Выбор материалов для зубчатых колес и определение допускаемых напряжений
Материалы, применяемые для зубчатых колес, рассмотрены в разделе 1.2. Их характеристики приведены в таблице 2.2.
Таблица 2.2 - Характеристики материалов для зубчатых колес
Марка стали | Термообра- ботка | Размер сечения, мм, не более | Твердость поверхности HB или HRC | Предел прочности sb,МПа | Предел текучести sТ, МПа |
40 | Улучшение | 60 | HB192...228 | 700 | 400 |
45 | Нормализация Улучшение | 80 100 | HB170...217 HB192...217 | 600 750 | 340 450 |
50 | Нормализация Улучшение | 80 80 | HB179...228 HB228...255 | 640 700...800 | 350 530 |
40Х | Улучшение Улучшение Улучшение | 100 100...300 300...500 | HB230...280 HB163...269 HB163...269 | 850 750 700 | 650 500 450 |
40ХН | Улучшение Улучшение Закалка | 100 100...300 40 | HB230...300 HB³241 HRC 48...54 | 850 800 1600 | 600 580 1400 |
20Х | Цементация | 60 | HRC 56...63 | 650 | 400 |
12ХН3А | Цементация | 60 | HRC 56...63 | 900 | 700 |
38ХМЮА | Азотирование | - | HRC 57...67 | 1050 | 900 |
Примечание. Под размером сечения подразумевается радиус заготовки вал-шестерни или толщина обода колеса. |
Для удобства рассмотрения в дальнейшем излагаемые материалы будут размещаться параллельно: для прямозубой передачи в левой колонке, для косозубой в правой колонке.
При выборе твердости и термообработки зубчатых колес следует придерживаться следующих рекомендаций.
Для прямозубой передачи можно принять как для шестерни, так и для колеса термообработку - улучшение с разностью твердости 10...20 единиц для обеспечения прирабатываемости. Для уменьшения габаритов редуктора твердость шестерни и колеса на начальном этапе расчета принять НВ280 и НВ260, соответственно. | Для косозубой передачи можно принять для колеса улучшение до твердости HB<350 ед. Для шестерни можно принять объемную закалку до твердости HRC45, для колеса НВ 260ед с целью использования головочного эффекта для получения более высокой нагрузочной способности. Для соосных редукторов материал для косозубой передачи выбрать как у прямозубой |
|
|
В соответствии с выбранным материалом и поверхностной твердостью главным расчетным критерием работоспособности является контактная прочность. Цель расчета по допускаемым усталостным контактным напряжениям - предотвратить усталостное выкрашивание рабочих поверхностей зубьев зубчатых колес в течение заданного срока службы t.
Допускаемые усталостные контактные напряжения определяются по формуле
(2.3)
где – предел контактной выносливости активных поверхностей зубьев, соответствующий базовому числу циклов NH lim перемены напряжений (табл. 2.3);
ZR – коэффициент, учитывающий шероховатость поверхности;
ZV – коэффициент, учитывающий окружную скорость;
|
|
SH – коэффициент запаса прочности;
ZN – коэффициент долговечности.
Таблица 2.3 – К определению предела контактной выносливости
Термическая или химико-терми- ческая обработка | Твердость поверхностей | Группа материалов | sHlim, Мпа |
Улучшение, нормализация | HB£350 | Углеродистые
и легированные
стали | 2×(HB)+70 |
Объемная закалка | HRC=38...50 | 17×(HRC)+100 | |
Поверхностная закалка | HRC=40...56 | 17×(HRC)+200 | |
Цементация, нитроцементация и закалка | HRC=56...65 |
Легированные стали | 23×(HRC) |
Азотирование | HV=550...750 | 1050 | |
Без термической обработки | - | Чугун | 2×(HB) |
Значения коэффициентов ZR , ZV и S Н приведены в таблице 2.4
Таблица 2.4 – К определению коэффициентов ZR , ZV и S Н
Коэф- фици- ент | Наименование коэффициента | Значение коэффициента |
ZR | Коэффициент, учитывающий шероховатость сопряженных поверхностей зубьев | Шлифование Ra=1,25...0,63 мкм. ZR=1. Зубофрезерование, шлифивание Ra=2,5...1,25 мкм. ZR=0,95. Зубофрезерование Ra=10...2,5 мкм. ZR=0,9. |
ZV | Коэффициент, учитывающий влияние окружной скорости | При HB£350 Vм/с до5 до10 до20 ZV 1,00 1,07 1,15 При HB>350 Vм/с до5 до10 до20 ZV 1,00 1,04 1,07 |
SH | Коэффициент запаса прочности | Нормализация, улучшение, объемная закалка SH=1,2. Поверхностное упрочнение SH=1,3. |
|
|
Предварительно принимается коэффициент ZV =1. В процессе расчета определяется окружная скорость в зацеплении, по которой можно уточнить ZV и при необходимости скорректировать [σ ]Н.
