На тем: Расчет режимов резания при шевинговании зубьев дисковым шевером
МИНОБРНАУКИ РОССИИ
Сарапульский политехнический институт (филиал)
федерального государственного бюджетного образовательного учреждения высшего образования
"Ижевский государственный технический университет имени М.Т.Калашникова"
(СПИ (филиал) ФГБОУ ВО «ИжГТУ имени М.Т.Калашникова)
СОВРЕМЕННЫЕ ТЕХНОЛОГИИ
Методические указания
к выполнению лабораторных работ по дисциплине «Современные технологии»
для студентов направления 151900.62 «Конструкторско-технологическое обеспечение машиностроительных производств»,
всех форм обучения
Сарапул
2016
Кафедра «Технология машиностроения, металлорежущие станки и инструменты»
Составитель ст. преподаватель Лунин Денис Анатольевич
Методические указания составлены на основании государственного образовательного стандарта высшего образования и утверждены на заседании кафедры
Протокол №10 от 01 сентября 2016 г.
Современные технологии: Метод указания к выполнения лабораторных работ по дисциплине «Современные технологии»/ Составитель Лунин Д.А.- Сарапул, 2016 – 17с.
СОДЕРЖАНИЕ
Лабораторная работа №1. Расчет параметров алмазного выглаживания.............................. 3
Лабораторная работа №2. Расчет режимов резания при шевинговании зубьев дисковым шевером......................................................................................................................................................... 5
Лабораторная работа №3. Расчет режимов поверхностного дорнования............................. 10
|
|
Лабораторная работа №4. Расчет сил, действующих на накатник при накатывании зубьев 13
СПИСОК ЛИТЕРАТУРЫ.......................................................................................................... 16
Лабораторная работа №1.
На тему: Расчет параметров алмазного выглаживания
Цель работы: Научиться рассчитывать режимы алмазного выглаживания.
Ход работы:
- Рассчитать усилилие при выглаживании
- Оформить отчет
- Защитить отчет по лабораторной работе
РАСЧЕТ РЕЖИМОВ АЛМАЗНОГО ВЫГЛАЖИВАНИЯ
Для обработки деталей с высокой точностью и малой шероховатостью поверхности применяют алмазное выглаживание, с помощью которого достигается шероховатость поверхности Rа=0,1 мкм. В качестве инструмента при алмазном выглаживании применяют державку, в которой закрепляют в оправе кристалл алмаза или синтетического сверхтвердого материала массой 0,5-1,0 карата. Алмазное выглаживание осуществляют, как правило, за один проход, так как увеличение числа проходов не изменяет существенно шероховатость поверхности упрочняемой детали.
Алмазное выглаживание сопровождается смятием гребешков микронеровностей и появлением наклепа на обрабатываемой поверхности вследствие скольжения по ней алмазного инструмента под определенным давлением. Поверхности, обработанные алмазным выглаживанием, обладают высокой износоустойчивостью при образовании пар трения и высокой усталостной прочностью. Особо важно значение этого процесса при изготовлении подвижных пар гидроуплотнений. В этом случае металлическая деталь гидроуплотнения не подвергается традиционной термической обработке для повышения твердости, поскольку необходимая твердость поверхности обеспечивается алмазным выглаживанием сырой заготовки.
|
|
Рабочая поверхность алмаза имеет форму полусферы и отличается высоким качеством. Жестко закрепленная в резцедержателе державка с алмазом при поперечном движении суппорта подводится к вращающейся детали. При дальнейшем движении суппорта в поперечном направлении создается небольшой натяг. Затем при равномерной продольной подаче суппорта алмаз перемещается вдоль обрабатываемой поверхности детали.
Усилие прижатия инструмента к детали также имеет большое значение. При усилии меньше оптимального микронеровности сглаживаются не полностью, а при большем поверхностный слой перенаклепывается и разрушается.
|
|
Алмазный инструмент представляет собой кристаллический алмаз, закрепленный в специальной державке и отшлифованный по сфере с радиусом 0,6—4,0 мм. Отклонения выглаживания в положении алмазного инструмента при выглаживании фиксируется индикаторной головкой. На точность обработки алмазное выглаживание влияет слабо. Шероховатость поверхности в результате процесса может снизиться на 2-3 класса с доведением ее до 0,16-0,025 мкм. На качество поверхности в основном влияют усилие выглаживания и подача. Микротвердость поверхности повышается на 50—60%.
