Конструкции центрифуг и сепараторов
ЦЕНТРОБЕЖНОЕ ОСАЖДЕНИЕ И ЦЕНТРОБЕЖНОЕ ФИЛЬТРОВАНИЕ
Центробежная сила и фактор разделения
Отстойное центрифугирование
Центробежное фильтрование
Конструкции центрифуг и сепараторов
Разделение неоднородных систем в циклонах
Для разделения неоднородных систем – суспензий и эмульсий под воздействием центробежной силы применяется центрифугирование. Под действием центробежной силы в аппарате более тяжелые частицы отбрасываются к стенкам сосуда и неоднородная система разделяется. Использование центробежной силы вместо силы тяжести позволяет регулировать процесс разделения систем и значительно его интенсифицировать, так как создаваемое значение центробежной силы может во много раз превосходить значение силы тяжести.
В процессе разделения центробежную силу можно получить вращением сосуда, содержащего неоднородную смесь, или вращением разделяемого потока, вводимого с большой скоростью в неподвижный аппарат специальной формы.
Аппараты с вращающимся сосудом – ротором носят название центрифуг и жидкостных центробежных сепараторов; неподвижные аппараты с вращающимся в них потоком газа называют циклонами, а жидкости – гидроциклонами.
Стенки ротора центрифуги могут быть сплошными, тогда на их поверхности накапливается твердый осадок или тяжелая жидкость, которые периодически или непрерывно удаляются - такие центрифуги называются отстойными.
|
|
Применяются также центрифуги с перфорированными стенками ротора, на поверхности которых размещается фильтровальная ткань, задерживающая осадок и пропускающая фильтрат; такие центрифуги называются фильтрующими.
Суспензии можно разделять в роторах как со сплошной, так и с перфорированной стенкой, а эмульсии – только в роторах, имеющих сплошную стенку.
В нефтегазоперерабатывающей и нефтехимической промышленности центрифугирование применяется для отделения воды и твердых частиц от нефти и нефтепродуктов, разделения суспензий с нерастворимой твердой фазой (обработка поливинилхлорида, полистирола, полиэтилена высокого давления, сажевой пульпы и т.д.), при производстве парафина, церезинов и др. процессах.
Центробежная сила и фактор разделения
При вращении тела возникает центробежная сила С (в (кг·м)/с2), направленная по радиусу от оси вращения и равная произведению массы тела m (в кг) на квадрат окружной скорости W (в м/с), деленному на радиус вращения r (в м):
C=mW2/ r .
При замене массы весом, деленным на ускорение свободного падения, получим
С = G W/2 gr .
Выражая окружную скорость через угловую W = ω r или через частоту вращения n (число оборотов в минуту)
|
|
W = 2π rn /60, представим значение центробежной силы в виде
C = m ω 2 r = G ω 2 r/g (XIV.1)
или С = Gm 2 /900= GDn 2 /1800, так как π2 ≈ g .
Определим отношение центробежной силы к силе тяжести, которое соответствует отношению ускорения, создаваемого центробежной силой ω2 r, к ускорению силы тяжести g:
C / G = W 2/ gr = ω2 r / g = m 2 /900=Кц (XIV.2)
Это отношение показывает, во сколько раз центробежная сила больше силы тяжести, и называется фактором разделения. В поле действия центробежных сил процесс разделения интенсифицируется пропорционально величине фактора разделения.
Из выражения (XIV.2) следует, что величина Кц растет пропорционально квадрату числа оборотов n и радиусу вращения r. Существенное увеличение Кц обычно достигается возрастанием числа оборотов ротора, тогда как увеличение радиуса вращения ротора лимитируется его прочностными свойствами. Фактор разделения промышленных центрифуг изменяется от 90 до 4000 для нормальных центрифуг и достигает 15000 для сверхцентрифуг.
Отстойное центрифугирование
При подаче суспензии во вращающийся ротор образуется кольцевой жидкостный слой, максимальная толщина которого равна ширине закраины ротора (рис. XIV-1).
|
|
Рис. XIV-1. Схема отстойной центрифуги для разделения суспензий:
1 — питающая (загрузочная) труба; 2 — закраина ротора; 3 — ротор; 4 — кожух.
