Устройство кузова полувагона.
СОДЕРЖАНИЕ
Стр. | ||
Введение. | 3 | |
1. | Конструкция четырехосного полувагона с глухим кузовом | 5 |
1.1. | Устройство кузова полувагона | 5 |
1.1.1. | Боковая стена полувагона | 5 |
1.1.2. | Торцевая стена полувагона | 6 |
1.1.3. | Рама полувагона | 7 |
1.2. | Ходовая часть | 10 |
1.3. | Автосцепное устройство | 12 |
1.4. | Расцепной привод, ударно-центрирующий прибор, упряжное устройство и опорные части | 12 |
1.5. | Поглощающий аппарат | 14 |
1.6. | Тормозное оборудование | 16 |
2. | Основные параметры грузового вагона | 18 |
2.1. | Расчет технико-экономических параметров вагона | 18 |
3. | Расчет несущих конструкций кузова | 23 |
3.1. | Расчет прочности кузова вагона | 23 |
3.2. | Уточненный расчет рамы полувагона на продольную нагрузку по МКЭ | 25 |
4. | Оценка соответствия ходовых качеств вагона требованиям «Норм» | 27 |
4.1. | Коэффициенты динамики и амплитуды ускорений | 27 |
4.2. | Показатели плавности хода | 29 |
4.3. | Коэффициент запаса устойчивости колеса от вкатывания на головку рельса | 29 |
4.4. | Валкость кузова | 32 |
5. | Расчеты прочности элементов ходовых частей | 34 |
5.1. | Боковая рама тележки | 34 |
5.2. | Колесо и ось | 37 |
5.3. | Буксовый узел | 38 |
6. | Оценка соответствия требованиям «Норм» элементов ударно-тяговых устройств | 40 |
6.1. | Проверка автоматической сцепляемости вагона | 40 |
6.2. | Проверка прохода вагоном сортировочных горок и аппарелей паромных переправ | 41 |
7. | Дополнительные оценки безопасности движения вагона, предусмотренные «Нормами» | 42 |
7.1. | Устойчивость от выжимания продольными силами | 42 |
7.2. | Устойчивость вагона от опрокидывания наружу кривой | 43 |
Список литературы | 45 | |
Графическая часть | ||
А1 | Четырехосный полувагон с глухим кузовом (Общий вид) |
|
|
Введение.
Общие закономерности циклического развития экономики отражаются в начавшемся с 1989 года сокращении объема перевозок на железных дорогах России. Но рост спроса на транспортном рынке в процессе стабилизации экономики и особенно в начале ее подъема также будет интенсивным. Вагонный парк должен быть подготовлен к этому времени заблаговременно.
В бывшем СССР грузовые вагоны выпускали семь заводов России и четыре Украины. Суммарная мощность этих заводов на 1.01.91 года составляла 73,12 тысяч единиц в год, из которых на Россию приходилось 48,5%, Украину – 51,5%. При этом действовала внутриотраслевая кооперация вагоностроительных заводов и сложившаяся система поставки комплектующих частей, полуфабрикатов, материалов.
После распада СССР в ближайшие годы необходимо создать новую схему размещения производства вагонов в России, организовать более гибкую специализацию действующих и создающихся мощностей, обеспечить наращивание производственных мощностей до уровня, определяемого потребностями народного хозяйства. Важно предусмотреть такое развитие вагоностроения, при котором потребности железнодорожного транспорта будут обеспечиваться отечественными предприятиями. Роль железных дорог в России очень велика, чтобы допустить стратегическую зависимость народного хозяйства от поставок подвижного состава из других стран.
|
|
Однако, имеющихся действующих мощностей недостаточно для удовлетворения потребностей железнодорожного транспорта. В этих условиях целесообразно создавать новые рабочие места на территории России, перепрофилировать на выпуск подвижного состава предприятий специального назначения. Важно и то, что при активном развитии отечественного производства и вагоностроения создаются наиболее благоприятные условия для изготовления запасных частей (на тех же мощностях), облегчается возможность сервисного обслуживания вагонов.
