Унификация диаграмм работы стали
Раздел 1. Введение в проектирование металлических конструкций 1.1 Области применения МК : n Промышленные здания; n Большепролетные покрытия зданий; n Мосты и эстакады; n Листовые конструкции; n Башни и мачты; n Каркасы многоэтажных зданий; n Крановые и другие подвижные конструкции; n Прочие конструкции (по использованию атомной энергии, радиотелескопы, стационарные платформы для разведки и добычи нефти в море и др.). 1.2 Достоинства и недостатки МК Достоинства: n Надежность. Надежность МК обеспечивается близким совпадением их действительной работы с расчетными предположениями. n Легкость. Легкость конструкций определяется отношением плотности материала к его расчетному сопротивлению C=r/R: для бетона С=21,4∙10-4 м-1; для древесины сосны С=3,6∙10-4 м-1; для малоуглеродистой стали С=3,2∙10-4 м-1. n Индустриальность. МК изготавливаются в основном на заводах, оснащенных современным оборудованием. n Непроницаемость. Металлы обладают высокой прочностью и высокой плотностью, что делает их непроницаемыми для жидкостей и газов. Недостатки: n Коррозия (сталь, алюминий, чугун). Незащищенная от влажной и агрессивной среды сталь окисляется и корродирует, что приводит к полному разрушению МК. Скорость действия коррозии может достигать 0,5 мм/год. n Небольшая огнестойкость. При температуре 200 оС у стали уменьшается модуль упругости, а при температуре 600 оС сталь полностью переходит в пластическое состояние. При проектировании МК должны учитываться следующие основные требования: n Условия эксплуатации; n Экономия металла; n Транспортабельность; n Технологичность; n Скоростной монтаж; n Долговечность; n Эстетичность.
|
|
Анализ свойств материалов для строительных МК
Для строительных металлических конструкций используется в основном малоуглеродистая сталь и алюминиевые сплавы. В некоторых видах элементов конструкций, где требуется высокая износоустойчивость при работе на сжатие также используется чугун.
Сталь обладает почти идеальным комплексом свойств для использования в строительных конструкциях:
1. сочетание прочности и пластичности;
2. хорошая свариваемость;
3. однородность механических свойств.
Основные недостатки стали:
1. относительно низкая коррозионная стойкость и необходимость специальной защиты стальных конструкций от коррозии;
2. снижение пластических свойств при низких температурах;
3. малая огнестойкость.
К достоинствам алюминиевых сплавов относятся:
1. малая плотность (почти в 3 раза меньше, чем у стали) при относительно высокой прочности;
2. повышенная стойкость против коррозии;
|
|
3. сохранение высоких упругопластических свойств при низких температурах.
Однако низкий модуль упругости приводит к повышенной деформативности алюминиевых конструкций и ухудшает их устойчивость, а падение прочностных свойств алюминиевых сплавов при температуре 300 °С снижает огнестойкость.
Чугун хорошо работает на сжатие и обладает высокой коррозионной стойкостью, однако малая прочность при растяжении, хрупкость материала и плохая свариваемость привели к тому, что в настоящее время чугун практически не применяется для строительных конструкций. Чугунные конструкции можно встретить в зданиях и сооружениях, построенных в XIX и XX вв. В настоящее время из чугуна делаются тюбинги метро. Применяется он иногда в литых деталях опор тяжелых конструкций.
Механические свойства сталей
1. Прочностьхарактеризует сопротивляемость материала внешним силовым воздействиям без разрушения. Основными прочностными характеристиками металла являются временное сопротивление sи и предел текучести sу . Диаграммы растяжения различных металлов показаны на рис. 1.1, а.
Временное сопротивление sи -это наибольшее условное напряжение в процессе разрушения образца (предельная разрушающая нагрузка, отнесенная к первоначальной площади поперечного сечения).
|
|
Предел текучести sу -напряжение, при котором деформации образца растут без изменения нагрузки и образуется площадка текучести - металл «течет». Для металлов, не имеющих площадки текучести, определяется условный предел текучести s02 , т.е. такое напряжение, при котором остаточное относительное удлинение достигает 0,2 %.
|
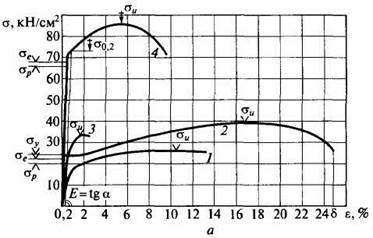
|
Если металл подвергается действию циклически меняющихся напряжений (например, чередующихся растяжения и сжатия), то при достаточно большом числе циклов разрушение может произойти при напряжении меньше временного сопротивления и даже предела текучести. Это явление называется усталостью металла. Склонность металла к усталостному разрушению устанавливается на основании результатов вибрационных испытаний.
|
|
Несколько ниже s е находится предел пропорциональности s р — напряжение, до которого материал работает линейно по закону Гука
s = E*e.
2. Упругость — свойство материала восстанавливать свою первоначальную форму после снятия внешних нагрузок.
Упругие свойства материала определяются модулем упругости
Е = tga,
где a — угол наклона линии деформирования металла к оси абсцисс, и пределом упругости s е , т.е. таким максимальным напряжением, при котором деформации после снятия нагрузки исчезают.
3. Пластичность — свойство материала сохранять деформированное состояние после снятия нагрузки, т. е. получать остаточные деформации без разрушения.
Мерой пластичности материала служит относительное остаточное удлинение при разрыве d.
Мерой пластичности может служить также относительное сужение при разрыве, %:
y = (A-A0)/A*100%,
где А и Ао — первоначальная и конечная после разрыва площади сечения образца.