Потоки: I — суспензия; II — фугат; III—осадок
В аппарате под действием центробежной силы происходит осаждение частиц на стенках ротора, а осветленная жидкость по мере поступления новых порций суспензии переливается через закраину и выводится из ротора.
В жидкостном кольце устанавливается движение жидкости снизу вверх. Взвешенные частицы, содержащиеся в исходной суспензии, находятся под воздействием центробежных и выталкивающих сил. Центробежная сила перемещает частицу со скоростью Wц по направлению от центра к стенке ротора, а выталкивающая — со скоростью v вдоль его стенок. Если время нахождения жидкости в роторе является достаточным для осаждения частиц, то они достигают стенки и образуют слой осадка, а из ротора будет уходить только чистая жидкость.
Такие отстойные центрифуги бывают непрерывно и периодически действующими и отличаются методами удаления осадка и конструкцией ротора. При полной остановке ротора выгрузка и съем осадка производятся вручную без применения специальных механизмов, а также контейнерным или кассетным способом; на ходу при полном или уменьшенном числе оборотов ротора – при помощи ножей или скребков; при непрерывной работе машины – шнеком, вращающимся относительно ротора, поршнем-толкателем, движущимся возвратно-поступательно (пульсирующим), а также под действием центробежной силы или силы тяжести и вибраций.
|
|
Если в ротор подавать эмульсию из жидкостей с различной плотностью, состоящую, например, из масла со взвешенными в нем капельками воды, то последние, имея большую плотность, под действием центробежных сил будут двигаться к стенке и, сливаясь около нее, образовывать второе внешнее кольцо воды – тяжелой жидкости (рис. XIV-2). Разделившиеся жидкости постоянно выводят из ротора. Таким образом, отстойная центрифуга для разделения эмульсий работает непрерывно.
Рис. XIV-2. Схема центрифуги для разделения эмульсий:
1 – кольцевая диафрагма; 2 – закраина ротора; 3 – ротор.
Потоки: I – эмульсия; II – тяжелая жидкость; III – легкая жидкость
Для расчета скорости движения в поле центробежных сил используют те же положения, которые были рассмотрены в процессе осаждения под действием силы тяжести, заменяя силу тяжести центробежной силой или их отношением Кц.
Такое допущение не учитывает некоторого различия, обусловленного тем, что осаждение под действием силы тяжести происходит в плоском слое, тогда как центробежное осаждение протекает в кольцевом слое. Общая толщина кольцевого слоя жидкости в роторе центрифуги по его длине несколько убывает, однако при достаточно большом числе его оборотов это различие настолько мало, что внутренняя поверхность слоя может быть принята за цилиндрическую.
При осаждении частиц в поле центробежных сил по мере движения частиц к стенке ротора в связи с увеличением радиуса вращения возрастает центробежная сила, что также несколько отличает процесс от осаждения под действием силы тяжести.
Если суспензия или эмульсия вращается с угловой скоростью ω и, если плотности жидкости ρж и взвешенных в ней частиц ρч различны, то под действием центробежной силы частицы будут двигаться в направлении ее действия, т.е. радиально, удаляясь от оси вращения или приближаясь к ней.
Не учитывая отмеченных различий и принимая, что действующая сила при центробежном осаждении будет больше движущей силы при отстаивании в поле действия силы тяжести в Кц раз, получим выражение для скорости центробежного осаждения W4i аналогичное уравнению (XII.2):
Для ламинарного режима аналогично уравнению (XII.5) получим
Кц (Х1I.3)
а для газовых суспензий
Кц
При центробежном осаждении границы возможных режимов движения определяются также численными значениями критерия Рейнольдса: для ламинарного движения Re < 2,0; для переходного 2,0 < Re < 500; для турбулентного
Re > 500.
Критериальное уравнение для центробежного осаждения имеет вид аналогичный уравнению (ХII.3):
𝞷Re2 = Аг·Кц
или
Re =1,155 0,5 (XIV.4)
Для наиболее часто встречающегося в практике при расчетах ламинарного режима движения 𝞷 = 24/Re, тогда уравнение (XIV.4) принимает вид
Re=
т.е. режим осаждения будет ламинарным, если Ar · K ц < 36.
