Восстановление работоспособности оборудования
Цель и задачи технической диагностики
Техническая диагностика — молодая наука, возникшая в последние десятилетия в связи с потребностями современной техники. Все возрастающее значение сложных и дорогостоящих технических систем, применяемых при добыче, транспортировке и переработке нефти и газа, требования их безопасности, безотказности и долговечности делают весьма важной оценку состояния системы, ее надежности.
Уровень безопасности связан со свойствами перерабатываемых веществ, режимами и условиями эксплуатации оборудования, его техническим состоянием. Техническая диагностика является одним из основных элементов системы управления промышленной безопасностью в России. Общие требования по безопасности промышленных объектов установлены Федеральным законом Российской Федерации «О промышленной безопасности опасных производственных объектов» № 116-ФЗ от 20 июля 1997 г. Этот закон обязывает организации, эксплуатирующие опасные производственные объекты (к ним относятся все объекты нефтегазовой промышленности), проводить диагностику и испытания технических устройств, оборудования и сооружений в установленные сроки и в установленном порядке. Диагностика, в том числе с использованием методов неразрушающего контроля, может проводиться как самой эксплуатирующей организацией, так и с привлечением специализированной организации (имеющей соответствующую лицензию) в составе экспертизы промышленной безопасности. Надзор за безопасностью потенциально опасных производственных объектов осуществляется государственными надзорными органами: Федеральной службой по экологическому, технологическому и атомному надзору, МЧС, Минэнерго, ГУПО МВД, каждым по своей части.
|
|
Техническая диагностика — наука о распознавании состояния технической системы, включающая широкий круг проблем, связанных с получением и оценкой диагностической информации. Согласно ГОСТ 20911-89, техническая диагностика — область знаний, охватывающих теорию, методы и средства определения технического состояния объектов. Здесь и далее интересующими нас объектами являются буровое и газонефтепромысловое оборудование, газонефтепроводы и нефтехранилища.
Целью технической диагностики являются определение возможности и условий дальнейшей эксплуатации диагностируемого оборудования и в конечном итоге повышение промышленной и экологической безопасности. Задачами технической диагностики, которые необходимо решить для достижения поставленной цели, являются:
• обнаружение дефектов и несоответствий, установление причин их появления и на этой основе определение технического состояния оборудования;
|
|
• прогнозирование технического состояния и остаточного ресурса (определение с заданной вероятностью интервала времени,
в течение которого сохранится работоспособное состояние оборудования).
Таким образом, техническая диагностика решает обширный круг задач, многие из которых являются смежными с задачами других научных дисциплин. Основной проблемой технической диагностики является распознавание состояния технической системы в условиях ограниченной информации.
Решение перечисленных задач, особенно для сложных технических систем и оборудования, позволяет получить большой экономический эффект и повысить промышленную безопасность соответствующих опасных производственных объектов. Техническая диагностика благодаря раннему обнаружению дефектов позволяет предотвратить внезапные отказы оборудования, что повышает надежность, эффективность и безопасность промышленных производств, а также дает возможность эксплуатации сложных технических систем по фактическому техническому состоянию. Эксплуатация по техническому состоянию может принести выгоду, эквивалентную стоимости 30 % общего парка машин.
|
|
Виды дефектов, качество и надежность машин
Техническое состояние оборудования определяется числом дефектов и степенью их опасности. Дефектом называют каждое отдельное несоответствие детали или технической системы требованиям, установленным технической документацией. По расположению дефекты подразделяют на явные (наружные) и внутренние (скрытые). Наружные дефекты чаще всего обнаруживают визуально, скрытые — посредством различных методов неразрушающего контроля. По форме дефекты бывают объемные и плоскостные. Объемные проявляются в виде изменения (искажения) начальной формы или размеров объекта, плоскостные — в виде трещин или полос скольжения. По происхождению дефекты подразделяют на производственные и эксплуатационные. Производственные дефекты могут быть металлургическими, возникающими в процессе металлургического передела, и технологическими, возникающими при изготовлении детали.