4. Хрупкость— способность разрушаться при малых деформациях.
5. Ползучесть — свойство материала непрерывно деформироваться во времени без увеличения нагрузки.
Ползучесть в металлах, применяемых в строительных конструкциях, проявляется в основном при высоких температурах, а также для термообработанных высокопрочных сталей. Оценка степени ползучести производится по результатам длительных испытаний образцов на растяжение.
6. Твердость — свойство поверхностного слоя металла сопротивляться упругой и пластической деформациям или разрушению при внедрении в него индентора из более твердого материала.
Долговечность металлических конструкций определяется в первую очередь коррозионной стойкостью металла. Сопротивляемость металла коррозионным повреждениям зависит от химического состава и проверяется путем длительной выдержки образцов в агрессивной среде. Мерой коррозионной стойкости служит скорость коррозии по толщине металла, мм/год.
Основной способ соединения элементов МК – сварка, поэтому важнейшим требованием, предъявляемым к металлам строительных конструкций, является свариваемость. Оценка свариваемости производится по химическому составу (углеродному эквиваленту) и др. способами.
С течением времени свойства стали несколько меняются: увеличиваются предел текучести и временное сопротивление, снижается пластичность, сталь становится более хрупкой. Это явление называется старением стали.
Из физических характеристик металлов с точки зрения работы строительных конструкций наиболее важными являются плотность, модуль упругости при растяжении, модуль упругости при сдвиге, коэффициент поперечной деформации и коэффициент линейного расширения (см. таблицу).
Физические характеристики материалов, применяемых для МК
Общая характеристика сталей
Сталь — это сплав железа с углеродом, содержащий легирующие добавки, улучшающие качество металла, и вредные примеси, которые попадают в металл из руды или образуются в процессе выплавки.
Структура стали.В твердом состоянии сталь является поликристаллическим телом, состоящим из множества различно ориентированных кристаллов (зерен). В каждом кристалле атомы (точнее, положительно заряженные ионы) расположены упорядоченно в узлах пространственной решетки. Для стали характерны объемно-центрированная (ОЦК) и гранецентрированная (ГЦК) кубическая кристаллическая решетка (рис. 1.2).
Рис. 1.2 - а — объемно-центрированная; б — гранецентрированная
Температура плавления чистого железа равна 1535 °С, при твердении образуются кристаллы чистого железа – феррита (δ-железо); при температуре 1490 оС δ-железо переходит в γ-железо; при температуре 910 оС кристаллы γ-железа перходят в α-железо. При введении углерода температура плавления снижается и для стали с содержанием углерода 0,2 % составляет примерно 1520 оС. При остывании образуется твердый раствор углерода в γ-железе, называемый аустенитом. При температуре ниже 910 оС аустенит распадается с образованием феррита, который при температуре 723 оС превращается в перлит – смесь феррита и к4арбида железа Fe3C.
При нормальной температуре сталь состоит из двух основных фаз: феррита и цементита. Феррит очень пластичен и малопрочен, цементит тверд и хрупок.
При введении легирующих добавок в раствор с ферритом происходит упрочнение феррита. Кроме того, некоторые добавки образуя карбиды и нитриды увеличивают количество очагов кристаллизации и способствуют образованию мелкозернистой структуры (чем мельче зерно, тем сталь прочнее).
Простейшим видом термической обработки является нормализация – повторный нагрев проката до температуры образования аустенита и последующее охлаждение на воздухе.
При быстром остывании стали, нагретой до температуры, превосходящей температуру фазового превращения, сталь закаливается. Сталь имеет высокую прочность, но при этом очень хрупкая. Чтобы снизить хрупкость, сталь нужно отпустить (нагреть до температуры структурного превращения, выдержать при этой температуре некоторое время и дать стали медленно остыть).
1.6 Основные химические элементы, применяемые при легировании
Углерод (У), повышая прочность стали, снижает ее пластичность и ухудшает свариваемость, поэтому для строительных металлических конструкций применяются только низкоуглеродистые стали с содержанием углерода не более 0,22%.
В состав легированных сталей помимо железа и углерода входят специальные добавки, улучшающие их качество. Поскольку большинство добавок в той или иной степени ухудшают свариваемость стали, а также удорожают ее, в строительстве в основном применяются низколегированные стали с суммарным содержанием легирующих добавок не более 5 %.
Основными легирующими добавками являются кремний (С), марганец (Г), медь (Д), хром (X), никель (Н), ванадий (Ф), молибден (М), алюминий (Ю), азот (А).
n Кремний раскисляет сталь, т. е. связывает избыточный кислород и повышает ее прочность, но снижает пластичность, ухудшает при повышенном содержании свариваемость и коррозионную стойкость. Вредное влияние кремния может компенсироваться повышенным содержанием марганца.
n Марганец повышает прочность, является хорошим раскислителем и, соединяясь с серой, снижает ее вредное влияние. При содержании марганца более 1,5 % сталь становится хрупкой.
n Медь несколько повышает прочность стали и увеличивает ее стойкость против коррозии. Избыточное содержание меди (более 0,7 %) способствует старению стали и повышает ее хрупкость.
n Хром и никель повышают прочность стали без снижения пластичности и улучшают ее коррозионную стойкость.
n Алюминий хорошо раскисляет сталь, нейтрализует вредное влияние фосфора, повышает ударную вязкость.
n Ванадий, молибден и бор (Р) увеличивают прочность стали почти без снижения пластичности; сталь не разупрочняется при сварке.
n Азот (А) в несвязанном состоянии способствует старению стали и делает ее хрупкой, поэтому его должно быть не более 0,008 %. В химически связанном состоянии с алюминием, ванадием, титаном и другими элементами он образует нитриды и становится легирующим элементом, способствуя получению мелкозернистой структуры и улучшению механических свойств.
n Фосфор относится к вредным примесям, так как, образуя твердый раствор с ферритом, повышает хрупкость стали, особенно при пониженных температурах (хладноломкость) и снижает пластичность при повышенных. Однако при наличии алюминия фосфор может служить легирующим элементом, повышающим коррозионную стойкость стали. На этом основано получение атмосферостойких сталей.
n Сера вследствие образования легкоплавкого сернистого железа делает сталь красноломкой (склонной к образованию трещин при температуре 800—1000 °С). Это особенно важно для сварных конструкций. Вредное влияние серы снижается при повышенном содержании марганца. Содержание серы и фосфора в стали ограничивается и должно составлять не более 0,03—0,05 % в зависимости от типа (марки) стали.
