Теоретические аспекты менеджмента знаний.
Лекция 1. Теоретические аспекты менеджмента качества.
1. Роль менеджмента качества в современном менеджменте.
2 определение понятий качество и управления качеством.
3. Вклад Деминга в развитие менеджмента качества.
4. Принципы Деминга.
5. Вклад западных ученых в развитие менеджмента качества
6. Вклад японских ученых в развитие менеджмента качества.
7. Принципы всеобщего управления качеством.
Вопрос 1. Значение управления качеством заключается в том, что данная дисциплина стала одним из первых направлений в менеджменте, ориентированных на создание новой философии управления в условиях, когда принципы организации массового производства уже не обеспечивают требуемой эффективности. Для старой парадигмы управления, ориентированной на массовое производство стандартной продукции и разработанной Тейлором, Файолем, Мэйо и Маслоу, были характерны следующие основные элементы:
1. Предприятие это закрытая система, действующая в стабильных условиях.
2. Рост масштаба производства является главным фактором успеха и конкурентноспособности.
3. Рациональная организация производства, эффективное использование всех видов ресурсов и повышение производительности являются главными задачами управления.
4. Главный источник прибыли — производственный рабочий.
5. Система управления должна быть построена на контроле всех видов деятельности, функциональном разделении труда, нормах, стандартах и инструкциях.
|
|
Управление включает в себя следующие элементы:
1. Предприятие это открытая система, которая должна приспосабливаться к изменениям во внешней среде.
2.Повышение качества и удовлетворённости клиентов, скорость развития фирмы являются главными факторами успеха.
3. Скорость реакции на изменения во внешней среде и быстрота выполнения заказов являются главными задачами управления.
4. Главный источник прибыли — умение создавать новые знания и успешно использовать их на практике.
5. Система управления должна быть ориентирована на повышение роли организационной культуры, мотивацию работников и поощрение инноваций.
Иными словами, если в массовом производстве основными элементами, определяющими результаты деятельности организации, были люди, то в управлении качеством акцент делается на совершенствовании работы производственных систем с широким использованием знаний из таких областей, как математика, статистика, программирование......
Вопрос 2. Существуют различные подходы к определению понятий "качество" и "управление качеством". Деминг указывал, что качество можно определить только пользуясь системой оценок того человека, который использует товар и судит о качестве. Гарвин выделял 8 аспектов качества, среди которых: соответствие техническим требованиям, долговечность, надежность, эксплуатационные характеристики, конструктивные особенности, удобство обслуживания, эстетичность и ощущаемое качество. Джуран выделяет два аспекта качества: соответствие назначению и степень удовлетворённости потребителей. Харрингтон понимает под качеством удовлетворение ожиданий потребителя за цену, которую он себе может позволить, когда у него возникает потребность. Тагути понимает под качеством потери, нанесенные обществу с момента поставки продукта. С его точки зрения высокое качество предполагает минимизацию потерь. Согласно международному стандарту ISO под качеством понимается совокупность свойств объекта, относящихся к его способности удовлетворять установленные и предполагаемые потребности.
|
|
Согласно данному стандарту менеджмент качества рассматривается как скоординированная деятельность по руководству и управлению организацией применительно к качеству. В свою очередь менеджмент качества состоит из четырех элементов:
1. Планирование качества это часть менеджмента качества, направленная на установление целей в области качества и требуемых ресурсов для достижения целей.
|
|
2. Управление качеством это часть менеджмента качества, направленная на выполнение требований к качеству.
3. Обеспечение качества - это часть менеджмента качества, направленная на создание уверенности, что требования к качеству будут выполнены.
4. Улучшение качества - это часть менеджмента качества, направленная на увеличение способности выполнять требования к качеству.
Вопрос 3. Одним из наиболее известных ученых в области управления качеством является Уильям Эдвард Деминг. Американец по происхождению он впервые получил признание в Японии, где в 1951 году была учреждена премия его имени за качество и надежность продукции.
Деминг является одним из основоположников процессного подхода в менеджменте. Он считал, что любая работа — это процесс по трансформации сырья в готовую продукцию. Длительность пребывания фирмы на рынке определяются не полученной прибылью, а инновациями, исследованиями, обучением персонала и постоянным совершенствованием организации. Деминг утверждал, что человек должен черпать радость в труде, а задача лидеров совершенствовать характеристики людей и машин, улучшать качество, повышать производительность и одновременно воспитывать гордость за рабочее мастерство. Ученый был последователем Шухарта, предложившего использовать контрольные карты. С его точки зрения нужно было отделять общие причины вариации от специальных. Другими словами с помощью контрольных карт можно определить, есть ли в процессе конкретные источники, вызывающие брак, что позволит повысить качество до значения, определяемого существующим уровнем организации производства. Деминг разработал цикл PDCA. Основными элементами цикла являются:
|
|
P — разработка плана или стандарта для достижения поставленных целей ( определение целей и принятие решения о необходимых переменах)
D — реализация плана или выполнения стандарта ( осуществления перемен)
C — измерение и анализ результатов ( проверка)
A - проведение необходимых изменений, если результаты не отвечают первоначально запланированным или стандартизация действий в случае успеха.
Во многом благодаря деятельности Деминга Япония стала одним из лидеров в международном бизнесе. Последующая работа ученого и его сподвижников в США и других странах было попыткой изменить стиль западного менеджмента.
Подход Деминга, как и современные взгляды на проблему управления качеством концентрируется на потребителе. Он учил японцев рассматривать клиента как самую важную часть производственной цепи. Он указывал:
" Нам совершенно недостаточно иметь потребителя, который просто удовлетворён. Неудовлетворенный потребитель, конечно, уйдёт от нас. Но, к сожалению, удовлетворенный потребитель также может уйти от нас, полагая что не много потеряет, а зато может приобрести что-то лучшее. Прибыль в бизнесе проходит от постоянных потребителей, которые хвастаются вашим продуктом или услугой и которые приводят к вам своих друзей."
Вопрос 4. Наиболее полно взгляд Деминга отражены в его 14 принципах управления качеством:
1. Постоянство цели (непрерывное улучшение продукции и услуг при ориентации на долгосрочные цели и потребности).
2.Новая философия (необходимы коренные изменения в системе управления организациями).
3. Устраните потребность в массовых проверках и контроле ( необходимо улучшить работу организации, тогда не создающие добавленной ценности операции по контролю и, следовательно, значительные затраты на них будут устранены).
4. Отказ от выбора поставщиков на основе цены ( Необходимо стремиться к поставке деталей только от одного производителя. Низкая цена при низком качестве ведет к росту расходов фирмы и потере репутации. Детали от различных поставщиков ведут к росту вариации и необходимости переналадки оборудования, то есть к росту затрат)
5. Непрерывно улучшайте процессы ( результаты деятельности организации определяется качеством процессов)
6. Введите в практику подготовку и обучение персонала на рабочем месте ( необходимо, чтобы рабочие хорошо знали свою работу)
7. Учредите лидерство, направленное на помощь людям в наилучшем выполнение их работы (Лидер должен понимать особенности функционирования фирмы и подразделения и быть скорее тренером, мотивирующим подчинённых, чем судьей)
8. Изгоняйте страх (современный бизнес предполагает работу в условиях неопределенности, что связано с риском, поэтому работники не должны бояться экспериментировать)
9. Разрушайте барьеры между подразделениями и функциональными областями (Победа в современной конкуренции во многом обеспечивается посредством быстрой реакции фирмы на изменения рынка, поэтому все элементы организации должны координировать свою деятельность)
10. Откажитесь от пустых лозунгов и призывов ( Производительность и качество работы во многом зависят от характеристик машин и уровня организации производства. Рядовые работники, как правило, не могут оказать значительное влияние на результаты. Особенное раздражение вызывают призывы, не содержащие информацию о методах достижения целей)
11. Исключите произвольные количественные цели ( Формулировка цели не должна быть слишком детальной, чтобы не ограничивать инициативы. В условиях нестабильности цели скорее являются прогнозируемыми значениями, а не директивными показателями. Необходима система целей, учитывающих интересы других подразделений, а также клиентов и других партнеров фирмы).
12. Дайте сотрудникам гордиться своей работой. (Лучшие работники в условиях снижения качества обучения всегда в дефиците. Менеджеры должны если не сделать их счастливыми, то, по крайней мере, высоко удовлетворенными. В экономике знаний результаты деятельности работников определяются как произведение компетентности на мотивированность. Адаптация даже высококвалифицированных работников на новом предприятии ведет к значительному снижению производительности.
