Зубо- и резьбообрабатывающие станки.
Схема зубодолбежного станка. Настройка цепей.
Основными методами изготовления резьб являются нарезание их резцами и гребенками на токарных станках; фрезерование; нарезание метчиками, плашками, резьбонарезными головками; холодное и горячее накатывание; шлифование однониточными и многониточными кругами.
Выбор метода получения резьбы зависит от типа производства, размеров резьбы, ее точности, материала заготовки и т.д. Например, накатывание резьб широко распространено в крупносерийном и массовом производстве, так как этот способ обеспечивает высокую производительность, низкую себестоимость обработки, высокую прочность и износостойкость резьбовой заготовки. Накатывание можно производить плоскими или круглыми плашками. Резьбошлифование широко применяют не только для отделки, но и для первоначального нарезания резьбы.
Резьбошлифовальные станки предназначены для шлифования резьб повышенной точности узкими (однониточными) и широкими (многониточными) кругами.
Метод шлифования однониточным кругом применяют в тех случаях, когда требуется высокая точность резьбы. При использовании этого метода помимо вращения круга и изделия, происходит продольное перемещение изделия (рис. 1, а). Метод характеризуется малой окружной скоростью изделия и большой поперечной подачей. Ось круга повернута относительно оси заготовки на угол подъема резьбы, что позволяет получить большую точность профиля шлифуемой резьбы.
|
|
а) б)
Рис. 1. Способы шлифования резьбы
а) метод шлифования однониточным кругом;
б) метод шлифования многониточным кругом
Шлифование резьбы многониточным цилиндрическим кругом применяют в том случае, когда к поверхности резьбы предъявляются высокие требования по чистоте, а точность может быть меньшая, чем в первом случае (рис. 1,б).
При использовании метода помимо вращения круга и изделия, происходит перемещение изделия на длину шага резьбы за один оборот изделия.
Резьбошлифовальные станки, в которых продольное перемещение стола с изделием осуществляется при помощи ходового винта и сменных зубчатых колес, имеют коррекционное устройство, настройкой которого компенсируется влияние температуры на величину шага шлифуемой резьбы, а также накопленная ошибка шага ходового винта.
Эти устройства в большинстве конструкций станков выполнены в виде поворотной линейки, которая при продольном перемещении стола производит добавочное вращение гайки ходового винта.
В некоторых моделях (ФРГ «Линднер») применяют дополнительную гитару корректировки шага, которая включается в цепь настройки на шаг последовательно с основной гитарой.
|
|
В серийном производстве широко используют резьбофрезерование, так как этот метод высокопроизводителен и прост.
Резьбофрезерные станки подразделяются на станки для фрезерования длинных резьб и станки для фрезерования коротких резьб.
Станки для фрезерования резьб изготовляются в следующем исполнении: станки с перемещением фрезерной головки и станки с перемещением стола с изделием.
Станки для фрезерования коротких резьб бывают универсальные, с планетарным движением фрезы и полуавтоматы.
При фрезеровании резьбы на станке осуществляются следующие движения: вращение фрезы, вращение заготовки, поступательное перемещение (заготовки или фрезерной головки). Для фрезерования резьб применяются дисковые и групповые фрезы (гребенчатые). Дисковые фрезы применяют для фрезерования длинных резьб, а групповые фрезы – для коротких.
В зависимости от вида применяемой фрезы различают способы фрезерования:
1. Последовательное фрезерование каждой нитки резьбы, инструмент – дисковая фреза. Путь инструмента соответствует длине резьбы.
2. Одновременное фрезерование всей длины резьбы групповой фрезой. Путь инструмента равен шагу резьбы.
|
|
Направление движения фрезы и изделия при наружном и внутреннем фрезеровании показаны на (рис. 2, а и б).
Рис. 2. Виды движений при фрезеровании резьбы
Зубообрабатывающие станки подразделяются на различные типы по следующим признакам:
1) назначению - для нарезания цилиндрических колес с прямыми и винтовыми зубьями, червячных и шевронных колес, зубчатых реек, конических колес с прямыми и криволинейными зубьями;
2) виду рабочего движения - зубофрезерные, зубодолбежные, зубострогальные и зубопротяжные;
3) характеру обработки - для нарезания зубьев и для чистовой обработки (отделки) зубьев.
