Вакуумные фильтры непрерывного действия.
Барабанные вакуум-фильтры применяют при непрерывном разделении суспензий концентрацией 50...500 кг/м3. Твердые частицы могут иметь кристаллическую, волокнистую, аморфную, коллоидальную структуру. Производительность фильтра зависит от структуры твердых частиц и снижается в указанной выше последовательности.
Барабанные вакуум-фильтры (рис. 8) выпускают с внешней и внутренней фильтрующей поверхностью, которая обтягивается текстильной фильтровальной тканью. Вращающийся горизонтальный перфорированный барабан разделен перегородками на несколько секций одинаковой формы, которые за оборот барабана проходят несколько рабочих зон: фильтрования, обезвоживания, промывки, удаления осадка и регенерации фильтровальной ткани. Устройством, управляющим работой фильтра, является распределительная головка, через которую секции барабана в определенной последовательности подсоединяют к магистралям вакуума, сжатого воздуха и промывной жидкости.
Рис. 8 Барабанный вакуум-фильтр с распределительной головкой:
1 - перфорированный барабан; 2 - фильтровальная ткань; 3 - ножевое устройство; 4 – секция; 5 – корыто; 6 – мешалка; 7 – труба; 8 – разбрызгиватель; 9 - распределительная головка
В стадии фильтрования зона фильтра под фильтрующей тканью соединяется с вакуумом и фильтрат, находящийся в корыте, проходит через фильтровальную ткань. Осадок откладывается на ее поверхности. Промытый и подсушенный осадок непрерывно срезается ножом. Чтобы взвешенные частицы не отстаивались, корыто снабжено качающейся мешалкой.
|
|
Рис. XVIII-11. Схема барабанного вакуум-фильтра:
/ — суспензия; // — подача промывной жидкости; /// — фильтрат; IV — вывод промывной жидкости; V — газ на продувку; VI — инертный газ; / — барабан; 2 — корыто; 3 — привод барабана; 4 — крышка; 5 — коллектор промывной жидкости; 6 — отводная трубка; 7 — распределительная головка; 8 — сменный диск распределительной головки; 9 — продольная перегородка; 10 — нож для удаления осадка; 11 — шнек для выгрузки осадка; 12 — продольная перегородка.
Барабанные вакуум-фильтры широко применяют на установках депарафинизации масел. Основу фильтра (рис. XVIII-11) составляет горизонтальный барабан 1 диаметром до 3 м и длиной свыше 5 м, который вращается на двух цапфах со скоростью около 0,5 об/мин.
На боковой поверхности барабана крепятся металлическая сетка, и фильтровальная ткань, обмотанная по спирали проволокой. Изнутри фильтрующая перегородка разделена по образующим продольными перегородками 12 на отдельные секции (12 и более), каждая из которых отводными трубками 6 соединена с диском 9, укрепленным на цапфе. К диску прижата пружинами неподвижная распределительная головка, которая разделена на три камеры, соответствующие отдельным стадиям фильтрации, промывки и продувки. Нижняя часть барабана погружена в суспензию, которая подается в корыто 2 (см. рис. XVIII-11). Центральный угол, соответствующий погруженной в суспензию фильтрующей поверхности барабана, равен 120—140р. Над барабаном установлен трубный коллектор 5 для подачи промывной жидкости. Сбоку размещены нож 10 для срезания осадка и шнек 11 для удаления осадка из фильтра.
|
|
Барабанный вакуум-фильтр работает следующим образом. Каждая секция барабана при его вращении погружается в суспензию.
Под влиянием разности давлений в корпусе фильтра и внутри секции происходит фильтрация. Пока данная секция погружена в суспензию и идет процесс фильтрации. По мере поворота секции вместе с барабаном по часовой стрелке на поверхности секции образуется слой осадка. Фильтрат через штуцер в распределительной головке выводится в сборник фильтрата, осадок сушится потоком инертного газа. Разбрызгиваемая из коллектора промывная жидкость проходит через осадок, вытесняя находящийся там фильтрат. Затем осадок вновь просушивается проходящим через осадок потоком инертного газа. Секция соединяется с третьим окном, через которое газодувкой в секцию подается инертный газ под избыточным давлением примерно 5 кПа. Осадок отделяется от поверхности барабана и затем снимается ножом. После этого для данной секции вновь начинается процесс фильтрации.
|
|
Ленточный фильтр (рис. 12) состоит из рамы, приводного и натяжного барабанов, между которыми натянута бесконечная перфорированная резиновая лента. Под ней расположены вакуум-камеры, соединенные в нижней части с коллекторами для отвода фильтрата и промывной жидкости. За счет вакуума лента прижимается к верхней части вакуум-камер. К резиновой ленте натяжными роликами 7 прижимается фильтровальная ткань, выполненная также в виде бесконечной ленты.