Коэффициент долговечности
(2.4)
где m –показатель степени кривой усталости, равный 6.
NH lim – базовое число циклов кривой контактной выносливости в зависимости от твердости рабочих поверхностей зубьев подсчитывается по формуле
NH lim = (НВ)3 ≤ 12 · 107 . (2.5 )
Для перевода единиц твердости HRС в единицы НВ использовать таблицу 2.5.
Таблица2.5 – Перевод твердости HRС в единицы НВ
HRС | 35 | 40 | 45 | 50 | 55 | 60 |
НВ | 330 | 375 | 430 | 485 | 540 | 600 |
N к – фактическое число циклов нагружения зубчатого колеса определяется по формуле
N к 1(2) = 60 n 1(2) t , (2.6)
где n – число оборотов того зубчатого колеса, для которого определяется N к.
|
|
Если нагрузка переменная, то вместо фактического числа циклов нагружения в формуле (2. ) подставляется эквивалентное число циклов N НЕ.
При наличии графика (гистограммы) нагружения
N НЕ1(2) = 60 n 1(2 ) t еН , (2.7)
где еН - коэффициент эквивалентности, который определяется по гистограмме нагружения
, (2.8)
где Tmax - наибольший из длительно действующих моментов. В нашем случае это будет момент T, действующий t1 часть общего времени работы t; тогда q1=1.
Ti - каждая последующая ступень нагрузки, действующая в течении времени ti= t i × t. Первая ступень гистограммы, равная по нагрузке Tпик=qпик×T, при подсчёте числа циклов не учитывается. Эта нагрузка при малом числе циклов оказывает упрочняющее действие на поверхность. Ее используют при проверке статической прочности.
Таким образом,
. (2.9)
Коэффициент эквивалентности показывает, что момент T, действующий в течение eH × t времени, оказывает такое же усталостное воздействие как и реальная нагрузка, соответствующая гистограмме нагружения в течение времени t.
Исследованиями установлено, что большинство режимов нагружения современных машин сводятся приближенно к шести типовым режимам (ГОСТ 21354 – 87), рисунок 2.3.
Рисунок 2.3 - Типовые режимы нагружения
На рисунке 2.3: Ti – текущее значение момента нагрузки; T мах – максимальный из моментов, которые учитывают при расчете на усталость; ΣN i – число циклов нагружения при работе с моментами, равными и большими Ti; N к – суммарное число циклов нагружения за расчетный срок службы передачи. Типовые режимы нагружения обозначены: 0 – постоянный; I – тяжелый; II – средний равновероятный; I I I – средний нормальный; IV – легкий; V – особо легкий.
Эквивалентное число циклов
N НЕ1(2) = μн N к1(2) , (2.10)
где μн – начальный момент соответствующего распределения (таблица 2.6).
Таблица 2.6 - Начальные моменты
Режим работы | Расчет на контактную усталость | Расчет на изгибную усталость | |||||||
термооб-работка | т/2 | μн | термо- обработка | т | μ F · | термо- обработка | т | μ F · | |
0 I II I I I IV V | Любая | 3 | 1,0 0,5 0,25 0,18 0,125 0,063 | Улучшение, нормализа-ция, азотирова- ние | 6 | 1,0 0,30 0,143 0,065 0,038 0,013 | Закалка объемная, поверхност-ная, цементация | 9 | 1,0 0,20 0,10 0,036 0,016 0,004 |
Расчетные допускаемые контактные напряжения для передачи
Для расчета прямозубых передач в качестве расчетного выбирается наименьшее из двух | Для расчета косозубых передач в качестве расчетного для реализации головочного эффекта принимается |
![]() | ![]() |
Кроме того, должно соблюдаться соотношение
![]() |
Для соосных редукторов материалы и термообработка зубчатых колес косозубой быстроходной передачи принимаются такие же, как и для тихоходной прямозубой пары в связи с ее меньшей загруженностью.
Установив значения U, Ka , T2 , KHβ , ψва и [σ ]Н их подставляют в формулу 2.1 и определяют межосевое расстояние проектируемой зубчатой передачи.
Дата добавления: 2019-02-13; просмотров: 269; Мы поможем в написании вашей работы! |
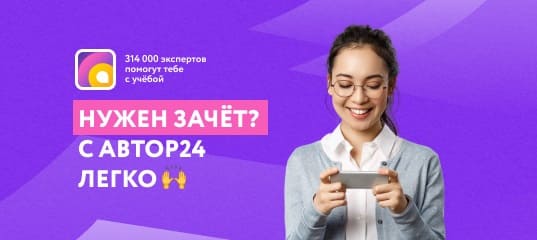
Мы поможем в написании ваших работ!