Дисперсионно-упрочненные композиционные материалы.
В отличие от волокнистых композиционных материалов в дисперсионно-упрочненных композиционных материалах матрица является основным элементом, несущим нагрузку, а дисперсные частицы тормозят движение в ней дислокаций. Высокая прочность достигается при размере частиц 10-500 нм при среднем расстоянии между ними 100-500 нм и равномерном распределении их в матрице. Прочность и жаропрочность в зависимости от объемного содержания упрочняющих фаз не подчиняется закону аддитивности. Оптимальное содержание второй фазы для различных металлов неодинаково, но обычно не превышает 5-10 объёмных %.
Использование в качестве упрочняющих фаз стабильных тугоплавких соединений (оксиды тория, гафния, иттрия, сложные соединения оксидов и редкоземельных металлов), не растворяющихся в матричном металле, позволяет сохранить высокую прочность материала от 0,9 до 0,95 температуры плавления. В связи с этим такие материалы чаще применяются как жаропрочные. Дисперсно-упрочненные композиционные материалы могут быть получены на основе большинства применяемых в технике металлов и сплавов.
Наиболее широко используют сплавы на основе алюминия — САП (спеченный алюминиевый порошок). САП состоит из алюминиевых дисперсных чешуек Al2O3эффективно тормозящих движение дислокаций и тем самым повышающих прочность сплава. Плотность этих материалов равна плотности алюминия, они не уступают ему по коррозионной стойкости и даже могут заменять титан и коррозионностойкие стали при работе в интервале температур 250-500 °С. По длительной прочности они превосходят деформируемые алюминиевые сплавы.
|
|
Композиционные материалы с неметаллической матрицей.
В качестве неметаллических матриц используют полимерные, углеродные и керамические материалы. Из полимерных матриц наибольше распространение получили эпоксидная, фенолформальдегидная и полиамидная. Угольные матрицы, коксованные или пироуглеродные, получают из синтетических полимеров, подвергнутых пиролизу. Матрица связывает композицию, придавая ей форму. Упрочнителями служат волокна: стеклянные, углеродные, борные, органические, на основе нитевидных кристаллов (оксидов, карбидов, боридов, нитридов и др.), а также металлические (проволоки), обладающие высокой прочностью и жесткостью.
Композиты, армированные однотипными волокнами, получили названия по упрочняющему волокну. Так, композицию, содержащую наполнитель в виде длинных стекловолокон, располагающихся ориентировано отдельными прядями, называют ориентированным стекловолокнитом. Неориентированные стекловолокниты содержат в качестве наполнителя короткое волокно. В том случае, если упрочнителем является стеклоткань - стеклотекстолитом. Композиционный материал, содержащий углеродное волокно, называют углеволокнитом, борное волокно - бороволокнитом, органическое волокно - органоволокнитом (органитом).
|
|
Композиционные материалы с полимерной матрицей обнаруживают целый ряд достоинств, среди которых следует назвать высокие удельные прочностные и упругие характеристики, стойкость к воздействию агрессивных сред, хорошие антифрикционные и фрикционные свойства наряду с высокими теплозащитными и амортизационными свойствами. Вместе с тем пластики имеют и недостатки: низкую прочность и жесткость при сжатии и сдвиге, снижение прочности при повышении температуры до 100 – 200 °C, изменение физико-механических характеристик при старении и под воздействием климатических факторов.
В настоящее время пластики получают все большее, интенсивное распространение по причине простоты, технологичности и дешевизны производства из них деталей.
Изделия из композиционных материалов с полимерной матрицей стараются получать одновременно с материалом. Несмотря на сравнительно большую трудоемкость, в этом случае удается наиболее полно реализовать преимущества композиции и существенно снизить стоимость детали.
|
|
Свойства композиционных материалов зависят от состава компонентов, их сочетания, количественного соотношения и прочности связи между ними. Армирующие материалы могут быть в виде волокон, жгутов, нитей, лент, многослойных тканей.
