Сертификация продукции и систем качества
The Quality Management System (QMS) is a component of the general enterprise management system which has to provide stability of quality of production or services and to increase satisfaction of the consumer. Methodologically, QMS is the system of the business processes constructed on the basis of process model of management and directed to quality management of a product or service of the organization.
The purpose of certification of systems of quality management is creation of confidence of consumers in ability of the enterprise to deliver production of the required level of quality and to maintain quality of production at optimum expenses. Certification of QMS is carried out within voluntary certification. Despite voluntariness of the procedure, observance of the established rules and requirements for all participants is obligatory. Objects of check at certification of QMS are: QMS purposes, quality of production, documentation of QMS, processes of QMS. The system designation of quality management on Altyn Dan LLC it is called to provide quality of production or services of the enterprise and "to adjust" this quality on expectations of consumers (customers). At the same time her main task – not to control each unit of production, and to make so that there were no mistakes in work which could lead to emergence of marriage (bad quality of production or services). Always the wrong actions are the reason of marriage. And in order that to avoid them, it is necessary to formalize the correct actions for creation of qualitative production or services, to develop instructions for performance of the correct actions and to control these actions. The algorithm of action for improvement of QMS on Altyn Dan LLC is given in the figure 10.
The order on improvement an action about reconstruction of policy of «Altyn Dan» LLC |
Implementation of the plan introduction of measures for improvement of policy of «Altyn Dan» LLC and improvement of the quality system in production |
According to ISO 9001-2015: ü To consider all procedures of performance ü Appointment responsible for the producer ü Term of creation and production ü Time of implementation of the order |
Policy in the field of quality. Strategy of the purpose. Tactics. Discussion and a statement at all levels. Purpose of improvement of the quality system. ü In view of readiness of administrative personnel of the quality system ü Analysis of the ISO standards 9000 |
|
|
Training of leading experts, working groups and training of personnel for improvement of an element of the quality system |
Standards of the enterprise: ü order of their creation ü provisions on divisions ü order of registration official insturktion ü management of information on documents Reconstruction action for a improving of corporate standards |
Managements and recommendations about quality management of ISO 10013 for encouragement of management, personnel and heads of the enterprises |
Definition of the working group. Standards correspond to all ISO 9000 elements. Responsibility of the enterprise for standardization of activity of executive power and quality system, relationship of administrative personnel. To encourage employees and the management of the enterprise |
Inspection of quality elements and quality management in structural units, independent experts |
Carry out corrective actions for all elements of the certification system and quality assurance ISO/IEC 9000. Promote the management of the enterprise, leaders and employees. Deadline - after each verification of the plan |
Introduction of all elements of the quality improvement system in the enterprise division by the decision of the Council of Enterprises |
Plan of improvement and implementation of the quality system. Leading experts, the working groups, teaching leadership for improvement of quality of all employees |
Development of the corporate standard in structural divisions on the basis of the uniform quality system uniting all employees with structural divisions |
Creation of the guide to improvement of the quality system and guide on divisions to the quality system |
Development of the corporate standard on the basis of all improvements of the ISO 9000 |
Check about introduction an action for improvement of the quality system |
Carrying out the correcting actions |
Introduction of works on improvement of the quality system |
Issue of the document about passings training on quality systems |
Quality manual |
Results of control of the quality system |
Compliance of results of check |
Introduction change of normative documents in the quality system |
Management of the responsible departments of the company to improve the quality system |
In accordance with the requirements of ST RK 3.15.2 and ISO 9000, the filing of an application for a certification body for re-certification of the quality system |
Picture 10– Algorithm of action for improvement of QMS «Altyn Dan» LLC |
Reesertifiсation of the quality system |
|
|
Policy and purposes in area of quality. Policy in the field of quality are those main objectives and the directions of the organization which concern quality of the product released by her. QMS and policy in the field of quality are key concepts of the sphere of quality management at the enterprises. They in many respects define success of work and development of the organization. QMS ensures very effective functioning of the company, including, and in the sphere of quality management of the released goods. When forming a control system of quality requirements which are recorded in the international standards of ISO of a series 9000 are considered as the most effective. It should be noted that productively functioning QMS can be created when it conforms to requirements of the existing standard.
Competently to carry out policy in the field of quality, at the enterprise such QMS elements have to be created:
first, the document where all purposes and tasks and also the principles of their achievement are formulated;
secondly, the system of the complementing and interconnected processes which corresponds to policy in the field of quality;
thirdly, the normative documents regulating and describing various business processes of activity of the company within QMS;
fourthly, the effective mechanism of implementation of various requirements which are regulated by the regulatory base; at last,
fifthly, the prepared personnel of the organization.
