэтому в промышленности наиболее часто реализуются способы подвода тепла в следующих аппаратах: подогревателе с паровым пространством (парциальный испаритель); теплообменном аппарате без парового пространства с последующим ОИ нагретого потока в низу колонны (так называемая горячая струя).
Подогреватель с паровым пространством.Схема этого способа подвода тепла дана на рис. 11,г. При подводе тепла в низ колонны кипятильником (рибойлером) осуществляется дополнительный подогрев кубового продукта в выносном кипятильнике, где он частично испаряется. Образовавшиеся пары возвращаются под нижнюю тарелку колонны. Характерной особенностью этого способа является наличие в кипятильнике постоянного уровня жидкости и парового пространства над этой жидкостью. По своему разделительному действию кипятильник эквивалентен одной теоретической тарелке. Тепло, подводимое в нижнюю часть колонны ограничено температурой теплоносителя, в случае использования водяного пара температура не превышает 180оС, если в качестве теплоносителя используется высококипящие масла, то температура может достигать 250оС.Этот способ подвода применяется на установках фракционирования газов, при стабилизации бензинов. При высокой температуре низа колонны подвод тепла через кипятильник в целом ряде случаев требует применения специальных высокотемпературных теплоносителей
Горячая струя.Этот способ подвода тепла (рис. 11,д) применяется в тех случаях, когда нагрев остатка обычными теплоносителями (водяной пар и др.) не представляется возможным или целесообразным. При подводе тепла в низ колонны трубчатой печью часть кубового продукта прокачивается через трубчатую печь, и подогретая парожидкостная смесь (горячая струя) вновь поступает в низ колонны ..
Этот способ применяют при необходимости обеспечения сравнительно высокой температуры низа колонны., например при перегоне нефти или мазута.
Для подвода дополнительного тепла в низ атмосферной и вакуумной колонн промышленных установок перегонки нефти такие способы, как кипятильник с паровым пространством или «горячая струя», неприемлемы по причине низкой термостабильности кубовых остатков — мазута и гудрона. В этой связи для создания требуемого парового орошения в отгонной секции этих колонн,также испарения (отпаривания) низкокипящих фракций нефти на практике широко применяют перегонку с подачей водяного перегретого пара.
При вводе водяного пара в отгонную секцию парциальное давление паров снижается и создаются условия, при которых жидкость оказывается как бы перегретой, что вызывает ее испарение (то есть действие водяного пара аналогично вакууму). При этом теплота, необходимая для отпаривания паров, отнимается от самой жидкости, в связи с чем она охлаждается. Испарение жидкости, вызванное водяным паром, прекращается, когда упругость паров жидкости при понижении температуры снизится настолько, что станет равным парциальному давлению. Таким образом, на каждой теоретической ступени контакта установится соответствующее этим условиям равновесие фаз.
Количество водяного пара определяется по формуле
;
где Z - количество водяного пара,
G - масса паров углеводородов,
π - внешнее давление в системе,
Р - давление насыщенных паров,
MG - молекулярная масса углеводородов.
Поскольку величина Р зависит от состава жидкости и ее температуры, то при постоянном расходе водяного пара Z масса перешедших в парообразное состояние углеводородов будет тем больше, чем больше содержится НКК в жидкости и чем выше ее температура.
Наибольший эффект испаряющего влияния перегретого водяного пара проявляется при его расходе, равном 1,5 - 2,0 % масс, на исходное сырье. Общий расход водяного пара в атмосферные колонны установок перегонки нефти составляет 1,2 - 3,5, а в вакуумные колонны для перегонки мазута - 5-8 % масс, на перегоняемое сырье.
Поэтому вносимое водяным паром тепло также мало и заметной роли в образовании потока паров в нижней части колонны не играет. Однако важно, чтобы водяной пар был перегретым или сухим насыщенным, так как вследствие значительной теплоты испарения влаги наличие даже небольшого ее количества приведет к сильному охлаждению остатка и уменьшению массы паров.
При малом расходе водяного пара масса углеводородных паров будет мала, рабочая линия будет крутой, а необходимое число теоретических тарелок значительно возрастет. С увеличением расхода водяного пара число тарелок уменьшится, однако вследствие увеличения общего объема паров возрастет диаметр колонны. Кроме того, увеличится поверхность конденсатора и расход хладагента.
Необходимо указать на следующие недостатки применения водяного пара в качестве испаряющего агента:
- увеличение затрат энергии (тепла и холода) на перегонку и конденсацию;
- повышение нагрузки колонн по парам, что приводит к увеличению диаметра аппаратов и уносу жидкости между тарелками;
- ухудшение условий регенерации тепла в теплообменниках;
- увеличение сопротивления и повышение давления в колонне и других аппаратах;
- обводнение нефтепродуктов и необходимость их последующей сушки;
- усиление коррозии нефтеаппаратуры и образование больших количеств загрязненных сточных вод.
Рассмотренные выше особенности работы колонны с вводом водяного пара остаются справедливыми, если вместо водяного пара использовать газ, который при условиях ведения процесса не содержится в жидкой фазе, например азот, двуокись углерода, метан и др.
В этой связи в последние годы в мировой нефтепереработке проявляется тенденция к существенному ограничению применения водяного пара и к переводу установок на технологию сухой перегонки.
Выбор давления в ректификационной колонне обусловлен главным образом необходимым температурным режимом: давление в колонне повышается по сравнению с атмосферным, когда необходимо повысить температуру в колонне, или понижается путем создания вакуума, когда температура в колонне должна быть снижена.
Необходимость повышения температуры, а следовательно, и давления в ректификационных колоннах возникает при разделении компонентов с низкими температурами кипения, например, при ректификации таких низкомолекулярных углеводородов, как пропан, бутан, изобутан, пентан и др.
Путем подбора соответствующего давления в ректификационной колонне обеспечивают такой температурный режим, при котором для конденсации паров ректификата в качестве охлаждающих агентов можно использовать дешевые и легко доступные хладагенты — воду и атмосферный воздух. Так, например, при получении в качестве ректификата пропана при работе колонны под атмосферным давлением температура верха колонны будет равна — 42 °С, тогда как при повышении давления до 1,9 МПа она возрастет до +55 "С, что позволит использовать в конденсаторе воду.
Увеличение температуры верха колонны при соответствующем повышении в ней давления приводит к уменьшению поверхности конденсатора вследствие роста средней разности температур между конденсирующимися парами ректификата и охлаждающим агентом.
Вместе с тем при повышении давления в колонне увеличивается и температура остатка, отбираемого из низа колонны. Это приводит к увеличению поверхности кипятильника или к необходимости применения более высокотемпературного и более дорогого теплоносителя.
Кроме того, давление в ректификационной колонне может быть обусловлено также работой других аппаратов технологической установки, а также сопротивлением аппаратов и коммуникаций, расположенных после ректификационной колонны.
Понижение давления в ректификационной колонне путем создания вакуума позволяет снизить температуру в колонне, что бывает необходимо при разделении компонентов, обладающих высокими температурами кипения или термической нестабильностью. Так, например, благодаря созданию вакуума можно при температурах менее 400 "С осуществить ректификацию мазута, температура кипения которого при атмосферном давлении выше 500 оС, обеспечивая ведение процесса без заметного разложения. В случае ректификации с водяным паром применение вакуума позволяет существенно сократить расход водяного пара.
Давление системы влияет также на коэффициенты относительной летучести компонентов смеси. Для большинства смесей эта характеристика с понижением давления увеличивается. Увеличение коэффициента относительной летучести благоприятно сказывается на процессе ректификации, позволяя снизить количество орошения, уменьшить число тарелок в колонне или повысить четкость разделения компонентов.
Наиболее значительно ухудшаются условия ректификации в области высоких давлений, близких к критическому. В этом случае кривая равновесия фаз становится пологой, так как величина коэффициента относительной летучести приближается к единице.
Давление в ректификационной колонне влияет также на ее производительность. С увеличением давления удельная производительность колонны растет. Однако при этом необходима большая толщина стенки корпуса колонны, кроме того, увеличиваются затраты на перекачку сырья, орошения и др.
Из вышеизложенного следует, что величина давления в ректификационной колонне существенно влияет на ряд показателей ее работы, приводя к улучшению одних и ухудшению других. Поэтому при выборе давления в колонне в каждом конкретном случае необходимо проводить всесторонний анализ. При этом основным критерием, как правило, является обеспечение благоприятного режима.
При разделении бинарной смеси путем ректификации обычно достаточно одной простой колонны, чтобы получить заданные составы ректификата и остатка. Лишь в специальных случаях (получение чистых веществ и др.) приходится применять более сложные варианты колонн.
При разделении многокомпонентной смеси приходится выделять несколько целевых продуктов (фракций), к составу которых предъявляются определенные требования. Это обусловливает необходимость применения нескольких простых колонн, соединенных определенным образом, что и определяет последовательность выделения компонентов или соответствующих фракций из смеси. Поскольку каждая простая колонна делит смесь на два продукта, то для разделения смеси, состоящей из п компонентов (фракций), необходимо иметь N— 1 простых колонн. С увеличением числа компонентов системы возможное число вариантов взаимного соединения простых колонн быстро возрастает.
На рис. IV-30 приведены схемы вариантов соединения простых колонн: последовательный по потокам ректификатов, последовательный по потокам остатков, последовательно-параллельный и с рециркуляцией потоков при разделении многокомпонентной смеси на несколько продуктов (фракций).
