Условия испытаний по Роквеллу
ФЕДЕРАЛЬНОЕ АГЕНТСТВО ЖЕЛЕЗНОДОРОЖНОГО ТРАНСПОРТА
ФЕДЕРАЛЬНОЕ ГОСУДАРСТВЕННОЕ БЮДЖЕТНОЕ ОБРАЗОВАТЕЛЬНОЕ УЧРЕЖДЕНИЕ ВЫСШЕГО ПРОФЕССИОНАЛЬНОГО ОБРАЗОВАНИЯ
"МОСКОВСКИЙ ГОСУДАРСТВЕННЫЙ УНИВЕРСИТЕТ
ПУТЕЙ СООБЩЕНИЯ»
МГУПС (МИИТ)
Одобрено кафедрой: «Строительная механика,
Машины и оборудование»
Руководство к выполнению лабораторных работ с методическими указаниями
по дисциплине:
МАТЕРИАЛОВЕДЕНИЕ. ТЕХНОЛОГИЯ
КОНСТРУКЦИОННЫХ МАТЕРИАЛОВ
Для студентов 3-го курса
Специальность: 271501.65 – «Строительство железных дорог,
Мостов и тоннелей»
Москва 2014 г.
Руководство к выполнению лабораторных работ по дисциплине. «Материаловедение. Технология конструкционных материалов» с методическими указаниями составлено в соответствии с Государственным образовательным стандартом профессионального высшего образования, в соответствии государственными требованиями к минимуму содержания и уровню подготовки по специальности 271501.65 – «Строительство железных дорог, мостов и тоннелей» для студентов 3-го курса.
Составитель д.т.н., профессор Нисаев И.П.
ЛАБОРАТОРНАЯ РАБОТА № 1
ИССЛЕДОВАНИЕ МИКРОСТРУКТУРЫ ОТОЖЖЕННОЙ
СТАЛИ И ЧУГУНОВ. ОПРЕДЕЛЕНИЕ МАРКИ СТАЛИ.
|
|
ЗАДАЧИ РАБОТЫ
1.Закрепить теоретические положения курса по микроструктуре стали в отожженном состоянии и чугуна на основе диаграммы железо – углерод.
2.Изучить основы микроанализа.
3.Экспериментально подтвердить коренные качественные изменения в структуре и свойствах стали как результат количественных изменений (температура, содержание углерода).
4.Получить навыки в определении состава стали по ее структуре.
СОДЕРЖАНИЕ РАБОТЫ
Методика микроструктурного анализа
В различных металлах и сплавах нас, в первую очередь, интересуют их свойства. Чем полнее эти свойства отвечают запросам современного уровня развития техники, тем более качественным и более ценным будет данный сплав. Все основные свойства сплава определяются их внутренним строением (структурой), которую исследуют с помощью металлографического микроскопа.
Строение сплавов, наблюдаемое под микроскопом, называется микроструктурой.
Микроанализ сплавов был впервые применен в 1831 году русским горным инженером П.П. Аносовым, который, используя микроскоп для изучения структуры сплавов, положил начало развитию одного из основных и самого распространенного метода исследования и технического контроля металлических сплавов в промышленности.
|
|
Исследование микроструктуры металлов имеет большое значение для оценки их механических свойств, качества и технологии изготовления деталей машин. «Структура определяет свойства» – таков один из основных тезисов науки металловедения. Микроструктурный анализ позволяет определять структуру металлов на различных стадиях термической обработки, оценивать качество по наличию микроскопических неметаллических включений, определять величину зерен микроструктуры, от которой существенно зависят механические свойства.
Микроструктурный анализ металлов включает этапы:
а) приготовление микрошлифов (шлифование, полирование);
б) травление микрошлифов для выявления структуры;
Микроструктура металлов выявляется на металлографических микроскопах при увеличении до 2 000 раз или на электронных микроскопах при увеличении до 20 000 раз и более.
Изучение микроструктуры металлов на металлографических микроскопах основано на принципе отраженного света.
Поверхность изучаемого образца металла должна иметь отражающую способность, что достигается путем ее шлифовки, полировки и последующего травления.
|
|
Для изучения микроструктуры из исследуемой детали вырезается образец (микрошлиф) в виде куба или цилиндра, имеющий поперечные размеры от 10 до 20 мм. Одна из поверхностей образца подвергается шлифованию с последующим полированием.
Микроструктура металла выявляется в результате воздействия на полированную поверхность тех или иных химических реактивов. Различные структурные составляющие металла и границы зерен по разному поддаются травящему действию реактивов. На результаты травления оказывает также влияние ориентировка кристаллических плоскостей зерен. Вследствие неровностей протравленной поверхности образца получается рассеивание отраженных лучей света и образование теней от выступающих участков поверхности, что позволяет выявлять размеры зерен и структуру металла. Для травления стали и чугуна применяют 4 % раствор азотной кислоты в этиловом спирте. Продолжительность травления составляет 3-5 с.
В работе изучается микроструктура деталей, изготовленных из конструкционной стали в отожженном (медленно охлажденном) состоянии применительно к диаграмме состояния железоуглеродистых сплавов. Изучаются также особенности микроструктуры белого, серого, ковкого и высокопрочного чугунов.
|
|
Изучаемая коллекция микрошлифов содержит образцы:
- доэвтектоидной стали, содержащей углерода до 0,83 %;
- эвтектоидной (С – 0,83 %);
- заэвтектоидной стали (С 0,83 %).
При рассмотрении микроструктуры необходимо различать ее составляющие, к которым относятся:
1. Твердые растворы – феррит и аустенит.
2. Химическое соединение - цементит (Fe3C);
3. Механические смеси – перлит и ледебурит;
4. Графит.
Сталь
Микроструктура отожженной стали имеет вид участков полиэдрической (равновесной) формы с границами в виде тонких извилистых линий.
При содержании углерода до 0,006 % структура имеет вид светлых зерен феррита. Такая сталь (технически чистое железо) характеризуется малой прочностью, низкой твердостью и высокой пластичностью. Она имеет предел прочности σв = 200 МПа, твердость 800 НВ (МПа) единиц по Бринеллю (НВ), относительное удлинение δ = 35 %.
По мере увеличения содержания углерода до 0,83 % возрастает количество перлита в виде темных участков при соответствующем уменьшении светлых ферритных участков. При содержании углерода свыше 0,50 % феррит расположен в виде сетки. При увеличении микроскопа свыше 300х) выявляется пластинчатое строение перлита в виде чередующихся пластинок феррита и цементита.