Такие дефекты обычно проявляются в начальный период работы оборудования — период приработки. Эксплуатационные дефекты возникают после некоторой наработки в результате износа, накопления усталостных и иных повреждений, а также из-за неправильного технического обслуживания и ремонта. Практика показывает, что можно выделить следующие основные причины накопления дефектов и повреждений, приводящих к отказам оборудования по мере его эксплуатации:
|
|
• сквозные трещины, разрушения и деформации элементов
оборудования, возникающие при превышении допускаемых напряжений;
• механический износ, обусловленный трением сопрягаемых поверхностей;
• эрозионно-кавитационные повреждения, вызванные воздействием потока жидкости или газа;
• деградация свойств материалов с течением времени и под воздействием эксплуатационных факторов;
• коррозия металлов и сплавов, коррозионно-механические повреждения, возникающие под влиянием коррозии, напряжений, трения и т.п.
По степени опасности дефекты разделяют на критические, значительные и малозначительные. Критическими являются дефекты, при наличии которых использование агрегата невозможно или недопустимо по условиям безопасности. К значительным относят дефекы, существенно влияющие на использование агрегата по назначению или на его долговечность. Малозначительные соответственно не оказывают существенного влияния ни на использование агрегата по назначению, ни на его долговечность.
При определении степени опасности дефекта учитывают напряженное состояние контролируемого изделия, вид дефекта, его размеры и ориентацию относительно действующих напряжений. Основными факторами, определяющими степень опасности дефекта, являются величина утонения герметичных перегородок и коэффициент концентрации механических напряжений (в трещинах — коэффициент интенсивности напряжений), показывающий, во сколько раз максимальные местные напряжения в зоне дефекта выше, чем в бездефектной зоне. Виды допустимых дефектов и их величины приводятся в нормативной документации на контроль соответствующего изделия. Наиболее опасными являются плоскостные трещиноподобные дефекты, располагающиеся перпендикулярно действующим напряжениям.
Совокупность свойств, определяющих степень пригодности машины для использования по назначению, называется качеством. Эти свойства характеризуются эксплуатационными показателями (мощность, расход топлива, скорость, производительность и т.д.), экономической эффективностью, технологичностью, показателями эстетики и эргономики, надежностью.
Надежность эксплуатируемой машины определяется в первую очередь ее техническим состоянием. По ГОСТ 27.002—83 надежность — свойство объекта сохранять во времени в установленных пределах значения всех параметров, характеризующих способность выполнять требуемые функции в заданных режимах и условиях применения. Надежность оценивается безотказностью, долговечностью, ремонтопригодностью, ресурсом, а также сочетанием или совокупностью этих свойств.
Свойства надежности: безотказность, долговечность, ремонтопригодность, сохраняемость.
Состояние объекта: работоспособное, неработоспособное, предельное, исправное и неисправное
События: повреждение, отказ, сбой, исчерпание ресурса.
Временные понятия: наработка, ресурс, срок службы, срок сохраняемости.
Виды объектов: обслуживаемый/необслуживаемый, восстанавливаемый/ невосстанавливаемый, ремонтируемый/неремонтируемый.
В зависимости от вида изделия его надежность может включать только часть составных свойств надежности. Так, например, если изделие не подлежит ремонту, то для таких изделий в свойство надежности не включаются долговечность и ремонтопригодность, для них важно только свойство безотказности.
Безотказность - свойство объекта непрерывно сохранять работоспособное состояние в течение некоторого времени или некоторой наработки.
Долговечность - свойство объекта сохранять работоспособное состояние изделия до наступления предельного состояния при установленной системе технического обслуживания и ремонта.
Ремонтопригодность - свойство объекта, заключающееся в приспособленности к поддержанию и восстановлению работоспособного состояния путем проведения технического обслуживания и ремонта.
Сохраняемость - свойство объекта сохранять значения показателей безотказности, долговечности и ремонтопригодности в течение и после хранения и транспортирования.
В зависимости от того, предусмотрены или нет документацией для данного изделия операции технического обслуживания, изделия подразделяются на обслуживаемые и необслуживаемые, а в зависимости от того, предусмотрены или нет операции ремонта - на ремонтируемые и неремонтируемые. В зависимости от того, возможно или невозможно у данного изделия восстановление работоспособного состояния в рассматриваемой ситуации и предусмотрено ли такое восстановление в нормативно-технической и конструкторской документации, они подразделяются на восстанавливаемые и невосстанавливаемые. Одно и то же изделие может быть как восстанавливаемым так и невосстанавливаемым, в зависимости от его целевого назначения и условий эксплуатации.
