Приемка и сдача тепловоза. 1 страница
1.1 Сдающая бригада должна выполнить предусмотренную уборку на локомотиве согласно инструкции ЦТ - 329, а также произвести записи в журнале ТУ- 152 о всех не исправностях.
1.2 Машинист, сдающий локомотив несет ответственность за скрытие имеющихся на тепловозе неисправностях (в том числе и переключении эл схемы на аварийный режим работы).
1.3 Принимающая бригада должна проверить по журналу ТУ 152 выполнение записанного ремонта, убедиться в исправном состоянии тепловоза, обратив особое внимание на действие тормозов, скоростемера, радиосвязи и АЛСН, проверить наличие и состояние инструмента и инвентаря, наличие пломб на приборах, которые должны запломбированы.
1.4 Обнаруженные во время приемки неисправности на тепловозе должны быть устранены. Если неисправности не могут быть устранены силами бригад, то ма- шинист, принимающий тепловоз, обязан поставить в известность дежурного по депо.
Уход и содержание экипажной части тепловоза.
Приемка тепловоза из депо
1.5 В соответствии с пунктом 12.4 ПТЭ локомотив ная бригада обязана проверить:
состояние и износ узлов и деталей и их соответствие установленным размерам.
1.6 Исправность действия тормозного оборудования и автосцепного устройства контрольно - измерительных приборов.
Запрещается выпускать под поезда тепловозы в эксплуатацию, у которых имеется хотя бы одна из следующих неиправностей:
- неисправность прибора для звукового сигнала;- неисправность пневматического, электро-пневматического ручного тормоза или компрессора;
|
|
- неисправность или отключение хотя бы одного тя гового электродвигателя;
- неисправность вентилятора холодильника дизеля, электродвигателей и выпрямительной установки;
- неисправность автостопа, АЛСН или устройств проверки бдительности;
- неисправность скоростемера;
- неисправность устройств поездной или маневровой радиосвязи;
- неисправность автосцепных устройств;
- неисправность системы подачи песка;
- неисправность прожектора, буферного фонаря, освещение контрольно — измерительных приборов;
- трещина в хомуте рессоры, рессорной подвески или коренном листе рессоры, излом рессорного листа;
- трещина в корпусе буксы;
- неисправность буксового или моторно – осевого подшипника;
- отсутствие или неисправность предусмотренного конструкцией предохранительного устройства от падения деталей на путь;
- трещина или излом хотя бы одного зуба тяговой зубчатой передачи;
- неисправность кожуха зубчатой передачи;
- неисправность защитных блокировок высоковольтных шкафов и камер;
- неисправность средств пожаротушения;
- неисправность устройств защиты от токов короткого замыкания, перегрузки, аварийной остановки ди- зеля;
|
|
- появление стука, постороннего шума в дизеле;
- неисправность гидродемферов, аккомуляторной батареи.
- неисправность предохранительных клапанов;
- отсутствие тормозных башмаков (должно быть 14 штук на тепловоз).
ТОРМОЗНОЕ ОБОРУДОВАНИЕ ТЕПЛОВОЗА 2ТЭ116
Пневматическая схема тепловозов 2ТЭ116. выпускавшихся в разные годы, предусматривает возможность вождения сдвоенных поездов с помощью синхронизации управления тормозами. Тепловозы 2ТЭ116 имеют автоматический, вспомогательный (неавтоматический) и ручной тормоз. Отличительной особенностью тепловозов 2ТЭ116 является наличие электрического (реостатного) тормоза на локомотивах, постройки начала 90-х годов прошлого века.
На тепловозах (рис. 2.6), выпускавшихся до 1976года, установлен компрессор (К) КТ-7 с приводом от электродвигателя, работой которого совместно управляют регулятор давления (РГД) № 3РД и реле давления (РДК) типа АК-11Б. РДК отрегулировано на давление 5,0 – 5,5кгс/см2.
