Режимы склеивания заготовок и деталей
Параметр | Нормы склеивания для клея | ||
КФ-МХ | КФК-20 | КФ-ЖМ | |
Массовая доля сухого остатка, % | Не менее 70 | 65 ± 2 | 67 ± 2 |
Вязкость клея при 20°С, – ВЗ-4 – ВЗ-1 (диаметр сопла 5,4 мм) | - 50–100 | 90–300 - | - 40–60 |
Жизнеспособность клея при 20±1°С,ч | 2–8 | 0,5–4 | 10 |
Расход клея, г/м2 | 140–160 | 130–150 | 150–170 |
Давление прессования, МПа | 0,5–0,8 | 0,5–0,8 | 0,5–0,6 |
Температура отверждения клея, °С | 18–22 | 120–130 | 18–20 |
Время прессования, ч | 2–3 | 60–90 с на 1 мм толщины заготовки | 1,5–2 |
Технологическая выдержка после склеивания, ч, не менее | 4 | 2 | 2 |
Режимы склеивания отдельных клеев на основе ПВА дисперсий представлены в табл. 2.3.
Таблица 2.3
Режимы склеивания
Параметр | Нормы склеивания для клея | ||||||
Клебит 303.0 | Rakoll Duplit AL | Bindan-F | Иваколь 102.70 | Cascol 3339 | |||
1. Основа | ПВА дисперсия | ПВА дисперсия | Синтетический клей | ПВА дисперсия | ПВА дисперсия | ||
2. Отвердитель | 5% «турбо» Клебит 303.5 | 5 мас. ч. Rakoll Duplit | – | 5% Иоват 195. 40 | – | ||
3. Жизнеспособность при 20°С: – без отвердителя | Неогранич. | Неогранич. | 12 месяцев | Неогранич. | 6 месяцев | ||
– с отвердителем | 24 ч | 5 ч | – | 5 ч | – | ||
4. Нанесение клея | Одностороннее или двустороннее | Одностороннее или двустороннее | Двустороннее | Одностороннее или двустороннее | Одностороннее | ||
5. Расход клея, г/м2 | 120–200 | 180–200 | 130–170 | 150–200 | 60–200 | ||
6. Время открытой выдержки, мин | 6–10 | 9–11 | 10–14
| 5–8 | max 4 | ||
7. Время закрытой выдержки, мин | – | – | – | max 7 | |||
8. Давление прессования, Н/мм2 | 0,7–1,0 | 0,1–0,5 | 0,7 | ³ 0,2 | 0,1–1,0 | ||
9. Время прессования, мин при: 20°С 50°С 80°С | 15 5 2 | 15–25 – – | 60 30 10 | 30 4 1,5 | 2–5 2 ³ 2 | ||
10. Класс водостойкости: ―с отвердителем ―без отвердителя | D4 D3 | D4 – | – D3 | D4 D3 | – D3 |
Для склеивания древесины по пластям и кромкам используют прессы и ваймы различных конструкций, производительность которых, компл./ч, можно рассчитать по формуле
![]() | (2.26) |
где n – количество одновременно запрессовываемых деталей, шт.;
tц – время цикла, мин;
z – количество деталей в комплекте, шт.;
Кд, – коэффициенты использования рабочего времени (Кд= 0,7–0,85).
tц = tпр+ tво, | (2.27) |
где tпр –продолжительность выдержки под давлением, мин;
tво – продолжительность открытой выдержки и вспомогательных операций, мин (tво =5-15 мин.).
Пример: Рассчитать производительность пресса и количество клея необходимое для склеивания мебельного щита размером 1000×800 мм, толщиной 20, мм клеем Клебит 303.0 в прессе с рабочим промежутком 1200×800 мм при температуре 20ºС. Ширина склеиваемых ламелей 50 мм.
Решение . Исходя из размеров мебельного щита и рабочего промежутка пресса, делаем вывод, что количество одновременно запрессовываемых деталей равно 1. Время прессования по табл. 2.5. для клея Клебит 303.0 при температуре 20ºС составляет 20 мин. С учетом времени загрузки и разгрузки пресса время цикла составит 25 мин. Определим производительность пресса:
|
|
компл./ч.
Определим количество поверхностей склеивания k по формуле
k = m – 1, | (2.28) |
где m – количество склеиваемых ламелей,
![]() | (2.29) |
где B и b – ширина склеиваемых ламелей и щита соответственно, мм.
k =16 – 1=15.
Определим количество клея, g, г, необходимое для склеивания мебельного щита:
![]() | (2.30) |
где S – площадь поверхности склеивания, м2;
с – удельный расход клея, г/м2 (табл. 2.4–2.5).
,
Для склеивания заготовок по длине наибольшее распространение получили автоматические и полуавтоматические линии сращивания различных конструкций. В состав таких линий входят один или два шипорезных узла и пресс проходного или позиционного типа. За производительность линии сращивания принимается производительность менее производительного узла. Производительность шипорезного узла, компл./ч, можно рассчитать по формуле
![]() | (2.31) |
где U – скорость подачи, м/мин;
|
|
n – количество заготовок в одной закладке, шт.;
lср – средняя длина сращиваемых заготовок, м;
h – длина хода каретки, м (h =1,5м);
∑ lкомпл – суммарная длина ламелей, входящих в комплект, м;
m – количество проходов через станок, шт.;
Кд, Км – коэффициенты использования рабочего и машинного времени соответственно(Кд=0,8–0,9; Км=0,55–0,60).
Количество заготовок в одной закладке можно определить по формуле:
для горизонтального шипа
![]() | (2.32) |
для вертикального шипа
![]() | (2.33) |
где B – ширина закладки шипорезного узла, м;
b и s – ширина и толщина сращиваемых заготовок соответственно, м.
Полученные значения n округляют до ближайшего меньшего значения.
Производительность пресса, компл./ч, можно рассчитать по формуле:
![]() | (2.34) |
где N – число тактов работы пресса в минуту;
L – рабочая длина пресса, м;
∑ lкомпл – суммарная длина ламелей, входящих в комплект, м;
Кд, – коэффициенты использования рабочего времени (Кд = 0,7–0,85).
