Применение стеклопластиковых штанг
С декабря 1995 года в НГДУ «ЛН» начали внедрять стеклопластиковые штанги. В течение 1995–1996 года они были внедрены на 14 скважинах, как девонских, так и сернистых скважинах с различной обводненности, добываемой продукции.
Опыт в эксплуатации стеклопластиковых штанг показал их хорошие прочностные и эксплуатационные характеристики, по сравнению со стальными штангами, нагрузка на головку балансира снизилась на 25%. Положительными факторами в работе стеклопластиковых штанг является то, что центраторы хорошо армируются на теле штанг, а так же не подвержены коррозии в скважинах с большим содержанием сероводорода и высокой обводненностью добываемой продукции.
Недостатками стеклопластиковых штанг является слабое соединение узла стеклопластика с металлической головкой, а так же они менее работоспособны в скважинах со значительным отложением парафина, так в скважинах 9288 А, 24356, 9232, 12446 стеклопластиковые штанги были извлечены из-за обрывов штанг по причине больших дополнительных нагрузок при запарафинивании колонны НКТ.
В качестве эксперимента НГДУ «ЛН» была закуплена партия стеклопластиковых штанг. СПНШ изготавливаются из сплетенных жгутов стеклонитей, пропитанных эпоксидной смолой.
Штанги состоят из двух головок и стеклопластикового стержня, которые крепятся между собой с помощью эпоксидной смолы.
Таблица. 6 Техническая характеристика СПНШ
|
|
Номинальный диаметр по телу Длина Плотность Разрушающее напряжение при растяжении Усталостная прочность (количество циклов до разрушения) Эксплуатация и хранение при Т | 19 мм 8000–8500 м 2,00г/см3 760 Мпа 1,2·1012(у стальных) 1,05·108 от -50° до +90 °C |
3.2.3 Физические методы, применяемые в НГДУ «ЛН» для борьбы с отложениями АСПО
В НГДУ «ЛН» магнитные депарафинизаторы типа МОЖ-22Ш были внедрены на 17 скважинах (в 2000 году – на 7 скважинах, в 2002 году – на 10 скважинах) В качестве основного метода борьбы с АСПО магнитные депарафинизаторы были использованы на трех скважинах (№108, 6551А, 12518А), на 4 скважинах – в комбинации с остеклованными НКТ и на 10 скважинах – в комбинации со штангами центраторами – депарафинизаторами.
За период с октября 2000 года, когда началось внедрение магнитных депарафинизаторов, по октябрь 2002 года на данной категории скважин было проведено 16 подземных ремонтов по причине АСПО, причем на 3 скважинах (№108, 4030, 12946) по два ремонта. На скважинах, где магнитные депарафинизаторы были использованы в качестве основного метода борьбы с АСПО без применения других методов, межочистной период составил 50–110 суток и при подземных ремонтах по причине АСПО они были извлечены. На остальных скважинах межочистной период составил от 80 до 360 суток.
|
|
Анализ применения магнитных депарафинизаторов в качестве самостоятельного метода борьбы с АСПО и в комбинации с другими методами показал неэффективность данного метода и отказ от его применения в дальнейшем.
3.2.4 Химические методы, применяемые в НГДУ «ЛН» для борьбы с отложениями АСПО
3.2.4.1 Применение промывок различного типа
В качестве дополнительного метода борьбы с АСПО, в НГДУ «ЛН» на 77,9% осложненного фонда скважин, эксплуатируемых УШГН, используются промывки различного типа (дистиллятом в комбинации с нефтью, МЛ-80Б).
Динамика проведения промывок представлена в таблице 7
Таблица 7. Динамика проведения промывок
Виды промывок | Годы | ||||
1997 | 1998 | 1999 | 10 месяцев | ||
2000 | 2001 | ||||
Всего промывок, – дистиллят + нефть | 1516 745 | 1684 1174 | 1289 625 | 1128 546 | 938 551 |
В качестве растворителя используется нефтяной дистиллят, как собственного производства, так и получаемый в ОЭ НГДУ «Татнефтебитум».
Более 58% всех проведенных в 2004 году обработок составили промывки дистиллятом в комбинации с нефтью. Содержание нефти в растворе при этом составляет от 20 до 50%. Выбор концентрации осуществляется технологическими службами нефтепромыслов с учетом скважинных условий.
|
|
Всего промывками охвачено 484 скважины с периодичностью промывок 2–3 раза в год. Объем разовой нефтедистиллятной обработки составляет в среднем 8 м3.