13. Пошощряйте стремление к образованию ( в экономике знаний побеждает тот, кто совершенствует свою деятельность быстрее).
14. Вовлеченность высшего руководства. (Коренные изменения деятельности организации вызывают сопротивление и их осуществление невозможно без поддержки высшего руководства. В условиях неопределенности качество высшего руководства во многом определяет результаты)
Вопрос 5. К представителям западной школы относят Джурана, считавшего, что 85 процентов недостатков в работе вызваны имеющейся системой организации производства, которая должна постоянно совершенствоваться. Для снижения уровня брака требуются значительные усилия со стороны высшего руководства.
Филипп Кросби руководил работой по качеству компании ITT и опубликовал книгу "качество бесплатно". Он разработал концепции "делай правильно с первого раза" и "ноль дефектов". Суть его подхода заключается в следующих утверждениях:
1. Качество означает соответствие требованиям
2. Качество достигается профилактикой, а не оценкой.
3. Стандарт качества - это отсутствие дефектов.
4. Измерителем качества являются потери от несоответствия требованиям.
Кросби разработал "решётку зрелости" управления качеством, позволяющую руководству оценить стадию развития фирмы с точки зрения менеджмента качества.
Фейгенбаум является основоположником концепции всеобщего контроля качества. Он выделяет четыре основных вида деятельности по контролю качества:
1. Контроль в процессе проектирования нового изделия
2. Входной контроль материалов
3. Контроль готовой продукции
4. Анализ специальных процессов
Вопрос 6. Развитие японской школы управления качеством связано с фамилиями Исикавы, Тагути, Синго и других. Однако её становление во многом обусловлено объективными факторами, а также американским и западноевропейским влиянием. Быстрое развитие управления качеством началась в Японии после поражения во Второй Мировой войне. Промышленность находилась в упадке, но американские оккупационные власти стали внедрять методики по управлению качеством, прежде всего в области управления телефонной связью. Исикава разработал причинно-следственную диаграмму, которая позволяет находить, сортировать и документировать причины снижения качества продукции. Он также разработал 7 инструментов контроля качества: контрольные листы, причинно-следственные диаграммы, диаграммы Парето, стратификацию, гистограммы, корреляционные диаграммы, контрольные карты Шухарта. Исикава также известен как пионер движения кружков качества в Японии ( первые кружки качества появились в пятидесятых годах прошлого века в США). В Японии под кружком качество понимается добровольная группа из 5-10 рабочих, которые регулярно собираются под руководством мастера или его помощника. Задачами кружков качества являются: содействие развитию предприятия; создание творческой и доброжелательной атмосферы на рабочем участке; всестороннее развитие способностей работников.
Еще одним известным японским ученым в области менеджмента качества являются Тагути. Его подход ориентирован в большей степени на организованную оптимизацию продукции и процессов до начала производства, чем на достижение качества посредством контроля. Основные элементы философии качества Тагути включает следующие положения:
1. Важнейшей мерой качества произведенного продукта являются суммарные потери для общества, порождаемые этим продуктом.
2. Чтобы в условиях конкурентной экономики оставаться в бизнесе, необходимы постоянное улучшение качества и снижения затрат.
3. Программа постоянного улучшения качества включает в себя непрерывное уменьшение отклонения рабочих характеристик продукта относительно заданных величин.
4. Потери потребителей, связанные с отклонениями при функционировании продукта, обычно приблизительно пропорциональны квадрату отклонений фактических характеристик от заданных значений.
5. Качество и стоимость готового продукта определяются в большей степени процессами его разработки и изготовления.
6. Отклонения в функционировании продукта или процесса могут быть снижены посредством использования нелинейных зависимостей рабочих характеристик от параметров продукта или процесса.
7. Для определения параметров продукта или процесса, влияющих на снижение отклонений при функционировании, могут использоваться статистически планируемые эксперименты.
Другим известным японским ученым является Сингo. Он разработал концепцию "пока - ека", позволяющую избежать непреднамеренных ошибок ( защита от дурака). Также ученый внес значительный вклад в разработку методов быстрой переналадки оборудования.
Для японской школы в области управления качеством характерны следующие элементы:
1. Ориентация на постоянное совершенствование.
2. Акцент на контроле качества процессов, а не качества продукции.
3. Создание необходимых условий для профилактики возможности появления дефектов.
4. Тщательное исследование и анализ возникающих проблем по принципу восходящего потока, то есть от последующей операции к предыдущей.
5. Полное закрепление ответственности за качество результатов за непосредственным исполнителем.
6. Развитие творческого потенциала работников, культивирование морали, что нормальному человеку стыдно плохо работать.
7. Ориентация прежде всего на качество, а не на кратковременную прибыль.
8. Управление качеством в общенациональном масштабе в течение длительного времени.
Различия в подходах японской и американской школ в области управления качеством отражены в таблице
1. Подход к качеству. Качество - это проблема фирмы. Качество - общенациональная проблема.
2. Цель управления качеством. Получение прибыли, сохранение и упрочение конкурентных позиций. Улучшение качества жизни.
3. Роль службы качества. Значительная. Низкая.
4. Роль высшего руководства. Организация и контроль за исполнением. Лидерство, активное участие.
5. Роль работников. Четкое следование инструкции. Постоянное самосовершенствование и саморазвитие, а также взаимное развитие.
6. Влияние на организационную культуру. Незначительное. Значительное, требующее перестройки сознания.
Сфера деятельности | Американский подход | Японский подход |
Подход к качеству. | Качество - это проблема фирмы. | Качество - общенациональная проблема. |
Цель управления качеством | Получение прибыли, сохранение и упрочение конкурентных позиций. | Улучшение качества жизни |
Роль службы качества. | Значительная. | Низкая. |
Роль высшего руководства. | Организация и контроль за исполнением. | Лидерство, активное участие. |
Роль работников. | Четкое следование инструкции. | Постоянное самосовершенствование и саморазвитие, а также взаимное развитие. |
Влияние на организационную культуру. | Незначительное. | Значительное, требующее перестройки сознания. |
Вопрос 7. Всеобщее управление качеством (TQM) - это подход к управлению организации, ориентированный на качество, предполагающий участие всех работников и направленный на достижение успехов в долгосрочной перспективе на основе удовлетворения требований клиентов и обеспечения выгоды для членов организации и общества. Выделяют от 5 до 17 принципов TQM. Рассмотрим 7 основных принципов TQM:
1. Ориентация организации на клиента. Организации создаются для выполнения работы, требуемой клиентам. Можно их разделить на внешних и внутренних. Внешних клиентов можно разделить на три группы:
А. Конечные пользователи, как правило, это физические лица.
B. Промежуточные, например оптовые торговцы.
С . Крупные и средние потребители ( организации и предприятия).
К внутренним пользователям относят представителей других подразделений организации. Необходим сбор информации о предпочтениях потребителей, так как их логика, как правило, значительно отличается. Для сбора информации могут использоваться опросы, наблюдение, эксперименты, анализ документов.
2. Роль руководства. Руководство должно быстро реагировать на изменения, учитывать интересы всех "акционеров" организации, определять долгосрочные перспективы развития, управлять организационной культурой, поощрять лучшее.
3. Вовлечение в улучшение качества сотрудников и поставщиков. Необходимо создать систему мотивации персонала, обеспечивающую их активную вовлеченность. Работники должны иметь правило принимать решения и нести за них ответственность. Необходимо обучение работников методам и инструментам улучшения качества. Деятельность поставщиков значительно влияет на качество. Лучшие предприятия устанавливают долгосрочные отношения с поставщиками и помогают им внедрять новые системы управления качеством. Как правило, имеет место покупка значительной доли акций поставщиков или участие в совместных проектах. В некоторых случаях представители потребителей контролируют качество продукции на предприятиях поставщиков.
4. Процессный подход. Под процессом понимается совокупность операций по достижению поставленной цели. Важность процессов в современных условиях вызвана необходимостью учета индивидуальных запросов клиентов. Всё чаще имеет место назначение владельцев процессов. Основными параметрами процесса являются издержки, сроки выполнения, уровень обслуживания, уровень качества.
5. Постоянное совершенствование. В условиях усиления конкуренции простое выживание предприятия предполагает осуществление значительных затрат на улучшение своей работы. Цель жизни человека - стремление к совершенству. Выделяют два типа улучшений:
А. Значительные (кайрио) требуют больших инвестиций и, как правило, работы нескольких специалистов.
Б. Серия малых улучшений (кайдзен) требует небольших инвестиций и вовлечения почти всего персонала.