Пример. Рассчитать производительность линии сращивания по длине, компл./ч, при производстве филенки двери с черновыми размерами 800×624 мм, если в состав комплекта входят 3 такие филенки. Линия сращивания состоит из одного шипорезного узла с шириной закладки 400 мм и пресса с рабочей длиной 6 м. Соединение по длине осуществляется на горизонтальный шип. Средняя длина сращиваемых заготовок составляет 300 мм, скорость подачи шипорезного узла 10 м/мин, число тактов пресса в минуту 3.
|
|
Решение . Исходя из рекомендуемой ширины ламелей для склеивания мебельного щита (b = 40–60 мм) принимаем, что одна филенка состоит из 12 ламелей шириной 52 мм и длиной 800 мм. Определим суммарную длину ламелей, входящих в комплект:
.
Определим количество заготовок в одной закладке шипорезного узла. Для горизонтального шипа
Принимаем ближайшее меньшее целое значение n = 7 шт.
Для условий задачи число проходов через станок m = 2.
Рассчитаем производительность шипорезного узла:
компл./ч.
Рассчитаем производительность пресса:
компл./ч.
Таким образом, менее производительным является шипорезный узел и его производительность определит производительность линии в целом 7 компл./ч.
Повторная механическая обработка чистовых заготовок включает нарезку шипов и проушин, фрезерование, сверление отверстий, выборку пазов и шлифование.
Сверление отверстий в пластях и кромках заготовок производится на сверлильно-присадочных станках СГВП-1, СГВП-2.
При небольшом количестве отверстий в пласти мебельного щита (например, в дверках шкафов), а также в случаях, когда не все отверстия могут быть просверлены на присадочном станке, применяют одношпиндельные сверлильно-пазовальные (СВП-2, СВА-2), фрезерно-копировальные станки (ВФК-1, ВФК-2), а также нестандартное оборудование. Указанные станки применяют также для фрезерования пазов в щитовых заготовках.
Часовую производительность, компл./ч, сверлильно-пазовальных станков определяют по следующим формулам:
для одношпиндельных
![]() | (2.35) |
где Кд– коэффициенты использования рабочего времени (k д =0,7–0,85);
Км – коэффициент учитывающий время укладки, базирования и перемещения заготовок (для станков с ручной подачей Км =0,15–0,2, для станков с механической подачей Км =0,55–0,65)
z – количество фрезеруемых пазов (отверстий) в заготовке;
tц – машинное время обработки (для фрезерования одного паза, tц = 0,3–1,0 мин; для сверления одного отверстия tц = 0,15–0,2 мин).
для многошпиндельных (СГВП-1А, Rover, Wekke и т. п.)
![]() | (2.36) |
где z – количество обрабатываемых деталей комплекта.
Кд, – коэффициенты использования рабочего времени (Кд=0,7–0,85);
Шлифование. Производительность шлифовальных станков при шлифовании щитовых заготовок на шлифовальных станках 2ШлК или ШлПС9(10), Butfering и т. п. определяют по следующей формуле
![]() | (2.37) |
где U – скорость подачи, м/мин;
L – длина шлифуемых деталей, м;
m – количество проходов через станок, шт.;
n – количество шлифуемых сторон, шт.;
f – количество одновременно шлифуемых деталей, шт.;
Кд, Км – коэффициенты использования рабочего и машинного времени соответственно(Кд = 0,8–0,9; Км = 0,90–0,95).
Центр для домостроения. Производит операции зарезка чашек, сверление отверстий и др. Центры, в зависимости от модели могут производить операции последовательно разными модулями, причем эти модули стоят постоянно, либо производится обработка агрегатами, аналог многооперационного центра с ЧПУ.
Производительность такого центра определяется следующим образом. Отдельно рассчитываются производительности каждой операции, определяется норма времени на выполнение каждой операции. Затем время суммируется, а обратная величина – есть производительность центра.
Пример. Рассчитать производительность центра для домостроения BigLOG260A, если на одном брусе необходимо сделать 2 чашки, просверлить два отверстия и на двух брусьях сделать одно торцовое примыкание. Длина бруса 6 метров.
Технические данные для BigLOG260A (данные производителя):
– время выполнения операции для сечения 230 х 230 мм:
- угловое соединение: 20 - 25 с
- сверление: 6 - 10 с
- торцевание: 8 - 10 с
- соединение «ласточкин хвост» паз: 20 - 25 с
- соединение «ласточкин хвост» гребень: 20 - 40 с (зависит от качества)
- пазование: 8 - 10 с
- манипуляции с обрабатываемым материалом: дополнительно 1 с на 1 м.п. бревна
Решение. Расчет будем вести для двух брусьев.
Производительность по зарезанию чашек:
[чашек/мин],
где z – количество чашек в двух брусьях.
Кд, – коэффициенты использования рабочего времени (Кд=0,7–0,85);
чашек/мин
Производительность по сверлению отверстий:
[отверстий/мин],
где z – количество отверстий в двух брусьях.
Кд, – коэффициенты использования рабочего времени (Кд=0,7–0,85);
отверстий/мин
Производительность по зарезанию примыканий:
[примыканий/мин],
где z – количество обрабатываемых деталей примыкания.
Кд, – коэффициенты использования рабочего времени (Кд=0,7–0,85);
примыкания/мин
Таким образом, норма времени по каждой операции:
,
,
мин,
мин,
мин.
Норма времени на выполнение всех операций, в том числе перемещения:
Н=Нч+Нсв+Нпр+Нпер
Н=1,96+0,63+0,98+12∙1/60=3,77 мин
Тогда производительность центра будет:
П=1/Н=1/3,77=0,265 двойных брусьев в минуту. В переводе на один брус – П=0,265∙2=0,53 бруса в минуту.
