Материалы для износостойкой наплавки.
Методы легирования наплавленного металла.
Нужные свойства наплавленного слоя обычно получают легированием, т. е. введением в его состав легирующих элементов. Существует много методов легирования. Методы легирования и способы наплавки взаимосвязаны – выбранный способ наплавки, как правило, диктует рациональный метод легирования, и, наоборот, эффективный метод легирования требует применения соответствующего способа наплавки. С другой стороны, основными признаками, по которым следует оценивать метод легирования, являются: точность (надежность) получения заданного химического состава наплавленного металла при возможных колебаниях режимов наплавки, однородность состава по объему наплавленного слоя, экономичность и удобство применения метода легирования. Что касается экономичности метода легирования, то здесь необходимо учитывать целесообразность применения тех или иных легирующих элементов для наплавки данной детали и потери этих легирующих элементов при выборе метода легирования.
Легировать сварочную ванну можно за счет обменных реакций между металлом и шлаком (окислами), через газовую среду и путем введения металлических добавок. Примером легирования за счет обменных реакций являются известные кремне- и марганцевовосстановительные процессы при наплавке под флюсами АН-348-А, ОСЦ-45, АН-60 и др. Легирование посредством газовой фазы имеет место при дуговой наплавке плавящимся электродом в атмосфере воздуха или азота, когда наплавленный металл содержит заметные количества азота. Благодаря этому повышается износостойкость хромистых сплавов или регулируется количество аустенитной фазы.
|
|
Однако эти два процесса легирования для износостойкой наплавки применяются редко, так как они не могут обеспечить необходимый уровень содержания легирующих элементов. Поэтому наибольшее распространение получило легирование путем введения в сварочную ванну металлических сплавов, чистых металлов, карбидов и др.
При ручной наплавке штучными электродами легирование осуществляется введением легирующих элементов в покрытие электрода или в электродный стержень; также применяют комбинированное легирование, когда легирующие элементы вводят и в стержень, и в покрытие.
При электродуговой наплавке под флюсом применяют следующие методы легирования:
1) применение легированной электродной проволоки или ленты (в том числе и металлокерамической ленты) и плавленого флюса;
2) присадка легирующих элементов через проволоку или ленту (порошковую проволоку или ленту, проволоку с армированным легирующим покрытием и др.), плавленый флюс;
|
|
3) использование низкоуглеродистой проволоки или ленты и легирующего флюса (керамического флюса, механической примеси ферросплавов к флюсу);
4) наплавка по неподвижной присадке в виде прутка, ленты, порошка, пасты с полным расплавлением присадки.
Ни один из этих методов не встречается в чистом виде: электродный материал всегда в какой-то степени взаимодействует со шлаком и часть элементов переходит в наплавленный металл из флюса. При использовании легирующего флюса часть легирующих элементов может вноситься электродным материалом.
При легировании через проволоку и наплавке под химически активными флюсами АН-348А, ОСЦ-45, АН-60 увеличение относительной массы шлака, происходящее при повышении напряжения дуги или уменьшении силы тока, сопровождается окислением легирующих элементов и легированием сварочной ванны кремнием и марганцем из флюса. В результате при изменении режимов наплавки изменяется и химический состав наплавленного металла.
При наплавке под менее активными флюсами влияние относительной массы шлака на процессы окисления и легирования уменьшаются, и влияние режима на химический состав наплавленного металла тем меньше, чем меньше окислительная способность применяемого флюса.
|
|
Продолжительность взаимодействия капли расплавленного металла с окружающей средой, и относительная масса шлака уменьшаются при увеличении силы сварочного тока и скорости наплавки. Поэтому изменение химического состава наплавленного металла в зависимости от изменения режима наплавки меньше в области больших токов и больших скоростей наплавки. Эти процессы относятся к верхним слоям наплавки, когда влияние основного металла и его доля в наплавленном объеме невелики.