Инструмент для выглаживания состоит из наконечника с алмазом и державки. Державка при работе крепится на суппорте станка или в пиноли задней бабки. Нагружающие механизмы державок имеют упругие элементы (пружины), обеспечивающие непрерывный контакт алмаза с обрабатываемой поверхностью и примерно одинаковое усилие выглаживания.
Скорость алмазного выглаживания принимается в зависимости от материала обрабатываемой заготовки. Так, для цветных сплавов и мягких сталей она принимается в пределах 10—80 м/мин, для закаленных сталей 200—250 м/мин. Алмазным выглаживанием обрабатывают заготовки из черных и цветных металлов, предварительно обработанных шлифованием, тонким точением и другими методами, обеспечивающими заданную точность. Из-за нестабильности качества выглаживанием не обрабатывают детали со значительными отклонениями формы в поперечном сечении или неравномерной твердостью поверхности (разброс значений твердости не более 4—5 единиц по Роквеллу). Выглаживание можно выполнять на универсальных и специальных станках.
|
|
В процессе выглаживания поверхностей в месте контакта деформирующего элемента и обрабатываемой детали возникают значительные контактные напряжения. При определенном усилии выглаживания происходит пластическая деформация поверхностного слоя, в результате чего сминаются микронеровности и изменяются физико-механические свойства поверхностного слоя. Выглаживанием могут обрабатываться наружные и внутренние поверхности вращения (цилиндрической, сферической и другой формы), торцовые поверхности на токарных, карусельных, сверлильных, расточных и других станках.
Алмаз обладает анизотропными свойствами, свойства его неодинаковы по различным кристаллографическим осям; это оказывает влияние, в частности, на износостойкость алмаза при выглаживании. Поэтому при креплении алмаза его ориентируют по риске, которую наносят на корпусе наконечника в направлении скорости. Риска определяет положение, при котором износ будет происходить в направлении наибольшей твердости алмаза.
Алмазное выглаживание проводится копирующим инструментом. Поэтому отклонения формы в продольном и поперечном сечениях изменяются незначительно, а размер детали (за счет смятия исходных микронеровностей) — на 1-15 мкм. Точность обработки при этом может несколько снизиться. В связи с этим целесообразно на предшествующем переходе обеспечивать точность размеров на 20—30% выше заданной для окончательно обработанной детали.
Качество обработанной поверхности существенно зависит от режимов выглаживания — усилия выглаживания и подачи. Число проходов и скорость выглаживания влияют на шероховатость и микротвердость обработанной поверхности в меньшей степени. При правильно подобранных режимах выглаживания микронеровности на поверхности могут быть уменьшены в несколько раз (Ra = 0,1 ÷ 0,05 мкм), микротвердость увеличивается на 5—60% (глубина наклепанного слоя до 400 мкм). На выглаженной поверхности возникают значительные остаточные напряжения сжатия. Так, например, величина наибольших остаточных напряжений для образцов из стали 45 после нормализации равна 200—350 МПа, а после закалки - 700 - 1000 МПа.
Детали с поверхностью, обработанной алмазным выглаживанием, обладают хорошими эксплуатационными качествами: высокой износостойкостью и усталостной прочностью.
Параметрами выглаживания, влияющими на шероховатость являются: сила выглаживания, подача и радиус рабочей части инструмента. При увеличении силы до определенного значения шероховатость уменьшается.
Оптимально значение силы при выглаживании:
для закаленных сталей:
(1)
для материалов невысокой и средней твердости:
(2)
HV – твердость, обрабатываемой поверхности по Виккерсу; D – диаметр, обрабатываемой поверхности, мм.; R – радиус рабочей части алмаза, мм.
Сила выглаживания большая 200-250Н. для деталей из высокопрочных материалов и большая 100-150Н. для деталей из материалов средней твердости, как правило, нецелесообразна.
Таблица 1 – Исходные данные
| Исходные данные по вариантам | |||||||||||||||||||
1 | 2 | 3 | 4 | 5 | 6 | 7 | 8 | 9 | 10 | 11 | 12 | 13 | 14 | 15 | 16 | 17 | 18 | 19 | 20 | |
Радиус алмазного наконечника | 10 | 3,2 | 13 | 10 | 13 | 2,0 | 3,2 | 13 | 10 | 2,0 | 13 | 3,2 | 2,0 | 10 | 13 | 3,2 | 13 | 10 | 13 | 3,2 |
Диаметр обрабатываемой заготовки | 50 | 55 | 60 | 65 | 70 | 75 | 80 | 85 | 50 | 55 | 60 | 65 | 70 | 75 | 80 | 85 | 60 | 65 | 70 | 75 |
Твердость материала детали по Виккерсу | 156 | 320 |
Лабораторная работа №2.
