Основные виды термической обработки стали.
Изменяя режим охлаждения нагретой до аустенитного состояния стали, можно в широком диапазоне изменять ее дислокационно-фазовое строение и, таким образом, получать различные комплексы механических и других свойств. На преобразовании фазово-зёренной структуры сталей основаны такие наиболее часто применяемые виды термообработки, как отжиг, нормализация и закалка. Важным видом термообработки, выполняемым после закалки, является отпуск.
Отжиг.
Традиционно сложившееся понятие «отжиг» охватывает несколько отличающихся друг от друга по режиму операций термообработки, объединенных единой целью — привести сталь в термодинамически равновесное состояние с минимальной плотностью дислокаций (106 – 107 см-2), по возможности низкой твердостью и высокой пластичностью.
Наиболее распространенной разновидностью отжига является обыкновенный отжиг, который производится с целью умягчить сталь перед механической обработкой и подготовить ее структуру к окончательной обработке, состоящей из закалки и отпуска. Такому отжигу подвергаются имеющие неблагоприятную грубозернистую структуру литые заготовки, а также заготовки, прошедшие ковку, штамповку и другие виды обработки давлением, также нуждающиеся в изменении структуры.
В ряде случаев, когда получающиеся после отжига свойства обеспечивают долголетнюю службу детали, он оказывается окончательным видом термообработки.
|
|
Отжиг стали – метод термической обработки стали при котором сталь нагревают до температуры на 30 – 50°C выше линии GSK диаграммы состояния системы железо – цементит, выдерживается при этой температуре до полного завершения структурно-фазовых превращений и охлаждается со скоростью менее 100°C/ч (рис. 2.11).
Заэвтектоидную сталь при отжиге нельзя нагревать выше точки Асm (линия SE), так как образующаяся при очень медленном охлаждении вокруг зерен перлита цементитная сетка затрудняет механическую обработку заготовки резанием и охрупчивает сталь. Умягчению стали при отжиге способствует очень малая плотность дислокаций.
Диффузионный отжиг, или гомогенизация, является разновидностью отжига, применяемого с целью устранения в легированной стали (как и в других сплавах) дендритной ликвации.
При диффузионном отжиге с целью интенсификации диффузионных процессов сталь нагревают до 1000 – 1100°C и подвергают длительной выдержке (18–24 ч). Для устранения крупнозернистости после гомогенизации производится обыкновенный отжиг, или нормализация.
![]() | Рис. 2.11. Температура нагрева стали при видах термообработки: отжиг, нормализация, закалка, в зависимости от содержания углерода. |
|
|
Рекристаллизационный отжиг. Этот вид отжига производится с целью устранения наклепа холоднодеформированного металла. Наклепанный металл очень тверд и хрупок, поскольку его кристаллическая решетка вследствие высокой плотности дислокаций и наличия большого числа других дефектов (вакансий, перемещенных в междоузлия атомов), а также из-за искажений и больших внутренних напряжений находится в неравновесном состоянии, обладая большим запасом избыточной свободной энергии. В сильно наклепанном металле из-за слияния дислокаций в местах их скопления наблюдаются опасные дефекты – зародыши трещин.
В ряде случаев наклеп необходимо устранять. Для этого требуется нагрев, стимулирующий диффузионные процессы. От наклепа можно избавиться, применяя обыкновенный отжиг. Однако рекристаллизационный отжиг из-за значительно более низкой температуры и намного меньшей продолжительности его проведения при практически одинаковых результатах более предпочтителен.
Температура нагрева при этом виде отжига выбирается на 150 – 250°С выше температуры рекристаллизации (ТР) обрабатываемого сплава. Это наименьшая температура, необходимая для протекания в наклепанном металле процессов, возвращающих ему исходные (до деформации) значения характеристик механических и других свойств.
|
|
Температура рекристаллизации зависит от состава сплава и связана с температурой его плавления уравнением TP= αТПЛ (где ТПЛ выражена в K; α – коэффициент, зависящий от природы сплава). Для углеродистых сталей и не сложных по составу сплавов он составляет 0,4, а у легированных сталей и сложных сплавов твердых растворов достигает 0,6 - 0,8.