При содержании углерода 0,83 % все поле зрения микроскопа занято перлитом, сталь - эвтектоидная.
Увеличение количества перлита сопровождается увеличением твердости и прочности стали. Твердость перлита составляет 2000 НВ, предел прочности σв 900 МПа. Повышение твердости и прочности объясняется увеличением количества твердой структурной составляющей цементита, твердость которого свыше 8000 НВ.
По виду микроструктуры доэвтектоидной стали определяют примерное содержание углерода и марку стали. Для этого устанавливают путем сравнения со стандартной шкалой или примерно на глаз наличие перлита в составе микроструктуры шлифа в процентном отношении. На микрофотографии количество перлита может быть определено более точно путем измерения площади перлитных участков планиметром. Содержание углерода С в доэвтектоидной стали находят из пропорции, учитывая, что 100 % перлита в структуре может быть при наличии в стали 0,83 % углерода.
Так, например, установлено, что перлит П занимает n % площади в изображении микроструктуры. Тогда составим пропорцию:
100% П – 0,83% С,
n% П – Х% С;
откуда определяемое содержание углерода Х составит:
Х = .
В зависимости от количества углерода определяют марку стали по ГОСТ-1050-90, по которому марка соответствует содержанию углерода, выраженному в сотых долях процента (табл. 1.3). Если, например, n = 40%, то количество углерода окажется равным 0,33%, что соответствует марке стали 35.
Структура заэвтектоидной стали (С от 0,83 до 2,14%) состоит из перлита и вторичного цементита. Структурным признаком заэвтектоидной стали являются иглы цементита на фоне перлита. Количество игл цементита тем больше, чем больше углерода содержится в стали. Цементит может выделяться также в виде сетки вокруг зерен перлита аналогично ферриту доэвтектоидной стали, однако, линии очертания цементитной сетки более резки. Количество углерода в заэвтектоидной стали определяется по формуле:
С = 0,8П/100 + 6,67(100–П)/100, %
Твердость эаэвтектоидной стали более высокая, чем эвтектоидной, что
позволяет применить ее для режущих инструментов. Такая сталь называется углеродистой инструментальной и маркируется У7 – У13, где цифры показывают содержание углерода в десятых долях процента. Если в конце марки стоит буква А (У10А), то это обозначает, что сталь высококачественная.
На твердость и другие механические свойства стали оказывает влияние величина зерна. Лучшими свойствами обладает мелкозернистая сталь. Величину зерна определяют по стандартной шкале при увеличении в 100 раз.
Вычертить диаграмму Fe-C (рис. 1), описать превращения, происходящие на линиях диаграммы при нагреве или охлаждении сплавов.
АСD-
АЕСF-
АС-
СD-
АЕ-
ЕS-
РSК-
GS-
В таблице 1.2 зарисовать: три микроструктуры доэвтектоидной стали, микроструктуры эвтектоидной и заэвтектоидной сталей, структуры серого, ковкого и высокопрочного чугунов. Дать описание и характеристики структур чугунов.
По зарисованным микроструктурам сталей определить примерное содержание перлита в процентах. По формулам определить содержание в сталях углерода. В зависимости от содержания перлита по формулам определить механические характеристики.
По таблице 1.1 определить марку стали и механические характеристики и сравнить их с расчетными значениями.
Рис. 1 Диаграмма состояния железоуглеродистых сплавов
Таблица 1.1
Сталь углеродистая качественная конструкционная по ГОСТ 1050-90
Марка стали | Углерод | Механические свойства после нормализации, не менее | ||||
Содержание углерода | предел текучести, МПа | предел прочности, МПа | относительное удлинение, % | относительное сужение, % | ударная вязкость, Дж/см | |
05 кп | <0,06 | 19 | - | - | - | - |
08кп, пс, 08 | 0,05-0,11 | 196 | 324 | 33 | 60 | - |
10кп, пс, 10 | 0,07-0,14 | 206 | 321 | 31 | 55 | - |
15кп, пс, 15 | 0,12-0,19 | 225 | 373 | 27 | 55 | - |
20кп, пс, 20 | 0,17-0,24 | 245 | 412 | 25 | 55 | - |
25 | 0,22-0,30 | 274 | 451 | 23 | 50 | 88 |
30 | 0,27-0,35 | 294 | 490 | 21 | 50 | 78 |
35 | 0,32-0,40 | 314 | 529 | 20 | 45 | 69 |
40 | 0,37-0,45 | 321 | 568 | 19 | 45 | 59 |
45 | 0,42-0,50 | 353 | 598 | 16 | 40 | 49 |
50 | 0,47-0,55 | 373 | 627 | 14 | 40 | 38 |
55 | 0,52-0,60 | 382 | 647 | 13 | 35 | - |
58 (55пп) | 0,55-0,63 | 314 | 598 | 12 | 28 | |
60 | 0,57-0,65 | 402 | 676 | 12 | 35 | |
65 | 0,62-0,70 | (42) | (71) | 10 | 30 | - |
70 | 0,67-0,75 | (43) | (73) | 9 | 30 | - |
75 | 0,72-0,80 | (90*) | (100*) | 7* | 30* | - |
80 | 0,77-0,85 | (95*) | (100*) | 6* | 30* | - |
85 | 0,82-0,90 | (100*) | (115*) | 6* | 30* | |
60г | 0,57-0,65 | 42 | 71 | 11 | 25 | |
65Г | 0,62-0,70 | 42 | 75 | 9 | - | |
70Г | 0,67-0,75 | 46 | 80 | 8 | - |
Содержание других элементов в %:
Si кп не более 0,77 Mn кп 0,25-0,50 Cr до 0,25
Si пс 0,05-0,17 Mn пс 0,35-0,65 S до 0,04
Si сп 0,17-0,37 Mn сп 0,80 Р до 0,035
Схемы микроструктур. Определение марки стали
по микроструктуре.
Таблица 1.2
№ п/п | Структура |
Фазовый состав
|
% С |
Свойства | ГОСТ Марка стали | |||||
|
|
|
| |||||||
|
|
|
| |||||||
|
|
|
| |||||||
|
|
|
| |||||||
|
|
|
| |||||||
|
|
|
| |||||||
|
|
|
| |||||||
По микроструктуре можно также определить и механические свойства стали: твердость, временное сопротивление, относительное удлинение.