Рассмотрим расчет производительности отстойных центрифуг. Проведем расчет для следующих заданных размеров ротора центрифуги R0, Rи Н (см. рис. ХIV-1).
При расчете примем ламинарный режим осаждения, что соответствует осаждению наиболее мелких частиц, лимитирующих производительность центрифуги, и рассмотрим свободное осаждение, когда концентрация твердого вещества невелика и частицы не оказывают влияния одна на другую. В соответствии с уравнением (XIV.3) переменная скорость осаждения Wц может быть выражена производной от радиуса по времени, так как частица движется в радиальном направлении:
W ц =
Разделяем переменные и, интегрируя в пределах самого длинного пути от R 0 до R, находим время, затрачиваемое на осаждение наименьшей частицы диаметром d в самом неблагоприятном случае:
(XIV.5)
Время осаждения должно быть меньше или в крайнем случае равно времени τ н нахождения жидкости в роторе. Последнее можно найти, принимая, что ротор работает по принципу полного вытеснения, из соотношения
где Vp — рабочий объем ротора, равный объему жидкостного кольца, находящегося в нем,
Vp = π( R 2 - )Н;
V — объем подаваемой в центрифугу жидкости, м3/с.
Отсюда
V = =
(XIV.6)
В роторе центрифуги жидкость не претерпевает полного обмена, она движется только в части слоя, прилегающей к внутренней стороне кольца; кроме того, по мере отложения в роторе осадка рабочий объем жидкости уменьшается. Таким образом, приведенный выше расчет вследствие уменьшения величины τ н не вполне точен. Расчет можно скорректировать, если при нахождении V ввести коэффициент запаса (меньший единицы).
Совместное решение уравнений (XIV.5) и (XIV.6) позволяет определить предельный диаметр частиц полидисперсной смеси, выше которого центрифуга обеспечит осаждение при принятой производительности.
При разделении эмульсий (см. рис. XIV-2) ход расчета остается таким же, с той лишь разницей, что капелька диспергированной жидкости должна пройти путь меньший, чем R - R0, так как ей надо лишь пересечь слой ''чужой" жидкости и добраться до "своего" слоя. Учесть это в расчете можно, используя другие пределы интегрирования в уравнениях (XIV.5). Если во взвешенном состоянии находятся капельки тяжелой жидкости, то для обеспечения отстоя они должны пройти путь в пределах радиусов вращения от R0 до R1, если взвешены капельки легкой фазы — от R до R1. Радиус R1 поверхности раздела слоев обеих жидкостей можно определить из соотношения поперечных сечений обоих жидкостных колец, равного объемному отношению жидкостей в исходной смеси. Например, если объемная доля тяжелой жидкости в эмульсии равна х, то доля легкой жидкости окажется 1 - х, и определяется из уравнений
π( R 2 - )= хπ( R 2 -
) или π(
)= (1-х)π( R 2 -
).
Центробежное фильтрование
В роторах центрифуг осуществляется фильтрование суспензий за счет перепада давления, создаваемого центробежной силой.
Для этого в фильтрующих центрифугах боковая стенка ротора 3 перфорирована, а на внутренней поверхности стенки размещена дренажная сетка 4 и фильтровальная ткань 5 (рис. XIV-3). Под действием центробежной силы суспензия давит на стенку, жидкость проходит через фильтрующую ткань, ее капли попадают в кожух, внутри которого вращается ротор, стекают в поддон и в виде фильтрата выводятся через сливной штуцер. Осадок образуется на стенке и удаляется с нее вручную (при остановке центрифуги) либо на ходу при помощи скребков, ножей или шнеков.
Рис. XIV-3. Схема фильтрующей центрифуги;
1– питающая (загрузочная) труба; 2 – закраина ротора; 3 – перфорированная стенка ротора;
4 – дренажная сетка; 5 – фильтровальная ткань; 6 – кожух.
