ТЕОРЕТИЧЕСКИЕ ОСНОВЫ ФИЛЬТРОВАНИЯ
Г. ФИЛЬТРОВАНИЕ
Виды фильтрующих перегородок и осадков
Теоретические основы фильтрования
Режимы ф ильтрования
Аппаратура для фильтрования
Расчет фильтровального оборудования
Фильтрованием называется процесс разделения суспензий и аэрозолей с использованием пористых перегородок, на поверхности которых задерживаются взвешенные в жидкости или газе твердые частицы, образующие на перегородке слой осадка. Жидкость, отделенная от осадка, называется фильтратом.
В нефтеперерабатывающей и нефтехимической промышленности фильтрование применяется в процессах депарафинизации масел, производства парафина, церезина, пластичных смазок, при очистке нефтепродуктов и контактной очистке масел, для улавливания технического углерода, отделения химических реактивов и особо чистых химических веществ и других ценных продуктов от газов, отходящих от технологических установок распиливающего типа и печей кипящего слоя. Движение жидкости через пористые перегородки и слой осадка создают за счет разности давления в аппарате, являющейся движущей силой процесса.
Перепад давления может создаваться: 1) столбом жидкости над фильтрующей перегородкой (гидростатическое фильтрование); 2) избыточным давлением жидкости, например, при подаче ее насосом (фильтрование под давлением); 3) путем создания разрежения под фильтрующей перегородкой при помощи вакуум-насоса (фильтрование под вакуумом), фильтрующие центрифуги.
|
|
На рисунке 1 даны принципиальные схемы фильтров.
Рис. 1 Принципиальные схемы фильтров по способу создания движущей силы: а — гидростатический; б — под давлением; в — вакуумный; г — центробежный; 1 — суспензия; 2 — осадок; 3 — фильтровальная перегородка; 4 — фильтрат.
Разделение суспензий на фильтрах обычно состоит не только из основной операции по фильтрованию суспензий, но в ряде случаев и из вспомогательных операций, таких как промывка осадка (при которой с помощью специальной жидкости фильтрат выдавливается из пор осадка), его продувка и сушка воздухом или инертным газом.
Эффективность разделения и производительность фильтра зависят от свойств обрабатываемой суспензии, правильного выбора типа фильтра,- его оснащения и режима работы.
ВИДЫ ФИЛЬТРУЮЩИХ ПЕРЕГОРОДОК И ОСАДКОВ
Для фильтрования применяются следующие виды перегородок:
насыпные, состоящие из слоя мелкозернистых материалов (гравий, песок и др.), обладающие высокой полнотой разделения суспензий, но отличающиеся большим сопротивлением, поскольку осадок проникает внутрь фильтрующего слоя и требуются специальные приемы для его отделения. Такие фильтровальные перегородки применяют для суспензий с малой концентрацией осадка;
|
|
набивные, состоящие из слоя волокнистых материалов (вата хлопчатобумажная, шерстяная, шлаковая, стеклянная, асбестовое волокно и т.д.); характеристика та же, что и для насыпных перегородок;
керамические , состоящие из плоских пористых кислотоупорных плиток, применяющиеся для фильтрования кислых сред; характеристика та же, что и для насыпных перегородок;
тканевые, обладающие относительно малым сопротивлением и удобные в конструктивном отношении;
плетеные, представляющие собой сетки из тонкой проволоки, выполненные из цветных металлов и сплавов; отличаются пониженной задерживающей способностью и поэтому в начале фильтрования пропускают в фильтрат мелкие частицы. Однако осадок, который откладывается в последующем, обеспечивает высокую фильтровальную способность. Плетеные перегородки часто применяют для фильтрования при повышенной температуре, причем первые порции мутного фильтрата возвращаются на повторное фильтрование.
В ряде случаев фильтровальная перегородка не обладает достаточной задерживающей способностью и для придания ей необходимых фильтрующих свойств на ее поверхность намывают слой вспомогательного фильтрующего вещества (кизельгура, диатомита, перлита и т.п.). Слой осадка из вспомогательного вещества служит фильтровальной перегородкой, которая и задерживает мелкие частицы суспензии (менее 1 мкм).
|
|
Важной характеристикой осадка является его пористость, влияющая на проницаемость жидкости и обусловливающая величину сопротивления, оказываемого потоку фильтрата. Осадок, который при фильтровании независимо от давления имеет одну и ту же пористость, называется несжимаемым и состоит обычно из твердых кристаллических частиц, размеры которых варьируются в широком интервале.