3.2.4.2 Гидравлический расчет промывки скважины нефтедистиллятной смесью
Исходные данные:
Скважина №1828А,
Н забой = 1620 м – искусственный забой,
Диаметр эксплуатационной колонны Dэкс. к =146 мм,
Диаметр НКТ dHKT = 73 мм,
Диаметр штанг dШТ. = 22 мм,
НН2Б – 44,
Плотность дистиллята ρД = 707 кг/м3,
Q = 8 м3, В=0%.
Техника для промывки:
ЦА – 320; dпоршня = 100 мм; N = 180 л/с
Производительность агрегата:
1 скорость – 1,4 л/с 2 скорость – 2,55 л/с
3 скорость – 4,8 л/с 4 скорость – 8,65 л/с
1. Расчет гидравлического сопротивления при движении дистиллята в кольцевом пространстве.
P1 = λ· (HHKT · ρД)/(Dэкс.к – dHKT) х (vн2/2), Πa (1)
где: l – коэффициент трения, l = 0,035;
ННКТ - длина колонны НКТ, м;
v н – скорость нисходящего потока жидкости, м/с;
ρД – удельный вес дистиллята, кг/м3;
Dэкс. к – диаметр эксплуатационной колонны, м;
dHKT – диаметр НКТ, м;
При работе на 1 скорости:
Р1 = 0,035·(1450·707)/(0,146 – 0,073) х (0,172/2) = 0,0071·106 Па;
на 2 скорости:
Р1 = 0,035·(1450·707)/(0,146 – 0,073) х (0,372/2) = 0,0339·106 Па;
|
|
на скорости 3:
Р1 = 0,035·(1450·707)/(0,146 – 0,073) х (0,532/2) = 0,0696·106 Па;
на скорости 4:
Р1 = 0,035·(1450·707)/(0,146 – 0,073) х (1,032/2) = 0,263·106 Па.
2. Гидравлическое сопротивление по уравновешиванию столбов жидкости в НКТ и колонне:
P2 = (ρн – ρД)·g ·ННКТ, (2)
где: ρн – плотность нефти.
С достаточной точностью для расчетов
P2 = (820 –707)·9,81·1450 = 1,607 ·106 Па
3. Гидравлическое сопротивление в трубах НКТ:
Р3 = j ·lНКТ· ННКТ·ρД · v 2в/[2 (dВН – dШТ.)] (3)
где: j – коэффициент, учитывающий потери на местных сопротивлениях при движении дистиллята в НКТ,
j =1,1;
lНКТ – коэффициент трения в НКТ, lНКТ = 0,04;
dВН – внутренний диаметр НКТ, м;
dШТ. – диаметр штанг, м;
v в-скорость восходящего потока, м/с;
на 1 скорости:
Р3 = 1,1·0,04·1450·707·0,4 2/[2·(0,062 – 0,022)] = 0,09·10 6 Па
на 2 скорости
Р3 = 1,1·0,04·1450·707·0,8 2/[2·(0,062 – 0,022)] = 0,361·10 6 Па
на скорости 3
Р3 = 1,1·0,04·1450·707·1,6 2/[2·(0,062 – 0,022)] = 1,443·10 6 Па
на скорости 4
Р3 = 1,1·0,04·1450·707·2,91 2/[2·(0,062 – 0,022)] = 4,775·10 6 Па
Гидравлические сопротивления на выходе агрегата ЦА-320 при обратной промывке ничтожно малы, при расчете их не используют.
5. Давление на выкиде насоса:
Рв = Р1+ Р2+ Р3; (4)
На 1 скорости:
Рв = 0,0071·10 6 + 1,607·10 6 + 0,09·10 6 = 1,704·10 6 Па;
На 2 скорости:
Рв = 0,0339·10 6 + 1,607·10 6 + 0,361·10 6 =2,002·10 6 Па;
На 3 скорости:
Рв = 0,0696·10 6 + 1,607·10 6 + 1,443·10 6 =3,120·10 6 Па;
На 4 скорости:
Рв = 0,263·10 6 + 1,607·10 6 + 4,775·10 6 =6,645·10 6 Па.
6. Рассчитываем мощность насоса:
N = Pв· Q/η, (5)
где η – К.П.Д насоса, η = 0,65;
на 1 скорости:
N =1,704·10 6 Па·1,4/0,65 = 3,67 кВт;
на 2 скорости:
N =1,704·10 6 Па·2,55/0,65 = 6,68 кВт;
на 3 скорости:
N =1,704·10 6 Па·4,8/0,65 = 12,58 кВт;
на 4 скорости:
N =1,704·10 6 Па·8,65/0,65 = 22,68 кВт.