Потоки: I – суспензия; II– фильтрат; III – осадок
Определим движущую силу центробежного фильтрования. Выделим внутри кольца суспензии, находящейся во вращающемся роторе центрифуги, элементарный слой толщиной dr, находящийся на расстоянии r от оси вращения (см. рис. XIV-3). Масса этого слоя равна произведению его плотности ρс на объем:
dm =ρс Н·2πr·dr.
Центробежная сила, действующая на элементарное кольцо, согласно уравнению (XIV. 1) равна dC = ω2rdm = ρс Н · 2πω2 r2 · dr.
Давление этого кольца на поверхность S суспензии, расположенную за кольцом, составит
dp= =
= ρс · ω 2 r · dr.
По закону Паскаля это давление через суспензию передается стенке ротора – фильтрующей перегородке – или слою осадка у стенки. Общий перепад давления при центробежном фильтровании найдем суммированием давлений, соответствующих всем элементарным слоям суспензии:
Δр = =
(R-
).
При центробежном фильтровании окружная скорость вращения ротора ω постоянна и поэтому значение общего перепада давления Δр не меняется. Найдя Δр, дальнейшие расчеты производят как для режима фильтрования при постоянном перепаде давления Δр = const по уравнениям (XIII.4) – (XIII.7),
При расчете производительности фильтрующих центрифуг периодического действия учитывают, что полный цикл работы складывается из следующих этапов: загрузки, пуска и разгона ротора, центрифугирования, промывки осадка, дополнительного отжима, торможения, разгрузки осадка. У автоматически работающих центрифуг ряд отмеченных этапов отсутствует.
Оценивая продолжительность каждого этапа τ1, τ1 и т.д., находят длительность полного цикла τ1 + τ2 +. . . = ∑τ и число циклов в секунду
z = 1 / ∑τ.
Далее для центрифуги выбранного типоразмера определяют рабочий объем ротора
Vp = π( R 2 - )Н.
Для периодически действующей центрифуги объем Vp будёт равен максимальной ее производительности за один цикл по исходной суспензии; тогда объемная и массовая производительности центрифуги составят соответственно
V 1 = Vp и G 1 = V 1 ρс (XIV.6)
а число центрифуг на установке
где G — массовый расход суспензии, кг/с.
Если суспензия подается в ротор непрерывно, то весь рабочий объем ротора может быть занят осадком. Тогда в соответствии с уравнением (XIV.6) для исходной суспензии производительность по объему составит
V1 = Vp(1+ x)z,
где х — объем осадка, приходящийся на 1 м3 фильтрата.
Конструкции центрифуг и сепараторов
Современные промышленные центрифуги и сепараторы — это сложнейшее технологическое оборудование, состоящее из многих механизмов высокой точности, обладающее высотами скоростями и управляемое с помощью сложных электрогидравлических или электрических систем.
В силу сложившихся традиций центрифуги и сепараторы имеют самостоятельные системы классификации.
Центрифуги могут быть классифицированы по следующим характерным признакам:
а) по характеру протекания процесса центрифуги делят на машины периодического и непрерывного действия;
б) по технологическому назначению или принципу разделения различают следующие типы центрифуг: осадительные (отстойные) и осветляющие — для разделения суспензий; разделяющие (сепарирующие) — для разделения эмульсий; фильтрующие — для разделения суспензий; комбинированные, в которых сочетаются два принципа разделения — осаждение и фильтрование;
в) по основному конструктивному признаку центрифуги бывают горизонтальные (с горизонтальным расположением вала); вертикальные; наклонные; подвесные с верхним приводом; подвесные с нижним приводом (маятниковые); вертикальные трубчатые;
г) по способу выгрузки осадка из ротора различают центрифуги с ручной, контейнерной (кассетной), ножевой, шнековой, инерционной, механико-пневматической выгрузкой и выгрузкой пульсирующим поршнем.
В нефтехимических производствах наиболее перспективны саморазгружающиеся сепараторы.
По конструкции разгрузочных устройств такие сепараторы разделяются на три основные группы: с непрерывным, пульсирующим и непрерывно-циклическим отводом осадка.
