ВТОРИЧНЫЕ ЭНЕРГОРЕСУРСЫ. ОСНОВНЫЕ СВЕДЕНИЯ
МИНОБРНАУКИ РОССИИ
Федеральное государственное бюджетное образовательное
учреждение высшего образования
«Юго-Западный государственный университет»
(ЮЗГУ)
Кафедра теплогазоводоснабжения
Расчет котла-утилизатора
Методические указания для практических занятий студентов, обучающихся по направлению подготовки 13.04.01 Теплоэнергетика и теплотехника, 08.04.01 – Строительство
Курск 2017
УДК С07.34
Составитель В.С. Ежов
Рецензент
Кандидат технических наук, доцент Н.Е. Семичева
Расчет котла–утилизатора: методические указания для практических занятий студентов, обучающихся по направлению подготовки 13.04.01 Теплоэнергетика и теплотехника / В.С. Ежов, Н.Е. Семичева; Юго-Зап. гос. ун-т. - Курск, 2017. - 48 с. – Библиогр.: с. 47
Наряду с теоретическими сведениями об основных принципах утилизации тепловых ВЭР промышленных печей, излагаются материалы для выполнения курсового и дипломного проектирования студентов, по дисциплинам «Теплоутилизирующие установки и оборудование», «Утилизация вторичных энергоресурсов на объектах теплоэнергетики», «Теплоиспользующие установки и утилизация вторичных энергоресурсов», тепловой и аэродинамический расчет, котла–утилизатора, определение его основных конструктивных размеров и технологических параметров.
Предназначено для студентов очной и заочной форм обучения, обучающимся по направлениям 13.04.01– Теплоэнергетика и теплотехника и 08.04.01 – Строительство.
|
|
Текст печатается в авторской редакции
Подписано в печать 2017 г. Формат 60х84 1/16.
Усл. печ. л. 1,2. Уч.-изд.л. 1,1 Тираж 30 экз. Заказ ____. Бесплатно.
Юго-Западный государственный университет.
305040, г. Курск, ул. 50 лет Октября, 94.
СОДЕРЖАНИЕ
СОДЕРЖАНИЕ. 3
ПРЕДИСЛОВИЕ. Ошибка! Закладка не определена.
ВВЕДЕНИЕ. 4
1 ВТОРИЧНЫЕ ЭНЕРГОРЕСУРСЫ. ОСНОВНЫЕ СВЕДЕНИЯ.. 6
2 КОТЛЫ-УТИЛИЗАТОРЫ. ОСНОВНЫЕ СВЕДЕНИЯ.. 16
3 МЕТОДИКА ВЫПОЛНЕНИЯ КУРСОВОЙ РАБОТЫ.. 27
4 ПРИМЕР ВЫПОЛНЕНИЯ КУРСОВОЙ РАБОТЫ.. 38
4.1 Расчет пароперегревателя. 39
4.2 Расчет испарительных секций. 41
4.3 Расчет экономайзера. 43
4.4 Расчет паропроизводительности котла. 45
БИБЛИОГРАФИЧЕСКИЙ СПИСОК.. 46
ВВЕДЕНИЕ
Использование вторичных энергетических ресурсов /ВЭР/, т.е. энергетических отходов технологических процессов, является наиболее экономичным по сравнению с остальными способами получения энергии, так как для этого не требуется дополнительного расхода топлива. Такой путь позволяет сократить расход постоянно дорожающего топлива, уменьшить загрязнение окружающей среды, разгрузить транспорт. Основные виды вторичных энергоресурсов – это ВЭР давления (ДВЭР), горючие ВЭР (ГВЭР) и тепловые (ТВЭР). Первые и вторые используются почти полностью, вторые – совершенно недостаточно. Поэтому данные методические указания посвящено утилизации ТВЭР.
|
|
Как правило, на технологические цели расходуется очень много топлива с низким коэффициентом полезного действия. Например, для промышленной печи он составляет всего 20…30%, а значит, имеют место огромные потери теплоты. Утилизация этой теплоты ТВЭР в масштабе страны может дать значительную экономию условного топлива – более 63 млн.т.в год. При рациональном решении сопутствующих вопросов теплоэнергетики и с учетом потерь транспортировки заменяемого топлива или электроэнергии экономия составит 75 млн.т. Такое количество топлива достаточно для теплоснабжения 50 городов с население 50 млн.чел. или эквивалентно годовой выработке электроэнергии 10 АЭС мощностью 4 млн. кВт каждая.