Необходимо создание системы сбора предложений, которая обеспечит быструю реакцию, доброжелательное отношение к инноваторам, вознаграждение в той или иной форме.
6. Принятие решений, основанное на фактах. Большинство инноваций терпит неудачу из-за ошибочного представления о предпочтениях клиентов. Необходимо разработать методики исследования, обеспечивающие сбор достоверной информации, и внедрить ответственность за низкие результаты.
7. Установление длительных и взаимовыгодных отношений с клиентами, сотрудниками и поставщиками. Недостаточный уровень качества государственных услуг вынуждает корпорации создавать собственные учебные подразделения и даже корпоративные университеты. Однако инвестиции в обучение персонала имеют смысл лишь в случае низкой текучести кадров. В ином случае фирма будет просто дотировать конкурентов. Для наиболее способных сотрудников применяется система "пожизненного найма", когда зарплата повышается по мере увеличения срока работы на предприятии ( при отсутствии грубых проступков). Если предприятие становится поставщиком фирмы Тойота, то оно получает доступ к консультационным услугам, выгода от результатов которых распределеются между фирмами. Как правило, контракт заключается на поставку деталей для данного вида модели автомобиля, хотя в конкурсе участвуют несколько поставщиков.
ЛЕКЦИЯ 2. ПРОСТЫЕ ИНСТРУМЕНТЫ КОНТРОЛЯ КАЧЕСТВА
1 .Возникновение простых инструментов контроля качества.
2.Контрольный листок.
3. Гистограмма.
4.Диаграмма разброса.
5.Расслоение и стратификация данных.
6.Графики.
7.Диаграмма Парето.
8.Причинно-следственная диаграмма.
9.Диаграмма потока.
Вопрос 1. Первым начал использовать простые инструменты контроля качества ученый из США У. Шухарт, создавший контрольную карту. Так как в Японии успешно развивались кружки качества, к деятельности которых широко привлекали рабочих, то японские специалисты отобрали 7 методик, не требовавших особых знаний. Количество методик увеличилось, и они были названы "простыми инструментами контроля качества". К данным инструментам относятся:
1 .Контрольные карты.
2.Контрольный листок.
3. Гистограмма.
4.Диаграмма разброса.
5.Расслоение и стратификация данных.
6.Графики.
7.Диаграмма Парето.
8.Причинно-следственная диаграмма.
9.Диаграмма потока.
Вышеуказанные инструменты применяются для того, чтобы найти отклонения от требуемых значений и выявить их причины. Как правило данные для контроля качества могут быть получены на основе анализа хозяйственной деятельности и изучения документации ,Однако полученная информация требует дополнительной трансформации. При определении отклонений применяются контрольной карты и диограммы.
Факторы, являющиеся причиной отклонения могут быть найдены с помощью стратификации, диаграммы разброса, причинно-следственной диаграммы, диаграммы Парето.
Вопрос 2. С целью регистрации данных и их систематизации применяется контрольный листок, как правило имеющий вид графика или таблицы. Данный инструмент позволяет выявить информацию о количественных и качественных параметрах наблюдаемых процессов и явлений. Кане с соавторами выделяют следующие правила разработки и использования контрольных листков:
1. Необходимо установить суть проблемы, которую нужно решить.
2.Следует разработать форму контрольного листка, позволяющего с минимальными затратами времени и средств получить достоверную информацию о процессе.
3 Необходимо разработать методику измерений, исключающую получение данных, которые не могут быть использованы для анализа.
4. Следует выбрать сборщика данных, имеющего информацию о процессе и не заинтересованного в ее искажении.
5. Необходимо обучение сборщиков данных.
6 Средства и методы измерения должны обеспечивать требуемую точность.
7. Следует осуществлять постоянный мониторинг сбора данных и периодически корректировать данный процесс.
Вопрос 3. Гистограмма представляют собой столбчатый график, который отражает распределение значений показателя в выборке. При разработке программы определяются результаты измерений. Затем определяют максимальное и минимальное значение в выборке. Разницу между ними разбивают на Z интервалов. С точки зрения Кане с соавторами,
Z= квадратному корню из N, где N - объем выборки.
Чаще всего этот параметр находится в пределах от 7 до 11. Затем определяется абсолютное число наблюдений попадающих в каждый интервал. На основе полученной информации строят гистограмму, с помощью которой можно осуществить предварительный анализ процесса. При колоколообразном распределении имеет место симметричность расположения данных.Отклонение от данной формы свидетельствует о наличии преобладающих факторов или ошибках в методике сбора данных. Наличие двух пиков в распределении свидетельствует об объединении результатов работы двух и более процессов или наличии различных условий в работе. При скошенном распределении, когда пик находится не в середине, имеет место значительное влияние конкретного фактора.
Вопрос 4. Диаграммы разброса используются для определения характера взаимосвязи между двумя переменными без применения математических моделей посредством построения соответствующих графиков. После сбора данных (25-30 пар данных) заполняют таблицу. Затем удаляют попарно значительно отличающиеся результаты. На основе нахождения максимальных и минимальных значений каждой из переменных строят оси ординат и абсцисс, выбрав требуемый масштаб. Потом отображают на графике имеющиеся точки. На основе построенного графика пытаются определить характер взаимосвязи между переменными.
Вопрос 5. Стратификация или расслоение данных применяется для нахождения причин возникновения проблем либо факторов, влияющих на целевую переменную. Расслоение может осуществляться по ряду признаков:
1. Оборудование ( вид, длительность работы, износ ...)
2. Люди ( пол, опыт работы, работник, квалификация ...)
3. Условия работы ( давление, температура, дата, начало смены, день недели, период года, время ...)
4. Материалы ( поставщик, сорт, номер заказа...)
Чаще всего используются три способа стратификации:
1. При табличном результаты работы в разных условиях заносятся в отдельные таблицы и сравниваются между собой.
2. При графическом результаты наносятся на график, где указаны зоны для каждого из анализируемых факторов.
3. При дисперсионном определяют долю дисперсии результатов для конкретного условия к общей дисперсии.
Вопрос 6. Значительная часть людей для понимания проблемы нуждается в её графическом представлении. Для облегчения процесса восприятия могут использоваться следующие виды графиков: в виде ломаной линии, столбчатые, круговые, ленточные.
Вопрос 7. Использование диаграммы Парето позволяет определить факторы, оказывающие наиболее сильное влияние на переменную. Парето в 1897 году определил, что 80% богатства контролирует 20% населения. Затем оказалось что подобная пропорция характерна для большого количества ситуаций. При построении диаграммы Парето осуществляются следующие действия:
1. Собирают данные и определяют влияние каждого фактора на результирующую переменную.
2. Располагают факторы в порядке убывания их влияния на переменную.
3. Определяют кумулятивную сумму влияния факторов, начиная с факторов, имеющих наибольшее влияние.
4. Находят факторы, влияние которых на переменную составляет более 80%.
Вопрос 8. Причинно-следственная диаграмма применяется с целью определения и классификации причин, влияющих на конечный результат. Как правило, данную диаграмму лучше строить на основе применения методики "мозгового штурма". Как правило чаще всего выделяют следующие разделы: материалы , методы, люди, внешняя среда, машины, измерения.
Вопрос 9. Диаграмма потока строится с целью отображения последовательности основных операций процесса. В целом ряде случаев возможно отражение нескольких уровней, указывающих на выполнение операций отдельными работниками или подразделениями. Для акцентирования внимания на схожих типах операций могут использоваться различные символы ( ромбы, треугольники, овалы ...)
ЛЕКЦИЯ. 3 7 НОВЫХ ИНСТРУМЕНТОВ КОНТРОЛЯ КАЧЕСТВА.
1.Особенности новых инструментов контроля качества
2. Диаграмма сродства
3. Диаграмма взаимосвязи
4. Прочие новые инструменты контроля качества.
Вопрос 1. Хотя простые инструменты контроля качества и позволяют решить около 95% имеющихся проблем, но они в основном направлены на анализ количественных данных. Для решения проблем, имеющих качественный характер, были разработаны 7 новых инструментов контроля качества. Сбор данных в этом случае, как правило, осуществляется с использованием методики "мозгового штурма с применением высококвалифицированных специалистов. К новым инструментам относятся:
1. Диаграмма сродства.
2. Диаграмма взаимосвязей.
3. Древовидная диаграмма.
4. Матричная диаграмма.
5. Стрелочная диаграмма.
6. Диаграмма планирования осуществления процессов.
7. Матрица приоритетов.