Конструкции центрифуг и сепараторов, применяемых в нефтегазоперерабатывающей и нефтехимической промышленности, многочисленны и рассматриваются в специальной литературе. Опишем принципиальное устройство только некоторых из них.
Центрифуги маятниковые с нижним приводом. Маятниковые центрифуги представляют собой вертикальные подвесные самоустанавливающиеся машины периодического действия с нижним приводом. В зависимости от технологического назначения они могут быть фильтрующими и осадительными. По способу выгрузки осадка различают центрифуги с верхней ручной выгрузкой через борт, с нижней ручной выгрузкой через днище ротора и с контейнерной выгрузкой.
Конструкция фильтрующей маятниковой центрифуги с нижней выгрузкой осадка представлена на рис. XIV-4.
На подвеске, состоящей из фундаментной плиты 1 и трех оперных колонок 3t подвешена станина 2, на которой монтируют основные узлы и детали центрифуги. Подвеска станины выполнена на тягах, снабженных шаровыми опорными поверхностями, позволяющими центрифуге самоустанавливаться во время работы. Вибрация машины гасится пружинами, надетыми на тяги и установленными в опорных колонках. В центре станины расположена опора 10 ротора. На верхнем конце вала опоры 9 крепится ротор 5, снабженный бортовым кольцом (закраиной) 5; на нижнем — приводной шкив 14 и тормоз 15. Ротор огражден кожухом 4, который вместе со станиной образует сборник фильтрата (фугата для осадительных центрифуг) и одновременно изолирует зону обработки продукта в машине от окружающей среды.-В верхней части кожух оснащен загрузочным устройством 7 и закрыт крышкой 8. Привод центрифуги расположен снизу и состоит из электродвигателя И, на валу которого закреплена турбомуфта 12, и клиноременной передачи 13, передающей вращение на приводной шкив 14, закрепленный на валу центрифуги. Роторы фильтрующих центрифуг укомплектованы подкладными (дренажными) ситами.
Маятниковые центрифуги характеризуются простотой и компактностью, малой массой и низкой стоимостью.
Рис. XIV-4. Конструкция фильтрующей маятниковой центрифуги с нижней выгрузкой осадка:
1 — фундаментная плита; 2 — станина; 3 — опорные колонки; 4 — кожух; 5 — ротор; 6 — бортовое кольцо (закраина); 7 — загрузочное устройство; 8 — крышка; 9 — вал; 10 — опора ротора; 11 — электродвигатель; 12 — турбомуфта; 13 — клиноременная передача; 14 — приводной шкив; 15 — тормоз
Существенными их недостатками являются применение ручного труда для выгрузки осадка и периодические остановки для проведения этой операции, поэтому количество таких центрифуг в производстве постепенно уменьшается. На смену им приходят более совершенные маятниковые центрифуги — с механизированной выгрузкой осадка (с помощью ножа или скребка).
Центрифуги подвесные с верхним приводом и нижней выгрузкой осадка. Особенностью таких центрифуг является шарнирная подвеска вертикального вала с ротором, допускающая отклонение системы от вертикальной оси и самоцентрирование вращающихся масс. Вследствие этого центрифуги малочувствительны к неравномерной загрузке ротора и обладают большой динамической устойчивостью во время работы. Подвесные центрифуги изготовляют с фильтрующим или осадительным ротором, ручной или механизированной выгрузкой осадка. В механизированных центрифугах осадок
выгружается при пониженной скорости вращения ротора, у центрифуг с ручной разгрузкой — при остановленном роторе.
На рис. XIV-5 представлена подвесная осадительная центрифуга, применяемая в нефтеперерабатывающей и нефтехимической промышленности для очистки присадок к маслам от механических примесей.
Центрифуга снабжена осадительным ротором 7 и обогреваемым кожухом 6 со специальным разгрузочным бункером 8. Загрузка ротора осуществляется непрерывно через питающую трубу 4 с калиброванным наконечником при наибольшей скорости вращения ротора 1500 об/мин. Фугат отводится из ротора непрерывно подвижной отводящей трубой 3. Осадок выгружают из ротора с помощью механизма среза 5 периодически при пониженном числе оборотов ротора (до 100 об/мин) в специальный бункер 8. Привод центрифуги — от фланцевого электродвигателя 1, соединенного с валом 2 специальной упругой муфтой.