Компрессор нагнетает сжатый воздух в четыре последовательно соединенных главных резервуара (ГР) объемом по 250 л каждый. Главные резервуары снабжены выпускными кранами для удаления конденсата. На нагнетательном трубопроводе между компрессором и ГР установлен маслоотделитель (МО) № Э-120, обратный клапан (КО1) № 3-155 и два предохранительных клапана (КП1, КП2) № Э-216, отрегулированные на давление 10,7 кгс/см2.
|
|
При давлении воздуха в главных резервуарах менее 7,5 кгс/см2 регулятор давления РГД сообщает трубопровод между РГД и РДК с атмосферой. При этом контакты РДК замыкаются и происходит пуск двигателя компрессора. Одновременно с пуском электродвигателя получает питание катушка разгрузочного вентиля (ЭПВ1) типа ВВ-32, который начинает пропускать воздух давлением 5,5 кгс/см2 из воздухопровода управления к разгрузочным устройствам компрессора. Последние отжимают всасывающие клапаны компрессора, соединяя его напорную магистраль с атмосферой и обеспечивая тем самым пуск компрессора без противодавления. С выходом электродвигателя компрессора на номинальную частоту вращения катушка ЭПВ1 обесточивается, и разгрузочный вентиль вытекает в атмосферу сжатый воздух из полости разгрузочных устройств компрессора. Электродвигатель компрессора начинает работать под нагрузкой, а компрессор переходит в рабочий режим. При достижении давления в главных резервуарах 9,0 кгс/см2 регулятор давления РГД подает сжатый воздух к реле давления РДК, контакты которого размыкаются, разрывают цепь питания электродвигателя компрессора и компрессор останавливается.
|
|
При зарядке тормозной сети воздух из ГР поступает в питательную магистраль (ПМ), откуда через устройство блокировки тормозов (БТ) № 367 подходит к поездному крану машиниста (КМ) № 395, который обеспечивает зарядку уравнительного резервуара (УР) объемом 20 л. и крану вспомогательного локомотивного тормоза (КВТ) № 254. По отводам ПМ сжатый воздух через разобщительный кран 3 и фильтр (Ф) № Э-114 подходит к электропневматическому клапану автостопа (ЭПК) № 150, а также через клапан максимального давления (КМД) № ЗМД к реле давления (РД) № 304. КМД понижает давление питательной магистрали с 9,0 кгс/см2 до 5,0 кгс/см2.
Через КМ сжатый воздух поступает в тормозную магистраль (ТМ), из которой имеются отводы к скоростемеру (СЛ), через разобщительный кран 4 к ЭПК и через разобщительный кран 5 к воздухораспределителю (ВР) № 483. Через ВР из тормозной магистрали происходит зарядка запасного резервуара (ЗР) объемом 55 л. На отводе ТМ установлено также реле давления воздуха (РДВ) типа АК-11Б.
При падении давления в ТМ ниже 2,7 – 3,2 кгс/см2 контакты РДВ размыкаются и обеспечивают перевод тягового генератора тепловоза в режим холостого хода. Таким образом, РДВ исключает приведение тепловоза в движение при давлении в ТМ менее 4,5 кгс/см2.
Тормозная магистраль может сообщаться с питательной магистралью через обратный клапан КО2 № Э-175 и разобщительный кран 1 (кран холодного резерва), который открывается только в случае пересылки тепловоза в недействующем (холодном) состоянии. При движении тепловоза с составом или при следовании резервом разобщительный кран 1 закрыт.
При торможении КВТ воздух из питательной магистрали через устройство блокировки тормозов БТ поступает в магистраль тормозных цилиндров (МТЦ) и далее в тормозные цилиндры (ТЦ) первой тележки. Из МТЦ сжатый воздух поступает также в управляющую камеру реле давления (повторителя) РД, которое срабатывает на торможение и наполняет ТЦ второй тележки из питательной магистрали через КМД. Отпуск тормоза производится постановкой ручки КВТ в поездное положение. При этом через КВТ выходит в атмосферу воздух из ТЦ первой тележки и из управляющей камеры реле давления РД, которое в свою очередь опорожняет в атмосферу ТЦ второй тележки.
При снижении давления в ТМ поездным краном машиниста КМ воздухораспределитель ВР срабатывает на торможение и пропускает сжатый воздух из ЗР в импульсную магистраль ПМ, к которой подключен «ложный тормозной цилиндр», - резервуар -компенсатор РКР объемом 5 л. По импульсной магистрали воздух проходит в КВТ, который срабатывает как повторитель. и сообщает питательную магистраль с ТЦ первой тележки и с управляющей камерой реле давления РД. Реле давления срабатывает на торможение и наполняет ТЦ второй тележки из ПМ через КМД. Для обеспечения отпуска тормозов необходимо установить ручку КМ в положение I или II. При этом давление в ТМ повышается и ВР, сработав на отпуск, выпускает воздух в атмосферу из импульсной магистрали, а кран вспомогательного тормоза КВТ - из ТЦ первой тележки и управляющей камеры РД. Реле давления, в свою очередь, выпускает воздух в атмосферу из ТЦ второй тележки.