На тем: Расчет режимов резания при шевинговании зубьев дисковым шевером
Цель работы: Научиться рассчитывать режимы резания при шевинговании зубьев.
Ход работы:
- Рассчитать режимы резания при шевинговании
- Оформить отчет
- Защитить отчет по лабораторной работе
Шевингование зубьев — метод окончательной обработки незакаленных колес — обеспечивает повышение точности до 5-6-й степени и качество поверхности (Ra = 0,63-0,16 мкм). Шевингованию подвергают зубья с твердостью ≤380HB.
В процессе шевингования с поверхности зубьев снимаются (соскабливаются) тонкие стружки толщиной 0,005-0,001 мм. При этом происходит исправление эксцентриситета начальной окружности, возникают ошибки в шаге, в профиле эвольвенты. Шевингование осуществляется двумя способами: шевером-колесом (диском) или шевером-рейкой.
Шевер имеет зубья, на боковых поверхностях которых расположены радиальные канавки глубиной 0,8 мм. Эти канавки образуют режущие кромки, которые осуществляют снятие тонких стружек с поверхности зубьев.
Рисунок 1 – Расположение канавок на зубе шевера
Припуск, оставляемый на шевингование, составляет 0,06-0,2 мм на сторону по толщине зуба (в зависимости от модуля). Для получения точности 5-6-й степени исходная точность должна быть не ниже 8-9-й.
Обрабатываемое колесо устанавливается на оправке в центрах стола станка. Шевер располагается над зубчатым колесом под углом 15°, образуя с колесом как бы винтовую пару со скрещивающимися осями. Наличие скрещивания осей зубчатой пары — колеса и шевера — создает необходимое условие: продольное скольжение зубьев шевера относительно зубьев колеса, в результате чего и происходит соскабливание стружек с поверхности последнего.
Рисунок 2 – Схема шевингования дисковым шевером(а) и схема работы зуба шевера (б): 1 – шевер; 2 – заготовка колеса.
Вращение сообщается шеверу, а шевер вращает обрабатываемое колесо. Шевер вращает колесо попеременно в одном и в другом направлениях для обработки обеих сторон зуба. Стол станка имеет также вертикальное перемещение и продольное (осевое) для обработки всей длины зуба при коротком шевере.
Инструмент. При использовании шеверов, изготовляемых в соответствии с ГОСТ 8570—80, рекомендуется следующее:
а) числа зубьев шевера zш и колеса zк не должны иметь общих множителей; это можно не соблюдать для колес 7-8-й степени точности по нормам плавности работы; б) при обработке колес с числом зубьев zк <20, особенно с положительным смещением исходного контура, следует применять шеверы с наибольшим числом зубьев; в) выбранный нормализованный шевер должен обеспечивать выполнение условия рр0 < рp, где рр0 и рp – соответственно нижняя точка активного профиля зуба колеса в передаче и в станочном зацеплении с шевером при минимальном межосевом расстоянии в обработке а0..
Припуск на шевингование по межцентровому расстоянию для прямозубых колес можно определить по формуле:
, мм. (1)
где m – модуль зубчатого колеса, мм; α – угол зацепления зубьев, град.
Припуск на шевингование для прямозубых колес по толщине зуба:
, мм. (2)
Припуск по межцентровому расстоянию для косозубых колес:
, мм. (3)
Припуск на толщину зуба для косозубых колес:
, мм. (4)
Продольная подача Sпр осуществляется вдоль оси заготовки и сообщается столу
станка с обрабатываемым колесом.
Продольная подача стола /зубчатого колеса/ может быть вычислена по формуле:
мм/об. колеса. (5)
где HB – твердость обрабатываемого материала, из которого изготовлено колесо.
Значения CSП , q1 и n1 приведены в таблице 1.
Таблица 1.
Радиальная подача Sр производится в конце продольного хода каждого прохода или после двойного прохода в прямом и возвратном направлениях. Радиальная подача производится путем сближения осей шевера и обрабатываемого колеса до получения требуемых размеров зубьев колеса.
Радиальная подача шевера после прохода стола станка может быть вычислена по
формуле:
мм/об. шевера. (6)
Значения СSР , q2 и n2 приведены в таблице 1.
Обычно вращение сообщается шеверу Vош , а обрабатываемое колесо находится с ним в плотном зацеплении и свободно вращается в центрах.