3. КОНТРОЛЬНЫЕ ЗАДАНИЯ
Вариант выбирается по двум последним цифрам зачетной книжки в соответствии с табл. 3.1. При этом в числителе указаны номера теоретических вопросов, а в знаменателе – номера практических задач.
Таблица 3.1
Варианты контрольных заданий
Последняя цифра номера зачетной книжки | |||||||||||
Предпоследняя цифра номера зачетной книжки | 1 | 2 | 3 | 4 | 5 | 6 | 7 | 8 | 9 | 0 | |
1 | 27, 85 2, 33 | 5, 53 49, 38 | 22, 74 26, 48 | 2, 52 10, 62 | 1, 88 60, 39 | 5 , 24 1, 29 | 4, 53 51, 47 | 20, 67 48, 61 | 1, 46 15, 72 | 11, 59 52, 86 | |
2 | 7, 94 47, 86 | 8, 81 16, 99 | 16, 67 26, 92 | 10, 61 24, 88 | 17, 73 9, 24 | 3, 60 29, 68 | 14, 90 27, 46 | 45, 92 28, 73 | 4, 76 41, 70 | 38, 91 53, 99 | |
3 | 31, 95 3, 61 | 26, 68 38, 85 | 15, 89 14, 78 | 22, 61 37, 56 | 40, 82 17, 64 | 19, 70 51, 87 | 48, 80 18, 90 | 16, 84 20, 69 | 21, 60 1, 55 | 2, 54 11, 34 | |
4 | 36, 88 23, 89 | 25, 66 16, 100 | 23, 77 22, 63 | 14, 51 42, 62 | 33, 64 8, 91 | 49, 87 36,59 | 27, 75 34, 98 | 6, 58 46, 98 | 41, 51 35, 83 | 37, 89 28, 50 | |
5 | 7, 69 13, 93 | 28, 80 44, 100 | 35, 93 20, 77 | 39, 78 43, 92 | 20, 72 50, 81 | 12, 85 54, 79 | 40, 54 23, 37 | 15, 62 30, 45 | 9, 57 41, 97 | 24, 81 19, 70 | |
6 | 50, 92 4, 94 | 5, 58 7, 70 | 44, 76 44, 76 | 11, 64 30, 89 | 37, 79 27, 77 | 2, 86 33, 75 | 30, 68 12, 31 | 34, 87 32, 64 | 29, 63 25, 66 | 10, 82 74, 84 | |
7 | 50, 74 5, 67 | 19, 79 39, 49 | 42, 59 57, 72 | 17, 67 5, 82 | 41, 83 58, 65 | 42, 95 43, 65 | 25, 73 56, 97 | 13, 66 55, 96 | 44, 77 17, 87 | 33, 83 6, 95 | |
8 | 46, 57 32, 63 | 23, 69 4, 93 | 12, 55 15, 91 | 47, 92 21, 60 | 30, 71 15, 84 | 6, 63 54, 76 | 3, 55 52, 66 | 43, 84 21, 95 | 28, 62 12, 67 | 49, 93 6, 80 | |
9 | 43, 79 11, 96 | 8, 70 8, 58 | 38, 72 18, 71 | 36, 75 45, 57 | 34, 90 3, 83 | 32, 85 53, 74 | 29, 88 36, 94 | 18, 65 7, 90 | 35, 78 35, 68 | 18, 51 13, 85 | |
0 | 45, 56 19, 81 | 39, 91 22, 82 | 47, 65 40, 75 | 32, 86 9, 25 | 46, 95 31, 73 | 48, 94 14, 69 | 13, 56 2, 71 | 9, 64 59, 88 | 31, 93 10, 40 | 26, 71 1, 42 |
Теоретические вопросы
1. Стадии технологического процесса производства изделий из древесины. Характеристика процессов производства изделий из древесины. Виды изделий из древесины, их характеристика.
2. Характеристика основных материалов, применяемых в производстве изделий из древесины.
3. Характеристика вспомогательных материалов, применяемых в производстве изделий из древесины.
4. Характеристика современных конструкционных материалов, применяемых в производстве изделий из древесины.
5. Характеристика современных клеевых материалов, применяемых в производстве изделий из древесины.
6. Основные понятия о производственном и технологическом процессах. Принципы организации производственного процесса.
7. Типы производств и их технологические особенности.
8. Принципы организации труда в основном производстве.
9. Принципы проектирования рабочих мест.
10. Выбор и обоснование расчета производственной программы, необходимого количества технологического оборудования при изготовлении изделий из древесины.
11. Методика расчета производственной программы цеха, участка по производству изделий из древесины. Определение потребного количества оборудования.
12. Методика расчета оптимальных показателей механизации и автоматизации производственных процессов.
13. Основные факторы и взаимосвязи рациональной организации производства и труда.
14. Классификация типов деревообрабатывающего оборудования в производстве изделий из древесины.
15. Основные факторы, определяющие выбор оборудования в производстве изделий из древесины.
16. Основные требования и рекомендации, которые необходимо учитывать при разработке плана расположения оборудования в цехах (участках) по производству изделий из древесины.
17. Основные факторы, определяющие выбор оборудования при производстве изделий из древесины.
18. Основные правила и нормативы по охране труда при проектировании рабочих мест в цехах (участках) по производству изделий из древесины.
19. Классификация загрузочно-разгрузочных и транспортных устройств в цехах по производству изделий из древесины.
20. Основные положения организации труда на транспортных, загрузочно-разгрузочных работах. Направления совершенствования.
21. Раскрой пиломатериалов на заготовки. Припуски. Роль припусков в производстве изделий из древесины. Виды, методы, расчет величины припусков.
22. Раскрой пиломатериалов на заготовки. Цель операции раскроя. Эффективность использования материалов при раскрое. Виды раскроя. Организация процесса, оборудование, производительность.
23. Особенности организации процесса поперечного раскроя пиломатериалов на заготовки. Анализ применяемого оборудования и его производительность.
24. Особенности организации процесса продольного раскроя пиломатериалов на заготовки. Анализ применяемого оборудования, его производительность, организация рабочих мест.