Большая часть осадков состоит из мягких частиц, которые с повышением давления уплотняются, вследствие чего их проницаемость уменьшается. Такие осадки называются сжимаемыми.
Существуют суспензии, содержащие очень мелкие илистые частицы, которые при прохождении через фильтрующую перегородку образуют на ней непроницаемый для жидкости осадок. Чтобы сделать возможным фильтрование для таких суспензий, в них добавляют мелкие частицы другого материала (например, песок, кварц и др.), которые придают осадку жесткую пространственную структуру с мелкими порами, и в этом случае осадок становится проницаемым. Осадки, структура которых различна в отдельных частях их объема, называются неоднородными.
|
|
ТЕОРЕТИЧЕСКИЕ ОСНОВЫ ФИЛЬТРОВАНИЯ
Рис. 2. Схема процесса фильтрования: 1 – фильтр; 2 - фильтровальная перегородка; 3 – суспензия; 4 – фильтрат; 5 – осадок.
Движение жидкости (фильтрата) через каналы неправильной формы, образующиеся между частицами осадка и элементами фильтрующей перегородки, подчиняется общим закономерностям гидравлики и, как отмечалось ранее, связано с преодолением сопротивления как слоя осадка, так и фильтровальной перегородки (рис. 2). В связи с малыми размерами каналов и небольшой скоростью движения жидкости процесс фильтрования обычно протекает в ламинарном режиме и перепад давления линейно зависит от вязкости среды. Одним из основных показателей процесса является скорость фильтрования С, определяемая как объем фильтрата dV, проходящий через поверхность фильтра F за промежуток времени dτ, т.е. С= dV / F * dτ
Скорость фильтрования пропорциональна перепаду давления Δр в слое осадка и фильтрующей перегородке и обратно пропорциональна их сопротивлению R, т.е. С= dV / F * dτ = Δр/ R (2)
где перепад давления Δр измеряется в Па, а сопротивление R — в (Па.с)/м.
Сопротивление R — величина переменная, так как фильтрование идет с постоянным увеличением высоты слоя осадка, а следовательно, и его сопротивления. В уравнении (2) общее сопротивление R целесообразно представить в виде суммы меняющегося сопротивления осадка Rос и практически постоянного сопротивления фильтрующей перегородки Rф:
R = Rос + Rф.
В свою очередь Rос пропорционально толщине осадка h, т.е.
Roc = r·h.
Обозначим отношение объема образующегося осадка к объему фильтрата через х = Vос/V; тогда для любого момента фильтрования получим
Vос = V ·х
В то же время из геометрии следует, что Vос= Fh, откуда
Fh = V ·х; h = V ·х/F
После подстановки полученного в уравнение (2) основное дифференциальное уравнение фильтрования принимает вид
С= dV / F * dτ =Δр/(Rос + Rф)= Δр/ (r ·V ·х/F +Rф ) (3)
Удельное сопротивление r = Rос/h измеряется в (Па * с)/м2.
РЕЖИМЫ ФИЛЬТРОВАНИЯ
В промышленной практике наибольшее распространение получили два режима фильтрования - режим при постоянном перепаде давления и режим при постоянной скорости.
Режим при постоянном перепаде давления Δр – это вакуумное фильтрование, гидростатическое фильтрование с постоянным столбом жидкости над фильтрующей перегородкой, подача суспензии центробежным насосом при постоянном избыточном давлении на выкиде насоса. При этом режиме скорость фильтрования в связи с постоянным увеличением высоты слоя осадка и ростом его сопротивления с течением времени уменьшается.
При ΔP = const и неизменной температуре для фильтра данной конструкции и выбранной фильтровальной перегородки все входящие в уравнение (3) величины, за исключением V и τ, постоянны. Проинтегрировав это уравнение получим:
(4)
Из уравнения (4) следует, что при ΔP=const, по мере протекания процесса, а следовательно, увеличения объёма фильтрата, скорость фильтрования уменьшается. Такое фильтрование называется нестационарным.
Режим при постоянной скорости С – это подача суспензии на фильтр поршневым или плунжерным насосом постоянной производительности). При режиме с постоянной скоростью фильтрования слой осадка и его сопротивление постоянно увеличиваются, вследствие чего должно непрерывно расти давление поступающей суспензии, а следовательно, и перепад давления Δр.