Повышение механических свойств низколегированной стали осуществляется присадкой металлов, вступающих в соединение с углеродом и образующих карбиды и нитриды.
Вредное влияние на механические свойства стали оказывает насыщение ее газами, которые могут попасть из атмосферы в металл, находящийся в расплавленном состоянии. Кислород действует подобно сере, но в более сильной степени, и повышает хрупкость стали. Несвязанный азот также снижает качество стали. Водород хотя и удерживается в незначительном количестве (0,0007 %), но, концентрируясь около включений в межкристаллических областях и располагаясь преимущественно по границам зерен, вызывает в микрообъемах высокие напряжения, что приводит к снижению сопротивления стали хрупкому разрушению, снижению временного сопротивления и ухудшению пластических свойств. Поэтому расплавленную сталь (например, при сварке) необходимо защищать от воздействия атмосферы.
Примечание. При обозначении марки стали каждому химическому элементу присвоена буква русского алфавита (указана в скобках около каждого элемента), содержание каждого элемента в процентах с округлением до целых значений указывается после буквы, обозначающей данный элемент (элемент содержащийся в пределах 1 %, цифрами не указывается). Поскольку углерод содержится во всех сталях, его обозначение (буква У) не ставится, а количественное содержание указывается в сотых долях процента в начале обозначения марки. Так, 15Г2СФ означает, что в этой стали среднее содержание углерода 0,15 %, марганца - в пределах 1—2 %, кремния и ванадия - в пределах 1 % каждого.
Классификация сталей
По прочностным свойствам стали условно подразделяются на три группы: обычной (sу<29 кН/см2), повышенной (sу = 29...40 кН/см2) и высокой прочности (sy>40 кН/см2).
Повышение прочности стали достигается легированием и термической обработкой.
По химическому составу стали делятся на углеродистые и легированные. Углеродистые стали состоят из железа и углерода с некоторой добавкой кремния (или алюминия) и марганца.
Поскольку большинство добавок в той или иной степени ухудшают свариваемость стали, а также удорожают ее, в строительстве в основном применяют низколегированные стали с суммарным содержанием легирующих добавок не более 5 %.
В зависимости от вида поставки стали подразделяются на:
- горячекатаные;
- термообработанные (нормализованные или термически улучшенные).
В горячекатаном состоянии сталь далеко не всегда обладает оптимальным комплексом свойств. При нормализации измельчается структура стали, повышается ее однородность, увеличивается вязкость, однако существенного повышения прочности не происходит. Термическое улучшение (закалка в воде и высокотемпературный отпуск) позволяют получить стали высокой прочности, хорошо сопротивляющиеся хрупкому разрушению.
По степени раскисления стали могут быть кипящими, полуспокойными, спокойными.
Нераскисленные стали кипят при разливке вследствие выделения газов: такая сталь носит название кипящей и оказывается более засоренной газами и менее однородной.
Кипящие стали, имея достаточно хорошие показатели по пределу текучести и временному сопротивлению, хуже сопротивляются хрупкому разрушению и старению.
Чтобы повысить качество малооуглеродистой стали, ее раскисляют добавками кремния от 0,12 до 0,3 % или алюминия до 0,1 %. Кремний (или алюминий), соединяясь с растворенным кислородом, уменьшает его вредное влияние. Кроме того, при соединении с кислородом раскислители образуют силикаты и алюминаты, которые увеличивают число очагов кристаллизации и способствуют образованию мелкозернистой структуры стали, что ведет к повышению ее качества и механических свойств. Раскисленные стали не кипят при разливке в изложницы, поэтому их называют спокойными. Спокойная сталь более однородна, лучше сваривается, лучше сопротивляется динамическим воздействиям и хрупкому разрушению. Ее применяют при изготовлении ответственных конструкций, подвергающихся статическим и динамическим воздействиям.
Спокойные стали примерно на 12 % дороже кипящих, что несколько ограничивает их применение.
Полуспокойная сталь по качеству является промежуточной между кипящей и спокойной. Ее раскисляют меньшим количеством кремния - 0,05...0,15 % (редко алюминием). По стоимости полуспокойные стали также занимают промежуточное положение. Низколегированные стали поставляют в основном спокойной (редко полуспокойной) модификации.
Нормирование сталей
Основным стандартом, регламентирующим характеристики сталей для строительных металлических конструкций, является ГОСТ 27772 — 88. Согласно ГОСТу фасонный прокат изготовляют из сталей С235, С245, С255, С275, С285, С345, С345К, С375, для листового и универсального проката и гнутых профилей используются также стали С390, С390К, С440, С590, С59ОК. Стали С345, С375, С390 и С440 могут поставляться с повышенным содержанием меди (для повышения коррозионной стойкости), при этом к обозначению стали добавляется буква «Д».
Буква С в наименовании означает сталь строительную, цифра показывает значение предела текучести в МПа, буква К - вариант химического состава.
