Жаростойкие стали и сплавы на основе никеля и железа
Основными жаростойкими материалами, которые используют в газовых турбинах, печах и различного рода высокотемпературных установках с рабочей температурой до 1350 °С, являются сплавы на основе железа и никеля. Высокое сопротивление окислению сталей и сплавов связано в первую очередь с большим количеством хрома, входящего в состав сплавов. Например, максимальное содержание хрома (по массе) в количестве 26-29 % имеет сплав на основе никеля ХН70Ю.
Сплав ХН70Ю (ЭИ652)
Химический состав по ГОСТ 5632-72, % (по массе): 26-29 Cr; 2,8-3,5 Al; <= 0,З Mn; <= 0,8 Si; <= 0,12 С; <= 0,1 Ва; <= 0,03 Се; <= 0,012 S; <= 0,015 Р; остальное никель.
Технологические данные:
1. сплав выплавляется в открытых дуговых или индукционных электропечах;
2. температура деформации - начало 1180, конец выше 900 °С, охлаждение после деформации на воздухе;
3. рекомендуемый режим термической обработки - нагрев до 1100-1200 °С, выдержка 10 мин, охлаждение на воздухе;
4. сварка сплава в тонких сечениях может производиться всеми видами сварки;
5. сплав обладает способностью к глубокой вытяжке, предельный коэффициент вытяжки K = D / (d + s) = 2,17, где D - диаметр заготовки; d - диаметр пуансона; s - толщина стенки в мм.
Сплав ХН78Т (ЭИ435)
Химический состав по ГОСТ 5632-72, % (по массе): 19-22 Cr; <= 6 Fе; 0,15-0,35 Ti; <= 0,7 Mn; <= 0,8 Si; <= 0,12 С; <= 0,012 S; <= 0,015 Р; остальное никель.
Технологические данные:
1. сплав выплавляется в открытых дуговых или индукционных электропечах;
|
|
2. температура деформации - начало 1160, конец не ниже 950 °С, охлаждение после деформации на воздухе;
3. рекомендуемый режим термической обработки - нагрев до 980-1020 °С, охлаждение на воздухе или в воде;
4. сварка сплава может производиться всеми видами сварки;
5. сплав обладает способностью к глубокой вытяжке при штамповке.
Сплав ХН60ВТ (ЭИ868)
Химический состав по ГОСТ 5632-72, % (по массе): 23,5-26,5 Cr; 13-16 W; <= 4 Fе; 0,3-0,7 Ti; <= 0,5 Mn; <= 0,8 Si; <= 0,5 Al; <= 0,1 С; <= 0,013 S; <= 0,013 Р; остальное никель.
Технологические данные:
1. сплав выплавляется в открытых дуговых или индукционных электропечах;
2. температура деформации - начало 1180, конец не ниже 1050 °С, охлаждение после деформации на воздухе;
3. рекомендуемый режим термической обработки - нагрев до 1150-1200 °С, выдержка листа 10 минут, прутков 2-2,5 часов, охлаждение на воздухе;
4. сварка сплава может производиться всеми видами сварки;
5. сплав обладает способностью к глубокой вытяжке, предельный коэффициент вытяжки составляет 2,06.
Сплавы ХН65МВ (ЭП567), ХН65МВУ (ЭП760) (хастеллой)
Химический состав по ГОСТ 5632-72, % (по массе): 14,5-16,5 Cr; 15-17 Mo; 3-4,5 W; <= 1 Fе; <= 1 Mn; <= 0,15 Si; <= 0,03 С; <= 0,012 S; <= 0,015 Р; 59,8-67,5 Ni.
Полуфабрикаты из указанных сплавов подвергаются термической обработке, которая заключается в закалке при температуре 1050-1090 °С и последующем охлаждении в воде.
|
|
Применяются для сварки конструкций, работающих при повышенных температурах в достаточно агрессивных средах (серная, уксусная кислота, хлориды и др.).
Высоколегированные стали
Сталь СВ-06Х15Н60М15 (ЭП367)
Химический состав по ГОСТ 2246-70, % (по массе): 14-16 Cr; 14-16 Mo; <= 4 Fе; 1-2 Mn; <= 0,5 Si; <= 0,5 Al; <= 0,08 С; <= 0,015 S; <= 0,015 Р; остальное никель.
Указанная сталь не относится к категории жаропрочных или жаростойких, но используется для сварки конструкций из таких сплавов. Она применяется для сварки деталей из сплавов на никелевой основе, например, ХН78Т, ХН70ВМЮТ и подобных, а также для сварки разнородных металлов, например, хромистых сталей со сплавами на никелевой основе. Помимо сварки может осуществляться наплавка.