25. Особенности организации раскроя пиломатериалов на заготовки криволинейных деталей. Анализ применяемого оборудования, его производительность, организация рабочих мест.
26. Особенности организации процесса раскроя (виды раскроя) плитных материалов. Какие задачи ставятся для оптимального планирования раскроя? Порядок составления карт раскроя.
27. Особенности организации процесса раскроя плитных и листовых материалов. Анализ применяемого оборудования, его производительность, организация рабочих мест.
28. Особенности организации процесса раскроя листовых и рулонных материалов. Анализ применяемого оборудования, его производительность, организация рабочих мест.
29. Задачи, последовательность и содержание операций первичной механической обработки заготовок. Характеристика технологических баз и правила их выбора.
30. Охарактеризовать организацию процесса первичной механической обработки заготовок. Анализ применяемого оборудования, его производительность, организация рабочих мест.
31. Создание базовых поверхностей. Особенности процесса. Анализ применяемого оборудования, его производительность, организация рабочих мест.
32. Обработка заготовок в размер по сечению. Особенности процесса. Анализ применяемого оборудования, его производительность, организация рабочих мест.
33. Торцевание брусковых заготовок. Особенности процесса. Анализ применяемого оборудования, его производительность, организация рабочих мест.
34. Требования к склеиваемым материалам (конструкционным, облицовочным, клеевым) и их подготовка при изготовлении изделий из древесины. Требования техники безопасности и производственной санитарии на участке.
35. Виды склеивания заготовок из древесины и древесных материалов в производстве изделий из древесины. Теоретические основы склеивания. Режимы склеивания.
36. Интенсификация процесса склеивания заготовок из древесины. Классификация методов интенсификации процесса склеивания.
37. Основные факторы, влияющие на прочность склеивания заготовок из древесины.
38. Основные методы контроля режимов и качества склеивания заготовок из древесины.
39. Основные стадии технологического процесса склеивания заготовок из древесины.
40. Способы нанесения клея. Режимы склеивания заготовок из древесины.
41. Организация технологического процесса склеивания заготовок из древесины по длине. Последовательность и содержание технологических операций. Анализ применяемого оборудования, его производительность, организация рабочих мест на участке склеивания.
42. Выбор и расчет производительности участка склеивания заготовок из древесины по длине.
43. Оптимизация процесса склеивания заготовок по длине. Анализ применяемого оборудования, его производительность, организация рабочих мест на участке. Режимы склеивания.
44. Особенности организации технологического процесса склеивания заготовок из древесины по ширине. Анализ применяемого оборудования, его производительность, организация рабочих мест на участке. Режимы склеивания.
45. Особенности организации технологического процесса склеивания заготовок из древесины по толщине. Анализ применяемого оборудования, его производительность, организация рабочих мест на участке. Режимы склеивания.
46. Классификация и виды оборудования на участке вторичной механической обработки. Состав и последовательность операций. Классификация и анализ применяемого оборудования для обработки чистовых заготовок. Их преимущества и недостатки. Производительность, организация рабочих мест на участке.
47. Формирование шипов и проушин на брусковых заготовках. Схемы формирования шипов и проушин. Анализ применяемого оборудования, его производительность, организация рабочих мест на участке.
48. Технологический процесс изготовления строительного бруса. Анализ применяемого оборудования, его производительность, организация рабочих мест.
49. Технологический процесс изготовления чашек в строительном брусе. Анализ применяемого оборудования, его производительность, организация рабочих мест.
50. Технологический процесс изготовления инженерного паркета. Анализ применяемого оборудования, его производительность, организация рабочих мест.
51. Технологический процесс изготовления доски пола. Анализ применяемого оборудования, его производительность, организация рабочих мест.
52. Формирование гнезд и сверление отверстий. Анализ применяемого оборудования, его производительность, организация рабочих мест на участке.
53. Виды фрезерования. Особенности фрезерования: прямолинейных заготовок по линейке; криволинейных заготовок по кольцу и шаблону; фрезерование поверхности двойной кривизны; торцовое фрезерование по копиру. Анализ применяемого оборудования.
54. Особенности процесса фрезерования прямолинейных заготовок по линейке. Анализ применяемого оборудования, его производительность, организация рабочих мест на участке.
55. Особенности процесса фрезерования криволинейных заготовок по кольцу и шаблону. Анализ применяемого оборудования, его производительность, организация рабочих мест на участке.
56. Особенности процесса фрезерования поверхности двойной кривизны. Анализ, применяемого оборудования его производительность, организация рабочих мест на участке.
57. Особенности процесса фрезерования соединений паркетных планок («клик»). Анализ, применяемого оборудования его производительность, организация рабочих мест на участке.
58. Особенности процесса изготовления деталей окон. Анализ, применяемого оборудования его производительность, организация рабочих мест на участке.
59. Особенности процесса склеивания криволинейных балок. Анализ, применяемого оборудования его производительность, организация рабочих мест на участке.
60. Особенности процесса склеивания строительного бруса и прямолинейных балок. Анализ, применяемого оборудования его производительность, организация рабочих мест на участке.
61. Особенности процесса фрезерования поверхности криволинейных балок. Анализ, применяемого оборудования его производительность, организация рабочих мест на участке.
62. Особенности процесса формирования деталей стропильных систем. Анализ, применяемого оборудования его производительность, организация рабочих мест на участке.
63. Особенности торцового фрезерования деталей по копиру. Анализ применяемого оборудования, его производительность, организация рабочих мест на участке.
64. Проектирование деревянных домов. Программное обеспечение.
65. Технологический процесс шлифования деталей. Анализ применяемого оборудования, его производительность, организация рабочих мест. Режимы шлифования.
66. Технологический процесс сборки деталей в изделие. Сборка деталей в узлы и сборочные единицы. Оборудование, состав, последовательность операций. Общая сборка и ее организация.
67. Качество изделий из древесины. Показатели качества. Контроль качества продукции. Виды контроля и их характеристика. Основные пути повышения качества.