Последовательное соединение колоннможет осуществляться как по потокам остатков, когда остаток данной колонны поступает на ректификацию в следующую, а остаток в виде готового продукта получают только в последней колонне (рис. IV-30, а), так и по потокам ректификатов, когда ректификат данной колонны направляется в следующую, а в качестве готового продукта выводится ректификат только из последней колонны (рис. IV-30, б).
Последовательно-параллельное соединение колонн(см. рис. IV-30, в) состоит в том, что колонны соединены последовательно: одна часть по потокам ректификатов, другая — по потокам остатков.
С рециркуляциейодного или нескольких продуктов при разделении многокомпонентной смеси применяют (см. рис. IV-30, г, д), если рециркулируемые потоки не являются товарными продуктами для данной технологической схемы.
Комбинируя приведенные выше варианты соединения простых колонн, изменяя последовательность выделения тех или иных компонентов, а также их отбор в виде ректификата или в виде остатка, можно получать различные схемы для ректификации многокомпонентной смеси.
Так (см. рис. IV-30), например, переход от последовательного по потокам ректификатов к последовательно-параллельному соединению простых колонн позволяет получить в виде ректификата как первый (колонна II), так и третий (колонна III) компоненты. Последовательное же соединение колонн по потокам остатков позволяет выделить три компонента в виде ректификатов. Это имеет важное практическое значение, когда к получаемым продуктам предъявляются специальные требования, например, по механическим примесям и др.
Выбор конкретного варианта соединения колонн обусловливается как технологическими требованиями к перерабатываемым продуктам, так и экономическими показателями, определяющими затраты на ректификацию.
Если смесь разделяют на меньшее число продуктов, чем содержится компонентов в смеси (некоторые компоненты могут быть выделены в виде фракций), то число колонн будет меньше, чем в случае выделения каждого компонента в отдельности. Это характерно для установок АВТ, вторичной перегонки бензинов, ректификации продуктов каталитического крекинга и др., где целевыми являются фракции, кипящие в сравнительно широком интервале температур.
На нефтеперерабатывающих заводах нашли применение сложные колонны, представляющие собой систему простых колонн, соединенных в один агрегат (рис. IV-31).
Такая сложная колонна отвечает схеме последовательного соединения простых колонн по потокам ректификатов (см. рис. IV-30, б). Она представляет собой колонну /, на которой как бы установлены концентрационные части колонн II и III. Таким образом, получилась одна основная колонна, включающая концентрационные части всех трех колонн и отгонную часть колонны I. Отгонные части колонн II и III выполнены в виде отдельных аппаратов, называемых отпарными колоннами или стриппинг-секциями. Отпарные колонны связаны с основной колонной потоками жидкости и пара.
Такая сложная колонна требует меньше места для своей установки и нуждается только в одном насосе для подачи орошения. Однако при такой конструкции увеличивается высота колонны и обслуживающих ее металлоконструкций. Кроме того, потоки всех секции колонны жестко взаимосвязаны, что осложняет четкое разделение продуктов Wu и Wlu и одновременное обеспечение их качества.
![]() |
Рис. 15.1. Схемы основных способов соединения простых колонн при ректификации многокомпонентной смеси:последовательное по потокам остатка; б — последовательное по потокам ректификата; в — последовательно-параллельное; г — с рециклом остатка; д — с рециклом ректификата; 1—Ш — условные номера колонн а —
F
![]() |
Рис. IV-31. Схема сложной колонны для ректификации четырехкомпонентной смеси:
1—111 — контуры, выделяющие части сложной колонны, аналогичные (по номерам) колоннам, приведенным на рис. IV-31, б
В такой сложной колонне процесс протекает следующим образом. Флегма, образованная при конденсации паров на верху колонны, последовательно перетекает с тарелки на тарелку . достигнув нижней тарелки этой колонны, флегма делится на два потока. Один поток отводится в отпарную секцию колонны III, где получается продукт Wm. Второй поток флегмыперетекает на верхнюю тарелку колонны II, являясь орошением для этой колонны.
Пары G'm из отгонной секции колонны III возвращаются под нижнюю тарелку концентрационной части этой колонны. Аналогично протекает процесс и в других колоннах II и /.
При отводе всего тепла только на верху сложной колонны поток орошения должен быть достаточным, чтобы обеспечить необходимое флегмовое число во всех нижерасположенных секциях колонны. Однако вследствие отбора боковых погонов в сложной колонне масса паров увеличивается сверху вниз, а масса орошения — снизу вверх. Таким образом, наибольшее флегмовое число в сложной ректификационной колонне соответствует верхней секции (III колонна), и в направлении сверху вниз оно уменьшается, что ухудшает процесс ректификации.
Для обеспечения более равномерного распределения потоков паров и флегмы по высоте сложной колонны, разгрузки вышележащих сечений и регенерации тепла съем части тепла с целью образования дополнительного потока флегмы производят промежуточным циркуляционным орошением в одном-двух сечениях на верху соответствующих простых колонн (рис. IV-32). Поток промежуточного циркуляционного орошения (ПЦО) прокачивается через регенеративный теплообменник, например нефти, и при более низкой температуре t , поступает на верхнюю тарелку концентрационной части соответствующей простой колонны. Поднимающиеся снизу пары контактируют с более холодной циркулирующей флегмой и частично конденсируются, образуя дополнительный поток флегмы, который присоединяется к потоку флегмы и создает поток орошения.
Массу ПЦО рассчитывают по уравнению (55). Обычно для организации ПЦО используются 2 — 4 тарелки.
Каждую секцию сложной колонны рассчитывают как соответствующую часть простой колонны, имея в виду, что пары ректификата секции, расположенной ниже, поступают на ректификацию в секцию, расположенную выше.
Применение сложных колонн оправдано в основном в тех случаях, когда требуется относительно невысокая четкость разделения, например, при выделении широких по температурам кипения фракций.
15.1 Особенности расчета много компонентных смесей
Схема потоков в простой колонне, разделяющей многокомпонентную смесь, принципиально не отличается от потоков в колонне для разделения бинарной смеси (рис. IV-5). Однако в отличие от бинарной системы в многокомпонентной смеси содержится компонент, имеющий самую низкую температуру кипения , т.е. НКК, компонент с наибольшей температурой кипения, т.е. ВКК, а также компоненты, которые по температурам кипения располагаются между НКК и ВКК. Это вносит целый ряд особенностей в расчет и поведение компонентов при ректификации.
При ректификации многокомпонентной смеси материальный и тепловой балансы для колонны в целом можно составить таким же образом, как и при ректификации бинарной смеси.
13 вопрос
Для проведения процесса ректификации необходимо в низ колонны подвести тепло. При этом часть жидкости, стекающей с нижней тарелки отгонной части колонны, испаряется, образуя необходимый для процесса ректификации встречный поток паров. Подвод тепла может быть осуществлен различными способами.
На установках для подвода тепла применяют змеевики или пучки труб, вмонтированные непосредственно в корпус колонны.. Змеевики и пучки труб целесообразно применять лишь при сравнительно небольшой поверхности теплообмена и при переработке чистых и некоррозионных сред.
Поэтому в промышленности наиболее часто реализуются способы подвода тепла в следующих аппаратах: подогревателе с паровым пространством (парциальный испаритель); теплообменном аппарате без парового пространства с последующим ОИ нагретого потока в низу колонны (так называемая горячая струя).
Подогреватель с паровым пространством. Схема этого способа подвода тепла дана на рис. 11,г. При подводе тепла в низ колонны кипятильником (рибойлером) осуществляется дополнительный подогрев кубового продукта в выносном кипятильнике, где он частично испаряется. Образовавшиеся пары возвращаются под нижнюю тарелку колонны. Характерной особенностью этого способа является наличие в кипятильнике постоянного уровня жидкости и парового пространства над этой жидкостью. По своему разделительному действию кипятильник эквивалентен одной теоретической тарелке. Тепло, подводимое в нижнюю часть колонны ограничено температурой теплоносителя, в случае использования водяного пара температура не превышает 180оС, если в качестве теплоносителя используется высококипящие масла, то температура может достигать 250оС.Этот способ подвода применяется на установках фракционирования газов, при стабилизации бензинов. При высокой температуре низа колонны подвод тепла через кипятильник в целом ряде случаев требует применения специальных высокотемпературных теплоносителей
Горячая струя. Этот способ подвода тепла (рис. 11,д) применяется в тех случаях, когда нагрев остатка обычными теплоносителями (водяной пар и др.) не представляется возможным или целесообразным. При подводе тепла в низ колонны трубчатой печью часть кубового продукта прокачивается через трубчатую печь, и подогретая парожидкостная смесь (горячая струя) вновь поступает в низ колонны ..
Этот способ применяют при необходимости обеспечения сравнительно высокой температуры низа колонны., например при перегоне нефти или мазута.
14 вопрос
Перепад давления. Известное влияние на эффективность колонки оказывает перепад давления в ней. Чтобы пары проходили через колонку, они должны преодолеть сопротивление смоченной насадки или слоев жидкости на тарелках. Поэтому в кубе всегда должно быть некоторое избыточное (по отношению к конденсатору) давление, величина которого зависит прежде всего от типа насадки (или тарелки) и количества флегмы в ней, а также и от физических свойств перегоняемой жидкости*. Между тем у большинства жидких смесей, приближающихся к идеальным, увеличение давления ухудшает результаты ректификации. Кроме того, изменение давления по высоте колонны или колонки влияет на объем паров, а следовательно, и на скорость и характер их движения. Практика показала, что чем меньше перепад давления в колонке, тем обычно лучше протекает процесс ректификации. Поэтому при конструировании колонок, при прочих равных условиях, следует отдавать предпочтение насадкам, создающим малый перепад давления. Особенно важно это для вакуум-разгонок.