Достоинства / недостатки жаростойких и жаропрочных сплавов
Достоинства:
1. обладают высокой жаропрочностью;
2. имеют хорошие показатели жаростойкости.
Недостатки:
1. сплавы с содержанием хрома и особенно никеля имеет высокую стоимость;
2. имея в своем составе большое количество различных компонентов, достаточно трудоемки в производств
23. Маркировка инструментальных сталей. Стали для режущего инструмента. свойств обрабатываемого материала, условий резания, требований к точности размеров и качеству обрабатываемой поверхности, экономических соображений и т. д.
|
|
Инструментальная сталь должна обладать высокой твердостью, износостойкостью, обеспечивающей сохранение режущей кромки инструмента, достаточной прочностью и вязкостью (для инструментов ударного действия).
Режущие кромки инструмента могут нагреваться до 500—900° С. В этих случаях основным свойством инструментальных материалов является теплостойкость (красностойкость), т.е. способность сохранять высокую твердость и режущую способность при продолжительном нагреве,
Этот комплекс свойств обеспечивается выбором стали и оптимальным режимом термической обработки. При этом важное значение имеет прокаливаемость стали. В зависимости от сечения инструмента его изготавливают из сталей небольшой, повышенной прокаливаеммости или из быстрорежущих сталей.
24. Стали для измерительного инструмента.
Ценообразование
4. Принципы учета внешнего состояния изделия (ценообразование) Основные требования к качеству ювелирных товаров указаны в ОСТ 25-
|
|
1290-87 "Изделия ювелирные из драгоценных металлов. Общие технические
условия". Качество камнерезных изделий, выпускаемых серийно, должно
соответствовать требованиям ОСТ 25-843-78.
Контроль качества изделий из драгоценных металлов необходимо начинать
с проверки наличия на каждом изделии клейма Инспекции пробирного
надзора и именника предприятия-изготовителя, которые должны быть
четкими и не ухудшать внешнего вида изделия.
Парные изделия (серьги, запонки) должны быть подобраны по размерам,
форме, виду огранки и цвету вставок. Незначительные различия в цветовых
оттенках вставок не являются браковочным признаком. Если полупары имеют
асимметричную конструкцию верхушки, то они должны быть подобраны в
пару по принципу зеркального отражения. Шлифование и крацование
поверхностей изделий должны осуществляться равномерно, полированные
поверхности должны быть блестящими, матовые — равномерно матовыми и
бархатистыми на вид. На поверхности изделий не должно быть трещин, раковин, заусенцев. На
нелицевых поверхностях допускаются незначительные пористость,
волнистость, следы инструмента. Эмалевые покрытия изделий должны быть
гладкими, блестящими, без сколов, трещин, пропусков, просветов, пятен и
видимых под прозрачной эмалью дефектов металла.
На эмалевых покрытиях изделий (кроме предметов сервировки стола и
украшений интерьера) не должно быть царапин, пузырей, включений, пор,
наплывов на канты и перегородки.
На эмалевых покрытиях допускаются незначительная волнистость слоя
эмали и наличие волосовидной черты в местах соединений эмали с
перегородками и кантами.
На гальванических покрытиях могут быть незначительные следы мест
контактов с токопроводящими приспособлениями без нарушения слоя
покрытия и ухудшения внешнего вида изделия.
На черненых покрытиях предметов сервировки стола и украшениях
интерьера не должно быть более пяти рассредоточенных пор.
Сварные и паяные швы в изделиях должны быть плотными, ровными и без
прожогов. Со стороны лицевой поверхности изделия швы должны быть
близкими по цвету к сплаву, из которого оно изготовлено.
Штампованный, чеканный, филигранный, резной и гравированный рисунки
на поверхности изделий должны иметь четкое изображение.
В реставрированных изделиях по согласованию с заказчиком допускаются
дефекты, не поддающиеся исправлению.
Вставки должны быть закреплены в оправе неподвижно, при этом
возможность их выпадения должна быть исключена.
Крапаны и корнеры соответствующих закрепок должны быть заправлены,
а концы их плотно прижаты к поверхности вставок.
При глухой закрепке касты должны обжимать вставки по рун-дисту плотно,
без зазора. При отделке гризантом его рисунок должен быть четким и без разрыва.
Вставки из жемчуга, кораллов, янтаря, раковин, поделочного камня
допускается крепить на клей в сочетании с глухой закрепкой или на клей и
на штифты.
Замки в изделиях должны исключать самопроизвольное открывание.