Главная возможность использования ТВЭР – обеспечение теплоснабжения, т.е. покрытие тепловой нагрузки технологических нужд, питательного цикла котлов и систем испарительного охлаждения, горячего водоснабжения городов, отопления и вентиляции, кондиционирования воздуха.
|
|
Кроме того, энергетические выбросы могут существенным образом влиять на состояние окружающей среды.
Так, анализ выбросов теплоты в атмосферу от совокупности промышленных объектов показывает наличие регионов площадью до 10 тыс. км2 с тепловыделением от 10 до 200 Вт/м2. Результатом такого теплового воздействия является образование устойчивого «острова теплоты» с температурой, на (1-4)°С, превышающей естественную для воздушной среды данного региона. Это приводит к возникновению в «островах теплоты» туманов, облачности, увеличению атмосферных осадков.
Сброс теплоты в водоемыповышает температуру континентальных и прибрежных вод. Это приводит к уменьшению содержания растворенных в них кислорода, диоксида углерода, азота, что негативно сказывается на воспроизводстве рыб, насекомых, растений. Вместе с тем часть тепловых потерь, прежде всего установок конечного использования (технологических аппаратов), может быть утилизирована как вторичные энергетические ресурсы (ВЭР).
Предлагаемые методические указания посвящены утилизации и снижению тепловых выбросов в атмосферу.
ВТОРИЧНЫЕ ЭНЕРГОРЕСУРСЫ. ОСНОВНЫЕ СВЕДЕНИЯ
|
|
В соответствии с официальным определением, вторичные энергоресурсы – это энергетический потенциал (запас энергии в виде физической теплоты, потенциальной энергии избыточного давления, химической энергии и др.) продукции, отходов, побочных и промежуточных продуктов, которые не могут быть использованы в самом агрегате, но могут частично или полностью применяться для энергоснабжения других потребителей [1].
По виду содержащегося в них энергетического потенциала ВЭР подразделяются на три основных группы: горючие, тепловые и избыточного давления.
Горючие ВЭР – это отходы одного производства, которые могут быть утилизированы непосредственно в виде топлива в других производствах. К ним относятся, например, технологические газы черной и цветной металлургии, жидкие и твердые топливные отходы химической и нефтегазоперерабатывающей промышленности, щепа, опилки, стружка, щелоки деревообрабатывающей и целлюлозно-бумажной отраслей.
Тепловые ВЭР – это физическая теплота отходящих газов, основной и побочной (нецелевой) продукции производства: нагретых металла, шлаков и зол; горячей воды и пара, отработанных в технологических установках, системах охлаждения и пр.
Следует отметить, что тепловая энергия отходов, выходящая из технологического агрегата и используемая для подогрева вещественных потоков, поступающих в этот же агрегат (процессы регенерации и рекуперации), ко вторичным энергоресурсам не относятся.
ВЭР избыточного давления – это потенциальная энергия покидающих установку газов, воды, пара, имеющих повышенное давление, которое может быть еще применено перед выбросом в окружающую среду. Основное направление утилизации таких ВЭР – получение электрической или механической энергии.
Многие горючие ВЭР, например черной металлургии, имеют низкую теплоту сгорания и химически агрессивны. Это создает значительные трудности при их утилизации. Они же имеют место и при сжигании высококалорийных, но одновременно легко воспламеняемых, взрывоопасных и токсичных ВЭР (водород, сухие абгазы и др.).
Для утилизации горючих вторичных энергетических ресурсов часто необходимо специальное оборудование, однако основной путь их использования – применение в агрегатах индустриальных технологий.