Прокат поставляют как в горячекатаном, так и в термообработанном состоянии. Выбор варианта химического состава и вида термообработки определяется заводом. Например, листовой прокат стали С345 может изготовляться из стали с химическим составом С245 с термическим улучшением. В этом случае к обозначению стали добавляют букву Т, например С345Т.
В зависимости от температуры эксплуатации конструкций и степени опасности хрупкого разрушения испытания на ударную вязкость для сталей С345 и С375 проводятся при разных температурах, поэтому они поставляются четырех категорий, а к обозначению стали добавляют номер категории, например С345-1, С375-2.
Оценку свариваемости стали проводят по углеродному эквиваленту (%):
,
где С, Mn, Si, Cr, Ni, Си, V и Р - массовая доля углерода, марганца, кремния, хрома, никеля, меди, ванадия и фосфора, %.
Если Сэ<0,4%, то сварка стали не вызывает затруднений, при 0,4 %<СЭ<0,55% сварка возможна, но требует принятия специальных мер по предотвращению возникновения трещины. При Сэ>0,55 % опасность появления трещин резко возрастает.
По ГОСТ 380-88 в обозначении марки стали указывается группа поставки, способ раскисления и категория.
При поставке по группе А завод гарантирует механические свойства, по группе Б – химический состав, по группе В - механические свойства и химический состав.
Степень раскисления обозначается буквами: кп - кипящая; сп - спокойная; пс - полуспокойная.
Категория стали указывает вид испытаний на ударную вязкость:
категория 2 – испытания на ударную вязкость не проводятся;
категория 3 – проводятся при температуре +20 оС;
категория 4 - проводятся при температуре -20 оС;
категория 5 – при температуре -20 оС и после механического старения;
категория 6 - после механического старения.
1.9 Стали обычной прочности (s y < 29 кН/см2)
К этой группе относят малоуглеродистые стали (С235...С285) различной степени раскисления, поставляемые в горячекатаном состоянии. Обладая относительно небольшой прочностью, эти стали очень пластичны: протяженность площадки текучести составляет 2,5 % и более, соотношения s y / s u 0,6...0,7. Хорошая свариваемость обеспечивается низким содержанием углерода (не более 0,22 %) и кремния. Коррозионная стойкость - средняя, поэтому конструкции, выполненные из сталей обычной прочности, следует защищать с помощью лакокрасочных и других покрытий. Однако благодаря невысокой стоимости и хорошим технологическим свойствам стали обычной прочности очень широко применяют для строительных металлических конструкций. Потребление этих сталей составляет свыше 50% от общего объема. Недостатком малоуглеродистых сталей является склонность к хрупкому разрушению при низких температурах (особенно для кипящей стали С235), поэтому их применение в конструкциях, эксплуатирующихся при низких отрицательных температурах, ограничено.
1.10 Стали повышенной прочности (29 кН/см2 ≤ s y < 40 кН/см2)
Стали повышенной прочности (С345...С390) получают либо введением при выплавке стали легирующих добавок (в основном марганца и кремния, реже никеля и хрома), либо термоупрочнением низкоуглеродистой стали (С345Т). Пластичность стали при этом несколько снижается и протяженность площадки текучести уменьшается до 1...1,5%. Например, 15ХСНД.
Стали повышенной прочности хуже свариваются (особенно стали с высоким содержанием кремния) и требуют иногда использования специальных технологических мероприятий для предотвращения образования горячих трещин.
По коррозионной стойкости большинство сталей этой группы близки к малоуглеродистым сталям. Более высокой коррозионной стойкостью обладают стали с повышенным содержанием меди (С345Д, С375Д, С390Д).
Высокое значение ударной вязкости сохраняется при температуре -40°С и ниже, что позволяет использовать эти стали для конструкций, эксплуатируемых в северных районах. За счет более высоких прочностных свойств применение сталей повышенной прочности приводит к экономии металла до 20...25%.
1.11 Стали высокой прочности (s y ≥ 40 кН/см2)
Прокат из стали высокой прочности (С440...С590) получают легированием и термической обработкой. Для легирования используют нитридообразующие элементы, способствующие образованию мелкозернистой структуры.
Стали высокой прочности могут не иметь площадки текучести (при s y ≥ 50 кН/см2), и их пластичность (относительное удлинение) снижается до 14% и ниже. Отношение s y / s u увеличивается до 0,8...0,9, что не позволяет учитывать при расчете конструкций из этих сталей пластические деформации.
Подбирая химический состав и режим термообработки, можно значительно повысить сопротивление хрупкому разрушению и обеспечить высокую ударную вязкость при температурах до - 70°С. Однако высокая прочность и низкая пластичность сталей требуют более мощного оборудования для резки, правки, сверления и других операций.
При сварке термообработанных сталей вследствие неравномерного нагрева и быстрого охлаждения в разных зонах сварного соединения происходят различные структурные превращения. На одних участках образуются закалочные структуры, обладающие повышенной прочностью и хрупкостью (жесткие прослойки), на других металл подвергается высокому отпуску и имеет пониженную прочность и высокую пластичность (мягкие прослойки).
Разупрочнение стали в околошовной зоне может достигать 5...30 %, что необходимо учитывать при проектировании сварных конструкций из термообработанных сталей. Эффект разупрочнения снижает введение в состав стали некоторых карбидообразующих элементов (молибден, ванадий).
Применение сталей высокой прочности приводит к экономии металла до 25...30 % по сравнению с конструкциями из низкоуглеродистых сталей и особенно целесообразно в большепролетных и мощных конструкциях.
