Этапы развития автоматизации и механизации.
Автоматизация производственных процессов
ВВЕДЕНИЕ
Автоматизация производства — механизация производства с полным или частичным устранением физического труда рабочих. В процессе автоматизации труд людей замещается работой оборудования, действующего по принципу саморегуляции. По английски: Automazed of works … Финансовый словарь
Автоматизация производства— призвана устранить физически тяжелый, монотонный труд, переложив его на плечи машин. … Экономический словарь
Автоматизация производства — процесс в развитии машинного производства, при котором функции управления и контроля, ранее выполнявшиеся человеком, передаются приборам и автоматическим устройствам; … Большой медицинский словарь
Автоматизация производства— способ орг- ции произ- ва, при к- ром ф- ции управления и контроля, ранее выполнявшиеся человеком, передаются автоматич. устройствам. Цель А. п. - повышение производительности и улучшение условий труда, обеспечение высокого качества продукции, оптим.… … Большой энциклопедический политехнический словарь
Автоматизация производства — осуществление технологических механизированных производственных процессов с помощью устройств (приборов, аппаратов) для автоматического контроля, управления или регулирования этих процессов без непосредственного участия оператора (машиниста).… Строительный словарь
|
|
Комплексная автоматизация производства — методология автоматизации производственных процессов с помощью компьютеров. Комплексная автоматизация объединяет проектные работы, технологические средства, системы планирования, контроля, управления и учета. По английски: Complex automation… … Финансовый словарь
Автоматизация— применение машин, машинной техники и технологии с целью облегчения человеческого труда, вытеснения его ручных форм, повышения его производительности. Автоматизация производства призвана устранить физически тяжелый, монотонный труд, переложив его на плечи машин.2010… …Экономический словарь
Основа автоматизации технологических процессов — это перераспределение материальных, энергетических и информационных потоков в соответствии с принятым критерием управления (оптимальности).
1.ОБЩИЕ ПОЛОЖЕНИЯ АВТОМАТИЗАЦИИ ПРОИЗВОДСТВЕННЫХ ПРОЦЕССОВ.
1.1.Основные понятия и терминология.
Автоматизация производства- - процесс в развитии машинного производства, при котором функции управления и контроля, ранее выполнявшиеся человеком, передаются приборам и автоматическим устройствам. А. п. — основа развития современной промышленности, генеральное направление технического прогресса. Цель А. п. заключается в повышении эффективности труда, улучшении качества выпускаемой продукции, в создании условий для оптимального использования всех ресурсов производства. Различают А. п.: частичную, комплексную и полную.
|
|
Предшествует автоматизации –механизация(совершенствование орудий труда).Ручной деревообрабатывающий станок – примет частичной механизации. Универсальный токарный станок – пример полной механизации.
Частичная А. п., точнее — автоматизация отдельных производственных операций, осуществляется в тех случаях, когда управление процессами вследствие их сложности или скоротечности практически недоступно человеку и когда простые автоматические устройства эффективно заменяют его. Частично автоматизируется, как правило, действующее производственное оборудование (универсальное). По мере совершенствования средств автоматизации и расширения сферы их применения было установлено, что частичная автоматизация наиболее эффективна тогда, когда производственное оборудование разрабатывается сразу как автоматизированное. Это связано с тем, что если автоматизировать уже существующий механизм, то в результате получается излишне сложный автомат. К частичной А. п. относится также автоматизация управленческих работ. Пример ч.А.п. является станок –автомат (токарный прутковый)
|
|
При комплексной А. п. участок, цех, завод функционируют как единый взаимосвязанный автоматизированный комплекс. Комплексная А. п. охватывает все основные производственные функции предприятия, хозяйства, службы; она целесообразна лишь при высокоразвитом производстве на базе совершенной технологии и прогрессивных методов управления с применением надёжного производственного оборудования, действующего по заданной или самоорганизующейся программе, функции человека при этом ограничиваются общим контролем и управлением работой комплекса.
Полная А. п. — высшая ступень автоматизации, которая предусматривает передачу всех функций управления и контроля комплексно-автоматизированным производством автоматическим системам управления. Она проводится тогда, когда автоматизируемое производство рентабельно, устойчиво, его режимы практически неизменны, а возможные отклонения заранее могут быть учтены, а также в условиях недоступных или опасных для жизни и здоровья человека.
|
|
При автоматизации или при определении ее степени учитывают прежде всего её экономическую эффективность и целесообразность в условиях конкретного производства. А. п. не означает безусловное полное вытеснение человека автоматами, но направленность его действий, характер его взаимоотношений с машиной изменяется; труд человека приобретает новую качественную окраску, становится более сложным и содержательным. Центр тяжести в трудовой деятельности человека перемещается на техническое обслуживание машин-автоматов и на аналитически-распорядительную деятельность.
