Use your contacts: develop the art of networking
Start with family and friends. They are an easily forgotten resource. Draw up a list of those who might be able to support you in your decisions or help you find vacation work.
When networking, ask people for advice. They are usually willing. Also ask them whether they know other people who might be able to help, and whether you can mention their name. Your network will expand, and all kinds of help may result.
Explore options
Don't sit in an academic oxygen bubble. Read a newspaper. Talk to people (questioning, listening, recording). Visit the careers service to look for vacation work. Use AIESEC and Student Industrial Society networks at university. Find out about the changing graduate job market. Visit careers fairs in the first or second year.
Turn research into action. Be proactive. Set objectives and do some "action planning".
Make the most of your final year project. It can be a route into employment.
Practice negotiation skills
Negotiations occur all the time. Practice negotiation skills and recognise all the opportunities to develop them in everyday life.
Recognise that negotiation within a long term relationship should aim for a "win/win" outcome.
Do something different
What will make you different from the other thousands of graduates? Perhaps you could learn an unusual language, take up a distinctive hobby or set up a new voluntary organisation.
10. Don't panic! You don't have to be perfect
Tackle this Action Plan in manageable chunks and review your progress regularly. You will find you can achieve a great deal over three or four years if you start now.
Degree Course Checklist
When choosing a degree, ask universities some searching questions. Try to discover the answers to the questions below. If necessary show them this checklist.
1. How do staff gather student feedback on the course, and how do they respond to it?
2. Do the staff have a clear idea of the skills which students develop as part of the course, in addition to subject knowledge?
3. What teaching methods are used to help students develop these skills?
4. How are staff teaching skills developed?
5. Is there evidence that the staff work together as a team? For example, has the course been developed as a team or by individuals?
6. How are students encouraged to develop their learning skills? For example, do they encourage 'learning logs' to help students reflect on their learning?
7. Is there any employer input in the way the course is taught?
|
|
8. Is it possible to meet graduates who are now working, and can comment on the value of the course?
9. What is the 'dropout rate' for the course, and what are the reasons people leave?
10. What kind of learning environment do they offer? Find out about teaching styles, projects, working in teams, work timetable, the kind of students, access to staff support (e.g. tutors) and the level of structure or independence, and then see how the course will match your preferred learning style.
PROPERTIES OF MATERIALS 1
A material's property is an intensive, often quantitative property of a material, usually with a unit that may be used as a metric of value to compare the benefits of one material versus another to aid in materials selection.
A material property may be a constant or may be a function of one or more independent variables, such as temperature. Material's properties often vary to some degree according to the direction in the material in which they are measured; a condition referred to as anisotropy. Materials properties that relate two different physical phenomena often behave linearly or approximately so in a given operating range and may then be modeled as a constant for that range. This linearization can significantly simplify the differential constitutive equations that the property describes.
Some material's properties are used in relevant equations to determine the attributes of a system a priori. For example, if a material of a known specific heat gains or loses a known amount of heat, the temperature change of that material can be determined. Materials properties may be determined by standardized test methods. Many such test methods have been documented by their respective user communities and published through ASTM International.
PROPERTIES OF MATERIALS 2
Iron is a metallic chemical element with the symbol Fe (Latin: ferrum) and atomic number 26. Iron is a group 8 and period 4 element and is therefore classified as a transition metal. Iron and iron alloys (steels) are the most common metals and the most common ferromagnetic materials in everyday use. Pure iron is a metal but is rarely found in this form on the surface of the earth because it oxidizes in the presence of oxygen and moisture. Fresh iron surfaces are silvery-grey in color, but oxidize in air to form a red or brown coating of ferric oxide or rust. Pure single crystals of iron are soft (softer than aluminium). The properties of iron can be modified by alloying it with various other metals to form steels. Alloying iron with appropriate small amounts (up to a few per cent) of other metals produces steel, which can be 1,000 times harder than pure iron. Iron is a necessary element used by almost all living organisms.
|
|
A glass is an amorphous (non-crystalline) solid material. Glass breaks easily, and often optically transparent. Glass is commonly used for windows, bottles, modern hard drives, eyewear, etc. The word glass developed in the late Roman Empire. It was in the Roman glassmaking center at Trier, now in modern Germany, that the late-Latin word glesum reffered to a transparent substance. Glass plays an important role in science and industry. The optical and physical properties of glass make it suitable for applications such as flat glass, container glass, optics and optoelectronics material, laboratory equipment, etc.