Академик Н.С. Курнаков установил зависимость между родом диаграммы состояния сплавов и свойствами сплавов. Согласно этой зависимости механические свойства сплавов, образующих механические смеси, изменяются по прямолинейному закону и имеют среднеарифметическое значение от свойств структурных составляющих соответственно количеству последних. Поскольку сталь является сплавом, образующим механическую смесь; ее механические свойства, согласно правилу Курнакова, также можно определить графическим и аналитическим путем.
При аналитическом определении свойств исходят из того, что
для перлита σв 900 МПа, δ
10%, НВ=2000;
для феррита σв 300 МПа, δ
30%, НВ=1000.
Следовательно, временное сопротивление стали, имеющей в структуре 60% перлита и 40% феррита,
σв = ,
относительное удлинение
δ = ,
твердость по Бринеллю
НВ = .
Чугуны белые.
Ледебурит. При температуре свыше 723 С он представляет собой механическую смесь аустенита и цементита. Так как при температуре 723
С аустенит превращается в перлит, то при более низких температурах белый чугун имеет структуру видоизмененного ледебурита, который, сохраняя прежний вид, является уже механической смесью перлита и цементита.
Эвтектический белый чугун имеет пестрый вид – темные точки на светлом фоне. Светлые участки его представляют цементит, а темные – перлит (углерода 4,3%).
Доэвтектический белый чугун имеет структуру в виде чередующихся участков ледебурита и перлита. Перлит имеет форму темных дендритных образований на фоне пестрых участков ледебурита. В структуру доэвтектического чугуна входит также вторичный цементит, но он отдельно не наблюдается, так как в процессе выделения сливается с цементитом ледебурита (углерода 2,14 – 4,3%).
По мере повышения содержания углерода от 2,14 до 4,3% увеличивается количество ледебурита при соответствующем уменьшении площади перлитных участков.
Заэвтектический белый чугун характеризуется наличием первичного цементита в виде крупных игл на фоне пестрой структуры ледебурита.
Все белые чугуны отличаются высокой твердостью и хрупкостью и не поддаются обычной механической обработке резанием (углерода 4,3 – 6,67%).
Серый, ковкий и модифицированный (высокопрочный) чугуны
Металлическая основа (структура) серого, ковкого и высокопрочного чугунов – это структура стали (феррит, феррит + перлит и перлит) и на ее фоне графит в свободном состоянии.
Основная часть содержащегося в них углерода находится в свободном состоянии в виде графита, который является главным признаком их микроструктуры.
Серый чугун имеет графит в форме чешуек, которые на микрошлифе наблюдаются в виде зигзагообразных линий. В зависимости от микроструктуры металлической основы серый чугун подразделяется на перлитный, ферритно-перлитный и ферритный.
Обычный серый чугун имеет более низкие (по сравнению со сталью) механические свойства при испытании на растяжение. При сжатии прочностные свойства серого чугуна достаточно высокие, практически близкие к свойствам стали того же состава и структуры. Эти свойства тем выше, чем больше перлита в металлической основе чугуна.
Пластичность (относительное удлинение - δ%) обычного серого чугуна практически не зависит от строения металлической основы. Она имеет очень низкие значения, близкие к нулю.
Твердость НВ определяется структурой металлической основы и практически не зависит от графитных выделений.
Однако нужно иметь в виду, что влияние графита не ограничивается только снижением механических свойств чугуна на растяжение по сравнению со сталью. В ряде случаев, именно благодаря графиту, чугун имеет преимущества перед сталью. Чугун обладает лучшими литейными свойствами; имеет хорошие антифрикционные свойства, благодаря смазывающему действию графита; наличие графита быстро гасит вибрации, резонансные колебания и др.
Указанные преимущества чугуна обеспечивают ему широкое применение для отливки деталей машин, главным образом тогда, когда детали не испытывают значительных растягивающих и ударных нагрузок (станины металлорежущих станков, прессов и др.).
Общее содержание углерода в сером чугуне может быть такое же, как и в белом. Получение белого или серого чугуна зависит от химического состава и скорости охлаждения. Особое влияние при этом оказывает кремний и марганец. Кремний способствует графитизации и, следовательно, получению серого чугуна, а марганец, как и повышение скорости охлаждения, способствует карбидообразованию и получению белого чугуна.
Микроструктура ковкого чугуна имеет основу, аналогичную серым чугунам, с выделениями графита в виде включений округлой формы. Ковкий чугун получают путем длительного отжига отливок белого чугуна. Маркировка серого и высокопрочного чугунов. Например: СЧ 28, ВЧ 80, Сч – серый чугун, ВЧ – высокопрочный чугун, цифры показывают предел прочности на растяжение в кг/мм2. Ковкий чугун КЧ 42-12. КЧ – ковкий чугун, 42 – предел прочности на растяжение в кг/мм2, 12 – относительное удлинение в %. Из ковких чугунов изготавливаются головки и наконечники соединительных рукавов воздушной тормозной магистрали и крышки букс локомотивов и вагонов и другие детали.
В модифицированном чугуне графит имеет округлую (шаровидную) форму в результате добавок легирующих элементов (магний, кремний и др.). для чугуна с шаровидным графитом принципиально возможны все виды термической обработки,
применяемые для стали и их используют для улучшения свойств высокопрочного чугуна. Сочетание высокой прочности и пластичности высокопрочных чугунов дает возможность применять их для изготовления ответственных изделий.
ПОРЯДОК ВЫПОЛНЕНИЯ РАБОТЫ
1. Изучить приемы работы на микроскопе и подготовить его к работе.
2. Подготовить и протравить один из образцов и рассмотреть его на микроскопе до травления и после.
3. Изучить микроструктуру коллекции 7-8 образцов, в том числе 4 образца доэвтектоидной стали, по одному образцу – эвтектоидной, заэвтектоидной стали, белого, серого, ковкого и высокопрочного чугунов, обращая внимание на признаки их микроструктуры. Образцы подготовлены и протравлены по указанной ранее методике.
4. По заданию преподавателя зарисовать микроструктуру 3-4 образцов стали и 2-3 образцов чугуна (таблица 1.2), указав в таблице названия их микроструктур, определить примерное содержание перлита в % к общей площади поля зрения микроскопа (для стали) или по фото микроструктуры, подсчитать содержание углерода, определить механические характеристики и марки сталей по ГОСТ 1050-90. Привести примеры применения сталей с такой микроструктурой и свойствами.