7. Использование максимальной мощности:
К = (6),
где максимальная мощность насоса Nmах = 130 кВт;
на 1 скорости:
К = 3,67·100/130 = 2,82%;
на 2 скорости:
К = 6,68·100/130 = 5,14%;
на 3 скорости:
К = 12,58·100/130 = 9,68%;
на 4 скорости:
К = 22,68·100/130 = 17,45%.
8. Скорость подъёма дистиллята в Н.К.Т.
v п =v в (7),
на 1 скорости v п = 0,4 м/с
на 2 скорости v п = 0,8 м/с
на 3 скорости v п = 1,6 м/с
на 4 скорости v п = 2,91 м/с
9. Продолжительность подъёма дистиллята в НКТ с разрыхлением парафина и его выносом:
t =HHKT/ v п (8),
на 1 скорости:
t =1450/0,4 = 3625 сек. = 60,42 мин.;
на 2 скорости:
t =1450/0,8 = 1812,5 сек. = 30,21 мин.;
на 3 скорости:
t =1450/1,6 = 902,25 сек. = 15,10 мин.;
на 4 скорости:
t =1450/2,91 = 498,28 сек. = 8,30 мин.
В НГДУ «ЛН» применяется для промывки скважин нефтедистиллятной смесью комплекты из агрегата ЦА-320 на базе КрАЗ-257 и автоцистерны на базе КамАЗ – 5220 емкостью 8 м3.
Из гидравлического расчета промывки скважины видно, что оптимальный режим работы агрегата осуществляется на 3 скорости, т. к. при этом режиме происходит наилучшее вымывание парафина с НКТ и соблюдаются технические условия безопасности работы с горючим материалом – давление выкида насоса меньше или равно 7 МПа.
Из условий наименьших гидравлических сопротивлений промывку желательно начинать на 1 скорости, производительностью 1,4 л/с, с постепенным наращиванием расхода (т.е. переходом на 2–3 скорости)
Продолжительность промывки на 3 скорости (объём 8 м3) составит 15,10 минут. При окончании промывки в обратной последовательности опускаемся до 1 скорости и заканчиваем промывку.
3.2.4.3 Применение ингибиторов различного типа
Наиболее эффективным методом борьбы с парафином является химический метод, который основан на добавке в поток жидкости при помощи агрегатов ЦА 320 М и АКПП -500, ДРС и ДРП-1, а также УДЭ и УДС, химических реагентов способных гидрофилизации стенок труб, увеличению числа центров кристаллизации парафина в потоке, повышению дисперсности частиц парафина в нефти.
Такими растворителями могут быть водо- и нефтерастворимые ПАВ.
Существует множество типов отечественных и импортных ингибиторов для предотвращения и удаления отложений парафина. Большинство реагентов способствует так же предупреждению образования или разрушению водонефтяных эмульсий. Наиболее эффективные реагенты СНПХ – 7202, 7204, 7400. На месторождениях АО «Татнефть» широко применяется ингибитор для предотвращения и удаления отложений парафина СНПХ-7215, который закачивается в затрубное пространство скважины при помощи агрегатов УЭД и УДС.
Наибольшее распространение на промыслах НГДУ «ЛН» получил ингибитор СНПХ-7212 М, который закачивается в затрубное пространство скважин при помощи устьевых дозаторов УЭД и УДС из расчета 100–200 г./т нефти.
Ингибиторы парафиноотложений можно дозировать в скважины при помощи глубинных дозаторов ДСИ-107. Скважинный дозатор ДСИ-107, разработан ТатНИПИнефти, предназначен для подачи водо-нерастворимых ингибиторов на приём штангового насоса. Дозатор может, применятся в скважинах с обводненностью продукции не менее 10% при температуре рабочей среды от 283 до 373 К (10 – 1000С). Плотность применяемого ингибитора должна быть ниже плотности воды не менее чем на 50 кг/м3, а кинематическая вязкость – не более 450 м2/с. Дозатор обеспечивает непрерывную подачу химреагента в пределах от 0,1 до 40 л/сут.
Эксплуатация дозатора состоит в следующем: определяются необходимый объём химреагента, длина колонны НКТ для размещения ингибитора и диаметр втулки дозатора для установления режима его работы. На скважину завозят расчетное количество ингибитора и НКТ. Из скважины извлекается насосное оборудование.