Creation of QMS and the politician in the field of quality represent processes which consist of several main stages. It is possible to carry to such stages: decision of the management, training of personnel, formation of the program of introduction of QMS, description and optimization of various business processes, development of standard documentation of a quality management system, testing of QMS and internal audit, obtaining certificate. The decision of the management, for example, means that the head has to make a certain decision on the beginning of the project, then inform on it the staff of the company and create all necessary prerequisites for the fastest implementation of all other stages. Besides, at this stage it is necessary to formulate all main objectives of creation of QMS and also to allocate at the top level directly those processes of a quality management system which it is necessary to control, and, in addition, criteria for evaluation of their quality.
|
|
Then, when QMS and policy in the field of quality are implemented, the purposes of system need to be recorded in the special document which is called "Policy in the field of quality" where too various questions on this subject are described. This document – fundamental in all standard documentation in the sphere of QMS of the company. It is important as well a personnel grade level because for the most successful further work of a control system of quality the personnel of the company have to study fully the theory of the matter, the ISO standards 9000, to understand the theory of process approach and the main requirements to process of introduction of QMS. Training of this sort in use of system can be carried out both by means of specialists consultants, and in an independent order if at firm there is an employee who has experience of introduction of QMS. The further stage means directly formation of the program for creation of QMS. In general, introduction of a quality management system should be considered as rather difficult and long project, as a rule, for up to one and a half-two years. Therefore, it is necessary to make the program of creation of system which includes, first, the description of stages of introduction, secondly, the list of responsible persons for each stage of the project. Usually they are chosen from among by managing directors, top managers and also those qualified specialists who it is better than others know specifics of activity of the divisions.
|
|
APPROVED
General director
«Altyn Dan» LLC
________ Abdukarimov B.S.
«___»___________ 2018 y.
Aim at areas of quality
«Altyn Dan» LLC
Basic principle of Altyn Dan LLC: the quality is the highest. For achievement of this purpose the company makes the system of ensuring quality for all products made according to the ISO series ISO standards 9000.
1. continuous increase in effectiveness and efficiency of the organization taking into account requirements of interested parties;
2. Aspiration to qualitative production anyway;
3. Ensuring continuous improvement of quality of production in production;
4. supervision of level of production in comparison with indicators of previous year;
5. constant improvement of the developed control system in working order for continuous increase in effectiveness and efficiency of the organization in production;
6. Providing conditions for continuous improvement of a quality management system.
7. The maximum satisfaction of needs of consumers on quality of production.
8. Ensuring release of normal high-quality products.
9. Continuous improvement of quality of the made production.
The quality management system approves policy and the purpose of the organization for orientation. They define desirable results and promote use of means for achievement of these results. The policy in the field of quality forms a basis for development and the analysis of the purposes in area of quality. The purposes in area of quality have to be agreed with policy in the field of quality and need of continuous improvement. Meanwhile, results have to be measured. Achievement of the goals in the field of quality will positively affect quality of production and its efficiency and also satisfaction of requirements of interested parties.
APPROVED
General director
«Altyn Dan» LLC
________ Abdukarimov B.S.
«___»___________ 2018 y.
POLICY
in the field of quality
«Altyn Dan» LLC
The policy in the field of quality of Altyn Dan LLC is an integral part of the general policy and the management of the company which strategic value is based on continuous improvement of quality control, advance and preservation of all products and services for the purpose of production expansion.
It is planned to approve and expand the concept of quality according to requirements of ISO 9000 which belongs to production of dairy products and can be used in Altyn Dan LLC. Thus, Altyn Dan LLC as the main objective - constantly to improve quality of the products and services, encouraging all personnel of the enterprise to this process.
The company makes production according to state standard specification and other standard and technical requirements. Improvement of the control system of quality functioning at the enterprise considerably improves reliability of clients of the company according to the established requirements.
The policy in olast of quality of the company consists in production of products which completely satisfy expectations of clients. For this purpose each employee of the enterprise bears responsibility for quality, and each employee has to participate in improvement of quality and productivity of a product.
Ultimate goal of improvement of a control system of quality at the enterprise is obtaining the international certificate of quality of products and improvement of models of management as the integrated control system at all levels will help to solve many problems at the enterprise: quality of production, quality of work of personnel and competitiveness of competitiveness of production at the international level.
Important task in project management and in general in management – it is accurate to define who, for what is responsible. For this purpose also the "responsibility matrix" tool (responsibility matrix) is used.