Для количественной характеристики каждого из свойств надежности отдельного объекта служат такие временные понятия, как наработка, наработка до отказа, наработка между отказами, ресурс, срок службы, срок сохраняемости, время (трудоемкость) восстановления. Значения этих характеристик, обычно полученные по экспериментальным данным, служат основой для последующего вычисления оценок таких показателей надежности, как средняя наработка на отказ, средний ресурс и т.д. Наработка до отказа исчисляется от начала эксплуатации объекта до возникновения первого отказа, наработка между отказами исчисляется от окончания восстановления его работоспособного состояния после отказа до возникновения следующего отказа.
Ресурс исчисляется как суммарная наработка объекта от начала его эксплуатации или ее возникновения после ремонта до перехода в предельное состояние. Срок службы выражается в единицах календарной продолжительности и исчисляется так же, как и ресурс: от начала эксплуатации объекта или ее возобновления до перехода в предельное состояние. Таким образом, отличие ресурса и срока службы состоит только в единицах измерения.
Срок сохраняемости исчисляется как календарная продолжительность хранения и транспортирования объекта, в течение и после которой значения показателей надежности сохраняются в установленных пределах.
Время восстановления характеризует календарную продолжительность операций по восстановлению работоспособного состояния объекта или продолжительность операций по техническому обслуживанию и ремонту.
Наработка - это временное понятие, которое служит для количественной оценки надежности объекта. Она может измеряться в часах, числах циклов нагружения, километрах пробега и других величинах, определяемых специфическими особенностями изделия.
Из-за большого числа конструктивных, технологических и эксплуатационных факторов, влияющих на надежность, точно ее рассчитать или предсказать нельзя. Надежность можно оценить только приближенно путем расчета с использованием теории вероятностей и математической статистики или специально организованных испытаний, а также сбора эксплуатационных данных об отказах.
Для оценки фактического технического состояния и контроля надежности оборудования (его основных узлов) производится анализ данных по временным показателям надежности оборудования — ресурсу, сроку службы, наработке (суммарной — с начала эксплуатации, с момента проведения последнего капитального ремонта). Показатели надежности, определяемые по годам за период не менее двух лет эксплуатации в соответствии с ГОСТ 27.002—83, рассчитывают по формулам, приведенным в табл. 1.1.
Таблица 1.1
Наименование и условное обозначение показателя по ГОСТ 27.002 | Формула для расчета статической оценки показателя надежности |
Средняя наработка на отказ (наработка на отказ) ![]() | ![]() |
Средний ресурс (средний срок службы) ![]() | ![]() |
Среднее время внепланового восстановления (ремонта) ![]() | ![]() |
Среднее время планового восстановления (ремонта) ![]() | ![]() |
Вероятность безотказной работы P(t) | ![]() |
Коэффициент технического использования ![]() | ![]() |
Примечания:
r - число отказов, произошедших за период наблюдений t ;
ti - наработка между двумя последовательными отказами;
n - число объектов, работоспособных в начальный момент времени (эксплуатационных наблюдений) t = 0;
tpecj- наработка каждого из объектов от начала эксплуатации;
t в i - продолжительность внепланового восстановления после 1-го отказа оборудования;
tППРi- продолжительность i-го планового восстановления оборудования;
NППР- число плановых ремонтов оборудования за период наблюдений t ;
п( t ) — число объектов (оборудования), отказавших на отрезке времени 0...t.
На основе анализа количественных показателей надежности принимается решение о необходимости проведения диагностики оборудования, его ремонта или замены. Уровень количественных оценок различается в зависимости от типа оборудования. Так, для магистральных насосно-перекачивающих станций при снижении величины средней наработки на отказ на 10 %, вероятности безотказной работы на 3 % оборудование, независимо от выработки назначенного ресурса, подлежит техническому освидетельствованию. Снижение коэффициента технического использования оборудования на 3...5 % свидетельствует о необходимости проведения экономической оценки целесообразности его дальнейшей эксплуатации.
Приведенные определения показывают, что надежность оборудования зависит не только от качества его изготовления, но и от своевременности технического диагностирования и обнаружения дефектов, полноты и качества производимых ремонтов.