Содержание упрочнителя в ориентированных материалах составляет 60 - 80 объёмных %, в неориентированных (с дискретными волокнами и нитевидными кристаллами) – 20 - 30 объёмных %. Чем выше прочность волокон, тем выше прочность и жесткость композиционного материала. Свойства матрицы определяют прочность и жесткость композиции при сдвиге и сжатии, и сопротивление усталостному разрушению.
В слоистых материалах волокна, нити, ленты, пропитанные связующим, укладываются параллельно друг другу в плоскости. Плоскостные слои собираются в пластины. Свойства получаются анизотропными. Для работы материала в изделии важно учитывать направление действующих нагрузок. Можно создавать материалы, как с изотропными, так и с анизотропными свойствами. Можно укладывать волокна под разными углами, варьируя свойства композиционных материалов. От порядка укладки слоев по толщине пакета зависят изгибные и крутильные жесткости материала.
|
|
Применяется укладка упрочнителей из трех, четырех и более нитей. Наибольшее применение имеет структура из трех взаимно перпендикулярных нитей. Упрочнители могут располагаться в осевом, радиальном и окружном направлениях.
Трехмерные материалы могут быть любой толщины в виде блоков, цилиндров. Объемные ткани увеличивают прочность на отрыв и сопротивление сдвигу по сравнению со слоистыми. Система из четырех нитей строится путем расположения упрочнителя по диагоналям куба. Структура из четырех нитей равновесна, имеет повышенную жесткость при сдвиге в главных плоскостях. Однако создание четырехнаправленных материалов сложнее, чем трехнаправленных.
Углепласты.
Углепласты (карбоволокниты, карбон от «carbon», «carbone» — углерод) - полимерные композиционные материалы, состоящие из переплетённых нитей углеродного волокна, расположенных в матрице из полимерных (например, эпоксидных) смол. Материалы на основе углеродных волокон и углеродной матрицы называют углерод-углеродными материалами. В производстве углепластов применяют как термореактивные синтетические смолы (эпоксидные, фенольные, полиэфирные, полиимидные и др.), так и термопластичные (полиамиды, поликарбонаты, полисульфоны, полиэфиры и др.). Используют следующие виды наполнителей: углеродные нити, жгуты, ленты, ткани, маты, короткие рубленые волокна. Повышенные характеристики имеют углепластики на основе непрерывных высокопрочных и высокомодульных (модуль упругости выше 150 ГПа) углеродных волокон. Углепластики характеризуются низкой плотностью, высокой прочностью, высоким модулем упругости, статической и динамической выносливостью, вибропрочностью, повышенной химической и радиационной стойкостью, теплопроводностью, близким к нулю коэффициентом линейного расширения.
Впервые идею об углеродных волокнах высказал Эдисон в 1880 году, предложив использовать их в качестве нити накаливания световых ламп. Вскоре с приходом вольфрамовой проволоки идея была забыта. В середине двадцатого века интерес к углепластикам проявился вновь. Искались новые материалы, способные выдержать многотысячную температуру ракетных двигателей. Впервые карбон был использован в программе NASA, при постройке космических кораблей. В 1967 году карбон появился в свободной продаже в Англии. В 1981 г. Джон Барнард впервые использовал карбоновое волокно при создании моноблока болидов формулы 1. С триумфом ворвавшись в автоспорт, углепластик оказался конкурентно способным материалом от сложнейших космических систем до бытовых удилищ.
Основная составляющая часть углепластика — это нити углерода. Такие нити очень тонкие (примерно 0.005-0.010 мм в диаметре[1]), сломать их очень просто, а вот порвать достаточно трудно. Из этих нитей сплетаются ткани. Они могут иметь разный рисунок плетения (ёлочка, рогожа и др.)