На каждой тележке тепловоза установлено по шесть тормозных цилиндров № 553 диаметром 8".
Для вождения соединенных поездов тепловоз оборудован устройством пневматической синхронизации работы кранов машиниста. Это устройство включает в себя магистраль синхронизации (МСТ) с соединительным рукавом и трехходовой кран 6, соединенный штуцерами с КМ и УР.
При управлении тормозами соединенного поезда по системе синхронизации на локомотиве в середине состава концевой рукав магистрали синхронизации соединяют с тормозной магистралью хвостового вагона и открывают концевые краны. Трехходовой кран 6 устанавливают в положение «Синхронизация включена», а ручку крана машиниста КМ переводят в IV положение и закрепляют специальной скобой для исключения перемещения ее в положения I, II и III. Таким образом, уравнительный резервуар УР сообщается через кран 6 с атмосферой, а полость над уравнительным поршнем крана машиниста КМ с тормозной магистралью хвостового вагона первого поезда. Следовательно, изменение давления воздуха в ТМ первого поезда вызывает перемещение уравнительного поршня КМ локомотива, находящегося в середине соединенного поезда, что, в свою очередь, приводит к торможению или к отпуску тормозов.
Для следования тепловоза в холодном состоянии в одной кабине блокировка тормозов БТ должна быть включена, ручка крана машиниста КМ установлена в положение экстренного торможения, а крана вспомогательного локомотивного тормоза - в поездное положение. Во второй кабине устройство блокировки тормозов выключают, а ручки КМ и КВТ устанавливают в VI положение. Комбинированные краны на БТ в обеих кабинах устанавливают в положение двойной тяги, разобщительные краны 3 и 4 к ЭПК перекрывают. На каждой секции необходимо установить ВР на средний режим торможения, перекрыть разобщительный кран 3 между третьим и четвертым ГР и открыть кран холодного резерва 1. Скоростемеры и пневматические цепи вспомогательных аппаратов должны быть отключены от источников сжатого воздуха соответствующими разобщительными кранами, концевые краны питательной магистрали закрыты, а соединительные рукава ПМ сняты.
Пневматическая схема (рис. 2.7) тепловозов 2ТЭ116 последующих выпусков (до № 1540) подверглась существенной модернизации. Один из главных резервуаров объемом 250 л стал выполнять функции питательного резервуара (ПР). Он подключен к питательной магистрали через обратный клапан КО3 № Э-175. Питательный резервуар ПР обеспечивает наполнение ТЦ в случае саморасцепа секций тепловоза.
На тепловозе установлена система осушки сжатого воздуха (СОВ), которая может быть отключена разобщительным краном 3.
Объем запасного резервуара ЗР уменьшен до 20 л. Реле давления (РД1, РД2) установлены на каждой тележке. Сжатый воздух к обоим реле давления подводится из питательного резервуара через соответствующие редукторы давления (РЕД1, РЕД2) № 348, которые понижают давление ПМ до 5,0 кгс/см2.
К трубопроводам тормозных цилиндров подключены сигнализаторы отпуска тормозов (датчики-реле давления) СОТ1, СОТ2 типа Д250Б. Их контакты в цепи сигнальных ламп замыкаются при давлении в ТЦ более 0,4 кгс/см2.
Кран вспомогательного локомотивного тормоза КВТ включен по независимой схеме, для чего разобщительный кран 4 закрывают. Отпуск тормозов локомотива при заторможенном составе осуществляется кнопкой, расположенной на пульте машиниста. Нажатием этой кнопки подается питание на электропневматический вентиль ЭПВ2, который через дроссель (Др) вытекает воздух из рабочей камеры воздухораспределителя в тормозную магистраль. Для получения ступенчатого отпуска тормозов локомотива при заторможенном составе ВР должен быть включен на горный режим отпуска.
При торможении КВТ воздух из ПМ проходит в магистраль вспомогательного тормоза (МВТ) и далее через переключательный клапан № 3ПК поступает в управляющие камеры реле давления РД1 и РД2, которые, сработав на торможение, наполняют из питательного резервуара ТЦ обеих тележек.