Вагоны отечественного производства значительно дешевле импортных. Цена нового современного грузового вагона в США, в зависимости от типа, колеблется от 72 тысяч до 40 тысяч долларов, что в 2,5-3 раза больше, чем цена наших вагонов. Суровые климатические условия российских железных дорог предъявляют повышенные требования к качеству металла и других материалов при температуре окружающего воздуха до -600С. в других странах, даже в Канаде, такой проблемы не существует.
|
|
Основные направления развития конструкции и параметров грузовых вагонов железных дорог России на среднесуточную перспективу представляются следующими: освоение нового поколения четырехосных вагонов с осевой нагрузкой брутто до 24,5-25,0 кН, погонной нагрузкой на путь 8-8,3 т/мп, увеличенными габаритными размерами, обеспечивающими более высокие грузоподъемность и вместимость, дальнейшее расширение парка специализированных вагонов при рациональном выборе степени специализации, которая должна обеспечить повышение качества перевозок, снизить трудоемкости и стоимости погрузочно-разгрузочных работ, сокращение, вплоть до полной ликвидации, потерь грузов и загрязнения окружающей среды, ужесточение требований к прочности, износостойкости и надежности узлов и элементов вагонов, снижение трудоемкости и стоимости ремонта, повышение безопасности движения.
|
|
В настоящее время назрела необходимость в новой системе производства грузовых вагонов на предприятиях России. Нужна максимальная, гибкая технология производства, особенно в заготовительных и сборочно-сварочных цехах и участках. Это должно помочь заводам переходить на выпуск новых моделей вагонов, быстро реагировать на изменение спроса и потребностей железнодорожного и промышленного транспорта.
С учетом имеющихся мощностей вагоностроительных предприятий России и их развития, намечаемого проектом Федеральной программы, в ближайшие годы можно ожидать освоения производства нескольких новых типов грузовых вагонов: платформы длиной 19,6 м; крытых вагонов для двухъярусной перевозки автомобилей; вагонов со съемной крышей для рулонной стали; вагоны-цистерны для перевозки нефтебензиновых грузов, цемента; вагонов-самосвалов шестиосных с грузоподъемностью 105 т, а также работы по усовершенствованию предыдущих моделей грузовых вагонов, например, четырехосных полувагонов, цельнометаллических с глухим кузовом и полом с повышенными осевой и погонными нагрузками.
1. Конструкция четырехосного полувагона с глухим кузовом.
Парк вагонов на железных дорогах СНГ состоит из нескольких миллионов единиц подвижного состава. Среди них 2,5 миллиона приходится на грузовые составы, остальные, около 700-800 тысяч единиц – на пассажирские. В составе грузового парка вагонов находятся различные типы конструкций вагонов: полувагоны, крытые вагоны, цистерны, платформы, хоппера, рефрежераторные вагоны, универсальные вагоны, а так же специализированные – для перевозки автомобилей, зерновозы, цементовозы. В перечисленном парке преобладают полувагоны. На их долю приходится 50% от состава грузового парка вагонов.
Полувагоны предназначены для перевозки каменного угля, руды, леса, проката, металлов, строительных материалов, а так же других сыпучих и штучных грузов, не требующих защиты от атмосферных осадков. По числу осей полувагоны бывают четырех-шести-, и восьмиосными. Применяются два основных типа полувагонов: с торцевыми, открывающимися внутрь вагона дверями и разгрузочными люками в полу, другой же тип представляет рассматриваемая модель четырехосного полувагона с глухим кузовом, то есть без дверей и разгрузочных люков в полу. Такие модели полувагонов используются в основном для перевозки только сыпучих грузов в замкнутых маршрутах с разгрузкой на вагоноопрокидывателях.
Конструкция полувагона состоит из следующих основных узлов: цельнометаллического кузова вагона; ходовых частей, состоящих из двух двухосных тележек модели 18-100 ГОСТ 9246-79; ударно-тяговых приборов, включающих в себя автосцепку типа СА-3, поглощающий аппарат Ш2В и тяговый хомут с клином.
Устройство кузова полувагона.
Кузов полувагона предназначен для размещения и перевозки всех грузов, не требующих укрытия от атмосферных осадков, как насыпных пылевидных, так и навалочных (за исключением горячих с температурой более 100оС), штучных, с креплением их в соответствии с требованиями правил погрузки, а также для передачи продольных сжимающих или растягивающих усилий, возникающих при движении поезда.
Кузов полувагона состоит из следующих составных частей: двух боковых стен, двух торцевых стен, рамы.
1.1.1. Боковая стена кузова полувагона (рис. 1.1.1.) состоит из стоечносварной конструкции, представляющей собой каркас и металлическую обшивку. Боковая стена является основным несущим элементом конструкции кузова, выполненной из стали 09Г2. Боковые стены кузова воспринимают вертикальные нагрузки, распорные и динамические нагрузки, действующие на полувагон при эксплуатации.
Рис. 1.1.1. Боковая стена полувагона.
Каркас боковой стены состоит из верхней 2 и нижней 5 обвязок, соединенных между собой угловыми стойками 1, шкворневыми 4 и промежуточными 3. К каркасу боковой стены приварена обшивка 6.
Верхняя обвязка предназначена для восприятия эксплуатационных нагрузок, а также нагрузок, возникающих при разгрузке вагонов на вагоноопрокидывателях. Обвязка выполнена из холодногнутого уголка 155×10×6 по ТУ-12-2-341-78 и горячекатаного по ГОСТ 5267.14-78.