Вопрос 2. Диаграмма сродства используется для классификации идей на группы. Её строят на основе результатов мозгового штурма или анализа какой-либо проблемы. Построение диаграммы сродства обычно производят в следующей последовательности:
1. Составляют перечень идей, записывают их на самоклеющихся листках бумаги, прикрепляют к большой доске, которая доступна для обозрения всем членам команды
2. Систематизируют идеи, имеющие общую направленность, по группам. Эту работу выполняют без дискуссий.
3. Если имеется сходство между некоторыми группами, их можно объединить в одну большую группу. На этом этапе в процессе общей дискуссии согласуется состав групп, некоторые идеи переформулируются, объединяются или дифференцируются
Вопрос 3. Диаграмма взаимосвязей предназначена для ранжирования родственных факторов по силе связей между ними. Она дает возможность сгруппировать переменные по признаку внутренней общности и выявить наиболее приоритетные факторы. Выводы при этом делаются на основе экспертных оценок в процессе мозгового штурма.
Рекомендуется следующий порядок построения диаграммы взаимосвязей:
1. Запишите каждую проблему на отдельном самоклеющемся листке и прикрепите листки по кругу на доске.
2. Начните с верхнего листка и, двигаясь по часовой стрелке, задавайте вопрос:"Имеется ли между этими двумя событиями связь." При наличии связи задайте следующий вопрос:"Какое событие вызывает другое или является причиной возникновения другого события".
3. Нарисуйте стрелку между двумя событиями, показывая направление влияния.
4. После выявления взаимосвязей между всеми событиями посчитайте число стрелок, исходящих из каждого события и входящих в каждое событие.
События с наибольшим числом исходящих ссылок является исходным. Команда обычно выделяет два или три исходных события, которые она должна обсудить, чтобы решить на каком из них следует сконцентрировать усилия в первую очередь. При этом могут учитываться такие факторы как например имеющиеся у организации ограничения, ресурсы, опыт.
Вопрос 4. С помощью древовидной диаграммы ищут методы решения проблемы и обеспечения требуемых характеристик продукции. При поиске причин возникновения проблемы используют метод "5 Почему". Участники команды, которая занимается решением проблемы задают вопрос: " Почему она возникла". После этого получают список причин первого уровня. Затем задают тот же вопрос для каждой из причин первого уровня и получают список причин второго уровня. Данную процедуру повторяют несколько раз. Взаимосвязи между проблемой и причинами различного уровня изображают в виде многоступенчатой древовидной структуры.
Матричная диаграмма позволяет наглядно представить взаимосвязи между различными факторами а также отобразит силу этих связей. Как правило применяются различные виды диаграмм для случаев, когда имеют место взаимосвязи между двумя 2,3 и 4 группами факторов.
Стрелочная диаграмма используется для облегчения разработки и контроля план работ на основе повышения его наглядности. Наиболее известными стрелочными диаграммами являются диаграмма Ганта и различные виды сетевых графиков.
Стрелочная диаграмма применяется для планирования и контроля сравнительно простых процессов, а диаграмма планирования осуществления процесса используется для планирования и оценки сроков выполнения сложных процессов в области научных исследований, производства новой продукции , решение задач менеджмента со многими неизвестными, когда необходимо предусмотреть различные варианты решений и возможность корректировки программы работ.
Матрица приоритетов предназначена для выявления факторов ,которые оказывают наибольшее влияние на целевые переменные. В данном случае используется многофакторный анализ большого числа данных. Данный метод требует знания математической статистики и применения вычислительной техники, поэтому он применяется гораздо более редко, чем предыдущие шесть методов.
ЛЕКЦИЯ. 4.СТРУКТУРИРОВАНИЕ ФУНКЦИИ КАЧЕСТВА.
1. Особенности применения структурирования функции качества.
2. Этапы СФК
Вопрос 1. Целью СФК является обеспечение учета запросов клиентов при создании товаров и разработке технологического процесса производства, что к значительному снижению затрат. Как правило клиенты предъявляют требования, которые носят качественный характер, а для производителя необходимо определить количественные показатели товара и процесса, обеспечивающие высокий уровень удовлетворенности потребителей. Для данных целей и предназначена СФК. Методику СФК можно применять при планировании продукта, его проектировании, разработке параметров технологического процесса, организации производства. Построение СФК предполагает выполнение следующих действий:
1. Уточнение требований потребителей и степени важности отдельных характеристик.
2. Перевод требований клиентов в технические характеристики продукта.
3. Определение силы связи между характеристиками товара предпочтениями клиентов.
4. Выбор значений параметров характеристик продукта, которые обеспечат удовлетворенность клиентов.
Выделяют 4 стадии СФК: планирование продукта, проектирование продукта, проектирование процесса, проектирование производства.
Вопрос 2. Рассмотрим методику на стадии планирования продукта. На первом этапе происходит определение потребительских требований к новой продукции. Нужно определить основные сегменты рынка, на которые будет направлен продукт, а также основные характеристики клиентов. Затем проводится опрос с использованием открытых вопросов с целью составления списка потребительских требований к новому продукту, которой может составлять несколько сотен элементов. На втором этапе имеет место ранжирование потребительских требований, что позволит установить приоритеты в работе. Клиентов опрашивают повторно и предлагают определить важность каждого потребительского требования по шкале в 10 баллов. На третьем этапе специалисты по созданию продукции на основе потребительских требований разрабатывают список наиболее важных инженерных характеристик. Это позволит обеспечить требования клиентов. На четвертом этапе происходит оценка степени тесноты парных взаимосвязей между требованиями потребителей и инженерными характеристиками. Связь может быть сильной (9 баллов), средней (3 балла), слабой (1 балл). На пятом этапе определяют характер взаимосвязей между инженерными характеристиками, что отражается на "крыше" дома качества. Данные взаимосвязи могут быть как положительными, так и отрицательными. На шестом этапе определяется абсолютная важность инженерной характеристики путем умножения силы связи на важность для клиентов потребительского требования. Относительная важность определяется в процентах как доля важности каждой инженерной характеристики в абсолютном объеме. Но седьмом этапе специалисты определяют технические и экономические трудности изменения инженерной характеристики в нужном направлении, что отражается в "подвале" СФК. На восьмом этапе определяются целевые значения инженерных характеристик, которые затем сравниваются с инженерными характеристиками существующих продуктов фирмы, а также со значениями инженерных характеристик продукции фирм - конкурентов.
ЛЕКЦИЯ 5. Концепции бережливого производства
ВОПРОС 1 История формирования концепции бережливого производства
Основателем концепции бережливого производства считается Тайити Оно, начавший работу в Toyota Motor Co в 1943 году. В 1945 году Япония проиграла войну, и, чтобы выжить в условиях экономического спада и остаться передовой державой, необходимо было применить огромные интеллектуальные усилия. В то время безусловным лидером автомобильной промышленности была Америка. Десятилетиями Америка снижала издержки за счет наращивания массовости производства и уменьшения номенклатуры выпускаемых моделей автомобилей. Этот американский стиль - массовое производство - эффективно использовался во многих отраслях.
В то время президент автомобильной компании Toyota Motor Co («Тойота мотор компани») Тойода Кийтиро сказал: «Необходимо догнать Америку за три года. В противном случае автомобильная промышленность Японии не выживет». Японцы поняли: чтобы догнать Америку, нужно разработать свою собственную систему производства, отличную от традиционной американской системы массового производства. И это удалось компании «Тойота». В течение нескольких десятков лет автомобильная корпорация создавала свою систему управления, интегрируя лучшую мировую практику. Один из основателей нового подхода к организации производства в корпорации «Тойота», Таити Оно, в 1950 годах побывал в США и познакомился с неизвестным тогда в Японии каналом продаж — супермаркетами. На фоне огромного спроса гигантские магазины с большим запасом товаров были рентабельными. Сравнив ситуацию с Японией, где уровень спроса находился на гораздо более низком уровне, он пришел к выводу, что понижение себестоимости производимой на японских заводах продукции посредством эффекта большого масштаба недостижимо. Выход был найден и реализован — производство на заводах «Тойота» должно основываться не на планируемых объемах продаж (стратегия выталкивания), а на реальном спросе (стратегия вытягивания).
Достигалось это не увеличением закупок металла для автомобилей, не расширением производственных площадей и набором кадров, не усиленным налаживанием массового производства. Компания «Тойота» достигла успехов, сломав принятый во всем мире американский стереотип системы массового производства и организовав выпуск широкой номенклатуры моделей автомобилей небольшими партиями по совершенно новой, изобретенной сотрудниками «Тойоты» системе.