Конструкция деталей крепления серег и брошей должна обеспечивать
правильное положение изделий при эксплуатации.
Ювелирка
33. Сбор и обработка отходов ювелирного производства
34. Техника рельсовой закрепка.
Этот вид закрепки камня в ювелирном изделии является одним из самых востребованных при изготовлении свадебных колец. Удачно подходит для установки прозрачных камней, поскольку в таком закрепе кристаллы хорошо освещены. Но из-за того, что камни плотно примыкают друг к другу рундистами, то существует большая вероятность сколов.
Технология такова, что камень помещается в безободковую чашечку – в так называемый канал. Все камни одинакового размера крепятся плотно друг к другу без разделительных перегородок из металла. В некоторых изделиях канал для рельсовой закрепки камней может пролегать по всей поверхности кольца.
Таким видом закрепки устанавливаются камни, ограненные «багетом», «принцессой» или круглой формы. Наиболее идеален такой закреп для бриллиантов и почти никогда не используется для изумрудов. Ведь камни в таком закрепе подвергаются значительной нагрузке. Часто такой закреп используется для плоских колец.
35. Вырезка пресс-форм. Инструменты и приспособления для вырезки
Изготовление резиновых пресс-форм. В качестве сырья для резиновых форм используют сырые резиновые смеси.
Подготовка резиновой смеси заключается в распрессовывании в вулканизационном прессе при температуре не выше 100°С в течение 1...1.5 мин. Для этого кусок сырой резиновой смеси помещают между двумя стальными полированными плитами, смазанными кремнииорганической жидкостью во избежание прилипания смеси к металлу. Между плит устанавливают ограничители, позволяющие отрегулировать необходимый зазор. Выдержав 1...1,5 мин под давлением верхней плиты, смесь охлаждают под струей воды и отделяют от плит. Распрессовывать сырую резиновую смесь лучше непосредственно перед изготовлением пресс-форм. Для того чтобы фиксировать резиновые пластины относительно друг друга при сборке в пакет (несколько слоев резины), изготовляют резиновые замки - ребристые с одной стороны пластины. Для их изготовления распрессованную сырую резину вырезают по размерам пресс-форм и очищают ватным тампоном, смоченным в бензине. Пресс-форму протирают кремнийорганической жидкостью. Собранный пакет помещают в вулканизационныи пресс, прогревают 5 мин; затем в течение 40 мин вулканизируют под давлением 40...100 кгс/см2 при температуре 140°С. По окончании вулканизации пакет охлаждают под струей воды и из пресс-формы извлекают ребристую резиновую пластинку.
При изготовлении резиновой пресс-формы следует учитывать свойства и параметры мастер-модели, знать специфику и следствия физических процессов, протекающих в ходе вулканизации, а также другие технологические особенности:
• размерная усадка каучуковых матриц, воска и отливаемого изделия;
• разница в толщине различных частей изделия и препятствия, возникающие при кристаллизации металла;
• точки изделия, к которым можно подводить литники для изготовления изделия без нарушения его рисунка. Эти точки должны удовлетворять требованиям нормальной заливки металла;
Также требуется строгое следование технологическим режимам. Некоторые из них указываются производителем резины, некоторые определяются экспериментально, опираясь на выше приведенные особенности. Наиболее важны предварительные операции по подготовке обойм и резины. Для этого обоймы тщательно обезжириваются и сушатся перед закладкой резины, в процессе которой также следует избегать загрязнения резины любого вида жирами (в т.ч. кожным), поскольку это пагубно сказывается на свойствах силиконовых эластомеров и может привести к расслоению пресс-формы.
Порядок выполнения операций при изготовлении резиновых пресс-форм:
1. Выбрать стремянку (обойму) в зависимости от габарита мастер модели.
2. Подготовить мастер модель, закрепить в стремянке.
3. Подготовить резину.
4. Заполнить стремянку «сырой» резиной (эластомером).
5. Позиционирование опорных штырей.
6. Закрытие матрицы металлическими пластинами и последующий нагрев в вулканизаторе.
7. Извлечение из стремянки.
8. Резка резины
.
9. Извлечение мастер модели.
10. Установка позиционирующих штырей.
11. Пробная инжекция.
12. Контроль качества.
13. Складирование.
36. Техника соединения деталей. Пайка
Пайка — это процесс соединения металлических деталей, находящихся в твердом состоянии, посредством расплавленного связующего металла или сплава — припоя, имеющего более низкую температуру плавления, чем соединяемый основной металл.