Спускается в скважину колонна НКТ расчетной длины, нижний конец которой снабжен заглушкой и пробкой.
Определяется плотность ингибитора (денсиметром) и вязкость его (вискозиметром) при температуре среды на глубине подвески дозатора в скважине, содержание воды в продукции скважины по данным предыдущей эксплуатации скважины.
При условии соответствия параметров раствора ингибитора расчетным, химреагент заливается в колонну НКТ.
Помещается втулка в камеру и заворачивается корпус в корпус. Присоединяют дозатор к колонне НКТ, предварительно ввернув трубку в нижний конец гидролинии, и устанавливают фильтр на нижнем конце нагнетательной гидролинии. Присоединяют насос к дозатору.
Спуск штангового насоса с дозатором в скважину производится в обычном порядке на необходимую глубину.
Подъём оборудования, и извлечение его из скважины производится в порядке, обратном спуску. При этом для подъёма труб без жидкости необходимо слить их содержимое, сбив полую пробку сбрасыванием металлического лома в колонну НКТ после отсоединения от нее дозатора.
Работу дозатора в скважине следует контролировать по изменению дебита скважины, величине нагрузки на головку балансира СК, химическими анализами устьевых проб добываемой жидкости.
Длину колонны НКТ для заливки раствора ингибитора целесообразно подобрать с таким расчетом, чтобы повторная заправка химреагентом производилась при очередном текущем ремонте скважины.
В зимнее время на ряде удаленных скважин применяются обработки ингибитором парафиноотложения ТНПХ – 1А в объеме 20–30 литров на скважину с периодичностью 1 раз в месяц.
3.2.5 Тепловые методы, применяемые в НГДУ «ЛН» для борьбы с отложениями АСПО
Если интенсивность отложения парафина невелика, то при каждом подземном ремонте поднимают трубы на поверхность и удаляют из них парафин пропариванием с помощью ППУ.
Очистка скважин, оборудованных ШГН от парафина производится за счет тепловой энергии пара, закачиваемое в затрубное пространство скважин. При этом происходит расплавление парафина находящегося в НКТ и вынос его из скважины. Настоящая технология предусматривает соблюдение следующих требований:
– периодичность очистки и количество ППУ корректируется старшим технологом промысла;
– очистка скважины от парафина при работающем СГН, при остановленном из-за отложений парафина;
– закачка пара в затрубное пространство производится после предварительного прогрева манифольда до температуры 100–150 0С;
– при очистке от парафина заклиненных скважин полированный шток устанавливается в верхнее положение, а головка балансира в нижнее положение. После того, как шток уйдет вниз, начинается попытки расхаживания штанговой колонны.
В настоящее время в НГДУ «ЛН» стремятся отказаться от тепловых методов борьбы с АСПО из-за высокой энергоемкости.
Экспериментальные исследования и расчеты распределения температуры по стволу скважины при проведении горячей промывки при помощи АДП показывают, что при глубине спуска насоса, равной 1200 метров, температура, необходимая для расплавления парафина (30–400С) достигает глубины 400–450 метров. Особенно затруднена промывка через насосы малого диаметра (28–32 мм) из-за малого проходного сечения в клапанных узлах.
Для снижения затрат и повышения эффективности горячих промывок насосного оборудования в компоновку колонны НКТ на глубине около 500 метров включают обратный клапан.
В существующих условиях передвижные парогенераторные установки применяются редко и только в тех случаях, где использование других методов невозможно по технологическим причинам.
3.2.5.1 Расчет потерь теплоты по стволу скважины при паротепловой обработке
Исходные данные: диаметр НКТ d = 0,062 м; суммарный коэффициент теплопередачи К = 666,2 кДж/м2Кч; средний коэффициент теплопроводности горных пород λ = 1,02 кДж/мКч; время прогрева t = 3 час.; потеря теплоты в породе в функции времени за время прогрева f(τ) = 3,78; температура рабочего агента (пара) на устье скважины То = 468 К; среднегодовая температура воздуха J0 = 275 К; глубина интервала закачки рабочего агента Н = 1300 м; геотермический градиент s = 0,0154 К/м;
1. Определим потери теплоты по стволу скважины
Q = 2πrKλ/[λ+rKf(τ)]·[(To-J0) H – σH 2/2] (9)
Q = 2·3,14·0,031· 666,2·1,02/(1,02+0,031·666,2·3,78)·[(468 – 275)·1300 – (0,0154·13002)/2] = 400000 кДж/ч. = 400 МДж/ч;
2. Суммарные потери теплоты за время прогрева:
Qc = Q·t; (10)
Qc = 400·3 = 1200 МДж = 1,2 ГДж;
3. Общее количество теплоты подведенное к скважине:
Q' = i·G (11)
Где i – энтальпия пара при температуре 468 К и давлении 1,2 Мпа,
i = 2820 кДж/кГ; G – массовый расход закачиваемого пара, G = 4200 кГ;
Q' = 2820·4200 = 11844000 кДж = 11,844 ГДж;
4. Определяем количество теплоты дошедшей до забоя;
Q'' = Q' – Qc; (12)
Q'' = 11,844 – 1,2 =10,644 ГДж;
5. Потери теплоты составляют:
η = Qc·100%/Q' (13)
η = 1,2·100%/11,844 = 10,13%.