Горизонтальные центрифуги с ножевой выгрузкой осадка. Центрифуги этого типа изготовляются в двух конструктивных исполнениях: с фильтрующим (рис. XIV-6) и осадительным ротором.
Рис. XIV-6. Конструкция горизонтальной центрифуги с ножевой выгрузкой осадка:
1 — разгрузочный бункер; 2 — питающая труба; 3 — механизм для среза осадка; 4 — воздушник; 5 — кожух; 6 — ротор; 7 — опоры вала; 8 — вал; 9 — станина; 10 — клиноременная передача; И — электродвигатель
Общий конструктивный признак центрифуг — горизонтальное расположение оси ротора 6, вал 8 которого вращается в подшипниках качения 7, установленных в станине 9. Привод центрифуги от — электродвигателя 11 через клиноременную передачу 10. На передней крышке центрифуги смонтированы механизм среза осадка 3, разгрузочный бункер 1, питающая труба 2. В кожухе 5 центрифуги предусмотрен люк для доступа к ротору при замене или ре монте сит для фильтрующих центрифуг и люк-воздушник 4 для отвода паров и газов из внутренней полости кожуха.
Ротор в фильтрующих центрифугах — сварной с перфорированной обечайкой. Внутри ротора при помощи планок и колец закреплены дренажное и фильтрующее сита. В зависимости от обрабатываемой суспензии фильтрующие сита могут быть заменены фильтровальными тканями.
Ротор осадительных центрифуг — сплошной сварной. У этих центрифуг в отличие от фильтрующих имеется механизм отвода осветленной жидкости, состоящий из отводящей трубы с силовым гидроцилиндром и дросселем для регулирования скорости поворота отводящей трубы.
Основное преимущество горизонтальных центрифуг с ножевой выгрузкой осадка состоит в возможности проведения всех стадий процесса в автоматическом режиме и при постоянной частоте вращения ротора. К недостаткам следует отнести измельчение кристаллов при срезе осадка и большие трудности регенерации фильтрующей перегородки при обработке суспензии с нерастворимой твердой фазой.
Осадительные горизонтальные центрифуги со шнековой выгрузкой осадка (рис. XIV-7). Общий конструктивный признак таких центрифуг — горизонтальное расположение оси конического или цилиндроконического ротора 3 с соосно расположенным внутри него шнеком 4. Ротор и шнек вращаются в одном направлении, но с различным числом оборотов, в результате чего образующийся осадок перемещается шнеком вдоль ротора. Ротор установлен на двух опорах и приводится во вращение от электродвигателя через планетарный редуктор. Суспензия подается по питающей трубе 1 во внутреннюю полость шнека, откуда через окна обечайки шнека поступает в ротор. Под действием центробежной силы происходит ее разделение и на стенках ротора осаждаются частицы твердой фазы. Осадок транспортируется шнеком к выгрузочным окнам 2, расположенным в узкой части ротора. Осветленная жидкость (фугат) течет в противоположную сторону к сливным окнам 6, переливается через сливной порог и выбрасывается из ротора. Диаметр сливного порога можно регулировать с помощью сменных заслонок или поворотных шайб. Ротор закрыт кожухом 5 с перегородками, отделяющими камеру 7 (для фугата) от камеры 8 (для осадка).
Осадительные центрифуги со шнековой выгрузкой осадка предназначены в основном для разделения суспензий с нерастворимой твердой фазой и применяются для обезвоживания кристаллических и зернистых продуктов, классификации материалов и осветления суспензий. Такие центрифуги успешно применяются в качестве первой ступени сепарирования при переработке нефтешлама.
Главное достоинство этих центрифуг — непрерывность процесса и высокая производительность при низком удельном расходе энергии и массе машин. К недостаткам таких центрифуг следует отнести невысокую степень обезвоживания осадка, невозможность проведения в машине качественной его промывки, а также быстрый износ шнека и ротора при обработке абразивных продуктов.