* (О влиянии орошения на величину задержки и гидравлические свойства насадок см.60.)
Из рис. 15 видно, что для получения дестиллатов с одинаковым содержанием нижекипящего компонента, равным хд, при перегреве колонки в кубе должна находиться смесь, более богатая нижекипящим компонентом (х1), нежели при ректификации в адиабатических условиях. Это означает, что колонка при перегреве работает с меньшим эффектом. Из рисунка следует далее, что при охлаждении центральной трубки (дефлегмация) колонка должна работать лучше.
Однако при этом надо учитывать, что для каждой колонки имеется оптимальный режим работы. При дефлегмации или нижняя, или верхняя часть оказывается вне этого оптимального режима, что снижает эффективность колонки в целом. Перегрев значительно сильнее влияет на уменьшение эффективности колонки, нежели охлаждение.
Во избежание перегрева разгонку следует вести "с небольшой дефлегмацией. При хорошей теплоизоляции достаточно, чтобы температура прилегающих к колонке стенок теплоизолирующего устройства была все время на 1 - 5° ниже температуры центральной трубки.
15 вопрос
При разделении бинарной смеси путем ректификации обычно достаточно одной простой колонны, чтобы получить заданные составы ректификата и остатка. Лишь в специальных случаях (получение чистых веществ и др.) приходится применять более сложные варианты колонн.
При разделении многокомпонентной смеси приходится выделять несколько целевых продуктов (фракций), к составу которых предъявляются определенные требования. Это обусловливает необходимость применения нескольких простых колонн, соединенных определенным образом, что и определяет последовательность выделения компонентов или соответствующих фракций из смеси. Поскольку каждая простая колонна делит смесь на два продукта, то для разделения смеси, состоящей из п компонентов (фракций), необходимо иметьN— 1 простых колонн. С увеличением числа компонентов системы возможное число вариантов взаимного соединения простых колонн быстро возрастает.
На рис. IV-30 приведены схемы вариантов соединения простых колонн: последовательный по потокам ректификатов, последовательный по потокам остатков, последовательно-параллельный и с рециркуляцией потоков при разделении многокомпонентной смеси на несколько продуктов (фракций).
Последовательное соединение колонн может осуществляться как по потокам остатков, когда остаток данной колонны поступает на ректификацию в следующую, а остаток в виде готового продукта получают только в последней колонне (рис.IV-30,а), так и по потокам ректификатов, когда ректификат данной колонны направляется в следующую, а в качестве готового продукта выводится ректификат только из последней колонны (рис.IV-30, б).
Последовательно-параллельное соединение колонн (см. рис. IV-30, в) состоит в том, что колонны соединены последовательно: одна часть по потокам ректификатов, другая — по потокам остатков.
С рециркуляцией одного или нескольких продуктов при разделении многокомпонентной смеси применяют (см. рис.IV-30,г, д), если рециркулируемые потоки не являются товарными продуктами для данной технологической схемы.
Комбинируя приведенные выше варианты соединения простых колонн, изменяя последовательность выделения тех или иных компонентов, а также их отбор в виде ректификата или в виде остатка, можно получать различные схемы для ректификации многокомпонентной смеси.
Так (см. рис. IV-30), например, переход от последовательного по потокам ректификатов к последовательно-параллельному соединению простых колонн позволяет получить в виде ректификата как первый (колоннаII), так и третий (колоннаIII) компоненты. Последовательное же соединение колонн по потокам остатков позволяет выделить три компонента в виде ректификатов. Это имеет важное практическое значение, когда к получаемым продуктам предъявляются специальные требования, например, по механическим примесям и др.
Выбор конкретного варианта соединения колонн обусловливается как технологическими требованиями к перерабатываемым продуктам, так и экономическими показателями, определяющими затраты на ректификацию.
Если смесь разделяют на меньшее число продуктов, чем содержится компонентов в смеси (некоторые компоненты могут быть выделены в виде фракций), то число колонн будет меньше, чем в случае выделения каждого компонента в отдельности. Это характерно для установок АВТ, вторичной перегонки бензинов, ректификации продуктов каталитического крекинга и др., где целевыми являются фракции, кипящие в сравнительно широком интервале температур.
На нефтеперерабатывающих заводах нашли применение сложные колонны, представляющие собой систему простых колонн, соединенных в один агрегат (рис.IV-31).
Такая сложная колонна отвечает схеме последовательного соединения простых колонн по потокам ректификатов (см. рис. IV-30,б). Она представляет собой колонну /, на которой как бы установлены концентрационные части колоннII иIII. Таким образом, получилась одна основная колонна, включающая концентрационные части всех трех колонн и отгонную часть колонныI. Отгонные части колоннII иIII выполнены в виде отдельных аппаратов, называемыхотпарными колоннами илистриппинг-секциями. Отпарные колонны связаны с основной колонной потоками жидкости и пара.
Такая сложная колонна требует меньше места для своей установки и нуждается только в одном насосе для подачи орошения. Однако при такой конструкции увеличивается высота колонны и обслуживающих ее металлоконструкций. Кроме того, потоки всех секции колонны жестко взаимосвязаны, что осложняет четкое разделение продуктов Wu иWlu и одновременное обеспечение их качества.
Рис. 15.1. Схемы основных способов соединения простых колонн при ректификации многокомпонентной смеси:последовательное по потокам остатка;б — последовательное по потокам ректификата;в — последовательно-параллельное; г — с рециклом остатка;д — с рециклом ректификата;1—Ш — условные номера колонн а —
F
Рис. IV-31. Схема сложной колонны для ректификации четырехкомпонентной смеси:
1—111 — контуры, выделяющие части сложной колонны, аналогичные (по номерам) колоннам, приведенным на рис.IV-31,б
В такой сложной колонне процесс протекает следующим образом. Флегма, образованная при конденсации паров на верху колонны, последовательно перетекает с тарелки на тарелку . достигнув нижней тарелки этой колонны, флегма делится на два потока. Один потокотводится в отпарную секцию колонныIII, где получается продуктWm. Второй поток флегмыперетекает на верхнюю тарелку колонныII, являясь орошением для этой колонны.
Пары G'm из отгонной секции колонныIII возвращаются под нижнюю тарелку концентрационной части этой колонны. Аналогично протекает процесс и в других колоннахII и /.
При отводе всего тепла только на верху сложной колонны поток орошения должен быть достаточным, чтобы обеспечить необходимое флегмовое число во всех нижерасположенных секциях колонны. Однако вследствие отбора боковых погонов в сложной колонне масса паров увеличивается сверху вниз, а масса орошения — снизу вверх. Таким образом, наибольшее флегмовое число в сложной ректификационной колонне соответствует верхней секции (III колонна), и в направлении сверху вниз оно уменьшается, что ухудшает процесс ректификации.
Для обеспечения более равномерного распределения потоков паров и флегмы по высоте сложной колонны, разгрузки вышележащих сечений и регенерации тепла съем части тепла с целью образования дополнительного потока флегмы производят промежуточным циркуляционным орошением в одном-двух сечениях на верху соответствующих простых колонн (рис.IV-32). Поток промежуточного циркуляционного орошения (ПЦО) прокачивается через регенеративный теплообменник, например нефти, и при более низкой температуреt , поступает на верхнюю тарелку концентрационной части соответствующей простой колонны. Поднимающиеся снизу пары контактируют с более холодной циркулирующей флегмой и частично конденсируются, образуя дополнительный поток флегмы, который присоединяется к потоку флегмыи создает поток орошения.
Массу ПЦО рассчитывают по уравнению (55). Обычно для организации ПЦО используются 2 — 4 тарелки.
Каждую секцию сложной колонны рассчитывают как соответствующую часть простой колонны, имея в виду, что пары ректификата секции, расположенной ниже, поступают на ректификацию в секцию, расположенную выше.
Применение сложных колонн оправдано в основном в тех случаях, когда требуется относительно невысокая четкость разделения, например, при выделении широких по температурам кипения фракций.
15.1 Особенности расчета много компонентных смесей
Схема потоков в простой колонне, разделяющей многокомпонентную смесь, принципиально не отличается от потоков в колонне для разделения бинарной смеси (рис. IV-5). Однако в отличие от бинарной системы в многокомпонентной смеси содержится компонент, имеющий самую низкую температуру кипения , т.е. НКК, компонент с наибольшей температурой кипения, т.е. ВКК, а также компоненты, которые по температурам кипения располагаются между НКК и ВКК. Это вносит целый ряд особенностей в расчет и поведение компонентов при ректификации.
При ректификации многокомпонентной смеси материальный и тепловой балансы для колонны в целом можно составить таким же образом, как и при ректификации бинарной смеси.
16 вопрос
Цели азеотропной ректификации те же, что и экстрактивной – разделение смесей компонентов с близкими летучестями и азеотропных смесей. Для разделения применяется разделяющий агент, но в отличие от экстрактивной ректификации, он образует в простейшем случае с одним из компонентов исходной смеси азеотроп с минимальной температурой кипения. В дальнейшем эта азеотропная смесь при понижении температуры расслаивается. И это позволяет отделить составляющие ее компоненты отстаиванием, если они практически нерастворимы друг в друге. Схема установки азеотропной ректификации бинарной смеси представлена на рис.14.34.