Рекристаллизационный отжиг углеродистой стали производится при температуре нагрева в пределах 600 – 700 °С.
Во время нагрева и выдержки в холоднодеформированном металле происходят рекристаллизационные процессы, суть которых сводится к таким следующим друг за другом по мере нагрева и выдержки явлениям, как аннигиляция (самоликвидация) противоположных по знаку дислокаций, выстраивание дислокационных стенок (из леса дислокаций) и, наконец, зарождение и рост новых равновесных зерен. Причем если первые два явления происходят при Т< ТР, то зарождение новых зерен происходит только при T > ТР.
Заметное укрупнение рекристаллизованных зерен за счет поглощения более крупными зернами соседних мелких (собирательная рекристаллизация) происходит по окончании процесса формирования новых зерен из материала разрушенных старых. Для этого требуются продолжительные выдержки при повышенных температурах.
|
|
В рекристаллизованном металле плотность дислокаций составляет 107см-2, поэтому он имеет низкие прочностные характеристики и высокую пластичность.
Наклеп необходимо устранять после холодной обработки металла давлением, производимой при T < Tp (ковка, штамповка, тонколистовая прокатка и в других случаях).
Отжиг рекресталлизационный – метод термической обработки холоднодеформированного металла с высокой плотностью дислокаций и других видов дефектов кристаллической структуры, при температурах, определяемых по уравнению TР= αТПЛ (α – для углеродистых сталей 0,4, температура отжига 600 – 700 °C, для легированных сталей 0,6 - 0,8) в процессе которого и прежних зёрен с высокой плотностью дефектов происходит рост новых преимущественно равноосных зёрен.
Нормализация.
Особенностями режима этого вида термообработки являются температура нагрева (на 30 – 50° выше линии GSE, рис. 2.11) и охлаждение на спокойном воздухе. Эти особенности обусловлены специфическими целями нормализации. Применительно к доэвтектоидным сталям, особенно низкоуглеродистым (0,05 – 0,25% С), нормализация за более короткое время и при большей простоте режима охлаждения позволяет получить те же результаты, что и при отжиге, т. е. весьма эффективное измельчение зерна у литых и кованых заготовок.
Так как охлаждение на воздухе обеспечивает более высокую степень переохлаждения аустенита, чем при отжиге, то продукты его распада оказываются более дисперсными, а плотность генерируемых дислокаций приближается к 108см -2. Вследствие этого нормализацией можно получить более благоприятную мелкозернистую структуру стали, обладающую повышенными прочностными свойствами.
В ряде случаев, когда от материала изделия не требуется повышенных прочностных свойств, нормализация заменяет закалку. Особенно это касается деталей из низкоуглеродистой стали, для которых применение закалки исключается из-за очень высокой критической скорости закалки.
При нормализации заэвтектоидных сталей из-за ускоренного выделения из аустенита избыточного (вторичного) цементита (в интервале температур Асm – Аr1) нежелательная цементитная сетка вокруг перлитных зерен не образуется. В связи с этим одной из целей нормализации является разрушение упомянутой сетки у заэвтектоидных сталей.
Нормализация – метод термической обработки стали, при котором сталь нагревают на 30 – 50° выше линии GSE диаграммы состояния системы железо – цементит и охлаждают на спокойном воздухе, что приводит к измельчению зерна у литых и кованых заготовок.
Закалка.
В общем понимании закалка – метод термической обработки, включающий нагрев до температуры более высокой, чем температура фазового превращения, выдержка при заданной температуре и быстрое охлаждение, после которого фиксируется состояние сплава, соответствующее более высокой температуре.
В отношении сталей исторически сложившееся понятие закалка предполагает такую термообработку, при которой сталь приобретает неравновесную структуру, что, прежде всего, выражается в повышении твердости стали. К закалке можно отнести термообработку на сорбит, , бейнит и мартенсит. Степень неравновесности продуктов закалки с увеличением скорости охлаждения повышается и возрастает от сорбита к мартенситу.