Идеологическая основа (Toyota Production System, TPS) -стремление к постоянному совершенствованию, постепенным, но непрерывным улучшениям. Цель — устранить любые потери, которые увеличивают затраты, не создавая добавленной ценности.
Ключевым в философии Toyota Production System является опора на человеческий фактор и, упрощенно говоря, командная работа, формирование атмосферы взаимопомощи.
По мере увеличения доли мирового рынка производственная система «Тойота» (ПСТ) стала предметом изучения и западных экономистов. Взяв ПСТ за основу, Джон Крафчик в 1988 году и вслед за ним Дэниэл Джонс и Джеймс Вумек в 1990 году развили концепцию «бережливое производство». В оригинале это название звучит как «Lean production», где английское слово «lean» означает «тощий, худой» (оптимист сказал бы «стройный»), но переводчики выбрали в русском варианте «бережливый». Безусловно, так звучит лучше. Дело в том, что основной задачей этой стратегии было избавление процесса производства от всех ненужных, неоправданных, лишних затрат и потерь. Наверное, авторы термина «lean» обладали чувством юмора и сравнили неэффективное производство с чрезмерно упитанным человеком. Как человек по совету врачей может похудеть и стать тощим, так и производство под управлением опытных менеджеров может избавиться от ненужных операций и стать эффективным.
Японцы раньше всех осознали выгодность и перспективность такого подхода, в полной мере проявленного корпорацией «Тойота» и другими ведущими японскими предприятиями. Концепция массового производства, господствовавшая в США и во всем «цивилизованном» мире, проиграла в новых условиях. Конкуренцию выдержали те компании, которые перешли от массового производства к бережливому, которое отличают гибкость и способность быстрее реагировать на то, что необходимо для удовлетворения потребностей конкретного покупателя. Изначальное кустарное и сменившее его массовое уступает место бережливому производству. Иными словами, за счёт организации бережливого производства можно производить лучшую продукцию за меньшее время, затрачивая при этом меньше усилий и ресурсов. Основной инструмент — сокращение потерь на каждом этапе производства.
Сначала концепция на Западе и в Японии применяли в отраслях с дискретным производством, прежде всего в автомобилестроении. Затем концепция была адаптирована к условиям непрерывного производства, а потом в торговле, сфере услуг, коммунальном хозяйстве, здравоохранении, вооруженных силах и государственном секторе. Привлекательность ее в том, что система на 80% состоит из организационных мер и только на 20% из инвестиций в технологию.
Постепенно бережливое производство превращается в международную философию менеджмента. Оно воздействует не только на само предприятие или организацию, но и на ее клиентов и поставщиков, постепенно распространяясь на все общество. Этому немало способствуют регулярные международные и региональные конференции, многие из которых проводятся по инициативе Lean Enterprise Institute (США) и Lean Enterprise Academy (Англия).
ВОПРОС 2. Принципы бережливого производства
Мировая экономика находится в состоянии состояния кризиса, угрожающего значительными социальными потрясениями. Во многом сложившаяся ситуация вызвана неадекватностью применяемых принципов менеджмента условиям в которых приходится функционировать современным предприятия. Из существующих подходов к управлению предприятиями наиболее приближенной к современной ситуации является концепция «бережливого производства». Бережливое (Lean) производство представляет собой методологию улучшения операций, главная цель которой - минимизировать затраченные ресурсы, максимизировать выпуск продукции. Обычно это достигается за счет рационализации и оптимизации процессов, повышения культуры и навыков сотрудников, эффективного управления материальными потоками, улучшения дисциплины и прочего. Бережливое производство ориентировано на то, чтобы в нужное время нужные ресурсы попадали в нужное место в нужном количестве для достижения идеального потока работы, при одновременном сведении к минимуму отходов. Менеджмент бережливого производства также ориентирован на выявление потребностей рынка и создание максимальной ценности для клиента при минимальных затратах ресурсов. Отправной точкой применения бережливого производства является потребительская ценность в значении полезность, которая присуща продукту с точки зрения покупателя. Ценность каждого продукта складывается из ряда последовательных действий, выполняемых производителем. «Сердцем» системы бережливого производства называют процесс устранения потерь. И под потерями в данном случае понимают любое действие, потребляющее ресурсы, но при этом не создающее ценности для покупателя. В японском языке есть слово муда. Оно обозначает потери, отходы, или любую деятельность, потребляющую ресурсы и не создающую при этом ценности. Скажем, потребителю совершенно не важно, лежал ли готовый продукт или его детали на складе или нет. А при традиционной системе управления все складские издержки, расходы по переделке, браку, и другим косвенным издержкам оплачивает потребитель. Концепция бережливого производства в том, чтобы разделить производственные процессы на две группы: деятельность, добавляющая ценности для потребителя, и деятельность, не добавляющая этой ценности. И далее начинается работа по ликвидации всех процессов второго типа.
В связи с недостаточным объемом информации бережливое производство (БП) иногда представляют как японскую философию, примененную к организации производства. Под БП следует понимать методологию, обеспечивающую работникам на всех уровнях организации получение навыков и знаний, которые позволяют им целенаправленно и систематически устранять бесполезные расходы (БР), улучшая взаимодействие и ускоряя движение заказов и деталей внутри цепи поставок. Устраняя БР, мы можем одновременно снижать затраты, более эффективно использовать ресурсы и обеспечивать лучшую ценность для потребителей. В БП под БР понимают любую деятельность, которая потребляет ресурсы, но не создает ценность. Тайучи Оно выделяет семь видов БР:
1) Ожидание как ресурсов, так и распоряжений.
2) Использование несоответствующего оборудования.
3) Перепроизводство, связанное как с наличием излишних запасов предметов труда, так и со стремлением полностью использовать имеющиеся ресурсы.
4) Брак, включающий отходы, затраты на исправление дефектов, ошибки в оформлении документов.
5) Излишние перемещения, вызванные плохим размещением рабочих мест.
6) Излишние запасы готовой продукции и размеры передаточных партий.
7) Излишние операции по складированию.
Выделяют также восьмой вид БР – проектирование товаров и услуг, которые не пользуются спросом. Неиспользуемый человеческий потенциал можно рассматривать как девятый вид БР. В обычном процессе БР или не добавляющие ценность операции составляют, иногда, более 95% от всех расходов. Традиционно специалисты концентрируют внимание на повышении производительности работников и тому подобное, то есть на 5% добавляющих ценность операциях.
Выделяют 5 принципов БП:
1) Конкретизируйте ценность, обеспечиваемую продуктом. Определите, что в действительности желает потребитель. Если вы не желаете платить за чужую расточительность, то почему то должен делать наш клиент.
2) Определите поток ценности. Как конкретно функционируют ваши процессы по проектированию, материально-техническому обеспечению, производству, распределению, продажам, обслуживанию в целях обеспечения удовлетворенности потребителей. Каковы характеристики вышеназванных процессов, где имеют место БР?
3) Обеспечьте непрерывное движение продуктов и заказов через систему. Имеют ли место очереди и пролеживание деталей в вашей производственной (обслуживающей) системе? Имеются ли узкие места? Сбалансированы ли отдельные операции в соответствии с тактом процесса? При наличии вышеназванных проблем их надо устранять, стремясь снизить размер передаточной партии в идеале до одной детали, а объем производства до объема продаж на определенный период.
4) Внедрите тянущую производственную систему. Производите только то, что требует потребитель и когда он требует.
5) Стремитесь к совершенству. Совершенство означает полное устранение БР, когда осуществляется только та деятельность, которая создает ценность для потребителя. Методики по непрерывному улучшению качества продукции основываются на непримиримости с сохранением сложившейся ситуации.
ВОПРОС 3. Инструменты бережливого производства
.
Бережливое производство насчитывает много методов, но наиболее популярными и часто применяемыми инструментами являются следующие:
1. Картирование потока создания ценности, или VSM (Value Stream Mapping);
2. Вытягивающее поточное производство;
3. Кайдзен;
4. Канбан;
5. Система всеобщего ухода за оборудованием, или TPM (Total Productive Maintenance);
6. Система выполнения работ точно в срок, или JIT (Just-In-Time);
7. Система быстрой переналадки оборудования, или SMED (Single Minute Exchenge of Dies);
8. U-образные ячейки;
9. Визуализация;
10. Система 5С
11. Система «Пока - ёкэ» (яп. «защита от ошибки», «защита от дурака») -.