При снижении давления в ТМ поездным краном машиниста КМ воздухораспределитель ВР срабатывает на торможение и через переключательный клапан № 3ПК сообщает ЗР с управляющими камерами реле давления РД1 и РД2, которые, в свою очередь наполняют из ПР тормозные цилиндры обеих тележек.
Торможение секций при их саморасцепе или при разъединении соединительных рукавов между секциями обеспечивается срабатыванием на торможение воздухораспределителя при падении давления в ТМ и дальнейшим наполнением ТЦ из питательного резервуара ПР, воздух из которого не может выйти в атмосферу, благодаря наличию обратного клапана КОЗ.
Конструктивные изменения внесены также и в систему пневматической синхронизации работы кранов машиниста. Магистраль синхронизации объединена с питательной магистралью и снабжена двумя разобщительными кранами 5 и 6, а вместо трехходового крана используется стоп-кран 7. Таким образом, при управлении тормозами соединенного поезда по системе синхронизации на локомотиве в середине состава концевой рукав питательной магистрали соединяют с тормозной магистралью хвостового вагона и открывают концевые краны. Разобщительный кран 6 перекрывают, кран 5 открывают, а ручку крана ~ устанавливают в положение синхронизации.
Включение КВТ по независимой схеме несколько изменило порядок подготовки тепловоза к следованию в холодном состоянии.
Для этого необходимо в обеих кабинах установить ручки КМ в положение экстренного торможения, а ручки КВТ в крайнее тормозное (VI) положение, выключить устройство блокировки тормозов БТ, установить комбинированный кран этого устройства в положение двойной тяги и перекрыть разобщительные краны на ЭПК. На каждой секции установить ВР на средний режим торможения и равнинный режим отпуска, перекрыть разобщительный кран 2 и открыть кран холодного резерва 1. Скоростемеры и пневматические цепи вспомогательных аппаратов должны быть отключены от источников сжатого воздуха соответствующими разобщительными кранами, концевые краны питательной магистрали закрыты, а соединительные рукава ПМ сняты.
После подготовки тепловоза к следованию в недействующем состоянии все ручки разобщительных кранов должны быть опломбированы.
Пневматическая схема тепловозов 2ТЭ116 последующих выпусков (рис. 2.8) с № 1540 дополнена блокировочным клапаном (БК), обеспечивающим самоторможение секций при саморасцепе. Установка блокировочного клапана обусловлена тем, что кран вспомогательного локомотивного тормоза на этих локомотивах включен по повторительной схеме. Вместо реле давления (повторителей) № 304 используются реле давления № 404.
Блокировочный клапан подключен к отводу ТМ через разобщительный кран 4 и соединен, с оной стороны, с импульсной магистралью ИМ, а с другой стороны, через переключательный клапан № 3ПК с управляющим камерам РД1 и РД2.
В случае снижения давления в тормозной магистрали ТМ до 2,7 – 2,9 кгс/см2 (например, при саморасцепе секций) срабатывает на торможение воздухораспределитель ВР и сообщает ЗР с импульсной магистралью. При этом блокировочный клапан БК открывает проход воздуха из ИМ через переключательный клапан № 3ПК в управляющие камеры реле давления РД1 и РД2. Реле давления, сработав на торможение, наполняют ТЦ обеих тележек воздухом из питательного резервуара ПР. Поскольку питательный резервуар соединен с ПМ через обратный клапан КО2, то при разъединении межсекционных рукавов воздух из ПР в атмосферу не уходит. Объем ПР позволяет обеспечить в ТЦ давление около 2,0 кгс/см2. Нормальная работа блокировочного клапана восстанавливается при повышении давления в тормозной магистрали более 3,0 кгс/см2.
Тепловозы 2ТЭ116 с реостатным тормозом дополнительно оборудованы редуктором давления № 348, отрегулированным на давление 2,0 – 2,2 кгс/см2 и установленным в пневматической цепи замещения реостатного тормоза, электроблокировочный клапаном, исключающим совместное действие электрического и пневматического тормоза, датчиком-реле давления, отключающим реостатный тормоз при давлении в ТЦ более 1,4 кгс/см2, а также электропневматическими вентилями блокировки тормоза и замещения тормоза.