68. Технологическая подготовка производства. Задачи и содержание подготовки производства.
69. Последовательность расчета норм расхода пиломатериалов (заготовок) из древесины при изготовлении столярно-строительных изделий.
70. Методика расчета количества отходов древесных материалов при изготовлении столярно-строительных изделий.
71. Баланс отходов древесных материалов при изготовлении столярно-строительных изделий. Пути использования отходов древесных материалов.
72. Выбор и обоснование расчета производственной программы, необходимого количества технологического оборудования при изготовлении изделий из древесины.
73. Методика расчета производственной программы цеха, участка по производству изделий из древесины. Определение потребного количества оборудования.
74. Методика расчета оптимальных показателей механизации и автоматизации производственных процессов.
75. Основные задачи организационной подготовки производства столярно-строительных изделий.
76. Методика нормирования потребного количества материалов. Пути экономии материалов в производстве изделий из древесины.
77. Деревообрабатывающие центры (многооперационные машины) с числовым программным управлением для всех видов обработки в производстве изделий из древесины.
78. Многооперационные машины с числовым программным управлением для изготовления деталей окон. Особенности обработки, режимы, краткая характеристика.
79. Многооперационные машины с числовым программным управлением для изготовления деталей деревянных домов и стропильных систем. Особенности обработки, режимы, краткая характеристика.
80. Многооперационные машины с числовым программным управлением для изготовления лестниц. Особенности обработки, режимы, краткая характеристика.
81. Многооперационные машины с числовым программным управлением для присадки. Многошпиндельные сверлильно-присадочные станки, линии. Особенности обработки, режимы, краткая характеристика.
82. Шлифовально-калибровальные станки с числовым программным управлением. Особенности обработки, режимы, краткая характеристика.
83. Технологический процесс изготовления паркета. Анализ применяемого оборудования, его производительность, организация рабочих мест.
84. Технологический процесс изготовления дверей рамочно-филенчатой конструкции. Анализ применяемого оборудования, его производительность, организация рабочих мест.
85. Технологический процесс изготовления дверей с сотовым заполнением. Анализ применяемого оборудования, его производительность, организация рабочих мест.
86. Технологический процесс изготовления оконных блоков. Анализ применяемого оборудования, его производительность, организация рабочих мест.
87. Технологический процесс изготовления двухкамерных стеклопакетов. Анализ применяемого оборудования, его производительность, организация рабочих мест.
88. Коэффициент сопротивления теплопередаче. Расчеты. Предельные значения в строительных конструкциях.
89. Технологический процесс изготовления строительного бруса. Анализ применяемого оборудования, его производительность, организация рабочих мест.
90. Технологический процесс изготовления чашек в строительном брусе. Анализ применяемого оборудования, его производительность, организация рабочих мест.
91. Технологический процесс изготовления инженерного паркета. Анализ применяемого оборудования, его производительность, организация рабочих мест.
92. Технологический процесс изготовления доски пола. Анализ применяемого оборудования, его производительность, организация рабочих мест.
93. Технологический процесс изготовления обшивки. Анализ применяемого оборудования, его производительность, организация рабочих мест.
94. Технологический процесс изготовления лестниц. Анализ применяемого оборудования, его производительность, организация рабочих мест.
95. Инновационные технологии производства изделий из древесины. Перспективные технологические процессы. Пути повышения эффективности производства.
Практические задачи
1–10. Рассчитать производительность оконного центра, компл./ч, при изготовлении окна размерами, приведенными в табл. 3.2. Выбрать оконный центр, рассчитать количество деталей.
Таблица 3.2
Условия задач 1–10
№ задачи | Окно | Размеры окна, мм | |
А | В | ||
1 | одностворчатое | 1500 | 700 |
2 | двустворчатое | 1300 | 1200 |
3 | трехстворчатое | 1500 | 1400 |
4 | одностворчатое | 1300 | 500 |
5 | двустворчатое | 1450 | 900 |
6 | трехстворчатое | 1620 | 1420 |
7 | одностворчатое | 1400 | 600 |
8 | двустворчатое | 1830 | 930 |
9 | трехстворчатое | 1650 | 1600 |
10 | одностворчатое | 1000 | 450 |
11–20. Рассчитать производительность торцовочного станка, компл./ч, при поперечном раскрое пиломатериалов длиной l м, на заготовки длиной lзаг м, если кратность заготовок по ширине составляет nш, а в комплект входит m таких заготовок. Время цикла составляет tц мин. Данные для расчета приведены в табл. 3.3.
Таблица 3.3
Условия задач 11–20
№ задачи | Станок | l, м | lзаг, м | nш | m | Tц мин |
11 | ЦПА-40 | 6,50 | 1,20 | 1 | 2 | 0,92 |
12 | ЦМЭ-3Б | 4,00 | 0,95 | 1 | 4 | 0,85 |
13 | TR 350 | 4,25 | 1,30 | 2 | 3 | 1,30 |
14 | ЦКБ-40 | 5,50 | 2,15 | 3 | 5 | 1,15 |
15 | СТБ00-01 | 4,50 | 1,04 | 2 | 7 | 1,20 |
16 | ЦТ10-5М | 3,75 | 1,25 | 3 | 6 | 1,12 |
17 | СТ-350-1 | 5,75 | 0,65 | 2 | 8 | 1,18 |
18 | ЦТ-450 | 6,00 | 0,75 | 1 | 3 | 1,15 |
19 | СМА-10 | 5,00 | 0,85 | 3 | 4 | 1,08 |
20 | TR 450 | 5,25 | 1,60 | 2 | 2 | 1,14 |
21–30. Рассчитать производительность, компл./ч, круглопильного станка для продольного раскроя пиломатериалов. Данные для расчетов принять согласно табл. 3.4.