В процессе выполнения работы необходимо изобразить в журнале лабораторных работ диаграмму состояния железоуглеродистых сплавов (рис. 1) и дать характеристику микроструктур (таблица 1.2).
ЛАБОРАТОРНАЯ РАБОТА № 2
ОПРЕДЕЛЕНИЕ МАРКИ СТАЛИ. ИЗУЧЕНИЕ ВЛИЯНИЯ СОДЕРЖАНИЯ УГЛЕРОДА И ПЛАСТИЧЕСКОЙ ДЕФОРМАЦИИ (НАКЛЕПА) НА ПРОЧНОСТЬ И ПЛАСТИЧНОСТЬ
ЗАДАЧИ РАБОТЫ
1. Закрепить теоретические положения, определяющие механические свойства металлов.
2. Научить студентов проводить статическое испытание на растяжение и рассчитывать диаграмму растяжения.
3. Научить пользоваться ГОСТами.
4. Экспериментально установить влияние содержания углерода и наклепа на механические свойства стали.
СОДЕРЖАНИЕ РАБОТЫ
При испытаниях на растяжение определяют важные для технологических целей и инженерных расчетов механические свойства прочности и пластичности металлов.
Прочностью называется способность материала сопротивляться разрушению при действии на него внешних сил. К характеристикам прочности относятся: предел прочности при растяжении σв, предел текучести σт, предел пропорциональности σпц.
Пластичностью называется свойство твердого тела получать остаточные изменения формы и размеров без нарушения сплошности. Характеристиками пластичности являются относительное удлинение δ и относительное сужение ψ.
Образцы. Для испытаний на растяжение применяют пропорциональные образцы круглого сечения или плоские образцы.
Между расчетной длиной образца l0 и его диаметром d0 существует соотношение:
длинные образцы
l0 = 10d0,
короткие образцы
l0 = 5d0
В результате разрушения образца на диаграммном аппарате разрывной машины записывается диаграмма разрушения в координатах нагрузка-удлинение. Используя эту диаграмму и образец после разрушения, определяются все необходимые механические характеристики: σв, σт, σпц, σ0,2, δ, ψ.
Предел прочности при растяжении σв, МПа, (временное сопротивление) определяется как напряжение, отвечающее наибольшей нагрузке, предшествующей разрушению образца.
σв = , МПа
Предел текучести (физический) σт, МПа, определяют как наименьшее напряжение, при котором образец удлиняется без заметного увеличения нагрузки.
σт = , МПа
Для материалов, у которых явно не выражена площадка текучести, определяется условный предел текучести σ0,2, МПа, под ним понимается то напряжение, при котором образец получает остаточное удлинение в 0,2% первоначальной расчетной длины:
σ0,2 = , МПа
Нагрузка Р0,2, соответствующая условному пределу текучести, определяется на основании диаграммы растяжения.
Предел пропорциональности σпц, МПа, есть наибольшее напряжение, которое материал может выдержать без отклонения от закона прямой пропорциональной зависимости между нагрузкой и удлинением:
σпц = , МПа
Относительное удлинение δ подсчитывается как отношение приращения длины образца после разрыва к его первоначальной расчетной длине:
δ = .
Относительное сужение ψ есть отношение уменьшения площади поперечного
сечения образца после разрыва к первоначальной площади его поперечного сечения
ψ = .
Предел текучести и предел прочности используются в расчетах для определения допускаемых напряжений в деталях конструкций при учете нормативных запасов прочности.
Проводимое в работе испытание образцов позволяет оценить влияние на механические свойства содержания углерода и механического наклепа.
Увеличение содержания в стали углерода приводит к повышению прочности и снижению пластичности за счет возрастающего количества твердой составляющей – цементита.
Влияние наклепа определяют на образце, предварительно растянутом на машине нагрузкой более Рт на 3 000-5 000 Н. Под наклепом понимают изменение механических и физических свойств металла в результате холодной пластической деформации. Наклеп приводит к повышению прочности и снижению пластичности.
Ударная вязкость. Ударная вязкость характеризует способность конструкционной стали сопротивляться воздействию ударных и взрывных нагрузок. Она имеет решающее значение применительно к деталям машин, работающим в условиях динамического нагружения. Ударная вязкость определяется как работа, затраченная на деформацию и разрушение стандартного образца, имеющего надрез в форме U, V или Т и измеряется в Дж/м2.
1 кгм/см2 = 10 Дж/см2 = 1 даДж/м2 = 10+5 Дж/м2 = 0,1 МДж/м2.
В работе определяют влияние на величину ударной вязкости содержание углерода, различия структуры прокатного или термически обработанного металла, низкой температуры. Указанные факторы обеспечивают либо высокую ударную вязкость, либо приводят к хрупкому состоянию металла, непригодному для использования в условиях динамического нагружения.
По мере увеличения содержания углерода ударная вязкость снижается вследствие образования все большего количества хрупкой структурной составляющей – цементита. Например, при повышении содержания углерода от 0,25% до 0,50% ударная вязкость углеродистой стали после нормализации снижается от 0,9 до 0,4 МДж/м2.
Снижение температуры испытаний приводит к снижению ударной вязкости, о чем свидетельствуют случаи хрупкого разрушения некоторых деталей машин при ударных нагрузках в условиях низких температур.
Глубокие и острые надрезы приводят к уменьшению ударной вязкости и опасности хрупкого разрушения в результате концентрации напряжений в местах надрезов. Поэтому при изготовлении любых деталей машин не рекомендуется применять острые переходы и надрезы.
Низкую ударную вязкость имеет закаленная сталь в результате неравновесного и напряженного ее структурного состояния. Наилучшее сочетание ударной вязкости и других механических свойств имеет сталь после закалки и последующего высокого отпуска.
Ударную вязкость определяют на маятниковом копре, имеющем запас кинетической энергии 300 Дж.
Мерой сопротивления материала ударному нагружению служит ударная вязкость
КСU, КСV или КСТ (U, V, Т) в зависимости от формы надреза), которая определяется как отношение работы излома К образца данного типа к площади его поперечного сечения F в месте надреза:
КСU = [Дж/м2] ; КСV =
[Дж/м2]
Ударная вязкость как техническая характеристика материала не применяется в инженерных расчетах, но имеет большое, нередко определяющее значение при приемке металла, изделий из него и условий эксплуатации.