Автосцепка.
При осмотре автосцепки необходимо проверить:
2.1 Действие автосцепки на саморасцеп, для чего правой рукой нажимаем замкодержатель и ставим его в рабочее положение т.е. на 18 - 20 мм от торцевой плоскости автосцепки. Левой рукой нажимаем на замок, который должен перемещаться в пределах 7-18 мм, но не должен полностью входить в карман автосцепки.
2.2 Проверяем положение замка: расстояние кромки малого зуба должно быть в пределах 2-8 мм.
2.3 Высота автосцепки должна быть 950 -1080 мм (грузового гружёного вагона 950 -1080 мм);
2.4 Провисание автосцепки допускается не более 10 мм, а возвышение не более 3 мм;
2.5 Расстояние между хвостовиком автосцепки и розеткой должно быть в пределах 25 - 40 мм;
2.6 Осмотреть нет ли трещин хвостовика, головки клина, тяговом хомуте, поддерживающей полочке, маятниковых болтов. Толщина клина должна быть не менее 30 мм, ширина не менее 89 мм (у вагона 87 мм);
2.7 После прицепки тепловоза к составу надо проверить надёжность сцепления автосцепок по сигнальном отростку и зуба замка, разницу центров автосцепок, которая должна быть не более100мм (для грузового груженого вагона тепловоза 110 мм).
Колёсные пары
При осмотре колёсных пар необходимо руководствоваться требованиями, изложенными в пунктах 10.1, 10.3 ПТЭ и инструкции МПС ЦТ 2306 по ремонту колесных пар запрещается выдавать под поезд тепловоза с колесными парами, имеющими хотя бы одну из следующих неисправностей:
1. Ослабление бандажа, признаками которого являются: глухой, дребезжащий звук при ударе молотком по бандажу или укрепляющему кольцу, скопление смазки ржавчина в местах посадки бандажа и кольца, проворот бандажа, контролируемый по контрольным рисункам (кернам).
2. Трещина на бандаже, оси, диска и ступницы коле са.
3. Раковины или выщербины на поверхности катания.
4. Местное увеличение ширины бандажа, наплыв более 5мм.
5. Прокат по кругу катания больше 7мм.
6. Толщина гребня более 33мм и менее 25мм.
7. Вертикальный подрез гребня, высотой более 18мм, измеряемый специальным шаблоном. 8. Ползун (выбоина) на поверхности катания более 1мм. При обнаружения в пути следования у вагона (кроме моторного у МВПС глубиной более 1мм но не более 2мм разрешается довести такой вагон без отцепки от поезда (пассажирских со скоростью не выше 100 км/ч, грузовой не свыше 70 км/ч) до ближайшего ПТО, имеющего средства для замены колёсных пар. При величине ползунов вагонов (кроме вагонов МВПС) от 2 до 6 мм, у локомотива моторного вагона МВПС от 1 до 2 мм допускается следование до ближайшей станции со скоростью 15 км/ч, а при величине ползуна соответственно свыше 6 мм до 12 мм и свыше 2 до 4 мм - со скоростью 10 км/ч где колёсная пара должна быть заменена. При ползуне свыше 12 мм у вагона и тендера свыше 4 мм у локомотива и вагона МВПС разрешается следовать со скоростью 10 км/ч при условиях вывешивания или исключений возможности вращения колесной пары. На стрелочных переводах скорость не должна превышать 3 км/ч, тормозные башмаки должны быть изъяты.. Глубина ползуна па поверхности бандажа колесной пары тепловоза определяется по следующий таблице:
- глубина ползуна 1 мм - длина 60 мм;
- глубина ползуна 1,5 мм - длина 75 мм;
- глубина ползуна 2 мм—длина 85 мм;
- глубина ползуна 3 мм - длина 100 мм.
Буксовый узел и моторно - осевые подшипники.
При осмотре буксового узла моторно - осевых под шипников проверьте:
1. надёжность крепления крышки поводков букс.
2. исправность гасителей колебании (нет ли трещин в местах приварки к раме).
3. буксы заправляются ЖРО (при полной заправке 2 кг, на ТР - 2 добавляется 0.2 кг).