Исходная смесь компонентов А и В подается в колонну 1, орошаемую флегмой и разделяющим агентом С. Компонент С с компонентом А образует азеотропную смесь с минимальной температурой кипения, пары которой конденсируются в дефлегматоре 2, затем делятся в делителе 4 на флегму и дистиллят. Дистиллят охлаждается в холодильнике 5, после чего расслаивается в отстойнике 6. Компонент А отводится в виде готового продукта, а разделяющий агент С нагревается в подогревателе 7 и вновь подается на орошение колонны. Практически чистый компонент В отводится в виде кубового остатка.
Если сравнить схемы процессов экстрактивной и азеотропной ректификации, то преимуществом экстрактивной будут являться меньшие тепловые затраты в колонне 1, так как нет необходимости испарения разделяющего агента, он отводится в виде кубового остатка, а при азеотропной ректификации разделяющий агент удаляется в виде дистиллята. В то же время для азеотропной ректификации не требуется второй ректификационной колонны и тепловых затрат на ее функционирование, так как разделяющий агент отделяется отстаиванием.
Рис.14.34. Схема установки азеотропной ректификации бинарной смеси: А, В – компоненты исходной смеси, С – разделяющий агент, 1 – колонна, 2 – дефлегматор; 3 – кипятильник; 4 – делители; 5 – холодильник, 6 – отстойник, 7 – подогреватель.
Подбор разделяющего агента для азеотропной ректификации, позволяющий реализовать процесс по такой простой схеме (рис. 14.34) не всегда возможен. Поэтому процесс иногда проводят с разделяющим агентом, образующим азеотропную смесь с максимальной температурой кипения. В этом случае она отбирается в виде кубового остатка. Кроме того, компоненты образующейся азеотропной смеси могут и при охлаждении обладать частичной растворимостью, то есть при расслоении фазы будут содержать не чистые компоненты, а их смеси. Иногда возможно образование тройного азеотропа разделяющего агента с двумя компонентами исходной смеси. Все это затрудняет регенерацию разделяющего агента и требует применения кроме отстаивания таких процессов, как ректификация или экстракция. Окончательный выбор способа разделения исходной смеси решается на основе экономического анализа.
17 вопрос
В нефтеперерабатывающей и химической промышленности СССР нашли применение в основном стандартные конструкции тарелок, разработанные ВНИИНЕФТЕМАШем (клапанные прямоточные, из S-элементов, ситчатые из просечного листа с отбойниками, решетчатые провальные, желобчатые колпачковые) и УКРНИИХИММАШем (колпачковые капсульные, провальные решетчатые, ситчатые, жалюзийно-клапанные).
При этом, до 50-х годов в нефтеперерабатывающей промышленности находились в эксплуатации в основном колонны с колпачковыми тарелками различных конструктивных модификаций; в отдельных случаях применялись ситчатые тарелки.
После 50-е годов появились новые различные конструкции тарелок, нашедшие широкое применение в промышленности, к которым можно отнести [5]:
· струйные тарелки с вертикальными перегородками;
· комбинированные ситчато-клапанные и ситчато-прямоточные тарелки;
· тарелки из S-образных элементов с отбойниками;
· тарелки из S-образных элементов с прямоточными клапанами (ТSK);
· решетчатые тарелки провального типа с отогнутыми кромками щелей;
· решетчатые тарелки провального типа из труб;
· струйные тарелки с компенсацией прямоточного движения фаз и т.д.
В большинстве случаев тарелки новых конструкций имели существенные преимущества перед колпачковыми и ситчатыми тарелками, что позволило применить их для различных процессов нефтепереработки.
Однако, в настоящее время наряду с самыми современными конструкциями, в эксплуатации находятся тарелки таких типов (желобчатые и др.), которые хотя и обеспечивают получение необходимых продуктов, но не могут быть рекомендованы для современных производств. Конструкции и принцип работы тарелок рассмотрим на примере наиболее распространенных типов тарелок: колпачковых, клапанных и провальных.
Колпачковые тарелки
К колпачковым относят тарелки с круглыми колпачками, с желобчатыми, с S-образными элементами и т.д.
Колпачковые тарелки относятся к группе барботажных. Рассмотрим особенности работы барботажной тарелки на примере колпачковой тарелки с круглыми (капсульными) колпачками, схема и общий вид которой приведены на рисунках 2.14 и 2.15.
а – общий вид тарелки; б – схема барботажа газа в зоне контакта
Рисунок 2.14 – Схема работы барботажной тарелки
С круглыми колпачками
Основной частью колпачковой тарелки (рисунок 2.15) является стальной диск 2 (или полотно тарелки) с отверстиями для паровых патрубков 6. Патрубки приварены к диску. Над патрубками установлены колпачки 5 диаметром 60, 80 или 100 мм. Колпачки имеют прорези высотой 15, 20 или 30 мм.
![]() | ![]() |
Рисунок 2.15 – Колпачковая тарелка
Для создания необходимого уровня жидкости на тарелке ее снабжают сливной перегородкой 3. Переливная перегородка 1 образует переливной карман, в который погружается сливная планка 4 тарелки, расположенной выше.
Применяют два варианта крепления колпачка к тарелке. В исполнении 1 положение колпачка можно регулировать по высоте, в исполнении 2 регулирование невозможно, и нижние кромки прорезей в этом случае упираются в полотно тарелки. Тарелка работает следующим образом. Жидкость поступает на полотно тарелки из переливного устройства. Поступающая жидкость заполняет тарелку на высоту, определяемую сливной перегородкой 3, при этом прорези колпачков должны быть погружены в жидкость. Пар проходит через паровые патрубки, щели колпачков и барботирует сквозь слой жидкости.
Газ и жидкость взаимодействуют в перекрестном токе: жидкость движется по тарелке от переливного кармана к сливной перегородке и далее на расположенную ниже тарелку, а газ – вверх по оси колонны.
Стенка переливного устройства погружена в жидкость, находящуюся на нижележащей тарелке, что обеспечивает в колонне соответствующий гидравлический затвор.
Колпачковые тарелки можно изготовлять из чугуна, меди, керамики, углеграфита, пластмасс и др.
Тарелки с капсульными колпачками имеют относительно высокий КПД (0,75–0,80) и работают в широком диапазоне производительностей по газу. Их можно использовать при нестабильных нагрузках по жидкости и пару. К недостаткам этих тарелок следует, прежде всего, отнести значительные металлоемкость и трудоемкость изготовления.
Колпачковые тарелки с капсульными колпачками до недавнего времени считали лучшими контактными устройствами для ректификационных и абсорбционных аппаратов благодаря простоте эксплуатации и универсальности.
К недостаткам колпачковых тарелок следует отнести низкую удельную производительность, относительно высокое гидравлическое сопротивление, большую металлоемкость, сложность и высокую стоимость изготовления.
В ректификационных аппаратах нефтеперерабатывающих производств используют тарелки с желобчатыми (туннельными) колпачками (рисунок 2.16).
![]() | ![]() |
Рисунок 2.16 – Тарелка с желобчатыми (туннельными) колпачками
Такие тарелки собирают из штампованных желобов 1, уложенных по ходу жидкости на опорные уголки 2 и накрытых колпачками 3 так, что между ними образуются паровые каналы. Для равномерного распределения пара колпачки в нижней части имеют трапецеидальные прорези. Колпачки крепят на полотне тарелки шпильками 4. Для равномерного распределения жидкости на тарелке сливную планку 5 также выполняют с прорезями.
Основной эксплуатационный недостаток желобчатых тарелок заключается в малой площади барботажа и в неполном использовании площади поперечного сечения колонны для создания зеркала барботажа.
Колпачки тарелки регулируют по высоте с учетом нагрузки колонны по жидкости, чтобы не допустить чрезмерных гидравлических сопротивлений.
В настоящее время в нефтеперерабатывающих колоннах используют и тарелки с S-образными элементами 4 (рисунок 2.17), установленными перпендикулярно направлению движения жидкости на тарелке. Тарелки из S-образных элементов являются разновидностью колпачковых тарелок и состоят из отдельных элементов, каждый из которых образует одновременно полость для паров и жидкости.
Для того чтобы закрыть каналы с торцов и увеличить жесткость тарелки, между S-образными элементами 4 устанавливают пластины 5.
![]() | ![]() |
1 – корпус колонны; 2 – сливная перегородка; 3 – паровой элемент; 4 – S-образный элемент; 5 – поперечные перегородки; 6 – разъемный S-образный элемент; 7 – жидкостный элемент; 8 – отверстие для слива жидкости; 9 – опорное кольцо; 10 – струбцина; 11 – заглушки; 12 – прорези в S-образных элементах
Рисунок 2.17 – Конструкция тарелки из S-образных элементов
Узел крепления S-образного элемента к корпусу аппарата показан на рисунке 2.18.
Рисунок 2.18 – Узел крепления S-образного элемента
В зависимости от диаметра аппарата такие тарелки бывают одно- и многосливными. Характерная особенность этих тарелок состоит в том, что пар выходит из контактных элементов в направлении движения жидкости
Это способствует уменьшению разностей уровней жидкости на тарелке у сливной и переливной перегородок.
Металлоемкость тарелок с S-образными элементами почти вдвое меньше, а производительность на 20–30% больше по сравнению с тарелками с капсульными колпачками. Эффективность сравниваемых тарелок примерно одинаковая (КПД равен 0,60–0,80). Оптимальная нагрузка по газу для этой тарелки на 10–25% меньше, чем для колпачковой.
