Анализ поведения условий инструмента
Статистический анализ условий процесса глубокого сверления с использованием вибраций и силовых сигналов
Hazwan Syafiq1, M.A.N. Kamarizan1, M.F. Ghazali2 и A.R Yusoff1, a
1 Факультет производственной инженерии, Университет Малайзии Паханг, 26600, Пекан, Паханг
2 Факультет машиностроения, Университет Малайзии Паханг, 26600, Пекан, Паханг
Аннотация.
Системы охлаждения являются ключевым моментом для процесса горячей формовки сверхпрочных сталей (UHSS). Обычно,
системы охлаждения производятся методом глубокого сверления. Хотя глубокое сверло лучше, чем другое сверление технологий в условиях более высокой производительности, однако его основной проблемой является преждевременное разрушение инструмента, которое влияет на качество производства. В этой статье анализируются параметры процесса глубокого сверления, такие как скорость резания, скорость подачи и глубина резки с использованием статистического анализа для определения условия инструмента. Также изучаются две геометрии инструмента. Измеряемые данные от вибраций и датчиков силы анализируются через несколько статистических параметров, таких как среднеквадратичное отклонение (стандартное отклонение), среднее значение, эксцесс, и асимметрия.
Результат показал, что эксцесс и значение асимметрии являются наиболее подходящими параметрами для представления глубокого сверления, влияния условий работы инструмента от значений вибраций и сил. Состояние процесса глубокого сверления было классифицировано в соответствии с хорошим, тупым и переломным состоянием инструмента. Он также обнаружил, что различные параметры геометрии инструмента влияют на производительность инструмента. Мы полагаем, что результаты этого исследования полезны при определении подходящего метода анализа, который будет использоваться для разработки онлайн-системы мониторинга состояния инструмента для определения стадии жизни третичного инструмента и помогает избежать созревание разрушения инструмента во время сверления.
|
|
Введение
Сверление - это наиболее знакомые операции станков в технологии производства на сегодняшний день. Почти 75 процентов операций по резке металла все еще выполняется обычными сверлами [1]. Поскольку отрасль выделяет значительную сумму денег на инструменты сверления, идея снизить себестоимость при сверлении осуществляется путем внедрения глубокого сверления. В этом методе отверстие можно просверлить как минимум 10 раз от диаметра бурового долота, которые позволяют создавая более глубокое отверстие [2]. Существует несколько глубоких методов сверления, применяемых в промышленности, такие как сверлильный трепаннинг, бурение эжектора систем и пулемета. Однако есть альтернативные методы, предложенные исследователями для преодоления слабости глубоких методов сверления, называемая техника глубокого сверления. Глубокое сверление может уменьшить издержки производство используя высокую скорость и скорость подачи по сравнению с другими глубокими методами сверления. Основываясь на текущих исследованиях, установлено, что метод глубокого сверления может улучшить скорость охлаждения. Увеличивая резку длина инструмента сверла для увеличения охлаждения энергоэффективность, которая может уменьшить количество горячих образующих блоков. Однако одна из основных проблем в технологии глубокого сверления - преждевременный разрыв инструмента;
|
|
из-за износа инструмента, засорения и прогибов стружки, которые могут повлиять на устойчивость процесса. Поэтому существует необходимость в более четком понимании явления глубокого сверления.
Применяются статистические параметры в анализе исследований. Благодаря внедрению статистического анализа можно улучшить процесс понимания, повышенного уровня контроля и, следовательно, вносить вклад в снижение изменчивости процесса и качество выходного сигнала [3]. Существует несколько статистических параметров, такие как среднее геометрическое, среднее арифметическое, стандартное отклонение, дисперсия и эксцесс и т. д. Они широко используется в производственных процессах. Гхореши и другие [4] применили дисперсию для анализа взаимодействий между шестью контролируемых переменных на конусности и округлости отверстия в лазерном перкуссионном сверлении. ANOVA также используется для изучения эффекта параметров сверления, таких как скорость резания, скорость подачи, угол и диаметр инструментального сверла [5, 6]. В то же время,
|
|
Гая [7] внедрил RMS для анализа глубины резки данных обнаружения и зацепления заготовки с помощью системы контроля акустической эмиссии во время фрезерования. Значения RMS также использовались для классифицированного инструмента уровни износа в токарных, фрезерных и сверлильных станках [8, 9, и 10]. Выраженность и асимметрия данных вибрационного сигнала также должны быть реализованы для обозначения различных типов износостойкости [11].
