Мизурская обогатительная фабрика.
Фабрика была открыта в 1928г.
Руду поставляют с Джимидонского месторождение и с Архона.
За 6 месяцев накопили 15 тыс тонн руды за год. Это связано с тем, что фабрика не успевает за щахтой. По плану фабрика должна переработать 25 тыс тонн руды в год.
Грохота-устройство в виде крупной сетке, регулирующее размеры руды, поподаемой в щековую дробилку.
Щековая дробилка:0.75 мм- крупное дробление, 0.50мм- среднее дробление, 0.25 мм- мелкое дробление.
На фабрике установлены огромные ёмкости для воды. На 1 тонну руды требуются 4.5м воды. Вода поступает с Бакского ущелья.
Руду выгружают через грохота в бункера. Оттуда на щековую дробилку. Далее руда поподает на основной конвейер. Под конвейером находится 10 бункеров, вместимостью 60-70 тонн. После этого руда попадает в мельницу.
На фабрике 2 мельницы. Производительность мельницы 35 тонн в час. Руда в мельницах дробится до состояния, когда можно отделить свинец или цинк.
Измельчённая руда попадает в цинковые или свинцовые флотации.
Потом через насосы руда попадает в спустители.
Пустая порода и шлаки по трубопроводу выпускаются в Уналское водохранилище.
Последняя стадия- фильтры. В них через насосы попадает воздух, для осущения руды до влажности 6-8%, для получение 50% концентрата.
Дальнейшая переработка на заводе «ЭЛЕКТРОЦИНК»
|
|
Зарамагская ГЭС.
Зарама́гские гидроэлектроста́нции — гидроэнергетический комплекс на реке Ардон в Алагирском районе Северной Осетии, состоящий из двух взаимосвязанных гидроэлектростанций — действующей Головной ГЭС и строящейся Зарамагской ГЭС-1. Строительство комплекса было начато в 1976 году, его окончание намечено на 2018 год.
Проект реализуется в сложных природных условиях и отличается рядом уникальных для российской гидроэнергетики технических решений — в частности, Зарамагская ГЭС-1 будет иметь самый большой в России напор, самые мощныековшовые гидротурбины, самый длинный деривационный тоннель. Управление строительством осуществляет АО «Зарамагские ГЭС», являющееся дочерним предприятием ПАО «РусГидро».
Природные условия
Сооружения Зарамагских ГЭС расположены на участке верхнего течения реки Ардон (приток Терека) от села Нижний Зарамаг, где река выходит из Туальской котловины (в которой сливаются четыре основные составляющие реки —Мамисондон, Нардон, Адайком и Цмиакомдон), до впадения реки Баддон, протяжённостью около 16 км. На данном участке река протекает в горной местности на высотах 1730—1010 метров, в узком (ширина по дну 20—40 м)Кассарском ущелье, глубиной до 600—800 м и уклоном склонов до 45°. Ущелье прорезает Боковой хребет, сложенный скальными метаморфическими (сланцы) и изверженными (граниты) породами, разорванными тектоническими нарушениями и зонами дробления. Пойменная часть долины заполнена слоем аллювиальных и озерно-аллювиальных отложений мощностью до 45 м, на глубине около 25 м среди этой толщи в основании плотины залегает слой пылеватых суглинков. Строительство сооружений осложняется наличием в скальных породах многочисленныхтектонических зон, активным развитием склоновых процессов (оползни, обвалы, сели, снежные лавины).
|
|
Описание сооружений
Зарамагский гидроузел представляет собой сложный комплекс взаимосвязанных сооружений, который разделяется на две группы: сооружения головного узла (Головная ГЭС) и сооружения Зарамагской ГЭС-1. Головная ГЭС создана по приплотинной схеме и использует напор, создаваемый грунтовой плотиной. Зарамагская ГЭС деривационного типа, использует напор, создаваемый при помощи длинного деривационного тоннеля. Суммарная установленная мощность комплекса ГЭС — 352 МВт, среднесуточная мощность — 24,9 МВт, суммарная среднегодовая выработка — 812 млн кВт·ч.
|
|
Головной узел
Сооружения комплекса головного узла обеспечивают забор воды в деривационный тракт Зарамагской ГЭС-1 из образуемого плотиной водохранилища. При этом создаваемый плотиной напор используется для дополнительной выработки электроэнергии на Головной ГЭС. Комплекс головного узла включает в себя плотину, водохранилище, строительно-эксплуатационный водосброс, водоприёмник, напорный тоннель №1, здание Головной ГЭС, ОРУ 110 Кв.