В процессе паяния между расплавленным припоем и основным металлом на небольшой глубине происходят процессы взаимного растворения и диффузии. Причем в отличие от сварки, при которой наряду с припоем оплавляются кромки или торцы соединяемых деталей, при паянии расплавляется только присадочный материал, т. е. припой. При этом для получения прочного паяного соединения необходимо добиться такого взаимодействия припоя с паяемым металлом, при котором атомы жидкого припоя вступают во взаимодействие с атомами паяемого металла, т. е. происходит смачивание жидким металлом твердого.
Смачивание металлов можно улучшить с помощью флюса, который наряду с облегчением процесса соединения металлов способствует удалению окислов из мест пайки.
Плотность прилегания и строгая параллельность — одно из непременных условий получения прочного и долговечного шва. На механическую прочность шва оказывают влияние выбранный тип соединения и качество размещения припоя, а также его количество, которое должно быть (по возможности) минимальным. При этом необходимо обеспечить также правильное втекание правильное втекание, что во многом зависит от самого ювелира, который должен уметь управлять (с помощью пламени горелки) перемещением расплавленного припоя.
Рис. 3.42. А - Структура паяного шва (схема):1 — основной материал; 2 — припой; 3 — зона диффузии основного материала; 4 — зона диффузии припоя
Б-тип соединения
Типы соединений. При пайке ювелирных изделий применяются два основных типа соединений: внахлестку и встык; при необходимости можно сочетать оба этих типа (рис. 3.42, Б). Соединения встык используют при пайке изделий, не требующих особой жесткости, герметичности и прочности. Соединения внахлестку обеспечивают наиболее прочный и надежный шов; ими пользуются во всех возможных случаях. Так называемые скошенные соединения (разновидность соединения встык) позволяют увеличить площади соединяемых поверхностей, но значительно затрудняют качественную подгонку деталей. Комбинированные соединения применимы при пайке сложных, индивидуального назначения изделий.
Подготовка паяемых поверхностей. До начала процесса пайки необходимо тщательно очистить соединяемые поверхности от загрязнений и оксидов: место пайки должно быть абсолютно чистым. Очистка производится двумя способами: химическим и механическим. Для удаления загрязнений (жировых и масляных пятен) наиболее эффективен химический метод очистки. Он ведется с помощью четыреххлористого углерода, трихлорэтилена, тринатрийфосфата. Механическая очистка (удаление оксидов) производится с помощью напильника, надфиля, шабера, наждачной шкурки, проволочной (стальной) или стеклянной щетки. При этом нужно соблюдать осторожность, чтобы не повредить соединяемый зазор. При необходимости после механической очистки следует произвести еще и химическую.
Подгонка спаиваемых частей. Поверхности спаиваемых частей следует с большой точностью и плотностью состыковать одну с другой. Расстояние между ними должно быть незначительным, то есть, чтобы осталось место лишь для припоя. Зазор должен быть в пределах от 0,025 до 0,1 мм. При пайке замкнутых пустотелых деталей необходимо проделать в них (в малозаметных местах) небольшие отверстия для беспрепятственного выхода воздуха. Иначе, нагреваясь и расширяясь, воздух может вспучить деталь и даже разорвать ее. Чтобы снять внутренние напряжения в соединяемых деталях, оставшиеся после предшествующей обработки, и избежать, таким образом, возможных излишних дефектов, соединяемые части подвергают отжигу. Перед пайкой прессованных деталей и изделий следует тщательно проверить, нет ли в них трещин или дырочек, которые при пайке, вследствие затекания припоя, расширятся, что неизбежно приведет к некачественной пайке, то есть к браку. При пайке слабо подвижных шарнирных соединений, а также пружинных замков браслетов, затекания припоя в зазоры можно избежать, проложив маленькие кусочки бумаги или картона. Перед пайкой (при ремонте) полых цепочек и полых звеньев браслетов поврежденные (протертые) места опиливают и между стыками (перпендикулярно к ним) вставляют тонкую серебряную пластинку; на обе стороны пластинки наносят припой, паяют, а после пайки выступающие концы пластинки опиливают.