In essence it is very simple and represents the table where in lines usually list works of the project, and in columns – design roles. Works take from structural decomposition of works (WBS), a role – from organizational structure of the project (OBS).
Both works, and role can be specified with different extent of specification. So, it is possible to write "specialists of the company", and it is possible to paint all by name. At early stages of life cycle of the project usually build the integrated responsibility matrix, on later – detailed.
On crossings of works and roles designate whether this person has relation to this work, and if has, then what. In literature it is possible to meet a set of designations, for example, such as "idea man". However, in our opinion, it creates excessive confusion and complicates use of the tool. Practice shows that enough following concepts:
Responsible. For each work one has to be surely specified and only one responsible.
Performers. Them can be a little, and can be so that itself responsible is also a performer. I.e. in one cell there can be more than one designation.
Approving. That person who approves some document (if this work is connected with creation of the document). He can be only one.
Coordinating. That person who participates in coordination of some document (if this work is connected with creation of the document). Them can be a little.
Gradual creation of a matrix of responsibility is made in the following order:
1. The list of the main results of the project is formulated (including their products and the project documentation on their number).
2. The list of participants of the project is created.
3. The table at the beginning of which every line specifies any result of the project and at the head of a column - the specific participant of the project is in development.
4. Specify the function or a role appointed to this participant of the project for obtaining desirable result in the cell created in line and a column.
At throws and functions try not to appoint more than one responsible for the received concrete result to avoid effect of collective irresponsibility. Also you watch that there is no such result left for which nobody bears personal responsibility. You seek to avoid also numerous statements not to tighten this part of work. As consultants choose those who really have qualities of the expert in this circle of tasks. The responsibility matrix for Altyn Dan LLC is presented in table 8.
Table 8 – Matrix of responsibility on «Altyn Dan» LLC
The project team Works | Customer representative of the project | Project Manager | Monitoring Operator | Marketing and Advertising Consultant | Project Support Specialist | Responsible for communication in the project | Chief Engineer |
Organizational support of the project | A | C.P | I.М | P | P | ||
Drawing up a business plan for the project | P | C | I.М | I | I | ||
Purchase of process equipment | A | C.P | I.М | P | I | I | |
Conducting reconstructive preparatory works at the production site | A | C | I.М | I | I | P | |
Preparation of premises for the requirements of the European standard ISO | A | C | I.М | I | I | P | |
Staff training in high-tech production | A | C.P | I.М | I | I | P | |
Conducting production certification | A | C.P | I.М | P | I | I | |
Certification of products | A | C.P | I.М | P | I | I | |
Production of an industrial batch | A | C.P | I.М | I | I |
Notation: P – performs, I – informs, A – approves, C – controls, M – monitoring.
Confirmation of compliance of kefiric products is carried out on ST of PK 3.27-2002 "An order carrying out certification of food and agricultural products".".
Order carrying out certification
1. The order carrying out certification of foodstuff defines frequency of procedures of certification and provides elimination of duplication of the work performed by the accredited bodies for certification and testing laboratories.
2. Order of certification of foodstuff:
- the order and viewing including documents for certification; the analysis of documents (the copy of the license for licensed activity is required);
- making decision on the order, including choice of the scheme of certification
- to conclude the agreement on certification with the applicant and body for certification;
- sorting, identification and tests of samples (samples); the analysis of a condition of production (if it is considered in the scheme of certification) or certification of the quality system;
- making decision on the analysis of the received results and a possibility of issue of the certificate of conformity (further - the certificate);
- The certified traceability of a product (according to the existing schedule of certification);
- In case of violation of compliance of a product to the established requirements and the appropriate address with compliance marking.
3. The applicant obtains necessary information, the recommendation and the application for certification from body for certification which he wishes. An application form - ST of PK 3.4-2008 "The state system of certification of the Republic of Kazakhstan. Procedure of ensuring compliance. General requirements
4. Together with body for certification the applicant chooses structure of certification. The body for certification makes the decision on certification, signs the contract with the applicant. The decision on the application is approved by ST of PK 3.4-2008 "The state system of certification of the Republic of Kazakhstan". Procedure of confirmation of compliance. General requirements ".
5. Raw materials, technology of cooking and other functions which characterize product type for comparison and test of a product are carried out in the reliable samples delivered to the consumer.
6. Sampling is carried out by body for certification or body of the state control of the Republic of Kazakhstan for the Contract and, if necessary, sampling can be sent to the registered testing laboratory.