Jantunen et al. [12] сравнили семь статистических параметров, как RMS, асимметрия, эксцесс, среднее арифметическое, максимальное и минимальное значение износа инструмента измерение. Основываясь на сравнении, он обнаружил, что значение RMS является подходящими параметрами для представления данных тематического исследования. Патрик [13] в своем тезисе сравнивал шесть статистических параметров: среднее, пиковое, среднеквадратичное отклонение, дисперсия, ассиметрия и эксцесс в изучении схемы сигналов острого сверла и изношенного сверла. Результаты показывают, что четыре параметра, которыми являются RMS, пиком, ассиметрией и эксцессом способны оценивать шаблоны и уровни разных
|
|
измеренных сигналов. Однако он также обнаружил, что пик неподходящий для применения в процессе сверления из-за поведение стохастического древа и пиковый уровень не являются усреднем статистической величины. Резюмируется, что лучше результаты могут быть получены путем рассмотрения производных факторов, таких как асимметрия и эксцесс. Сюй [14] несколько статистических параметров для нахождения отношений между условиями процесса сверления с несколькими процесса обработки такими как материал заготовки, диаметр сверла,
скорость шпинделя, скорость подачи и угол поворота сверла.
Применяемые статистические параметры представляют собой средние значения, RMS, дельта и стандартные отклонения. Основываясь на анализе, материал, скорость шпинделя, скорость подачи и диаметр сверла сравнения, он обнаружил, что данные производятся средним значением и RMS почти аналогичны, но отличаются от дельта-функций из-за статистического алгоритма. Между тем другие параметры четко различаются по значениям, особенно в скорости подачи. Сделан вывод о том, что среднее и среднеквадратичное значение аналогичные значениям и вариационным формам, таким образом, некоторые из них можно устранить как избыточные.
Основываясь на обзоре, можно резюмировать, что многие особенно в буровых работах используют статистический анализ параметров. Хотя нет примеров статистического анализа случая глубокого сверления, исследование показало, что предполагается, что концептуальные этапы и методология будет такими же, как и стандартное бурение. В статье обсуждается идентификация инструмента глубокого сверления когда различные параметры обработки, такие как скорость резания, скорость подачи и глубина резки.
Идентификация осуществляется через несколько статистических параметров; среднеквадратичный (среднеквадратичный), средний, эксцесс, стандартное отклонение и асимметрия. Тогда по сравнению с поиском наиболее подходящих статистических параметров, которые могут представлять собой поведение условия устройства. В этом исследовании это также приводит к нахождению подходящих параметров обработки и геометрии инструмента, которую можно использовать в глубоком сверлении чтобы получить максимальную глубину сверления.
Экспериментальная установка
Эксперименты с условием глубокого твист-сверления прводятся на 3-осевой вертикальной машине с ЧПУ (HAAS CNC Вертикальная машина). Используемый инструмент - высокая сталь, сверлильные сверла серии HSS диаметром 8 мм, общая длина 165 мм и длина канавки 109 мм. Поскольку это начальное исследование, хорошо начать со стандартной геометрии инструментального сверла, как указано в таблице 1. Основываясь на
проведенном обзоре литературы, нет исследования, в котором основное внимание уделяется на производительность этого инструмента даже главный производитель продолжает производить и продвигать эти типы геометрии.
Материал, SKD 61. Это труднорежущий материал с диапазонами HRC 50-55 в области штамповки и плесени.
Заготовку разрезают на блок размером 90 мм х 70мм х 80 мм. 25 отверстий просверлены в блоке, который удерживается в тисках на динамометре. Каждое из отверстий сверлят с использованием различных условий резания, таких как скорость резания, скорость подачи и глубина резки от проектирования эксперимента, как указано в таблице 2.
Резюме
диапазоны условий резания, используемые при проектировании эксперимента, DOE относятся к данным, используемым другими исследователями и данным, предоставленным производителем инструмента. Эксперименты разделены на 5 областей, которые представляют собой число разрезов и скорость. Этот эксперимент повторяется до 3 раз, чтобы получить надежные результаты. Все отверстия были отмечены предварительными центрами с использованием пилотного сверла диаметром 8 мм и глубиной 1,5 мм. Это может минимизировать эффекты, связанные с отключением инструмента [15].
Между тем, для сбора данных, силы и вибрации
датчики установлены на заготовку и шпиндель
машины, как показано на рисунке 1. Динамометр; модель Kistler 9257B со встроенным 3-осевым усилителем заряда прилагается на заготовке. Между тем для вибрации триаксиальный акселерометр (модель 356B21) с чувствительностью + 10 мВ / г прикрепляется к шпиндельной машине. Аналоговые сигналы от этих датчиков подавались в сбор данных на плату, DAQ с возможностью выборки частоты 2000.
Между тем, для экспериментов для сравнения между двумя инструментами различной геометрии, отверстия с оптимальными результатами условия инструмента из предыдущего эксперимента снова повторяются другой геометрией инструмента, такая как угол точки, угол спирали, сетка толщины и угла рельефа. Собранные данные сравниваются и анализируются. Детали для обеих спецификаций инструментальных сверл приведены в таблице 1.