Рис. 3.43. Примеры фиксации деталей при пайке Рис. 3.44. Виды пайки:
А —точечная пайка (схема);
Б — микроплазменная сварка (схема)
Фиксация деталей. В процессе пайки детали располагают на специальной подкладке — асбестовом листе. Пайку нельзя начинать, не произведя фиксацию (упрочение, закрепление в требуемом положении) деталей. При ручном изготовлении ювелирных украшений пригодны традиционные методы фиксации деталей: удержание пинцетом, круглогубцами, укрепление с помощью проволоки, булавок, зажимов и т. д. (рис. 3.43, А и Б). В условиях массового производства незаменимым способом фиксации деталей перед пайкой является контактная пайка-прихватка: припаиваемые детали изделий помещают в соответствующих форм выемки съемных матриц, закрепляемых на опорной плите, затем к деталям подводят электрод. Соединение деталей в определенных точках происходит за счет местной пластической деформации, которая вызывается нагревом электрическим током; при этом электроды, проводящие ток, одновременно играют роль пуансонов для осадки металла в нагретой зоне. Способ этот пригоден для абсолютного большинства ювелирных украшений. Точечный паяный шов между деталями достаточно прочен, чтобы выдержать (в последующем) нанесение флюса, припоя, транспортировку деталей к месту пайки, которая должна осуществляться немедленно после очистки соединяемых поверхностей, причем важнейший элемент качественной пайки — правильно выбранный припой.
Способы пайки. В ювелирном производстве различают два способа пайки: пайку вручную с помощью газовых (пламенных) горелок и механизированную пайку в печах с защитной атмосферой. Газовая горелка используется массово и повсеместно. Однако в отдельных случаях ее применение не дает нужного эффекта и тогда пайка ведется с помощью горелок специального назначения: для точечной пайки и пайки крупногабаритных изделий.
Точечная пайка. Обеспечивает быстрый, интенсивный нагрев до высоких температур. Необходима, когда недопустим нагрев изделий или деталей вне зоны пайки: при соединении тонких сложных деталей, при проведении реставрационных работ, для исправления дефектов литых изделий, для проведения многоступенчатой пайки одного изделия припоем одного состава. Выполняется точечная пайка (рис. 3.44,А) с использованием отечественного аппарата модели АП-25А., а также моделей горелок зарубежного производства. Температура пламени в горелке достигает 2500 °С; длина факела — до 40 мм; максимальный диаметр пламени — 2 мм.
Пайка крупногабаритных изделий. В отличие от точечной требует высокотемпературного нагрева всего изделия, например при пайке серебряных изделий посудной группы с филигранью, масса которых может достигать 1500 г. Перед началом такой пайки детали филигранного рисунка наклеиваются на корпус заготовки, напайка же их осуществляется с помощью многофакельной горелки, которая позволяет вести одновременный нагрев всей поверхности, заполненной филигранью. Для исключения местного перегрева, изделие на время пайки устанавливают на вращающийся столик.
Механизированная пайка. Этот способ пайки применяется для изделий из сплавов золота и осуществляется в конвейерных печах (Печи «Соло») с защитной атмосферой. Подготовленные для пайки изделия (с нанесенным припоем) укладывают на металлический поддон, который затем устанавливают на движущуюся ленту. Режим пайки (температура, время) регулируется автоматически.
Пайка методом микроплазменной сварки. Микроплазменная сварка (рис. 3.44, Б) является одной из разновидностей дуговой сварки неплавящимся электродом на очень малых токах (2—30 А) для соединения' металла (золота, серебра, меди) толщиной от 0,1 до 1,5 мм. В качестве источника тепла используется сжатая дуга, стабильно горящая между вольфрамовым электродом и. изделием в непрерывном или импульсном режиме. В начале возбуждают малоамперную де-журную дугу в аргоне между электродом и водоохлаждаемым соплом, а затем приближают горелку к изделию, что приводит к возбуждению рабочей дуги. Для защиты расплавленного металла используют инертные газы (аргон, гелий) или их смеси.
На предприятиях ювелирной промышленности микроплазменная сварка применяется как метод пайки изделий из золота и серебра, причем процесс такой пайки идет без использования присадочного материала (припоя), т. е. шов образуется за счет расплавления основного металла. Наибольший эффект от применения микроплазменной сварки достигается при пайке изделий массового назначения, например колец, а также изделий, выполненных в технике филиграни (пайка зерни).
Инструмент для пайки
Основной инструмент для пайки — пламенная горелка. В качестве топлива для горелок используется газ (от сети и в баллонах). Горелки, работающие на газовом топливе, состоят из двух трубок (стальных или латунных): одна — для подачи газа, другая—воздуха. Каждая трубка, как правило, снабжена вентилем, выполняющим одновременно роль запорного и регулировочного. Для смешивания воздуха с газом конец воздушной трубки впаивают в газовую или две ведущие трубки впаиваются в третью. Трубка смешения оканчивается насадкой, в которой происходит окончательное смешение воздуха с газом и которая придает факелу определенную форму. В своей работе ювелиры используют несколько модификаций газовых горелок (рис. 3.45, А), в том числе миниатюрных, с очень тонким пламенем и температурой горения 1300 -3500 °С (рис. 3.45, Б), а также специальный паяльный аппарат для выполнения точечной пайки (рис. 3.45, В) с очень тонким пламенем и температурой горения, достигающей 2850 °С.