7. The quantity of samples (samples) has to conform to requirements to a concrete product which has to be included in state standards, with requirements for selection and verification of normative documents for uniform procedures of certification of production. The body for certification can regulate sample weight if he has proved detection of data of safety. Samples (samples) are made by the act of sorting. Type of the Law ST PK 3.4-2008 "State system of certification of the Republic of Kazakhstan. Order carrying out potverzhdeny compliances of a product. General requirements ". The sorted samples separate and contact the main product.
8. The body for certification which is the control sample which is selected for certified tests has to provide samples (selections) of all types of products for storage in body for certification or laboratory for maintaining visibility of the certified product where permission of complaints and disagreements can be required.
9. Duration of storage of samples (samples) in laboratory has to be during period of validity of the certificate or an expiration date of a product then samples (samples) have to be returned to the applicant. Duration of control samples (selection), their requirements to marking and registration, their return and write-off are specified in documents of body for certification (test laboratory).
10. The certified testing laboratory which isn't included into body for certification is under observation of the representative of body for certification. The body for certification which has passed test bears responsibility for correctness of such tests together with testing laboratory. In this case the test report is signed by testing laboratory authorized representatives of body for certification.
11. The body for certification analyzes results of tests and prepares the decision on issue of the certificate.
Results of tests have to conform to state standards, sanitary standards and rules, etc. correctly and completely to prove compliance to the requirements and standards of safety stated in normative documents. Test reports of a product are transferred to the applicant and body for certification which certifies the number of copies of the protocol which has to be certified by body for certification.
The copy of test reports has to be stored in testing laboratory not less than three years till the expiry date. Results of tests will be stopped if test results are negative, at least, one of indicators. Negative results of tests have been sent to body for certification together with the test report. Applicants can present to certification authority certificates of the tests which are carried out to time of preparation and realization of a product or other tests which are carried out in other testing laboratory registered by the Republic of Kazakhstan.
12. Period of validity of the certificate of conformity decides by body for certification on the indication of a product and the approved schedule of certification.
13. The certificate of conformity is made out in shape with the established form. The form of the certificate on obligatory and voluntary certification of production and the rule of their filling is specified in ST of PK 3.4-2008 "The state system of certification of the Republic of Kazakhstan. General requirements ".
Besides, this group is prepared for the same group of products, as a product. If one producer has released one product and is certified according to the same standard requirements, as for a product, uniform raw materials are used, and other methods which influence safety of a ready-made product can be divided into several groups of products.
When obtaining the certificate for several names of uniform products the list of uniform names of products is displayed, and for the certificate of conformity the following addition is prepared.
14. Changes in technical documentation and process of production of the certified production have to be made by the customs applicant in accordance with the established procedure to body for certification.
15. The certified product can be noted by a mark of conformity.
Production and services are noted by the producer or the dealer according to marking. After obtaining the certificate of conformity the body for marking has to be given, with the consent of body for certification, the manufacturer or the supplier for whom entry of compliance in the certificate of conformity has to be specified.
16. The certified foodstuff is certified by body which has been certified for this product, as often as possible, and also other competent authorities as required.
An inspection is carried out at least once a year during period of validity of the certificate of conformity to confirm that products and conditions of their production still meet the requirements of certification.
Check of frequency and type of work is defined by body for certification with the schedule of certification.
Inadvertent check can be made in case information on quality of a product is obtained from consumers, dealers and also behind the state quality control of suppliers.
By results of check the statement in which results of check of options and results of other checks and also the general conclusion about a condition of release of the certified production and validity of the issued certificate of conformity are estimated is exposed. This act is stored by body for certification, his copy go to the manufacturer and the agencies participating in inspection.
17. According to results of check, in case of violation of normative documents the body for certification can suspend or cancel validity of the certificate of conformity and suspend the right to mark a product a mark of conformity if:
- if the product or test methods haven't been received by body for certification from change of normative documents;
- non-compliance with requirements of technology;
- the quality system, methods of testing and control have been changed or not agreed with body for certification;
- in case of not release of this type of a product.
The body for certification notifies the applicant, consumers and all interested parties in the system of certification on stay or cancellation of the certificate of conformity.
18. Correction of period of validity of the certificate of conformity and renewal of the marking sign has to be executed.
19. In case of non-compliance with standard requirements by the manufacturer (seller) or if they don't do it, the certification authority cancels the certificate and forbids use of a mark of conformity.
Certification of systems of quality management. Main objectives of certification of systems of quality management:
- assessment of degree of compliance of a quality management system to requirements of ST of RK ISO 9001;
- assessment of effectiveness of systems of quality management;
- increase in competitiveness of production of the Kazakhstan producers, including development and expansion of sales markets.
