Информация в «Классификаторе» о некоторых видах дефектов.
1. Локальный прижог - может образовываться в результате врезания шлифовального круга в деталь, в результате остановки вращения детали при шлифовании или из-за отклонений геометрических параметров заготовки
Рис. 10. Полоса прижога по отверстию внутреннего кольца 2.
2. Пятнистый прижог образуется в результате завышенных режимов обработки, засаливания круга или из-за отклонений геометрических параметров заготовки
Рис. 11. Пятнистые прижоги по отверстию внутреннего кольца, выраженные вторичной закалкой и вторичным отпуском
3. Штриховой прижог может образовываться из-за завышенных режимов обработки, из-за некачественной правки круга, недостаточного охлаждения или из-за загрязнения СОЖ.
Рис. 12. Штриховые кольцевые прижоги по цилиндрической поверхности (1) и следы метального обеднения (2)
4. Периодические прижоги образуются в результате вибраций, которые воз-никают из-за: - дисбаланса шлифовального круга; - неисправной работы шпинделей шлифовального станка; - неравномерно распределенного припуска по поверхности заготовки; - увеличенного припуска на обработку.
Рис. 13. Периодические штриховые прижоги по дорожке качения
5. Трещина металлургического происхождения по цилиндрической поверхности ролика
Рис. 14. Трещина металлургического происхождения по цилиндрической поверхности ролика и
брационный наклеп (1)
|
|
6. Трещина закалочная глубокая по цилиндрической поверхности ролика
Рис. 15. Трещина закалочная глубокая по цилиндрической поверхности ролика
В работе Д.О. Пчелинцева рассматривались выборочные дефекты с геометрическими классификационными признаками, которые считывались визуально из признакового пространства (рис. 1.3). Также аппроксимирующие коэффициенты вычислялись визуальным представлением расстояний от абсолютного максимума до абсолютного минимума и обратно [1]. . Рис. 16. Определение классификационных признаков дефектов для их распознавания
Как видно из рис. 16 и рис. 17 форма сигнала у различных дефектов различная, что дает возможность распознавания неоднородностей поверхностного.
Рис. 17. Участки сканограмм и примеры формы сигналов локализованных дефектов. (Слева направо: метальная трещина, прижог, трооститное пятно).
Таким образом, рассматривая вышеприведённые рисунки, при определённых навыках и опыте, можно визуально примерно определить вид поверхностного дефекта обработанной детали. Виды недопускаемой неоднородности, связанной с абразивной обработкой приведены в таблице 2.
|
|
Вопросы для самопроверки
1. Какие виды допускаемой неоднородности (напряжённо-деформированное состояние без изменения микроструктуры) Вам известны.
2. Какой вид контроля является неразрушающим контроем.
3. Назовите известные Вам факторы, влияющие на качество обработки подшипников.
4. Опишите поле, создаваемое индукционным током.
5. Как распределяется вихревой ток в заданной зоне.
6. Как и в зависимости от чего изменяются амплитуды и фазы вихревого тока.
7. Расскажите об эффекте дроблеия вихревых токов.
8. Какой присущий вихревому току эффект положен в основу вихретоковой дефектоскопии.
9. Какова глубина проникновения вихревого тока и как он меняется с глубиной.
10. Практические использование вихревых токов в дефектоскопии.
6. Задание и порядок его выполнения.
1. Общие данные. Опытные образцы обрабатывались шлифованием на черновых и чистовых режимах: установленная черновая подача: 1,2 мм/мин - 2.4 мм/мин;
установленная чистовая подача: 0,3 мм/мин - 0,6 мм/мин.
Припуск на шлифование: 640 мкм - 670 мкм; припуск на чистовую подачу 150 мкм 200 мкм.
Диаметр образца 40мм.
2. Вы получили сканограмму. Рассмотрите её внимательно. Попробуйте визуально определить поверхностный дефект, сравнивая сканограмму с рисунками в классификаторе. Прочитайте правильный ответ на сканограмме.
|
|
3. Пошаговое пояснение выполняемой работы со сканограммой.
1.) Перед разработкой классификатора СГТУ и СПЗ – 3 проводился обучаемый эксперимент: брались образцы из подшипниковой стали диаметром 40 мм и высотой 48 мм, на них выполнялись все виды обработки резанием на самых разных режимах, а затем смотрели, какие режимы обеспечивают качественную обработку, а какие нет и дефекты.
2.) Определение дефекта выполнялось на приборе ПВК-К2М при вращении детали вокруг своей оси. Тем самым происходило как-бы развёртывание поверхности детали со всеми дефектами в прямоугольник с площадью 120*40 мм
Рис. 18. Развёртка экспериментального цилиндра (шаблон) диаметром 40 мм
В классификаторе рисунки c отображёнными на них результатами измерения были напечатаны в произвольном масштабе: длина L, высота h, т. е. эти рисунки «искажены» относительно реальных размеров.
Мы имеем искажение по оси y – Ky = 40 / H, а искажение по оси x – Kx = 120 / L
Назовём Ky и Kx коэффициентами искажений по осям X и Y.
Дата добавления: 2020-04-08; просмотров: 215; Мы поможем в написании вашей работы! |
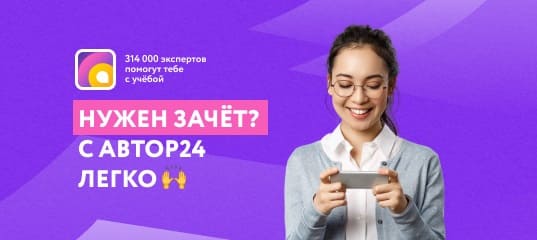
Мы поможем в написании ваших работ!