Общая технологическая схема производства бумаги и картона
Производство бумаги складывается из 5-ти основных технологических процессов:
1. Получение исходных волокнистых компонентов: разволакнивание исходных материалов, освобождение их от вредных примесей.
2. Изготовление бумажной массы: массный размол, смешение компонентов.
3. Отливка бумажного полотна на бумагоделательных машинах.
4. Отделка листового материала: выравнивание, лощение, тиснение.
5. Резка, сортировка, упаковка продукции.
Каждая операция вносит в полуфабрикат характерные признаки, которые в конечном счете создают совокупность признаков, общую лишь для какого-то определенного количества готовой продукции.
Основным компонентом бумаги являются волокнистые материалы (полуфабрикаты - целлюлоза, полуцеллюлоза, древесная масса), вырабатываемые из древесины хвойных и лиственных пород, из соломы различных злаков, стеблей однолетних растений, лубяных волокон льна, конопли, джута, рами, волокон хлопка, тряпичной массы и макулатуры.
Химически необработанная древесная масса применяется лишь при изготовлении бумаги низких сортов, к которым не предъявляется требование долговечности.
Для промышленного производства писчей бумаги различных видов в настоящее время применяется главным образом беленая и небеленая древесная целлюлоза, (основу которой составляют оболочки клеток растений), полученная одним из способов варки - сульфитным (кислотным) или сульфатным (щелочным). Соответственно способу получения целлюлоза носит название сульфитной или сульфатной.
|
|
На первом этапе технологического процесса получения бумаги выделяется один компонент - волокна целлюлозы. Для этого сырье мелко измельчают, смешивают с водой и подвергают термической обработке - варке.
В процессе вываривания первичного сырья чистая целлюлоза освобождается в той или иной степени от входящих в древесно-растительную массу так называемых инкрустирующих веществ: лигнина, смолы, гемицеллюлозы и других веществ.
Для придания полуфабрикату белого цвета и более глубокой очистки волокон проводится отбелка целлюлозы. Для отбелки используются: хлор, хлорная известь, гипохлорид кальция, перекись водорода и др.
На втором этапе технологического процесса изготовления бумаги волокна целлюлозы подвергаются массному размолу (дефибрилляции). Процесс массного размола способствует лучшему формированию листа бумаги. Благодаря ему из одних и тех же волокон можно изготовить бумагу с разными свойствами. По степени разработанности различают три вида помола: тощий (волокна измельчаются и укорачиваются главным образом в длину, при этом структура волокна остается без изменений); жирный (большая часть волокна расщепляется на элементарные волокна - фибриллы); очень жирный помол (все волокна расщепляются на фибриллы). Различного вида помолы характеризуются еще по длине входящих в их состав волокон (длинный, средний, короткий).
|
|
Массу с тощим помолом волокна используют при производстве газетных, фильтровальных бумаг, а с жирным и очень жирным - при производстве прочных, плотных бумаг.
Для получения бумажной массы измельченные волокнистые компоненты сильно разбавляют водой; в зависимости от вида (сорта) изготавливаемой бумаги в полученную таким образом взвесь вводят наполнители, проклеивающие вещества, отбеливающие и красящие вещества.
Третьим технологическим этапом является отлив бумажного волокна, который осуществляется на бумагоделательных машинах (БДМ).
Бумажная масса из специального дозирующего устройства поступает на движущуюся в виде транспортерной ленты металлическую или полимерную сетку, натянутую на ряд валов. Волокна бумажной массы, двигаясь вместе с сеткой, которой дополнительно придается боковая тряска, спутываются, обезвоживаются и принимают вид бумажного полотна. Сетчатая часть БДМ заканчивается прессующими обрезиненными валами, на которых бумажное полотно уплотняется. Далее специальными сукнами оно подается в прессовальную часть машины, представляющую собой несколько валов, которые уплотняют и обезвоживают бумагу. Окончательно бумажное полотно обезвоживается в сушильной секции БДМ, состоящей из системы обогреваемых цилиндров, где оно высушивается до влажности 6-8 %.
|
|
В отделочной части БДМ бумага проходит между вращающимися металлическими полированными валами, которые сглаживают ее поверхность, придавая ей матовый вид - машинную гладкость. У такой бумаги гладкость нижней стороны (имеющей следы рисунка от нитей сетки) будет меньше верхней (лицевой) стороны.
На данном технологическом этапе при производстве бумаги, предназначенной для особо важных документов, осуществляется введение в ее толщу синтетической нити и нанесение водяных знаков.
На четвертом этапе технологического процесса получения бумаги для улучшения гладкости и дальнейшего уплотнения некоторые сорта бумаги каландрируются, т.е. бумажное полотно пропускается через суперкаландр. Бумага, подвергнутая такой обработке, называется каландрированной, лощенной или глазированной.
Иногда бумаге придают односторонний лоск, а в некоторых случаях подвергают тиснению.
На пятом этапе производства бумаги бумажное полотно разрезается вдоль на менее широкие части. Для этого оно разматывается и пропускается через роликовые ножи. Полученные бумажные полосы сматывают в бухты, которые отправляют потребителям. На этом этапе на бумагу может быть нанесено пленочное покрытие, либо ее поверхность может быть обработана иным способом.
.
Дата добавления: 2018-11-24; просмотров: 3574; Мы поможем в написании вашей работы! |
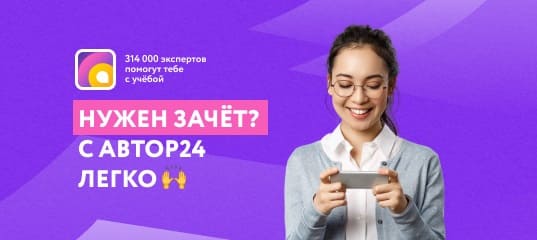
Мы поможем в написании ваших работ!