Сочетаются нити различных материалов, например нити углепластика и резины, углепластика и полимера полипарафенилен-терефталамид, торговая марка кевлар, нити углепластика и стекловолокон. Нити переплетают между собой под определенным углом, образуя слои, причем, в каждом слое карбона углы переплетения разные. Это делается для компенсации ярко выраженных разнонаправленных свойств углепластиков. В листе карбона на 1 мм толщины приходится 3-4 таких слоя. Вся эта конструкция скрепляется эпоксидными смолами и другими видами смол. Присутствие в углепластиках армирующих компонентов и одного связующего благоприятно сказывается на характеристиках карбонового волокна: высокая прочность, износостойкость, жесткость.
Высокая энергия связи С-С углеродных волокон позволяет им сохранять прочность при очень высоких температурах (в нейтральной и восстановительных средах до 2200°С), а также при пониженных температурах. От окисления поверхности волокна предохраняют защитными покрытиями (пиролитическими). В отличие от стеклянных волокон карбоволокна плохо смачиваются связующими (низкая поверхностная энергия), поэтому их подвергают травлению. Применяется вискеризация нитевидных кристаллов TiO2, AlN и Si3Ni4, что дает увеличение межслойной жесткости в 3 раза и прочности в 2,8 раза. Применяются пространственно армированные структуры. Карбостекловолокниты содержат наряду с угольными стеклянные волокна, что удешевляет материал.
Карбоволокниты отличаются высоким статическим и динамическим сопротивлением усталости, сохраняют это свойство при нормальной и очень низкой температуре; высокая теплопроводность волокна предотвращает саморазогрев материала за счет внутреннего трения. Теплопроводность углепластиков в 1,5-2 раза выше, чем теплопроводность стеклопластиков. Углепластики стойки к воздействию воды и химических реагентов. Для углепластиков с ориентированным (однонаправленным, перекрестным или пространственно армированным) расположением высокомодульных волокон коэф. теплопроводности 0,75-0,90 Вт/(м·К), коэф. температуропроводности (5-8)·10-7 м2/с, уд. теплоемкость 0,8-1,5 кДж/(кг·К). Температурный коэффициент линейного расширения однонаправленного углепластика вдоль волокон (-0,5-0,5)·10-6 К-1. Электропроводящие свойства углепластиков такие же, как и у исходных углеродных волокон. Углепластик имеет сравнительно невысокую плотность от 1.4 до 1.8 г/cм2. Диапазоны прочности при растяжении составляют 500 – 3000 МПа. Наиболее прочны на растяжение углепластики с одноосно направленными нитями.
Углеродные волокна изготавливают несколькими способами: выращивание кристаллов в световой дуге, химическое осаждение углерода, создание органических волокон в специальной печи автоклаве. Последний способ получил наибольшее распространение.
Исходным сырьём являются волокна полиакрилонитрила или вискозы, которые окисляют на воздухе в течение 24 часов, при температуре 250 градусов. Образующиеся волокна, переносят в инертный газ, где производится последующий процесс карбонизации - высокотемпературный длительный нагрев в пределах от 800 до 1500 градусов. При нагреве убывают летучие соединения, а в самих волокнах образуются новые связи, материал обугливается. Далее следует графитизация (насыщение углеродом) при температурах 1600-3000 градусов, так же в инертной среде. Из образовавшегося материала изготавливают нити, которые переплетают с другими армирующими нитями в слои.
Помимо обычных органических волокон, для получения нитей углерода могут быть использованы специальные волокна из фенольных смол, лигнина, каменноугольных и нефтяных пеков. Кроме того, детали из карбона превосходят по прочности детали из стекловолокна, но, при этом, обходятся значительно дороже аналогичных деталей из стекловолокна.
Изделия из углепластика формируются двумя основными способами:
1. "мокрый" способ - самый распространенный. Волокна укладываются в форму, пропитываются эпоксидной смолой, излишки смолы удаляются в вакууме или под давлением, а оставшаяся смола полимеризуется, само карбоновое изделие формируется под давлением.
2. "сухой" метод является более сложным процессом. Исходные углепластиковые заготовки, изготовленные под давлением, которые формуют в процессе создания. Углепластик, изготовленный сухим способом, намного прочнее и легче мокрого.