Плотина
Плотина грунтовая насыпная, максимальная высота плотины 39 м, длина 300 м, ширина по подошве 330 м, объём насыпи 1,586 млн м³. Плотина отсыпана из галечно-гравелистых грунтов, имеет противофильтрационное ядро изсупесчано-щебенистых грунтов. В ходе строительства первоначальный проект плотины был изменён — уменьшена высота плотины (по первоначальному проекту она должна была составлять 79 м при объёме насыпи 3,726 млн м³), насыпь галечно-гравелистых грунтов в упорных призмах была частично заменена на насыпь рядового камня из горныхосыпей, что существенно повысило надёжность плотины. Особенностью плотины является повышенная по отношению к нормальному подпорному уровню воды в водохранилище (НПУ) отметка гребня плотины (1708 м при отметке НПУ 1690,6 м; таким образом, гребень плотины выше нормального уровня воды в водохранилище на 17,4 м), что обеспечивает безопасность плотины в случае обрушения в водохранилище крупного оползня или обвала. Кроме того, конструкция плотины обеспечивает возможность наращивания её высоты в случае принятия в будущем такого решения.
|
|
3.6.Заводы: « Электроцинк » и « Победит » .
Завод «Электроци́нк» — одно из крупнейших предприятий цветной металлургии России. Завод расположен в Промышленном муниципальном округе Владикавказа. Входит в структуру Уральской горно-металлургической компании.
История предприятия
История завода восходит к Алагирскому заводу по выплавке свинца и серебра, давшему первую продукцию 21 мая 1853 года. Завод по производству цинка начинался как небольшое предприятие с бельгийским капиталом «Алагир» в 1898 году. Первый в России цинк был получен на этом заводе 1 января 1905 года. В марте 2005 года на «Электроцинке» отметили 100-летие со дня выработки первой партии цинка.
В 1922 году на базе предприятия было создано объединение «Кавцинк»[1]. Директором индустриального построения комбината и первым директором уже построенного комбината был Ефрем Иванович Осепян, окончивший Промакадемию и институт «Цветметзолото» в Москве, репрессирован в 1938 году и замещён тогдашним начальником свинцового цехаЕфимом Павловичем Славским (будущим крупным руководителем Атоммаша). 2 января 1934 года на заводе был получен первый в СССР электролитный цинк(содержание металла 99,9 %). С того времени завод стал называться «Электроцинк». Для обеспечения работы электролитного цеха строилась Гизельдонская ГЭС.
С началом Великой Отечественной войны завод перешёл на обслуживание оборонных заказов и производство запчастей для сельскохозяйственной техники. Основное технологическое оборудование было вывезено в казахстанский город Усть-Каменогорск, где был позже построен свинцово-цинковый комбинат.
В 1945—1970-е годы на заводе разрабатывали и осваивали уникальные технологии. Первые промышленные печи для обжига концентратов в кипящем слое взамен многоподовых печей были построены на «Электроцинке», предложены они были в 1946 году[1]:87. Завод рассматривался как базовый для внедрения и отработки новых технологий и систем автоматизации.
Начало рыночных реформ принесло на предприятие серьёзные проблемы экономического, технического и экологического характера. Производство было практически на грани остановки.
В конце 2003 года завод вошёл в состав холдинга «Уральская горно-металлургическая компания». Заработало производство на самом заводе, активизировалась работа и на старой сырьевой базе «Электроцинка» — Садонском горнорудном предприятии.
Производство.
Сегодня завод производит цинк, свинец, кадмий, серную кислоту, цинк-алюминиевые сплавы, полипропилен, индий. В 2007 году завод произвёл свыше 35,6 тысяч тонн мягкого свинца, свыше 90,4 тысяч тонн чушкового цинка, 258,8 тонн кадмия
Экологические проблемы.