При легировании наплавленного металла, когда основным источником поступления легирующих элементов (в виде металлических добавок) является флюс, увеличение напряжения дуги и уменьшение силы тока приводит к тому, что относительная масса шлака возрастает и содержание легирующих элементов в капле остается примерно постоянным. При наплавке под легирующим флюсом электродной лентой сила тока и напряжение дуги влияют на относительную массу шлака незначительно, поэтому обеспечивается более стабильный химический состав наплавленного металла, чем при наплавке проволочным электродом. Потери легирующих элементов в шлаковой корке существенно возрастают при их высоком содержании во флюсе, поэтому нецелесообразно применение легирующих флюсов (керамических, флюсов-смесей) для получения высоколегированного наплавленного металла.
|
|
При наплавке плавящимся электродом по неподвижной легирующей присадке в виде порошка, пасты и т.п. количество присадки выбирают так, чтобы она вся переплавлялась дугой. Наплавку обычно производят под плавленым флюсом низкоуглеродистой проволокой. Благодаря интенсивному перемешиванию металла в сварочной ванне, присадка, введенная указанным путем, распределяется равномерно по сечению наплавленного слоя. При равномерном распределении присадки по длине наплавляемого валика можно получить наплавленный металл заданного состава. Если на деталь нанесено заданное количество легирующего материала, то химический состав наплавленного металла в значительной мере зависит от скорости подачи электродной проволоки (силы тока) и скорости наплавки. Кроме того, состав наплавленного металла зависит от напряжения дуги, что обусловлено изменением относительной массы шлака. Поэтому заданный химический состав наплавленного металла можно получить в весьма ограниченном диапазоне режимов.
Важной характеристикой процесса легирования является однородность химического состава наплавленного металла по объему, которая обусловлена, в первую очередь, равномерностью распределения легирующих элементов в самом электродном металле. Так, при исследовании распределения легирующих элементов в наплавленном слое установлена разная степень однородности состава металла, наплавленного под флюсом холоднокатанной, металлокерамической и порошковой лентами. Металлокерамическая и холоднокатанная ленты дают наплавленный металл примерно с одинаковой однородностью.
При выборе способа легирования необходимо учитывать не только стабильность и однородность состава металла при наплавке, но и экономические показатели. Например, порошковая и тем более металлокерамическая лента дороже низкоуглеродистой и среднелегированной проволоки сплошного сечения. Применение этих дорогостоящих материалов оправдывается в тех случаях, если необходимо получить легированный наплавленный металл со стабильным химическим составом. При наплавке по слою гранулированного порошка используют сравнительно недорогие материалы, но этот метод малопригоден для деталей сложной формы и неприменим в тех случаях, когда требуется большая стабильность состава наплавленного металла.
Для решения многих задач получения легированного наплавленного металла особенно перспективной является плазменная наплавка порошковыми материалами, т. к. она обеспечивает получение стабильного состава наплавленного металла даже при однослойной наплавке благодаря возможности обеспечения минимального проплавления основного металла и его перемешивания с наплавленным.
Материалы для износостойкой наплавки.
Выбор типа износостойкого сплава основывают на следующих характеристиках: свариваемости с основным металлом, служебных свойствах, технологичности при механической обработке наплавленных деталей, возможности термической обработки биметаллического соединения и экономических показателей сплава. Выбор марки наплавочного материала производится в соответствии с условиями работы упрочняемых деталей и метода наплавки.
Для характеристики свойств наплавленного металла данных только о химическом составе и твердости недостаточно. В зависимости от скорости охлаждения, режима термообработки и, наконец, от величины и ориентации первичных кристаллитов по отношению к разрушающим нагрузкам наплавленный металл одного и того же химического состава обладает разной работоспособностью.
Перлитные материалы. Состав перлитных материалов (Нп-25, Нп-20ХГСА,
Нп-90ХГСА и др.) обеспечивает, в зависимости от скорости охлаждения наплавки, перлитно-сорбитную структуру. Твердость наплавленного металла находится на уровне 25–40 HRC. Износостойкость наплавленного слоя значительно уступает мартенситной структуре, поэтому сопротивление износу при трении невысоко. Наплавочные материалы этого класса часто применяют для создания «подслоя», на который наплавляют слой повышенной твердости.
Мартенситные материалы. Данные материалы характеризуются образованием мартенситной структуры сразу после наплавки. Обладая повышенной твердостью, стойкостью при абразивном износе, наплавка этого типа характеризуется пониженными пластическими свойствами, хрупкостью, склонностью к образованию холодных трещин. При работе в условиях ударного нагружения возможны отколы по основному металлу или в зоне сплавления.
