ИНДИВИДУАЛЬНОЕ ЗАДАНИЕ И ПОРЯДОК ВЫПОЛНЕНИЯ РАБОТЫ
Министерство науки и образования Украины
Николаевский кораблестроительный университет имени адмирала Макарова Кафедра “Материаловедение и технологии материалов”
ПРОЕКТИРОВАНИЕ ПРЕСС-ФОРМ ДЛЯ ПРЕССОВАНИЯ ИЗДЕЛИЙ ИЗ ПОРОШКОВЫХ МАТЕРИАЛОВ
Выполнил: студент группы 3131
Догиль В.А.
Николаев 2014
П РОЕКТИРОВАНИЕ ПРЕСС-ФОРМ ДЛЯ ПРЕССОВАНИЯ ИЗДЕЛИЙ ИЗ ПОРОШКОВЫХ МАТЕРИАЛОВ
Цель работы: изучить метод проектирования и приобрести навыки расчета инструмента для прессования изделий из порошковых материалов.
ВВЕДЕНИЕ
Разработка изделий из порошковых материалов (ПМ) связана с формованием. На этой стадии дисперсное, сыпучее тело приобретает свойства твердого. Для проведения операции формования применяют различные инструменты: пресс-формы, которые устанавливают на прессах, экструдеры инжекционных и иных установок, прокатные валки станов для получения лент и листов. Все группы инструмента характеризуются определенными требованиями к поверхности (твердости), прочности (на изгиб, сжатие, кручение, растяжение). Существуют требования по долговечности и теплостойкости деталей оснастки и специфические свойства, например немагнитность и т.п. В связи с этим имеет значение освоение студентами соответствующих методов проектирования. Они позволяют подготовить и использовать необходимые данные для разработки, конструирования и расчета оснастки ПМ. В методических указаниях в качестве объекта проектирования используется пресс-форма для изготовления детали типа “втулка с буртом”, приводятся примеры, иллюстрации и методология. При выполнении индивидуальных заданий строго необходимо выполнять идентичность требований к разработкам конструкторских, технологических, исследовательских и расчетных проектов, изложенных в ЕСК(Т)Д РФ и СТП 1- V-НГТУ-93.
|
|
КРАТКИЕ СВЕДЕНИЯ ИЗ ТЕОРИИ
2.1. Принципы конструирования пресс - форм для холодного прессования металлических порошков
Холодное прессование в закрытых пресс-формах состоит из операций дозировки шихты, засыпки шихты в полость пресс-формы, прессования изделия, выдержки под давлением и выталкивания спрессованного изделия. Все операции проводятся в одной оснастке. Конструкции пресс-форм зависят от эксплуатационных особенностей - стационарные и съемные; от вида заполнения полости матрицы порошком - с весовой или объемной дозировкой; по принципу уплотнения - односторонние, двухсторонние; по конструкции матрицы - со сплошной или составной; по количеству формующихся
|
|
одновременно изделий - одно- и многогнездные; по роду применяемых прессов
- специализированные и универсальные; по количеству слоев прессуемого изделия - одно- и многослойные; по контролю за ходом прессования - прессование до упора или по окончательному давлению; по сложности конфигурации прессуемого изделия - для прессования изделий определенной группы сложности. Многообразие конструкционных признаков позволяет при прессовании порошка получить структуру, плотность, пористость и прочность формовки, пригодную для спекания, и затем обеспечить требуемый комплекс свойств изделия. Отнесение изделий к определенной группе сложности производят по параметрам табл. 1 и рис. 1, а классификацию элементов закрытых пресс -форм - по табл. 2. Для снижения трудоемкости изготовления всего изделия из ПМ поверхности формовки после спекания не дорабатывается резанием, если необходимо, спеченное изделие калибруют в специальной пресс- форме. Поэтому к пресс-формам ПМ выдвигают жесткие требования по соосности, радиальному биению, жесткости и чистоте обработке рабочей поверхности, унификации пресс-форм, пресс-блоков и опорных частей.