Требование повышения надежности оборудования вступает в противоречие с требованием достижения максимального экономического эффекта. Любое повышение надежности достигается за счет увеличения расходов на изготовление машин, оснащения современными системами мониторинга и диагностики их технического состояния. Одновременно с повышением затрат на изготовление машины Q и с целью повышения ее надежности Р уменьшаются затраты на содержание и ремонт Q Р в течение всего срока службы машины (рис. 1.1). Суммарные эксплуатационные затраты Q С = Q и + Q Р имеют некоторое минимальное значение, соответствующее оптимальной надежности. Снижение эксплуатационных затрат и потерь от аварий и простоев оборудования является одним из основных источников повышения рентабельности производственных предприятий.
Рис. 1.1 Затраты на изготовление, ремонт и эксплуатацию оборудования
Наиболее важным показателем надежности является безотказ ность.
Отказ — событие, заключающееся в нарушении работоспособности технической системы или ее элементов. Критериями отказов оборудования являются: прекращение функционирования, снижение эксплуатационных параметров за предельно допустимый уровень. Наиболее опасными являются отказы, приводящие к катастрофическим ситуациям, возникновение которых создает угрозу для жизни и здоровья людей, приводит к тяжелым экономическим потерям или причинению большого вреда окружающей среде.
Если последствием отказа является катастрофическая ситуация, то уровень надежности должен задаваться максимально высоким. Экономические вопросы в таком случае не являются первостепенными.
Отказы можно разделить на два вида: внезапные и постепенные. Внезапные отказы происходят в любой момент времени из-за различных непредвиденных обстоятельств: внезапного повышения нагрузки, механического повреждения, стихийных бедствий и др. Появлению постепенных отказов предшествует накопление дефектов и повреждений. Общая закономерность распределения интенсивности отказов по времени приведена на рис. 1.2.
Рис. 1.2. Распределение интенсивности отказов:
Т1 — период приработки; Т2 — период нормальной эксплуатации; Т3 — период ускоренного накопления повреждений
Причина отказа - это явление, процессы, события и состояния, из-за которых возникает отказ объекта. Исследование причин отказа невозможно без привлечения физической теории надежности и ряда инженерных дисциплин. К явлениям, вызывающим отказы изделий машиностроения, могут быть отнесены: пластическая деформация, химическое воздействие среды, охрупчивание или разупрочнение поверхностей и т.п. К процессам могут быть отнесены: изнашивание, рост трещин, коррозия, старение материалов и т.п. Событиями, приводящими к отказам, могут являться: появление перегрузок, изменения напряжения в сети коррозионной защиты, попадание абразива в масло, схватывание сопрягаемых поверхностей, нарушение установленных режимов и правил эксплуатации и т.п.
Состояниями изделий, являющимися причиной отказов, могут быть: отсутствие защиты от попадания коррозионно-активной среды и влаги, наличие остаточных напряжений или концентраторов напряжений, макро- и микротрещины, дефекты сборки, наличие рисок и т.п.
При установлении причин отказа необходимо устанавливать явления, процессы, события и состояния, приводящие к их появлению, а также возможное сочетание этих факторов. В зависимости от причин отказов, последние могут быть разделить на конструкционные, производственные и эксплуатационные.
К конструкционным относятся отказы, возникающие в результате несовершенства или нарушения установленных правил и норм конструирования объекта (наличие концентраторов напряжений, ошибки в учете распределения напряжений, неправильный выбор материалов, незащищенность элементов от коррозии и т.п.).
К производственным относятся отказы, возникшие в результате несовершенства или нарушения установленного процесса изготовления или ремонта объекта, выполнявшегося на ремонтном предприятии. К наиболее типичным дефектам технологии следует отнести:
- дефекты из-за неправильного состава материала (включения, охрупчивающие примеси и т.д.);
- дефекты при плавке и изготовлении заготовок (пористость, усадочные раковины, неметаллические включения, расслоения);
- ошибки при механической обработке (задиры, заусенцы, трещины, прорезы, избыточная локальная пластическая деформация, ожоги);
- дефекты сварки (трещины, остаточные напряжения, углубления или недостаточная глубина провара шва, термическое повреждение отдельных участков основного материала и т.д.);
- дефекты термообработки (перегрев, закалочные трещины, обезуглероживание, избыточные остаточные аустениты и др;
- дефекты при обработке поверхностей (химическая диффузия, водородное охрупчивание, снижение механических свойств материала и др.);
- дефекты сборки (повреждения поверхностей, задиры, внесение абразива, несоответствие размеров деталей и др.).