В процессе эксплуатации регулярно проверяйте нагрев букс. При нормальной работе температура её наружных поверхностей не должна превышать температуру окружающего воздуха более чем на 30С. Максимальная температура наружных частей буксы не должна превышать 70С. Нагрев буксы считается выше нормального, если руку, положенную на корпус буксы тыльной стороны ладони невозможно удержать.
4. осмотреть крепление кожухов тяговой передачи МОП, наличие трещин, вытекание смазки.
5. систему смазывания МОП заправляют осевым маслом марок Л, 3 или С. Уровень масла в польстерных камерах должен быть по нижний кромке окна вкладыша (по верхней контрольной пробке), а в маслосборнике до верхней кромки заправочного отверстия. Всего заправляется 32 кг масла на 1 эл. двигатель.
Рессорное подвешивание и рычажная передача тормоза.
При осмотре рессорного подвешивания, рычажной тормозной передачи и других узлов экипажа проверьте:
1. отсутствие трещин пружин рессорного подвешивания и рамы тележки.
2. наличие шайб, шплинтов и предохранительных устройств.
3. прочность крепления тормозных колодок, рычагов, тяг с муфтами рычажной передачи тормоза.
4..выход штока тормозного цилиндра должен быть 55 -120 мм, а разность по сторонам одной колесной пары не более 5мм.
5. песочные трубы должны быть установлены по оси рельса и находиться от головки рельса на расстоянии 50 – 60 мм, 20 - 40 мм от бандажа.
6. тормозные колодки подлежат замене при наличии сквозных трещин, износа по толщине до 15мм, клиновидном износе, измеряемом на расстоянии 50мм от торца.
Тяговые электродвигатели и редукторы
Для предотвращения преждевременного выхода из строя ТЭД и увеличения их срока службы необходимо уделять внимание содержанию щеточного аппарата, коллектора, моторно - осевым и якорным подшипникам, сохранности изоляции обмоток, нормальной работы системы охлаждения.
1..Щетки и щеточный аппарат.
При осмотре щеточного аппарата необходимо проверить:
а) нет ли зависания (заедания) щетки в корпусе щеткодержателя прижимной палец пружины должен быть расположен по центру щетки. Щетки должны иметь прилегание к коллектору не менее 75 % рабочей поверхности;
б) зазор по толщине между щеткой и корпусом щеткодержателя должен быть не более 0,5 мм, по ширине -1 мм;
в) щетка считается негодной и подлежит замене при срабатывания до высоты 23 мм или наличии околов краёв более 15 % от площади рабочей поверхности;
г) крепление щеткодержателей на кронштейнах, исправность и чистоту изоляторов. Щеткодержатель должен располагаться от поверхности коллектора на расстоянии 2 -4мм, его перекос вдоль коллектора должен быть не более 1 мм;
д)состояние шунтов, их крепление в щетках, состояние пружин и их упругость, которая должна обеспечивать прижатие щетки с силой 4 - 5 кг.
2. Коллектор.
Коллектор является как бы зеркалом, по состоянию поверхности которого можно судить о нарушении нормального режима работы и наличие неисправности в электрической части машины. Исправный коллектор имеет глянцевую поверхность с фиолетовокрасным или каштановым оттенком.
При неудовлетворительном состоянии поверхность коллектора заметно отличается от нормальной. Наличие темного цвета побежалости говорит о допущенном перегреве коллектора большим током при трогании с места или следовании на подъёме длительное время со скоростью 23,5 км/час. В подобных случаях на коллекторе можно наблюдать прогары или коробление пластин, выплавление припоя в петушках.
При круговом огне и плохой коммутации происходит почернение рабочей поверхности коллектора с отложением копоти, следов оплавления и капель металла, прогар миканита между коллекторными пластинами, разрушение отдельных щеток, обгар шунтов. Кроме того, при осмотре коллектора и внутренних полостей электродвигателя надо проверить состояние бандажа, нет ли течи масла, воды, топлива через не плотность воздухоподводящих каналов, люков и попадания их на обмотки и коллектор.
3. Якорные подшипники.
Следить за состоянием якорных подшипников. Признаком ненормальной работы подшипника является повышенный нагрев, следствием чего проходит вытекание смазки во внутреннюю полость или по подшипниковому щиту. Ржавчина в местах крепления болтов подшипникового щита, ненормальный скрежет из-за разрушения подшипников обойм сепараторов, заклинивание колёсной пары, следить за наличием смазки ЖРО и своевременно добавлять.