Plastic is the general common term for a wide range of synthetic or semisynthetic organic amorphous solid materials used in the manufacture of industrial products. Plastics are typically polymers of high molecular mass, and may contain other substances to improve production, the quality of products and/or reduce costs. Monomers of Plastic are either natural or synthetic organic compounds.
The word is derived from the Greek πλαστικός (plastikos) meaning “suitable for moulding”, and πλαστός (plastos) meaning “moulded”. It refers to their plasticity during manufacture, that allows them to be pressed, or shaped into a variety of forms — such as films, fibers, plates, tubes, bottles, boxes, and much more.
The common word plastic should not be confused with the technical adjective plastic, which is applied to any material which undergoes a permanent change of shape (plastic deformation) when strained beyond a certain point. Aluminium, for instance, is plastic in this sense, but not a plastic in the common sense; in contrast, in their finished forms, some plastics will break before deforming and therefore are not plastic in the technical sense.
|
|
There are two types of plastics: thermoplastics and thermosetting polymers. Thermoplastics will soften and melt if enough heat is applied; examples are polyethylene, polystyrene, polyvinyl chloride and polytetrafluoroethylene (PTFE). Thermosets can melt and take shape once;
Plastics can be classified by chemical structure. Some important groups in these classifications are the acrylics, polyesters, silicones, polyurethanes, and halogenated plastics. Plastics can also be classified by the chemical process used in their synthesis, such as condensation, polyaddition, and cross-linking.
Other classifications are based on qualities that are relevant for manufacturing or product design. Examples of such classes are the thermoplastic and thermoset, elastomer, structural, biodegradable, and electrically conductive. Plastics can also be classified by various physical properties, such as density, tensile strength, glass transition temperature, and resistance to various chemical products.
Due to their relatively low cost, ease of manufacture, versatility, and imperviousness to water, plastics are used in an enormous and expanding range of products, from paper clips to spaceships. They have already displaced many traditional materials, such as wood; stone; horn and bone; leather; paper; metal; glass; and ceramic, in most of their former uses.
The use of plastics is constrained chiefly by their organic chemistry, which seriously limits their hardness, density, and their ability to resist heat, organic solvents, oxidation, and ionizing radiation. In particular, most plastics will melt or decompose when heated to a few hundred degrees celsius. While plastics can be made electrically conductive to some extent, they are still no match for metals like copper or aluminium. Plastics are still too expensive to replace wood, items like ordinary buildings, bridges, dams, pavement, and railroad ties.
|
|
The first human-made plastic was invented by Alexander Parkes in 1855; he called this plastic Parkesine (later called celluloid). It was demonstrated at the 1862 Great International Exhibition in London. The development of plastics has come from the use of natural plastic materials (e.g., chewing gum, shellac) to the use of chemically modified natural materials (e.g., rubber, nitrocellulose, collagen, galalite) and finally to completely synthetic molecules (e.g., bakelite, epoxy, polyvinyl chloride, polyethylene).
A metal is a chemical element that is a good conductor of both electricity and heat. In chemistry, a metal (Ancient Greek métallon, μέταλλον) is an element, compound, or alloy that conducts electricity. In a metal, atoms readily lose electrons to form positive ions. Those ions are surrounded by delocalized electrons, which are responsible for the conductivity.