К эксплуатационным относятся отказы, возникшие в результате нарушения правил и условий эксплуатации объекта (неправильное техническое обслуживание, низкое качество запасных частей, появление перегрузок, использование не по назначению и т.д.).
Анализ причин отказов проводится с целью обоснованной разработки мероприятия по их предотвращению, а также обоснованного выбора методов повышения ресурса и надежности аппаратов.
Начальный и завершающий периоды эксплуатации характеризуются повышенным количеством неисправностей и отказов по сравнению с этапом нормальной эксплуатации. Статистически закономерность увеличения количества отказов на начальном периоде эксплуатации объясняется приработкой деталей и проявлением конструктивных и производственных дефектов. Период нормальной эксплуатации является наиболее продолжительным и характеризуется практически постоянным значением интенсивности отказов. В третьем, завершающем, периоде проявляются так называемые деградационные отказы, интенсивность которых возрастает по мере увеличения износа, накопления микроповреждений и ухудшения (деградации) свойств материалов. При этом с увеличением зазоров в сопряжениях нарушается кинематика механизмов, ухудшаются условия смазки и возникают дополнительные динамические нагрузки. Обеспечить требуемую безотказность оборудования, особенно при монотонном накоплении дефектов и повреждений, исключить аварийные ситуации и минимизировать эксплуатационные затраты возможно только путем проведения своевременной диагностики.
Восстановление работоспособности оборудования
Из-за износа и накопления повреждений при эксплуатации оборудование подвергается ремонту. Технологическое оборудование в нефтяной и газовой промышленности в обязательном порядке снабжается паспортами. Данные о выполненных ремонтах, техническом обслуживании, испытаниях, а также проведенном диагностировании заносятся в паспорт в течение всего срока эксплуатации оборудования. Такие записи позволяют осуществить систематизацию и ретроспективный анализ накопления дефектов и повреждений, оценить эффективность проведенных ремонтов. Они также обязательно учитываются при проведении очередного технического диагностирования.
По мере эксплуатации и ремонта для каждого оборудования наступает такой момент, когда в результате физического и морального износа его эксплуатация и ремонт становятся невозможными или экономически невыгодными. В этом случае оборудование подвергается замене на новое.
Моральным износом называется уменьшение стоимости действующей техники под влиянием технического прогресса. Различают две формы морального износа:
• утрата действующей стоимости по мере того, как машины такой же конструкции начинают воспроизводиться дешевле;
• обесценивание действующей техники вследствие появления
более совершенных конструкций машин.
Согласно РД 22-36-13, оптимальный ресурс машины или ее составной части можно определить из соотношения
Где - стоимость объекта;
- затраты на поддержание надежности объекта по интервалам выработки; t – наработка.
Затраты на поддержание надежности объекта, как правило, можно аппроксимировать функцией вида
Где w – коэффициент; n – показатель уровня надежности машины.
Средние затраты на поддержание надежности объекта за наработку t могут быть определены из следующего выражения:
Оптимальный ресурс определяется из уравнений
Решив последнее уравнение относительно t, получим соотношение для определения оптимального ресурса объекта.
В общем виде изложенная выше методика позволяет определить предельное состояние любой машины через оптимальное значение затрат на приобретение и эксплуатацию машины.
Для восстановления работоспособности оборудования применяют следующие виды ремонта: реактивный ремонт, планово-предупредительный ремонт (ППР) и ремонт по фактическому техническому состоянию. Реактивная система имеет ограниченное применение и предполагает выполнение ремонта оборудования только в том случае, если оно выходит из строя или полностью вырабатывает свой ресурс. Данную систему применяют при использовании легкозаменяемого недорогого оборудования при наличии дублирования наиболее важных участков технологического процесса.
При невозможности или нецелесообразности дублирования применяют систему ППР, которая представляет собой совокупность организационно-технических мероприятий по техническому обслуживанию и ремонту, проводимых в плановом порядке. Сущность системы ППР заключается в том, что после отработанного заданного числа часов проводится определенный вид планового ремонта — регламентное техническое обслуживание, текущий, средний и капитальный ремонты.