а). Принципиальная схема
б). Экспериментальная установка
Рисунок 1. Схема и фактическая настройка
эксперимент.
Таблица 2. Условия резания для 25 экспериментов.
Таблица 2. Условия резания для 25 экспериментов.
Экспериментальный регион
Резка
Скорость
(М / мин)
Скорость подачи
(Мм / об)
Глубина
Порез
(Мм)1
1
30 0.10 40
2 30 0.15 50
3 30 0.20 60
4 30 0.25 70
5 30 0.30 80
6
2
40 0.10 50
7 40 0.15 60
8 40 0.20 70
9 40 0.25 80
10 40 0.30 40
11
3
50 0.10 60
12 50 0.15 70
13 50 0.20 80
14 50 0.25 40
15 50 0.30 50
16
4
60 0.10 70
17 60 0.15 80
18 60 0.20 40
19 60 0.25 50
20 60 0.30 60
21
5
70 0.10 80
22 70 0.15 40
23 70 0.20 50
24 70 0.25 60
25 70 0.30 70
Статистическое измерение
Для анализа данных, генерируемых динамометром и
датчики акселерометра, статистические параметры применялись и сравнивались. Этими параметрами являются среднеквадратичный (среднеквадратичный), средний μ, стандартное отклонение, эксцесс K и асимметрия S. Эти параметры могут быть рассчитанной по следующим формулам, упомянутам в [11].
Среднее (μ) вычисляет сигналы силы и вибрации среднее значение для N = 2000 образцов:
(1)
Среднее квадратическое (RMS) является наиболее распространенным параметром используется в статистическом анализе [16]. Его значение содержит все энергии в сигнале и, следовательно, также весь шум и все элементы, которые зависят от процесса резания. RMS
определяется как:
(2)
где они относятся к мгновенной амплитуде сигнала от силы и вибрации. Между тем для стандартных
отклонения, данные были стандартизированы и
это среднее квадратное значение относительно среднего значения:
(3)
Далее, эксцесс (K) является мерилом того, как рассеяно распределение [17]. Основываясь на Иссаме [11], нормальное распространение эксцесса - 3. Между тем для распространения то есть более или менее склонный к структуризации, имеющий эксцесс более или менее 3. Эксцесс определяется как:
(4)
Где х среднее значение амплитуды силы и вибрации. В ходе анализа он обнаружил, что эксцесс был довольно чувствительным к появлению шипов или импульсов в временной области вибрационного сигнала [18]. Асимметрия (S) является мерой симметричности данных вокруг выборочного среднего. Скошенность определяется как:
(5)
В следующем разделе, результаты экспериментов анализируются и обсуждаются.
Результаты и обсуждение
Анализ поведения условий инструмента
На рисунках 2 и 3 показано поведение условий на основе инструментов на пяти статистических анализах вибраций и сил. Инструментальные условия классифицируются в три категории; хорошие, сломанные и тупые. Основываясь на состоянии инструмента, только 6 из 25 отверстий способны заканчиваться без сбоев.
Эксперименты № 1, 2, 3, 4, 6 и 7 относятся к категории «хорошее состояние», в то время как другие находятся в тупых и сломанных категориях. Самая высокая скорость резания, которая может быть адаптирована через стандартный инструмент для сверления длинной серии (Шервуд SHR-025) через эксперимент номер 7 с 40 м / мин, скорость подачи 0,15 мм / об. и глубина резки 60 мм.
Сеть конференций MATEC 74, 00002 (2016) DOI: 10.1051 / matecconf / 20167400002
0,25 мм / об. С частотой резания 30 м / мин и глубиной 70 мм через эксперимент № 4. В терминах глубокого сверления, отношение длины к диаметру L / D должно быть не менее 10 [1]. Через параметр резания эксперимент номер 7, он может достичь 8,75 L / D, где этого недостаточно, чтобы стоять как теория глубокого сверления.
Однако на основе рисунка, показанного номером эксперимента 6; среднее значение его вибрации является самым низким. Установлено, что можно увеличить глубину от 50 мм до 80 мм до L / D 10. В связи с этим, условие резания эксперимента номер 6 будет использовано для эксперимента геометрии инструмента, изменяя глубину от 50 до 80 мм.
Дата добавления: 2018-11-24; просмотров: 110; Мы поможем в написании вашей работы! |
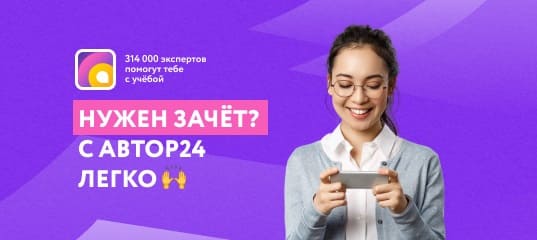
Мы поможем в написании ваших работ!