Ethylene and gas/chemical carriers
Ethylene carriers are the most sophisticated of the semi-pressurised tankers and have the ability to carry not only most other liquefied gas cargoes but also ethylene at its atmospheric boiling point of -104°C. The first ethylene carrier was built in 1966 and, as of 1995, there were about 100 such ships in service ranging in capacity from 1,000 to 12,000 m3.
Of this ethylene carrier fleet, about one dozen form a special sub-group of ships able to handle a wide range of liquid chemicals and liquefied gases simultaneously. These ships feature cylindrical, insulated, stainless steel cargo tanks able to accommodate cargoes up to a maximum specific gravity of 1.8 at temperatures ranging from a minimum of -104°C to a maximum of +80°C and at a maximum tank pressure of 4 bar. The ships can load or discharge at virtually all pressurised and refrigerated terminals, making them the most versatile gas carriers in terms of cargo-handling ability.
Fully refrigerated ships
The 1960s also saw another major development in gas carrier evolution — the appearance of the first fully refrigerated ship, built to carry liquefied gases at low temperature and atmospheric pressure between terminals equipped with fully refrigerated storage tanks. The first purpose-built, fully refrigerated LPG carrier was constructed by a Japanese shipyard, to a United States design, in 1962. The ship had four prismatic-shaped (box-like) cargo tanks fabricated from 31/2 per cent nickel steel, allowing the carriage of cargoes at temperatures as low as -48°C, marginally below the atmospheric boiling point of pure propane. Prismatic tanks enabled the ship's cargo carrying capacity to be maximised, thus making fully refrigerated ships highly suitable for carrying large volumes of cargo such as LPG, ammonia and vinyl chloride over long distances. Today, fully refrigerated ships range in capacity from 20,000 to 100,000m3.
The main types of cargo containment system utilised on board modern fully refrigerated ships are independent tanks having rigid foam insulation. Older ships can have independent tanks with loosly filled perlite insulation. In the past, there have been a few fully refrigerated ships built with semi-membrane or integral tanks and internal insulation tanks, but these systems have only maintained minimal interest.
Liquefied natural gas (LNG) carriers
At about the same time as the development of fully refrigerated LPG carriers was taking place, naval architects were facing their most demanding gas carrier challenge. This was the transport of LNG. Natural gas, another clean, non-toxic fuel, is now the third most important energy source in the world, after oil and coal, but is often produced far from the centres of consumption. Because a gas in its liquefied form occupies much less space, and because of the critical temperature of liquefied methane, the ocean transport of LNG only makes sense from a commercial viewpoint if it is carried in a liquefied state at atmospheric pressure; as such, it represents a greater engineering challenge than shipping LPG, mainly because it has to be carried at a much lower temperature; its boiling point being -162°C.
|
|
The pioneering cargo of LNG was carried across the Atlantic Ocean in 1958 and by 1964 the first purpose-built LNG carriers were in service under a long-term gas purchase agreement. LNG containment system technology has developed considerably since those early days: now about one-half of the LNG carriers in service are fitted with independent cargo tanks and one-half with membrane tanks. The majority of LNG carriers are between 125,000 and 135,000 m3 in capacity. In the modern fleet of LNG carriers, there is an interesting exception concerning ship size. This is the introduction of several smaller ships of between 18,000 and 19,000 m3 having been built in 1994 and later to service the needs of importers of smaller volumes.
1.4 THE SHIP/SHORE INTERFACE AND JETTY STANDARDS
In comparison to most other ship types, gas carriers have a better safety record. However, casualty statistics involving gas carriers demonstrate that the risk of a serious accident is potentially greater when the ship is in port than when at sea. For this reason it is appropriate that attention should concentrate on the port facilities and the activities of ship and shore personnel involved in cargo operations.