Так, ударная вязкость должна быть для шатунов из хромистой стали 40Х не менее 0,6 МДж/м2, для коленчатых валов ответственного назначения из хромоникелемолибденовой стали 40ХНМА – не менее 10 МДж/м2.
Порядок выполнения работы
Работа выполняется группами студентов по 3-4 человека. Каждая группа проводит испытание и обработку результатов испытаний одного образца. Два образца изготовлены из малоуглеродистой, а третий – из среднеуглеродистой или легированной стали.
Работу выполняют в следующей последовательности:
1. Измерить микрометром или штангенциркулем диаметр образца.
2. На делительной машине нанести по всей длине образца равномерные деления и кернами отметить границы расчетной длины.
3. Закрепить образец в зажимах машины.
4. Закрепить миллиметровую бумагу, карандаш и подготовить диаграммный аппарат к работе.
5. Включить мотор масляного насоса и плавным открыванием вентиля распределительной коробки производить нагружение образца вплоть до разрыва.
6. В момент нагружения зафиксировать по остановке стрелки на отсчетной шкале нагрузки, соответствующие пределам текучести и прочности.
7. Соединить половинки образца, закрепить их в зажимное приспособление, измерить штангенциркулем диаметр образца в месте шейки F1 и расчетную длину l1.
8. По приведенным ранее формулам подсчитать все механические характеристики и результаты подсчета записать в рабочий журнал.
9. По механическим свойствам установить марку стали.
10.Для выявления влияния наклепа разметка одного из образцов малоуглеродистой стали, производится после его растяжения на машине до нагрузки, на 3 000 _ 5 000 Н несколько превышающей нагрузку, соответствующую пределу текучести. После этого испытание образца производится обычным порядком.
11.При определении ударной вязкости используются образцы с разным содержанием углерода. Образец установить на предметном столике, взвести маятник копра в рабочее положение, поставить оградительную сетку, освободить маятник, определить угол отклонения маятника и по таблице работу в зависимости от отклонения маятника.
Каждый студент проводит обработку результатов испытаний образцов, записывает в отчетный журнал результаты испытаний и делает заключение о факторах, оказывающих влияние на механические свойства стали. В отчетном журнале приводятся также диаграмма растяжения и расчетные формулы.
Эскиз образца и схема испытания на ударную вязкость
Протокол испытаний образцов на ударную вязкость
№ п/п | Работа по излому образца К, Дж/м2 | Площадь сечения F, см2 | Форма надреза U, V, T | КСU Дж/м2 | КСV Дж/м2 |
Протокол испытаний на растяжение
С % | d0 мм | d1 мм | l0 мм | l1 мм | F0 мм2 | F1 мм2 | Pт Н | Pв Н | σт МПа | σв МПа | δ % | Ψ % |
Диаграммы растяжения Эскизы образцов до и после растяжения
ЛАБОРАТОРНАЯ РАБОТА № 3
ТВЕРДОСТЬ МЕТАЛЛОВ И ФАКТОРЫ ЕЕ ОПРЕДЕЛЯЮЩИЕ
ЗАДАЧИ РАБОТЫ
Научить студентов самостоятельно проводить испытание твердости металлов. В процессе выполнения работы необходимо изучить:
1. Устройство пресса Роквелла и пресса Бринелля для определения твердости.
2. Порядок выбора диаметра шарика и нагрузки.
3. Порядок подготовки образца.
4. Порядок проведения испытания на прессах.
5. Методику измерения полученного отпечатка.
6. Порядок определения твердости по таблице.
СОДЕРЖАНИЕ РАБОТЫ
Твердостью, называется способность материала сопротивляться проникновению в него другого, более твердого тела без деформации последнего (например. Наконечника прибора). Большинство способов определения твердости основано на вдавливание в испытуемый материал наконечника той или иной формы (шарик, конус, пирамида) при различных величинах и характере приложения нагрузки. Поэтому естественно, что получаемые при различных способах определения твердости цифровые значения ее для одного и того же материала различны как по величине, так и по физическому смыслу.
Следовательно, показатель твердости металла – число твердости – должен во всех случаях сопровождаться указанием метода, которым он определен. Сравнение чисел твердости, полученных различными методами, производится на основании опытных данных.
Показатель твердости для большинства способов характеризует сопротивление металла местной, сосредоточенной в небольшом объеме, пластической деформации, которая зависит от структуры, химического состава и напряженного состояния металла. Изменение любого из этих факторов вызывает изменение твердости.
Определение твердости металлов, как один из методов их исследования, отличается надежностью, быстротой и несложностью проведения испытания, не требует изготовления специальных образцов, может проводиться непосредственно на готовом изделии.
Указанные преимущества определяют очень широкое применение испытания на твердость, как в производственных условиях, так и для научных исследований.
Определение твердости по Бринеллю
При определении твердости металлов по Бринеллю стальной закаленный шарик диаметром D вдавливается в испытуемый образец (изделие) под действием нагрузки Р. Нагрузка выдерживается в течение определенного времени, после чего снимается. От вдавливания шарика на поверхности испытуемого металла образуется сферический отпечаток диаметром d, по величине которого и судят о твердости.
Число твердости по Бринеллю НВ, МПа, вычисляют как отношение нагрузки Р к площади поверхности сферического отпечатка F:
НВ = =
,
где Р – нагрузка, Н;
F – площадь поверхности сферического отпечатка, мм2;
D – диаметр шарика, мм;
d – диаметр отпечатка, мм.
Диаметр отпечатка d измеряют специальным отсчетным микроскопом, на окуляре которого нанесена шкала с ценой деления 0,1 мм. Микроскоп устанавливают на поверхности испытуемого образца так, чтобы край отпечатка совпал с началом шкалы. Деление шкалы, совпадающее с противоположным краем отпечатка, указывает диаметр отпечатка d.
При измерении твердости по Бринеллю используют шарики с диаметром
2,5; 5 и 10 мм. Требуемый для данного испытания шарик выбирают в зависимости от толщины образца, величины прикладываемой нагрузки и испытываемого материала образца.
Для получения сопоставимых результатов испытания необходимо соблюдать стандартные условия при выборе диаметра вдавливаемого шарика, нагрузки и продолжительности выдержки. Эти условия определяют согласно табл. 3.1.