Особыми являются ограничения по жесткости. Толщина стенки матрицы должна обеспечить достаточную жесткость и минимальную упругую деформацию под действием бокового давления. Напряжения изгиба в стержне, возникающие при прессовании должны быть значительно меньше максимальных допустимых напряжений.
|
|
Зазор между подвижными элементами пресс-форм должен обеспечить надежное перемещение пуансонов относительно матрицы и стержня, заданную точность изделия и исключить попадание порошка в пространство между подвижными элементами. Это возможно при зазоре, меньше минимального размера частиц порошка. Точность изготовления деталей пресс - формы должна быть на класс выше точности, требуемой при изготовлении изделий.
Для изделий IV и V групп сложности, имеющих переходы по высоте, применяют составные пуансоны с независимо перемещающимися элементами или проводят формование выступающих элементов изделия на неподвижных деталях пресс-формы (матрица или стержень). Изделия VI и VII групп сложности имеют большое число переходов по высоте. Для обеспечения равномерного распределения плотности применяют составные верхние и нижние пуансоны. После образования замкнутой полости матрицей и составными пуансонами производится перемещение порошка в полость, образованную верхними пуансонами, подпрессовка буртов, уплотнение нижней и верхней частей изделий и его полное уплотнение. При необходимости создания кольцевых пазов формующему пуансону необходимо придать конусообразную форму с обеих сторон с углом наклона образующей
|
|
до 5 - 100.
Таблица 1
Классификация порошковых конструкционных изделий по группам сложности
Группа слож- ности | Характеристика сечения изделия по высоте (вдоль оси прессования) | Характеристика ограничивающих по высоте изделия поверхностей | Отношение высоты изделия к минимальной толщине стенки |
I | Неизменное сечение без отверстия | Параллельные плоскости | 1 - 3 |
II | То же, с одним или несколькими отверстиями в направлении прессования | То же | 8 - 10 |
III | То же | То же | 8 - 10 |
IV | Изделие с наружным или внутренним буртом | То же | 6 - 8 |
V | То же | То же | 6 - 8 |
VI | Изделия с несколькими переходами по высоте | То же | _ |
V I I | Несколько наружных или внутренних переходов при наличии отверстий в направлении прессования | Непараллельные плоскости или криволинейные поверхности, пересекающие ось прессования | _ |
Внешнее давление пресса в системе “порошок - матрица - пуансоны - стержень” создает группу сил, природа которых обусловлена многообразием свойств дисперсного тела. Порошок способен передавать боковое давление, как жидкость, но в отличие от большинства жидких и твердых тел значительно (в 2...3 раза) уменьшает свой объем, пластически деформируется и отличается резким проявлением сил трения на рабочих поверхностях элементов.
Совокупность этих факторов приводит к неравномерной плотности по сечению формовки.
Классификация элементов закрытых пресс - форм.
Таблица 2
Группа сложности | Характеристика подвижности элементов пресс-формы относительно матрицы |
Характеристика элементов пресс - формы | |||
Пуансон нижний | Стержень | Матрица | Пуансоны | Стержень | |
I | Неподвиж- ный | _ | Без переходов по высоте | Несостав- ные | То же |
II | Подвижный | Неподвиж- ная | То же | То же | Без перехо- дов по высоте |
III | То же | Подвижная | То же | То же | То же |
IV | То же | Неподвиж- ная | То же | Нижний - составной | То же |
V | То же | Подвижная | Неболь- шое изменение сечения по высоте для формова- ния буртов | То же | То же |
VI | То же | С переходам и по высоте | Составные | То же | |
VII | То же | Подвижная | То же | То же | То же |
Распределение плотности зависит от кинематической схемы прессования. Предпочтительно двухстороннее прессование. Условие достижения
равномерной плотности в данном сечении изделия определяют через коэффициент уплотнения (Ку):
Ку = H / h = H 1 / h 1 = g1/gн
где Н, Н1 - высота слоя порошка в пресс-форме в соответствующих сечениях; h,
h1 - высота изделия в этих же сечениях; g1,gн - плотность спрессованного изделия и насыпная плотность порошка.
Рис.1. Классификация прессуемых изделий по группам сложности
Для улучшения равномерности распределения плотности в местах переходов от одного сечения изделия к другому предусматривают фаски на пуансонах или неподвижных элементах и обеспечивают приложение усилий к составным пуансонам, пропорциональные площади проекций элементов прессуемой детали. В последнем случае уплотнение протекает равномерно, без “перетекания” порошка между полостями.