Атмосферостойкие стали
Для повышения коррозионной стойкости металлических конструкций применяют низколегированные стали, содержащие в небольшом количестве (доли процента) такие элементы, как хром, никель и медь.
В конструкциях, подвергающихся атмосферным воздействиям, весьма эффективны стали с добавкой фосфора (например, сталь С345К). На поверхности таких сталей образуется тонкая оксидная пленка, обладающая достаточной прочностью и защищающая металл от развития коррозии. Однако свариваемость стали при наличии фосфора ухудшается. Кроме того, в прокате больших толщин металл обладает пониженной хладостойкостью, поэтому применение стали С345К рекомендуют при толщинах не более 10 мм.
В конструкциях, совмещающих несущие и ограждающие функции (например, мембранные покрытия), широко используют тонколистовой прокат. Для повышения долговечности таких конструкций целесообразно применение нержавеющей хромистой стали марки ОХ18Т1Ф2, не содержащей никеля. В больших толщинах прокат из хромистых сталей обладает повышенной хрупкостью, однако свойства тонколистового проката (особенно толщиной до 2 мм) позволяют применять его в конструкции при расчетных температурах до -40°С.
1.13 Выбор сталей для строительных конструкций
Выбор стали зависит от следующих факторов, влияющих на работу материала:
- температуры среды, в которой монтируется и эксплуатируется конструкция; этот фактор учитывает повышенную опасность хрупкого разрушения при пониженных температурах;
- характера нагружения, определяющего особенность работы материала и конструкций при динамической, вибрационной и переменной нагрузках;
- вида напряженного состояния (одноосное сжатие или растяжение, плоское или объемное напряженное состояние) и уровня возникающих напряжений (сильно или слабо нагруженные элементы);
- способа соединения элементов, определяющего уровень собственных напряжений, степень концентрации напряжений и свойства материала в зоне соединения;
- толщины проката, применяемого в элементах. Этот фактор учитывает изменение свойств стали с увеличением толщины.
При выборе стали необходимо учитывать группу конструкций.
К первой группе относят сварные конструкции, работающие в особо тяжелых условиях или подвергающиеся непосредственному воздействию динамических, вибрационных или подвижных нагрузок (например, подкрановые балки, балки рабочих площадок или элементы эстакад, непосредственно воспринимающих нагрузку от подвижных составов, фасонки ферм и т.д.). Напряженное состояние таких конструкций характеризуется высоким уровнем и большой частотой нагружения.
Конструкции первой группы работают в наиболее сложных условиях, способствующих возможности их хрупкого или усталостного разрушения, поэтому к свойствам сталей для этих конструкций предъявляются наиболее высокие требования.
Ко второй группе относят сварные конструкции, работающие на статическую нагрузку при воздействии одноосного и однозначного двухосного поля растягивающих напряжений (например, фермы, ригели рам, балки перекрытий и другие растянутые, растянуто-изгибаемые и изгибаемые элементы), а также конструкции второй группы при отсутствии сварных соединений.
Общим для конструкций этой группы является повышенная опасность хрупкого разрушения, связанная с наличием поля растягивающих напряжений. Вероятность усталостного разрушения здесь меньше, чем для конструкций первой группы.
К третьей группе относят сварные конструкции, работающие при преимущественном воздействии сжимающих напряжений (например, колонны, стойки, опоры под оборудование и другие сжатые и сжато-изгибаемые элементы), а также конструкции второй группы при отсутствии сварных соединений.
В четвертую группу включены вспомогательные конструкции и элементы (связи, элементы фахверка, лестницы, ограждения и т.п.), а также конструкции третьей группы при отсутствии сварных соединений.
Если для конструкций третьей и четвертой групп достаточно ограничиться требованиями к прочности при статических нагрузках, то для конструкций первой и второй групп важным является оценка сопротивления стали динамическим воздействиям и хрупкому разрушению.
В материалах для сварных конструкций обязательно следует оценивать свариваемость. Требования к элементам конструкций, не имеющим сварных соединений, могут быть снижены, так как отсутствие полей сварочных напряжений, более низкая концентрация напряжений и другие факторы улучшают их работу.
В пределах каждой группы конструкций в зависимости от температуры эксплуатации к сталям предъявляют требования по ударной вязкости при различных температурах.
В СНиП II-23-81 содержится перечень марок сталей в зависимости от группы конструкций и климатического района строительства.
Алюминиевые сплавы
Алюминий по своим свойствам существенно отличается от стали. Его плотность r = 2,7 т/м3, т.е. почти в 3 раза меньше плотности стали. Модуль продольной упругости алюминия E=71 000 МПа, модуль сдвига G = 27000 МПа, что примерно в 3 раза меньше, чем модуль продольной упругости и модуль сдвига стали.
Алюминий не имеет площадки текучести. Прямая упругих деформаций непосредственно переходит в кривую упругопластических деформаций (рис. 1.3). Алюминий очень пластичен: удлинение при разрыве достигает 40 — 50%, но прочность его весьма низкая: s = 6...7 кН/см2, а условный предел текучести s02 = 2...3 кН/см2. Чистый алюминий быстро покрывается прочной оксидной пленкой, препятствующей дальнейшему развитию коррозии.
Рис. 1.3 - Характеристики алюминиевых сплавов:
а — диаграммы растяжения; 1 — чистый алюминий; 2— сплав 1915; 3 — сплав 1915Т1; 4— сталь С245; б— зависимости временного сопротивления (1) и условного предела текучести (2) от температуры
Вследствие весьма низкой прочности технически чистый алюминий в строительных конструкциях применяется довольно редко. Значительное увеличение прочности алюминия достигается путем легирования его магнием, марганцем, медью, кремнием, цинком и некоторыми другими элементами.