Картирование потока создания ценности, или Value Stream Mapping - это метод, представляющий собой создание достаточно простой и наглядной графической схемы, на которой изображены все материальные и информационные потоки, которые должны осуществиться до получения продукта или услуги конечному потребителю. Карта потока создания ценности позволяет заметить слабые места в потоке, и на основе проделанного анализа оценить все ненужные затраты и процессы и по возможности ликвидировать их.
Картирование потока создания ценности состоит из следующих этапов:
1 этап: документирование карты настоящего состояния.
2 этап: анализ производственного потока.
3 этап: подготовка карты будущего состояния.
4 этап: разработка плана по ликвидации слабых мест ».
Традиционный подход описывает компанию как иерархическую, функциональную структуру, и если мы посмотрим на нее, то увидим своеобразный лабиринт, а оценить эффективность его функционирования достаточно сложно, а иногда и вовсе невозможно. И компании становится нужна своеобразная нить Ариадны, которая помогла бы связать все звенья производственной цепи по созданию конечного продукта в единую картину. Такой нитью является процессный подход к описанию деятельности компании. Процессом называется определённая логическая взаимосвязь действий для получения конечного продукта или услуги. И представить себе полную картину этих действий, то есть одновременно увидеть их невозможно.
Поэтому в системе бережливого производства есть инструмент, который дает возможность создать наглядное описание процессов с учётом их взаимосвязи. Таким инструментом является карта потока создания ценности, или VSM (англ. Value Stream Map).
«Картой потока создания ценности называют достаточно простую наглядную графическую схему, изображающую все базисные показатели и их взаимосвязь в материальных и информационных потоках в связи с производством товара или услуги. Использование этого инструмента, VSM – один из ключевых моментов в концепции «бережливого производства». В первую очередь, карта потока создания ценности показывает то, что видит клиент, и позволяет оценить весь поток создания ценности для конечного потребителя, а также отдельные процессы.
Следующим инструментом, который мы рассмотрим, будет вытягивающее поточное производство.
«Вытягивающее поточное производство (от англ. pull production) - это инструмент организации производства, представляющий из себя схему, в которой объём продукции на каждом отдельном этапе производства определяются исключительно потребностями последующих этапов, и на конечном этапе - потребностями потребителя.
Идеальным вариантом данной схемы является так называемый «поток в одно изделие» (англ. «single piece flow»). В этом случае поставщик, который находится выше по потоку, производит свой продукт лишь тогда, когда потребитель, ему сообщит об этом. Получается, что каждая последующая операция в схеме «вытягивает» продукцию из предыдущей.
Особое место в концепции бережливого производства занимает такой инструмент как кайдзен. Некоторые авторы считают, что кайдзен даже претендует на звание концепции эффективного управления на производстве.
Сам термин «кайдзен» является составным из двух слов: «изменения» и «хорошо». Обычно он переводится как «изменения к лучшему» или же «непрерывное улучшение».
Идея кайдзен была сформулирована в 1950 году У. Демингом. А после того, как введение данного инструмента стало приносить весомые преимущества японским компаниям, в 1960 году У. Деминг был награжден медалью самим императором Японии.
Преимущества системы кайдзен уже давно применяются во всех отраслях промышленности и не только, во всех областях, где необходимо создать условия для лучшей эффективности и производительности.
Кайдзен - японская философия, заключающаяся в постоянных изменениях для того, чтобы повысить производительность труда. Это убеждение, что только положительные изменения способствуют прогрессу. Упор в данном случае делается на улучшение производительности за счет бессмысленной работы.
Ниже рассмотрим, в чем же заключаются преимущества системы Кайдзен:
1. Сокращение потерь.
Первым и самым главным преимуществом внедрения принципов Кайдзен в производство можно назвать то, что он в значительной степени снижает потери в каждом производственном процессе. Система Кайдзен предполагает активное включение в себя каждого сотрудника. Это дает возможность получать комментарии и предложения об улучшении процесса производства со всех уровней управления. Очевидно, что это очень помогает минимизировать потери ресурсов.
2. Немедленное устранение неисправностей.
Еще одно преимущество, устранение проблем компании каждым работником помогает в быстром их решении. Неравнодушное отношение персонала позволяет быстро реагировать на неисправности и устранять их. Оперативное устранение неполадок уменьшает срок выполнения производственных циклов и делает производство более эффективным.
3. Оптимальное использование.
Система экономит ресурсы компании за счет быстрого решения проблем, а значит, они могут быть направлены на достижения других целей и усовершенствований. Таким образом, система гарантирует непрерывное совершенствование.
4. Улучшенная работа в команде.
Система Кайдзен развивает связи в команде. Когда коллектив не равнодушен, и все разбираются с проблемами сообща и успешно, это укрепляет командный дух компании. Коллеги меньше конфликтуют между собой и учатся больше доверять другим работникам с разных уровней иерархии. Все это благотворно сказывается на командной работе, а также на обеспечении бесперебойной качественно сделанной работы.
5. Лучшее качество.
Вследствие применения системы Кайдзен качество неизменно улучшается. Когда неполадки быстро и хорошо устраняются, работа в команде налажена, это благотворно влияет и на качество. А повышение качества выводит компанию на совершенно новый уровень.
Следующий инструмент «бережливого производства», который мы рассмотрим – это канбан.
Канбан – термин, произошедший от японского слова, обозначающего «сигнал» или «карточка». Этот метод используется для того, чтобы вытягивать продукты и материалы на бережливые производственные линии.
Существует не один вариант системы «Канбан»: в зависимости от применения различают двухбункерный канбан(однокарточный), многокарточный канбан, запускающий предыдущий процесс, канбан однократного использования и другие варианты.
Эта система дает возможность оптимизировать всю цепочку планирования производственных операций, на различных этапах: прогнозирование спроса, построение плана производственных заданий, балансировка и распределение этих заданий по производственным мощностям, а также оптимизация их загрузки. Под оптимизацией в данном случае понимается применение нескольких принципов: не делать лишних действий, не делать их преждевременно, всегда сообщать о возникающей потребности именно в момент необходимости».
Следующий инструмент Бережливого производства - система всеобщего ухода за оборудованием, или TPM (англ. Total Productive Maintenance).
TPM – это система, которая предполагает всеобщий уход за оборудованием, и в основном отвечает за увеличение эксплуатационного срока оборудования. Она позволяет максимально эффективно использовать оборудование за счет всеобщей системы профилактического обслуживания.
Принцип работы системы в предупреждении поломок или раннем их выявлении, ранняя диагностика дефектов оборудования, чтобы они не повлекли за собой более серьезных проблем.
«В системе ТРМ основную роль играют операторы и ремонтники, обеспечивающие повышение надежности оборудования, но и остальные сотрудники не должны терять бдительность. Основа системы ТРМ заключается в профилактических мерах: составление графика профилактического техобслуживания, смазка, очистка и общая проверка оборудования. Благодаря соблюдению подобных мер можно обеспечить повышение такого показателя, как OEE (от английского «Overall Equipment Effectiveness» - полная эффективность оборудования).
Далее следует остановиться на системе JIT (Just-In-Time - точно вовремя)
Система JIT (Just-In-Time) - это инструмент «бережливого производства», который представляет собой порядок управления потоком деталей в производстве, при котором компоненты из прошлой операции доставляются именно в тот момент, когда они необходимы, не раньше и не позже. Эта система способствует сокращению объемов незавершенного производства, а также устраняет необходимость содержания складов материалов и готовой продукции.
Данная система предлагает компаниям специфический подход по выбору и оцениванию поставщиков, который основывается на работе с узким кругом поставщиков, отбираемых по критерию способности гарантировать поставку "точно в срок". При этом качество поставляемых материалов и продуктов не должно страдать. Этот подход предполагает сокращение количества поставщиков в два и более раз. С оставшимися поставщиками предполагается длительное сотрудничество.
Еще одна система управления эффективностью в рамках концепции Бережливого производства – это система быстрой переналадки, или SMED (англ. Single Minute Exchange of Die)
Эта концепция была разработана также японским автором, Сигео Синго. В свое время она совершила революцию в подходах к переналадке и переоснастке оборудования.
Чуть позже, в результате внедрения системы SMED, была создана система OTED (англ. One Touch Exchange of Dies), которая предполагает, что смену любого инструмента и переналадку можно осуществить всего в несколько минут, в некоторых случаях даже секунд, «в одно касание».
Результатом исследований явились следующие принципы, которые позволяют сократить время переналадки в десятки и даже сотни раз:
1. Разделение операций наладки на внутренние и внешние;
2. Преобразование внутренних действий во внешние:
3. Применение функциональных зажимов или, наоборот, полное устранение крепежа;
4. Использование в процессе переналадки дополнительных приспособлений»[15].