На рис. 2 показана схема пресс-формы для холодного прессования из металлического порошка детали типа “втулка с наружным буртом”. Матрица
1 - сплошная. Части 7 и 9 соединены между собой резьбовым соединением, при помощи которого производится регулировка перемещения матрицы. Регулировка высоты Н1 осуществляется нижним пуансоном 12, а высоты Н2 нижним пуансоном 10 с помощью упора 11. Упор 7 производит регулирование хода матрицы и остановку ее в определенном положении относительно нижнего пуансона в конце процесса прессования. Матрица подвешена на пружине 8 для осуществления двухстороннего прессования. Стержень 6 в процессе прессования неподвижен. При прессовании в системе “порошок - матрица - верхний пуансон 3” за счет сил трения о стенки матрицы происходит прочное сцепление элементов системы, матрица опускается вниз,
производя окончательное формование. Выталкивание осуществляется нижними пуансонами. Кольцо 4, закрепленное болтами 5, удерживает матрицу при выталкивании формовки 2.
Рис. 2. Конструкция и схема регулировки высот засыпки порошка в стационарной пресс-
форме для формования втулки с наружным буртом
2.2. Расчет размеров пресс-форм
Исходными данными для расчета размеров пресс - форм являются величины:
- размеры готового изделия (высота h, поперечный размер D, размер отверстия
d) и допуски D на них;
- плотность готового изделия и ее пределы (нижний g1, верхний g2);
- упругие последействия по линейным размерам после прессования в % aп или по абсолютной величине lп;
- объемная усадка (или рост) по линейным размерам при спекании в процентах
b или в абсолютной величине e;
- увеличение (или уменьшение) площади поперечного сечения при спекании в процентах c;
- припуск (положительный или отрицательный) на калибрование линейных
размеров Пк;
- упругие последействия по линейным размерам после калибрования (или
допрессовки) в процентах aк или в абсолютных единицах lк;
- увеличение (или уменьшение) площади поперечного сечения после
калибрования (или допрессовки) в процентах y;
- прирост плотности при калибровании (или допрессовке) спеченного изделия в процентах t;
- уменьшение веса изделия при спекании за счет выгорания смазок,
восстановления окислов и пр. в % x.
Выше перечисленные величины определяются опытным путем или выбираются по таблицам. При проектировании пресс-формы учитываются абсолютные величины допусков готового изделия. Здесь возможны два момента: когда они в совокупности пренебрежимо малы в сравнении с значением допуска детали или, наоборот, перекрывают его. В первом случае значения технологических параметров в расчеты не включают. Для оценки используют формулы:
(+Dmax) - (lп + e + Пк + DD) = 0 ; ( | - Dmin |) - (lп + e + Пк - DD) = 0 ,
где DD - припуск на износ инструмента (он не учитывается для горизонтальных поверхностей). Если условие не выполняется то размеры элемента оснастки изменяют на величину получаемой разницы.
2.1.1. Определение высоты загрузочной камеры
Ее высота Н определяется по формуле: Н = k * hпр, где k - коэффициент обжатия; hпр - высота спрессованного изделия. Величину k вычисляют по среднеарифметическому значению gпр. Если известно значение интервала пористости (П), для расчета k применяют величину gпр, определяемую по формуле gпр = gк (1 - П / 100), где gк - удельный вес компактного материала. При прессовании изделий, имеющих вертикальные переходы, высота слоя засыпанного порошка определяется для каждого из участков прессовки. Высоту прессовки рассчитывают по формулам:
- в случае роста при спекании:
hпр = hcп[(100-х)/100][(100+x)/100](gсп.ср/gпр)
- в случае усадки:
hпр = hcп[(100+х)/100][(100+x)/100](gсп.ср/gпр),
где gсп.ср. - средняя плотность спеченного изделия.
2.1.2. Определение общей высоты матрицы
Она определяется по формуле Нм = Н + hв + hн, где hв - величина захода в матрицу верхнего пуансона, hн - величина захода в матрицу нижнего пуансона. В стационарных пресс-формах, где матрица служит дозирующим устройством, нет необходимости предусматривать величину hв.
Здесь Нм = Н1 + Н2 + hн.
2.1.3. Расчет размеров рабочей полости матрицы
Если задан конечный размер изделия с допусками Dmin и Dmax, то определение номинального размера рабочей полости матрицы ведут по выражению Dм = Dmax - lп ± e ± Пк - lк..