Центрифуги трубчатые. При разделении стойких эмульсий и осветлении суспензий, содержащих незначительные количества твердых высокодисперсных примесей, необходимо увеличить фактор разделения Кц. Как видно из уравнения (XIV.2), этого можно достичь увеличением либо г, либо п, так как при этом увеличивается окружная скорость W, Учитывая, что механические напряжения в корпусе ротора возрастают пропорционально квадрату окружной вкорости, что является лимитирующим фактором, увеличение фактора разделения предпочтительнее обеспечить за счет повышения числа оборотов при уменьшении диаметра ротора.
Использование этого принципа и привело к созданию трубчатых центрифуг (сверхцентрифуг) с внутренним диаметром ротора 105 и 150 мм и числом оборотов соответственно 15000 и 13500 в минуту. Для увеличения времени пребывания жидкости в сверхцентрифуге высоту ротора принимают в 5-н7 раз большей его диаметра.
Трубчатые центрифуги выпускают с осветляющим или разделительным (сепарирующим) ротором (рис. XIV-8). Общий конструктивный признак центрифуг — трубчатый ротор 1, подвешенный на валу 4, с вертикальной осью вращения и плавающей нижней опорой скольжения. Трехлопастная крыльчатка 2 сообщает разделяемой жидкости угловую скорость ротора. Станина 7 — чугунный литой корпус одновременно служит защитным кожухом. Привод центрифуги от индивидуального электродвигателя 3, расположенного в верхней части корпуса, через плоскоременную передачу с натяжным устройством.
При работе центрифуги эмульсия подается через сопло питающей трубы 10 в нижнюю часть ротора, струя отражается от отбойного диска 9 к стенкам ротора. Эмульсия, вращаясь вместе с ротором, протекает вдоль его стенок в осевом направлении вверх и разделяется на тяжелую и легкую жидкости. Тяжелая жидкость проходит через отверстия головки, расположенные у стенки ротора, поступает в нижнюю сливную тарелку 6 и через патрубок выводится из центрифуги. Легкая жидкость проходит через отверстия головки, расположенные ближе к оси ротора, собирается в верхней сливной тарелке 5 и выводится через патрубок. Положение поверхности раздела слоев тяжелой и легкой жидкости регулируют сменной кольцевой диафрагмой.
При соответствующем изменении головки ротора и периодической разгрузке осадка сверхцентрифуги применяют также и д*я разделения суспензий с незначительным содержанием твердой фазы.
Сепараторы. Жидкостные сепараторы — одна из разновидностей оборудования для разделения жидких гетерогенных систем под действием центробежной силы. По характеру процесса и его движущей силы жидкостные сепараторы наиболее близки к центрифугам.
На рис. XIV-9 представлена конструкция саморазгружающегося тарельчатого сепаратора с центробежной пульсирующей выгрузкой осадка. На вертикальном валу 4 установлен ротор 8, внутри которого помещен пакет 7 тонкостенных вставок-тарелок, имеющих несколько отверстий по окружности. Тарелки собраны так, что их отверстия совпадают и образуют сквозные каналы, в которые поступает исходная жидкость из центрального патрубка. В корпусе ротора установлено также подвижное днище 5, которое периодически опускается и открывает разгрузочные щели 6. Под действием центробежной силы из разгрузочных щелей выбрасывается осадок, который собирается в полости кожуха 9 и выводится из сепаратора. Для отвода легкой и тяжелой жидкости используют неподвижные напорные диски 10 и 11. Привод сепаратора от электродвигателя 1 через червячный редуктор 3.
Рис. XIV-9. Конструкция саморазгружающегося тарельчатого сепаратора фирмы: "Алъфа-Лавалъ
1 — электродвигатель; 2 — тормоз; 3 — червячный редуктор; 4 ~ вал; 5 — подвижное днище;
6 — разгрузочные щели; 7 — пакет тарелок; 8 — ротор; 9 — кожух;
10 — напорный диск легкой жидкости; 11 — напорный диск тяжелой жидкости.