Таблица 3.1
Стандартные условия для выбора диаметра вдавливаемого шарика, нагрузки
и продолжительности выдержки
Материалы | Интервал твердости в числах Бринелля, МПа | Минимальная толщина испытываемого образца | Диаметр шарика В, мм | Соотношение между нагрузкой Р и диаметром шарика О | Нагрузка Р, Н | Выдержка под нагрузкой, с | |
Черные металлы | 1400-4500 | Более 6 От 6 до 3 Менее 3 | 10 5 2,5 | Р = 30 D2 | 30 000 7 500 1875 | 10 | |
Черные металлы | <1400 | Более 6 от 6 до 3 Менее 3 | 10 5 2,5 | Р = 30 D2 | 30 000 7 500 1875 | 30 | |
Сплавы: медь,латунь, бронза и др. | > 1 300 | Более 6 от 6 до 3 Менее 3 | 10 5 2,5 | Р = 10D2 | 10 000 2500 625 | 30 | |
Алюминий, Подшипн. сплавы | 80-350 | Более 6 от 6 до 3 Менее 3 | 10 5 2,5 | Р = 2,5 D2 | 2 500 625 156 | 60 |
Опытным путем установлено, что между временным сопротивлением σв и твердостью НВ для пластичных материалов существует определенная зависимость. Например, для незакаленной стали σв = 0,36 НВ.
Метод Бринелля для определения твердости является весьма точным, но имеет ряд недостатков:
1.Ограниченность области применения. Не рекомендуется испытывать материалы, имеющие твердость больше 4500 МПа, так как в этом случае шарик может деформироваться, что приведет к искажению результатов.
2. Невозможность определения твердости тонких изделий и поверхностного слоя металла. Толщина изделия должна быть не менее десятикратной глубины вдавливания.
3. Получение значительного отпечатка на изделии, что в ряде случаев недопустимо.
Определение твердости по Роквеллу
Твердость по Роквеллу характеризуется глубиной вдавливания в металл алмазного конуса или стального шарика под действием двух последовательно прилагаемых нагрузок – предварительной и основной. Алмазный конус с углом при вершине 1200 применяется для испытания металлов большой твердости (НВ > 2 300 МПа), а шарик диаметром 1,59 мм – для металлов средней твердости. Предварительная нагрузка в 10 Н обеспечивает плотное соприкосновение наконечника с образцом. Общая нагрузка в 1 500 Н применяется при алмазном наконечнике и в 1000 Н – при стальном шарике. Прибор Роквелла рассчитан на предельное проникание алмазного наконечника на глубину 0,2 мм.
Физический смысл единицы твердости по Роквеллу:
НRC = 100 - ,
где h, h1 – глубина проникания наконечника под действием основной и предварительной нагрузки.
В целях измерения твердости мягких материалов применен наконечник – стальной шарик, а шкала В смещена на 30 единиц, что позволяет определить твердость при углублении наконечника до 0,26 мм.
НRВ = 130 - .
Наиболее распространены условия испытаний, приведенные в табл. 3.2.
Таблица 3.2
Условия испытаний по Роквеллу
Нагрузка, Н | Шкала | Наконечник | Обозначение | Испытуемый металл |
1500 | С | Алмазный конус | НRС | Сталь закаленная, НВ более 2 300 |
1 000 | В | Стальной шарик | НRВ | Сталь средней твердости |
Метод Роквелла по сравнению с методом Бринелля имеет следующие преимущества:
1. Более широкие пределы измерения твердости.
2. Быстрота испытаний вследствие совмещения операций вдавливания наконечника и получения отсчета числа твердости.
3.Получение отпечатков малых размеров.
К числу недостатков относятся:
1. Несколько меньшая точность получаемых результатов вследствие меньшего объема материала, принимающего участие в зоне деформирования.
2. Необходимость более тщательной подготовки поверхности в месте отпечатка.
Определение твердости по Виккерсу
Наиболее совершенным методом определения твердости является метод Виккерса. Твердость по Виккерсу определяется вдавливанием в испытуемый металл правильной четырехгранной алмазной пирамиды (с углом между гранями 1360) под действием нагрузки Р, приложенной в течение определенного времени. После удаления нагрузки измеряются диагонали отпечатка d, оставшегося на образце.
Число твердости НV определяют путем деления нагрузки Р (Н) на площадь боковой поверхности (мм2) полученного пирамидального отпечатка:
НV = 1,854 ,
где Р – нагрузка, Н;
d – среднее арифметическое обеих диагоналей после снятия нагрузки, мм.
Диагональ отпечатка измеряют специальным микроскопом и оптическим микрометром.
Практически число твердости НV находят с помощью специальных таблиц по величине измеренной диагонали отпечатка с учетом приложенной нагрузки.
Метод Виккерса обеспечивает высокую точность измерения. На приборе Виккерса можно проводить испытания, как мягких металлов, так и металлов высокой твердости, а также металлов весьма малых сечений (0,3…0,5 мм) и тонких поверхностных слоев, образующихся при цементации, азотировании, цианировании и др. (0,3…0,5 мм).
Поверхность испытуемого образца должна быть гладкой и чистой. Подготовку поверхности следует производить способом, не изменяющим твердости металла. Изменение может вызвать нагрев при шлифовании или наклепе.
Прибор целесообразно применять в тех случаях, когда изделие требует приложения нагрузок значительно меньше тех, которые употребляются при испытании по Роквеллу
Определение твердости по методу Шора
Твердость по методу упругого отскока бойка (метод Шора) определяют в тех случаях, когда на поверхности контролируемого изделия не должно быть следов отпечатков прибора, например, при контроле твердости шеек коленчатых валов после закалки с применением нагрева токами высокой частоты. В настоящее время этот метод используется ограничено, но его принцип заложен в конструкции электронных приборов по определению твердости.
Твердость оценивается по высоте отскока бойка прибора (h). За основу градуировки шкалы прибора взята закаленная инструментальная сталь, высота отскока бойка при испытании которой разделена на 100 единиц. Перевод значений твердости по отскоку бойка hот в единицы Бринелля может быть сделан по приближенной зависимости
НВ = 7 hот.
На высоту отскока существенное влияние оказывают упругие свойства материала. Сопоставлять результаты испытаний можно только для материалов, имеющих примерно равные модули упругости.