Припуск на износ матрицы рассчитывают
DD = (Dmin - lп ± e ± Пк - lк) - Dм - Ам,
где Ам - действительный допуск отверстия матрицы при ее изготовлении.
2.1.4. Определение размеров стержня
Если известны конечные размеры отверстия детали ПМ Dmin и Dmax, то номинальный размер рабочей части стержня
dст = dmax ± lп ± e ± Пк ± lк.
Припуск на износ стержня Dd = dст - (dmin ± lп ± e ± Пк ± lк) - Аст.
где Аст - действительный допуск стержня при его изготовлении в абсолютном
значении.
2. 2. Расчет деталей пресс - форм на прочность
Главным условием изготовления качественных деталей из ПМ и КМ является жесткость элементов оснастки. Поэтому необходимо проверять это условие проводя расчеты давления прессования.
2.2.1. Расчет давления прессования.
Полное давление прессования складывается из затрат давления на уплотнение порошка и потерь давления на внешнее трение частиц о стенки матрицы: Робщ = Pтр + Р.
Для определения давления, идущего на уплотнение порошка, используют
формулы Ждановича, Канина и Юрченко, Бальшина, Николаева. Формула Николаева, выведенная на основе предположения, что при достаточно больших давлениях формование прессовки происходит за счет истечения металлических частиц в поры, имеет вид Р=ss C r ln(r/(1-r)),
где ss - пределы текучести металлических порошков: железа 200 Па, алюминия
35 Па, стали 400 Па, меди 80 Па; r = gпр/gк - относительная плотность ; С = 2,5
... 3 - постоянный коэффициент.
Формула Николаева применима для расчетов в интервале плотностей свыше 50% и не равной 100% теоретической плотности.
Потеря давления на внешнее трение Ртр = f * Pбок * (Sт/S),
где f - коэффициент трения порошка о стенки матрицы пресс-формы;
Pбок - боковое давление; Sт - площадь поверхности трения; S - площадь поперечного сечения изделия. Значение бокового давления для интервала плотности от 0.5 до 1 теоретической определяется по приближенной формуле Рбок = (0,3 ... 0,4)Росевое. Величина коэффициента трения f для “сухих” металлических порошков без специальных добавок колеблется от 0,06 до 0,20.
Добавки твердых смазок в смесь для прессования (графита) снижает f в 2...3 раза, а введение стеариновой кислоты, индустриального масла, глицерина - в
1,5 ... 5 раз. Смазки повышают чистоту поверхности прессовки.
На стадии выталкивания в крайних сечениях изделия на кромке матрицы возникают “упругие последействия”, вызванные разницей в радиальных упругих силах, что может вызвать трещины. Влияние упругого последействия уменьшается снижением удельного давления формования, введением смазок, закруглением острых кромок матрицы и увеличением скорости выталкивания. Для большинства металлических порошков и давлений прессования от 400 до
1000 МПа величина упругого последействия не превышает 4% от допуска детали.
Часто на практике для расчета давления используют экспериментальные значения Руд, определяемого по методике ГОСТ 25280-82.
2.2.2. Расчет матриц
Матрица представляет собой цилиндр, нагруженный внутренним давлением на части его длины. Матрицы изготавливаются с обжимающей обоймой и без, разделяются на составные (из нескольких несимметричных частей) и сплошные (рис. 3).
Наибольшие напряжения имеют место у внутренней поверхности. Для разрезных матриц напряжения концентрируются на внутренней поверхности обоймы, а для сплошных матриц на их внутренней поверхности. Обойму и матрицу соединяют за счет натяга горячей или прессовой посадки. Напряжения разрушения рассчитываются по зависимости sр £ sэкв = Рбок [(a2 + 1 ) / (a2- 1) +
1],
где а = rн/rв , rн и rв - наружный и внутренний радиус матрицы соответственно. Величина rв матрицы определена диаметром прессовки. Значение соотношения радиусов “а” рассчитывают по формуле
а = ([sp]/( [sp] -2Pбок))0.5.
Рис. 3. Места разреза составных матриц. Верхний ряд - неправильно, нижний - правильно.