Работа одного человека становится такой же важной, как и работа целого подразделения (участка, цеха, лаборатории). Одновременно с изменением характера труда изменяется и содержание рабочей квалификации: упраздняются многие старые профессии, основанные на тяжёлом физическом труде, быстро растет удельный вес научно-технических работников, которые не только обеспечивают нормальное функционирование сложного оборудования, но и создают новые, более совершенные его виды.
Этапы развития автоматизации и механизации.
Анализируя историю и тенденции развития (эволюцию) автоматизации производственных процессов, можно отметить
пять основных исторических этапа развития, на которых реша-
лись различные по своей сложности задачи.
1) -совершенствование орудий труда, создание механизмов, в том числе универсальных механизмов (универсальных станков).
2) –атоматизация рабочего цикла изготовления обьекта , создание машин –автоматов и полуавтоматов;
3) – обьединение систем машин, создание автоматических комплексов, линий , модулей.;
4) – комплексная автоматизация с созданием автоматических цехов и заводов;
5) – создание гибкого автоматизированного производства с автоматизацией серийного и мелкосерийного производства, инженерного и управленческого труда.
--------------
– применение нано-технологий (выращивание деталей и т.д.)
История развития А. п.
Самодействующие устройства — прообразы современных автоматов — появились в глубокой древности . Однако в условиях мелкого кустарного и полукустарного производства вплоть до 18 в. практического применения они не получили и оставаясь занимательными «игрушками», свидетельствовали лишь о высоком искусстве древних мастеров. К этому времени относится изобретение Нартовым ножного деревообрабатывающего станка. Совершенствование орудий и приёмов труда, приспособление машин и механизмов для замены человека в производственных процессах вызвали в конце 18 в. — начале 19 в. резкий скачок уровня и масштабов производства, известный как промышленная революция 18—19 вв.
Промышленная революция создала необходимые условия для механизации производства : в первую очередь прядильного, ткацкого, металло- и деревообрабатывающего.. Важнейшими изобретениями этого периода стали изобретения русским механиком И. И. Ползуновымавтоматического регулятора питания паровогокотла (1765) и английским изобретателем Дж. Уаттом центробежного регулятораскорости паровой машины (1784).Паровая машина становится после этого основным источником механической энергии для привода станков, машин и механизмов.
С 60-х гг. 19 в., в связи с быстрым развитием железных дорог, стала очевидна необходимость автоматизации железнодорожного транспорта и прежде всего создания автоматических приборов контроля скорости для обеспечения безопасности движения поездов. В России одними из первых изобретений в этом направлении были автоматический указатель скорости инженера-механика С. Прауса (1868) и прибор для автоматической регистрации скорости движения поезда, времени его прибытия, продолжительности остановки, времени отправления и местонахождения поезда, созданный инженером В. Зальманом и механиком О. Графтио (1878). О степени распространения автоматических устройств в практике железнодорожного транспорта свидетельствует то, что на Московско-Брестской железной дороге уже в 1892 существовал отдел «механического контроля поездов».
Учение об автоматических устройствах до 19 в. замыкалось в рамки классической прикладной механики, рассматривавшей их как обособленные механизмы. Основы науки об автоматическом управлении по существу впервые были изложены в статье английского физика Дж. К. Максвелла «О регулировании» (1868) и труде русского учёного И. А. Вышнеградского «О регуляторах прямого действия» (1877), в котором впервые регулятор и машина рассматривались как единая система. А. Стодола, Я. И. Грдина и Н. Е. Жуковский, развивая эти работы, дали систематическое изложение теории автоматического регулирования.
С появлением механических источников электрической энергии — электромашинных генераторов постоянного и переменного тока (динамомашин ) и электродвигателей оказалась возможной централизованная выработка энергии, передача её на значительные расстояния и дифференцированное использование на местах потребления. Тогда же возникла необходимость в автоматической стабилизации напряжения генераторов, без которой их промышленное применение было ограниченным. Лишь после изобретения регуляторов напряжения с начала 20 в. электроэнергия стала использоваться для привода производственного оборудования. Наряду с паровыми машинами, энергия которых распределялась трансмиссионными валами и ремёнными передачами по станкам, постепенно распространялся и электропривод, вначале вытеснивший паровые машины для вращения трансмиссий, а затем получивший и индивидуальное применение, т. е. станки начали оснащать индивидуальными электродвигателями.