Тепловые ВЭР – наиболее распространенный вид энергетических отходов. Их утилизация проводится практически повсеместно. В то же время привлекаются в основном высокопотенциальные (высокотемпературные) тепловые ВЭР (см. далее). Значительно меньше востребованы среднетемпературные энергетические отходы, низкотемпературные применяются еще реже.
Основное оборудование для использования тепловых ВЭР – котлы-утилизаторы (к/у), системы испарительного охлаждения промышленных печей, различного рода теплообменники, в том числе контактные нагреватели.
ВЭР избыточного давления образуются в ряде металлургических, химических, нефтеперерабатывающих производств. Ими могут обладать жидкие и газообразные отходы. Однако их применение пока не носит массового характера (избыточное давление доменного газа используют, например, в газовых бескомпрессорных турбинах).
По температуре, с которой тепловые ВЭР покидают технологические агрегаты, их делят на высоко-, средне- и низкопотенциальные.
Четкой градации ВЭР по этому признаку нет. Можно принять, что к высокопотенциальным относятся ВЭР, температура которых превышает наименьшую температуру газов в автогенном процессе сжигания топлива (не менее 600°С). К низкопотенциальным принадлежат ВЭР, представляющие собой жидкости с температурой менее 100°С и газы с температурой ниже 300°С [2]. В этом случае среднепотенциальные ВЭР по температуре будут занимать промежуточное положение между высоко- и низкопотенциальными энергетическими отходами.
В целом основными источниками тепловых ВЭР в различных отраслях промышленности выступают технологические агрегаты, как правило, недостаточно совершенные с энергетической стороны. Особенно неблагоприятны с точки зрения использования теплоты сгорания топлива нагревательные и термические печи (их тепловой КПД равен 12-18%), вагранки чугунолитейных цехов (теплопотери с газами превышают 50-60%), паровые котлы низкого давления (КПД порядка 50%), паровые молоты кузнечных цехов (КПД не более 2-5%) и др.
Разработка методов и способов утилизации ВЭР промышленных предприятий в нашей стране началась в 20-30-е гг. 20 в. Тогда были заложены теоретиче-ские основы энергосбережения и предложены первые технические решения. Наиболее значительные достижения в практике утилизации тепловых отходов приходятся на послевоенные годы (конец 40-х–начало 50-х гг. прошлого столетия).
В 60-х–70-х гг. 20 в. за счет использования ВЭР в стране ежегодно экономилось около 20 млн т условного топлива. Примерно на этом же уровне (около 25 млн т/год) сохранялось энергоснабжение за счет ВЭР в следующие десять лет.
Однако следует отметить, что за этот период объем энергопотребления вырос в 2,4 раза, а общая экономия энергоресурсов снизилась с 270 за 60-70 гг. до 135 млн т/год условного топлива за последующее десятилетие.
Эта негативная тенденция была связана со снижением в 60-х гг. стоимости первичных энергоресурсов за счет массового вовлечения в топливный баланс страны нефти и природного газа.
Начиная с конца 70-х–начала 80-х гг., интерес к использованию ВЭР вновь возрастает, поскольку энергоемкость единицы валового внутреннего продукта в нашей стране существенно (до 11 раз в сравнении с Японией) превысила уже достигнутый за рубежом уровень.
По мере интеграции в мировую экономику и в связи со вступлением страны в ВТО такое положение приводит к все большей неконкурентоспособности нашей продукции на мировом рынке. Именно поэтому в настоящее время одной из важнейших задач народного хозяйства России является всемерное использование ВЭР.
Из всех отраслей народного хозяйства России первое место по выходу и утилизации ВЭР занимает черная металлургия. Суммарный выход ВЭР в этой отрасли в пересчете на условное топливо равен 30-50 млн т/год при максимально возможном показателе утилизации около 20 млн т. Остальные отрасли промышленности (цветная металлургия, химическая промышленность и др.) имеют значительно меньшие выход и утилизацию ВЭР.