Для получения уравнения процесса для данного случая производную уравнения (31) dV/dτ заменяем равным отношением конечных величин V/τ и принимаем во внимание, что скорость фильтрования С= V / F * τ постоянная. При этом умножив и разделив первое слагаемое правой части этого уравнения на τ, получим уравнение фильтрования при постоянной скорости процесса, решая его относительно ΔР получим:
Δр= r * х* С2* τ + R ф (5)
Уравнение (5) показывает, что при С=const разность давлений возрастает по мере увеличения продолжительности фильтрования. Такое фильтрование называется стационарным.
АППАРАТУРА ДЛЯ ФИЛЬТРОВАНИЯ
По принципу действия фильтровальное оборудование делится на оборудование, работающее при постоянном перепаде давления либо при постоянной скорости фильтрования; по способу создания перепада давления на фильтровальной перегородке — на работающее под вакуумом либо под избыточным давлением; в зависимости от организации процесса — на оборудование непрерывного и периодического действия.
Избыточное давление может создаваться силами давления или центробежной силой. В зависимости от способа создания перепада давления фильтровальное оборудование может быть разделено на фильтры и центрифуги.
Фильтры, используемые для разделения суспензии, работают как под вакуумом, так и под избыточным давлением, периодически и непрерывно. К фильтрам, работающим под давлением, предъявляют повышенные требования к механической прочности. Их изготовляют по нормам Госгоркотлонадзора для сосудов, работающих под давлением.
В фильтрах периодического действия осадок удаляется после прекращения процесса фильтрования, в фильтрах непрерывного действия — по мере необходимости без остановки процесса.
При разработке новых видов фильтровального оборудования следует ориентироваться на создание компактных аппаратов с развитой фильтровальной поверхностью, позволяющих проводить ее регенерацию без остановки технологического процесса.
Нутч-фильтр (рис. 3), работающий как под вакуумом, так и под избыточным давлением, широко распространен в малотоннажных производствах. Выгрузка из него осадка механизирована. Для сброса осадка фильтр снабжен перемешивающим устройством в виде однолопастной мешалки. Для удаления осадка из фильтра на цилиндрической части корпуса предусмотрен люк.
Рис.3 Нутч-фильтр с перемешивающим устройством:
1-привод, 2-корпус фильтра, 3-мешалка, 4- спускной кран, 5-фильтровальная перегородка, 6- фильтровальная ткань
Суспензия и сжатый воздух подаются через раздельные штуцера, фильтрат удаляется через спускной кран 4. Фильтр снабжен предохранительным клапаном.
Цикл работы фильтра состоит из заполнения его суспензией, фильтрования суспензии под давлением, удаления осадка с фильтровальной перегородки при вращающейся мешалке и регенерации фильтровальной перегородки. В таких фильтрах может проводиться одновременно промывка осадка.
Для фильтрования суспензии применяют фильтровальные перегородки из картона, бельтинга и синтетических волокон. Преимуществами фильтровальных перегородок из синтетических волокон являются высокая механическая прочность, термическая и химическая стойкость.
Из синтетических волокон изготовляют фильтровальные перегородки с постепенно изменяющейся плотностью, что обеспечивает глубинное фильтрование суспензий, содержащих малое количество твердой фазы. Меняющаяся по глубине плотность фильтровального материала позволяет захватывать частицы по всей глубине фильтра. При этом крупные частицы задерживаются в наружных, а мелкие — в глубинных слоях фильтра. Селективное фильтрование обеспечивает высокую скорость фильтруемой среды, предотвращает закупоривание поверхностных пор и продлевает срок службы фильтров.
Рамный фильтр-пресс (рис. 4) используется для осветления виноматериалов, вина, молока и пива. Фильтрующий блок состоит из чередующихся рам и плит с зажатой между ними фильтровальной тканью или картоном. Рамы и плиты зажимаются в направляющих 6 зажимным винтом 7. Фильтр монтируют на металлической станине.
Рис.4 Рамный фильтр-пресс:
1 - опорная плита; 2 – рама; 3 – плита; 4 - фильтровальная перегородка; 5 - подвижная плита; 6 - горизонтальная направляющая; 7 – винт; 8 – станина; 9 -желоб
Каждая рама и плита (рис. 5) имеют каналы для ввода суспензии и промывной жидкости. На поверхности плит с обеих сторон расположены сборные каналы 4, ограниченные сверху дренажными каналами, а снизу отводным каналом.