Временное сопротивление легированного алюминия (алюминиевых сплавов) в зависимости от состава легирующих добавок в 2 — 5 раз выше, чем технически чистого; однако относительное удлинение при этом соответственно в 2 — 3 раза ниже. С повышением температуры прочность алюминия снижается и при температуре свыше 300 °С близка к нулю.
Из большого числа марок алюминия к применению в строительстве рекомендуются следующие:
n термически неупрочняемые сплавы: АД1 и АМцМ; АМг2М и АМг2МН2 (листы); АМг2М (трубы);
n термически упрочняемые сплавы: АД31Т1; АД31Т4 и АД31Т5 (профили);
n 1915 и 1915Т; 1925 и 1925Т; 1935, 1935Т, АД31Т (профили и трубы).
Все указанные выше сплавы, за исключением сплава 1925Т, который используется только для клепаных конструкций, хорошо свариваются.
1.15 Влияние различных факторов на свойства стали. Старение
Под старением понимают изменение свойств низкоуглеродистой стали без заметного изменения ее микроструктуры. При старении увеличиваются предел текучести временное сопротивление и уменьшается пластичность.
Старению способствуют:
механические воздействия и особенно развитие пластических деформаций (механическое старение);
температурные колебания, приводящие к изменению растворимости и скорости диффузии компонентов (физико-химическое старение).
Деформационное старение происходит в сталях, подвергавшихся холодной деформации (холодная гибка, правка и т.п.). Процесс развивается в течение 15... 16 суток при 20 °С и за несколько минут при 200...350 °С.
Наиболее подвержены старению стали, загрязненные и насыщенные газами, например, кипящая сталь.
Старение малоуглеродистых мостовых и строительных сталей может стать причиной разрушения конструкций, особенно при низких температурах. Чтобы уменьшить склонность стали к старению, при выплавке применяют дегазацию и модифицирование алюминием, титаном и ванадием, которые связывают азот и нитриды.
1.16 Влияние различных факторов на свойства стали. Наклеп
Повторные загружения в пределах упругих деформаций (до предела упругости) не изменяют вида диаграммы работы стали, нагружение и разгрузка будут происходить по одной линии.
Если образец загрузить до пластического состояния и затем снять нагрузку, то появится остаточная деформация e. При повторном нагружении образца после некоторого «отдыха» материал работает упруго до уровня предыдущего загружения. Повышение упругой работы материала в результате предшествующей пластической деформации называется наклепом. При наклепе искажается атомная решетка и увеличивается плотность дислокаций. Пластичность стали снижается, повышается опасность хрупкого разрушения, что неблагоприятно сказывается на работе строительных конструкций.
Наклеп возникает в процессе изготовления конструкций при холодной гибке элементов, пробивке отверстий, резке ножницами.
Повышение прочности благодаря наклепу используется в алюминиевых сплавах и арматуре железобетонных конструкций; в стальных конструкциях оно не используется, поскольку наклепанная сталь становится более жесткой, ее пластичность снижается, повышается опасность хрупкого разрушения.
1.17 Влияние температуры. Механические свойства стали при нагревании ее до температуры 200 —250 °С практически не меняются.
При температуре 250 —300 °С прочность стали несколько повышается, пластичность снижается. Сталь в изломе имеет крупнозернистое строение и становится более хрупкой (синеломкость). Не следует при этой температуре деформировать сталь или подвергать ее ударным воздействиям.
Нагревание выше температуры 400 °С приводит к резкому падению предела текучести и временного сопротивления, а при температуре 600 — 650 °С наступает температурная пластичность и сталь теряет свою несущую способность.
Наиболее склонны к хрупкому разрушению кипящие стали. Порог хладноломкости стали С235 (Ст3кп) лежит в интервале от 0 до -10 °С; для спокойной стали С255 (Ст3сп) переход в хрупкое состояние происходит при температуре -20...-30°С. Низколегированные стали имеют порог хладноломкости -40 °С и ниже.
При увеличении толщины проката порог хладноломкости смещается в область более высоких температур.
С изменением температуры меняется также вид поверхности излома. Бархатистая (волокнистая) часть излома свидетельствует о вязком разрушении, фасеточная часть — о хрупком. Чем больше бархатистая часть в изломе, тем лучше сталь сопротивляется хрупкому разрушению.
1.18 Работа стали под нагрузкой: работа стали при одноосном растяжении
Работу стали при одноосном напряжении рассмотрим на примере испытания образца на растяжение (рис. 1.11).
В первой стадии до предела пропорциональности s р связь между напряжениями и деформациями подчиняется закону Гука - это стадия упругой работы. Деформации происходят за счет упруговозвратных искажений кристаллической решетки и исчезают после снятия нагрузки.
При дальнейшем увеличении нагрузки появляются отдельные сдвиги в зернах феррита, дислокации начинают скапливаться около границ зерен: пропорциональность между напряжениями и деформациями нарушается (участок упругопластической работы между s р и s y. В упругой стадии модуль деформации Е имеет постоянное значение (для стали Е = 2,06 • 104 кН/см2). В упругопластической стадии модуль деформации переменный. Последующее увеличение напряжений приводит к интенсивному движению дислокации и увеличению их плотности, развитию линий сдвига в зернах феррита; деформации растут при постоянной нагрузке. На диаграмме появляется площадка текучести.
1- сталь обычной прочности; 2 - сталь повышенной прочности; 3 - сталь высокой прочности
Рис. 1.11 - Диаграмма растяжения стали
Протяженность площадки текучести низкоуглеродистых и некоторых низколегированных сталей составляет 1,5...2,5 %.