На долю черной металлургии приходится около 40% тепловых и до 80% горючих ВЭР, применяемых в промышленности. Потребности предприятий с полным металлургическим циклом в топливе (без угля для коксования) только на 30-40% покрываются за счет его привоза и на 60-70% — вторичными энергетическими ресурсами).
По виду потенциала ВЭР черной металлургии представлены всеми группами (горючие, тепловые, избыточного давления). К горючим прежде всего относятся доменный, конвертерный и коксовый газы. Они же являются высокопотенциаль-ными тепловыми выбросами с температурой от 300 до 1600°С, а доменный газ обладает также избыточным давлением. Из металлургических печей выносится 30-50% тепла, охлаждающими элементами воспринимается 8-20% и до 5% рассеивается в окружающую среду.
Наиболее мощным вторичным энергетическим ресурсом является доменный, или, точнее, колошниковый газ. В частности, за счет его сжигания в газовом балансе металлургических предприятий покрывается 35-45% потребности в теплоте. Характеристика колошникового газа: температура (175-250)°С, выход (1100-2200) м3/т чугуна; состав, %:( 23-40) CO, (12-22) CO2, (1,5-6,0) H2, остальное – азот (N2); теплота сгорания, QC – 4 МДж/м3; давление на колошнике, РК до 0,4 МПа.
Очищенный от пыли колошниковый газ применяется главным образом в доменных воздухонагревателях, энергетических котлах, для отопления коксовых батарей, нагревательных колодцев и печей прокатного производства. В данных случаях реализуется его горючий и тепловой потенциалы. Первый обусловлен горением СО до СО2.
Кроме того, доменный газ, обладая избыточным давлением, используется также в газовых бескомпрессорных турбинах. В 80-е гг. 20 в. себестоимость электроэнергии, вырабатываемой в них, была в 1,5-2,0 раза ниже получаемой на ТЭЦ завода и в 3,0-3,5 раза меньше, чем в единой энергетической системе (срок окупаемости не более двух лет) [3].
В США, Японии, Великобритании, Франции, Германии имеются десятки газотурбинных установок, работающих на колошниковом газе. Германия, установив, 7 в частности, газовые турбины на всех крупных доменных печах, ежегодно вырабатывает на них до 360 млн кВт-ч электроэнергии.
К ВЭР доменного производства относится также теплота отходящих газов воздухонагревателей, составляющая 15-20% от ее расхода на подогрев доменного дутья. Их температура колеблется в пределах 150-600°С. Они могут быть использованы для выработки пара, горячей воды или для подогрева доменного газа перед входом в газовую турбину.
Вторым (после доменного) по значению источником оксида углерода на предприятиях черной металлургии является конвертерный газ. Его усредненный состав при плавке с верхней и нижней продувкой, %: (67-79) СО, (13-16) СО2, (0-3) Н2 и Н2О, (5-14) N2. Теплота сгорания газа составляет (8,4-9,2) МДж/м3 при его температуре на выходе из конвертера 1400-1600°С.
Расчеты показывают, что на крупном заводе с производительностью порядка 7 млн т/год конвертерной стали выход газа составляет ~570 млн т/год, или около 130 млн м3 в пересчете на природный газ (при теплотворной способности последнего на уровне 40 МДж/м3). Таким образом, при выплавке 1 т стали с конвертерными газами выносится энергетический потенциал, равный 17-20 м3 природного газа.
На эффективность использования ВЭР конвертеров существенное влияние оказывает способ отвода газов от них. В настоящее время применяют три варианта:
1). с полным дожиганием СО перед котлом-утилизатором, т.е. с утилизацией физического тепла конвертерных газов и их энергетического потенциала. В этом случае в атмосферу сбрасывается обеспыленный охлажденный газ, содержащий СО2, О2, N2 и пары воды;
2). с частичным дожиганием СО перед котлом-утилизатором (при коэффициенте α расхода воздуха, равном 0,3-0,6) и полным его сжиганием на «свече» при сбросе газов в атмосферу. В данном варианте используется их физическое тепло и, частично, энергетический потенциал;
3). без дожигания СО перед котлом-утилизатором и его сжиганием на «свече» при сбросе газов в атмосферу (отечественная практика) или применением в качестве топлива (иностранный опыт). В первом случае утилизируется лишь их физическое тепло (при α = 0).