Metals occupy most of the periodic table, while non-metallic elements can only be found on the right-hand-side of the Periodic Table of the Elements. A diagonal line drawn from boron (B) to polonium (Po) separates the metals from the nonmetals. Most elements on this line are metalloids, sometimes called semiconductors. This is due to the fact that these elements have electrical properties common to both conductors and insulators. Elements to the lower left of this division line are called metals, while elements to the upper right of the division line are called non-metals.
Metals are very corrosive – they rust in contact with water. Painting (or any other form of covering) is a good way to prevent their corrosion.
Metals in general have high electrical conductivity, the ability to be deformed under stress. Optically speaking, metals are opaque, shiny and lustrous. The large number of free electrons in any typical metallic solid (element or alloy) is responsible for the fact that they can never be categorized as transparent materials.
An alloy is a mixture of two or more elements in which the major component is a metal. Most pure metals are too soft or chemically reactive for practical use. Combining different ratios of metals as alloys modifies the properties of pure metals to produce desirable characteristics. The aim of making alloys is generally to make them less brittle, harder, resistant to corrosion, or have a more desirable color. Of all the metallic alloys in use today, the alloys of iron (steel, stainless steel, cast iron, tool steel, alloy steel) make up the largest proportion both by quantity and commercial value. Iron alloyed with various proportions of carbon gives low, mid and high carbon steels. The addition of silicon will produce cast irons.
Other significant metallic alloys are those of aluminium, titanium, copper and magnesium. Copper alloys have been known since prehistory—bronze gave the Bronze Age its name—and have many applications today, most importantly in electrical wiring. The alloys of the other three metals have been developed relatively recently; due to their chemical reactivity they require electrolytic extraction processes. The alloys of aluminium, titanium and magnesium are valued for their high strength-to-weight ratios; magnesium can also provide electromagnetic protection. These materials are ideal for situations where high strength-to-weight ratio is more important than material cost, such as in aerospace and some automotive applications.
Alloys specially designed for highly-demanding applications, such as jet engines, may contain more than ten elements.
Brass is an alloy of copper and zinc. The proportions of zinc and copper can be varied; this creates a range of brasses with various properties. In comparison, bronze is principally an alloy of copper and tin. Brass is a substitutional alloy. It is used for decoration for its bright gold-like appearance; for applications where low friction is required such as locks, gears, bearings, doorknobs, ammunition, and valves; for plumbing and electrical applications; and extensively in musical instruments such as horns and bells for its acoustic properties. It is also used in zippers. Because it is softer than most other metals in general use, brass is often used in situations where it is important that sparks not be struck, as in fittings and tools around explosive gases.
Brass has a yellow color, somewhat similar to gold. It is relatively resistant to tarnishing, and is often used as decoration and for coins. In antiquity, polished brass was often used as a mirror.
Forms of brass have been in use since prehistory. But the direct alloying of copper and zinc metal was introduced to Europe in the 16th century.
Brass has good malleability and acoustic properties. It is used in many musical instruments, such as trombone, tuba, trumpet, cornet, euphonium, tenor horn, and the French horn. Even though the saxophone is classified as a woodwind instrument and the harmonica is a free reed aerophone, both are also often made from brass. In organ pipes of the reed family, brass strips (called tongues) are used as the reeds, which beat against the shallot (or beat "through" the shallot in the case of a "free" reed).
Brass has higher malleability than copper or zinc. The relatively low melting point of brass (900 to 940°C, depending on composition) and its flow characteristics make it a relatively easy material to shape. By varying the proportions of copper and zinc, the properties of the brass can be changed, allowing hard and soft brasses.
Today almost 90% of all brass alloys are recycled.
Aluminium makes brass stronger and more corrosion resistant. Aluminium also causes a highly beneficial hard layer of aluminium oxide (Al2O3) to be formed on the surface that is thin, transparent and self healing. Tin has a similar effect and finds its use especially in sea water applications (naval brasses). Combinations of iron, aluminium, silicon and manganese make brass wear and tear resistant.
