Расчет основных параметров непрерывных поточных линий
При проектировании и организации поточных линий необходимо решить следующие вопросы: -на основе заданной производственной программы выпуска изделий выбрать оборудование необходимой производительности; - рассчитать такт линии.
1.Такт - средний период времени между выпуском отдельных деталей (изделий)
r=(60 F_д)/N_b мин/шт, где Fд- действительный фонд времени работы линии;
Nb- программа выпуска деталей в шт.
2. Определим количество рабочих мест на операции (расчётное): W_рi=t_штi/r, где tштi – время выполнения i операции.
3. Принятое число рабочих мест получаем путем округления расчетного числа до ближайшего большего. За исключением тех случаев, когда перегрузка не превышает 5%.
4. Определим коэффициент загрузки оборудования на каждой операции:
K_зi=w_рi⁄W_пi
5. Определяем необходимое количество основных рабочих, выполняющих i-ю операцию. Ч_я=W_рi⁄H_oi, где Hoi - норма обслуживания рабочих мест одним рабочим.
6. Выбор вида поточной линии (непрерывно-поточная или прерывная) производится по выполнению условий синхронизации поточной линии. Синхронизация означает достижение равенства или кратности времени выполнения операции технологического процесса «установленному такту их работы». Условие синхронизации:
t_шт1/W_р1 =t_шт2/W_р2 =⋯=t_штn/W_рn =r.
Допускается отклонение от такта в пределах ± 10%, которое должно быть устранено путем проведения организационно технологических мероприятий по синхронизации операций. Способы синхронизации: 1)расчленение операций и комбинирование различных вариантов порядка их выполнения 2)концентрация операций 3)введение параллельных рабочих мест 4)рационализация рабочих приемов выполнения операции.
|
|
Производим выбор межоперационного транспорта и выполняем планировку поточной линии. Планировка должна обеспечить прямоточность, наиболее короткий путь движение предметов труда, рациональное использование производительных площадей, удобство транспортировки заготовок и деталей к рабочим местам и удобный доступ к местам обслуживания оборудования и доступ для выполнения ремонта.
Компоновка поточной линии зависит от конструкции и площади производственного здания, характера обрабатываемой детали, используемого оборудования и уровня его загрузки, а также вида применяемых ТС. На практике используются следующие формулы компоновки оборудования на поточных линиях: прямая; П,S,Х,F-образная; круговая; комбинированная. Наиболее эффективный является прямая форма компоновки при одностороннем или двустороннем расположении станков относительно ТС. Однако расположение оборудования по прямой линии требует значительной протяженности участка, поэтому на практике применяют различные формы изогнутых линий исходя из конкретных условий производства.
|
|
В поточном производстве важное значение имеет выбор средств межоперационного транспорта. Транспорт должен обеспечить бесперебойную работу потока, ритмичность выпуска, временное хранение межоперационных заделов, быть простым и надежным в работе, дешевым в изготовлении и эксплуатации ТС, применяемые в поточном производстве можно разделить на 3 группы:
1.приводные средства непрерывного или пульсирующего действия.
2.бесприводный транспорт.
3.транспорт периодического действия.
К приводным средствам относится конвейеры разного вида, которые наиболее точно отвечают требованиям непрерывно-поточного производства. Применяются следующие разновидности конвейеров: ленточные, тележечные, пластинчатые, роликовые, подвесные шнековые и т.п.
Бесприводные средства непрерывного действия основаны на использовании гравитационного принципа: бесприводные наклонные и винтовые спуски, катки, желоба и т.д.
ТС периодического действия состоит из различных грузоподъемных средств. Различные краны, тельферы, тележки, электрокары.
В непрерывно-поточном производстве применяют рабочие и распределительные конвейеры. Распределительные служат для перемещения предметов труда от одного рабочего места к другому. Для выполнения предметы труда снимаются с конвейера, куда снова устанавливаются после обработки и сборки. Применяются на сборке мелких изделий и на участках механической обработки.
|
|
Рабочие конвейеры являются не только ТС, но и представляют собой систему рабочих мест на которых ТО осуществляется без снятия предметов труда. Применяются на сборке, окраске или отделке крупных узлов агрегатов и машин при больших программах выпуска.
24. Понятие гибкой производственной системы, её структура.
Под ГПС понимают совокупность в разных сочетаниях оборудование с ЧПУ(числовое программное управление), роботизированных технологический комплексов, отдельных единиц технологического оборудования и систем обеспечения и функционирования в автоматном режиме в течение заданного интервала времени. ГПС могут автоматически переналаживаться при производстве изделий произвольной номенклатуры в установленных пределах значений их характеристик.