Жидкость по тарелке движется под напором пара, выходящего из прорезей колпачковых частей, направленных в одну сторону. Взаимное движение паров и жидкостей по тарелке обеспечивает ее устойчивую работу при различных нагрузках и повышенную производительность по сравнению с другими колпачковыми тарелками. В то же время потери напора на тарелках из S-образных элементов значительны, поэтому применение их в вакуумных колоннах нецелесообразно.
Для повышения диапазона устойчивой работы и производительности таких тарелок S-образные элементы 2 (рисунок 2.19 а) снабжают прямоточными клапанами 1 прямоугольной формы, размещенными на верхней площадке S-образных элементов. Для увеличения жесткости тарелки устанавливают пластины 3. По производительности эти тарелки примерно на 10 % превосходят клапанные прямоточные.
![]() ![]() | ![]() |
а) тарелка с S-образными элементами и клапанами | б) клапанная тарелка с прямоугольными клапанами |
Рисунок 2.19 Типы клапанных тарелок
Клапанные тарелки
Клапанные тарелки также широко применяют в нефтехимической промышленности. Основные преимущества этих тарелок – способность обеспечить эффективный массообмен в большом интервале рабочих нагрузок, несложность конструкции, низкая металлоемкость и невысокая стоимость.
Разработано множество разновидностей клапанных тарелок различной геометрической формы (дисковые, прямоугольные и т.д. – рисунки 2.19 б, 2.20), с балластом или без него, с отбойными элементами или без них и т.д.
![]() | ![]() |
а) колонна с клапанной тарелкой с прямоугольными клапанами | б) прямоугольный клапан |
Рисунок 2.20 – Тарелка клапанная с прямоугольными клапанами
Клапанные тарелки работают в режиме прямоточного или перекрестного движения фаз. В отечественной промышленности наиболее распространены клапанные прямоточные тарелки с дисковыми клапанами. На клапанной прямоточной тарелке (рисунок 2.21) в шахматном порядке расположены отверстия, в которых установлены саморегулирующиеся дисковые клапаны диаметром 50 мм, способные подниматься при движении пара (газа) на высоту до 6–8 мм.
![]() | ![]() |
А) б)
Рисунок 2.21 – Клапанно-прямоточная тарелка (а)
И дисковый клапан (б)
Дисковый клапан снабжен тремя направляющими, расположенными в плане под углом 45°, две из этих направляющих имеют большую длину. Кроме того, на диске клапана штамповкой выполнены специальные упоры, обеспечивающие начальный зазор между диском и тарелкой; это исключает возможность «прилипания» клапана к тарелке (рисунок 2.21, положение Ι). При небольшой производительности по пару поднимается легкая часть клапана (положение ΙΙ) и пар выходит через щель между клапаном и полотном тарелки в направлении, противоположном направлению движения жидкости по тарелке. С увеличением скорости пара клапан поднимается и зависает над тарелкой (положение ΙΙΙ); теперь пар барботирует в жидкость через кольцевую щель под клапаном. При дальнейшем увеличении производительности по пару клапан занимает положение, при котором пар выходит в направлении движения жидкости, уменьшая разность уровней жидкости на тарелке (положение IV). При этом короткая направляющая фиксируется в специальном вырезе на кромке отверстия, обеспечивая заданное положение клапана при его подъеме.
В зависимости от напора паров клапаны поднимаются на различную высоту в пределах, определяемой высотой удерживающих скоб. На некоторых тарелках клапаны не накрываются скобами, а снабжаются рожками (направляющими), которые при подъеме клапана упираются в нижнюю поверхность тарелки.
В отличие от тарелок, работающих в статическом режиме, т.е. при неизменном расстоянии между конструктивными элементами (например, между желобом и колпачком), клапанные тарелки работают в динамическом режиме.
В зависимости от напора восходящих по колонне паров клапаны поднимаются на соответствующую величину (обычно на 4–20 мм), регулируя тем самым площадь свободного сечения тарелки. Это позволяет поддерживать скорость паров примерно постоянной при изменении общей нагрузки на колонну, т.е. осуществлять наилучший режим массопередачи. Конструкция удерживающих скоб и клапанов такова, что обеспечивает их подъем с наклоном к поверхности тарелки и, следовательно, лучший баработаж паров через жидкость на тарелке.
Для большего повышения эффективности массообмена клапаны можно снабжать тангенциально расположенными щелями. При этом выходящие через них пары могут вращать клапан.
Важным эксплуатационным показателем клапанных тарелок является вес каждого клапана, который подбирают таким образом, чтобы при возможных колебаниях нагрузок клапан работал в заданном диапазоне подъема. В тех случаях, когда возможны очень большие изменения нагрузок, тарелки снабжают одновременно клапанами различного веса. В таких тарелках при малых нагрузках открываются легкие клапаны, а затем, по мере нарастания нагрузок, – более тяжелые.
Эффективность клапанных прямоточных тарелок (КПД) 0,70–0,85. В области саморегулируемой работы тарелки обладают относительно небольшим гидравлическим сопротивлением.
В настоящее время активно продолжаются работы по разработке новых конструкций клапанных тарелок. В частности, известны тарелки FLEXITRAY, которые могут быть применены для всех процессов с парожидкостным контактом (рисунок 2.22).
Рисунок 2.22 – Клапанные тарелки FLEXITRAY
Тарелки состоят из перфорированных панелей из металла с круглыми подвижными или фиксированными клапанами. Ряды клапанов в шахматном порядке расположены параллельно переливной планке. В тарелке осуществляется горизонтальное движение паров вдоль полотна тарелки.
Преимущества данных тарелок:
- высокая эффективность – полноценный контакт паров и жидкости;
- производительность до 10% выше, чем для ситчатых тарелок;
- равномерное распределение паров;
- малый перепад давления;
- широкий рабочий диапазон;
- малое флегмовое число при заданном диаметре колонны;
- возможность уменьшения диаметра колонны при заданном расходе сырья;
- экономическая эффективность: низкая стоимость, простой монтаж, несложный ремонт;
- универсальность.
Фирмой KOCH-GLITSCH также разработаны различные разновидности клапанов, некоторые из которых приведены на рисунке 2.23
![]() | ![]() |
|
клапаны подвижные
Рисунок 2.23 – Конструкции клапанов фирмы KOCH-GLITSCH
Для применения в процессах разделения под вакуумом и умеренным давлением весьма перспективны клапанные балластные тарелки прямоугольной формы с общим для всех клапанов подвижным балластом. Наличие подвижного балласта обеспечивает равномерное открытие всех клапанов при минимальных нагрузках по пару и регулируемый переход от перекрестного движения фаз к прямоточному при больших нагрузках. В результате клапанная балластная тарелка по сравнению с клапанной безбалластной имеет на 15–20% более высокую эффективность разделения во всем диапазоне нагрузок и на 10–15% меньше.
Использование клапанов прямоугольной формы вместо круглых позволяет примерно на 30% снизить расход металла при их изготовлении, а благодаря большим размерам клапанов (один прямоугольный клапан эквивалентен восьми круглым) – на 25% уменьшить трудовые затраты на сборку тарелки.
Над отверстием тарелки 1 (рисунок 2.24) на специальных ножках установлены ограничители подъема 4, а внутри их – на ножках 7 легкий клапан 5 и балласт 2. Для исключения прилипания клапана к балласту имеются упоры 3 и 6. При малой производительности по газу тарелка работает как обычная с дисковыми клапанами меньшей массы; при увеличении нагрузки клапан 5 упирается в балласт и работает совместно с ним как один утяжеленный клапан.
Рисунок 2.24 – Клапанная балластная тарелка
Балластные клапанные тарелки можно выполнять как с индивидуальным, так и с групповым балластом. Примером последнего варианта могут служить балластные тарелки ректификационных колонн (рисунок 2.25). Такая тарелка 1 имеет расположенные в несколько рядов прямоугольные вырезы, закрытые клапанами 2 прямоугольной формы.
Большие размеры клапанов (154×45 мм) позволяют уменьшить их число по сравнению с дисковыми клапанами в 2–4 раза. Над клапанами расположен общий подвижный балласт 3, выполненный из прутка диаметром 8 мм.
Рисунок 2.25 – Тарелка с групповым балластом
При работе таких тарелок вначале поднимается пластина клапана, затем она упирается в балласт и поднимается вместе с ним до упора в головку винта 4.
Клапанные балластные тарелки получают за последнее время все более широкое распространение, особенно для работы в условиях значительно меняющихся скоростей газа, и постепенно вытесняют старые конструкции контактных устройств.
Клапанные тарелки массообменные колонных аппаратов отличаются широким диапазоном нагрузки по газу (пару) при сохранении стабильной эффективности массообмена. Вместе с тем традиционные конструкции клапанных контактных цементов (круглой, прямоугольной, трапециевидной формы) имеют недостатки в организации гидродинамического процесса взаимодействия фаз.
В этих конструкциях газ выходит из-под диска клапана в основном в виде сплошной утолщенной струи, что приводит к ограничению площади поверхности контакта фаз из-за проскока части газа без взаимодействия с жидкостью и повышению уноса жидкости с тарелки из-за большой скорости локального выхода газовых струй с поверхности газожидкостного слоя. Кроме этого, газовый поток формируется непосредственно под верхней плоскостью клапана, в результате чего нижний, прилегающий к полотну тарелки слой жидкости практически исключается из взаимодействия с газом. В этом случае возможно течение жидкости от входа на тарелку до переливного порога без явного участия в массообмене.
