Характеристика вязкостных присадок
Показатели | КП-5 | КП-10 | КП-20 | ПМА "В-1" | ПМА "В-2" | Дизакрил |
Содержание активного вещества | ³65 | ³30 | ³25 | 58-65 | – | 30-36 |
Молекулярная масса активного вещества | 4000-6000 | 9000-15000 | 15000-25000 | 3000-43000 | 12000-17000 | – |
Кинематическая вязкость при 100оС, мм2/с | 250-1000 | 450-1000 | – | 200-320 | – | – |
Кинематическая вязкость при 50оС, мм2/с | – | – | – | 1100-1700 | 1100-1700 | 1100-1700 |
Температура вспышки, оС, не ниже |
Вязкостные присадки КП-5, КП-10, КП-20 являются продуктами полимеризации полибутилена, средняя молекулярная масса присадок от 4000 до 25000; применяются в виде масляных растворов: КП-5 - раствор полиизобутилена средней молекулярной массы 4000-6000 в трансформаторном масле; КП-10 – раствор полиизобутилена средней молекулярной массы 9000-15000 в масле И‑12А и, наконец, КП-20 - раствор полиизобутилена средней молекулярной массы 15000-25000 в масле И-12А.
Присадки типа полиизобутилена могут применяться в растворе и других масел при получении загущенных моторных, индустриальных, редукторных масел и гидравлических жидкостей.
Присадки типа полиметакрилатов ПМА "В-1", ПМА "В-2", Дизакрил представляют собой масляные растворы эфиров метакриловой кислоты и смеси синтетических первичных жирных спиртов С7-С12 (присадка ПМА "В-1") или спиртов С8-С10 (присадка ПМА "В-2" и Дизакрил).
Необходимое пояснение: метакриловая кислота СН2=С(СН3)СООН; она же 2-метилпропеновая кислота, она же пропенкарбоновая-2 кислота.
|
|
ПМА "В-2" - 30-35%-ный раствор полиметакрилатов в масле И-20А (индустриальное масло общего назначения, как и И-12А). Применяется в моторных маслах и рабочих жидкостях в концентрации до 6 % мас. По сравнению с ПМА "В-1" обладает лучшей загущающей способностью, но уступает по стабильности к механической деструкции.
ВНИИПОЛ ВБ-2 - полимер винил-н-бутилового эфира и предназначена в качестве загущающей присадки в производстве гидравлических, компрессорных и других масел.
Рис. 3.7. Технологическая схема производства присадки полиизобутилена.
1, 7, 11, 14, 15, 18, 19, 20, 23, 24 - емкости; 2, 6 - смесители;
3 - осушительная колонна; 4 - холодильники; 5 - реактор;
8, 9, 12, 16, 21 - колонны; 10, 13, 17, 22 - конденсаторы.
Основными стадиями процесса являются сушка изобутилена, его полимеризация и отгонка непрореагировавших компонентов. В процессе используют изобутилен-ректификат (95-96% изобутилена), изобутан, хлористый кальций и твердый едкий натр (осушители), этиловый спирт, хлористый этил, хлористый алюминий, масло-разбавитель и аммиак.
Изобутилен и свежий изобутан подаются в смеситель 2, куда поступают также регенерированные изобутилен и изобутан. Сырьевая смесь поступает в колонну 3, заполненную на 66% рабочей емкости хлористым кальцием и на 34% едким натром. Здесь происходит осушка сырья и освобождение от примесей - следов спирта, димеров изобутилена и др. Осушенная смесь в аммиачном холодильнике окончательно освобождается от влаги и охлаждается до заданной температуры полимеризации.
|
|
Реакция полимеризации происходит в жидкой фазе при -30оС и ниже в зависимости от необходимой глубины полимеризации. Сырьевая смесь поступает двумя потоками в реактор 5 через распылительные устройства, катализатор (2%-ный раствор хлористого алюминия в хлористом этиле) подается в реактор через три распределительных устройства. Степень полимеризации составляет 80-90%. Выделяющееся при реакции тепло снимается путем многократного пропускания реагирующей смеси над охлаждающими поверхностями реактора 5. Полимер, растворенный в изобутане, поступает из реактора в диафрагменный смеситель 6, куда подается этиловый спирт для дезактивации; затем полимер смешивается с маслом-разбавителем в емкости 7. Полиизобутилен, растворенный в масле, поступает на дегазацию, которая осуществляется в двух колоннах; одна из которых (8) работает при небольшом избыточном давлении, а вторая (12) - в вакууме. В колонне 8 отделяются непрореагировавшие изобутилен и изобутан, а также хлористый этил и этиловый спирт. Раствор полиизобутилена в масле из нижней части колонны 8 направляется в колонну 12 и после дополнительной перегонки направляется в емкость 15 товарного продукта.
|
|
Ректификация газов полимеризации осуществляется в колоннах 9, 16 и 21. Верхний продукт колонны 8 подается в колонну 9. С верха этой колонны отбираются изобутан и изобутилен; их через конденсатор 10 частично подают на орошение колонны 9, а избыток откачивается в емкость 1 регенерированной изобутан-изобутиленовой смеси. Кубовый остаток колонны 9 подается в колонну 16, с верха которой отбирается хлористый этил. Часть хлористого этила подают на орошение колонны 16, а остальное направляют в емкость 19. Из куба колонны 16 этиловый спирт поступает в емкость 20, откуда по мере необходимости его подают в периодически работающую колонну 21. Пары спирта после конденсации частично направляют на орошение колонны 21, а избыток - в емкость 24.
Дата добавления: 2015-12-21; просмотров: 10; Мы поможем в написании вашей работы! |
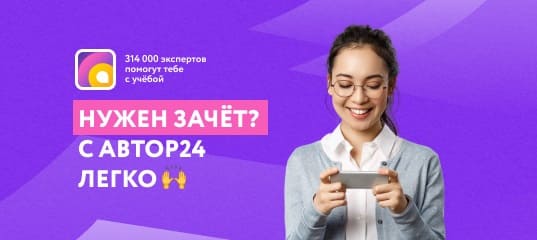
Мы поможем в написании ваших работ!