Рис.3.45. Горелки: А — обычные; Рис. 3.46. Огнеупорные приспособления (леткалы):
Б — миниатюрные с очень тонким пламенем А — асбестовые плиты, в том числе на
и высокой температурой (до 1300 — 3500 °С); деревянной основе и проволочные кольчушки; Б — бруски древесного угля;
В — специальный паяльный В — подставки из плетеной круглой проволоки;
аппарат для точечной пайки Г — поворотные стойки из плетеной проволоки;
Д — леткалы-вертушки
Процесс пайки требует применения всевозможных огнеупорных приспособлений — лет-калов. Для этих целей используют листы асбеста на деревянной основе и без основы, металлическую сетку (рис. 3.46, А) размерами 200x100, 200X150, 200x250, 200x300, 500x500 мм; бруски древесного угля, как правило, из липы (рис. 3.46, Б); подставки диаметром обычно 70 - 100 мм из переплетенной круглой проволоки и подставки с сетчатой (из проволоки) поверхностью размером 100x100 мм (рис. 3.46, В). Часто применяются леткалы в виде поворотных столиков с сетчатой (из проволоки) поверхностью и размерами, не превышающими 60 х 100 мм (рис. 3.46, Г). Для пооперационной пайки используют леткал-вертушку (рис. 3.46, Д), представляющий собой металлический цоколь, на котором (на ножке) укреплен вращающийся столик диаметром 80, 100, 120, 160, 200, 250, 300 мм. В последнее время для ускорения и облегчения процесса пайки часто используют специальные приспособления в виде стоек и столиков, действующие как зажимы-державки, которые за счет телескопической связки могут быть легко ориентированы в требуемом (заданном) положении и выступать в роли своеобразного дополнительного удерживающего устройства, то есть так называемой третьей руки (рис. 3.47). Вспомогательные средства для выполнения операции пайки включают в себя пинцеты и зажимы длиной от 150 до 200 мм; ножницы; кисточки для нанесения флюса, в том числе и двусторонние с размером (толщиной) щетинной части от 1 до 10 мм и длиной от 9 до 23 мм; в качестве флюса — буру ; очки .
Рис. 3.47. Приспособления для пайки — «третья рука»
37. Сплавы на основе золота
Сплавы золота
В России количество золота в золотых сплавах контролируется государством. Среди металлов, которые содержатся в сплавах золота, — серебро, медь, палладий, платина, кадмий и цинк. От того, какой металл и в какой пропорции добавлен в сплав, зависят характеристики конечно изделия.
Пробы золота
Количество содержания чистого золота в сплаве можно определить по пробе, проставленной на изделии. В России используется метрическая проба: ее значение указывает на количество граммов чистого благородного металла в одном килограмме сплава.
3. 958 проба содержит до 96,3% чистого золота. Этот сплав в качестве легирующих компонентов включает серебро и медь. Он очень устойчив к воздействию внешней среды, хорошо сохраняет полировку, но очень пластичный. Золото 958 пробы обладает насыщенным ярко-желтым оттенком. В основном оно используется для изготовления обручальных колец и подвесок.
4. 750 проба — второй по популярности сплав золота. В нем содержится до 75,5% благородного металла, а другие компоненты — это серебро, платина, палладий, никель, медь. Этот сплав прочен и отлично полируется, поэтому изделия из золота 750 пробы долговечны и красиво блестят.
5. 585 проба — самый популярный в ювелирном производстве сплав. Он содержит до 59% чистого золота и включает доли серебра, палладия, никеля, меди, цинка. Золото 585 пробы достаточно твердое и прочное, оно практически не тускнеет. Диапазон оттенков широк — от белого, красного и желтого до зеленого различных оттенков, в зависимости от пропорции добавленных металлов.
6. 500 и 375 пробы практически не используются в ювелирном производстве. 375 пробу обычно называют золотосодержащим сплавом серебра и меди. Такое золото довольно быстро тускнеет на воздухе, что существенно ограничивает его применение.
38. Финишная обработка ювелирных изделий. Шлифование и полирование
Шлифовка
Этот этап можно назвать «первопроходцем», ведь его применяют первым после литья. В ходе шлифовки, изделие «очищают» от:
7. литника (отверстие через которое заливается металл в форму);
8. облоя (лишний материал на изделии, оставшийся после литья).