Таким образом, формирование газового потока в виде сплошной струи, выходящей из-под диска клапана, ограничивает площадь поверхности контакта фаз и снижает эффективность массообмена.
Кроме того, для всех клапанов характерен общий недостаток – возможность засорения или закоксования клапанов, в результате чего они «прихватываются» и не работают в динамическом режиме.
Тарелки провального типа
К тарелкам провального типа относят обычно ситчатые и решетчатыетарелки.
Ситчатыетарелки со сливным устройством применяют в колонных аппаратах диаметром 400–4000 мм при расстоянии между тарелками от 200 мм и более. Основной элемент таких тарелок – металлический диск с отверстиями диаметром 2–6 мм, расположенными по вершинам равносторонних треугольников (рисунок 2.26).
![]() | | |
элемент ситчатой тарелки | ситчатая тарелка с переливными трубами |
Рисунок 2.26 – Ситчатая тарелка
В колоннах диаметром более 800 мм тарелки состоят из отдельных секций. По креплению секций тарелки к корпусу и устройству переливов такие колонны аналогичны аппаратам с колпачковыми и клапанными тарелками.
Преимущество ситчатой тарелки – большое свободное (т.е. занятое отверстиями) сечение тарелки, а, следовательно, и высокая производительность по пару, простота изготовления, малая металлоемкость. По производительности по пару (газу) эти тарелки на 30–40% превосходят колпачковые. Недостаток – высокая чувствительность к точности установки. Аппараты с ситчатыми тарелками не рекомендуется использовать для работы на загрязненных средах; это может вызвать забивание отверстий.
Для уменьшения гидравлического сопротивления и расширения диапазона устойчивой работы ситчатых тарелок их комбинируют с клапанными устройствами (рисунок 2.27), в результате повышается эффективность работы тарелки при малой и большой производительности по пару. При малых нагрузках тарелка работает как обычная ситчатая, с увеличением нагрузки открывается клапан 2 и между клапаном и тарелкой 1 образуется щель, откуда под некоторым углом к горизонтали выходит пар, обеспечивая перемещение жидкости по тарелке в направлении слива и уменьшая разность уровней жидкости на тарелке.
Рисунок 2.27 – Элемент ситчато-клапанной тарелки
Ситчато-клапанная тарелка обеспечивает большой диапазон устойчивой работы при небольшом гидравлическом сопротивлении, что делает ее пригодной для процессов, протекающих под вакуумом.
Ситчатые тарелки с просечно-вытяжными отверстиями (рисунок 2.28) используют в колонных аппаратах диаметром 1200–4000 мм. Такие тарелки состоят из отдельных секций, изготовляемых из листа толщиной 2–3 мм с просечно-вытяжными отверстиями. Тарелка работает как струйная прямоточная. Для уменьшения брызгоуноса над тарелкой устанавливают отбойные элементы 2 под углом 60°.
![]() | ![]() |
а) ситчатая тарелка с просечно-вытяжными отверстиями и отбойными элементами | б) ситчатая тарелка с просечными элементами (выштампованные просечки) с перфорированными вертикальными перегородками |
Рисунок 2.28 – Различные типы ситчатых тарелок
Свободное сечение тарелки, выбираемое из условия отсутствия «провала» жидкости, должно быть достаточно большим (не менее 30% сечения колонны), чтобы тарелка обладала, невысоким гидравлическим сопротивлением. Благодаря этому такие тарелки используют в вакуумных колоннах. Минимальное расстояние между тарелками в колонне 450 мм.
Одним из направлений технического прогресса в нефтеперерабатывающей промышленности – создание контактных устройств, обладающих высокой производительностью по жидкости и пару, в частности продольным и поперечным секционированием.
Известно, что производительность тарелок повышается при контактировании фаз в прямотоке. Однако при прямоточном движении и большой скорости пара (газа) жидкость смещается в направлении сливного кармана, что затрудняет работу сливных устройств.
Для компенсации прямоточного движения фаз и исключения его распространения на всю тарелку можно устанавливать на тарелке продольные и поперечные перегородки, обеспечивающие зигзагообразное движение жидкости от перелива к сливу, а также создающие условия для движения потоков парожидкостной смеси по тарелке в противоположных или пересекающихся направлениях.
Примером может служить продольно-секционированная тарелка с просечными элементами (рисунок 2.28б). На полотне тарелки выштампованы просечки, отогнутые под углом. Тарелка секционирована вдоль потока жидкости вертикальными перегородками, причем для создания постоянного гидравлического сопротивления по всей тарелке перегородки перфорированы.
Ситчатые тарелки наиболее распространены в качестве контактных устройств ректификационных колонн воздухоразделительных установок, работающих при низкой температуре.
В аппаратах небольшого диаметра применяют S-образные ситчатые тарелки (рисунок 2.29).
![]() | ![]() |
Рисунок 2.29 – Ситчатая тарелка с S-образной перегородкой
Такая тарелка представляет собой перфорированный лист 1, к которому припаяна S-образная перегородка 3, делящая тарелку на две части. Стекающая с верхней тарелки жидкость через прорези в сливном стакане 2 и далее через переливную перегородку 5 поступает на тарелку и движется в направлении, указанном стрелками, контактируя с паром, поднимающимся через отверстия в листе 1. Подойдя к перегородке 3 с другой стороны, жидкость стекает на следующую тарелку через сливную перегородку 4 и сливной стакан.
Решетчатые провальные тарелки (рисунок 2.30) используют в установках, рабочая производительность которых отклоняется от расчетной не более чем на 25%.
![]() | ![]() |
Рисунок 2.30 – Решетчатая провальная тарелка
К преимуществам этих тарелок следует, прежде всего, отнести простоту конструкции и малую металлоемкость. Кроме того, тарелки имеют большую пропускную способность по жидкости и, при достаточной ширине щели, могут быть использованы для обработки загрязненных жидкостей, оставляющих осадок на тарелке. По эффективности решетчатые провальные тарелки обычно не уступают тарелкам с переливом.
К недостаткам относятся узкий диапазон устойчивой работы и сложность обеспечения равномерного распределения орошения по поверхности тарелок в начале процесса. Тарелки этого типа гораздо более чувствительны к изменению нагрузок по жидкости и пару и имеют более узкий диапазон рабочих нагрузок, чем тарелки со специальными переливными устройствами. При небольшой паровой нагрузке напор паров недостаточен для образования слоя жидкости на тарелке. При больших паровых нагрузках сопротивление течению жидкости через отверстия тарелки становится столь значительным, что пена заполняет практически все межтарельчатое пространство и нормальный переток жидкости с тарелки на тарелку нарушается. При этом резко возрастает гидравлическое сопротивление потоку паров. Такой режим работы называется захлебыванием и определяет предельные паровую и жидкостную нагрузки колонны.
Конструктивно тарелка представляет собой плоский, перекрывающий все сечение колонны диск 1 с выштампованными в нем прямоугольными щелями, уложенный на опорную конструкцию 2. Обычно площадь прорезей составляет 10–30% всей площади тарелки. Прорези располагаются на поверхности тарелки с шагом t=10–36 мм.
При работе колонны под давлением поступающих паров на полотне тарелки создается слой жидкости, через которую барботирует пар.
При этом часть жидкости протекает через прорези на расположенную ниже тарелку. Прорези работают периодически: места стока жидкости и прохода пара произвольно перемещаются по полотну тарелки.
Насадочная колонна, наиболее простая по конструкции, представляет собой цилиндрический вертикальный аппарат, заполненный по всей высоте или на отдельных участках так называемой насадкой – определенных размеров и конфигурации телами из инертных материалов.
В насадочных колоннах контакт между газом (паром) и жидкостью осуществляется на поверхности специальных насадочных тел, а также в свободном пространстве между ними.
Насадка предназначена для создания большой поверхности контакта фаз между стекающей по ней жидкостью и поднимающимся потоком паров и интенсивного перемешивания их.
Контакт и массобмен в насадочной колонне происходит непрерывно на всем участке колонны, заполненном насадкой. Этим и отличается работа насадочной колонны от тарельчатой.
Насадочные колонны широко применяют для процессов абсорбции, а также очистки, охлаждения и увлажнения газов. Некоторое применение они находят и для процессов ректификации. Насадочные колонны удовлетворительно работают только при обильном и равномерном орошении насадки жидкостью.
Насадочные колонны применяются в малотоннажных производствах, а также в тех случаях, когда необходимо, чтобы задержка жидкости в колонне была невелика, а перепад давления мал. Благодаря созданию различных эффективных насадок (седла Берля, кольца Палля и др.), в последние годы повысился интерес к насадочным колоннам; их стали применять и для многотоннажных производств. Если использование тарельчатых или насадочных колонн является альтернативным, вопрос должен решаться на основе технико- экономических расчетов.
Различается два основных режима работы аппаратов:
· пленочныйрежим, при котором жидкость, омываемая газом, стекает по элементам насадки;
· эмульгационный режим, когда весь аппарат заполнен жидкостью, а через слой ее между элементами насадки барботирует газ.
К основным элементам насадочных колонн относятся: насадка, устройства для орошения и распределения жидкости, опорные колосники и другие устройства, поддерживающие слой насадки (см. рисунки 2.4 и 2.10).
В промышленности применяют разнообразные по форме и размерам насадки (рисунок 2.31), которые в той или иной мере удовлетворяют требованиям, являющимся основными при проведении конкретного массообменного процесса.