Суспензия подается на фильтровальную ткань из лотка 5. Фильтрат под вакуумом отсасывается в камеры и отводится через коллектор в сборник. Промывная жидкость подается через форсунки 2 на образовавшийся осадок и отсасывается в камеры, из которых через коллектор 9 отводится в сборник.
На приводном барабане фильтрующая ткань отделяется от резиновой ленты и огибает направляющий ролик. При этом осадок соскальзывает с фильтровальной ткани и падает в сборник осадка.
|
|
Рис. 12 Ленточный вакуум-фильтр:
1 - приводной барабан; 2 – форсунка; 3 - вакуум-камера; 4 - резиновая лента; 5 – лоток; 6 - натяжной барабан; 7 - натяжные ролики; 8 - коллектор для отвода фильтра; 9 - коллектор для отвода промывной жидкости; 10 - сборник осадка; 11 - фильтровальная ткань
При прохождении фильтровальной ткани между роликами 7 она промывается, просушивается и очищается.
Фильтры периодического действия. Плиточно-рамные (ФПР) и плиточно-камерные (ФПК) ф и л ь т р-п r е с с ы (рис. 5 и 6) предназначены для разделения средне- и труднофильтрующихся суспензий из водных и др. невзрывоопасных, инертных и агрессивных сред. Несмотря на негерметичность и невозможность поддержания постоянной рабочей температуры, эти фильтры распространены в промышленности вследствие развитой фильтрующей пов-сти, относительно низкой металлоемкости, возможности получения хорошо отмытых и отжатых осадков.
Общей особенностью фильтр-прессов всех конструкций является пакет фильтровальных элементов - плит (ФПК) или чередующихся плит и рам (ФПР), зажимаемый между неподвижной опорной и подвижной нажимной массивными жесткими плитами. Фильтровальные элементы опираются спец. кронштейнами на балки-стяжки. Плиты ФПК имеют круглую, квадратную или прямоугольную форму, плиты FПP - только квадратную либо прямоугольную. Все плиты снабжены рифлениями для стока фильтра и углублениями для накопления осадка, а для подачи и удаления осадка суспензии - сквозными отверстиями. Последние при сборке плит (рам) в пакет образуют каналы для подачи суспензии, промывной жидкости, сжатого газа и отвода фильтратов. На неподвижной плите имеются соответствующие этим каналам отверстия и штуцеры для присоединения трубопроводов. Между плитами (рамами) располагаются полотна ФП, в которых также находятся подобные отверстия.
Суспензия по каналу подается под давлением в камеры или рамы до заполнения этого пространства осадком, который при необходимости промывают, подавая промывную жидкость через ткань или по каналу, через который движется суспензия (во MH. горизонтальных фильтрах). Осадок обезвоживают продувкой сжатым газом или отжимом (эластичными диафрагмами из резины либо полипропилена) под давлением до 1,5 МПа, Выгрузка осадка производится гравитационно (иногда с вибропобуждением) либо при перемещении бесконечной фильтровальной ленты и перегибе ее на роликах с подчисткой ножом. Фильтровальную ткань регенерируют активаторами в заполненной жидкостью камере либо перемещением вдоль фильтра распылит. устройства, вода в форсунки которого поступает под давлением до 10 МПа. Большинство фильтр-прессов работает автоматически.