До 2003 года завод представлял собой серьезную экологическую проблему для территории. Однако с приходом Уральской горно металлургической компании началась широкомасштабная модернизация производства, которая к настоящему времени привела к полному снятию всех экологических и природоохранных вопросов. Ликвидация в 2005-2006 годах старого агломерационного производства позволила в 10 раз сократить выбросы свинца. Проведенная модернизация сернокислотного производства в 2006-2010 годах практически сняла все вопросы с несанкционированными выбросами предприятия, в 6-8 раз снизив уровень выбросов по сернистому газу. Начиная с 2011 года завод работает полностью в нормативах РФ по ПДВ, не имеет нарушений и аварийных выбросов. На техническое перевооружение и модернизацию за прошедшие 10 лет УГМК затратило более 13 млрд. руб. Сегодня доля завода в поступлении вредных веществ в атмосферу в городе Владикавказе составляет не более 0,2%. 99,8% приходится на автотранспорт, тепловые станции и 1050 других предприятий республики, занесенных в реестр Минприроды РФ. Выбросы завода в натуральных показателях составляют не более пятой части от утвержденных нормативов. В 2013 году предприятие пустило в эксплуатацию градирню охлаждения отработанного электролита в электролитном цехе. Это самый крупномасштабный проект не только завода, но и Северного Кавказа. Стоимость проекта составила 546 млн. руб. Вместе с пуском в 2008 году системы промливневой канализации предприятие фактически решило вопрос сбросов в водную среду. Оставшиеся технические воды проходят полную очистку на очистных сооружениях завода. Несмотря на явный экологический эффект работы УГМК в Северной Осетии, наблюдаются отдельные выступления экологов-общественников за закрытие предприятия. Данная позиция неоднократно характеризовалась правительством республики, как неконструктивная, а подчас и заказная. За последние 4 года протестное движение то набирало силу, то стихало. Но в последние годы оно фактически сошло на нет. Для справки: Состоянии атмосферного воздуха в промзоне города находятся под контролем станций СКАТ непрерывного мониторинга.
«Победи́т» — предприятие цветной металлургии во Владикавказе (Северная Осетия). Производит продукцию из вольфрама и молибдена (порошки, штабики, прокат), а также рений.
Решение о строительстве завода было принято Министерством цветной металлургии СССР в 1946 году, строительство началось в 1948 году. На выбор место повлияла близость источника сырья (Тырныаузский ГОК в Кабардино-Балкарии), транспортные связи (железнодорожный и автомобильный транспорт), наличие промышленной площадки завода «Электроцинк» и возможность кооперации двух заводов по ряду хозяйственных функций. Во Владикавказе также была учебная и научная база —Северо-Кавказский горно-металлургический институт.
Уже в 1948 году на экспериментальном участке завода вышла первая продукция из твёрдого сплава, который в те годы назывался «победитом». Название сплава дало имя заводу.
Сейчас ОАО «Победит» занимает площадь 39,7 гектаров, на предприятии работает около 1800 человек.
В январе 2009 года производство на «Победите» было полностью остановлено, впоследствии частично восстановлено. Планируется выйти на 80 % результата 2008 года.
Заключение
Во время учебно- ознакомитльной практики мы ознакомились с основами горного производства непосредственно на горных предприятиях, с производственной структурой предприятий, с технологическими процессами производства.
Ознакомились с технологией добычи руды на Садонской обогатительной фабрике: с получением щебеня, песка и.т.д в Михайловском карьере. Также узнали принцип работы Зарамагского ГЭС (Головной каскад) и ход построения второго каскада. Познакомились с горными машинами и составили их экскизы.
Литература
1. Братнов.В.В. и др. Метрология и климатология.Учебное пособие –Карачаевск:Издательсиво Карачаево-Черкесского государственного университета,2005-2007 24 ил.
2. Голик.В.И. «Разработка МПИ» Владикавказ издательство ООО НПКП «Мавр» 2006
3. Голик В.И. Подземная разработка МПИ.Учебное пособие,М.Издательство.Инфра,2013.
4. Горные машины Учебное пособие для ВУЗов М.Издательство.МГУ,2004.
5. Егоров.П.В. Бобёр.Е.А. «Основы горного дела».Москва Издательство МГГУ.2004.
Дата добавления: 2019-02-22; просмотров: 1013; Мы поможем в написании вашей работы! |
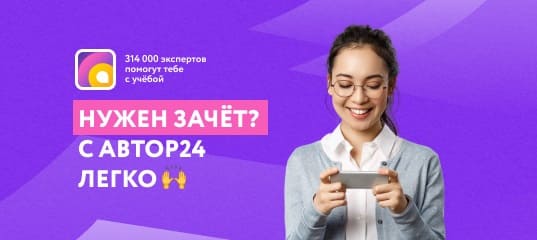
Мы поможем в написании ваших работ!