Определение твердости по методу Польди
Твердость по переносному твердомеру Польди определяется путем сравнения размеров отпечатков на эталоне и испытуемом изделии. Отпечатки шарика получаются одновременно при ударе молотком по бойку прибора. Так как усилие, прилагаемое к образцу и эталону, одинаково, то твердость испытуемого изделия НВиз. выражается зависимостью:
НВиз. =
где НВэт – твердость эталона (определяется заранее в лабораторных условиях);
dэт – диаметр отпечатка на эталоне;
dиз – диаметр отпечатка на изделии.
Показания переносного твердомера близки к числам твердости по Бринеллю.
Такой метод применяется для определения твердости массивных изделий и при испытаниях в полевых условиях.
ПОРЯДОК ВЫПОЛНЕНИЯ РАБОТЫ
1. Ознакомиться с методиками измерения твердости на приборах.
2. Произвести определение твердости 2-3 деталей (образцов) машин на прессе Бринелля: получить отпечаток, измерить диаметр отпечатка с помощью микроскопа и, в зависимости от диаметра отпечатка, определить твердость по таблице.
3. Произвести определение твердости на прессе Роквелла.
4. Произвести измерения твердости на других приборах.
5. Сопоставить результаты твердости, полученные разными методами и дать заключение о факторах, влияющих на твердость.
Таблица 3.3
№ № п/п |
Твердость по Бринеллю |
Твердость по Роквеллу |
Твердость по Виккерсу НV |
Твердость по Польди |
Примеча- ния | |||||
Диаметр отпечатка мм | НВ | НRВ | НRС | |||||||
|
|
| ||||||||
|
|
| ||||||||
|
|
| ||||||||
|
|
| ||||||||
|
|
| ||||||||
|
|
| ||||||||
|
|
| ||||||||
Сравнение чисел твердости, полученных разными способами
Таблица 3.4
Твердость по Бринеллю | Твердость | по Роквеллу | Твердость по Виккерсу | ||
Диаметр от- | НВ | Н RC | Н RВ | HV | |
печатка, мм | |||||
2,30 | 712 | 68 | 1022 | ||
2,40 | 653 | 64 | — | 868 | |
2,50 | 601 | 60 | — | 746 | |
2,60 | 555 | 56 | — | 650 | |
2,70 | 514 | 52 | — | 587 | |
2,80 | 477 | 49 | — | 534 | |
2,90 | 444 | 46 | — | 474 | |
3,00 | 415 | 43 | — | 435 | |
3,10 | 388 | 41 | — | «01 | |
3,20 | 363 | 39 | — | 380 | |
3,30 | 311 | 36 | — | 344 | |
3,40 | 321 | 33 | — | 320 | |
3,50 | 302 | 31 | — | 303 | |
3,60 | 285 | 29 | — | 285 | |
3,70 | 269 | - 27 | — | 270 | |
3,80 | 255 | 25 | — | 255 | |
3,90 | 241 | 23 | 102 | 240 | |
4,00 | 229 | 2.0 | 100 | 228 | |
4,10 | 217 | 17 | 98 | 217 | |
4,20 | 207 | 14 | 95 | 208 | |
4,30 | 197 | 12 | 93 | 197 | |
4,40 | 187 | 9 | 91 | 186 | |
4,50 | 179 | 7 | 90 | 178 | |
4,60 | 170 | 4 | 88 | 171 | |
4,70 | 163 | 2 | 86 | 162 | |
4,80 | 156 | 0 | 84 | 155 | |
4,90 | 149 | ------ | 82 | 149 | |
5,00 | 143 | --- | 80 | 143 | |
5,10 | 137 | — | 78 | 138 | |
5,20 | 131 | --- | 76 | 131 | |
5,30 | 126 | ------- | 74 | 127 | |
5,40 | 121 | — | 72 | 121 | |
5,50 | 116 | --- | 70 | 116 | |
5,60 | 111 | — | 67 | 113 |
ЛАБОРАТОРНАЯ РАБОТА № 4
ЭЛЕКТРОДУГОВАЯ СВАРКА МЕТАЛЛОВ
ЗАДАЧИ РАБОТЫ
1. Изучение принципов устройства и работы сварочного оборудования для электродуговой сварки на постоянном и переменном токах, контактной сварки (точечной, шовной и стыковой).
2. Изучение приемов работы на электросварочных аппаратах и определение коэффициента наплавки. Контроль качества сварных соединений.
СОДЕРЖАНИЕ РАБОТЫ
При сварке переменным током источником питания являются сварочные трансформаторы; при сварке постоянным током – специальные сварочные генераторы или выпрямители.
К источнику питания сварочной дуги предъявляются следующие требования:
1. Источник питания должен быть рассчитан на продолжительное короткое замыкание в сварочной цепи. Замыкание происходит при зажигании дуги и, периодически – 20-40 раз в секунду – замыкают цепь расплавленные капли металла электрода.
2. Напряжение источника тока должно быстро меняться с изменением длины дуги (при уменьшении длины дуги оно должно падать, и при увеличении – возрастать).
3. Для обеспечения зажигания дуги напряжение холостого хода должно быть достаточно высоким и в то же время безопасным для сварщика (не более 80 В).
4. Схема источника питания должна обеспечивать возможность регулирования сварочного тока.
В качестве источников питания сварочной дуги применяются машины и аппараты, имеющие падающую статическую (внешнюю) характеристику.
Электродуговая сварка на постоянном токе выполняется сварочным генератором.
Наиболее распространены сварочные генераторы с раздвоенными полюсами типа СМГ-2, у которых круто падающая характеристика получается за счет взаимодействия потока возбуждения и реакции якоря.
Регулирование сварочного тока достигается путем смещения щеток по направлению или против направления вращения якоря.
Сварочный генератор СМГ-2 имеет следующие основные характеристики:
Мощность при непрерывной продолжительной работе……………..10 кВт
Номинальное напряжение………………………………………………..40 В
Напряжение холостого хода……………………………………………..75 В
Пределы регулирования тока……………………………………..110-350 А
Генератор приводится в движение электродвигателем переменного тока или двигателем внутреннего сгорания.
Смещение щеток по направлению вращения якоря приводит к уменьшению сварочного тока, так как при этом вследствие изменения направления магнитного потока реакции якоря увеличивается размагничивающая составляющая реакции якоря Фяр.
У генераторов СМГ-2 щетки могут находиться в трех фиксированных положениях. Более тонкая регулировка сварочного тока осуществляется с помощью реостата, включенного в цепь регулируемой обмотки возбуждения поперечных полюсов.