I-суспензия, II-промывная жидкость, III-фильтрат, IV-промывной фильтрат, V-сжатый газ, VI-осадок
Емкостные фильтры, работающие под давлением, наз. друк-фильтрами, под вакуумом - нутч-фильтрами. Друк-фильтры (рис. 7) - вертикальные сосуды (обычно с рубашкой) с эллиптич. днищем, верх, пространство над которым служит для приема суспензии, нижнее - для фильтрата. На ложном днище и ниж. части корпуса крепится ФП. При Ф. в заполненный суспензией корпус подают сжатый газ. Полученный осадок промывают, просушивают и выгружают с помощью мешалки через люк в боковой пов-сти или в центре ложного днища. В ряде конструкций осадок удаляют после опускания ложного днища перемещением ленты фильтровальной ткани, которая по окончании выгрузки осадка проходит через камеру регенерации. Известны друк-фильтры, кор пус которых может поворачиваться на 90-180° в закрепленных на его цилиндрич. части цапфах. На друк-фильтрах разделяют средне- и хорошо-фильтрующиеся суспензии в средне- и малотоннажных про-из-вах; в последнем случае в одном аппарате последовательно проводят хим. реакцию с получением суспензии, Ф., промывку и сушку осадка. Требования к концентрации суспензии и скорости осаждения твердой фазы ограничиваются возможностями транспортирования ее по вертикальным трубопроводам. Герметичность и возможность изготовления фильтров из любых конструкционных материалов распространяет область применения друк-фильтров на пожаро- и взрывоопасные, кристаллизующиеся и токсичные среды.
Нутч-фильтры используются для разделения хорошо фильтрующихся, нетоксичных и невзрывоопасных суспензий в малотоннажных произ-вах. Эти фильтры - открытые сосуды круглого или прямоугольного сечения с ложным днищем, служащим опорой для ФП. Ниж. пространство соединяется с вакуум-ресивером и сборником фильтрата. Осадок выгружается с помощью мешалки вручную при опрокидывании корпуса или передвижной тканью.
Нутч-фильтр (рис. XVIII-9) является простейшим аппаратом для фильтрации суспензий под вакуумом. Изготавливается в виде цилиндрического сосуда / с нижним днищем 2. На некотором расстоянии от днища установлена плоская фильтрующая перегородка 3, на которой закреплена дренажная сетка 4 и ткань 5. Пространство под перегородкой сообщается с вакуумным насосом через штуцер 6.
Уровень суспензии Нх над фильтрующей перегородкой поддерживается переливным штуцером 7.
Рис. XVIII -9. Нутч-фильтр:
1 — корпус; 2 — днище; 3 — фильтрующая перегородка; 4 — дренажная сетка; 5 — ткань; 6 — штуцер вывода фильтрата; 7 — переливной штуцер.
Осадок откладывается на фильтре, а фильтрат и выделившиеся из суспензии в вакууме газы и воздух отсасываются вакуум-насосом. По окончании процесса фильтрации, когда слой осадка достигает предельной толщины, прекращают подачу суспензии, остаток суспензии отфильтровывают. Промывную жидкость подают из другого приемника, как и фильтруемую суспензию. Промывную жидкость направляют в специальный вакуумный сборник. Затем осадок разгружают. Режим фильтрации при ΔР = const
Фильтры под давлением. Наиболее широкое применение имеют фильтр-прессы и пластинчатые фильтры.
Рамный фильтр-пресс (рис. XVIII-13) представляет собой набор плит или рам 2 квадратной или круглой формы, которые опираются на балки 3 и сжимаются специальным приспособлением 5 через нажимную плиту 4. Плиты фильтра имеют с обеих сторон рифленую поверхность, на которую укладывают фильтровальную ткань. В собранном виде между двумя соседними плитами образуются камеры, в которых накапливается осадок
Рис. XVIII-13. Рамный фильтр-пресс:
/ — плита; 2 — рама; 3 — балка; 4 — нажимная плита; 5 — зажимное устройство, 6,9 — опоры; 7 — тяги; 8 — стойка; 10 — винт.
.
В плитах, рамах и листах фильтровальной ткани имеются отверстия, которые при сборке фильтра образуют каналы для подачи суспензии и промывной жидкости, а также для вывода фильтрата и промывного раствора (рис. XVIII-14).
При фильтрации (рис. XVIII-14, а) суспензия подается параллельно во все рамы и по каналам в них вытекает в пространство между плитами. Через ткань, уложенную на плитах, проходит фильтрат, который затем стекает по рифленой поверхности плит к выводному каналу и выводится из фильтра.
Рис. XVIII-14. Схема движения потоков в рамном фильтр-прессе:
а — при фильтрации; б — при промывке осадка; / — суспензия; // — фильтрат; /// — промывная жидкость; IV — промывной раствор; V — осадок; 1 — плита; 2 — рама; 3 — фильтровальная ткань.