Далее рассмотрим такой инструмент как U-образные ячейки.
U-образными ячейками называют группы работников или машин, созданных для поддержания постоянного потока. Использование этого инструмента предполагает непрерывную последовательность процессов без перепроизводства и задержек.
Ячейка работников в офисе – это также группа специалистов, подготовленных для оперативного решения задач или же работы с определенными клиентами.
Разница между традиционным конвейером и U-образной ячейкой в следующем.
Традиционный конвейер представляет из себя последовательность станков, где сырье превращается в готовую продукцию.
Какое-то время материал находится у станка, пока не совершится ряд задач. Все операторы закреплены за одной или несколькими рабочими станциями. Традиционно станки на конвейере расположены в ряд, прямой линией. Сырье движется по конвейеру из одного конца в другой, завершая создание готовой продукции;
На рисунке видно, что при очень высоком спросе у каждого станка находится оператор. С уменьшением спроса до высокого, среднего и низкого
Рисунок - Принцип работы U-образных ячеек при очень высоком, высоком, среднем и низком спросе
можно сокращать количество работников до 5, затем 3 и вовсе до 1 соответственно.
При изменениях спроса и уровня производства U-образные ячейки являются более гибкими по сравнению с традиционными конвейерами.
Еще следует остановить свое внимание на таком инструменте как визуализация.
«Визуализация – инструмент «бережливого производства», который заключается в том, чтобы информировать сотрудников о том, как должна выполняться работа. Как вариант, это такое размещение деталей, инструментов, тары и прочих индикаторов состояния производства, когда любой с первого взгляда поймет, в норме система или нет.
Есть много методов визуализации, самые популярные представлены ниже:
1. Оконтуривание;
2. Маркировка цветом;
3. Метод дорожных знаков;
4. Маркировка краской;
5. Метод «Было» - «стало»;
6. Графические рабочие инструкции.
Также в Бережливом производстве используют систему 5S.
Система 5S - инструмент Бережливого производства, позволяющая создать эффективное рабочее место.
5S - обозначение системы укрепления дисциплины, наведения порядка и чистоты в компании. Система 5 С содержит, соответственно, пять принципов организации рабочего места, взаимосвязанных между собой. Называется она так, потому что японские слова, означающие эти принципы, начинаются на букву «S».
В систему 5S входят следующие принципы:
1. Seiri, или организация: заключается в том, чтобы убрать с рабочего места все лишнее и не плодить ненужные предметы;
2. Seiton, или аккуратность: основан на расположении предметов в порядке, который наилучшим образом бы отвечал требованиям безопасности, качества и эффективности работы;
3. Seiso, или уборка: проведение регулярной тщательной уборки и проверки наличия и исправности оборудования, инструментов, инвентаря. Соблюдение принципа "чисто там, где не сорят";
4. Seiketsu, или стандартизация: установление на производстве такого порядка, чтобы любое отклонение от нормы было заметно с первого взгляда. Осуществляется при помощи системы указателей, бирок с надписями и инструкций;
5. Shitsuke, или дисциплина: соблюдение установленных правил поведения и норм общения, поддержание атмосферы и дружелюбия в отношениях между людьми»[35].
Последний инструмент, который мы рассмотрим – это «Пока ёкэ».
«Poka-yoke» (от японского - принцип нулевой ошибки, англ. Zero defects) - инструмент Бережливого производства, который предполагает предотвращение ошибок; этот метод заключается в том, что работа может быть сделана лишь одним, правильным, способом. В таком случае дефект не может появиться. Принцип нулевой ошибки допускает минимальное количество ошибок (или всего одну). «При внедрении данного способа отношение к дефектам должно быть следующим: такие ошибки как промахи из-за случайной перестановки, забывчивости рабочих, ложного считывания, неверной интерпретации, различных заблуждений, невнимательности и незнания возможны в ходе работы и неизбежны. Но они должны восприниматься работниками как нормальное явление. Ошибки следует как можно скорее вскрывать, а не замалчивать. Смысл в том, чтобы искать причину дефекта, а не его виновников.
Основные моменты метода следующие:
1. Создание предпосылок для бездефектной работы,
2. Внедрение методов для бездефектной работы,
3. Систематическое устранение, возникающих в ходе работы ошибок,
4. Принятие всех мер предосторожности,
5. Внедрение несложных технических систем, которые бы позволили работникам предотвратить совершение ошибок.
Метод Poka Yoke применяется в следующих случаях:
1. В поиске ошибок входного контроля: тогда дефект будет выявлен до совершения тех или иных операций;
2. Когда осуществляется контроль завершенного процесса;
3. При поиске ошибок во время выполнения процесса самим сотрудником;
4. При передаче изделия в процессы следующих уровней.
Метод Poka-yoke, в комплексе с другими инструментами бережливого производства гарантирует бездефектность изделия, а процесс его производства протекает без сбоев.
ВОПРОС 5. Основные особенности оргкультуры фирмы Тойота по Х. Такеучи
Такеучи с соавторами выделяют следующие элементы организационной культуры:
1.Силы экспансии вынуждают фирму изменяться и совершенствоваться и включают:
A. Труднодостижимые цели.
B. Учет локальных запросов.
C. Экспериментирование.
2. Силы интеграции способствуют стабильному развитию а также сохранению базовых ценностей. К ним относят:
A. Ценности основателей фирмы.
B. Пожизненный найм.
C. Поощрение искренности в общении.
Постановка целей, которых практически невозможно добиться, позволяет освободиться от ограничений, мешающих быстрому развитию. Таким образом обеспечивается повышение самооценки сотрудников. Само появление фирмы связано с решением основателей создать предприятие по производству автомобилей в Японии без использования зарубежных технологий. Многие из целей фирмы целенаправленно формируются нечеткими, чтобы предоставить возможность сотрудникам найти новое направление исследования, что позволит значительно повысить эффективность.
Фирма Тойота ставит своей целью удовлетворение потребностей каждого клиента и обеспечение полного ассортимента на каждом рынке, так как полагает, что это создает больше возможностей для развития. Фирма модифицирует как свои товары, так и операционные системы к потребностям каждой страны. Хотя выход на другие рынки и вынуждает к действиям в условиях жесткой конкуренции ,сложившаяся ситуация ведёт к созданию новых технологий, каналов сбыта, маркетинговых подходов.
Широкое использование экспериментов облегчает достижение амбициозных целей, однако это невозможно без наличия терпимости к совершению ошибок.
Значительные изменения связаны с высоким риском, поэтому стабильное развитие Toyota во многом связано с приверженностью к основополагающим ценностям фирмы. Данные ценности были сформированы во многом представителями семьи Тойода, которые за редким исключением традиционно занимали пост руководителя предприятия.
Уважение к людям выражается в стремлении сохранить работников, несмотря на финансовые потери. Для сохранения коллектива осуществляется прогноз спроса на автомобили на долгосрочную перспективу. Во время максимального спроса фирма осуществляет аутсорсинг отдельных видов деятельности и нанимает временных рабочих. Во время спада спроса происходит отказ от аутсорсинга и увольнение временных рабочих. Кроме того фирма вынуждена поддерживать значительные финансовые ресурсы для выплаты зарплаты работникам во время кризиса. Система пожизненного найма позволяет проводить значительные инвестиции в обучение. При оценке менеджеров их вклад в развитие работников, а так же доверие и уважение к ним со стороны окружающих.
Для стимулирования передачи информации и знаний в Тойоте поощряют различные виды коммуникаций. Информация свободно перемещается не только по уровням иерархии и функциональным отделам, но и среди клиентов и партнеров. Руководство участвует в вечеринках с рабочими, ответственные за продажи руководители лично посещают клиентов, руководители и сотрудники находятся в одном помещении. Поощряется высказывание идей, которые могут противоречить мнению руководства. Работник должен действовать в соответствии со своими представлениями о том, что хорошо или плохо. Игнорирование указаний начальства может быть признано целесообразным. Для сокращения бюрократизма применяются небольшие по объему документы, которые должны размещаться на листе А 3. Для стимулирования взаимодействия каждый работник, как правило, участвует в работе нескольких комитетов, самоуправляющихся команд и социальных групп. Таким образом, фирма стремится профилактировать естественное стремление крупной корпорации сохранить наиболее успешные процессы и методики, способствовавшие достижению успехов в прошлом, но которые могут стать препятствиями на пути будущего развития предприятия.