В любом из рассмотренных вариантов очистка газов производится после их использования в котле-утилизаторе.
Cхема утилизации тепла конвертерных газов с полным их дожиганием перед КУ применяется для агрегатов с емкостью по стали до 150 т. Сжигание осуществляется в газоходах паровых котлов. В этой схеме серийные котлы-утилизаторы, или ОКГ (охладители конвертерных газов), имеют производительность по пару 160-210 т/ч при его пиковом давлении до 5 МПа.
В связи с внедрением в промышленность большегрузных конвертеров емкостью до 400 т стали и связанным с этим увеличением объема вдуваемого кислорода количество выделяющихся газов значительно возрастает. Их дожигание приведет к такому росту объема продуктов сгорания, который существенно увеличит габаритные размеры и стоимость всей установки. В этих условиях рациональной является система газоотвода без дожигания.
В котлах ОКГ-400 (цифра – масса садки металла в конвертере) паропроизводительность достигает 325 т/ч (в максимальном режиме).
Полагают, что системы ОКГ без дожигания целесообразны также для конвертеров с донной и комбинированной продувкой [4].
Охлажденный в ОКГ и очищенный конвертерный газ может улавливаться (направляться в газгольдер). В этом случае, в соответствии с иностранной практикой, газ поступает в струйные охладители и полые скрубберы, затем в трубы Вентури и далее в центробежные скрубберы (мокрые циклоны), после которых попадает в газгольдер. Такие системы улавливания конвертерного газа с усреднением его состава и расхода в газгольдерах (мокрых или сухих) и последующим использованием в качестве топлива весьма распространены за рубежом. В Японии ими оборудовано около 90% работающих конвертеров.
Мокрые газгольдеры представляют собой емкость для воды, над которой размещен резервуар телескопической конструкции (верх ее способен подниматься, увеличивая объем резервуара).
В сухих газгольдерах поршень поднимается и опускается в результате изменения объема газа. Его верхнее положение соответствует полному заполнению газгольдера. Вместимость газгольдеров составляет от 30 до 70 тыс. м3 при производительности конвертеров (150-330) т.
Отметим, что на отечественных заводах конвертерный газ не улавливается.
В целом его энергетический потенциал в настоящее время используется лишь частично и только в самом конвертерном производстве. В качестве причин, сдерживающих полную утилизацию этого газа, обычно указывают нестабильность его выхода, изменяющийся по ходу плавки состав, взрывоопасность при содержании в нем 12,5-75% СО.
Коксовый газ – третий крупный источник горючих ВЭР черной металлургии. Из 1 т сухой шихты, помимо (750-800) кг кокса, получают (320-330) м3 коксового газа, а также 33 кг каменноугольной смолы, 80 кг – подсмольной воды, 11 кг – сырого бензола, 3кг – аммиака, которые перерабатывают в химические продукты. Из искусственных газообразных топлив (доменного, смешанного, конвертерного, генераторного) коксовый газ обладает наибольшей теплотой сгорания (свыше 17 тыс. кДж/м3).
Следует отметить в целом высокий выход ВЭР в коксохимическом производстве (около 80% от первичного энергопотребления). Это прежде всего энергетический потенциал коксового газа, выполняющего функции теплового и горючего ВЭР, а также физическое тепло кокса (тепловой ВЭР, не относящийся к газовым).
Потенциал коксового газа как теплового ВЭР определяется тем обстоятельством, что он покидает печь с температурой (700-800)°С и его теплосодержание составляет около 1000 МДж/т кокса, или до 30% расхода тепла.