Осадок отлагается на фильтровальной ткани. Максимальная толщина слоя осадка равна половине толщины рамы. Если промывку ведут через тот же канал, что и подачу суспензии, то толщину осадка необходимо контролировать (например, по величине перепада давления), чтобы не произошла полная забивка фильтра осадком. В противном случае для промывки используют специальные каналы в плитах, через которые промывная жидкость поступает под фильтровальную ткань и выводите из фильтра через коллектор (рис. XVIII-14, б).
Для снятия осадка превращают действие нажимного устройства, плиты и рамы раздвигают, рамы вынимают и разгружают осадок. Обычно рамные фильтр-прессы работают при давлении 0,3—0,4 МПа.
Рамный фильтр-пресс (рис. 4) используется для осветления виноматериалов, вина, молока и пива. Фильтрующий блок состоит из чередующихся рам и плит с зажатой между ними фильтровальной тканью или картоном. Рамы и плиты зажимаются в направляющих 6 зажимным винтом 7. Фильтр монтируют на металлической станине.
Рис.4 Рамный фильтр-пресс:
1 - опорная плита; 2 – рама; 3 – плита; 4 - фильтровальная перегородка; 5 - подвижная плита; 6 - горизонтальная направляющая; 7 – винт; 8 – станина; 9 -желоб
Каждая рама и плита (рис. 5) имеют каналы для ввода суспензии и промывной жидкости. На поверхности плит с обеих сторон расположены сборные каналы 4, ограниченные сверху дренажными каналами, а снизу отводным каналом.
Рис. 5 Рама (а) и плита (б) фильтр-пресса:
1,2 - каналы для ввода суспензии и промывной жидкости; 3 - жренажный канал; 4 - сборный канал; 5 - отводной канал
При фильтровании (рис. 6 а) суспензия под давлением подается через каналы в рамах и плитах и распределяется по всем рамам. Фильтрат стекает по дренажным и сборным каналам в плитах и удаляется через отводные каналы. При промывке осадка (рис. 6 б) промывная жидкость под давлением вводится через соответствующие каналы, распределяется по рамам и проходит обратным током через фильтровальную перегородку, промывает осадок, а затем удаляется из фильтра через отводные каналы. При промывке отводные каналы всех нечетных плит блока должны быть закрыты.
Основной недостаток рамных фильтр-прессов — трудоемкость выгрузки осадка и замены фильтровальной перегородки. Для выгрузки осадка необходимы разборка вручную фильтровального блока и промывка плит и рам.
Рис. 6 Схема работы фильтр-пресса:
а – фильтрование; б - промывка осадка; 1 – рама; 2 - плита
Дисковые фильтры с инерционной выгрузкой осадка (рис. 9) предназначены для осветительного фильтрования с намывным слоем ФВВ и разделения малоконцентрир. суспензий, в т.ч. токсичных, агрессивных, пожароопасных (vос < 10 мм/с). В вертикальном цилиндрич.-конич. корпусе на полом валу насажены диски (тарелки) с конич. уклоном для отвода фильтрата через вал. На верх. пов-сть крепятся дренажная решетка и ФП (сетка, ткань). Промывка осадка проводится после слива суспензии подачей жидкости на верх. тарелку и далее переливом на последующие. Промытый осадок выгружают в заполненный суспензией или пустой корпус.
Дисково-пакетные фильтры применяют только для осветительного фильтрования малоконцентрир. суспензий через картон, бумагу, нетканые материалы, картон с нанесенным слоем ФВВ из достаточно вязких горючих и агрессивных сред. В вертикальном цилиндрич. корпусе монтируется пакет дисков, стянутых по периферии шпильками и герметизируемых по наружной кольцевой пов-сти дисков и внутр. втулок; верх, пов-сть - фильтрующая. Суспензия подводится через отверстия в наружных пов-стях дисков, фильтрат отводится с дренажной пов-сти через отверстия во втулках. Последние в сборе образуют канал для отвода фильтрата. Осадок удаляют после извлечения и разборки пакета дисков.
Дисковые фильтры (рис. 11) применяют для разделения тонкодисперсных суспензий; они работают под давлением с намывным слоем вспомогательного вещества. Дисковый фильтр представляет собой вертикальную емкость с обогреваемой рубашкой. Внутри фильтра на полый вал 6 насажены дисковые металлические перфорированные фильтровальные элементы 7. На диски натягивают полипропиленовую или другую фильтровальную ткань, закрепляемую хомутами. Рабочее давление в фильтре достигает 0,5 МПа, в рубашке — 0,3 МПа.