Переход от центрального трансмиссионного привода к индивидуальному в 20-х гг. 20 в. чрезвычайно расширил возможности совершенствования технологии механической обработки и повышения экономического эффекта. Простота и надёжность индивидуального электропривода позволили механизировать не только энергетику станков, но и управление ими. На этой основе возникли и получили развитие разнообразные станки-автоматы, многопозиционные агрегатные станки и автоматические линии. Широкое применение автоматизированного электропривода в 30-е гг. 20 в. не только способствовало механизации многих отраслей промышленности, но по существу положило начало современной А. п. , тогда же возник и сам термин «Автоматизацияпроизводства».
В 1936 Д. С. Хардер (США) определял автоматизацию как «автоматическое манипулирование деталями между отдельными стадиями производственного процесса». По-видимому, вначале этим термином обозначали связывание станков с автоматическим оборудованием , передачей и подготовкой материалов. Позднее Хардер распространил значение этого термина на каждую операцию производственного процесса.
1.3. Организационно-технологические особенностиавтоматизации и механизации технологических процессов.
Первый этап автоматизации сопровождается появлением универсальных станков. Они состоят из трех основных механизмов: двигательного (привод), передаточного (кинематическая цепь) и исполнительного. Основным является исполнительный механизм, определяющий технологические возможности станка. Исполнительные механизмы м/р станка могут совершать движения как связанные непосредственно с процессом обработки: вращение детали, рабочая подача инструмента- так и не связанные с обработкой: зажим и разжим детали, быстрый подвод и отвод инструмента и т.д. В соответствии с этим , с точки зрения выполнения заданного технологического процесса, все перемещения механизмов можно разделить на рабочие и холостые. Рабочими перемещениями илиходами называют движения, во время которых производится непосредственно обработка на станке. Холостыми перемещениями или ходами называются вспомогательные движения , которые служат для подготовки рабочих ходов (загрузка, ориентация и зажим заготовки; подвод, ориентация и отвод инструмента и.т.п.). Обработка одного изделия требует обычно полного комплекса рабочих и холостых ходов. Таким образом время одного цикла работы машины и для обработки одного изделия определяется:
(1.1)
Зависимость (1.1) является одной из основополагающих при оценке эффективности оборудования и технологичности операции. Если станок может самостоятельно выполнять кроме рабочих но и холостые хода, то он называется автоматом. В связи с тем, что при автоматизации решается задача так же повышения производительности производственных процессов, то в соответствии с (1.1) необходимо минимизировать время цикла:
Это достигается следующими методами:
а) увеличение режимов резания – n, S;
б) совмещения tp и tx ;
в) применение многоинструментальной обработки ;
г) многопозиционная обработка на многошпиндельных автоматах – обрабатывающих центрах.
На рис.1.1 показана структура пруткового автомата.
На рис.1.1: 1 – продольный суппорт, 2 …4 – поперечные суппорта; 5 – резьбонарезное приспособление; 6 - механизм подачи прутка; 7 – механизм зажима прутка; 8 – механизм поворота шпиндельного блока; 9 – механизм фиксации; 10 – распределительный вал; 11 – тормоз; 12 – механизм выключения при отсутствии прутка.
Точность положения шпиндельного блока во время обработки обеспечивается механизмом фиксации. Управление циклом обработки построено на механической основе с помощью распределительного вала с кулачками, каждый из которых управляет соответствующим механизмом.
На третьем этапе автоматизации создаются системы машин – автоматические линии, выполняющие разнообразные операции обработки и контроля. Автоматической линией называется автоматическая система машин, расположенных в технологической последовательности , объединенных средствами межоперационной транспортировки, управления и автоматически выполняющих комплекс операций кроме наладки.
С точки зрения зависимости (1.1) в условиях автоматической линии рабочие движения выполняют отдельные автоматы (операции обработки, контроля и сборки). Холостые перемещения выполняют механизмы межстаночной транспортировки, накопления, ориентации, позиционирования и т.д.