Физическую теплоту коксового газа отбирают на разных стадиях охлаждения: в стояках коксовых камер – от (700-800) °С до 400°С; в газосборниках – от 400°С до 82°С; в первичных холодильниках – от 82°С до 30°С. Используется теплота первой и третьей стадий.
Для утилизации теплоты первой стадии стояки оборудуют теплообменниками, через которые в замкнутом контуре циркулирует теплоноситель. Его теплота может направляться для получения пара, горячей воды, нагрева органических теплоносителей. Теплота третьей стадии охлаждения применяется для подогрева улавливающих растворов цеха сероочистки коксового газа.
Физическая теплота кокса, выгружаемого из камеры, составляет порядка 50% от расходуемой на коксование. Ее утилизируют при сухом тушении кокса, т.е. охлаждении последнего в камере циркулирующим инертным газом (азотом). Нагревшись до (750-800)°С, газ поступает в теплообменник вторичного теплоносителя (паровой котел, воздухо- или газоподогреватель, подогреватель угольной шихты или сочетание различных теплоиспользующих аппаратов и силовых установок).
Наибольшее распространение получило сухое тушение кокса с подачей теплоты в котельные установки для выработки пара (давление в перегретом состоянии до 39 МПа, температура 440°С). Охлажденный до (150-170)°С газ очищается в циклонах от пыли и возвращается в камеру тушения.
Сухой способ тушения позволяет утилизировать более 80% теплоты раскаленного кокса.
После охлаждения в системе отбора теплоты коксовый газ проходит сложную систему очистки от смол, аммиака и бензола [5]. После этого его отправляют в газгольдер, а оттуда потребителю топлива – непосредственно или через газосмесительную станцию.
Основной потребитель коксового газа как горючего ВЭР – металлургическое производство. В первую очередь он используется для нагревания мартеновских печей и агрегатов термообработки металла. При достаточном количестве его применяют также в нагревателях коксовых батарей. В этом случае продукты сгорания на выходе из генератора имеют температуру (260-350)°С, унося (15-20)% подведенной теплоты. На некоторых предприятиях она расходуется на получение горячего воздуха для подогрева затворов угольной башни в зимнее время.
Структуру потребления коксового газа в качестве горючего ВЭР иллюстрируют данные по Японии, добившейся существенных результатов в его утилизации. В этой стране из общего годового потребления коксового газа (~10 млрд м3) на обогрев коксовых печей расходуется около 22%, в металлургическом производстве – 56%, в городских отопительных системах – 10%, на ТЭЦ – 8% и т.д. [6]. В ней же энергию коксового газа довольно широко используют в газовых турбинах, соеди-ненных в одном цикле с генераторами электрического тока.
Еще одним крупным источником горючих ВЭР является газ закрытых ферросплавных печей. Его выход составляет (400-800) м3/т сплава при концентрации СО в нем (70-90)%. После мокрого пылеулавливания на некоторых отечественных заводах он утилизируется как топливо, но в большинстве случаев сжигается на свечах. Помимо рассмотренных выше наиболее крупных горючих и тепловых ВЭР можно отметить наличие ряда других источников, преимущественно тепловых. Это газы агломерации, обжига известняка и окатышей, мартеновских, электросталеплавильных, ваграночных, металлонагревательных печей, колодцев прокатного производства и др. Их температура колеблется от (800-900)°С в печах с регенераторами до (900-1200)°С в термических, прокатных и кузнечных устройствах (без регенерации).
Теплота уходящих высокотемпературных газов таких мощных промышленных агрегатов может быть использована газотурбинными установками, встроенными в газовый тракт для выработки электроэнергии и подачи газа и воздуха в печь. Для более полной утилизации теплоты уходящих газов за теплообменниками газотурбинных установок обычно устанавливают котел-утилизатор, поскольку температура продуктов сгорания еще значительна (~450-500)°С. Он позволяет вырабатывать пар высоких параметров для технологических или энергетических нужд.
Поскольку температура газов после котла-утилизатора достаточна высока порядка (200-250)°С, их теплоту целесообразно использовать для коммунально-бытовых нужд, включая отопление (нагрев воды).