В дисковых фильтрах предусмотрен центробежный сброс подсушенного осадка. Полый вал вместе с фильтровальными дисками приводится во вращение электро- и гидродвигателем. Частота вращения вала достигает 250 мин-1. Вал имеет сальниковые тефлоновые уплотнения.
Рис. 11 Дисковый фильтр:
1 – шкив; 2 - сальниковое уплотнение; 3 – крышка; 4 - корпус фильтра; 5 – рубашка; 6 – вал; 7 - фильтровальный элемент; 8 - подпятник
Перед фильтрованием на фильтровальные элементы намывают слой вспомогательного вещества, суспензия которого готовится в суспензаторе. Готовая суспензия прокачивается насосом через фильтровальные элементы до образования намывного слоя толщиной 15...30 мм. Фильтрат из дисков через отверстия в полом валу поступает внутрь вала и выводится из фильтра в суспензатор. Аналогичным образом проводится фильтрование суспензии. После окончания фильтрования осадок промывается обратным током фильтрата и подсушивается воздухом.
Патронные фильтры (рис. 8) служат для фильтрования и сгущения малоконцентрир. суспензий, в т.ч. из токсичных, пожаро- и взрывоопасных, а также агрессивных сред. Из-за неравномерности распределения осадка по высоте фильтровальных элементов скорость осаждения твердой фазы не должна превышать 2-5 мм/с; возможность промывки осадка ограничена. Данные фильтры представляют собой вертикальные цилиндрич. сосуды (иногда с паровой рубашкой) с откидывающейся либо съемной крышкой, конич. (иногда с побудителем выгрузки осадка в виде мешалки или вибратора) либо эллиптич. (для фильтров с малой пов-стью фильтрования) днищем. Внутри корпуса располагаются цилиндрич. фильтрующие элементы (патроны), прикрепленные к коллекторам в верх. или ниж. части (свечевые фильтры) либо на решетке, разделяющей корпус на две половины (верхняя для фильтрата, нижняя для суспензии).
Патроны: 1) дренажные основания - пружины или перфорир. трубы круглого либо звездчатого сечения, снаружи с фильтровальной рукавной тканью, плотно навитой проволокой, нитью (бобина) или набором шайб; 2) пористые трубы из керамики, металлокерамики, пластмасс, прессованных волокнистых отходов с полимеризующейся пропиткой; 3) складчатые элементы из картона, полимерных мембран, сеток.
Суспензия подается в корпус фильтра под давлением, а образовавшийся осадок толщиной до 10-15 мм сбрасывается обратным током фильтрата или его смеси с газом и оседает в конич. части аппарата, после чего цикл повторяется до заполнения конуса. Выгрузка осадка м. б. мокрой (суспензию просто сливают) или сухой (после фильтрования в корпус подают сжатый газ, выдавливают суспензию, а затем сбрасывают и выгружают осадок). Конструкция позволяет возвращать мутный фильтрат и намывать слой ФВВ.
Листовые фильтры бывают вертикальные и горизонтальные. Фильтрующий элемент - лист-рама прямоугольной или круглой (только для горизонтальных фильтров) формы из труб либо проката с вкладышем; последний выполнен из гофрир. или перфорир. листа либо полимерных (деревянных) решеток, на которые натягивается сетка или фильтровальная ткань. Осадок снимают гидросмывом либо вибрацией; сброс - вибрацией, ножами при вращении пакета листов, отдувкой воздухом, гидросмывом или обратным током фильтрата; выгрузка - скребками, шнеками и др. По области применения эти фильтры близки к патронным фильтрам.
Дата добавления: 2019-07-15; просмотров: 562; Мы поможем в написании вашей работы! |
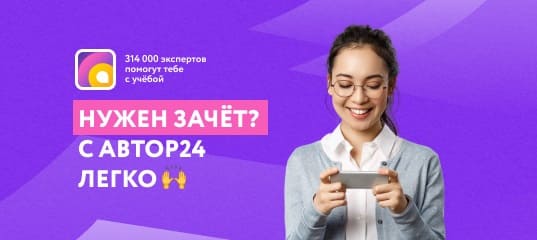
Мы поможем в написании ваших работ!