Таблица 3.4
Условия задач 21–30
№ задачи | Станок, скорость подачи U, м/мин | Размеры пиломатериалов, мм |
Дополнительные данные | |
длина l | ширина b | |||
21 | Однопильный U = 15 м/мин | 6500 | 75 | Суммарная длина заготовок в комплекте 15 м.п., кратность по ширине 1 |
22 | Многопиль-ный. U = 12 м/мин | 5750 | 100 | Длина заготовок lзаг = 1,25 м, ширина заготовок bзаг = 40 мм, количество заготовокв комплекте 10 шт. |
23 | Однопильный U = 20 м/мин | 4250 | 175 | Кратность заготовок по длине 4, по ширине 4, количество заготовок в комплекте 22 шт. |
24 | Многопиль-ный. U = 12 м/мин | 3750 | 125 | Длина заготовок lзаг = 1,55 м, кратность заготовок по ширине 3, в комплект входит 12 заготовок |
25 | Однопильный U =18 м/мин | 4500 | 150 | Суммарная длина заготовок в комплекте 22 м.п., кратность по ширине 3 |
26 | Многопиль-ный. U = 22 м/мин | 5500 | 75 | Длина заготовок lзаг = 1,72 м, ширина заготовок bзаг = 20 мм, количество заготовокв комплекте 17 шт. |
27 | Однопильный U = 16 м/мин | 2500 | 125 | Кратность заготовок по длине 3, по ширине 3, количество заготовок в комплекте 25 шт. |
28 | Многопиль-ный. U = 15 м/мин | 3250 | 150 | Длина заготовок lзаг = 1,40 м, кратность заготовок по ширине 2, в комплект входит 9 заготовок |
29 | Однопильный U = 10 м/мин | 2750 | 225 | Суммарная длина заготовок в комплекте 30 м.п., кратность по ширине 5. |
30 | Многопиль-ный. U = 16 м/мин | 4000 | 100 | Длина заготовок lзаг = 1,8 м, ширина заготовок bзаг = 40 мм, количество заготовокв комплекте 15 шт. |
31–40. Рассчитать производительность пресса для склеивания балок, строительного бруса, компл./ч, в состав комплекта входит n шт. таких деталей. Длина брусьев 6 м. Данные для расчетов принять согласно табл. 3.5.
Таблица 3.5
Условия задач 31–40
№ задачи | Размер рабочего поля пресса, мм | Клей | Размеры Склеиваемых брусьев, мм | Кол-во n, шт | |
А | В | ||||
31 | 1200×6500 | Меламиноформальдегидный | 230 | 230 | 80 |
32 | 1300×6500 | полиуретановый | 230 | 150 | 102 |
33 | 1400×13000 | полимеризоционатный | 600 | 200 | 24 |
34 | 1400×6500 | Меламиноформальдегидный | 700 | 210 | 9 |
35 | 1300×13000 | полиуретановый | 280 | 180 | 63 |
36 | 1200×13000 | полимеризоционатный | 780 | 200 | 14 |
37 | 1500×13000 | Меламиноформальдегидный | 1100 | 300 | 10 |
38 | 1500×6500 | полиуретановый | 610 | 200 | 8 |
39 | 1800×6500 | полимеризоционатный | 200 | 200 | 62 |
40 | 1800×13000 | полиуретановый | 200 | 250 | 20 |
41–50. Выбрать станок для формирования поперечного сечения брусьев, балок размером А×В мм, длиной s, рассчитать его производительность, компл./ч, если в состав комплекта входит i таких деталей. Данные для расчетов принять согласно табл. 3.6. Привести техническую характеристику выбранного оборудования.
Таблица 3.6
Условия задач 41–50
№ задачи | Размеры облицовываемых щитов, мм | Количество заготовок в комплекте, i, шт | |||
А | В | s | |||
41 | 230 | 230 | 6 | 40 | |
42 | 230 | 150 | 12 | 201 | |
43 | 600 | 200 | 15 | 33 | |
44 | 700 | 210 | 18 | 41 | |
45 | 280 | 180 | 6 | 80 | |
46 | 780 | 200 | 13 | 44 | |
47 | 1100 | 300 | 15 | 16 | |
48 | 610 | 200 | 9 | 53 | |
49 | 200 | 200 | 6 | 240 | |
50 | 200 | 250 | 15 | 120 |
51–60. Рассчитать производительность пресса и количество клея необходимое для склеивания щита размером А×В мм, толщиной s мм. Данные для расчетов принять согласно таблице 3.7
Таблица 3.7
Условия задач 51–60
№ задачи | Размеры рабочего промежутка пресса | Температура плит пресса t, ºC | Клеевая композиция | Размеры | Дополнительные | ||
А | В | s | |||||
51 | 2200×850 | 20 | КФ-МХ | 900 | 600 | 19 | Количество поверхностей склеивания 7 |
52 | 1200×800 | 80 | Bindan - F | 890 | 250 | 22 | Ширина склеиваемых ламелей 50 мм |
53 | 2400×1200 | 20 | Иваколь 102.70 | 600 | 600 | 20 | Количество ламелей по ширине 10 |
54 | 1000×1000 | 120 | КФК-20 | 700 | 240 | 25 | Ширина склеиваемых ламелей 40 мм |
55 | 2200×850 | 20 | Клебит 303.0 | 340 | 250 | 34 | Количество ламелей по ширине 5 |
56 | 3000×900 | 20 | Cascol 3339 | 780 | 280 | 28 | Количество поверхностей склеивания 6 |
57 | 1700×1300 | 50 | Bindan - F | 1800 | 400 | 26 | Ширина склеиваемых ламелей 50 мм |
58 | 2000×1200 | 20 | Rakoll Duplit | 500 | 200 | 18 | Количество ламелей по ширине 4 |
59 | 3000×900 | 20 | КФ-ЖМ | 700 | 400 | 24 | Количество поверхностей склеивания 7 |
60 | 1400×1200 | 50 | Иваколь 102.70 | 2000 | 750 | 30 | Количество ламелей по ширине 15 |
61–70. Выбрать станок для продольного строгания ламелей и определить их потребное количество при изготовлении мебельного щита размером А×В мм, толщиной s мм, если годовой выпуск щита составляет Пгод м2. Цех работает в одну смену 8 часов. Данные для расчетов принять согласно табл. 3.8.