Закалку на мартенсит принято считать истинной закалкой. Важнейшим преимуществом истинной закалки является возможность получения из мартенсита за счет последующего отпуска продуктов с такими ценными комплексами свойств, которые другими видами термообработки получить невозможно.
В связи с этим истинная закалка по сравнению с другими ее видами получила более широкое применение как предварительная обработка перед следующим за ней отпуском. Режим истинной закалки включает нагрев до температуры на 30 – 50° выше линии GSK (рис. 2.11) и охлаждение со скоростью не ниже критической.
Критическая скорость закалки имеет очень важное значение. От нее зависит такое технологическое свойство стали, как прокаливаемость, т. е. способность закаливаться на определенную глубину. Чем меньше величина критической скорости закалки, тем на большую глубину от поверхности детали распространяется закалка, поскольку фактическая скорость охлаждения по мере увеличения расстояния от поверхности уменьшается и на каком-то удалении может оказаться меньше критической скорости закалки. Критическая скорость закалки зависит от стабильности аустенита, которая, в свою очередь, определяется количеством растворенных в нем углерода и легирующих элементов. Введением в сталь углерода и легирующих элементов можно повысить прокаливаемость.
Прокаливаемость принято оценивать с помощью специальных цилиндрических образцов по глубине залегания в них полумартенситного слоя при охлаждении торца нагретого образца струей холодной воды. Полумартенситным принято считать слой стали, содержащий 50 % мартенсита (М) и 50 % тростита (Т).
Поскольку изменение скорости охлаждения от поверхности вглубь детали зависит от температуры и рода охлаждающей среды, то при оценке прокаливаемости следует учитывать и эти факторы.
Одной из целей легирования конструкционных сталей является уменьшение критической скорости закалки и получение сквозной прокаливаемости изготовленных из них деталей при закалке не только в воде, но и в более мягких охлаждающих средах: масле, теплой воде, на воздухе. От резкости охлаждающей среды зависит уровень термических и фазовых напряжений и вероятность образования трещин в детали или ее коробления. При закалке предпочтительны более мягкие закалочные среды.
При закалке режущего инструмента из высокоуглеродистой стали с целью уменьшения внутренних напряжений применяют охлаждение в двух средах. При этом кратковременным в течение нескольких секунд охлаждением в воде обеспечивается переохлаждение аустенита до температуры несколько выше точки МН. Дальнейшее охлаждение производится в мягкой среде, например в минеральном масле, вследствие чего мартенситное превращение происходит с меньшим уровнем возникающих внутренних напряжений. Такую закалку принято называть прерывистой или закалкой в двух средах.
Обработка холодом. При закалке в обычных охлаждающих средах в стали наряду с мартенситом сохраняется какое-то количество остаточного аустенита, тем большее, чем ниже точка МК.
У высокоуглеродистых сталей и, особенно, у сталей с достаточно высоким содержанием легирующих элементов точка МК лежит ниже комнатной температуры, а зачастую и ниже 0°С. В связи с этим при обычной закалке в них сохраняется много остаточного аустенита. Его наличие снижает твердость закаленной стали и ее теплопроводность, что для режущего инструмента является особенно нежелательным.
В течение определенного времени остаточный аустенит претерпевает фазовые превращения, приводящие к изменению размеров изделия. Это недопустимо для мерительного инструмента, такого как скобы, пробки, шаблоны.
Сущность обработки холодом состоит в том, что для устранения остаточного аустенита после обычной закалки изделие помещают в холодильную камеру с температурой, равной или близкой к точке МК обрабатываемой стали (обычно около -80 °С). При этом продолжается мартенситное превращение, и она приобретает структуру мартенсита с минимальным количеством неизбежно сохраняющегося остаточного аустенита.
Таким образом, суть обработки холодом состоит в продолжение мартенситного превращения в стали после обычной закалки. В результате обработки холодом повышается твердость и стабилизируются размеры изделия, что очень важно для режущего и мерительного инструмента.