Деформации идут в результате упругого деформирования и пластических необратимых сдвигов. При снятии нагрузки упругая часть деформации исчезает (линия разгрузки идет параллельно упругой части линии нагрузки), а необратимая остается, приводя к остаточным деформациям. Дальнейшее развитие деформации сдерживается у границ зерен. Линии сдвига искривляются, движение дислокации затрудняется, и рост деформаций возможен только при увеличении нагрузки (стадия самоупрочнения). В этой стадии материал работает как упругопластический.
При напряжениях, близких к временному сопротивлению (s u), продольные и поперечные деформации локализуются в наиболее слабом месте и в образце образуется шейка. Площадь сечения в шейке интенсивно уменьшается, что приводит к повышению напряжений в месте сужения, поэтому, несмотря на снижение нагрузки на образец, в месте образования шейки нарушаются силы межатомного сцепления и происходит разрыв.
На диаграмме (рис. 1.11) напряжения получены путем деления нагрузки на первоначальную площадь сечения. Истинная диаграмма растяжения (при напряжениях с учетом уменьшения площади сечения) не имеет нисходящей части.
Площадка текучести свойственна сталям с содержанием углерода 0,1...0,3 %. При меньшем содержании углерода получается недостаточно зерен перлита для сдерживания сдвигов по зернам феррита, при большем содержании углерода – зерен перлита получается так мало, что они не дают возможности развиваться по ним сдвигам.
Высокопрочные стали не имеют площадки текучести (рис. 1.11). Условный предел текучести для таких сталей устанавливают по остаточному удлинению, равному 0,2 %.
Важными показателями сталей являются также отношения предела текучести к временному сопротивлению и предела пропорциональности к пределу текучести.
Отношение s y / s u характеризует резерв прочности стали, поскольку рабочие напряжения в элементах металлических конструкций обычно не превышают предела текучести. В сталях обычной и повышенной прочности это отношение близко к 0,6, что свидетельствует о достаточно большом запасе работы материала и позволяет использовать в широких пределах пластические свойства стали. Для высокопрочных сталей предел текучести близок к временному сопротивлению s o 2 / s u = 0,8...0,9, что ограничивает использование работы материала в упругопластической стадии.
Отношение (s p / s u) характеризует сопротивление малым пластическим деформациям. Если на общих перемещениях конструкций пониженное значение предела пропорциональности сказывается слабо, то на устойчивость сжатых элементов этот показатель оказывает большое влияние. У большинства сталей s p / s uсоставляет 0,8...0,85. Однако для термообработанных сталей при низкой температуре отпуска (ниже 600°С) сопротивление малым пластическим деформациям падает и s p / s uможет понизиться до 0,5. Это следует учитывать при проверке устойчивости конструкций из таких сталей.
Унификация диаграмм работы стали
Диаграммы работы разных сталей при растяжении существенно различаются (рис. 1.12, а) по значениям параметров. Если же построить эти диаграммы в относительных координатах s / s o 2 и e / e o 2 , где s o 2 и e o 2 - соответственно предел текучести и относительные деформации в начале площадки текучести, то различия будут достаточно малы (рис. 1.12, б), что позволяет использовать такую диаграмму как унифицированную.
Рис. 1.12 - Унификация диаграмм работы стали
В целях упрощения расчетных предпосылок при работе конструкций в упругопластической области диаграмму работы стали без большой погрешности с некоторым запасом можно заменить идеализированной диаграммой упругопластического тела. При описании работы сталей с выраженной площадкой текучести используют диаграмму Прандтля (рис. 1.13, а), рассматривая материал совершенно упругим до предела текучести и совершенно пластичным после него. При отсутствии площадки текучести можно использовать диаграмму с линейным упрочнением (рис. 1.13, б). В этом случае до предела текучести сталь работает с начальным модулем упругости Е = tg a, а при напряжениях s > sy - с модулем Е1 = tg j.
а - Прандтля; б - с линейным упрочнением; в - криволинейная
Рис. 1.13 - Идеализированные диаграммы работы стали
При сжатии (имеется в виду сжатие коротких образцов, которые не могут потерять устойчивость) сталь ведет себя так же, как и при растяжении, т.е. предел пропорциональности, предел текучести и модуль упругости совпадают. Однако разрушить при сжатии короткие образцы, изготовленные из пластичной стали, и определить временное сопротивление лабораторным путем невозможно, поскольку образец сжимается и в результате расплющивается. Повышенная несущая способность при сжатии коротких образцов в области самоупрочнения учитывают при работе стали на смятие.
1.20 Коррозия и методы борьбы с ней
Коррозия– это разрушение поверхности металла вследствие химического, электрохимического и биохимического воздействий окружающей среды. Различают следующие виды коррозии: почвенная, структурная, электрокоррозия, контактная, щелевая, под напряжением, при трении, коррозионная кавитация, биокоррозия.
Строительные стальные конструкции подвержены главным образом электрохимической, атмосферной коррозии, которая определяется электрохимическими процессами на поверхности стали в присутствии влаги.
Для определения долговечности строительных конструкций важно знать не только скорость протекания, но и характер коррозионных разрушений. Коррозионное разрушение может иметь сплошной (общий) характер или сосредоточиваться на отдельных участках (местная коррозия). Сплошная коррозия распространяется по всей поверхности металла либо с одинаковой (равномерной коррозией) или неодинаковой (неравномерной коррозией) скоростью на различных участках.