Таблица 3.8
Условия задач 61–70
№ задачи | Станок
| Размеры щита, мм | Пгод, тыс. м2 | Дополнительные данные | ||
А | В | s | ||||
61 | Односторонний рейсмусовый | 900 | 800 | 20 | 60 | Количество ламелей по ширине 16 |
62 | Двусторонний рейсмусовый | 800 | 750 | 22 | 70 | Ширина ламелей 50 мм |
63 | Четырехсторонний продольно фрезерный | 1500 | 600 | 28 | 65 | Количество ламелей по ширине 12 |
64 | Двусторонний рейсмусовый | 1000 | 720 | 16 | 82 | Ширина ламелей 60 мм |
65 | Четырехсторонний продольно-фрезерный | 1200 | 800 | 32 | 48 | Количество ламелей по ширине 20 |
66 | Двусторонний рейсмусовый | 900 | 700 | 25 | 54 | Ширина ламелей 50 мм |
67 | Четырехсторонний продольно фрезерный | 780 | 620 | 26 | 62 | Количество ламелей по ширине 15 |
68 | Односторонний рейсмусовый | 1300 | 500 | 24 | 75 | Ширина ламелей 50 мм |
69 | Двусторонний рейсмусовый | 1500 | 1000 | 22 | 55 | Количество ламелей по ширине 25 |
70 | Односторонний рейсмусовый | 1100 | 900 | 19 | 40 | Ширина ламелей 30 мм |
71–80. Рассчитать производительность линии сращивания по длине, компл./ч, при производстве щита размером L× B×s. Данные для расчетов принять согласно таблице 3.9.
Таблица 3.9
Условия задач 71–80
№ задачи | Характеристика линии сращивания | Черновые размеры щита, мм | Примечание
| ||
L | B | s | |||
71 | 2 шипорезных узла, ширина закладки 400 мм, длина пресса 5000 мм | 1500 | 800 | 20 | Шип горизонтальный, средняя длина сращиваемых заготовок 300 мм, скорость подачи на шипорезном узле 10 м/мин. Число тактов пресса в минуту 2 |
Продолжение табл.3.9
№ задачи | Характеристика линии сращивания | Черновые размеры щита, мм | Примечание
| ||
L | B | s | |||
72 | 1 шипорезный узел, ширина закладки 600 мм, длина пресса 3000 мм | 500 | 200 | 20 | Шип горизонтальный, средняя длина сращиваемых заготовок 350 мм, скорость подачи на шипорезном узле 12 м/мин. Число тактов пресса в минуту 1,5 |
73 | 1 шипорезный узел, ширина закладки 450 мм, длина пресса 6000 мм | 2000 | 70 | 26 | Шип вертикальный, средняя длина сращиваемых заготовок 400 мм, скорость подачи на шипорезном узле 8 м/мин. Число тактов пресса в минуту 1 |
74 | 2 шипорезных узла, ширина закладки 500 мм, длина пресса 4000 мм | 1200 | 150 | 19 | Шип горизонтальный, средняя длина сращиваемых заготовок 380 мм, скорость подачи на шипорезном узле 13 м/мин. Число тактов пресса в минуту 2 |
75 | 1 шипорезный узел, ширина закладки 500 мм, длинна пресса 2500 мм | 920 | 680 | 23 | Шип горизонтальный, средняя длина сращиваемых заготовок 350 мм, скорость подачи на шипорезном узле 10 м/мин. Число тактов пресса в минуту 1,5 |
76 | 2 шипорезных узла, ширина закладки 600 мм, длинна пресса 3500 мм | 800 | 600 | 30 | Шип вертикальный, средняя длина сращиваемых заготовок 450 мм, скорость подачи на шипорезном узле 9 м/мин. Число тактов пресса в минуту 3 |
77 | 1 шипорезный узел, ширина закладки 400 мм, длина пресса 2000 мм | 1400 | 75 | 28 | Шип горизонтальный, средняя длина сращиваемых заготовок 300 мм, скорость подачи на шипорезном узле 12 м/мин. Число тактов пресса в минуту 1 |
78 | 1 шипорезный узел, ширина закладки 450 мм, длина пресса 2500 мм | 720 | 480 | 19 | Шип вертикальный, средняя длина сращиваемых заготовок 300 мм, скорость подачи на шипорезном узле 11 м/мин. Число тактов пресса в минуту 2 |
79 | 2 шипорезных узла, ширина закладки 430 мм, длина пресса 6000 мм | 670 | 180 | 21 | Шип горизонтальный, средняя длина сращиваемых заготовок 380 мм, скорость подачи на шипорезном узле 10 м/мин. Число тактов пресса в минуту 3 |
Окончание табл.3.9
№ задачи | Характеристика линии сращивания | Черновые размеры щита, мм | Примечание
| ||
L | B | s | |||
80 | 1 шипорезный узел, ширина закладки 400 мм, длина пресса 3000 мм | 1150 | 700 | 24 | Шип вертикальный, средняя длина сращиваемых заготовок 400 мм, скорость подачи на шипорезном узле 12 м/мин. Число тактов пресса в минуту 1. |
81–90. Выбрать станок для шлифования, привести его техническую характеристику и рассчитать его производительность при шлифовании продукции. Данные для раcчетов принять по табл. 3.10.