1.4.1 Safe jetty designs
The ship/shore interface is a vital area for consideration in the safety of the liquefied gas trade. Considering jetty design (and the equipment which may be needed), safety in this area requires a good understanding of ship parameters before construction begins. In this context the following points are often addressed by terminal designers:—
|
|
· The berth's safe position regarding other marine traffic
· The berth's safe position in relation to adjacent industry
· Elimination of nearby ignition sources
· Safety distances between adjacent ships
· The range of acceptable ship sizes
· Ships' parallel body length — for breasting dolphin positioning
· Suitable jetty fender designs
· Properly positioned shore mooring points of suitable strength
· Tension-monitoring equipment for mooring line loads
· Suitable water depths at the jetty
· Indicators for ship's speed of approach to the jetty
· The use of hard arms and their safe operating envelopes
· Emergency shut-down systems — including interlinked ship/shore control
· Suitable plugs and sockets for the ship/shore link
· A powered emergency release coupling on the hard arm
· Vapour return facilities
· Nitrogen supply to the jetty
· Systems for gas-leak detection
· A safe position for ship/shore gangway
· Design to limit surge pressures in cargo pipelines
· Verbal communication systems
· The development of Jetty Information and Regulations
· Jetty life saving and fire-fighting equipment
· Systems for the warning of the onset of bad weather
· The development of Emergency Procedures
Further issues have to be considered in the port approach. These may include the suitability of Vessel Traffic Management Systems, and the sizing of fairways and turning basins. However, these latter points fall outside of the scope of this publication.
1.4.2 Jetty operations
The ship/shore interface is the area where activities of personnel on the ship and shore overlap during cargo handling. Actions on one side of the interface will affect the other party and responsibility for safe operations does not stop at the cargo manifold for either ship or shore personnel. The responsibility for cargo handling operations is shared between the ship and the terminal and rests jointly with the shipmaster and
responsible terminal representative. The manner in which the responsibility is shared should, therefore, be agreed between them so as to ensure that all aspects of the operations are covered.
|
|
From an operational viewpoint it should be appreciated that at the ship/shore interface two differing cultures co-exist. To ensure safe operations, a proper understanding of the working practices of both ship and shore personnel is necessary. Equally, before and during operations, procedures of practical relevance have to be in place and jointly understood by ship and shore personnel. Most often this is best achieved by properly addressing the Ship/Shore Safety Check List (see Appendix 3) and this should be supplemented by a suitable terminal operating manual, containing Jetty Information and Regulations, which should be passed to the ship.
There is much variation in the design and operation of terminals and jetties and not all are dedicated solely to the handling of liquefied gases. Sometimes the combined nature of the products handled can complicate operations. Equally, however, variations in gas carrier and jetty construction can heighten the importance of safety issues at the interface, making them an important area requiring proper controls and good operational procedures.
LPG berths may have to handle ships of varying size and having a range of different cargo handling equipment. Jetties may be relatively new, and fitted with modern cargo facilities. Conversely, they may be relatively old using flexible hoses for cargo transfer. Of course, many jetties fall between these two extremes. At LPG berths, local design variation at the ship/shore connection may result in the need to use either hoses or all-metal hard arms. The hard arm may be hydraulically operated: it may be fitted with emergency release couplings and an emergency release system.
LNG terminals are an exception to the foregoing — they are primarily dedicated to this single product, although some LNG jetties also handle LPGs and condensates. In most cases such berths have been specially built for a particular export/import project. LNG jetties only use hard arms for cargo transfer. The hard arm is invariably hydraulically operated. Almost certainly it will be fitted with emergency release couplings and an emergency release system.
Liquefied gas cargo handling procedures can be complex and the cargo itself is potentially hazardous. For these reasons, the persons operating gas carriers and gas berths require a thorough understanding of ship and shore equipment and cargo properties. They need to have available good operating procedures so as to avoid accident and emergency plans should be in place in case an accident does occur.
For ships' personnel, much of this information is made available by means of approved courses to obtain dangerous cargo endorsements for sea-going certificates. For terminal personnel, such background may be available at national institutions;
alternatively, terminal managements may find References 2.19 and 2.32 of benefit.
Chapter 2
Дата добавления: 2018-02-28; просмотров: 798; Мы поможем в написании вашей работы! |
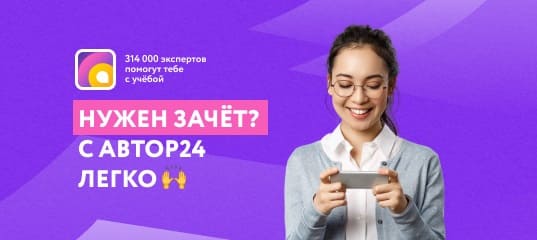
Мы поможем в написании ваших работ!