Соединенные между собой сваркой, профили верхней обвязки образуют жесткую коробчатую конструкцию. Для увеличения жесткости внутри верхней обвязки установлены ребра.
Нижняя обвязка выполнена из уголка 160×100×10 ГОСТ 8510-86 и предназначена для соединения боковой стены с рамой полувагона и для соединения заделки промежуточных стоек с балками рамы.
Угловые стойки выполнены из листа и предназначены для соединения боковых и торцевых стен с рамой.
Промежуточные стойки предназначены для восприятия распорных усилий, возникающих при перевозке сыпучих грузов, соединение боковой стены с рамой полувагона представляет собой омегообразный профиль, изготовленный горячей каткой.
Обшивка изготовляется из двух периодических профилей проката по ТУ-14-2-210-77 толщиной 3,6 и 4,5 мм, соединенных внахлестку по высоте.
С внутренней стороны, для возможности осмотра и очистки кузова от груза, по диагонали расположены в полу люки.
1.1.2. Торцевая стена кузова полувагона (рис. 1.1.2.) предназначена для восприятия распорных нагрузок от действия сыпучих грузов, а также продольных инерционных, действующих на полувагон в эксплуатации.
Рис. 1.1.2. Торцевая стена полувагона.
Торцевая стена включает в себя верхнюю 1 и нижнюю 6 обвязки; два горизонтальных пояса 2; стойки 3; усиливающие стойки 5; листы обшивки 4 и 7. Горизонтальные пояса выполнены из горячекатаного проката по ТУ-14-1-2220-77, как и промежуточные стойки боковой стены и расположены параллельно верхней и нижней обвязкам по всей ширине стены.
Верхняя обвязка выполнена из холодного швеллера 144×160×90×6 мм по ГОСТ 8281-80 с усилением его планкой для создания жесткой коробчатой конструкции.
Нижняя обвязка выполнена из уголка 160×100×10 мм ГОСТ 8510-86 и предназначена для соединения торцевой стены с рамой.
Стойки выполнены из горячекатаного швеллера 12 ГОСТ 8240-72 и обеспечивают соединение торцевой стены с угловой стойкой.
Усиливающие стойки выполнены из штампованного П-образного сечения 144×90×6 и предназначены для усиления заделки торцевой стены с рамой.
Обшивка торцевой стены по ТУ-14-2-280-77 толщиной 5 мм выполнена из двух гладких листов, соединенных между собой по высоте внахлестку.
Все элементы торцевой стены соединены между собой с помощью электродуговой сварки.
1.1.3. Рама полувагона (рис. 1.1.3.1.) является одной из ответственных частей полувагона, служит основанием кузова и воспринимает вертикальную нагрузку от груза, собственного веса и веса кузова, а также ударные усилия – растягивающие и сжимающие. Через пятники на шкворневых балках рама опирается на надрессорные балки тележек. В центральные отверстия пятников и подпятников вставлены шкворни. На раме устанавливается автосцепное устройство, тормоз полувагона.
Рис.1.1.3.1. Рама полувагона.
Рама полувагона состоит из хребтовой балки 1, двух концевых балок 2, двух шкворневых 3, четырех промежуточных 4 и 5.
В средней части рамы размещены: кронштейн для тормозного оборудования, то есть тормозного цилиндра 6, кронштейн для крепления камеры 7 и угольника для крепления запасного резервуара 8. На одной из концевых балок установлен поручень сцепщика.
Хребтовая балка(рис. 1.1.3.2) воспринимает вертикальные, растягивающие, сжимающие и ударные нагрузки и предназначена для размещения автосцепного устройства и крепления кронштейнов тормозного оборудования. Она состоит из двух зетов 1 высотой 310 мм. Расстояние между вертикальными стенками внутри хребтовой балки равно 350 мм. По концам хребтовой балки расположены передние и задние упоры 4. В узле соединения хребтовой балки с шкворневыми балками установлены подпятниковые коробки 5, которые усиливают место под пятником и связывают между собой вертикальные стенки хребтовой балки. В районе установки промежуточных балок, в хребтовую балку вварены нижние листы 6 и ребро жесткости 3.
Рис. 1.1.3.2. Хребтовая балка.
Концевая балка (рис. 1.1.3.3.) представляет собой сварную конструкцию, состоящую из верхнего листа 1, лобового листа 2, двух нижних листов 4, двух листов уплотнения 3. Средняя часть листа углублена по отношению к концу на 16 мм.
Концевая балка полувагона предназначена для восприятия нагрузки от всех видов перевозимых грузов, а так же для крепления и установки торцевой стены.