ВОПРОС. 5 Основные особенности оргкультуры фирмы Тойота по Д. Лайкеру.
Так как организационная культура должна соответствовать стратегии, то рассмотрим особенности миссии фирмы Тойота. Долгосрочной целью Toyota является обеспечение экономического роста фирмы и благосостояния общества в целом на основе создания ценностей для потребителей и формирования условий для стабильности и благополучия коллектива фирмы. Руководство фирмы выделяют следующие цели предприятия: прибыль, успех в долгосрочной перспективе, обеспечение вклада в развитие экономики и общества в целом, достижения высочайшего уровня качества продукции. При этом фирма стремится обеспечить для сотрудников следующие условия: высокий уровень зарплаты, личностный рост, хороший социальный пакет, безопасное рабочее место, осмысленную работу.
С самого начала своей деятельности на фирме Тойота считалось, что ключом к успеху являются инвестиции в человеческий капитал. Руководство фирмы стремится привлекать, формировать и удерживать лучших работников. Главное конкурентное преимущество фирмы заключается в наличии у неё особой корпоративной культуры. В центре внимания находятся уважение к людям и непрерывные улучшения. Работа на Toyota рассматривается компанией как средство формирования партнерских отношений с целью обеспечения долгосрочного развития как фирмы, так и коллектива. Toyota это самообучающаяся организация.
Выделяют пять основных ценностей корпоративной культуры Тойота:
1. Стимулирующие задачи — формирование долгосрочного мировоззрения. мужественное и творческое выполнение имеющихся задач. Для Toyota характерна готовность ставить перед фирмой невыполнимые задачи и добиваться успеха. Производство автомобилей фирмы открыла в условиях разрухи после проигрыша Японии во Второй Мировой войне, а до этого фирма занималась производством ткацких станков. За три года фирма догнала по производительности мирового лидера, которым было корпорация Ford. До этого фирма отставала по производительности в 8 раз.
2. Кайдзен — непрерывное совершенствование бизнеса, вечное стремление к инновациям и развитию. На западных предприятиях считается, что главная задача руководства добиться успеха. Руководство фирмы Тойота считает, что оно должно заботиться о коллективе, который создаёт и реализует улучшения.
3. Генти генбуцу — решение проблем на основе ознакомления с ситуацией именно там, где возникла проблема. Высшее руководство фирмы при создании новых продуктов зачастую самостоятельно занимается анализом поведения целевой группы клиентов.
4. Уважение — принятие на себя ответственности сделать всё возможное для создания взаимного доверия. Основатели компании полагали, что добиться эффективности производства возможно только на основе уважения к человеку. Если на западных предприятиях руководство стремиться сократить численность работников, то Тойота поддерживается принципа пожизненного найма, а мотивированные работники самостоятельно сокращают бесполезные расходы.
5. Стимулирование командной работы. Для американской культуры характерен индивидуализм, стремление быстро обеспечить себе карьерный рост, однако усложнение и рост масштабов технических систем делают командную работу наиболее важным приоритетом.
Необходимо учитывать особенности восприятия системы вознаграждения и поощрения на западе на востоке. В западной культуре человек ориентирован: на индивидуальное признание своих достижений, свободный выбор и определение собственного поведения, рассмотрение отношений в группе как неприятных ограничений, частое изменение места работы в поисках более высокой зарплаты, необходимость периодического вербального поощрения своей деятельности, равенство в межличностных отношениях и стремление к получению власти, наличие одинаковых для всех правил в обществе. Для восточной культуры характерны: рассмотрение успеха как результатов деятельности группы, а неудачи как вины отдельного работника; стремление человека стать членом группы и вместе достигать общих целей; высокая ценность долгосрочных партнерских отношений; допустимость краткосрочных потерь ради стабильности и выгоды; желание получить критические замечания для улучшения своей деятельности; благоприятная оценка своего места в иерархии и тщательное исполнение указания более мудрых коллег; учет особенностей контекста при рассмотрении поведения человека в конкретной ситуации.
ЛЕКЦИЯ 5. МЕНЕДЖМЕНТ ЗНАНИЙ.
Теоретические аспекты менеджмента знаний.
В настоящее время возрастает роль знаний в экономической деятельности. Менеджменту знаний посвящено большое количество работ, как отечественных, так и зарубежных ученых, но до сих пор теоретические аспекты менеджмента знаний всё ещё должны быть созданы. Под знаниями следует понимать «совокупность информации об объекте, его внутренней структуре и внешней среде, выступающей в качестве совокупности моделей, которые достоверно и с определённой точностью позволяют принимать эффективные решения и добиваться требуемых результатов в практической деятельности». Особое внимание к управлению знаниями связано с тем, что предприятие постепенно превращается в самоуправляющееся техническое устройство. «Согласно Р. Филцу, менеджеру фирмы «Белл Атлантик», один человек сможет делать то, что сейчас делает группа людей, владеющих различными профессиями… Но это не должно стать завершением реинжиниринга. Последняя его стадия, как она видится нам сейчас, есть стадия самообслуживания, когда клиенты будут напрямую взаимодействовать с нашей системой». Фактически в развитых странах большая часть людей не занимается тяжелым физическим трудом и даже не занята в сфере материального производства. Даже рабочие, как правило, заняты управлением техническими устройствами. По этой причине повышение производительности труда будет обеспечиваться за счет дальнейшей автоматизации операций, которые ранее выполнялись с участием людей. Фактически постепенно происходит процесс отделения знаний от людей, которые ими обладают, с целью превращения знаний сначала в письменные инструкции, а затем и в компьютерные программы, которые будут управлять техническими устройствами. Такая тенденция выглядит многообещающей, так как имеет место быстрое развитие информационных технологий и создана требуемая инфраструктура, представленная в виде сети интернет. Широкое внимание уделяется развитию интернета вещей. Общаясь между собой, технические устройства будут оптимизировать свою деятельность без вмешательства человека. Также происходит развитие искусственного интеллекта, что, в конечном счете, создает условия для появления быстро обучающихся компьютерных программ.
Теоретические основы управления организациями в экономике знаний находятся ещё на стадии формирования. Можно сформулировать следующие принципы управления организациями в экономике знаний:
1. Автоматизация рутиной деятельности.
2. Моделирование.
3. Экспериментирование.
4. Командная работа.
5. Развитие доверительных и взаимовыгодных отношений с клиентами, работниками, поставщиками.
6. Управление талантами.
Данные принципы следует дополнить таким элементом, как управление организационной культурой. Внимание, уделяемое специалистами в области менеджмента организационной культуре, связано с ее значительным влиянием на достижение успеха фирмой. Переход от промышленной эры к формирующейся новой экономике, основывающейся на широком применении знаний, требует отказа от принципов организации массового производства и перехода к процессному управлению. Ведущие зарубежные специалисты указывают, что при переходе от функциональной организации к процессному управлению неизбежно коренное изменение организационной культуры. Так для функциональной организации характерны иерархические структуры управления, распределение специалистов по функциональным отделам, наличие жестких инструкций и контроля, слабая адаптивность и медленная реакция на ситуацию во внешней среде, совершенствование на основе распоряжения вышестоящих органов, ограниченный доступ к информации, оценка индивидуальных результатов, предпочтение подходов, хорошо зарекомендовавших себя в прошлом. Для процессной организации можно выделить следующие особенности: незначительное количество иерархических уровней менеджмента, процессные команды, состоящие из специалистов в различных областях знаний, значительная автономия в работе и саморегулирование, высокая гибкость и адаптивность, непрерывное совершенствование, широкий доступ к информации, оплата по конечным результатам. Из вышесказанного и вытекает необходимость существенных изменений в организационной культуре. В условиях инновационной экономики нет заранее известных ответов, какой из возможных подходов принесёт лучшие результаты. Поэтому важно сформировать у работников не столько навыки, которые быстро устаревают, но ценности и представления, позволяющие правильно находить верные решения в условиях неопределенности.
Дата добавления: 2022-11-11; просмотров: 22; Мы поможем в написании вашей работы! |
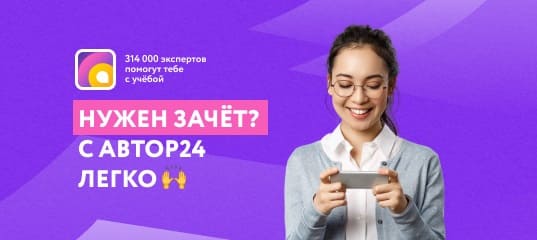
Мы поможем в написании ваших работ!