Certification of systems of quality management is carried out by the bodies for confirmation of compliance of systems of quality management accredited as it should be. As objects of audit can be allocated: field of certification and scope of systems of quality management; compliance of quality of production to requirements of normative documents of this production; completeness and accuracy of reflection of requirements of ISO 9001 in documents of a quality management system; functioning of a quality management system from the point of view of the actual implementation of requirements of system and ensuring its effectiveness according to ISO 9001.
Conditions of carrying out certification of systems of quality management are: work by the bodies for compliance confirmation accredited by body for accreditation to carrying out certification of systems of quality management; participation in work of experts-auditors in certification of the systems of quality management registered in the State Register of system of technical regulation of the Republic of Kazakhstan; definition of field of certification by the customer in coordination with the head of body for compliance confirmation; a possibility of presentation of additional requirements regarding legislatively adjustable sphere and requirements of consumers depending on sphere of activity of the checked organization, a type of production and the customer's wishes; a possibility of attraction to work of group on audit of technical experts in the stated area of accreditation, trainees and observers. Certification of systems of quality management in the State system of technical regulation of the Republic of Kazakhstan is based on the following principles: voluntariness, impartiality, competence, responsibility, openness, confidentiality, response to complaints.
Voluntariness. Certification of a quality management system is carried out concerning the applicants who have voluntarily shown willingness to receive the certificate of conformity to the criteria established in the State system of technical regulation of the Republic of Kazakhstan, the systems of quality management which have submitted in accordance with the established procedure the written application about it to body for confirmation of compliance and which have wished to conform to the established rules. Any coercion isn't allowed to certification.
Impartiality. For carrying out certification of systems of management the body for confirmation of compliance needs to be impartial and to fulfill requirements of ST of RK ISO/MEK 17021 and ST of RK ISO/OTU 17001. Any discrimination of participants of system is excluded (for example, unreasonable refusal in reception of the application, an unjustified delay on terms, inflated price and others).
Responsibility. The body for confirmation of compliance needs to observe the principle of responsibility and to fulfill requirements of ST oRK ISO 17021.
Openness. The body for confirmation of compliance has to provide for creation of confidence and persuasiveness of certification of systems of quality management free access of the public to the relevant information on processes of audit and certification in compliance of ST RK ISO 17021.
Confidentiality. In compliance of ST RK ISO 17021 and ST RK 1646 the body for confirmation of compliance has to save confidential certain information on the customer and results of audits.
Response to complaints. Effective response to complaints – an important way of protection of body for confirmation of compliance, his customers and other users of certification from errors, omissions or rash actions. At emergence of controversial issues on certification of systems of quality management, the applicant can submit the appeal in the order established in ST RK 3.10. The quality of production of the organization is estimated on the basis of information materials about quality. Certification of systems of quality management doesn't provide specially planned tests, analyses or measurements of indicators of quality of production. If at certification of a quality management system there are doubts in quality of production or reliability of the carried-out tests, experts-auditors can watch the tests which are carried out on the place. Payment for work on certification of systems of quality management is carried out on a contractual basis irrespective of results and consists of payment of all executed certification stages.
3 Development of regulatory documents (UIRS)
On individual work the standard of theorganization«Altyn Dan» LLC «Kefir» Specifications is developed.
The standard of the organization is developed and approved by the natural and legal entities located in the territory of the Republic of Kazakhstan for improvement of production management and the organization. The standard of the organization is developed and used in a product, process and service of the organization, including:
- product components, processing equipment, processes, their ecological and human health, safety, production requirements;
- organizational services, production management and organizational processes, i.e. control systems of the environment, product quality control, classification, coding and terminology.
UDC478.351.018.245IQC 980440001758
PQ TEA 10.51.11
Coordinate Approved
Institute on Director
Standardization andLLC «Altyn Dan»
Certification of RK
____________(Full name) ____________(Full name)
«___»______ 2018 «___»________ 2018
STANDARD OF THE ORGANIZATION
On «Kefir »
ST RK 2069-2010LLC ИУ 01 2018
Kefir
Validity period with «___»___________
to «___»__________
Дата добавления: 2018-06-27; просмотров: 332; Мы поможем в написании вашей работы! |
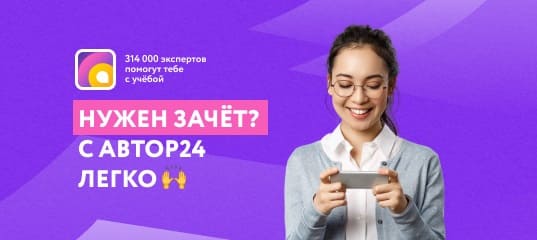
Мы поможем в написании ваших работ!