Закалка стали (на мартенсит) – метод термической обработки стали, при котором сталь нагревается до температуры на 30 – 50° выше линии GSK диаграммы состояния железо - цементит и охлаждается со скоростью не ниже критической, что позволяет получить мартенситную структуру стали.
Рис. 2.12 Фотографии процессов закалки деталей на воздухе (слева) и опусканием в масло (справа).
Отпуск стали.
Отпуском называется операция нагрева закаленной стали до температуры ниже критической температуры фазового превращения и последующего охлаждения для уменьшения имеющихся в стали остаточных напряжений и придания ей комплекса механических и других свойств, которые необходимы для долголетней эксплуатации изделия.
Отпуск является завершающей операцией термической обработки стали. Твердость мало и среднеуглеродистых сталей снижается по мере повышения температуры их отпуска. Если отпуск проводится при комнатной температуре или несколько ее превышающей, то он называется старением. Склонность к старению сталей может быть снижена введением добавок алюминия, титана и ванадия.
При отпуске закаленной на мартенсит стали в ней происходят превращения, приводящие к распаду мартенсита и образованию равновесного структурно-фазового состава. Интенсивность и результат этих превращений зависят от температуры отпуска.
С целью недопущения полиморфных превращений отпуск производится при температурах ниже точки Ас1. Однако поскольку от температуры зависят степень распада мартенсита и комплекс получаемых при этом физико-механических и других свойств, то температуру отпуска выбирают в зависимости от функционального эксплуатационного назначения изделия.
В процессе многолетней эксплуатационно-производственной практики сложились три основные группы изделий, требующие для их успешной эксплуатации «своих» специфических комплексов вязкостно-прочностных и других свойств.
В первую группу входят режущий и мерительный инструменты, а также штампы для холодной штамповки. От данных материалов требуется высокая твердость (свыше 58 HRC) и хотя бы небольшой запас вязкости.
Вторую группу составляют пружины, рессоры и другие изделия, от материала которых требуется сочетание высокого предела упругости с удовлетворительной вязкостью.
Третья группа изделий включает большинство деталей машин, испытывающих статические и особенно динамические или циклические нагрузки. При длительной эксплуатации изделий от их материала требуется сочетание удовлетворительных прочностных свойств с максимальными показателями вязкости.
Следовательно, в зависимости от температуры нагрева существует три вида отпуска: низкотемпературный (низкий), среднетемпературный (средний) и высокотемпературный (высокий).
Отпуск преследует цель не просто устранить внутренние напряжения в закаленной стали (этого можно добиться, применяя один-единственный вид отпуска при температуре несколько ниже точки Ac1). Он является средством придания стали требуемого комплекса свойств. И еще очень важно иметь в виду: при увеличении температуры отпуска возрастает степень диффузионного распада мартенсита на ферритно-цементитную смесь, что обусловливает уменьшение прочностных свойств стали и повышение ее вязкости.
Низкотемпературный (низкий) отпуск производится при 150–180°C, а для легированных сталей при температурах до 250 °С. В этом случае при низкой интенсивности диффузионных процессов в мартенсите происходит только начальная стадия к его переходу в равновесное состояние.
При низком отпуске мартенсит лишь частично освобождается от пересыщающих его решетку атомов углерода. Поэтому основу мартенсита после отпуска изделий составляет все еще пересыщенный твердый раствор углерода в α-Fe.
Однако в нем несколько уменьшается число охрупчивающих его трехцентровых ковалентных Fe – С – Fe связей. Освобождающийся при этом углерод еще не может образовать стабильного карбида железа в виде частиц цементита Fe3C, обособившихся от кристаллической решетки мартенсита.
Поэтому в мартенсите отпуска образуются лишь высокодисперсные частички карбидов промежуточного состава (FexC), когерентно связанные с его решеткой. Такая связь означает, что пограничные атомы карбидных образований одновременно входят в состав ячеек матричной решетки мартенсита. Часть из освободившихся атомов углерода вместе с имеющимися в стали атомами азота образуют вокруг дислокаций атмосферы Коттрелла.