В настоящее время в НГДУ «ЛН» стремятся отказаться от тепловых методов борьбы с АСПО из-за высокой энергоемкости.
3.3 Техника и оборудование, применяемое для депарафинизации скважин в условиях НГДУ «ЛН»
Для депарафинизации скважин в НГДУ «ЛН» применяют различное оборудование. Краткое их описание и технические характеристики приведены ниже.
Наиболее часто применяют для депарафинизации скважин метод промывки. При промывке микробиологическим раствором, нефтедистиллятной смесью, дистиллятом используются автоцистерны и промывочные агрегаты.
Доставка промывочного раствора на скважину осуществляется в автоцистернах ЦР-7АП, АЦН – 7,5–5334, АЦН-11–257, АЦ-15–5320/8350, АЦ-16П.
Таблица 9 Техническая характеристика автоцистерн
Автоцистерна Транспортная база Грузоподъемность, т Наибольшая скорость передвижения с полной нагрузкой, км/ч Тяговый двигатель-четырёхконтактовый дизель Номинальная мощность (при п=2100 мин-1), кВт Вместительность цистерны Центробежный насос Подача (дм3/с) при напоре, м 70 48 Время заполнения жидкостью, мин Наиб. мощн, потреб. насосом, кВт Условн. диам. линии, мм всасывающей напорной Всасывающее устройство Высота всасывания, м Рабочий агент Размеры, мм длина ширина высота Масса, кг полная комплекта | АЦН-11–257 КрАЗ-257Б1А 12 68 ЯМЗ-238 176,5 11 9 9600 2500 2860 22600 11040 | АЦН – 7,5–5334 МАЗ-5334 7,2 85 ЯМЗ-236 132 7,5 12,5 21 6 15 100 50 Эжектор 5 6950 2500 2870 15325 7450 | ЦР-7АП КрАЗ-255 7,5 71 ЯМЗ-238 176,5 7,5 8590 2500 3070 19035 10980 |
Для промывки скважин применяются самоходные насосные агрегаты: цементировочный агрегат ЦА-320М, насосные установки УН1–100х200,
УН1Т-100х200. Все агрегаты имеют трубки высокого давления с цилиндрической резьбой для быстрой сборки и разборки нагнетательной линии.
Таблица 10 Техническая характеристика ЦА-320 М
Монтажная база Силовая установка: марка тип двигателя Наиб.мощн. при частоте вращ. вала дв-ля 2800 мин-1, л.с. Насос марки Наибольшая подача насоса, л/с. Наибольшее давление, МПа Водопадающий насос Наибольшая подача, л/с. Наибольшее давление, МПа Объём мерной ёмкости, м3 Диам.проходн. сечения коллектора, мм приёмного нагнетательного Вспомогательный трубопровод число труб общая длина, м Масса агрегата, кг без заправки заправленного Габаритные размеры, мм | КрАЗ-257 5УС-70 ГАЗ-51 70 9Т 23 32 1В 13 1,5 6,4 100 50 6 22 16970 17500 10425х2650х3225 |
3.4 Техника и оборудование при паротепловой обработке
При паротепловой обработке используются специальная техника и оборудование, парогенераторные установки: отечественная ППГУ-4/120М с максимальной производительностью пара 4 т/ч и рабочим давлением 12 МПа, заграничные «Такума» и КSК.
Парогенераторная установка предназначена для выработки пара. Котлоагрегаты установок могут работать на природном газе или жидком топливе. Для предупреждения образования накипи на поверхности нагрева сырую воду перед подачей в котел осветляют и обессоливают в специальных фильтрах.