Низколегированные мартенситные материалы (Нп-40Х3Г2МФ, Нп-40Х2Г2М, НП-50Х6ФМС и др.) — материалы, процент легирующих элементов в которых относительно невысок, обеспечивают в наплавке мартенситно-бейнитные структуры и отличаются сравнительно невысокой твердостью (45–50 HRC ). Свойства наплавки повышаются в основном увеличением содержания в ней углерода и хрома, что приводит к соответствующему увеличению доли мартенситной составляющей.
Значительно большей твердостью характеризуются борсодержащие мартенситные наплавки (ЛС-У10Х7ГР1, ПЛУ-25Х25Г3Ф2РН, ПП-АН125, ПП-АН170), в структуре которых по границам высокоуглеродистого мартенсита расположены твердые карбиды и бориды. Материал отлично сопротивляется абразивному износу, задирам, но из-за повышенной хрупкости не может быть рекомендован для работы в условиях динамических нагрузок. Наплавка обладает повышенной склонностью к образованию горячих и холодных трещин, поэтому ведут ее, как правило, с подогревом и применением одного или нескольких подслоев. Отпуск в результате наложения нескольких слоев практически не снижает твердости.
Для обеспечения повышенной сопротивляемости к задирам применяют наплавочные материалы, содержащие в своей структуре наряду с мартенситом значительное количество аустенитной фазы (Нп-50Х6ФМС, Нп-30Х5).
Мартенситные хромистые материалы типа Нп-30Х13 после наплавки имеют в основном мартенситную структуру с небольшим содержанием феррита. Износостойкость наплавки повышается с увеличением углерода. Низкоуглеродистые наплавки, помимо достаточной износостойкости, обладают повышенной жаростойкостью и антикоррозионными свойствами. Увеличение количества углерода (Э-120Х12Г2СФ) приводит к появлению в структуре ледебуритной составляющей, что резко повышает износостойкость наплавки и делает ее пригодной для наплавки режущих кромок инструмента.
Высокомарганцовистые аустенитные материалы. Материалы типа Нп-Г12А при резком охлаждении от температуры 1000 °С образуют аустенитную структуру с повышенной вязкостью и пластичностью. Длительная выдержка при температурах выше 400 °С приводит к выделению по границам зерен карбидов и вторичной перлитной фазы, приводящих к снижению пластичности. Уменьшение содержания углерода снижает вероятность образования вторичных фаз. В зоне сплавления основного низкоуглеродистого или низколегированного металла и наплавки возможно образование хрупкой мартенситной прослойки и появление трещин. Для избежания этого рекомендуется применение промежуточного слоя из хромистомарганцовистой наплавки типа Нп-30Х10Г10Т.
Высокохромистые материалы. Высокохромистые материалы на основе железа типа Э-300Х28НЧСЧ, Э-320Х25С2ГР позволяют получать структуру, матрица которой состоит из аустенита с вкраплениями мелкодисперсных частиц карбидов В и Сr, придающих наплавке высокую твердость. Поскольку твердость в основном определяется количеством карбидов, она практически не изменяется в процессе нагрева и не зависит от скорости охлаждения. Тем не менее, наплавку следует производить при предварительном подогреве деталей до температур 400–500 °С с целью избежания появления горячих трещин, а также уменьшать скорость охлаждения.
Добавка Nb, W, Мо и других карбидообразователей способствует большему повышению твердости и появлению способности наплавки к вторичному твердению: износостойкость при этом повышается.
Коррозионностойкие материалы.Обычно наплавка проводится на изделиях из хромистых или хромоникелевых аустенитных сталей. Ферритная коррозионностойкая наплавка обеспечивается при высоком содержании Сr и весьма низком С. Наплавки этого типа в отношении к общей коррозии существенно уступают аустенитным, но превосходят последние по стойкости к коррозионному растрескиванию под напряжением.
Технологические свойства аустенитной наплавки достаточно высоки. Однако при наплавке на стали мартенситного класса следует опасаться появления холодных трещин в зоне сплавления. Рекомендуется применять предварительный подогрев до относительно невысоких температур — 100–150 °С. Превышение этой температуры может привести к замедленному охлаждению наплавки и ее охрупчиванию.