При низком отпуске наряду с процессами, обусловливающими разупрочнение мартенсита из-за частичного выхода из него атомов углерода (уменьшение числа ковалентных Fe – С – Fe-связей, частичное устранение искажений решетки и остаточных внутренних напряжений), происходят процессы и противоположного характера. К ним относятся образование стопоров в виде высокодисперсных карбидных включений и атмосфер Коттрелла, затрудняющих работу дислокационного механизма пластической деформации. При низком отпуске плотность дислокаций снижается лишь незначительно, оставаясь на уровне 1011 – 1012см -2 в зависимости от содержания углерода.
Таким образом, образующийся в результате низкого отпуска отпущенный мартенсит М0 обладает более благоприятным комплексом механических свойств, сочетающим высокий уровень твердости с некоторым, хотя и небольшим, запасом вязкости и пластичности.
Низкому отпуску подвергают изделия первой группы, включающей в себя режущий и мерительный инструмент, а также штампы для холодной штамповки и цементированные детали (для обеспечения высокой износостойкости цементированного слоя).
Среднетемпературный (средний) отпуск производится при температуре от 350 до 450°C (иногда до 470 °С). При таком нагреве завершается распад мартенсита, приводящий к образованию нормальных по составу и внутреннему строению феррита и цементита. Однако вследствие всё еще недостаточной интенсивности диффузионных процессов размер зерен образующихся фаз оказывается очень малым.
Образующийся при среднем отпуске продукт называется трооститом отпуска и обозначается как Т0. В нем, в отличие от троостита закалки, цементит представлен не пластиночками, а в виде мельчайших зерен, что обусловливает его более высокую вязкость в сравнении с трооститом закалки.
Вследствие происходящих в мартенсите при среднем отпуске диффузионных процессов почти устраняются ковалентные Fe – С – Fe-связи и искажения ОЦК решетки α-Fe, уменьшается плотность дислокаций (до 109 - 1010см -2), ликвидируются («рассасываются») атмосферы Коттрелла, а также снижается уровень остаточных напряжений.
Сложившиеся у троостита отпуска фазовая и дислокационная структуры обеспечивают материалу изделий благоприятный для пружин, рессор и им подобных изделий комплекс механических свойств, т. е. высокий предел упругости, сочетающийся с вполне удовлетворительной для изделий этой группы вязкостью.
Высокотемпературный (высокий) отпуск осуществляется при 500 – 650 °С. При таких условиях нагрева при усилившихся диффузионных процессах происходит образование более крупных, чем у троостита отпуска, зерен феррита и цементита, сопровождающееся дальнейшим снижением плотности дислокаций (до 108 – 109см -2) и практически полным устранением остаточных напряжений.
Получающийся при высоком отпуске продукт распада мартенсита, называется сорбитом отпуска и обозначается как С0. Сорбит отпуска обладает максимальной для стали вязкостью, сочетающейся с удовлетворительными показателями прочности. Такой комплекс является идеальным для деталей машин, подвергающихся динамическим и циклическим нагрузкам. Благодаря этому преимуществу термическую обработку, сочетающую закалку и высокий отпуск, издавна называют улучшением.
Отпуск при более высоких температурах (приближенных к точке Ас1 – 727 оC) нецелесообразен вследствие чрезмерного роста зерен цементита, что приводит к образованию структуры зернистого перлита и, как следствие, к значительному снижению прочности и особенно вязкости.
Углеродистые стали.
Углеродистые стали относятся к числу самых распространенных конструкционных материалов. Объем их производства достигает 80% от общей выплавки стали. Достоинствами сталей этого класса являются удовлетворительные механические свойства в сочетании с технологичностью обработки и низкой стоимостью. К главным недостаткам углеродистых сталей относятся высокая критическая скорость закалки, небольшая прокаливаемость (до 15мм), невысокая стойкость к отпуску.
Выпускают углеродистые стали трех групп: обыкновенного качества; качественную (общего назначения); специального назначения (котельную, мостовую, судостроительную и др.) (табл. 2.3.).
