Перед тем как нарезать резьбу, необходимо подобрать диаметр заготовки под данную резьбу.
Нарезая резьбу плашкой, надо иметь в виду, что при образовании профиля резьбы металл изделия, особенно сталь, медь и др., тянется и изделие увеличивается. Вследствие этого усиливается давление на поверхность плашки, что приводит к нагреву и прилипанию частиц металла, поэтому резьба может получиться рваной.
При выборе диаметра стержня под наружную резьбу следует руководствоваться теми же соображениями, что при выборе отверстий под внутреннюю резьбу. Практика нарезания наружных резьб показывает, что лучшее качество резьбы можно получить в том случае, если диаметр стержня несколько меньше наружного диаметра нарезаемой резьбы. Если диаметр стержня будет меньше требуемого, то резьба получится неполной; если же больше, то плашка или не сможет быть навинчена на стержень и конец стержня будет испорчен, или во время работы зубья плашки вследствие перегрузки могут поломаться, а резьба будет сорвана. Диаметр заготовки должен быть на 0,3-0,4 мм меньше наружного диаметра резьбы.
При нарезании резьбы плашкой стержень закрепляют в тисках так, чтобы выступающий над уровнем губок конец тисков был на 20-25 мм больше длины нарезаемой части. Для обеспечения врезания на верхнем конце стержня запиливается фаска. Затем на стержень накладывают закрепленную в клупп плашку и с небольшим нажимом вращают клупп так, чтобы плашка врезалась примерно на 0,2-0,5 мм. После этого нарезаемую часть стержня смазывают маслом и вращают клупп точно таким же образом, как при работе метчиком, т. е. один-два оборота вправо и пол-оборота влево
|
|
Для предупреждения брака и поломки зубьев необходимо, чтобы плашка заходила на стержень без перекоса.
Проверка нарезанной внутренней резьбы производится резьбовыми калибрами-пробками, а наружной - резьбовыми микрометрами или резьбовыми калибрами-кольцами.
Восстановление детали с применением резьбы.
В ремонтом производстве применяют следующие способы ремонта резьбовых отверстий: -заварка отверстий с последующем нарезанием резьбы; -установка ввертыша; -сверление отверстий и нарезание резьбы на новом месте; -обработка отверстия и нарезание резьбы увеличенного размера; -применение полимерных материалов; -установка резьбовой спиральной вставки. Заварка отверстий с последующим нарезанием резьбы. Во всех случаях при заварке резьбовых отверстий сначала удаляют старую резьбу путем рассверливания. В стальных деталях заварку отверстий производят газовой или электродуговой сваркой в различных защитных средах. Заварку в чугунных деталях производят газовой или электродуговой сваркой -с общим или местным нагревом или в холодном состоянии. В качестве присадочного материала или электродов при горячей заварке применяют чугунные прутки с повышенным содержанием кремния, поршневые кольца из серого чугуна, электроды ЦЧ-4, ОЗЧ-1, МНЧ-1, ЖНБ-1, ПАНЧ-11. Место заварки обрабатывают заподлицо с основным металлом, сверлят отверстие и нарезают резьбу номинального размера. Однако применение сварочных процессов вследствие большой зоны термического влияния приводит к появлению отбела, трещин и короблений детали, изменению структуры основного металла. Прочность восстановленной резьбы ниже новой.. Установка ввертыша может применяться, если конструкция детали позволяет увеличивать отверстия. Этот способ трудоемок, стоимость ремонта высокая. Сверление отверстий и нарезание резьбы на новом месте можно применять только для отдельных групп деталей, у которых расположение резьбовых отверстий может быть изменено без нарушения взаимозаменяемости соединения (ступицы, барабаны, фланцы и cпособ ремонта
|
|
Резьбовых отверстий на ремонтный размер влечет за собой введение увеличенного размера и дополнительной обработки сопряженной детали.
Паяние и лужение.
Паянием называется соединение металлических деталей при помощи расплавленного сплава — припоя. Для паяния используют мягкие припои, температура плавления которых ниже 300°С, и твердые — с температурой плав-ления свыше 700°С.
|
|
Мягкими припоями служат оловянно свинцовистые сплавы, например ПОС50 и ПОСЗО — цифрами указано содержание в них олова в процентах. К твердым припоям относятся медноцинковые сплавы (ПМЦ48—содержание меди в процентах) и серебряные сплавы (ПСр25— содержание серебра в процентах).
Для очистки и предохранения поверхности от окислов применяют различные флюсы. При паянии мягкими припоями флюсами служат хлористый цинк и канифоль, медно-цинковыми припоями—обезвоженная бура, серебряными — фтористый натрий. Нагревать места соединения и расплавлять припой можно паяльниками, паяльными лампой или трубкой и газовой горелкой. Наконечники паяльников изготавливают из меди как наиболее теплопроводного материала.
Перед паянием поверхности металлов очищают напильниками и металлическими щетками, затем нагревают до температуры плавления припоя и при помощи флюса удаляют с поверхности окислы, после чего вводят припой. После охлаждения спаянных деталей обрабатывают полученный шов.
|
|
Паяние алюминия и его сплавов является весьма трудной операцией в связи с тем, что на воздухе, а особенно при нагреве на их поверхности образуется тугоплавкая пленка окислов, препятствующая паянию. Перед паянием поверхности сначала обезжиривают бензином или спиртом, затем зачищают напильником или металли-ческой щеткой. После этого нагретые поверхности облуживают натиранием куском припоя с флюсом. Флюс удаляет окисленную пленку, а припой облуживает соединяемые поверхности. Облуженные поверхности паяют обычным способом. После паяния детали тщательно промывают. При паянии алюминия
припоем может служить сплав из 25% Zn, 40% Sn, 15% А1 и 20% Cd, а также другие сплавы.
В качестве флюса при паянии мягкими припоями применяют смесь из 85% хлористого цинка, 10% хлористого аммония, 5% фтористого натрия; при паянии твердыми припоями — смесь из 10% фтористого калия или натрия, 8% хлористого цинка, 32% хлористого лития и остальное — хлористый калий.
Дата добавления: 2019-02-22; просмотров: 219; Мы поможем в написании вашей работы! |
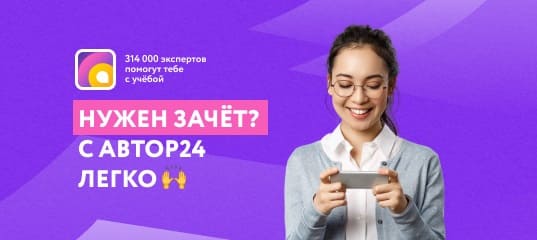
Мы поможем в написании ваших работ!