Углепластик, полученный сухим методом, имеет ребристую поверхность. Изделия, изготовленные мокрым методом совсем гладкие на ощупь.
Углепластик разделяется на сорта, зависящие от времени прогрева волокон в автоклаве.
Рис. 9.3. Фото болида Формулы 1, в конструкции которых используются детали из углепластика.
Преимущества углепластиков:
1. углеродные волокна карбона имеют механические характеристики на растяжение, соизмеримые с параметрами сталей; характеристики на сжатие значительно ниже, создание углепластикового волокна частично решают проблему;
2. плотность карбона составляет 1.4 – 1.8 г/см3, в сравнение плотность стали в среднем равна 7.7 г/см3, алюминия 2.72 г/см3;
3. карбон, собранный из углерода и кевлара (разновидность резины), хоть и имеет более высокую плотность, а при ударах трескается, крошится, но не разбивается на части;
4. карбоновое волокно выдерживает температуру воздействия до 1600К, в восстановительной атмосфере до 2200К;
5. карбон является хорошим энергопоглотителем (его можно увидеть вместо крыши двигателя).
6. неокрашенный карбон стильно и красиво выглядит.
Недостатки углепластиков:
1. стоимость карбона довольно высока, хотя постепенно карбон дешевеет;
2. высокая сложность ремонта карбона или невозможность восстановления в случае повреждения. Карбон разрушается от «точечных» ударов. Например, капот из карбона может превратиться в решето после частого попадания мелких камней. В отличие от металлических деталей или деталей из стеклоткани, восстановить первоначальный вид карбоновых деталей невозможно. Поэтому, после даже незначительного повреждения всю деталь придется менять целиком;
3. карбон обладает электропроводностью,
4. со временем карбон становится темно-желтоватого оттенка на солнце, карбон покрывают специальным лаком, а иногда и вовсе красят;
5. карбон, составленный из углепластика и резины, может выдержать мощнейшие ударные нагрузки, но если во время столкновения он не выдержит, то расколется на множество острых кусков;
6. карбон разрушается от точечных ударов;
7. в отличие от металла, карбон легче и, потому, может легко оторваться на прогулке с ветерком, потому карбоновым деталям требуется основательное крепление;
8. длительное время изготовления карбоновых деталей на заказ;
9. в местах контакта карбона с металлом в соленой среде металл быстро коррозирует (например, зимой, когда дороги посыпаются разной химией с солью), проблема устраняется стеклопластиковыми вставками между карбоном и металлом, которые встраиваются в углепластик.
Несмотря на недостатки карбона, его плюсы с лихвой перекрывают любые недостатки.
Углепластики нашли своё место среди современных материалов. Они используются как в массовых простых изделиях (удочки) так и в сложнейших технических аппаратах (космические корабли, болиды Формулы 1). Области и изделия использования углепластиков следующее:
1. ракетно-космическая техника;
2. авиатехника (самолётостроение, вертолётостроение);
3. судостроение (корабли, спортивное судостроение);
4. автомобилестроение (спортивные автомобили, мотоциклы, болиды Формулы 1);
5. наука и исследования;
6. усиление железобетонных конструкций;
7. спортивный инвентарь (роликовые коньки, велосипеды, футбольные бутсы, хоккейные клюшки, лыжный спорт (лыжи, палки, ботинки), ракетки для тенниса, основания для настольного тенниса, лезвия коньков, стрелы, оборудование виндсерфинга, моноласты, вёсла);
8. медицинская техника;
9. рыболовные снасти (удилища);
10. бытовая техника (отделка корпусов телефонов, ноутбуков);
11. моделизм;
12. струны музыкальных инструментов;
13. изготовление индивидуальных супинаторов (особенно для спорта).
Углепластик в тюнинге. Карбон обожают за его привлекательный вид, хорошие характеристики. Сейчас можно без особого труда найти: бумажники, кроссовки, разную одежду с карбоновыми вставками или целиком сделанные из карбона шлемы, ручки. И необязательно тот карбон настоящий. Изделия под карбон выполняют свою «карбоновую» задачу – притягивают восторженные взгляды.