Радиальную деформацию внутренней поверхности цилиндрической матрицы находят из выражения: Drв = [(Рбок rв) / Е] [(a2 + 1) / (a2 - 1) + m]
где m - коэффициент Пуассона. Е - модуль Юнга. rв - не может быть меньше, чем определенная величина, что следует из требования жесткости. При а® ¥
sэкв = 2 Рбок. Применение матриц с а > 4 не увеличивает жесткость. Если а больше 2, тогда переходят к составной матрице. Значение Drв задается конструктором оснастки, обычно ее принимают ±DD / с, где с = 10...20, ±DD - допуск детали. Жесткость матрицы достигается применением обойм. После сборки возникают напряжения сжатия, а в обойме - растяжения.
Рис. 4. Схема определения радиуса контактной поверхности составной цилиндрической матрицы
Значение радиуса контактной поверхности принято: r k = (rн / rв)0.5.
В расчете rk значения rн и rв определяются для наибольшего диаметра детали -
втулки. Величина контактного давления, возникающего при посадке
определяется по формуле Рк = Рбок (а-1)/[2 * (f+1)].
Величина натяга d = (2 Рбок rв) / Е.
Для диапазона бокового давления от 200 до 500 МПа и а = 2...4 пригодна
формула для подсчета толщины стенки t сжатой матрицы
t = rв (A Рбок - В),
где А = 6,67 10-4 и В = 0,33 - постоянные величины.
Толщину стенки обоймы сплошной матрицы s назначают 10...15 мм.
Для разрезных матриц используют перечисленные выражения, но боковое давление ограничивается значениями, при которых образуется зазор между вкладышами.
Расчет матриц сложной конфигурации требует математического моделирования или экспериментального определения численных величин возникающих напряжений и их распределения по толщине стенки разрезной матрицы.
2.2.3. Расчет пуансонов
При работе пуансоны подвергаются сжатию и продольному изгибу. На сжатие пуансоны проверяются по формуле sсж = Р / Sп = [scж],
где [scж] - допускаемое напряжение на сжатие для материала пуансона, Р -
усилие прессования, Sп - площадь наименьшего поперечного сечения пуансона.
При L > 3d пуансоны необходимо проверять на продольный изгиб по
формулеРкр = 2 P 2 Е Jmin / L2,
где L - длина свободной части пуансона (равна расстоянию от
пуансонодержателя до середины заходной части пуансона); Jmin - момент инерции наименьшего сечения пуансона, который для цилиндрических с отверстием пуансонов Jmin = (3.1459 / 64) (Dнар4 - Dст4),
где Dст и Dнар - диаметры стержня (детали) и наружный диаметр пуансона соответственно.
Напряжения, возникающие при продольном изгибе, будут меньше предела пропорциональности при условии P < [sи] / n, где Р - полное усилие, n - коэффициент безопасности (для пуансонов из закаленной стали n=2 ... 3). Максимальная длина свободной части пуансона
L = [(2 P 2 Е J min) / (n P)] 0.5.
Расчет стержней пресс-форм проводят, используя зависимости для пуансонов.
Исключение составляет формула момента инерции, которая для сплошных стержней имеет вид Jcтmin = (3.1459 / 64) (Dст4).
С каждой плитой пресса длина свободной части пуансонов увеличивается на толщину плиты пресса Z = (60 ... 120 мм) К, где К - номер пуансона. Первым пуансоном является пуансон формующий наружные выступы - бурт. Расчеты длины пуансонов проводят по формуле
Lп.общ = Нм[Lp] + Lн + Z. Z > Hвыт. (см. ниже.)
Величина Lн обычно составляет 25 мм (рис.2). Общая длина стержня
складывается из общей длины наибольшего пуансона и величины Z:
Lст.общ = Lп.общmax + Z.
Диаметры свободных частей деталей пресс - формы выполняются
меньшими для наружных и большими для внутренних на 0.75...1.5 мм. Сопрягаемые поверхности соединяют галтелью (радиусом).