Рис. 5 Рама (а) и плита (б) фильтр-пресса:
1,2 - каналы для ввода суспензии и промывной жидкости; 3 - жренажный канал; 4 - сборный канал; 5 - отводной канал
При фильтровании (рис. 6 а) суспензия под давлением подается через каналы в рамах и плитах и распределяется по всем рамам. Фильтрат стекает по дренажным и сборным каналам в плитах и удаляется через отводные каналы. При промывке осадка (рис. 6 б) промывная жидкость под давлением вводится через соответствующие каналы, распределяется по рамам и проходит обратным током через фильтровальную перегородку, промывает осадок, а затем удаляется из фильтра через отводные каналы. При промывке отводные каналы всех нечетных плит блока должны быть закрыты.
Основной недостаток рамных фильтр-прессов — трудоемкость выгрузки осадка и замены фильтровальной перегородки. Для выгрузки осадка необходимы разборка вручную фильтровального блока и промывка плит и рам.
Рис. 6 Схема работы фильтр-пресса:
а – фильтрование; б - промывка осадка; 1 – рама; 2 - плита
Фильтр-пресс автоматизированный камерный с механизированной выгрузкой осадка (ФПАКМ) используют для разделения тонкодисперсных суспензий концентрацией 10...500 кг/м3 при температурах до 80 °С. Является фильтром периодического действия. Он состоит из ряда прямоугольных фильтров (рис. 7), расположенных вплотную один под другим, благодаря чему возрастает удельная площадь поверхности фильтрования по отношению к площади, занимаемой фильтром.
Рис. 7 Фильтр-пресс с горизонтальными камерами (ФПАКМ):
1 - нижняя плита; 2 - верхняя плита; 3 - пространство для суспензии и осадка; 4 - перфорированный лист; 5 - пространство для фильтрата; 6 - эластичная диафрагма; 7, 9, 12 - каналы; 8 - коллектор для суспензии; 10 - коллектор для отвода фильтрата; 11 - пространство для воды; 13 - фильтровальная ткань
В положении А в камеру из коллектора 8 последовательно поступают суспензия на разделение, жидкость для промывки и сжатый воздух для подсушки осадка. Фильтрат, промывная жидкость и воздух отводятся по каналам 12 в коллектор 10. В пространстве 11 по каналам 9 подается вода под давлением, которая с помощью водонепроницаемой диафрагмы 6 отжимает осадок (положение Б). Затем плиты раздвигаются и осадок удаляется из фильтра через образовавшиеся щели (положение В).
Барабанные вакуум-фильтры применяют при непрерывном разделении суспензий концентрацией 50...500 кг/м3. Твердые частицы могут иметь кристаллическую, волокнистую, аморфную, коллоидальную структуру. Производительность фильтра зависит от структуры твердых частиц и снижается в указанной выше последовательности.
Барабанные вакуум-фильтры (рис. 8) выпускают с внешней и внутренней фильтрующей поверхностью, которая обтягивается текстильной фильтровальной тканью. Вращающийся горизонтальный перфорированный барабан разделен перегородками на несколько секций одинаковой формы, которые за оборот барабана проходят несколько рабочих зон: фильтрования, обезвоживания, промывки, удаления осадка и регенерации фильтровальной ткани. Устройством, управляющим работой фильтра, является распределительная головка, через которую секции барабана в определенной последовательности подсоединяют к магистралям вакуума, сжатого воздуха и промывной жидкости.
Рис. 8 Барабанный вакуум-фильтр с распределительной головкой:
1 - перфорированный барабан; 2 - фильтровальная ткань; 3 - ножевое устройство; 4 – секция; 5 – корыто; 6 – мешалка; 7 – труба; 8 – разбрызгиватель; 9 - распределительная головка
В стадии фильтрования зона фильтра под фильтрующей тканью соединяется с вакуумом и фильтрат, находящийся в корыте, проходит через фильтровальную ткань. Осадок откладывается на ее поверхности. Промытый и подсушенный осадок непрерывно срезается ножом. Чтобы взвешенные частицы не отстаивались, корыто снабжено качающейся мешалкой.
Для извлечения пива и дрожжей из дрожжевой суспензии, образующейся при седиментации в бродильных чанах и танках, применяют барабанный вакуум-фильтр, изображенный на рис. 9. Фильтровальный элемент состоит из крупноячеистой сетки, на которую накладывается мелкоячеистая сетка. Для улучшения условий фильтрования на мелкоячеистую сетку намывается слой вспомогательного материала — кизельгура либо картофельного крахмала. Пивная или дрожжевая суспензия, подаваемая из бака, при вращении барабана равномерно распределяется по фильтровальной поверхности, а дрожжевой осадок (лепешка) срезается ножом, установленным над баком.