В автомобилестроении из карбона выполняют: капоты, обвесы, спойлеры, крышу, днище, сиденья, приборные панели и все это радует глаз. Иногда на выставках можно встретить закарбоненные авто по максимуму (рис. 9.4.).
Рис. 9.4. Кузов автомобиля, изготовленный из углепластика.
Бороволокниты.
Бороволокниты представляют собой композиции из полимерного связующего и упрочнителя - борных волокон.
Бороволокниты отличаются высокой прочностью при сжатии, сдвиге и срезе, низкой ползучестью, высокой твердостью, теплопроводностью и электропроводимостью. Ячеистая микроструктура борных волокон обеспечивает высокую прочность при сдвиге на границе раздела с матрицей.
Помимо непрерывного борного волокна применяют комплексные боростеклониты, в которых несколько параллельных борных волокон оплетаются стеклонитью, придающей формоустойчивость. Применение боростеклонитей облегчает технологический процесс изготовления материала.
В качестве матриц для получения бороволокнитов используют модифицированные эпоксидные и полиамидные связующие.
Бороволокниты обладают высокими сопротивлениями усталости, они стойки к воздействию радиации, воды, органических растворителей и горюче-смазочных материалов.
Поскольку борные волокна являются полупроводниками, то бороволокниты обладают повышенной теплопроводностью и электропроводимостью.
Изделия из бороволокнитов применяют в авиационной и космической технике (профили панели, роторы и лопатки компрессоров, лопасти винтов и трансмиссионные валы вертолетов и т. д.).
Органоволокниты.
Органоволокнитыпредставляют собой композиционные материалы, состоящие из полимерного связующего и упрочнителей (наполнителей) в виде синтетических волокон. Такие материалы обладают малой массой, сравнительно высокой удельной прочностью и жесткостью, стабильны при действии знакопеременных нагрузок и резкой смене температуры. Для синтетических волокон потери прочности при текстильной переработке небольшие; они малочувствительны к повреждениям.
В органоволокнитах происходит диффузия компонентов связующего в волокно и химическое взаимодействие между ними. Структура материала бездефектна. Пористость не превышает 1 – 3 % (в других материалах 10 – 20 %). Отсюда стабильность механических свойств органоволокнитов при резком перепаде температур, действии ударных и циклических нагрузок. Недостатком этих материалов является сравнительно низкая прочность при сжатии и высокая ползучесть (особенно для эластичных волокон). Слабые межмолекулярные связи в волокнах-упрочнителях являются причиной низкой прочности и жесткости органоволокнитов при сжатии.
Предельная деформация при сжатии определяется искривлением волокон, а не их разрушением.
Органоволокниты устойчивы в агрессивных средах и во влажном тропическом климате; диэлектрические свойства высокие, а теплопроводность низкая. Большинство органоволокнитов может длительно работать при температуре 100 - 150 °С.
В комбинированных материалах наряду с синтетическими волокнами применяют минеральные (стеклянные, карбоволокна и бороволокна). Такие материалы обладают большей прочностью и жесткостью.
Органоволокниты применяются в качестве изоляционного и конструкционного материала в электропромышленности, авиационной технике, автостроении; из них изготавливают трубы, емкости для реактивов, покрытия корпусов судов и др.
Дата добавления: 2019-02-22; просмотров: 730; Мы поможем в написании вашей работы! |
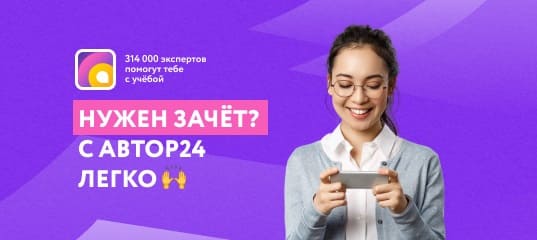
Мы поможем в написании ваших работ!