ГПС можно создавать на все стадиях изготовления изделий: в заготовительном, сварочном, кузнечном, сборочном производстве. Наибольшее распространение ГПС получили в механической обработке деталей. В соответствии с ГОСТ 26228-85 предусматриваются три вида ГПС:●гибкая автоматизированная линия ●гибкий автоматизированный участок ●гибкий автоматизированный цех
|
|
Основной составной частью ГПС является гибкий производственный модуль. В некоторых ГПС основной единицей м/б - роботизированный комплекс, который в отличие от модуля дополнительно оснащен промышл. роботом, а также устройствами накопления, ориентации и другими устройствами, обеспечивающими его функционирование.
Структура и состав ГПС. Структура и состав ГПС обусловлены наличием в них двух потоков: материального и информационного.Материальный поток обеспечивает подачу заготовок, инструмента, обработку изделий, транспортировку изделий со склада к станкам и обратно, установку и снятие изделий, замену инструмента, контроль за обработкой и состоянием инструмента и уборку отходов. Информационный поток обеспечивает передачу программ обработки непосредственно и исполнительным органам станка, выполнение программы работы станков, роботов, складов и передаточных механизмов, групповое управление станками и транспорто-накопительными системами, выполнение программы по управлению вспомогательными и обслуживающими процессами и планово-диспетчерскими функциями. Одним из важнейших элементов в ГПС является центральное управление всем комплексом, увязывающее в единое целое работу всех механ-ов, оборуд., тех. систем и работающее по специально разработанным программам.
ГПС - эффективное средство автоматизации серийного производства, обеспечивающее переход с выпуска одного вида продукции на другую с минимальными затратами. Эффективность ГПС достигается за счет снижение потребности в квалифицированных рабочих-станочников, оборудования и производственных площадях, а также за счет повышения качества продукции.
Рост эксплуатац. и эконом. показателей при внедрении ГПС обеспечивается за счет: 1) взаимозаменяемости основного технологического оборудования. 2)повышения коэффициента его использования. 3)повышения уровня регламентации работы производства. 4)автоматизации вспомогательных процессов. 5)концентрации операций и сокращение в связи с этим основного и вспомагательного времени. 6) использования многостаночного обслуживания и значительного сокращения сроков и объемов подготовки производств.
При расчете эффективности создания ГПС сравнение производится с группой аналогичного оборудования с обычным управлением. Задача экономического расчета заключается в определении эффективности, достигнутой путем автоматизации транспортно-складских операций, централизация управления с помощью ЭВМ, применение автоматизированных систем технологической подготовки производства, а также планирование, диспетчирования и учета хода производства. Эффективность ГПС определяется и социальными показателями, сокращением численности работников, повышением производственности труда и качества выпускаемой продукции, а также наиболее полного удовлетворения потребностей общества.
Система сетевого планирования
Система сетевого планирования и управления (ССПУ) - это один из методов кибернетического подхода к управлению сложными системами обеспечивающие получение оптимальных показателей. В зависимости от условий и заданных требований такими показателями могут быть:
●минимальное время выполнения комплекса работ
●минимальная стоимость разработки
●максимальный экономический эффект
Особенности СПУ заключаются в следующем:
- реализуется системный подход к решению вопросов организ. управления процессами.
- используется информационно-динамическая модель (сетевая) для логико-математического описания процесса и алгоритмизации расчетов параметров этого проц.
- применяются ЭВМ для обработки исх. данных и расчета необходимых параметров.
Системный подход в управлении заключается в том, что деятельность всех коллективов и исполнителей по процессу СОНТ рассматривается как единый комплекс взаимосвязанных и взаимозависимых операций направленных на достижение конечной цели.
Системы основанные на использовании сетевых моделей и электронно-вычислительной техники впервые появились в США в 56-57 г.г. в настоящее время данные методы получили развитие и распространение и основаны на новой технической базе (персональные компьютеры).
ССПУ позволяет наглядно в виде сетевой модели (графика) изобразить весь комплекс выполняемых работ и определить их взаимосвязь и взаимозаменяемость.
Параметры сетевой модели:
1) ранний срок наступления события. Для начального события =0. Для определения раннего срока свершения последующего события необходимо к крайнему сроку предыдущего события + продолжительность работы.
t_j^р=t_i^р+t_ij (мах)
2) позний срок. Для последнего события позний срок = раннему сроку. Для всех предшествующих событий необходимо из познего срока совершения последнего события вычесть работу.
t_i^n=t_j^n+t_ij(min)
3) полный резерв времени работы
П_ij=t_j^n-t_i^р-t_ij
4) свободный резерв времени
C_ij=t_j^р-t_i^п-t_ij
Дата добавления: 2015-12-21; просмотров: 18; Мы поможем в написании вашей работы! |
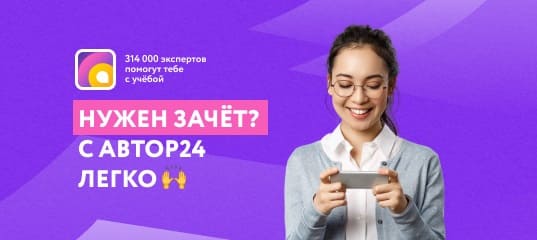
Мы поможем в написании ваших работ!