Создание автоматических линий потребовало решения более сложных организационно-технологических задач. Первая
из них – создание автоматической системы межстаночной транспортировки детали с учетом неодинакового цикла обработки на отдельных автоматах, а так-же несовпадения по времени их простоев из-за возникающих неполадок. Система межстаночной транспортировки должна включать в себя магазины – накопители межоперационных заделов, устройства аварийной блокировки на случай неполадок (поломка механизма, износ инструмента…) Создание автоматических линий потребовало также создание систем активного контроля с корректировкой работы оборудования. Автоматические линии относятся к специальным средствам автоматизации, проектируются и создаются для конкретных технологических процессов и эффективны в условиях массового производства. Экономический эффект достигается за счет повышения производительности, сокращения затрат на ручной труд на вспомогательных операциях. Структурная схема автоматической линии представлена на рис.1.2.
На рис.1.2: 1,2,…,4 – автоматы; 5- накопители заделов; 6- поворотные столы; 7 – механизмы ориентации; 8 – механизмы зажима и фиксации; 9 – транспортеры; 10 – накопители заделов; 11 – кантователи; 12 – механизмы удаления стружки; 13 ,14 ,…,17 – пульт управления, командоаппарат, гидропанель управления, искатель неполадок.
Четвертым этапом автоматизации является комплексная автоматизация производственных процессов – создание автоматических цехов и заводов. С точки зрения зависимости (1.1) рабочий ход в условиях цеха или завода выполняет каждая автоматическая линия. Здесь решаются задачи автоматизации межлинейной и межцеховой транспортировки, складирования, уборки и переработки стружки, диспетчерского контроля и управления производством. Система межлинейного и межцехового транспорта реализуется с помощью транспортеров (как правило портального исполнения), элеваторов , конвейеров с автоматическим адресованием.
Пятым этапом автоматизации технологических процессов
является создание гибких производственных систем, в том числе со сменным обьектом производства для мелкосерийного и единичного производства. Автоматические линии, цеха и заводы целесообразны для применения в массовом и крупносерийном производстве. В связи с изменением стратегии производства на изготовление небольших партий деталей с различными потребительскими качествами более эффективным является гибкое автоматическое производство.
Гибкое производство – комплексное понятие , включающее в себя целый ряд компонентов.
Машинная гибкость – легкость перестройки технологических элементов ГАП для изготовления заданного множество типа деталей.
Гибкость процесса – способность производить заданное множество типов деталей , в том числе из различных материалов , разными способами.
Гибкость по продукту – способность быстрого и экономичного переключения на производство нового продукта.
Маршрутная гибкость – способность продолжать обработку заданного множества типов деталей при отказах отдельных технологических элементов ГАП.
Гибкость по объему – способность ГАП экономически выгодно работать при различных обьемах производства
Гибкость по расширению – возможность легкого расширения ГАП за счет введения новых технологических элементов.
Использование ГАП в мелкосерийном производстве дает непосредственный экономический эффект за счет высвобождения персонала и увеличения сменности работы технологического и управляющего оборудования. Обычно в первую смену производится загрузка заготовок, материалов, инструмента, тех.заданий СУ ГАП. Вторую и третью смену ГАП работает самостоятельно под наблюдением диспетчера.
Гибкое производство связано обычно с частым обновлением выпускаемых изделий. Жёсткие автоматические линии не допускают смену номенклатуры изделий, поэтому получают распространение секционные линии, составляемые из независимых агрегатных многооперационных станков, которые объединяются транспортёрами, элеваторами и конвейерами, оснащёнными механическими «пальцами» и «руками». Группы таких станков образуют секции и параллельные линии. При этом у каждого станка создаётся некоторый запас деталей для постоянной загрузки главного конвейера линии; уход за станками и смена инструмента производятся без её остановки. Станки делают блочными, с взаимосвязанными узлами, у которых сохраняются силовые установки, каретки и заменяются только приспособления, инструмент и некоторые блоки, зависящие от конструктивных особенностей изделия. У металлообрабатывающих станков с программным управлением полный автоматизм рабочего цикла достигается при сохранении универсальности станка: при обработке деталей различной конфигурации заменяется лишь программа, записанная на перфорированной или магнитной ленте.
Дата добавления: 2019-02-12; просмотров: 1121; Мы поможем в написании вашей работы! |
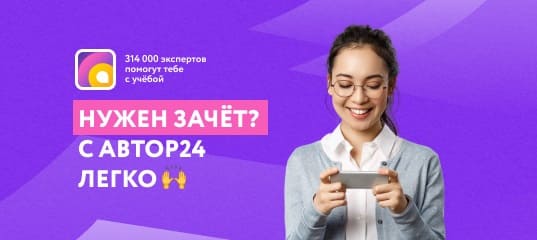
Мы поможем в написании ваших работ!