Рис. 9 Барабанный вакуум-фильтр:
1 - насос для фильтрата; 2 - вакуум-насос; 3 – пеногаситель; 4 - фильтровальный элемент; 5 – барабан; 6 - труба для фильтрата
Содержание сухих веществ в дрожжевой лепешке достигает 25...28 %. Обрызгивание подсыхающей лепешки водой способствует увеличению выхода пива примерно на 20 %.
Детали фильтра, находящиеся в контакте с фильтрующей средой, выполнены из нержавеющей стали. Все детали фильтра легко очищаются.
Схема фильтровальной установки с барабанным вакуум-фильтром показана на рис. 10. Суспензия подается в корыто фильтра, где установлена качающаяся мешалка, препятствующая сепарации крупных твердых частиц большой плотности. При погружении 30 % поверхности барабана в суспензию он подключается к вакуум-насосу. Фильтрат и промывная жидкость собираются в сборниках 3, где от них отделяется воздух, поступивший в фильтр во время обезвоживания и промывки осадка, и затем откачиваются насосами.
Дисковые фильтры (рис. 11) применяют для разделения тонкодисперсных суспензий; они работают под давлением с намывным слоем вспомогательного вещества. Дисковый фильтр представляет собой вертикальную емкость с обогреваемой рубашкой. Внутри фильтра на полый вал 6 насажены дисковые металлические перфорированные фильтровальные элементы 7. На диски натягивают полипропиленовую или другую фильтровальную ткань, закрепляемую хомутами. Рабочее давление в фильтре достигает 0,5 МПа, в рубашке — 0,3 МПа.
Рис.10 Схема фильтровальной установки:
1 - барабанный вакуум-фильтр; 2 - приемник осадка; 3 - сборники фильтрата и промывной жидкости; 4 – воздуходувка; 5 - вакуум-насос; 6 - насосы для отбора фильтрата и промывной жидкости; 7 - насос для суспензии; 8- ёмкость для суспензии
В дисковых фильтрах предусмотрен центробежный сброс подсушенного осадка. Полый вал вместе с фильтровальными дисками приводится во вращение электро- и гидродвигателем. Частота вращения вала достигает 250 мин-1. Вал имеет сальниковые тефлоновые уплотнения.
Рис. 11 Дисковый фильтр:
1 – шкив; 2 - сальниковое уплотнение; 3 – крышка; 4 - корпус фильтра; 5 – рубашка; 6 – вал; 7 - фильтровальный элемент; 8 - подпятник
Перед фильтрованием на фильтровальные элементы намывают слой вспомогательного вещества, суспензия которого готовится в суспензаторе. Готовая суспензия прокачивается насосом через фильтровальные элементы до образования намывного слоя толщиной 15...30 мм. Фильтрат из дисков через отверстия в полом валу поступает внутрь вала и выводится из фильтра в суспензатор. Аналогичным образом проводится фильтрование суспензии. После окончания фильтрования осадок промывается обратным током фильтрата и подсушивается воздухом.
Ленточный фильтр (рис. 12) состоит из рамы, приводного и натяжного барабанов, между которыми натянута бесконечная перфорированная резиновая лента. Под ней расположены вакуум-камеры, соединенные в нижней части с коллекторами для отвода фильтрата и промывной жидкости. За счет вакуума лента прижимается к верхней части вакуум-камер. К резиновой ленте натяжными роликами 7 прижимается фильтровальная ткань, выполненная также в виде бесконечной ленты.
Суспензия подается на фильтровальную ткань из лотка 5. Фильтрат под вакуумом отсасывается в камеры и отводится через коллектор в сборник. Промывная жидкость подается через форсунки 2 на образовавшийся осадок и отсасывается в камеры, из которых через коллектор 9 отводится в сборник.
На приводном барабане фильтрующая ткань отделяется от резиновой ленты и огибает направляющий ролик. При этом осадок соскальзывает с фильтровальной ткани и падает в сборник осадка.
Рис. 12 Ленточный вакуум-фильтр:
1 - приводной барабан; 2 – форсунка; 3 - вакуум-камера; 4 - резиновая лента; 5 – лоток; 6 - натяжной барабан; 7 - натяжные ролики; 8 - коллектор для отвода фильтра; 9 - коллектор для отвода промывной жидкости; 10 - сборник осадка; 11 - фильтровальная ткань
При прохождении фильтровальной ткани между роликами 7 она промывается, просушивается и очищается.
