Графический способ определения профиля резца
Содержание
Введение 4
1. Проектирование фасонного резца 5
2. Проектирование протяжки 12
3. Проектирование комбинированного инструмента21
Реферат 29
Заключение 38
Список литературы 39
Введение
В современном машиностроении обработка резанием является главным технологическим методом, обеспечивающим высокое качество и точность обрабатываемых поверхностей детали.
Эффективность машиностроения повышается за счет увеличения удельного веса автоматизированного оборудования, в том числе автоматических линий, станков с ЧПУ, роботизированных комплексов и гибких производственных систем, позволяющих быстро и эффективно перестраивать производство на выпуск новых изделий.
Эффективная эксплуатация указанного оборудования невозможна без создания совершенной инструментальной оснастки, обладающей повышенной надежностью, обеспечивающей экономичное, трудосберегающее использование дорогостоящей прогрессивной техники, что обуславливает возрастающую роль металлообрабатывающего инструмента
Целью данной курсовой работы является приобретение практических навыков расчета и конструирования инструментов, полученных в курсе «Режущий инструмент».
|
|
Проектирование фасонного резца.
Тип резца: Призматический
Обрабатываемый материал :50ХГ
Рис.1.1 Эскиз обрабатываемой детали.
Выбор переднего и заднего углов заточки резца.
В зависимости от материала заготовки выбираем передний и задний углы лезвия резца по ([9], табл. 47): .
Определение габаритных размеров резца и размеровприсоединительных частей.
Наибольшая глубина профиля детали:
мм,
где dmax, dmin – максимальный и минимальный диаметры заготовки.
Габаритные и конструкторские размеры резца для tmax=6 мм выбираем по ([9], табл. 44). Конструктивные размеры B=35 мм, Н=90 мм, Е=10, А=40, F=25, r=1, d=10, M(h9)=55,77.
Длина резца вдоль оси заготовки определяется размером получаемой детали. Также необходимо учитывать ширину дополнительной упрочняющей режущей кромки а, размеры которой оговорены ([9], стр. 137). Принимаем: с=1 мм. Ширина участка режущей кромки, предназначенной для протачивания канавки с целью облегчения отрезания b = 5.5 мм, перекрытие режущей кромки под отрезание b1 = 1,5 мм, и 1 мм на дополнительную обработку.
Тогда общая длина резца:
мм,
где - длина детали.
Профилирование резца.
Профиль фасонного резца не совпадает с профилем исходной заготовки. Поэтому профиль резца необходимо скорректировать. Профиль резца можно определить двумя способами: аналитическим и графическим.
|
|
Подбор величины подачи за один оборот детали.
Выбор величины подачи производим по рекомендациям [3]. По табл. IV.6. находим ближайшую ширину обрабатываемой детали и похожий профиль фасонного резца, которому соответствует значения подачи. Учитывая ширину обрабатываемой поверхности, физико-механические свойства обрабатываемого материала, а также увеличение сил резания с увеличением подачи, принимаем меньшееиз приведенных значений подач:
S=0,028 мм/об.
Графический способ определения профиля резца
Рис.1.3 Графическое построение профиля призматического фасонного резца.
Строим профиль заготовки, для чего проводим ось ОО (рис.1.3, от которой откладываем соответствующие размеры профиля заготовки.
Проецируем полученные точки 1,2,3,4,5,6,профиля заготовки на горизонтальную ось, проходящую через центр заготовки О (точки 1’,2’, 3’,4’,5’, 6’), через которые проводим соответствующие окружности.
Из точки 1’ (А1) проводим линию (след) передней поверхности лезвия резца под углом и линию (след) задней поверхности под углом
Обозначаем точки пересечения соответствующих окружностей резца с линией передней поверхности через А1-2, А3-4. Из этих точек проводим линии, параллельные задней поверхности резца до пересечения их с линией (следом нормальной плоскости) и далее соответствующими радиусами из точки 4' делаем засечки на горизонтальной прямой, проходящей через эту точку. Из полученных точек проводим вертикальные линии до пересечения с соответствующими горизонтальными линиями, параллельными линии ММ, находим точки 1’,2’,3’,4’,5’,6’. Соединяя эти точки прямыми, получаем профиль резца в нормальном сечении.
|
|
Дата добавления: 2018-06-27; просмотров: 201; Мы поможем в написании вашей работы! |
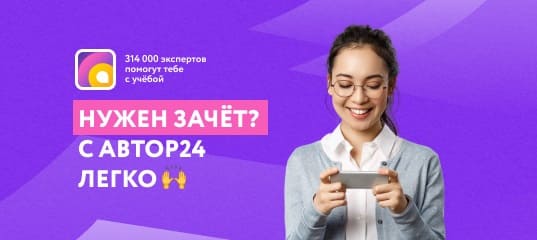
Мы поможем в написании ваших работ!