2.3. Выбор пресса
Выбор пресса начинают с определения группы сложности детали. Для этого проводят анализ формы детали: рассчитывают число сопрягаемых поверхностей, параллельных отверстий, переходов по высоте. Затем по данным табл. 1 и 2 находят число плит, стержней и пуансонов, тип матрицы и их назначение. Далее рассчитывают:
1) мощность пресса Робщ = kРудS, коэффициент технологического запаса
(к = 1,25 ... 1,35);
2) усилие выпрессовки (выталкивания) детали Рвыт = 0,25 Робщ;
3) ход верхнего пуансона Нвп = h1 + h2, где h1 - расстояние от нижнего торца пуансона до верхнего торца матрицы, h1 = hk + hб; hk - высота кассеты питателя (50 .. 75 мм), hб - зазор безопасности (10 ... 15 мм), h2 - путь прессования;
4) расстояние между столом пресса и ползуном в верхнем положении Нр
= Нм + Нвп + h3 + h4, где h3 и h4 - толщина плит верхнего пуансона и матрицы.
Затем проверяют условие Нпр > Нр. Рассчитывают ход выталкивателя:
Нвыт = Нм gпр / gн. Определяют часовую производительность: Q = 3600 nг / tx =
3600 nг / tобщ, где tx - время одного рабочего хода; tобщ - длительность цикла
прессования; nг - число формующих гнезд пресс-формы. Совокупность
перечисленных выше расчетных величин позволяет правильно выбрать
конструкцию пресс-блока и пресса для детали ПМ.
2.4. Особенности проектирования пресс-форм для калибрования изделий порошковой металлургии
Калибрование спеченных изделий производят для устранения коробления и повышения точности размеров и плотности . Требуемая величина рабочих ходов подвижных частей прессов и пресс-форм значительно больше, чем при холодном прессовании: рекомендуется величина хода плунжера, превышающая высоту калибруемого изделия в 4 - 6 раз. Величина давления калибровки для спеченных изделий составляет: стальных 250...300 МПа, медь и алюминий
100...200 МПа. Припуск под калибрование должен быть минимальным. Изменение плотности изделий при калибровании не более 3 %.
Пк = [(1 - A)/(2 - A)]bст
A = [(D - bст)bст Н]/[ (D1 - b’ст) b’ст Н1],
где Н и Н1 - высота изделия до калибрования и после него; D и D1 - диаметр
изделия до деформации и после него; bст и b’ст толщина стенки до
калибрования и после него соответственно.
Усилие обжатия пористой заготовки определяется ее материалом, его плотностью смазкой, чистотой обработки материала матрицы и стержня пресс- формы, а также формой выходных кромок матрицы и стержня. Входная кромка выполняется конусной 1 ... 2 0.
2.5. Материалы для изготовления пресс-форм
Результаты расчета деталей пресс-форм на прочность используются для выбора материала элементов оснастки. Пресс-форма ПМ и КМ, используемая в производстве, представляет собой сложный механизм, состоящий из большого количества деталей. В зависимости от выполняемых функций, нагружения изделий ПМ (табл. 4), серийности производства прессовок их разделяют на группы.
Таблица 3
Материалы для изготовления деталей пресс-форм, предназначенных для холодного формования порошков и допрессовки спеченных умереннонагруженных изделий в cреднесерийном производстве ПМ*
Детали пресс - форм | Рекомендуемый материал для изготовления деталей пресс-форм | Твердость, HRC | sсж, МПа | sр, МПа | sи, МПа |
Матрицы | 9ХС, 5ХНМ, 5ХНТ, 7Х3, ХВГ | 55 - 60 HRC | 900 | 800 | 1200 |
Пуансоны | 9ХС, 5ХНМ, 5ХНТ, 7Х3, ХВГ | 50 - 55 HRC | 1500 | 1200 | 1800 |
Стержни | Х12М, Х12Ф, 5ХНМ, 5ХНВ | 52 - 56 HRC | 2100 | 1800 | 2500 |
Вспомогатель- ные рабочие детали | Ст. 40Х, Ст.45, Ст. 40 | 40 - 45 HRC | 600 | 550 | 800 |
* Модуль Юнга принимают Е=220000 МПа; коэффициент Пуассона m=0,33.
Таблица 4
Характеристика порошковых общемашиностроительных деталей.