4. Сохранность изоляции и обмоток
Изоляция обмоток должна быть в сухом и чистом состоянии, а поэтому:
а) не допускайте течи воды, топлива, масла на электродвигатели;
б) следить за наличием и дозаправки смазки СТП (летом марки Л, зимой марки 3 в количестве 5 кг) в тяговом редукторе. В эксплуатации контроль уровня смазки и её дозаправку производить через горловину, закрытую резьбовой пробкой. Уровень должен быть и по нижнему краю заправочной горловины;
в) следить за надёжностью закрытия крышек, люков уплотнений в воздухоподводящие каналах;
г) если один или несколько тяговых эл. двигателей перегреваются в работе надо проверить статический напор в коллекторных камерах, который должен быть не менее 160 мм вод. ст. при работе дизель - генераторной установки на 15 позиции контролера.
Эксплуатация тепловоза и его обслуживание в пути следования.
Прицепка локомотива к составу
3.1 Подъезжая к составу, машинист должен только из первой кабины, не доезжая 40 - 50 м до состава для предотвращения буксования при взятии поезда с места подать песок на рельсы.
3.2 Перед прицепкой к составу машинист должен оста новить тепловоз применением вспомогательного тормоза, на растояние 5 – 10 метров после чего подъезжать к составу со скоростью не более 3 км/час, так чтобы в момент соединения автосцепок обеспечить плавность сцепления.
3.3 После сцепления локомотива с составом до соединения рукавов тормозной магистрали машинист обязан проверить надёжность сцепления автосцепок между локомотивом и первым вагоном кратковременным движением локомотива от состава в грузовом поезде (в пассажирском не производить), после этого осуществить переход в рабочую кабину.
3.4 Помощник машиниста обязан после прицепки локомотива к составу продуть тормозную магистраль локомотива через концевой кран, соединить рукава, открыть концевые рукава вначале у локомотива, а затем у вагона.
3.5 Машинист после соединения тормозной магистрали между локомотивом и первым вагоном обязан лично проверить правильность этого соединения и надежность сцепления автосцепок по сигнальным отросткам замков, а также разницу по высоте между осями автосцепок..
3.6 После прицепки локомотива к составу с незаряженной тормозной магистралью необходимо до соедине ния концевых рукавов и открытия концевых кранов произвести торможение снижением давления в уравнительном резервуаре 1,5атм, а затем ручку крана пере вести в VI положение после чего машинист даёт сигнал помощнику машиниста соединить рукава и открыть концевые краны.
3.7 После соединения рукавов и открытия концевых рукавов между локомотивом и первым вагоном ручку крана машиниста перевести в 1 положение и выдержать её в этом положении до восстановления давления в уравнительном резервуаре 5,2 атм при прицепке к пассажирскому поезду и 6,8 атм при прицепке к грузовому поезду, после чего ручку крана машиниста перевести во 2-е положение.
3.8 Проверить плотность тормозной магистрали и опробовать автотормоза установленным порядком.
Трогание поезда с места.
3.9 Перед троганием с места дизель - генераторная установка должна быть прогрета с таким расчетом, чтобы температура воды и масла была в пределах 60 -70 С.
З..10 Машинист перед отправление поезда обязан ознакомиться по натурному листу с составом грузового и грузопассажирского поезда, наличием вагонов на роликовых потшипниках, занятых людьми, грузами отдельных категорий, требующих особой осторожности, а также открытого подвижного состава..
3.11 Проверить правильность заполнения выданного разрешения на занятие перегона, по выданному предупреждению ознакомиться с участками, имеющими ограничение скорости и другими особыми условиям) следование поезда, проверить фактическое тормозное нажатие по справке ВУ - 45 и правильность ее заполнения, номер хвостового вагона.
Дата добавления: 2016-01-05; просмотров: 59; Мы поможем в написании вашей работы! |
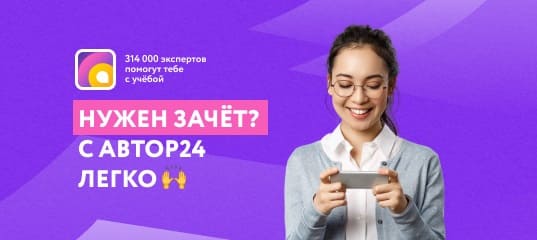
Мы поможем в написании ваших работ!