Окружная скорость шевера может быть вычислена по формуле:
м/мин. (7)
KМ – поправочный коэффициент, характеризующий марку стали, из которой изготовлено колесо, приведен в таблице 2.
Таблица 2.
KНВ – поправочный коэффициент, характеризующий твердость материала колеса:
(8)
KТ – поправочный коэффициент, характеризующий выбранную стойкость шевера, т.е.
отношение выбранной стойкости Tуст, мин. к нормативной Tнорм, мин. приведен в таблице 3.
Таблица 3.
Нормативную стойкость шевера можно посчитать по формуле:
, мин. (9)
где Dдш – диаметр делительной окружности шевера, мм.
Количество рабочих ходов стола станка определится как:
(10)
Количество одинарных ходов без радиальной подачи обычно принимается 2 - 4.
Частота вращения шевера:
об/мин. (11)
где Dш – диаметр шевера, мм.
Рассчитанное значение nш заменяется ближайшим значением частоты вращения
шпинделя no , имеющимся в станке.
Скорость движения стола станка с зубчатым колесом подсчитывается по формуле:
мм/мин. (11)
где zш и zк – число зубьев шевера и зубчатого колеса соответственно.
Подсчитанное значение VS заменяется ближайшим значением скорости стола Sмин,
имеющимся на станке.
Таблица 4 – Исходные данные для расчета
Исходные данные по вариантам | ||||||||||||||||||||
1 | 2 | 3 | 4 | 5 | 6 | 7 | 8 | 9 | 10 | 11 | 12 | 13 | 14 | 15 | 16 | 17 | 18 | 19 | 20 | |
Модуль, m | 1,25 | 1,25 | 1,375 | 1,375 | 1,5 | 1,5 | 1,75 | 1,75 | 2,0 | 2,0 | 1,375 | 1,5 | 1,25 | 1,75 | 2,0 | 1,375 | 1,25 | 2,0 | 1,5 | 1,75 |
Угол зацепления зубьев | 20 | 20 | 20 | 20 | 20 | 20 | 20 | 20 | 20 | 20 | 20 | 20 | 20 | 20 | 20 | 20 | 20 | 20 | 20 | 20 |
Твердость, НВ | 156 | 178 | 186 | 201 | 212 | 178 | 156 | 186 | 178 | 156 | 201 | 186 | 178 | 212 | 156 | 178 | 186 | 201 | 212 | 156 |
Установочная стойкость шевера | 1100 | 1100 | 1100 | 1100 | 1100 | 1100 | 1100 | 1100 | 1100 | 1100 | 1100 | 1100 | 1100 | 1100 | 1100 | 1100 | 1100 | 1100 | 1100 | 1100 |
Диаметр делительной окружности шевера | 144,3 | 148,8 | 158,7 | 163,7 | 173,1 | 178,6 | 175,7 | 181,2 | 166,6 | 171,8 | 158,7 | 178,6 | 148,8 | 181,2 | 166,6 | 163,7 | 148,8 | 171,8 | 173,1 | 175,7 |
Диаметр шевера | 135,537 | 139,262 | 149,090 | 153,189 | 162,643 | 167,115 | 165,000 | 169,537 | 156,515 | 160,818 | 149,090 | 167,115 | 139,262 | 169,537 | 156,515 | 153,189 | 139,262 | 160,818 | 162,643 | 165,000 |
Число зубьев шевера | 115 | 115 | 115 | 115 | 115 | 115 | 100 | 100 | 83 | 83 | 115 | 115 | 115 | 100 | 83 | 115 | 115 | 83 | 115 | 100 |
Число зубьев колеса | 58 | 58 | 58 | 58 | 58 | 58 | 51 | 51 | 42 | 42 | 58 | 58 | 58 | 51 | 42 | 58 | 58 | 42 | 58 | 51 |
Во всех вариантах материал заготовки – углеродистая сталь.
Лабораторная работа №3.
Дата добавления: 2018-11-24; просмотров: 976; Мы поможем в написании вашей работы! |
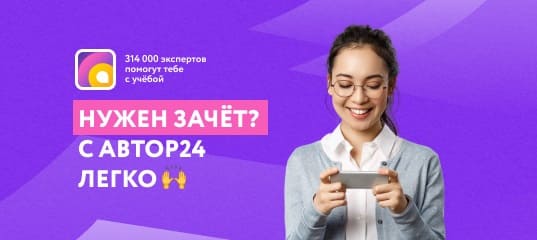
Мы поможем в написании ваших работ!