Потоки: I — исходная жидкость; II — легкая жидкость; III — тяжелая жидкость; IV — осадок
Принцип работы трехфазных тарельчатых сепараторов рассмотрим на примере разделения нефтешлама (рис. XIV-10). Перед началом сепарирования по каналу 11 подают буферную воду, которая поступает под подвижное днище 1. Под действием гидростатического давления подвижное днище поднимается и плотно прижимается к крышке ротора 3, перекрывая разгрузочные щели 2. Нефтешлам подается в центр ротора и по системе сквозных каналов в пакете тарелок 4 распределяется между ними. Процесс сепарирования происходит в пакете тарелок, число которых (50+200 шт.) зависит от размеров сепаратора. Выделенная нефть перемещается к оси вращения и выводится из ротора напорным диском б. Вода вместе с частицами осадка направляется к периферии ротора. Выйдя из пакета тарелок, вода отводится из ротора по каналам между разделительной тарелкой 5 и крышкой ротора к напорному диску 7.
![]() | в
![]() |
Рис. XIV-10. Схема работы ротора саморазгружающегося тарельчатого сепаратора фирмы "Альфа-Лаваль”: а — процесс сепарирования; б — процесс разгрузки; 1 — подвижное днище; 2 — разгрузочные щели; 3 — крышка ротора; 4 — тарелки; 5 — разделительная тарелка; б — напорный диск для нефти; 7 — напорный диск для воды; В — канал подачи промывной воды; 9 — вспомогательный поршень; 10 — пружина; 11, 12 — каналы подачи буферной воды; 13 — сливной канал. Потоки: I — нефтешлам; 11 — нефть; III — вода; IV — буферная вода; V — осадок |
После накопления н шламовом пространстве определенного количества осадка его вы- гружают из ротора. Предварительно прекращают отвод воды из сепаратора и по каналу 8 вводится промывная вода в количестве, равном объему подлежащего выгрузке осадка. При этом поверхность раздела легкой и тяжелой фаз смещается внутрь пакета тарелок с тем, чтобы при открытии разгрузочных щелей исключить возможность потерь нефти с выгружающимся осадком и водой. Такой способ оттеснения нефти к центру снижает возможность эмульгирования, требует меньшего количества воды и сохраняет качество отводимой нефти в период разгрузки.
После того как ротор подготовлен к разгрузке, по каналу 12 кратковременным импульсом подается буферная вода в камеру над вспомогательным поршнем 9. Гидростатическое давление преодолевает силу пружин 10, и вспомогательный поршень, опускаясь, открывает сливные каналы 13. Под действием гидростатического давления в роторе подвижное днище перемещается вниз, открывая разгрузочные щели для выгрузки осадка и воды.
Во время разгрузки подача нефтешлама не прекращается. Разгрузочные щели открываются лишь на 0,1 с, и за это время выбрасывается точно определенный объем осадка и воды. После разгрузки вспомогательный поршень под воздействием пружин перемещается вверх, закрывая сливные каналы 13, вода по каналу 11 подается под подвижное днище, и оно возвращается в верхнее положение, перекрывая разгрузочные щели 2. Прекращается подача промывной воды по каналу 8 и продолжается обычный процесс сепарирования.
Сепаратор комплектуется программным регулятором. Все операции цикла выполняются в заданной последовательности с помощью электронных датчиков. Сигнальная система обеспечивает наблюдение за давлением нефти на выходе, исправностью системы разгрузки, напряжением сети, температурой сепарирования, вибрацией.
Дата добавления: 2019-07-15; просмотров: 1534; Мы поможем в написании вашей работы! |
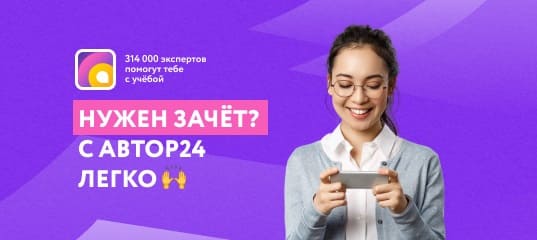
Мы поможем в написании ваших работ!