Виды наплавочных материалов.
Покрытые электроды. Электроды для ручной дуговой наплавки изготавливают по ГОСТ 10051–75. В качестве стержня обычно используют проволоку диаметром от 3 до 5 мм, реже до 8 мм.
ГОСТ 10051–75 устанавливает 44 типа наплавочных электродов. Значительное количество электродов для наплавки слоев с особыми свойствами изготавливается по отраслевым ТУ. Проверка твердости наплавленного металла производится по ГОСТ 9466–75 и ГОСТ 9013–59, а химического состава и остальных свойств — по ГОСТ 9466–75.
Твердость, получаемая при наплавке, характеризуется индексами, входящими в обозначение марки электрода и указывающими ее величину по Бринеллю и Роквеллу, а следующие цифры (1 или 2) указывают соответственно, в каком состоянии она измерялась; непосредственно после наплавки — 1 или после последующей термообработки — 2.
Так, например, в электродах марки ОЗН-350Ц 400/41-1 индексы характеризуют: 400 — твердость по Бриннеллю, 41 — по Роквеллу, 1 — характеристики определялись непосредственно после наплавки.
Флюсы. От свойства флюса зависят устойчивость горения электрической дуги, плотность наплавленного металла, отделимость шлаковой корки, интенсивность выделения вредных газов. Капли расплавленного металла перемешиваются с расплавленным флюсом, а затем отделяются от него. При этом происходит химическое взаимодействие: часть углерода, хрома, ванадия и других элементов, содержащихся в металле, окисляется и переходит в шлак. Если флюс содержит большое количество марганца и кремния, то эти элементы могут восстанавливаться и переходить из шлака в металл. Таким образом, состав флюса оказывает большое влияние на состав наплавленного металла. Для механизированной наплавки применяют флюсы трех типов: плавленые, керамические (неплавленные) и флюсы-смеси.
Плавленые флюсы можно разделить на четыре группы:
1. Высококремнистые марганцевые флюсы. К их числу относятся флюсы марок АН-348А, АН-15, ОСЦ-45, АН-60. Их обычно применяют для наплавки низко- и среднеуглеродистых, а также низколегированных сталей (сталей типов А и В по классификации МИС). Флюсы этой группы обеспечивают хорошее формирование наплавленных валиков, малую склонность к образованию пор и удовлетворительную отделимость шлаковой корки, если металл не содержит ванадия, вольфрама и больших количеств хрома (эти элементы вызывают прилипание шлаковой корки). В процессе наплавки под этими флюсами происходит частичное окисление углерода и легирование наплавленного металла марганцем и кремнием. Из рассматриваемых флюсов наилучшее качество формирования наплавленных валиков отмечается при наплавке под пемзовидным флюсом АН-60, поэтому его рекомендуется применять при наплавке электродной лентой, а также проволокой при больших скоростях.
2. Низкокремнистые безмарганцевые флюсы. Низкокремнистые флюсы содержат кремнезема SiO2 менее 35 %. Безмарганцевые флюсы содержат менее 1 % MnO. К их числу относятся флюсы АН-20, АН-28, 48-ОФ-6, 48-ОФ-10 и др. Их применяют для наплавки средне- и высоколегированных сталей с небольшим содержанием марганца.
Флюс АН-20 наиболее распространен из данной группы, т. к. обеспечивает высокую стабильность дуги, малую склонность к порам, хорошее формирование валиков. Его недостаток — относительно низкая температура плавления и малая вязкость, что затрудняет наплавку тел вращения малого диаметра, а также сравнительно высока активность кремнезема, что приводит в ряде случаев к нежелательному обогащению металла кремнеземом, окислению легирующих элементов и ухудшению отделимости шлаковой корки.
Флюс АН-28 рекомендуется для наплавки высокохромистых чугунов (тип G), он содержит мало кремнезема, поэтому не происходит значительного окисления легирующих элементов, достигается хорошая отделимость шлаковой корки. Недостатком флюса является плохое формирование валиков при содержании в наплавленном слое менее 1 % Si, а также повышенная склонность к порам вследствие низкого содержания SiO2 и CaF2 во флюсе.