Группа плот- ности | Степень нагруженности | П, % | бв относит.,% | d относит., % |
1 | Малонагруженные | 25 - 16 | 30 - 45 | 25 - 35 |
2 | Умереннонагруженные | 15 - 10 | 45 - 65 | 35 - 60 |
3 | Средненагруженные | 9 - 2 | 65 - 95 | 60 - 90 |
4 | Тяжелонагруженные | < 2 | 95 - 100 | 90 - 100 |
ИНДИВИДУАЛЬНОЕ ЗАДАНИЕ И ПОРЯДОК ВЫПОЛНЕНИЯ РАБОТЫ
Индивидуальное задание выдает преподаватель (указывает материал металлического порошка и номер варианта). Студент, используя содержание кратких сведений из теории, данные таблиц, соблюдая последовательность изложения разделов настоящих методических указаний, выполняет проектные расчеты пресс-формы для детали типа “втулка с буртом”.
Рис. 5. Эскиз детали втулка с буртом
Студент чертит на миллиметровой бумаге в масштабе 1:1 эскиз порошковой детали и в масштабе 1:10...20 схему пресс-формы. Исходные данные варианта выбирает по табл. 5 (расшифровка обозначений представлена выше). Затем проводит требуемые расчеты. Полученные результаты используются для выбора конструкции пресса (характеристика по данным табл. 1 и 2) и материалов для деталей оснастки (данные табл. 3 и справочников). Рекомендуется для этой же цели использовать “Программный комплекс выбора марки машиностроительной стали © ® 970062”.
Таблица 5
|
Для всех вариантов индивидуальных заданий общими являются данные:
- среднесерийное производство деталей ПМ. Деталь прессуют, спекают и калибруют;
- умеренное нагружение изделий при эксплуатации - пористость П = 8...10%;
- допуски на детали: линейные размеры ± 0.25 мм и диаметры ± 0.18 мм;
- величина заходной части нижних пуансонов 10...15 мм, пресс-форма одногнездная;
- объемная усадка при спекании по линейным размерам b = 2%;
- уменьшение площади поперечного сечения при спекании в процентах c = 2%;
- действительные допуски пресс-формы Аст = - 0,01 мм, Ам = +0,012 мм;
- припуск положительный на калибрование линейных размеров +Пк;
- уменьшение веса изделия при спекании за счет выгорания смазок,
восстановления окислов и пр. x = 3%;
- плотность компактных метериалов: железа 7,8 г/см3, меди 8,9 г/см3, алюминия
2,7 г/см3;
- удельное давление прессования Руд определенное по методу ГОСТ 25280- 82 металлических порошков при пористости П = 8%: медь (ПМС -1) 450 МПа, железо (ПЖ4М2) 1000 МПа; алюминий (АПС-1) 200 МПа;
- технологические свойства порошков железа, меди и алюминия приведены в табл. 6;
|
Таблица 6
- дополнительные данные в разделе “Краткие сведения из теории” настоящих методических указаний студент находит самостоятельно. На титульном листе указывается полное название практической работы и шифр варианта. В отчет включают рис. 1, 3, 4, данные индивидуального и общего задания и табл. 5, 6. Расчеты ведут с точностью второго знака после запятой.
РЕКОМЕНДУЕМАЯ ЛИТЕРАТУРА
1. Порошковая металлургия. Материалы, технология, свойства, области применения: Справочник / И. М. Федорченко, И. Н. Францевич, И. Д. Радомысельский и др.; Отв. ред. И. Д. Федорченко. Киев: Наук. думка, 1985.
624 с.
2. Порошковая металлургия и напыленные покрытия. Учеб. для ВУЗов / Под общ. ред. Б. С. Митина. М.: Металлургия, 1985. 567 с.
3. Проектирование структуры, свойств и технологии порошковых и композиционных материалов: Метод. указания по курсовому проекту по спец. дисциплинам специальности “Материаловедение в машиностроении” / НГТУ; Сост. : И. М. Мальцев, Ю. А. Шоткин Н.- Новгород, 1994.
Дата добавления: 2019-02-12; просмотров: 141; Мы поможем в написании вашей работы! |
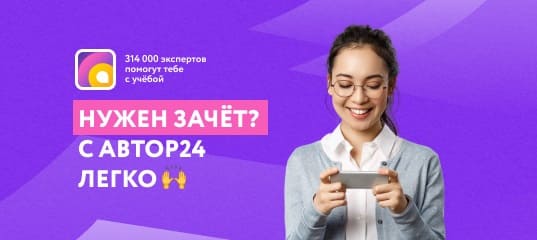
Мы поможем в написании ваших работ!