Рис. 1.1.3.3. Концевая балка.
По вершинам между лобовым листом, нижним и листом уплотнения установлены ребра жесткости. На лобовом листе устанавливается поручень сцепщика 7, кронштейн расцепного привода 5 и скобы для сигнального фонаря. К нижним листам снизу приварены листы для поддомкрачивания 6.
Шкворневая балка (рис. 1.1.3.4.) предназначена для передачи через пятники и скользуны на тележку всех, возникающих в процессе движения полувагона, статических и динамических усилий.
Рис. 1.1.3.4. Шкворневая балка.
Она представляет собой конструкцию коробчатого сечения переменной высоты с верхним корытообразной формы листом, двумя вертикальными листами и нижним листом. К нижнему листу приварены скользуны. Между вертикальными листами для жесткости установлены диафрагмы. К нижнему листу, зетам и подпятниковой коробке крепится пятник.
Соединение шкворневой балки со шкворневыми стойками боковой стены осуществляется посредством накладок.
Промежуточные балки предназначены для соединения боковой стены с рамой полувагона, они воспринимают часть нагрузок, действующих на раму. Балки представляют собой сварную конструкцию двутаврового сечения переменной высоты, состоящих из вертикальных листов, нижних листов и верхнего листа, имеющего корытообразную форму (рис. 1.1.3.5.).
Рис.1.1.3.5. Промежуточная балка.
Соединение балок со стойками боковой стены осуществляется с помощью накладок.
Ходовая часть
В настоящее время грузовые вагоны железных дорог России строят с тележками типа 18-100 (рис.1.2), которые имеют клиновые гасители колебаний.
Боковая рама 3 тележки выполнена в виде стальной отливки, в средней части которой расположен проем для рессорного комплекта, а по концам — проемы для букс.
В верхней части буксовых проемов имеются кольцевые приливы, которыми боковые рамы опираются на буксы, а по бокам — буксовые челюсти.
Сечения наклонных элементов (поясов) и вертикальных стержней (колонок) боковой рамы имеют корытообразную форму с некоторым загибом внутрь концов полок. Горизонтальный участок нижнего пояса имеет замкнутое коробчатое сечение. Балки с таким профилем хорошо сопротивляются изгибу и кручению.
По бокам среднего проема в верхней части рамы расположены направляющие для ограничения поперечного перемещения фрикционных клиньев, а внизу имеется опорная поверхность для установки рессорного комплекта. С внутренней стороны к этой поверхности примыкают полки, являющиеся опорами для наконечников триангелей в случае обрыва подвесок, которыми триангели подвешены к кронштейнам боковой рамы.) В местах расположения клиньев к колонкам рамы приклепаны фрикционные планки. На наклонном поясе отливают пять цилиндрических выступов (шишек), часть которых срубается в соответствии с, фактическим расстоянием между наружными челюстями буксовых проемов. Подбор боковых рам при сборке тележек производят по числу оставленных шишек, что гарантирует соблюдение необходимых допусков для обеспечения параллельности осей колесных пар.
Надрессорная балка тележки отлита заодно с подпятником, опорами для размещения скользунов, гнездами для фрикционных клиньев и приливом для крепления кронштейна мертвой точки рычажной передачи тормоза. Балка выполнена по форме бруса равного сопротивления изгибу в соответствии с эпюрой изгибающих моментов и имеет коробчатое замкнутое сечение.
Рис.1.2 Тележка 18-100.
Автосцепное устройство
Автосцепное устройство вагона обычно состоит из следующих частей: корпуса и расположенного в нем механизма; расцепного привода; ударно-центрирующего прибора; упряжного устройства; поглощающего аппарата; опорных частей.
Устройство корпуса и механизма автосцепки определяет ее тип и конструкцию, поэтому корпус с механизмом часто называют автосцепкой.
Вагоны и локомотивы магистральных железных дорог Советского Союза оборудованы автоматической сцепкой СА-3 (советская автосцепка, третий вариант), утвержденной в 1934 г. в качестве типовой. Эта автосцепка (рис. 1.3) относится к нежестким.
Рис.1.3 Корпус автосцепки СА-3.
Дата добавления: 2018-06-27; просмотров: 12272; Мы поможем в написании вашей работы! |
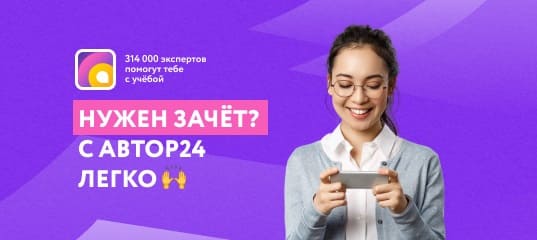
Мы поможем в написании ваших работ!