Стали обыкновенного качества. Углеродистые стали обыкновенного качества предназначены для изготовления различных металлоконструкций, а также слабонагруженных деталей машин и приборов. Они широко используются в строительстве при изготовлении железобетонных конструкций. Среднеуглеродистые стали номеров 5 и 6, обладающие большой прочностью, предназначаются для рельсов, железнодорожных колес, а также валов, шкивов, шестерен и других деталей грузоподъемных и сельскохозяйственных машин.
К недостаткам углеродистых сталей обыкновенного качества можно отнести то, что они часто не обеспечивают требуемых свойств по хладностойкости при эксплуатации сварных металлоконструкций в условиях Сибири и Крайнего Севера, где проявляются более суровые климатические условия. Существенным недостатком строительных углеродистых сталей является их малая прочность, что приводит к большому расходу металла и увеличению массы металлоконструкций.
Нелегированные конструкционные стали обыкновенного качества в соответствии с ГОСТ 380-94 обозначаются следующим образом: Ст3сп, Ст5кп, Ст7 и др. Здесь Ст – буквы, указывающие на принадлежность стали к группе сталей обыкновенного качества, следующая за ними цифра от 0 до 6 указывает на содержание углерода, в конце наименования стали привидятся буквы, определяющие степень ее раскисления (кп – кипяшая, пс – полуспокойная, сп – спокойная. В обозначение сталей с повышенным содержанием марганца после цифры добавляется также буква Г. Например, Ст3Гсп (табл. 2.3.).
Таблица 2.3.
Содержание углерода в сталях обыкновенного качества.
Обозначение стали | Содержание углерода, % | Обозначение стали | Содержание углерода, % |
Ст0 | <0,23 | Ст4 | 0,18-0,27 |
Ст1 | 0,06-0,12 | Ст5 | 0,28-0,37 |
Ст2 | 0,09-0,15 | Ст6 | 0,38-0,49 |
Ст3 | 0,14-0,22 |
Перед маркой указывают группу стали, причем группа A в обозначении марки стали не ставится. Для указания категории стали к обозначению марки добавляют в конце номер соответствующей категории, первую категорию обычно не указывают.
Ст1кп2 - углеродистая сталь обыкновенного качества, кипящая, номер марки 1, второй категории, поставляется потребителям по механическим свойствам (группа А);
ВСт5Г - углеродистая сталь обыкновенного качества с повышенным содержанием марганца, спокойная, номер марки 5, первой категории, с гарантированными механическими свойствами и химическим составом (группа В);
БСт0 - углеродистая сталь обыкновенного качества, номер марки 0, группы Б, первой категории (стали марок Ст0 и ВСт0 по степени раскисления не разделяют).
Пачки, концы или торцы прутков стали всех марок независимо от группы и степени раскисления маркируют несмываемой краской следующих цветов: сталь Ст0 - красной и зеленой, Ст1 - белой и черной, Ст2 - желтой, Ст3 - красной, Ст4 - черной, Ст5 - зеленой, Ст6 - синей.
Качественные стали. Качественные стали поставляются по ГОСТ 1050 - 88. Содержание серы и фосфора в них допускается в пределах 0,03 - 0,04% каждого из элементов. В машиностроении эти стали используются для изготовления деталей чаще всего неответственного назначения и являются достаточно дешевым материалом. Они имеют более низкое содержание вредных примесей и неметаллических включений, чем стали обыкновенного качества. В промышленность эти стали поставляются в виде проката, поковок, профилей различного назначения с гарантированным химическим составом и механическими свойствами.
К углеродистым сталям относят также стали с повышенным содержанием марганца (0,7 – 1 %) марок 15Г, 20Г, 25Г, 70Г, имеющих повышенную прокаливаемость.