Насадки, изготавливают из разнообразных материалов (керамика, фарфор, сталь, пластмассы и др.), выбор которых диктуется величиной удельной поверхности насадки, смачиваемостью и коррозионной стойкостью.
Насадки условно подразделяются на насадки нерегулярного типа и регулярного.
Нерегулярную насадку применяют в процессах массообмена, протекающих под давлением или в условиях неглубокого вакуума. Эта насадка обладает рядом преимуществ, одно из которых состоит в практическом отсутствии проблемы выбора материала.
Насадку можно изготавливать из металлов, полимеров, керамики. Полимерная и керамическая насадка наиболее приемлема для обработки агрессивных сред. Нерегулярная насадка имеет существенные преимущества по сравнению с регулярной по технологии изготовления, транспортирования и монтажа.
По конструктивным признакам эту насадку можно разделить на кольца и седла, хотя в отечественной и зарубежной практике применяют насадочные тела и других форм [3].
а) кольца Рашига, беспорядочно уложенные (навалом); б) кольца с перегородками, правильно уложенные; в) насадка Гудлое; г) кольца Паля; д) насадка «Спрейпак»; е) седла Берля; ж) хордовая насадка; з) седла «Инталлокс»
Рисунок 2.31 – Различные типы насадок
К насадкам нерегулярноготипа относятся беспорядочно уложенные (навалом) насадки из колец Рашига, седла «Инталлокс», кольца Паля и т.д. (см. рисунок 2.31 а, б, г, е, з).
Наиболее широко распространена насадка в виде тонкостенных керамических колец – кольца Рашига, диаметр которых изменяется в пределах 15–150 мм. Кольца малых размеров засыпают в колонну навалом (рисунок 2.31а).
Насадка малых размеров и сложной конфигурации имеет большую поверхность контакта фаз, но создает повышенное сопротивление.
Кроме того, при выборе размеров насадки необходимо знать, что мелкая насадка менее прочна и быстро забивается твердыми отложениями.
Вместе с тем в последние годы были предложены различные конструкции насадочных элементов, рабочие характеристики которых лучше, чем у колец Рашига.
В последние годы широкое распространение получили кольца Паля, изготовленные из металла, керамики или пластмасс. Отличительной характеристикой этой насадки является практическое постоянство эффективности в широком интервале изменения нагрузок. Хорошими рабочими характеристиками обладают также насадки из элементов седлообразного профиля – седла Берля и Инталлокс.
Кольца с перфорированными стенками позволяют существенно повысить производительность и эффективность ректификационной аппаратуры.
Из-за хаотического распределения тел в объеме насадки образуются избирательные каналы, по которым преимущественно проходит пар или жидкость, в результате происходит неравномерное распределение контактирующих фаз по высоте слоя. В этом существенный недостаток насадок нерегулярного типа.
Неравномерность распределения связана с высотой слоя и диаметром. В связи с этим не рекомендуется применять насадки нерегулярного типа в колоннах диаметром более 2 метров, а также использовать высокие слои насадки без промежуточных перераспределителей потоков.
Отмеченные выше недостатки насадок нерегулярного типа преодолены в конструкциях насадок регулярного типа, т.е. правильно уложенной насадки. Этот способ заполнения аппарата насадкой называют загрузкой в укладку, а загруженную таким способом насадку – регулярной. Расположение элементов в определенном порядке обеспечивает равномерное распределение контактирующих фаз по площади колонны и позволяет получить высокую эффективность массопередачи и одновременно низкое гидравлическое сопротивление (см. рисунки 2.4, 2.10, 2.11).
Примером насадки регулярного типа являются те же кольца Рашига, Паля и т.д. если они укладывают правильными рядами, сдвинутыми друг относительно друга (рисунок 2.31б). Обычно для этого применяют большие кольца (размером не менее 50х50 мм).
За последние годы стали применяться спиральные насадки, выполненные из металлических лент и проволоки, различные металлические сетчатые насадки (рисунок 2.31д), а также насадка из стеклянного волокна.
Данные насадки обеспечивают низкое гидравлическое сопротивление, что особенно важно для вакуумных колонн. Насадки указанных типов применяют для колонн, работающих под атмосферным или более высоким давлением, а также в условиях умеренного вакуума.
Кроме того, к наиболее известным конструкциям регулярных насадок относятся: Клитч-Грид, плоскопараллельная, Зульцер, Перформ-Грид, ромбовидная ВНИИнефтемаша и т.д.
Простейшая регулярная насадка – плоскопараллельная – представляет собой пакеты, набираемых из плоских вертикальных, обычно металлических пластин толщиной 0,4–1,2 мм, расположенных параллельно с одинаковым зазором 10–20 мм. Высота пакета пластин 400–1000 мм. Для повышения равномерности распределения жидкости в колонне пакеты устанавливают один над другим взаимно повернутыми на угол 45–90○.
Недостаток этой насадки – высокая металлоемкость, плохое перераспределение жидкости, сравнительно низкая эффективность.
Для устранения последнего недостатка листы плоскопараллельной насадки выполняют с рифлением или с различными турбулизирующими элементами.
Хорошие характеристики имеют насадки из проволочной сетки. Примером может служить насадка Гудлоу – пакеты свернутой в рулон гофрированной проволочной сетки (диаметр проволки 0,1 мм). Гофры расположены под углом 60○ к вертикали, высота пакета насадки 100–200 мм.
В последние годы в России и за рубежом разработаны различные виды новой высокоэффективной насадки. Примерами могут служить насадки «Зульцер», «Вакупак», «Кедр» (рисунок 2.32).
18 вопрос
Рассмотрим особенности работы барботажной тарелки на примере колпачковой тарелки с круглыми колпачками, схема которой приведена на рисунке 3.8.
I-область светлой жидкости; II-область газожидкостной системы (пены)
Рисунок 3.8-Схема работы колпачковой тарелки
Жидкость поступает на полотно тарелки из переливного устройства и течёт от приточной стороны тарелки к сточной; при этом возникает градиент уровня жидкости ∆. Стенка переливного устройства погружена в жидкость, находящуюся на нижележащей тарелке, что обеспечивает соответствующий гидравлический затвор, исключающий возможность прохождения паров через переливное устройство. Уровень жидкости Hж в переливном устройстве выше уровня жидкости на тарелке, что обеспечивает необходимый расход жидкости.
Высота слоя жидкости на полотне тарелки определяется высотой сливной перегородки hсп и подпором жидкости над сливной перегородкой h1. Изменяя высоту сливной перегородки, можно менять уровень жидкости на тарелке.
Вследствие наличия разности давлений P1 > P2между двумя смежными тарелками поток паров направляется через паровые патрубки под колпачки, а затем через прорези в нижних кромках колпачков поступает в слой жидкости на тарелке. При барботаже, т. е. прохождении газа (пара) сквозь слой жидкости, осуществляется контакт между фазами и протекает процесс массообмена между ними.
Данному рабочему режиму соответствует определенная степень открытия прорезей колпачков 1, которая обеспечивает пропуск паров, приходящихся на одну прорезь. При этом уровень жидкости под колпачком ниже, чем на полотне тарелки.
При поступлении в слой жидкости поток паров разбивается прорезями колпачков на большое число отдельных струй, которые с большой скоростью входят в жидкость. В пространстве между смежными колпачками паровые и жидкостные струи сталкиваются, деформируются, образуя слой газожидкостной системы (пены Hn) с сильно развитой поверхностью контакта фаз.
Наиболее развитая поверхность контакта и наиболее эффективный массообмен характерны для зоны пены. Высота слоя пены возрастает с увеличением слоя жидкости на тарелке и скорости потока паров. Высота слоя пены на тарелке зависит от физических свойств жидкости, характеризующих ее способность к пенообразованию (поверхностное натяжение, плотности фаз). Вместе с тем необходимо учитывать, что при увеличении высоты слоя пены увеличивается гидравлическое сопротивление движению потока паров и возрастает унос жидкости вследствие уменьшения высоты сепарационного пространства Hc(расстояния от поверхности пены до вышележащей тарелки). При максимальных рабочих нагрузках высота сепарационного пространства не должна быть меньше 100…150 мм.
В сепарационное пространство попадают капли жидкости различных размеров, выбрасываемые потоком паров с поверхности пены. Крупные капли, выброшенные в сепарационное пространство, как правило, оседают под действием силы тяжести и вновь возвращаются в слой жидкости, так как скорость паров в межтарельчатом пространстве меньше скорости витания крупных капель. Часть крупных капель, получивших большую начальную скорость, а также мелкие капли, скорость витания которых меньше скорости движения паров в межтарельчатом пространстве, транспортируются потоком паров на вышележащую тарелку, что приводит к уносу. Вследствие сложного движения капель жидкости в межтарельчатом пространстве их концентрация в сепарационном пространстве убывает в направлении движения паров. В сепарационном пространстве барботажных тарелок поверхность контакта фаз определяется поверхностью капель, вклад которой в массообмен невелик.
Для нормальной работы барботажной тарелки должно быть обеспечено равномерное распределение потока паров по всей рабочей площади тарелки. Чтобы обеспечить это, гидравлическое сопротивление каждого контактного элемента (колпачка, клапана, отверстия) должно быть одинаковым. Это достигается погружением контактных элементов в слой жидкости на одну и ту же глубину. Если высота слоя жидкости на тарелке меняется незначительно, что характерно для колонн относительно небольшого диаметра (обычно менее 1 м), то колпачки могут быть установлены на одном горизонтальном уровне. Для колонн большого диаметра и при значительных расходах жидкости, когда высота слоя жидкости на тарелке существенно меняется (более 10 мм), применяют разный уровень установки колпачков, тем более высокий, чем ближе колпачки ко входу жидкости на тарелку. Кроме того, устраивают несколько каскадов по пути движения жидкости или делят общий поток жидкости на несколько потоков (см. рисунок 3.5).