Таблица 11 Техническая характеристика парогенераторной установки ППГУ – 4/120М
Теплопроизводительность по отпускаемому пару, кВт/ч Давление на выходе из парогенератора, мПа максимальное рабочее Давление пара на выходе из установки. МПа Степень сухости пара, % Расход пара на скважину, кг/с Установленная электрическая мощность, кВт Вместимость осн. топливного бака, л Вместимость бака воды. л Метод деаэрации Масса установки, кг Масса блока парогенератора, кг Габариты, мм парогенератора водоподготовки | 2,32 13,2 6–12 0–12 80 0,55–1,11 75 1000 5000 термический 39700 29500 12080х3850х3200 6250х3850х3200 |
Установка ППУА-1200/100
Предназначена для депарафинизации скважин, промысловых и магистральных нефтепроводов, замороженных участков наземных коммуникаций в условиях умеренного климата. Можно использовать так же при монтаже и демонтаже буровых установок и при прочих работах для отогрева оборудования.
Включает в себя парогенератор, водяную, топливную и воздушную системы, привод с трансмиссией, кузов, электрооборудование и вспомогательные узлы. Оборудование установки смонтировано на раме, закрепленной на шасси автомобиля высокой проходимости КрАЗ-255Б или КрАЗ-257, и накрыто металлической кабиной для предохранения от атмосферных осадков и пыли.
Привод основного оборудования осуществляется от тягового двигателя автомобиля, управление работой установки – из кабины водителя.
Таблица 12 Техническая характеристика ППУА – 1200/100
Монтажная база Максимальная температура 0С Максимальное давление пара, МПа Применяемое топливо Максимальный расход топлива, кг/ч Ресурс работы установки (по запасу воды на максимальной производительности) ч Масса (с заправочными емкостями), кг | Шасси авт. КрАЗ 255Б или КрАЗ 257 310 10 Дизельное 83,2 3,5 19200 или 18380 |
Агрегаты АДПМ
Предназначены для депарафинизации скважин горячей нефтью. Агрегат, смонтирован на шасси автомобиля КрАЗ 255Б1А, включает в себя нагреватель нефти, нагнетательный насос, системы топливо и воздухоподачи к нагревателю, систему автоматики и КИП, технологические и вспомогательные трубопроводы.
Привод механизмов агрегата – от двигателя автомобиля, где размещены основные контрольно- измерительные приборы и элементы управления.
Таблица 13 Техническая характеристика агрегатов АДПМ-12/150 и 2АДПМ-12/150
Подачи по нефти м3/ч Максимальная температура нагрева нефти 0С безводной Рабочее давление пара на выходе. МПа Теплопроизводительность агрегата гДж | АДПМ-12/150 12 150 122 13 3,22 | 2АДПМ-12/150 12 150 122 13 3,22 |
Нефть, подвозимая в автоцистернах, закачивается насосом агрегата и прокачивается под давлением через нагреватель нефти, в котором она нагревается до необходимой температуры. Горячая нефть подается в скважину, где расплавляет отложения парафина и выносит их в промысловую систему сбора нефти
3.5 Расчет на прочность стеклопластиковых штанг
С целью определения нагрузок, возникающих в точке подвеса штанг, произведём расчет на прочность комбинированной колонны из стальных и стеклопластиковых штанг. Расчет будем вести согласно «Методики расчета колонны штанг из композиционного материала для ШСНУ», разработанной ВНИИнефтемаш 24.07.1994.