Таблица 3.10
Условия задач 81–90
№ задачи | Выполняемая операция | Размеры детали, мм | Количество деталей в комплекте, n, шт. | Примечание | ||||
длина l | ширина b | толщина s | ||||||
81 | Шлифование пластей | 2100 | 800 | 17 | 3 | Шлифовать тремя номерами шкурок 2 стороны | ||
82 | Шлифование кромок | 800 | 700 | 20 | 2 | Шлифовать тремя номерами шкурок 2 продольные и 1 поперечную кромки | ||
83 | Шлифование пластей | 900 | 650 | 22 | 5 | Шлифовать одним номером шкурки 2 стороны | ||
84 | Шлифование кромок | 1500 | 820 | 28 | 4 | Шлифовать двумя номерами шкурок 1 продольную и 1 поперечную кромки | ||
85 | Шлифование пластей | 1000 | 500 | 18 | 8 | Шлифовать одним номером шкурки 1 сторону | ||
Окончание табл.3.10
№ задачи | Выполняемая операция | Размеры детали, мм | Количество деталей в комплекте, n, шт. | Примечание | ||
длина l | ширина b | толщина s | ||||
86 | Шлифование кромок | 1200 | 700 | 19 | 2 | Шлифовать одним номером шкурки 2 продольные и 2 поперечные кромки |
87 | Шлифование пластей | 1250 | 680 | 22 | 1 | Шлифовать тремя номерами шкурок 2 стороны |
88 | Шлифование кромок | 1800 | 900 | 17 | 3 | Шлифовать тремя номерами шкурок 1 продольную кромку |
89 | Шлифование пластей | 1600 | 120 | 18 | 5 | Шлифовать двумя номерами шкурок 1 сторону |
90 | Шлифование кромок | 1750 | 200 | 16 | 4 | Шлифовать тремя номерами шкурок 2 продольные и 2 поперечные кромки |
91–100. Составить карту технологического процесса изготовления детали изделия и определить потребное количество оборудования указанного типа для выполнения годовой программы
Пгод, тыс. дет./год. Привести характеристики принятого оборудования. Данные для расчетов принять по табл. 3.11.
Таблица 3.11
Условия задач 91–100
№ задачи | Деталь | Материал | Размеры детали, мм | Примечание | Пгод, тыс. дет./ год | Тип расчетного оборудования | |
длина | ширина | ||||||
91 | Брусок вертикальный двери | Древесина бука | 2100 | 120 | – | 410 | Станок продольно-фрезерный |
92 | Брус стеновой, трехслойный | Древесина сосны | 6000 | 230 | – | 385 | Пресс |
93 | Брус стеновой | Древесина сосны | 6000 | 230 | 2 чашки | 280 | Чашкозарезной станок |
94 | Брус стеновой | Древесина сосны | 6000 | 230 | 2 отверстия | 300 | Станок для сверления отверстий |
95 | Балка | Древесина сосны | 13000 | 800 | - | 350 | Станок продольно-фрезерный |
96 | Брусок створки горизонтальный | Древесина сосны | 950 | 86 | – | 400 | Угловой обрабатывающий центр |
97 | Брусок створки вертикальный | Древесина сосны | 450 | 86 | 330 | Угловой обрабатывающий центр | |
98 | Перила лестницы | Древесина бука | 2 500 | 50 | В бруске выбран паз | 420 | Станок продольно-фрезерный |
99 | Щит | Ламели из древесины березы | 700 | 600 | Ширина ламели 50 мм | 300 | Пресс для склеивания по ширине |
100 | Балясина точеная | Древесина бука | 800 | d=60 | 140 | Станок для создания базы |
Литература
Основная
1. Игнатович, Л. В. Технология изделий из древесины. Проек-тирование производственного процесса: учеб. пособие для студ. спец. «Технология деревообрабатывающих производств» / Л. В. Игнатович, С. В. Шетько. – Минск: БГТУ, 2006. – 134 с.
2. Игнатович, Л. В. Технология изделий из древесины. Курсовое и дипломное проектирование: учеб.-метод. пособие для студ. спец. «Технология деревообрабатывающих производств» / Л. В. Игнатович, А. А. Барташевич, Л. М. Бахар. – Минск: БГТУ, 2007. – 140 с.
3. Игнатович, Л. В. Технология изделий из древесины. Лабораторный практикум / Л. В. Игнатович, Л. М. Бахар. – Минск: БГТУ, 2009. – 100 с.
4. Амалицкий, В. В. Оборудование отрасли: учебник / В. В. Амалицкий, Вит. В. Амалицкий. – М.: ГОУ ВПО МГУЛ, 2006. – 584 с.
5. Справочник мебельщика: учеб. пособие для вузов / под ред. В. П. Бухтиярова. – М.: МГУЛ, 2008. – 600 с.
6. Барташевич, А. А. Технология изделий из древесины: в 2 ч. – Ч.1: Типовые технологические режимы. Учебное пособие – республиканский нормативный документ / А. А. Барташевич [ и др.]. – Минск: БГТУ, 2010. –299 с.
7. Барташевич, А. А. Технология изделий из древесины: в 2 ч. – Ч.2: Нормы расхода сырья и материалов. Учебное пособие – республиканский нормативный документ / А. А. Барташевич [ и др.]. – Минск: БГТУ, 2010. –178 с.
8. Цитц Герхард, Производство оконных и дверных блоков – М.: Лесная промышленность, 1981.
Дополнительная
1. Гончаров, Н. А. Технология изделий из древесины: учебник для вузов / Н. А. Гончаров, В. Ю. Башинский, Б. М. Буглай. – М.: Лесная промышленность, 1990. – 512 с.
2. Трофимов, С. П. Проектирование д/о предприятий: учеб. пособие для студ. спец. «Технология деревообрабатывающих производств»: в 2 ч. – Ч. 1: Введение в системы автоматизации подготовки производства / С. П. Трофимов.– Минск.: БГТУ, 2005. – 138 с.
3. Справочное руководство по древесине – М.: Лесная промышленность, 1978. Пер. с английского Т.В. Михайловой
Дата добавления: 2018-11-24; просмотров: 236; Мы поможем в написании вашей работы! |
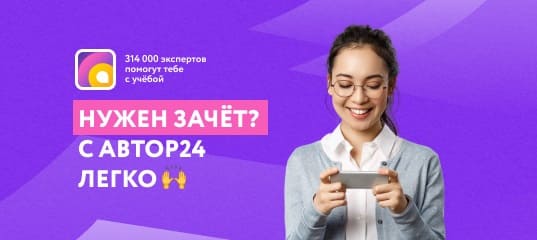
Мы поможем в написании ваших работ!