Техническое обслуживание (ТО) подразделяют на периодическое и сезонное. Сезонное ТО включает сезонную замену сортов масел (зимних или летних), установку или снятие утеплении, предпускового подогрева и т.д. Периодическое ТО регламентируется руководствами по эксплуатации соответствующего оборудования и включает периодическую промывку фильтров, замену шинно-пневматических муфт, регулировку тормозов, осмотр и чистку отдельных узлов, регулировку натяжения и т.д.
Текущий ремонт не бывает продолжительным и часто выполняется одновременно с ТО. В его состав входит устранение небольших неисправностей, замена мелких, быстро изнашивающихся деталей и узлов (например, замена вкладышей подшипников, сальниковых уплотнений, устранение повышенных зазоров, крепеж элементов оборудования и т.д.).
Средний ремонт в отличие от текущего предусматривает замену основных узлов и деталей (например, силовых и трансмиссионных валов, зубчатых колес, крыльчаток центробежных насосов и т.д.) и выполняется, как правило, с полной или частичной разборкой агрегата.
Капитальный ремонт всегда сопряжен с полной разборкой машины и ставит своей задачей замену или восстановление до первоначального состояния всех изношенных узлов и деталей. По окончании ремонта проводятся приемо-сдаточные испытания, в том числе испытания под нагрузкой. Нередко капитальный ремонт совмещают с модернизацией, что позволяет не только полностью восстановить ресурс машины, но и превзойти первоначальные показатели.
Помимо перечисленных возможны также внеплановые ремонты, вызванные аварийными отказами оборудования из-за преждевременного износа или форс-мажорных обстоятельств (например, наводнения или оползни, закупорка трубопроводов льдом или гидратами и т.д.).
Период между капитальными ремонтами называют ремонтным циклом. Число и последовательность входящих в него ремонтов и осмотров определяют структуру ремонтного цикла, а время между ремонтами — межремонтный период. Для некоторых видов оборудования структура ремонтного цикла может включать в себя не все виды плановых ремонтов. Так, для бурового оборудования средний ремонт не производится, а структура ремонтного цикла, например для буровой лебедки, имеет вид К-9Т-К, для буровых роторов К-7Т-К, где соответственно К — капитальный ремонт, Т — текущий ремонт, 9 и 7 — число текущих ремонтов в цикле.
В практике ресурс однотипного оборудования назначают по наиболее «слабым» экземплярам, показавшим наихудший результат при эксплуатации, поэтому длительность ремонтного цикла и его структуру в системе ППР назначают заведомо такими, чтобы максимально исключить аварии оборудования, особенно связанные с возможностью травмирования людей или большим экономическим или экологическим ущербом. При этом в ремонт, как правило, выводится значительная часть оборудования в достаточно хорошем техническом состоянии с большим остаточным ресурсом, которое могло бы еще долго работать. Более того, отремонтированное таким образом оборудование часто имеет более низкую надежность, что обусловлено появлением ранее отсутствовавших дефектов послеремонтной сборки и повторной приработкой трущихся поверхностей.
Таким образом, основным недостатком системы ППР является проведение преждевременных ремонтов технологического оборудования, что приводит к большим экономическим потерям. Кроме того, ППР не гарантирует полное исключение внезапных отказов оборудования и связанных с этим последствий. Исключить перечисленные недостатки позволяет переход на систему ремонта по фактическому техническому состоянию на основе проведения своевременной диагностики или мониторинга технического состояния оборудования.
В настоящее время системами диагностики и мониторинга в нефтяной и газовой промышленности оснащены большинство агрегатов большой единичной мощности, а также другие виды оборудования, аварии которого чреваты тяжелыми последствиями. Это позволяет планировать и производить ремонт или замену каждого экземпляра оборудования в зависимости от его реального технического состояния.
Дата добавления: 2019-07-15; просмотров: 7881; Мы поможем в написании вашей работы! |
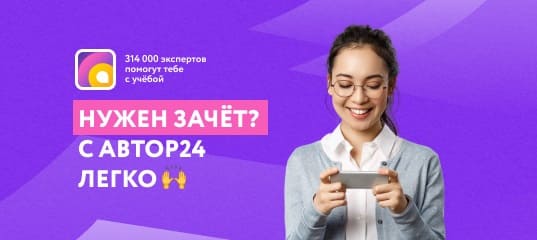
Мы поможем в написании ваших работ!