Diamond (from the ancient Greek αδάμας – adámas "unbreakable") is an allotrope of carbon. Diamond is less stable than graphite, but the conversion rate from diamond to graphite is negligible at ambient conditions. Diamond has the highest hardness and thermal conductivity of any bulk material. Those properties determine the major industrial application of diamond in cutting and polishing tools.
Diamond has remarkable optical characteristics. Combined with wide transparency, this results in the clear, colorless appearance of most natural diamonds. Diamond also has relatively high optical dispersion, that is ability to disperse light of different colors, which results in its characteristic luster. Excellent optical and mechanical properties, combined with efficient marketing, make diamond the most popular gemstone.
Diamond is the hardest natural material known, where hardness is defined as resistance to scratching and is graded between 1 (softest) and 10 (hardest) using the Mohs scale of mineral hardness. Diamond has a hardness of 10 (hardest) on this scale. Diamond's hardness has been known since antiquity, and is the source of its name.
Diamond hardness depends on its purity. The hardness of diamond contributes to its suitability as a gemstone. Because it can only be scratched by other diamonds, it maintains its polish extremely well. Unlike many other gems, it is well-suited to daily wear because of its resistance to scratching—perhaps contributing to its popularity as the preferred gem in engagement or wedding rings, which are often worn every day.
Other specialized applications also exist or are being developed, including use as semiconductors: some blue diamonds are natural semiconductors, in contrast to most diamonds, which are excellent electrical insulators.
Cement is a substance which can be mixed with water and become hard after drying. The term cement refers only to the dry powder substance. After the addition of water the cement mixture is referred to as “concrete”. Cement (mixed with water) can join other materials together.
The word "cement" traces to the Romans, who used the term "opus caementicium" to describe construction which was made from crushed rock with burnt lime as binder. Cements used in construction are characterized as hydraulic or non-hydraulic.
The most important use of cement is the production of a strong building material.
ALLOYS
An alloy is a mixture of two or more elements in solid solution in which the major component is a metal. Most pure metals are either too soft, brittle or chemically reactive for practical use. Combining different ratios of metals as alloys modifies the properties of pure metals to produce desirable characteristics. The aim of making alloys is generally to make them less brittle, harder, resistant to corrosion, or have a more desirable color and luster. Of all the metallic alloys in use today, the alloys of iron (steel, stainless steel, cast iron, tool steel, alloy steel) make up the largest proportion both by quantity and commercial value. Iron alloyed with various proportions of carbon gives low, mid and high carbon steels, with increasing carbon levels reducing ductility and toughness. The addition of silicon will produce cast irons, while the addition of chromium, nickel and molybdenum to carbon steels (more than 10%) results in stainless steels.
Other significant metallic alloys are those of aluminium, titanium, copper and magnesium. Copper alloys have been known since prehistory—bronze gave the Bronze Age its name—and have many applications today, most importantly in electrical wiring. The alloys of the other three metals have been developed relatively recently; due to their chemical reactivity they require electrolytic extraction processes. The alloys of aluminium, titanium and magnesium are valued for their high strength-to-weight ratios; magnesium can also provide electromagnetic shielding. These materials are ideal for situations where high strength-to-weight ratio is more important than material cost, such as in aerospace and some automotive applications.
Alloys specially designed for highly-demanding applications, such as jet engines, may contain more than ten elements.
Дата добавления: 2018-11-24; просмотров: 414; Мы поможем в написании вашей работы! |
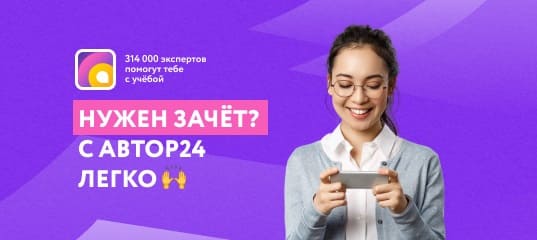
Мы поможем в написании ваших работ!