Наиболее химически нейтральны флюсы АН-70 и 48-ОФ-6, применяемые для наплавки высоколегированных сплавов с высоким содержанием хрома, вольфрама, ванадия и титана. При наплавке под этими флюсами велика опасность образования пор.
3. Низкокремнистые марганцевые флюсы. Марганцевые флюсы содержат более 1 % MnO. К их числу относятся флюсы АН-26, АН-22 и др. Данные флюсы применяют для наплавки аустенитных хромоникелевых сплавов типа D. Преимуществом флюса АН-26 является хорошее формирование наплавленного валика и малая склонность наплавленного слоя к порам; недостатком — сравнительно высокая окислительная способность, что приводит в ряде случаев к недопустимому снижению содержания титана и хрома в наплавленном слое и к появлению кристаллизационных трещин.
4. Специальные флюсы. К их числу следует отнести ряд флюсов, применяемых для электрошлаковой наплавки АНФ-1П, АН-8, АНФ-14 и АН-25. Например, флюс марки АНФ-1 содержит 92 % CaF2 и 5 % SiO2. Достоинством этих флюсов является высокая электропроводность. Однако технологические свойства этих флюсов, и в первую очередь качество формирования наплавленного валика, неудовлетворительны.
Керамические флюсы позволяют при использовании стандартных и недефицитных проволок получать легированный наплавленный металл повышенной износостойкости. Их приготавливают путем замешивания на жидком стекле смеси тонко размолотых ферросплавов, минералов, металлов и других легирующих элементов. Применяют керамические флюсы марок ЖСИ-5, ЖСИ-6, АНК-18, АНК-19, АНК-40 и др.
При наплавке под легирующим керамическим флюсом возможно опасное изменение химического состава наплавленного металла при изменении режима наплавки. Однако этот недостаток относится в основном к флюсам с высоким содержанием легирующих элементов, поэтому получение высоколегированного слоя целесообразно осуществлять через проволоку. Наплавка же низколегированного сплава возможна и при помощи слаболегирующих флюсов.
Флюс АНК-18 предназначен для механизированной наплавки проволокой Св-08 и Св-08А колес мостовых кранов, опорных катков, роликов и натяжных колес гусеничного хода тракторов, бульдозеров и экскаваторов. Флюс АНК-19 используют для широкослойной наплавки колеблющимся электродом рабочих кромок ножей бульдозеров, скреперов и грейдеров. Оба флюса обеспечивают хорошее формирование наплавленного металла, легкую отделимость шлаковой корки, высокую стойкость наплавленного металла против образования пор и трещин и возможность наплавки на переменном и постоянном токе.
С целью экономии дорогостоящих легирующих элементов разработаны флюсы, содержащие оксиды бора, хрома и других элементов. Одновременно в состав керамического флюса вводятся восстановители — углерод, алюминий, марганец, которые, в основном, и обеспечивают переход легирующих элементов в наплавленный металл. В результате реализации такой технологии удается в среднем в 2,5 раза снизить затраты на наплавку и обеспечить экономию легирующих элементов.
Проволока стальная сварочная. Проволока для наплавки (ГОСТ 2246–70) и проволока стальная наплавочная (ГОСТ 10543–75) для автоматической наплавки под флюсом, в защитных газах, а также для газовой наплавки может изготовляться из стали, выплавленной электрошлаковым (Ш), вакуумно-дуговым (ВД), или вакуумно-индукционным (ВИ) переплавами (табл. 2.14). Обычно для наплавки применяют проволоки диаметром от 0,8 до 6 мм. С целью уменьшения оксидов в металле наплавки проволоки содержат увеличенное количество раскислителей — Mn, Si, Al, Ti.
Порошковая наплавочная проволока. Порошковая проволока (ПП) представляет собой тонкостенную металлическую оболочку, заполненную легирующими и шлакообразующими порошками, стабилизаторами дуги и раскисляющими компонентами. Она позволяет получать наплавку практически любого заданного состава
Наиболее часто применяют ПП диаметром oт 1,6 до 3 мм с использованием дугового процесса в защитных газах, открытой дугой или под флюсом. Ввиду отсутствия общероссийского стандарта на ПП ее изготовляют по техническим условиям.