Исходные данные для расчета:
Номер скважины №1696
Глубина подвески насоса Ннас = 1200 м
Длина хода сальникового штока S = 0,9 м
Число качаний балансира п = 5 мин-1
Средняя масса 1 м колонны СПНШ тспнш = 1,05 кг
Средняя масса 1 м колонны стальных штанг тст = 2,35 кг
Диаметр плунжера Дпл = 32 мм
Диаметр штанг dшт = 19 мм
Внутренний диаметр НКТ Двн = 62 мм
Плотность жидкости r ж = 1090 кг/м3
1. Для вычисления максимальной нагрузки в точке подвеса штанг Ртах воспользуемся формулой Слоннеджера
Ртах=(Ршт + Рж)*(1 + S *п/137), Н (20)
где: Ршт – вес колонны штанг, Н
Рж – вес столба жидкости, Н
S – длина хода сальникового штока, м
п – число ходов, мин-1
2. Вычислим вес колонны штанг Ршт
Ршт= Ннас*g*(тспнш* ? + ?*тст)= 1200*9,81*(1,05 *0,5 + 0,5 *2,35) = 20012,4 Н
3. Найдем вес столба жидкости Рж
Рж=Fпл*Ннас*r ж *g (21)
где: Fпл= p/4*Дпл2=p/4*(32*10-3) 2=8,01*10-4 м 2
Рж=8,01*10-4*1200*1090 *9,81=10314,5 Н
Вычислим Ртах;
Ртах=(20012,4 + 10314,5)*(1 + 0,9 *5/137)=31323 Н
4. Минимальное усилие в точке подвеса штанг при ходе вниз
Рт1п=Ршт1 (1 – S *п/137), Н (22)
где: Ршт1 – вес колонны штанг в жидкости
Ршт1=Ннас*g* (?*g1спнш+ ? *g1ст) (23)
здесь: g1спнш – вес 1 м СПНШ в жидкости
g1ст – вес 1 м стальных штанг в жидкости
Ршт1=1200*9,81*(?*0,71+ ? *2,09)=16480,8 Н
Рт1п=16480,8*(1 -0,9*5/137)=15939,5 Н
5. Для определения напряжений, действующих в точке подвеса штанг, воспользуемся следующими формулами:
fшт=p/4*dшт2= 0,785*(19*10-3)2= 2,84*10-4 м2 (24)
sтах= Ртах/ fшт = 31323/2,44*10-4=110,3 мПа (25)
sт1п= Рт1п/ fшт = 15939,5/2,84*10-4=56,1 мПа (26)
sа=(sтах -sт1п)/2= (110,3–56,1)/2=27,1 мПа (27)
sпр= =
= 54,7 Мпа (28)
Как видно из вычислений, приведенное напряжение, действующее в точке подвеса штанг равно 54,7 МПа.
Так как по предельно допустимым приведенным напряжениям для стеклопластика у нас нет значений, то воспользуемся минимальным значением предельно допускаемых приведенных напряжений для стали марки 40. В пользу стеклопластиковых штанг говорит также, что разрушающее напряжение при растяжении у них больше, чем у стальных: 760 МПа у стеклопластика и 610 МПа у стали.
[sпр]=70мПа – приведенное напряжение для стали
Полученное sпр=54,7 мПа свидетельствует о возможности использовать в качестве материала для штанг стеклопластик.
Для приведения эксперимента было подобранно 9 скважин. Для определения эффективности использования стеклопластиковых штанг скважины были оборудованы счетчиками активной и реактивной электрической мощности.
Ниже в таблице №14 приведены результаты расчетов.
Таблица. 14 Результаты анализа работы СПНШ
Нагрузка на головку балансира кН | 1696 | 9288А | 15470 | 12428а | 26769 | 26504 | 16942 | 24356 | 26480 |
Стеклопластик Стек+сталь Сталь Потр. мощн с учетом веса штанг, кВт Стеклопластик Стек+сталь Сталь Умень. веса% Умень. потребляемой мощности | 21,4 31,3 38,5 18,3 23,2 33 | 20,5 28,1 35,9 17,1 20,6 24,2 22 19 | 10,6 12,7 18,5 2,9 3,3 4,5 31 26 | 21,6 29,2 37,8 18,2 22,4 32,9 22,7 31,4 | 17,5 24,1 30,6 12,6 17,6 24,6 21 28 | 12,6 17,1 27,9 5,6 7 10,5 38 32 | 17,1 22,1 29,9 10,3 11,8 14,3 26,1 17,5 | 22,5 33,3 39,4 18,5 24,6 33,1 15,4 27 | 11,9 15,7 26,5 3,9 4.8 7,3 40 34 |
Сравнивая результаты можно сделать вывод, что нагрузка на головку балансира станка-качалки уменьшилась в среднем на 20–25% при условии комплектации колонны штанг из стеклопластика и стали.
3.6 Выбор оборудования для подачи реагента (ингибитора)
Существуют два основных способа подачи реагента в обрабатываемую систему: непрерывное (периодическое) дозирование и разовая обработка.
Наиболее эффективным способом является непрерывное дозирование, обеспечивающее постоянный контакт реагента с обрабатываемой системой и частично предупреждающее образование АСПО. Однако этот способ требует обвязки специального оборудования на устье каждой скважины (насос – дозатор, емкость для реагента, поршневой насос для смешения, манифольд и др.).
Реагент в затрубное пространство постоянно подается устьевыми дозаторами УДЭ и УДC конструкции НПО Союзнефтепромхим и СКТБ ВПО Союзнефтемашремонт.