В практике станкостроения признано целесообразным создание унифицированных станков как базовых моделей, на основе которых создаются различные модификации, в частности специальные и специализированные станки.
Зубодолбежные станки
Обработку колес на зубодолбежных станках осуществляют режущим инструментом, выполненным в виде зубчатого колеса, - долбяком. На этих станках нарезают прямозубые колеса наружного и внутреннего зацепления, а при наличии копира и косозубого долбяка - косозубые колеса. Кроме того, на станках можно нарезать блоки из нескольких колес. Достоинством станков является непрерывность работы без потери времени на подход к заготовке и выход из нее.
|
|
Нарезание зубьев производится долбяком, выполненным в виде зубчатого колеса, зубья которого имеют углы резания. Модуль долбяка принимают равным модулю нарезаемого колеса.
Обрабатываемая заготовка закрепляется на оправке стола станка, долбяк - на ползуне (штосселе) шпиндельной головки, который во время обработки делает возвратно-поступательное движение резания (главное движение) и медленное вращение вокруг своей оси (круговая подача), согласованное с вращением заготовки (движение деления и обкатки) (рис. 3).
При движении вниз долбяк делает рабочий ход, снимая стружку из заготовки, при обратном (холостом) ходе долбяка стол с заготовкой отводится системой рычагов и эксцентриком на небольшое расстояние для исключения контакта долбяка с заготовкой. К моменту начала рабочего хода стол возвращается в исходное положение.
Одновременно происходит врезание долбяка в заготовку (радиальная подача) на установленную глубину резания с помощью кулачка. По окончании врезки радиальная подача прекращается, и заготовка в течение одного полного оборота обрабатывается только с круговой подачей до полного нарезания всех зубов.
Таким образом, для образования прямого зуба необходимы такие формообразующие движения:
1) (В1В2) – вращение долбяка (круговая подача) и согласованное с ним вращение заготовки (движение обкатки и деления) – для образования эвольвентного профиля;
2) (Пз) – поступательное движение долбяка (главное движение) – для получения формы зуба по длине;
3) (П4) – радиальное перемещение долбяка (радиальная подача) – для получения полной высоты зуба;
4) (П5) – отвод стола с заготовкой при обратном (холостом) ходе долбяка – для исключения контакта долбяка с заготовкой.
Рис. 3. Структурно-кинематическая схема зубодолбежного станка
iv - узел настройки возвратно-поступательного движения долбяка; ix - узел настройки цепи обкатки (вращение долбяка и вращение стола с заготовкой); is к - узел настройки круговой подачи; is р - узел настройки радиальной подачи;
i см - счетный механизм
В зависимости от величины модуля, точности и шероховатости боковых поверхностей зубов колеса, его обработка осуществляется за один, два или три прохода путем установки соответствующих кулачков (рис.4).
Рис. 4. Кулачки зубодолбежного станка:
а – однопроходный; б – двухпроходный;
в – трехпроходный
Настройка станка на нарезание косозубых колес не отличается от обычной. В этом случае устанавливают копиры с винтовой направляющей (рис. 5), которые сообщают долбяку дополнительное вращение. В результате вращательного и возвратно-поступательного движения зубья долбяка будут перемещаться по винтовой линии, угол наклона которой должен быть равен углу наклона винтовой линии зубьев нарезаемого колеса.
Рис. 5. Схема нарезания зуборезным долбяком винтовых зубьев
У цилиндрического колеса
Дата добавления: 2019-02-13; просмотров: 614; Мы поможем в написании вашей работы! |
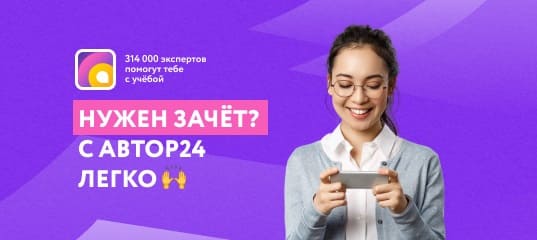
Мы поможем в написании ваших работ!