Наплавочные ленточные электроды. В России ленточные электроды или ленты производятся толщиной от 0,4 до 1 мм при ширине от 20 до 100 мм
Ленты подразделяются на стальные холоднокатаные, порошковые и металлокерамические. Все ленты изготовляются по техническим условиям. Нередко для целей наплавки применяют стандартизованную стальную ленту, предназначенную для других целей.
В последнее время разработана серия порошковых наплавочных лент (ЛП), представляющих собой оболочку из низколегированных или специальных сталей с сердцевиной, заполненной шихтой из легирующих материалов и флюса. Металлокерамическую ленту изготовляют методом спекания порошкообразных компонентов (ЛС), обеспечивая ей необходимые прочностные и пластические свойства.
Ленты применяют преимущественно при автоматической наплавке под флюсом.
Гранулированные порошки. В качестве присадочного материала при плазменной и индукционной наплавке используют гранулированные порошки, изготовленные путем распыления струи жидкого сплава водой или газом высокого давления. Форма частиц сферическая или осколочная. Сфероидизированные порошки отличаются хорошей сыпучестью, не застревают и не зависают в дозирующих устройствах. Для плазменно-порошковой наплавки используют преимущественно сферические порошки с размером частиц 40–300 мкм. Порошки осколочной формы применяют для плазменной наплавки по неподвижной присадке и для индукционной наплавки.
Порошки на основе никеля с хромом и бором обеспечивают получение наплавленного металла типа Qa и используют для износостойкой наплавки. Порошки на основе кобальта позволяют наплавить металл типа N — кобальтовые стеллиты. Порошок ПН-АН30 по своему химическому составу соответствует литым пруткам В3К и может заменять их.
Однако наибольшее распространение при плазменной наплавке нашли самофлюсующиеся наплавочные сплавы системы «Ni-Cr-В-Si». Такие сплавы, как правило, содержат 0,5–1,0 % углерода и 2–5 % железа. Данные сплавы предназначены для работы в условиях интенсивного абразивного изнашивания с умеренными ударными нагрузками, в агрессивных средах или при повышенных температурах (до 700 °С).
Растворимость бора в сплавах на основе никеля не превышает 0,005 %, поэтому большая часть бора идет на образование боридных фаз. Углерод в этих сплавах находится преимущественно в связанном состоянии и образует карбиды хрома. Кремний растворяется в пределах 1,5–5,0 %. В этих пределах кремний не образует самостоятельных фаз, увеличение его содержания свыше 5 % приводит к образованию эвтектики; кроме того кремний увеличивает активность хрома, что способствует образованию боридов, а при наличии углерода – карбидов хрома. Благодаря образованию избыточных твердых фаз повышается твердость и износостойкость сплавов. Кроме того, бор совместно с кремнием в процессе наплавки осуществляет деоксидирование сплава, образуя при этом боросиликатные шлаки, которые обеспечивают защиту сплавов от взаимодействия с атмосферой и придают сплаву свойства самофлюсования.
К достоинствам таких сплавов также следует отнести низкую температуру плавления и широкий интервал температур кристаллизации.
При выборе марки материала следует учитывать, что каждая марка сплава обеспечивает свойства, оптимальные для конкретных условий эксплуатации. Иногда фазы сплава, хорошо сопротивляющиеся изнашиванию в одних условиях, не пригодны для работы в других условиях. Необходимо учитывать не только состав фаз, но и их количественное соотношение в структуре сплава, их форму и расположение. Износостойкость наплавленных сплавов во многом зависит от характера карбидной фазы: ее кристаллографического строения, формы и расположения. Фазовые, структурные и механические свойства сплава зависят в первую очередь от его химического состава.
Прутки для наплавки. Литые прутки для наплавки износостойкого слоя на детали, работающие в условиях интенсивного абразивного изнашивания, ударных нагрузок, повышенных температур или в агрессивных средах, согласно ГОСТ 21449–75 подразделяются на пять марок, и их изготовляют с номинальными диаметрами от 4 до 8 мм и длиной 350–500 мм.
Широкое применение в судостроении, судоремонте и машиностроении находит наплавка прутковыми материалами на основе меди (Сu). В табл. 2.19 приведены основные марки прутковых материалов, выпускаемых по ГОСТ 16130–85.