Местная коррозия может быть: пятнами, язвами, точечная, питтинговая - разрушение может быть весьма глубоким и даже перейти в сквозное; подповерхностная - разрушение начинается с поверхности, но в дальнейшем распространяется преимущественно под поверхностью металла; избирательная - разрушение отдельных структурных составляющих или одного из компонентов стали; межкристаллитная - разрушение происходит по границам зерен; внутрикристаллитная - разрушение распространяется в глубь металла по телу зерен. Общая сплошная коррозия приводит к ослаблению сечения элемента конструкции и повышению уровня напряжений. Местная коррозия помимо ослабления сечения вызывает концентрацию напряжений, что повышает вероятность хрупкого разрушения стали. Поэтому местные коррозионные повреждения представляют особую опасность, особенно для конструкций, эксплуатируемых при пониженных температурах.
Кроме агрессивности эксплуатационной среды скорость коррозии зависит от химического состава стали. По коррозионной стойкости строительные стали можно разделить на три группы: 1) марганцовистые стали и сталь 14ГСМФР; 2) все стали, кроме входящих в первую и третью группы; 3) медистые и атмосферостойкие стали.
Стали 09Г2, 14Г2 и 14ГСМФР, входящие в первую группу, имеют пониженную коррозионную стойкость, их не следует применять в сильно - и среднеагрессивных средах.
Стали 09Г2С, 10Г2С1, 15Г2СФ по коррозионной стойкости аналогичны низкоуглеродистой стали.
Медистые стали (10ХСНД, 15ХСНД, 10ХНДП) имеют повышенную коррозионную стойкость и корродируют почти в 1,5 раза медленнее низкоуглеродистой стали. Атмосферостойкая сталь (10ХНДП) может быть применена без антикоррозионной защиты для открытых конструкций, расположенных в сухой климатической зоне.
При положительных температурах коррозионный износ практически не влияет на механические свойства стали. Снижение прочности корродирующих конструкций происходит за счет потери толщины сечений.
Более интенсивно снижаются прочностные характеристики строительных сталей из-за коррозии при отрицательных температурах. При - 60° С для стали 09Г2С снижение предела текучести достигает 15...20 %.
Местные коррозионные повреждения являются концентраторами напряжений и снижают ударную вязкость (рис. 2.2.3).
____ эталонные образцы; ------- образцы после 12 месяцев коррозии
Рис. 2.2.3. Зависимость ударной вязкости от температуры
для сталей 09Г2 и Ст3сп5
Обеспечение долговечной эксплуатации стальных конструкций возможно только при надежной защите их от разрушающего воздействия агрессивных сред. Способы защиты конструкций от коррозии можно разделить на три группы: воздействия на металл, воздействия на среду, комбинированные.
Для строительных конструкций широкое распространение получили методы нанесения защитных покрытий. В настоящее время из всех видов покрытий наиболее распространенными, доступными и достаточно эффективными являются лакокрасочные. Для защиты строительных конструкций от коррозии рекомендуют более 70 различных марок лакокрасочных материалов.
Выбор состава покрытий является технико-экономической задачей, при решении которой учитываются стоимость защитного покрытия, его долговечность, трудоемкость нанесения и другие факторы. Долговечность защитного покрытия в условиях производственной среды устанавливают обычно из опыта эксплуатации покрытий в аналогичных средах или экспериментальным путем.
Защитные свойства покрытия определяются тремя факторами: механическими и химическими свойствами пленки покрытия, сцеплением пленки с защищаемой поверхностью и коррозионной стойкостью конструкционного материала. Покрытие должно состоять из шпатлевки, грунтовки и покрывных слоев. Грунтовка предназначена для обеспечения прочного сцепления (адгезии) лакокрасочной пленки с поверхностью металла. Адгезия зависит от качества подготовки поверхности элементов под окраску.
По типу пленкообразователя лакокрасочные покрытия подразделяют на:
1. Лаки и краски на основе битумов, лаков и смол (БТ), например краска БТ-177, битумно-масляный лак БТ-783. Применяются для закрытых конструкций в слабоагрессивных средах при повышенной влажности.
2. Перхлорвиниловые лаки и эмали (ХВ), например эмали ХВ -1100, ХВ-124, грунтовка ХВ-050, лак ХС-724. Рекомендуются для средне- и сильноагрессивных сред при повышенных требованиях к водостойкости, а также стойкости против растворов кислот, щелочей.
3. Эпоксидные эмали (ЭП), например эмали ЭП-733 и ЭП-575, грунтовка ЭП-0200, шпатлевка ЭП-ЭП10 и др. Применяются для слабо- и среднеагрессивных сред.
4. Кремнийорганические эмали (КО), например эмаль КО-811 (наносится без грунтовки), краска КО-042 и др. Рекомендуются для открытых конструкций, эксплуатируемых в среднеагрессивной среде.
5. Масляные краски (МА), например, масляная черная МА-011, белила цинковые МА-012, железный сурик на олифе-оксоль. Могут быть применены для защиты конструкций в закрытых помещениях при слабоагрессивных средах. Не рекомендуются для производственных сельскохозяйственных зданий.
6. Глифталевые покрытия (ГФ). Грунтовки ГФ-021, ГФ-017 и другие применимы почти для всех видов покрытий. Грунтовка ГФ-017 рекомендуется для конструкций, монтируемых или эксплуатируемых при расчетной температуре -40 0С.
Дата добавления: 2018-11-24; просмотров: 601; Мы поможем в написании вашей работы! |
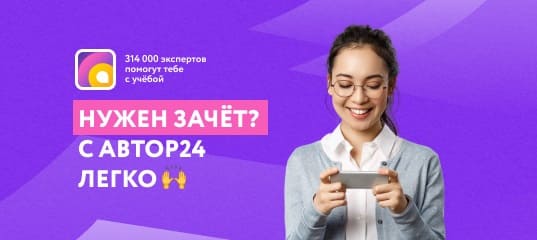
Мы поможем в написании ваших работ!