Шлифовка проводится сначала механическим способом, с помощью станка и кругов разной абразивности, и убирает самые заметные изъяны и неровности. После этого, ручным способом при помощи бормашины, обрабатываются мелкие элементы украшения. Разнообразные насадки позволяют добраться даже до самых «укромных местечек».
Галтовка
Промежуточный этап между шлифовкой и полировкой. С её помощью убираются более мелкие неровности и царапины. Проводится этот процесс во вращающихся барабанах или специальных вибромашинах. В барабанах изделие закрепляется неподвижно, а галтовочные тела или жидкость вращаются, обрабатывая заготовку. В машинах вибрационного типа, абразивы или растворы перемешиваются в хаотичном порядке, вместе с украшением.
Процесс галтовки разделяют на:
9. сухую;
10. мокрую.
Шлифовка в сухой среде происходит с помощью абразивных тел, в качестве которых используют фарфор, пластик, корунд, крошка оболочки грецкого ореха. Частицы, используемые для сухой галтовки, зачастую имеют форма конуса, шара, пирамиды или цилиндра.
Мокрая обработка подразумевает использование буферного раствора или рабочей жидкости. Реагентами могут быть средства, предназначенные для чистки и полировки, известь, сода или растворы щелочи.
Каждый ювелир использует подходящий именно ему способ галтовки. В технологическом процессе может использоваться только один из них, или их объединяют и они идут последовательно, друг за другом. Роль мастера в этом процессе не сложная, но очень ответственная, ведь он должен держать под контролем все ключевые факторы: время, параметры настроек, целостность всех элементов изделия.
Полировка
Для того, чтобы придать украшению великолепный зеркальный блеск, заключительным и решающим этапом будет полировка. В отличии от шлифовки, эта операция необходима для идеально гладкой обработки поверхности изделия. Она заключается в том, чтобы аккуратно снять самый тонкий, практически незаметный, слой покрытия. Зачастую ювелирами используется механический способ с применением мягкого полировочного материала:
11. фетр;
12. войлок;
13. шерсть.
Изначально заготовку необходимо обезжирить, затем, для усиления скольжения, наносится полировочная жидкость, которая представляет собой смесь из нашатыря и мыльного раствора. После всех подготовительных манипуляций, специалист с помощью бормашины или станка с соответственными насадками, проводит непосредственно саму полировку.
Этот процесс также может повторяться для изделия ещё раз, после закрепки вставок
39. Декорирование ювелирного украшения техникой чернения
Чернь (не путать с очернительством:) — древний приём украшения самых разных золотых и серебряных предметов путём придания им чёрного цвета. После применения этой техники фактура поверхности предмета становится контрастней и богаче, будь то рисунок орнамента, или детали рельефа. Правда, применяют ее и для сокрытия мелких дефектов, например соединительных швов.
Серебро с чернением – это классика жанра для украшений под старину, или с «традиционными» мотивами. Вкратце, суть чернения (англ. blackening, blackened silver) такова: «чёрный» сплав серебра, меди, свинца и серы вплавляют в основной металл. Сплав для чернения вплавляют в углубления (0,3 мм), нанесённые на выбор — гравировкой, чеканкой, травлением изделия или выдалбливанием. Под нагревом происходит химическая реакция между серебром и вплавляемой смесью. В результате кроме новых декоративных свойств, черненое изделие получает и практические: оно не тускнеет и не требует особого ухода. Палитра черни широка — от серебристо-серых до чёрно-бархатных тонов.
Чернь очень красива и на высокопробном золоте, и на серебре. На меди, низкопробном серебре, латуни чернь крошится и отпадает. Однако вывести качественный, «не слетающий» состав черни для золота крайне сложно, поэтому чернь на этом благородном металле редка. В обычной практике с древних времен чаще всего используется чернение серебра – изысканно и долговечно. Ну а если всё-таки вам хочется золота? Защитив специальным лаком участки с уже готовой чернью, можно вызолотить серебро — чем не выход!
Техники чернения серебра
Пожалуй, приём чернения металлов схож с техникой выемчатой эмали. Но, в отличие от покупных эмалевых составов, черневой нужно готовить самостоятельно (и сразу же наносить и обжигать).
Фабричная гальванизация — будни современной технологии, но не так уж и давно способы чернения серебра были иные. Упомянем три:
14. так называемый германский
15. дореволюционно-российский и
16. современный московский
В «германском» рецепте в медно-серебряный сплав медленно вливают свинец, хорошо перемешивая. Тройной сплав при постоянном помешивании выливают в нагретый серный порошок, размешивая для хорошего взаимодействия частей. Затем смесь выливают в воду. Застывшие куски черни тонко растирают в фарфоровой ступке в нужной дозе, — только свежую влажную черневую массу можно наносить на изделие.