Шнуровые материалы на основе карбида вольфрама. Для деталей, работающих в условиях интенсивного абразивного изнашивания, применяют шнуровые материалы серии «Сфекорд-HR» диаметром 4,75 и 6,35 мм с размером зерен литого карбида вольфрама в диапазоне от 0,1 до 3,0 мм, причем для конкретных видов изнашивания применяются специальные комбинации мелкозернистого и крупнозернистого карбида вольфрама. Наплавленный слой является композиционным материалом, состоящим из металлической вязкой матрицы на основе никелевого сплава системы Ni-Cr-B-Si с равномерно распределенными в ней зернами литого карбида вольфрама (релита) высокой твердости.
Литой карбид вольфрама — эвтектический сплав W2C-WC — является особо прочным, устойчивым к износу материалом. Применяемый в серии «Сфекорд-HR» литой карбид вольфрама обладает макротвердостью не менее 2000 HV, при этом микротвердость составляет 23000 - 25000 МПа. Содержание карбида вольфрама в наплавленном слое составляет от 40 до 80 % (по массе). Равномерное распределение зерен карбидов в порошковом шнуре обеспечивает наиболее благоприятное их расположение на рабочей поверхности, что приводит к повышению износостойкости наплавленного слоя.
Матрица наплавленного слоя из никелевого сплава обеспечивает хорошее смачивание зерен карбидов, обладает низкой температурой плавления (950-1050° С), имеет высокую текучесть и отличается высокой стойкостью к воздействию кислот, щелочей и других коррозионно-активных сред. Поверхность наплавленного слоя гладкая, с металлическим блеском. Максимальная температура эксплуатации наплавленного слоя – 600° С.
При обработке и использовании материалов, содержащих карбид вольфрама, необходимо учитывать, что их нагрев до температуры свыше 1800 °С приводит к растворению зерен карбида вольфрама в матричном сплаве и структурным изменениям, снижающим твердость покрытия и, соответственно, показатели его износостойкости.
Шнуровые материалы «Сфекорд-HR» получили широкое распространение для наплавки твердого поверхностного слоя при изготовлении и ремонте деталей в нефтехимическом, сельскохозяйственном машиностроении, горнодобывающей, нефтедобывающей промышленности, строительной индустрии и дорожном строительстве. Наплавленные слои из порошковых шнуровых материалов серии «Сфекорд-HR» обеспечивают повышенную долговечность деталей, эксплуатируемых в условиях абразивного изнашивания, коррозии, эрозии при повышенных температурах и воздействии агрессивных сред.
Для наплавки не требуется специального оборудования. Наплавка производится, как правило, с использованием кислородно-ацетиленовых горелок с наконечниками, обеспечивающими расход газов от 700 до 1500 л/ч. При этом применяются те же технологические приемы, что и при наплавке прутковыми материалами и трубчато-зерновым релитом (более подробно см. прил. 1). Для выполнения процесса наплавки возможно использовать оборудование, предназначенное для электродуговой сварки неплавящимся электродом.
Плавленые карбиды вольфрама (релиты). Карбиды вольфрама применяют для особо износостойких наплавок, работающих в условиях абразивного износа с ударными нагрузками. Наплавку производят восстановительным газовым пламенем, плазмой или в индукторах. Наплавленный слой характеризуется высокой твердостью (500–700 HV) и повышенной склонностью к образованию трещин и пор. Релитовые наплавочные материалы изготовляют по ТУ в виде зернового (З) или трубчатозернового (ТЗ) релита (ТУ 48-42-34-70) и ленточного АН-ЛЗ (ТУ 26-02-769-77), каждый из которых может иметь шесть степеней зернистости
Дата добавления: 2019-02-26; просмотров: 698; Мы поможем в написании вашей работы! |
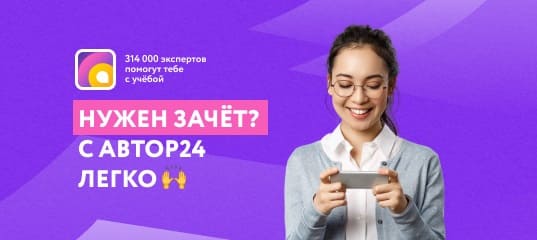
Мы поможем в написании ваших работ!