Фильтрующие центрифуги периодического и непрерывного действия разделяются по расположению вала на вертикальные и горизонтальные, по способу выгрузки осадка — на центрифуги с ручной, гравитационной, пульсирующей и центробежной выгрузкой осадка. Главным отличием фильтрующих центрифуг от отстойных является то, что они имеют перфорированный барабан, обтянутый фильтровальной тканью.
В фильтрующей центрифуге периодического действия (рис. 13) суспензия загружается в барабан сверху. После загрузки суспензии барабан приводится во вращение. Суспензия под действием центробежной силы отбрасывается к внутренней стенке барабана. Жидкая дисперсионная фаза проходит через фильтровальную перегородку, а осадок выпадает на ней. Фильт- рат по сливному патрубку направляется в сборник. Осадок после окончания цикла фильтрования выгружают вручную через крышку 3.
Рис.13 Фильтрующая центрифуга периодического действия:
1 – станина; 2 - перфорированный барабан; 3 – крышка; 4 – кожух; 5 – ступица; 6 - подшипник; 7 – электродвигатель; 8 - шкив с ременной передачей; 9 - дренажная сетка; 10 - фильтрующая ткань
Конструкция фильтрующей центрифуги с перфорированным барабаном аналогична конструкции автоматической отстойной центрифуги с непрерывным ножевым съемом осадка.
В саморазгружающихся центрифугах (рис. 14) осадок удаляется под действием гравитационной силы. Такие центрифуги выполняют с вертикальным валом, на котором располагается перфорированный барабан. Суспензия подается на загрузочный диск при вращении барабана с низкой частотой. Нижняя часть барабана имеет коническую форму, причем угол наклона делается большим, чем угол естественного откоса осадка. После окончания цикла фильтрования и остановки барабана осадок под действием гравитационной силы сползает со стенок барабана и удаляется из центрифуги через нижний люк.
Рис .14 центрифуга с гравитацонной выгрузкой осадка:
1 - вал; 2 – барабан; 3 - распределительный диск, 4 - упорная втулка
В непрерывно действующих фильтрующих центрифугах с пульсирующей выгрузкой осадка (рис. 15) фильтрат из центрифуги выводится непрерывно, а осадок периодически выгружается из барабана пульсирующим поршнем.
Поршень-толкатель перемещается в горизонтальном направлении в барабане с помощью штока, который находится внутри полого вала барабана. Шток вращается вместе с валом и совершает одновременно возвратно-поступательные движения (10... 16 ходов в минуту, длина каждого хода составляет примерно 0,1 длины барабана). Сервомеханизм автоматически изменяет направление движения поршня.
Рис.15 Центрифуга непрерывного действия с пульсирующей выгрузкой осадка:
1 - полый вал; 2 – шток; 3 – корпус; 4 - поршень – толкатель; 5 - приемный конус; 6 – барабан; 7 - сито
Суспензия подводится по оси вала в приемный конус. В конусе имеются отверстия, по которым суспензия поступает в барабан. Внутренняя поверхность барабана покрыта фильтровальным ситом. Осадок, отложившийся на поверхности сита, промывается и перемещается поршнем к открытому концу барабана. Из барабана осадок выгружается в камеру для осадка.
Центрифуга непрерывного действия с центробежной выгрузкой осадка имеет конический перфорированный барабан, внутри которого вращается шнек со скоростью, несколько меньшей скорости вращения барабана. При вращении витки шнека снимают с барабана отложившийся осадок и перемещают его в нижнюю часть барабана, в камеру для осадка. Выгрузка осадка происходит под действием центробежной силы. При этом осадок не измельчается, его структура не изменяется, как, например, в центрифугах с ножевым срезом и выгрузкой осадка пульсирующим поршнем.
Дата добавления: 2019-07-15; просмотров: 3087; Мы поможем в написании вашей работы! |
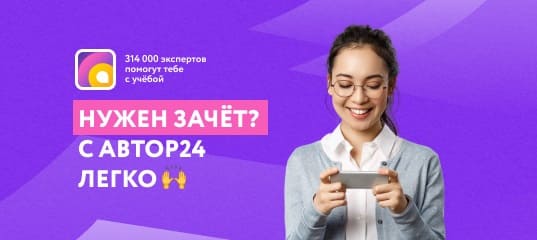
Мы поможем в написании ваших работ!