Согласно «русскому» рецепту, тройной сплав не выливают в серный порошок, а порциями добавляют серу в сплав, выливая после готовую чернь не в воду, а на чугунную сковороду. Этот твёрдый «блин» дробят на куски и вновь переплавляют с добавлением серы и флюса. И так до трех раз, если нужна чернь экстра-класса. Готовую чернь толкут в ступках и просеивают через мелкое сито.
Третий — авторский рецепт профессора А. Г. Спасского (Московский институт цветных металлов); готовят отдельно сернистое серебро, сернистую медь и сернистый свинец и сплавляют их вместе в нужных пропорциях. За тем строго определённым образом плавят и остужают.
40. Гальваническое родирование
РОДИРОВАНИЕ.
Ювелирные изделия родируют для придания им высоких оптических свойств, красивого внешнего вида, износостойкости и химической стойкости, поверхностной твердости. Твердость электролитического родия в 8—10 раз выше металлургического. Электрохимический способ осаждения родия позволяет получить качественные покрытия без предварительного нанесения подслоя на изделия из меди, латуни, мельхиора, никеля, серебра, золота, платины, палладия и их сплавов., Широко применяются родиевые покрытия в ювелирной промышлен-ности при выпуске изделий из белого золота и платины.
Из-за большой толщины слоя этот способ является слишком дорогим. Удовлетворительного результата, имеющего небольшую стоимость, можно добиться, нанося слой родия толщиной доли микрона на покрытие из никеля. В некоторых случаях можно ограничиться только никелированием в полировальной ванне.
Изделия, предназначенные для покрытия слоем родия, должны быть без внешних дефектов и тщательно отполированы. На полированное изделие можно нанести более тонкий слой родия, это не отражается на качестве покрытия, но уменьшает расход драгоценного металла. Как и другие виды гальванизации, родирование требует тщательной подготовки покрываемой поверхности, которая заключается в обезжиривании и промывке перед осаждением слоя родия.
После химического обезжиривания изделия промывают в дистиллированной и проточной воде.
Процесс подготовки поверхности изделий из серебра и недрагоценных металлов к осаждению родия более сложен и проводится по следующей схеме: обезжиривание органическое, промывка, обезжиривание электролитическое, промывка, химическая обработка, промывка, химическая обработка, промывка, декапирование.
Рабочая температура электролита 30— 40°С, плотность тока 0,8—1,5 А/дм2, продолжительность электролиза зависит от толщины покрытия. Для слоя родия толщиной 0,3—0,5 мкм время электролиза 4—6 мин.
Ниже приведены два рецепта, оба раствора используются при комнатной температуре. Существует множество других рецептов горячих и быстродействующих растворов, однако оборудование, необходимое для проведение таких процессов, должно быть оснащено нагревательными элементами, фильтрами и приспособлениями для перемешивания.
Неглянцевое никелирование:
· сульфат никеля 100 г/л,
· сульфат магния 30 г/л,
· хлорид никеля 10 г/л,
· борная кислота 30 г/л.
Глянцевое никелирование:
· сульфат никеля 250 г/л,
· хлорид никеля 10 г/л,
· борная кислота 30 г/л,
· блескообразователь в количестве, указанном поставщиком.
· ток 0,3-0,5 А/дм2; рН 5,5-5,8.
Для поддержания кислотности необходимо использовать серную кислоту, pH можно определять лакмусовой бумагой. Обычно добавляются 2-3 г на каждые 10 л.
Анод изготавливается из электролитического никеля, профилированного никеля, никеля в виде кусочков в корзине из титана. Последний вариант является наиболее экономичным.
Одним из дефектов является появление пятен на покрытии. Эффективными в данном случае являются небольшие добавки (доли грамма на литр) поверхностно активных веществ.
41. Технология изготовления резиновых пресс-форм
42. Ювелирные камни. Свойства и классификации. Виды огранки камней
Дата добавления: 2019-07-15; просмотров: 140; Мы поможем в написании вашей работы! |
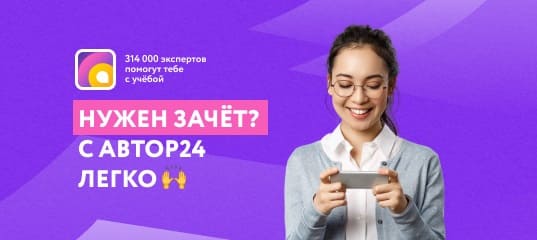
Мы поможем в написании ваших работ!