Резюмируя, отметим высокий уровень утилизации ВЭР черной металлургии, который уже в 1975 г. составлял более 96%, а на некоторых предприятиях приближался к 100% [7,8].
Практика проектирования и экономического обоснования эффективности утилизационных установок, их фактическая эксплуатация показывают, что они дают большой экономический эффект. Так, себестоимость «бестопливного» пара, вырабатываемого в котлах-утилизаторах, почти в два раза ниже, чем пара аналогичных параметров от котлов заводских ТЭЦ. Эффективность капитальных вложений в производство энергии при использовании ВЭР в (2-3) раза выше, чем в топливно-энергетическом комплексе промышленности.
Таким образом, важнейшим результатом применения ВЭР является экономия первичного топлива, которая в основном определяет величину получаемого экономического эффекта.
Эффективность вовлечения ВЭР резко повышается при многоступенчатой схеме утилизации тепловых выбросов. Примером такого «комплексного» использования теплоты природного газа является кузнечно-штамповочное производство Донецкого экскаваторного завода [9]. Применяемая на нем схема сводится к следующему. Продукты сгорания после кольцевой печи поступают в многофункциональный блочный теплообменник. В его первом модуле производится подогрев воды, используемой на технологические и хозяйственно–бытовые нужды. Следующие две ступени представляют собой рекуператор, в котором нагревают воздух, подаваемый на горение топлива, до 340°С. Четвертая ступень – нагреватель сжатого воздуха, поступающего на пневмомолоты. После блочного теплообменника продукты сгорания при (200-210)°С направляют в контактный экономайзер, а затем при темпера-туре (55-60)°С – в дымовую трубу. Использование рассмотренной схемы повышает КПД с 18% (кольцевая печь) до 92%.
Эффективность вовлечения ВЭР также повышается за счет увеличении числа потребителей НПТ при теплофикации прилегающих к предприятиям промышленных узлов и жилых районов. При этом улучшается и экологическая обстановка при закрытии мелких, без пылегазоулавливающих устройств, котельных, загрязняющих окружающую среду.
Вместе с тем расширение применения ВЭР, как и другие направления рационального использования сырьевых и топливно-энергетических ресурсов, требуют внедрения новой техники и прогрессивной технологии, что связано с дополнительными капитальными затратами, особенно остродефицитными в настоящее время.
Поэтому значительная часть вторичных энергетических ресурсов либо вообще не востребована, поскольку не найдены надежные технические решения их применения, например физической теплоты литейного чугуна, нагретого металла различных прокатных станов, либо утилизируется недостаточно (химическая энергия конвертерного газа, физическая теплота жидких шлаков, зол и др.). Эффективность ВЭР снижается также из-за сезонного характера потребления пара низких параметров и иных причин неполного использования действующих установок утилизации энергетических выбросов индустриальных технологий.
Очевидно, что качественный и количественный рост эффективности потребления ВЭР напрямую связан с проблемой общего возрождения народного хозяйства России, что в обозримом будущем представляется маловероятным. Действительно, в течение последних десятилетий лет наша страна реализует скудный, на уровне 20% в сравнении с 1980-1990 гг., объем инвестиций в народное хозяйство. На такой незначительной инновационной основе устойчивый рост экономики невозможен, в том числе и решение более частной задачи – эффективной утилизации вторичных энергетических ресурсов [10].
Дата добавления: 2018-11-24; просмотров: 1017; Мы поможем в написании вашей работы! |
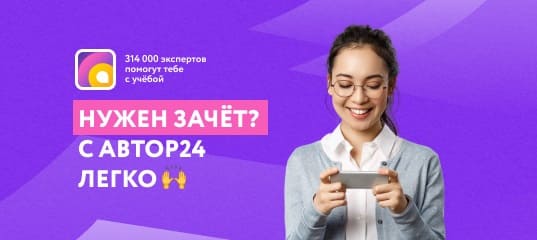
Мы поможем в написании ваших работ!