УДЭ и УДC можно применять также для борьбы с солеотложением, коррозией оборудования нефтяных скважин и внутрискважинной деэмульсации нефти.
Электронасосная дозировочная установка УДЭ в зависимости от дозировочного насоса имеет четыре типоразмера: УДЭ 0,4/6,3; УДЭ 1/6,3; УДЭ 1,6/6,3; УДЭ 1,9/6,3. Установки комплектуются специальными дозировочными насосами: НД 0,4/6,3 К14В; НД 1/6,3 К14В; НД 1,6/6,3 К14В; НД 1,9/6,3 К14В. Они обеспечивают максимальные подачи реагента 0,4; 1; 1,6 и 1,9 л/ч при максимальном давлении нагнетания 6,3 МПа. Потребляемая мощность насоса 0,5 кВт, масса 32 кг.
Установка имеет бак на 450 л; габаритные размеры установки 1230х690х1530 мм, масса 220 кг, рабочая температура 223 – 318 К.
Принцип работы УДЭ заключается в следующем. Реагент из бака 5 через фильтр 6 по всасывающему трубопроводу 11 поступает в плунжерный насос – дозатор 13 и по нагнетательному трубопроводу 14 подается в затрубное пространство скважины. Подача регулируется изменением длины хода плунжера.
Наибольшее число установок эксплуатируется в ПО «Татнефть». Дозировочные установки изготавливаются Лениногорским заводом «Нефтеавтоматика», а дозировочные насосы – Свесским насосным заводом.
Рис. 4 Дозировочная установка УДЭ
1 – дозировочный блок, 2 – электроконтактный манометр, 3 – указатель уровня, 4 – заливная горловина, 5 – бак, 6 – фильтр, 7 – рама, 8 – сливной вентиль, 9, 10, 15 – вентили, 11 – всасывающий трубопровод, 12 – обратный клапан, 13 – электронасосный агрегат, 14 – нагнетательный трубопровод, 16 – кожух
Комплектная дозировочная установка УДС с приводом от станка – качалки располагается на СК. Её нагнетательный трубопровод присоединяется к затрубному пространству скважины, а рычаг дозировочного насоса посредством гибкой тяги к балансиру СК. Подача устанавливается регулятором длины хода плунжера насоса и изменением мест крепления тяги к рычагу насоса и к балансиру СК. Подача дозировочного насоса составляет 0,04–0.63 л/с; давление нагнетания 6,3 МПа; вместимость бака 250 л, габаритные размеры 1500 х 730 х 735 мм, масса 145 кг.
По сравнению с другими дозировочными установками УДС-1 обеспечивает большую точность регулирования подачи, имеет более простую конструкцию, она безопасна (снабжена предохранительным устройством и не питается электрическим током) и удобна в эксплуатации.
Рис. 5 Дозировочная установка УДС
1 – указатель уровня, 2 – горловина, 3 – бак, 4 – манометр, 5 – предохранительный клапан, 6 – вентиль, 7 – кожух, 8 – насос дозировочный, 9 – обратный клапан, 10 – трехходовой клапан, 11 – фильтр, 2 – рама
Периодическое дозирование может осуществляться при использовании перечисленного выше оборудования или с помощью специального устройства для ввода реагента под давлением, первый случай имеет те же недостатки что и непрерывное дозирование. Во втором случае затрубное пространство перекрывают задвижкой 3, открывают вентиль 6 для сброса газа из емкости 4, снимают заглушку 5, закрывают вентиль 6, заливают реагент в емкость 4, закрепляют заглушку и открывают задвижку 3; регент поступает в затрубное пространство.
Рис. 6 Принципиальная схема устройства ввода реагента в затрубное пространство по давлением: 1 – устьевая арматура, 2 – выкидная задвижка,
3 – задвижка затрубного пространства, 4 – резервуар для реагента, 5 – заглушка, 6 – вентиль.
При этом способе подачи реагента обслуживание упрощается, но снижается эффективность действия реагента.
Дата добавления: 2019-07-15; просмотров: 311; Мы поможем в написании вашей работы! |
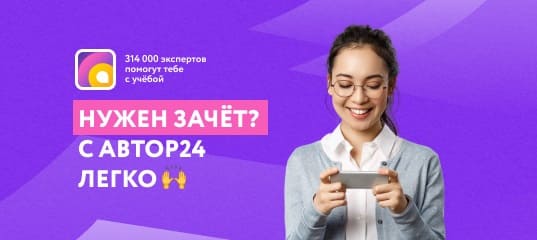
Мы поможем в написании ваших работ!