Качественные стали маркируют следующим образом:
1) в начале марки указывают содержание углерода цифрой, соответствующей его средней концентрации:
а) в сотых долях процента для большинства сталей:
сталь с содержанием углерода 0,07 – 0,14 % обозначается 10, сталь с содержанием углерода 0,42 – 0,50 % - 45, а сталь с углеродом 0,57 – 0,65 % - 60;
60 - сталь углеродистая качественная, спокойная, содержит в среднем 0,60 % углерода;
05кп - сталь углеродистая качественная, кипящая, содержит 0,05 % углерода;
б) в десятых долях процента для инструментальных сталей, которые дополнительно снабжаются буквой "У":
У7 - углеродистая инструментальная качественная сталь, содержащая 0,7 % C, спокойная (все инструментальные стали хорошо раскислены);
У12 - углеродистая инструментальная качественная сталь, спокойная, содержит 1,2 % C;
- легирующие элементы, входящие в состав стали, обозначают русскими буквами:
А - азот K - кобальт T - титан
Б - ниобий М - молибден Ф - ванадий
В - вольфрам Н - никель Х - хром
Г - марганец П - фосфор Ц - цирконий
Д - медь P - бор Ю - алюминий
Е - селен C - кремний Ч - редкоземельные металлы
Если после буквы, обозначающей легирующий элемент, находится цифра, то цифра указывает содержание легирующего элемента в процентах. Если цифры нет, то сталь содержит 0,8-1,5 % легирующего элемента, за исключением молибдена и ванадия (содержание которых в сталях обычно до 0,2-0,3 %), а также бора (в стали с буквой P его должно быть не менее 0,0010 %) и некоторых других элементов.
14Г2 - низколегированная качественная сталь, спокойная, содержит приблизительно 0,14 % углерода и до 2,0 % марганца.
03Х16Н15М3Б - высоколегированная качественная сталь, спокойная, содержит 0,03 % C, 16,0 % Сr, 15,0 % Ni, до 3,0 % Мо, до 1,0 % Nb.
Строительные стали. Строительные стали по ГОСТ 27772-88 обозначаются буквой С (строительная) и цифрами, соответствующими минимальному пределу текучести стали. Буква К в конце наименования указывает на сталь повышенной коррозионной стойкостью, буква Т – на термоупрочненный прокат, а буква Д – на повышенное содержание меди, например, С255, С345Т, С390К, С440Д.
Высококачественные и особовысококачественные стали маркируют так же, как и качественные, но в конце марки высококачественной стали ставят букву "А" (буква "А" в середине марочного обозначения указывает на наличие азота, специально введенного в сталь), а после марки особовысококачественной - через тире букву "Ш".
У8А - углеродистая инструментальная высококачественная сталь, содержащая 0,8 % углерода;
30ХГС-Ш - особовысококачественная среднелегированная сталь, содержащая 0,30 % углерода и от 0,8 до 1,5 % хрома, марганца и кремния каждого.
Инструментальные стали, предназначены для изготовления малоответственного режущего, измерительного инструмента и штампов холодного и горячего деформирования. Они являются наиболее дешевыми. Недостатком инструментальных углеродистых сталей является потеря прочности при нагреве выше 200 ºС. Инструмент, изготовленный из этих сталей, применяют для обработки сравнительно мягких материалов и при небольших скоростях резания или деформирования.
Автоматные стали маркируют буквой А и цифрами, показывающими среднее содержание углерода в сотых долях процента, например, А11, А20 и т.д. Если автоматная сталь легирована свинцом, то обозначение марки начинается с сочетания АС, например, АС14 (Свинец легируют с целью получения у стали хорошей обрабатываемости резанием, и ее широко применяют для изготовления деталей двигателей).
Стали А11, А12, А20 используются для крепежных деталей и изделий сложной формы, не испытывающих больших нагрузок, но к ним предъявляются высокие требования по точности размеров и чистоты поверхности.
Дата добавления: 2019-02-22; просмотров: 958; Мы поможем в написании вашей работы! |
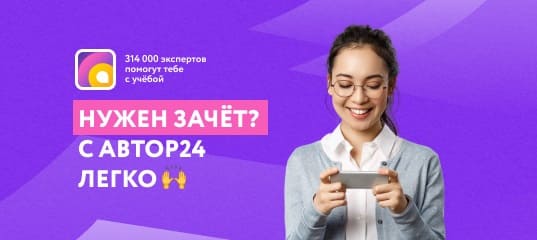
Мы поможем в написании ваших работ!