По аналогичному принципу работают распространенные на практике сварочные генераторы типа СМГ-2Г, преобразователи ПСО-500 и другие.
Сварочные генераторы работают на прямой или обратной полярности. В случае прямой полярности плюс генератора подключается к изделию, а минус к электроду, при обратной полярности – наоборот.
Прямая полярность обеспечивает более интенсивный режим сварки, так как поток электронов соответствует направлению потока капель материала электрода. Она применяется для сварки малоуглеродистой стали марок 10, 20, Ст3 и т.п. Обратная полярность применяется при сварке легированной стали, чугуна, алюминиевых сплавов, тонких листов металла.
Электродуговая сварка на переменном токе выполняется сварочным трансформатором (ТД, СТШ и др.). При ручной сварке обычно применяются сварочные трансформаторы с отдельной реактивной катушкой (регулятором).
Для получения падающей характеристики трансформатора во вторичную (сварочную) цепь последовательно с трансформатором включается реактивная катушка-регулятор, которая представляет собой железный сердечник с намотанным на него проводом, рассчитанным на максимальный сварочный ток.
При прохождении через реактивную катушку сварочного тока большое индуктивное сопротивление катушки вызывает падение напряжения сварочной дуги, причем индуктивное сопротивление возрастает с увеличением сварочного тока.
Регулировка сварочного тока осуществляется путем изменения сопротивления магнитопровода. Для этого железный сердечник реактивной катушки выполняется из двух частей: неподвижной (на ней расположены витки обмотки) и подвижной.
Увеличение зазора между подвижной и неподвижной частями вызывает увеличение магнитного сопротивления магнитопровода. Магнитный поток при этом уменьшается, вследствие чего индуктивное сопротивление катушки также уменьшается, а сварочный ток возрастает. При уменьшении воздушного зазора магнитный поток и индукционное сопротивление катушки возрастают, а сварочный ток уменьшается.
Регулировка тока, т.е. изменение зазора в сердечнике катушки, производится с помощью винта (на конец его надета рукоятка), перемещающего подвижную часть сердечника. Для надежной фиксации подвижной части сердечника в определенном положении реактивная катушка имеет стопор.
Рабочее место сварщика
1. Работы по электросварке выполняют в отдельной закрытой кабине.
2. Сварку выполняют на металлическом столе, к которому подсоединен один из проводов, ведущих к источнику тока. Второй провод идет от источника тока к
электрододержателю, который представляет собой зажим, удерживающий электрод с рукояткой из материала, не проводящего электрический ток.
3. Свариваемая деталь находится на столе. Сварщик работает сидя. Стул и ноги сварщика должны находится на резиновом коврике.
4. В ходе работы используется следующий инструмент:
- молоток для отбивки шлака со швов;
- стальные щетки для очистки детали от ржавчины и грязи перед началом сварки для обеспечения контакта;
- зубило для отбивки брызг и шлака после сварки.
4. Для предохранения глаз и кожи лица от действия сварочной дуги применяется щиток или шлем с темными защитными стеклами.
5. Спецодежда сварщика: комбинезон, фартук и рукавицы.
Выбор сварочного электрода
Выбор сварочного электрода проводят в зависимости от толщины свариваемого металла S, мм, по формуле:
d = + 1.
В соответствии с диаметром электрода d определяют величину сварочного тока I, генератора или трансформатора
I = В d .
где В - 35 50 А/мм, плотность тока на 1 мм диаметра электрода.
Тип электрода выбирают в зависимости от заданной прочности материала сварного металла шва: Э42, Э50, Э55 и другие (численное значение типа электрода указывает минимальное значение предела прочности наплавленного шва в 10 МПа). Для сварки малоуглеродистой стали Ст3 представляются электроды типа Э42 марок ОММ5 или К3, для сварки низколегированной стали – типа Э55 марки УОНИ-13/55.
В работе определяют значения технологических коэффициентов αр, αн и ψ. Они зависят от ряда факторов, главным из которых при ручной дуговой сварке (наплавке) является марка электрода. Значения этих коэффициентов изменяются в зависимости от рода и полярности тока.
Коэффициент расплавления αр, г/(А∙ч) определяют по формуле
αр = 3600 * Gр /(Iсв tсв),
где Gр = π*d2(lэ – lог)*ρ/4 - масса расплавленного металла, г;
Iсв – сварочный ток, А;
t – время горения дуги, сек, которое определяется в процессе проведения сварки.
Коэффициент наплавки αн, г/(А∙ч) определяют по формуле:
αн = Gн /( Iсв * tсв).
Gн = Gсв - Gпл - масса наплавленного металла,
Gсв - масса пластины после сварки
Gпл - масса пластины до сварки
Значения величин, входящих в формулы, определяют экспериментально: Qн – масса наплавки, т.е. разность масс пластины до и после наплавки.
Потери на угар и разбрызгивание составляют:
ψ = (GР – GН/ GР)*100 %.
Расчет расхода электродов по норме:
GЭЛ = KР * GН, г
где К – коэффициент использования сварочного поста, который для ручной сварки можно принять 0,5-0,55.
Расход электроэнергии А, кВт∙ч/кг рассчитывают по формуле
А = Uсв* Iсв* tсв*1000/3600 * Gн, кВт/кг
где η – КПД источника тока;
W – мощность, расходуемая источником тока при работе на холостом ходу, кВт.
Данные значений η и W приведены в табл. 4.1.
Таблица 4.1
Род тока | η | W, кВт |
Переменный | 0,8 - 0,9 | 0,2-0,4 |
Постоянный | 0,6-0,7 | 2,0-3,0 |
Величина αн для отдельных типов электродов составляют 7-12 г/А∙ч при ручной сварке и 15-17 г/А∙ч при автоматической сварке.
Расчет производительности процесса сварки (наплавки)
Qн = αн Iсв/1000 кг/ч
Дата добавления: 2019-02-12; просмотров: 228; Мы поможем в написании вашей работы! |
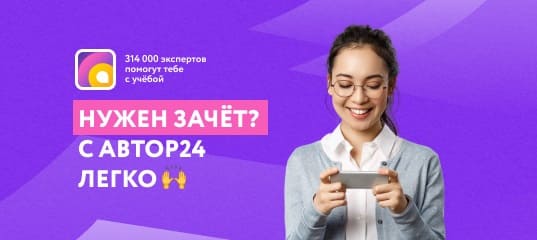
Мы поможем в написании ваших работ!