Из рассмотренной схемы работы колпачковой тарелки следует, что контакт между паровой и жидкой фазами на тарелке осуществляется по схеме перекрестного тока: пары движутся снизу вверх, а жидкость течет по тарелке перпендикулярно направлению движения потока паров. В пространстве между смежными колпачками жидкость интенсивно перемешивается по высоте слоя и концентрации ее в этих зонах выравниваются. Состав жидкости вдоль потока меняется. Обычно принимают, что в межтарельчатом пространстве пар полностью перемешан, т. е. имеется одинаковый состав во всех точках поперечного сечения колонны. Такое допущение справедливо для колонн относительно небольшого размера при достаточной величине межтарельчатого расстояния. Для колонн большого диаметра это допущение не соблюдается. Однако степень перемешивания пара в межтарельчатом пространстве оказывает значительно меньшее влияние на эффективность контакта фаз, чем степень перемешивания жидкости на полотне тарелки.
По принципу работы бесколпачковые барботажные тарелки (ситчатые, клапанные, а также секционированные по потоку жидкости), снабженные переливными устройствами, аналогичны колпачковой тарелке. У этих тарелок поток паров разбивается на струи в соответствии с числом отверстий, имеющихся на тарелке. Поскольку пары барботируют по всей площади жидкости, тарелки этого типа называют тарелками со свободным зеркалом барботажа (см. рисунок 3.6).
Слой жидкости на тарелках поддерживается благодаря напору потока паров, проходящих через отверстия в полотне тарелки. Высота слоя жидкости регулируется высотой сливной планки hсп,При недостаточном напоре паров жидкость начинает стекать через те же отверстия, через которые проходит пар, и поддержание необходимого уровня жидкости на тарелке становится невозможным; это приводит к поперечному движению пара по тарелке противотоком к стекающей жидкости. При малом расстоянии между тарелками противоточное движение пара может привести к значительному трению между паром и жидкостью и увеличить градиент уровня жидкости, что еще более ухудшит распределение пара по колпачкам (рисунок 3.9) [3].
Это приводит к значительному снижению эффективности контакта фаз (левая ветвь кривой зависимости эффективности от скорости пара, приведенной на рисунке 3.7).
Рисунок 3.9-Нарушение работы колонны
Отличительной особенностью клапанных тарелок является увеличение их свободного сечения по мере увеличения скорости газа. Благодаря этому скорость газа при его выходе в слой жидкости остается примерно постоянной вплоть до полного открытия клапана. Перекрытие отверстий тарелки саморегулирующимися клапанами позволяет расширить интервал рабочих
Нормально спроектированные переливные устройства должны удовлетворять следующим основным требованиям:
- обеспечивать перетекание заданного количества жидкости с тарелки на тарелку без захлебывания колонны;
- иметь малое гидравлическое сопротивление;
- обеспечивать достаточную величину гидравлического затвора, исключающую прорыв пара через переливное устройство;
- создавать спокойный ввод жидкости на тарелку;
-обеспечивать возможно более полную дегазацию жидкости, перетекающей на нижележащую тарелку.
При расчете переливных устройств обычно исходят из допущения, что через переливы течет свободная от пара жидкость, а способность жидкости к вспениванию (газонасыщению) учитывают последующим введением соответствующих поправочных коэффициентов.
Основные типы переливных устройств, нашедших практическое применение, представлены на рисунке 3.10. Чаще используют сегментные переливы с постоянной по высоте площадью поперечного сечения (с прямой переливной планкой) (а) и с уменьшающейся площадью поперечного сечения (с наклонной переливной планкой) (б), причём площадь перелива в верху примерно в два раза больше, чем в низу. Вариант (б) применяют для больших расходов жидкости с целью лучшей её дегазации. При одинаковой пропускной способности по жидкости, что и в варианте (а), вариант (б) позволяет более полно использовать сечение колонны для размещения контактных элементов тарелки [2].
а - площадь переливного устройства постоянна по высоте;
б - площадь переливного устройства уменьшается книзу; в - переток жидкости по трубам, г - то же, в случае равнонаправленного движения жидкости на смежных тарелках, д- истечение жидкости в межтарельчатое пространство
Рисунок 3.10 - Варианты схем основных типов переливных устройств тарельчатых колонн
Вариант (в) с переточными трубами часто применяется, однако условия для дегазации жидкости здесь хуже, чем в вариантах (а) и (б) Поэтому вариант (в) может быть рекомендован в отдельных случаях при малых нагрузках по жидкости и для слабопенящихся систем.
Вариант (г) обеспечивает одинаковое направление движения жидкости на смежных тарелках и большое обогащение пара (жидкости). Однако при этом усложняется конструкция колонны: при диаметре более 0,5 м этот вариант не даёт ощутимых преимуществ по сравнению со случаем разнонаправленного движения жидкости на смежных тарелках.
При больших нагрузках по жидкости применяют многопоточные тарелки (см. рисунок 3.5,б,в,г), а также переливы с истечением на нижележащую тарелку через щель (см. рисунок 3.10, ). При достаточном расстоянии между тарелками в последнем случае образуется вторая зона контакта фаз.
Длина сегментной сливной перегородки П для односливной тарелки обычно составляет (0,6…0,8) диаметра тарелки.
Большое влияние на работу перелива и тарелки оказывают конструкции узлов ввода и вывода жидкости (рисунок 3.11).
Узел ввода жидкости на тарелку должен оказывать умеренное сопротивление перетоку жидкости и равномерный, спокойный и безударный ввод жидкости.
Если необходимо уменьшить сопротивление перетоку жидкости, то по возможности стараются не применять затворную перегородку; кромки переливных и затворных перегородок делают скругленными (см. рисунок 3.11, а); на прямоточных тарелках узел ввода жидкости делают без начального гидравлического затвора (см. рисунок 3.11,б); применяют специальное устройство (см. рисунок 3.11, в). Для обеспечения равномерного и безударного ввода жидкости на тарелку применяют заглубленный сливной карман (см. рисунок 3.11,а,б),специальную фигурную переливную планку (см. рисунок 3.11,г) или первый ряд барботажных устройств располагают на таком расстоянии, чтобы поступающая жидкость не ударялась о них.
Узел вывода жидкости с тарелки должен обеспечить равномерный, по возможности безударный слив жидкости и способствовать дегазации жидкости в переливе. Безударный слив особенно необходим при больших расходах жидкости. В некоторых случаях достичь такого слива можно при помощи сегментных переливов с наклонными переливными перегородками (см. рисунок 3.10, б). Для обеспечения равномерного слива жидкости верхняя кромка сливной планки не должна иметь большое отклонение от горизонтали; при малых расходах жидкости сливную планку делают зубчатой. На прямоточных тарелках равномерный слив жидкости обеспечивается установкой над переливом специальных отражателей (см. рисунок 3.11.б) или более эффективных отбойных устройств (см. рисунок 3.11,г).Кроме обеспечения равномерного слива жидкости, указанные отбойные устройства способствуют также повышению производительности прямоточных тарелок за счет более интенсивного поступления жидкости в перелив.
а - со скругленными кромками переливных и затворных перегородок и с перегородкой (п) перед сливной планкой; б - без начального гидравлического затвора и |с отражателем (о); в - с эжектирующим устройством; г - с фигурной переливной планкой (ф) и с отбойным устройством над переливом (у); д - с трубами, установленными над сливной планкой (т); е - с перфорированными пластинами в переливе (Пл)
Рисунок 3.11 – Конструкции узлов ввода и вывода жидкости
Для дегазации жидкости в переливе, когда вылет струи стекающей жидкости больше максимальной ширины сливного кармана, рекомендуются устройства из труб (см. рисунок 3.11,д) или перфорированные пластины (см. рисунок 3.11,е).
На тарелках с перекрестным током газа и жидкости диаметром меньше 0,8 м, особенно при средних и малых расходах жидкости, желательно делать защищенный перелив, т. е. на некотором расстоянии от сливной планки устанавливать перегородку (см. рисунок 3.11,a), которая предотвратит выбросы паром всплески жидкости и возможное оголение части тарелки.
Не допускается конструкция переливного устройства с опорным кольцом над переливом. Подобное положение часто встречается в опытных колоннах или при замене старых тарелок новыми, когда опорное кольцо под тарелку выполнено по всей окружности корпуса колонны.
Максимальное отклонение кромки сливной планки от горизонтали должно быть не более 3 мм на 1 м ее длины. В основании сливного устройства надо предусматривать дренажные отверстия диаметром 10…16 мм, площадь которых может быть равной 0,01% от площади сливного кармана [8].
Дата добавления: 2019-07-15; просмотров: 1228; Мы поможем в написании вашей работы! |
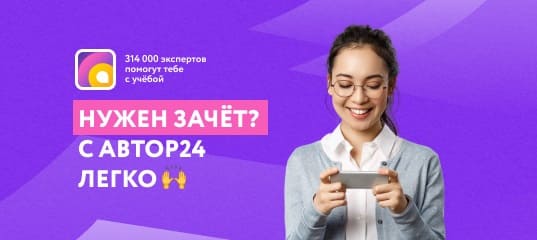
Мы поможем в написании ваших работ!